Attached files
file | filename |
---|---|
EX-32.1 - EXHIBIT 32.1 - EnSync, Inc. | exh32_1.htm |
EX-23.1 - EXHIBIT 23.1 - EnSync, Inc. | exh23_1.htm |
EX-21 - EXHIBIT 21 - EnSync, Inc. | exh21.htm |
EX-31.2 - EXHIBIT 31.2 - EnSync, Inc. | exh31_2.htm |
EX-31.1 - EXHIBIT 31.1 - EnSync, Inc. | exh31_1.htm |
EX-3.1 - EXHIBIT 3.1 - EnSync, Inc. | exh3_1.htm |
EX-4.1 - EXHIBIT 4.1 - EnSync, Inc. | exh4_1.htm |
EX-3.4 - EXHIBIT 3.4 - EnSync, Inc. | exh3_4.htm |
EX-32.2 - EXHIBIT 32.2 - EnSync, Inc. | exh32_2.htm |
UNITED STATES
SECURITIES AND EXCHANGE COMMISSION
Washington, D.C. 20549
__________________________________________________
FORM 10-K
__________________________________________________
ANNUAL REPORT PURSUANT TO SECTION 13 OR 15(d) OF THE SECURITIES EXCHANGE ACT OF 1934
For the fiscal year ended June 30, 2015
Commission File Number: 001-33540
__________________________________________________
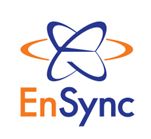
EnSync, Inc.
(Exact name of registrant as specified in its charter)
__________________________________________________
Wisconsin
|
39-1987014
|
(State or other jurisdiction of
|
(I.R.S. Employer Identification No.)
|
incorporation or organization)
|
|
N93 W14475 Whittaker Way
Menomonee Falls, Wisconsin
|
53051
|
(Address of principal executive offices)
|
(Zip Code)
|
(262) 253-9800
(Registrant’s telephone number, including area code)
__________________________________________________
Securities registered pursuant to Section 12(b) of the Act:
Title of each class
|
Name of each exchange on which registered
|
|
Common Stock, $0.01 Par Value
|
NYSE MKT
|
Securities registered pursuant to Section 12(g) of the Act: None
__________________________________________________
Indicate by check mark if the registrant is a well-known seasoned issuer, as defined in Rule 405 of the Securities Act. Yes o No þ
Indicate by check mark if the registrant is not required to file reports pursuant to Section 13 or Section 15(d) of the Act. Yes o No þ
Indicate by check mark whether the registrant (1) has filed all reports required to be filed by Section 13 or 15(d) of the Securities Exchange Act of 1934 during the preceding 12 months (or for such shorter period that the registrant was required to file such reports), and (2) has been subject to such filing requirements for the past 90 days. Yes þ No o
Indicate by check mark whether the registrant has submitted electronically and posted on its corporate website, if any, every Interactive Data File required to be submitted and posted pursuant to Rule 405 of Regulation S-T (Section 232.405 of this chapter) during the preceding 12 months (or for such shorter period that the Registrant was required to submit and post such files). Yes þ No o
Indicate by check mark if disclosure of delinquent filers pursuant to Item 405 of Regulation S-K is not contained herein, and will not be contained, to the best of the registrant’s knowledge, in definitive proxy or information statements incorporated by reference in Part III of this Form 10-K or any amendment to this Form 10-K. þ
Indicate by check mark whether the registrant is a large accelerated filer, an accelerated filer, a non-accelerated filer, or a smaller reporting company. See the definitions of “large accelerated filer,” “accelerated filer” and “smaller reporting company” in Rule 12b-2 of the Exchange Act. (Check one):
Large accelerated filer o
|
Accelerated filer o
|
Non-accelerated filer o
(Do not check if a smaller reporting company)
|
Smaller reporting company þ
|
Indicate by check whether the registrant is a shell company (as defined in Rule 12b-2 of the Exchange Act.) Yes þ No o
The aggregate market value of the voting stock held by non-affiliates, computed by reference to the last sales price on December 31, 2014, which was the last business day of the registrant's most recently completed second fiscal quarter, was $14,843,314.
The number of shares of the registrant’s Common Stock outstanding as of September 28, 2015 was 47,129,334.
DOCUMENTS INCORPORATED BY REFERENCE
The registrant intends to file a definitive proxy statement pursuant to Regulation 14A within 120 days after the end of the fiscal year ended June 30, 2015. Portions of such proxy statement are incorporated by reference into Part III of this Form 10-K.
ENSYNC, INC.
2015 FORM 10-K ANNUAL REPORT
TABLE OF CONTENTS
PART I
|
Page
|
||
Item 1.
|
Business
|
1
|
|
Item 1A.
|
Risk Factors
|
8
|
|
Item 1B.
|
Unresolved Staff Comments
|
19
|
|
Item 2.
|
Properties
|
19
|
|
Item 3.
|
Legal Proceedings
|
19
|
|
Item 4.
|
Mine Safety Disclosures
|
19
|
|
PART II
|
|||
Item 5.
|
Market for Registrant’s Common Equity, Related Stockholder Matters and Issuer Purchases of Equity Securities
|
20
|
|
Item 6.
|
Selected Financial Data
|
20
|
|
Item 7.
|
Management’s Discussion and Analysis of Financial Condition and Results of Operations
|
20
|
|
Item 7A.
|
Quantitative and Qualitative Disclosures About Market Risk
|
25
|
|
Item 8.
|
Financial Statements and Supplementary Data
|
26
|
|
Item 9.
|
Changes in and Disagreements with Accountants on Accounting and Financial Disclosure
|
54
|
|
Item 9A.
|
Controls and Procedures
|
54
|
|
Item 9B.
|
Other Information
|
55
|
|
PART III
|
|||
Item 10.
|
Directors, Executive Officers and Corporate Governance
|
56
|
|
Item 11.
|
Executive Compensation
|
56
|
|
Item 12.
|
Security Ownership of Certain Beneficial Owners and Management and Related Stockholder Matters
|
56
|
|
Item 13.
|
Certain Relationships and Related Transactions, and Director Independence
|
56
|
|
Item 14.
|
Principal Accounting Fees and Services
|
||
PART IV
|
|||
Item 15.
|
Exhibits and Financial Statement Schedules
|
57
|
|
Signatures
|
58
|
Forward-Looking Statements
The following discussion should be read in conjunction with our accompanying Consolidated Financial Statements and Notes thereto included within this Annual Report on Form 10-K. In addition to historical information, this Annual Report on Form 10-K and the following discussion contain statements that are not historical facts and are considered forward-looking within the meaning of Section 27A of the Securities Act and Section 21E of the Exchange Act. These forward-looking statements contain projections of our future results of operations or of our financial position or state other forward-looking information. In some cases you can identify these statements by forward-looking words such as “anticipate,” “believe,” “could,” “estimate,” “expect,” “intend,” “may,” “should,” “will” and “would” or similar words. We believe that it is important to communicate our future expectations to our investors. However, there may be events in the future that we are not able to accurately predict or control and that may cause our actual results to differ materially from the expectations we describe in our forward-looking statements. Investors are cautioned not to rely on forward-looking statements because they involve risks and uncertainties, and actual results may differ materially from those discussed as a result of various factors, including, but not limited to: our historical and anticipated future operation losses; our ability to raise the necessary capital to fund our operations and the risk of dilution to shareholders from capital raising transactions; our stock price volatility and trading volume; the competiveness of the industry in which we compete; our ability to successfully commercialize new products, including our Matrix TM Energy Management and Agile TM Hybrid Storage Systems; our ability to lower our costs and increase our margins; the failure of our products to perform as planned; our ability to build quality and reliable products and market perception of our products; our ability to grow rapidly while successfully managing our growth; our ability to maintain our current and establish new strategic partnerships; our dependence on sole source and limited source suppliers; our product and customer concentration and lack of revenue diversification; SPI’s ability to influence key decision making and potential to acquire complete control; our ability to enforce our agreements in Asia; our ability to retain our managerial personnel and to attract additional personnel; our ability to manage our international operations; the length and variability of our sales cycle; our increased emphasis on larger and more complex system solutions; our lack of experience in the power purchase agreement business; our reliance of third-party suppliers and contractors when developing and constructing systems for our PPA business; our ability to protect our intellectual property and the risk we may infringe on the intellectual property of others; future acquisitions could disrupt our business and dilute our stockholders; and other risks and uncertainties discussed under Item 1A. Risk Factors. Readers should not place undue reliance on our forward-looking statements. These forward-looking statements speak only as of the date on which the statements were made and are not guarantees of future performance. Except as may be required by applicable law, we do not undertake or intend to update any forward-looking statements after the date of this Annual Report on Form 10-K.
Item 1. BUSINESS
EnSync, Inc. and its subsidiaries (“EnSync,” “we,” “us,” “our,” or the “Company”) develop, license, and manufacture innovative energy management systems solutions serving the utility, commercial and industrial (“C&I”) building, utility, and off-grid markets. Incorporated in 1998, EnSync is headquartered in Menomonee Falls, Wisconsin, USA, with offices in San Francisco, California, Honolulu, Hawaii, Shanghai, China and Perth, Western Australia. In August 2015, we changed our corporate name from ZBB Energy Corporation to EnSync, Inc., and we regularly use the name EnSync Energy Systems for marketing and branding purposes.
EnSync develops and commercializes application solutions for advanced energy management systems critical to the transition from a “coal-centric economy” to one reliant on renewable energy sources. EnSync synchronizes conventional utility, distributed generation and storage assets to seamlessly ensure the least expensive and most reliable electricity available, thus enabling the future of energy networks.
Today there are generally three sources of electricity, particularly for behind-the-meter applications: conventional generation, generation from renewables and energy storage.
On their own, each of these sources can be limiting due to various factors such as cost, availability, resiliency and environmental impact. In a model environment, these disparate sources work in a synchronized manner, all three continually prioritized and optimized to always deliver the least expensive and most reliable electricity.
However, the conventional approach of power electronics provides limited capability in terms of optimization, efficiency, scalability, and the ability to accommodate ever-changing and evolving applications and policies. Essentially with a “stick-built” environment, the conventional inverter approach is inherently inflexible in what is now a dynamic world of electricity generation and load management.
1
Further complicating the realization of the model environment is that a “one size fits all” approach to energy storage has been the norm, relying on single-storage technology for both power and energy applications. The perfect battery does not exist, and forcing one type of storage technology to attempt a variety of both power and energy applications is limiting and costly.
EnSync’s energy management systems enable comprehensive functionality and provide for numerous applications that do away with limitations of conventional power electronics. EnSync’s energy management systems are being developed to provide:
|
·
|
active energy synchronization for any or all DC and AC inputs and outputs;
|
|
·
|
prioritization and optimization of all generating assets without system controllers and complex algorithms;
|
|
·
|
management of every power and energy storage application and asset in simultaneous operation; and
|
|
·
|
modular, scalable, efficient and “future proof” energy management as a 20-year asset.
|
Our energy storage system expertise enables us to design and deploy customized systems using whatever storage technology is most effective and economical for the specific needs of the customer and application, including applications where the optimum solution utilizes multiple storage technologies in a hybrid configuration. EnSync recently released the Matrix™ Energy Management System, a technology that makes it very easy to create hybrid systems by effectively “auto-segregating” power and energy applications, and pulling from the optimal battery technology to do the job without the complexity of a central control system; a highly complicated task accomplished simply and cost-effectively.
These capabilities provide the opportunity to rethink how we source electricity and monetize distributed generation and storage assets.
The macro ability to leverage the optimal use of electricity from the grid, renewables and storage is itself powerful; the ability to monetize numerous applications behind the meter provides the micro level ability to leverage almost any combination of known applications, including supply response, time-of-use, frequency regulation and back-up power.
Hybrid power and energy storage is the best way to optimize both power and energy applications, and an enabling energy management system distills all of the complexity to a simple means of creating cash behind the meter.
There is definitive movement towards the increasing complexity of applications and greater integration of functionality in order to solve more issues, while providing even higher value. We believe this trend will accelerate over the next four to five years.
We believe our energy management solutions are a significant improvement over conventional, static, 20-year asset that cannot accommodate the dynamic evolution of rate structures, programs and capabilities. We believe our solution will allow our customers to future-proof a building with an energy management system that is flexible and scalable by simply adding drawers to a cabinet, and each drawer designated as photovoltaics (“PV”), DC lighting, a diesel generator or storage, to list a few options. Hot swappable, drawer-based architecture similar to that of a rack mount server, should allow optimal uptime and reliability.
In some environments, such as remote micro grids, diesel generators could play the role of conventional generation. All of the aforementioned synchronization capabilities apply here as well, and even allow for the optimization of the diesel generation by eliminating inefficient load following by simply running the generators only at optimal efficiency to charge the batteries.
EnSync is excited about the industry shift to comprehensive energy management for behind-the-meter applications. We believe firmly that synchronization of disparate generating assets for the purpose of power and energy through state-of-the-art energy management systems is opening up numerous possibilities, as well as markets, for owners and operators of buildings, utilities, and micro grids.
2
Our goal at EnSync is to deliver the ability to lower the cost of electricity, create a more resilient grid infrastructure, prompt economic markets to leverage distributed assets and bring power to remote locales not served by traditional grid power.
Target Markets
EnSync’s energy management systems, storage technologies and power quality products target a variety of applications in three primary markets: (1) Commercial & Industrial (“C&I”) Buildings, Multi-tenant Buildings and Communities; (2) Utility Grid Power Distribution; and (3) Microgrids. We believe our solutions will enable utilities to reduce construction of under-utilized “peak” power generating plants and incorporate more renewable energy generating assets into the grid. EnSync’s ability to provide modular and configurable power control and storage solutions can be tailored to meet a variety of needs, whether it be shifting energy from low rate to high rate periods, or enabling complete grid independence.
Commercial & Industrial Buildings, Multi-Tenant Structures and Communities
EnSync offers a revolutionary energy synchronization system which we believe enables a dramatic reduction in the cost of electricity and increases the financial returns of distributed generation systems in the C&I market. Commercial and industrial buildings have become a major opportunity for distributed generation assets to create "net zero" buildings, and provide utilities with sources of energy in critical peak or critical load situations. We believe we are the only company today that can provide complete C&I building energy storage and energy management systems that unlock opportunities to generate income today, as well as "future proof" the building for any additional applications and requirements that are realized throughout the life of the asset. This includes energy management and hybrid energy storage systems.
For the C&I market, EnSync has introduced Matrix and Agile Hybrid systems engineered to:
|
·
|
enable distributed intelligence and active control of inputs and outputs inside buildings;
|
|
·
|
allow a building to be connected to others in a micro grid;
|
|
·
|
provide seamless connectivity to the utility for smart export on demand and “Internet of Energy” capability; and
|
|
·
|
create a net-zero building and deliver cash generation opportunities.
|
We recently began addressing the C&I market through power purchase agreements (“PPAs”) under which we agree to provide, and the customer agrees to purchase, electricity from us at a fixed rate for a 20-year period. Under this structure we develop and supply a system that uses our and other companies’ products and the customer receives the benefit of a low and fixed price for electricity without any upfront costs. Because this business model requires significant capital outlays, we intend to develop a monetization strategy under which we sell the PPAs we generate to investors.
Utility Grid Power Distribution
Utilities are faced with providing cheaper, cleaner and more reliable power as we transition away from a coal-centric economy which requires increased use of renewables. EnSync utility-scale energy storage systems are designed to improve power quality, smooth output from intermittent generating assets, help reduce emissions, defer transmission, distribution and substation upgrades, and reduce costs associated with traditional generating plants.
An integrated system that features Zinc Bromide flow battery technology can be partnered with Matrix power controls to provide for longer energy discharge applications prevalent in utility scale applications.
EnSync’s utility-scale flow batteries offer high energy density, are environmentally friendly, and are manufactured as 20-year assets. Multiple container units can be modularly interconnected and configured with EnSync’s inverter technology to deliver an end-to-end system for quick and simple installation. EnSync’s designs are easily transferable and portable with simple site permitting in places that can be constructed not always accessible by traditional generating sources.
Microgrids
Microgrids are localized grids that can disconnect from the traditional grid to operate autonomously and help mitigate grid disturbances to strengthen grid resilience, and can play an important role in transforming the nation’s electric grid.
Remote microgrids, in locations where utility power is not available, often use a combination of renewables, diesel generators and storage for their electricity requirements.
Resiliency, independence, environmentally friendly and cost-effective operation are key requirements for today’s microgrid environments, and we believe that EnSync is well-positioned to become the “go-to” microgrid enabling technology to deliver on these objectives.
3
Our Products
These are disruptive times for the power industry, and the industry must adapt to meet the challenges of a grid built on old technology and inefficient transmission and distribution. With an abundance of renewable energy generation being realized in various domestic and international locations, problems utilizing power from renewables persist because the grid network cannot effectively utilize the additional and inherently variable generation propensity of renewables. The grid today simply is not designed to accommodate such influxes and its intrinsic variability. Additionally, peak demand is often not realized during periods of maximum wind or sun, leading to a condition where overbuilding of heavily under-utilized generation capacity is required to meet the load during the highest usage periods of the day. Energy storage systems that are capable of long discharge can shift significant amounts of energy from relatively lower demand to higher demand periods, reducing the need for build-out of low utilization “peak power” generation.
EnSync products are designed to address the increasingly overtaxed grid networks throughout the world by enabling variable power generation from renewable sources to be introduced in large amounts in an economical, clean and reliable manner, improving the quality of life for an energy hungry population.
EnSync products have also been instrumental in enabling breakthroughs in distributed energy and micro-grid deployment in grid interactive or completely off-grid applications. From island power installations in the Pacific region to remote off-grid power for military use and diesel displacement for back-up power for buildings and facilities in Hawaii, EnSync’s advanced energy storage and power control systems deliver highly effective solutions for a variety of needs.
Matrix™ Energy Management System
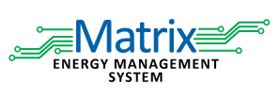
The Matrix Energy Management System is breakthrough technology as a “behind the meter” energy control system targeted specifically at the commercial, industrial and multi-tenant building markets. Matrix utilizes EnSync’s patented “Auto-Sync” DC-Bus Modular Controls that enable simple integration of all AC and DC system inputs, and automatically routes the generated electricity in the most efficient and cost-effective manner, in or out of the building. Matrix is modular and configurable, designed to meet the building owner’s needs today, as well as providing a “future proof” solution for potential applications tomorrow. Matrix enables complete distributed generation asset-to-utility communication for “smart export” and is able to be clustered in a secure network as a set of assets that enable real-time spot market electricity sales. Serviceability is simple with “hot swappable” drawers that can be replaced without taking the entire distributed generation system off line. DC-DC, DC-AC, and AC-DC transformers and communications drawers are all configurable to the same universal architecture in either single or multiple Matrix cabinets.
The full UL certification process of the Matrix system is well underway. This includes all individual medium power modules in the Matrix portfolio as well as the comprehensive modular integration for any combination of modularity, making the Matrix a fully configurable UL certified system for the commercial and industrial markets as well as distributed assets in the Electrical Utility market. As the Matrix is considered a “platform”, it has a roadmap for incorporation of features, functionality, capabilities and higher power ratings, whether created organically or from third parties. With basic DC-DC and DC-AC power conversion capability complete, the efforts ahead are on execution of the platform roadmap.
4
Advanced Energy Storage Products

The Agile Hybrid Storage System is forward-looking technology that seamlessly combines a variety of storage units to meet a breadth of applications. EnSync’s Agile Hybrid Series is an energy storage system optimized specifically for high performance, safety, longevity and ability to deliver both power and energy for all available behind-the-meter applications in commercial, industrial, multi-tenant and resort buildings.
The Agile Hybrid Series features EnSync’s flow battery which recently achieved third-party certification from a leading, globally-recognized test facility in China that validated the battery achieved performance at or beyond design and company specifications. Along with our flow battery, the Agile Hybrid integrates complementary storage technology best suited for the balance of applications, which is often Lithium-ion batteries because it marries well with renewable firming and other short-discharge, high-power applications. Highlights of the Agile Hybrid Storage System include:
|
·
|
Power and energy applications in one integrated platform - power applications: PV ramp, frequency regulation, power quality - energy applications: demand response, rate shifting, critical back-up power;
|
|
·
|
Configurable for any building, any application requiring discharge time from seconds to greater than 8 hours;
|
|
·
|
Controlled via a patented “Auto-Sync” DC-Bus;
|
|
·
|
High power, frequent cycling applications served by best-in-class Li-ion chemistry;
|
|
·
|
Li-ion is managed within its optimum operating range for extended life;
|
|
·
|
Hybridized solution with the potential to unlock additional value streams;
|
|
·
|
Long duration, deep discharge applications met with 4th generation zinc bromide flow chemistry;
|
|
·
|
System optimized for high performance, safety and longevity;
|
|
·
|
Modular and scalable to meet requirements for a wide variety of applications and locations; and
|
|
·
|
Field proven ability to perform in diverse operating environments.
|
Agile Hybrid Large-Format Storage
The Agile Hybrid Large-Format Storage System delivers all of the advantages of the smaller format described above, but in a larger format for larger scale applications. Highlights of the large-format system include:
|
·
|
Operates as a self-contained, 480VAC interconnected container, designed for drop and deploy in larger scale C&I installations;
|
|
·
|
Modular and can be interconnected on the AC for larger installations;
|
|
·
|
The system includes a 450 kWh zinc bromide flow battery, 160kWh Li-ion battery, 250kW 480VAC inverter and inputs for PV, wind or alternate power inputs;
|
|
·
|
The communications and control interface is designed for easy integration into C&I level Building Management Systems or utility integrated control through SCADA;
|
|
·
|
Internally, all components are interconnected on a 725-820VDC bus using the patented EnSync integration platform to provide real-time control and millisecond level electrical response to variable loads and intermittent renewable power; and
|
|
·
|
The on-board module controller is capable of hybrid battery control logic, which instantly dispatches rapid power response to the Li-ions and energy response to the flow battery providing maximum system efficiency, reliability and monetization options.
|
EnSync Utility Scale Flow Battery
Primarily for utility scale applications, EnSync offers a 945kWh, 0-465kW zinc bromide flow battery module, designed for interconnection via a 725-820 VDC bus to other system containers that provide options to include additional flow batteries, Li-ion or other battery types for hybridization, power electronics for integration of PV or other generating assets and inverter modules that lead to the desired VAC interconnection.
This product is designed to be more flexible than the basic large format in its configuration and engineered to be deployed in larger applications. The communications and control are facilitated at the utility level, and the EnSync patented hybrid control and DC integration logic is incorporated just as it is in the large format hybrid.
5
Power Quality - GridStrong™ Distribution Grid Control
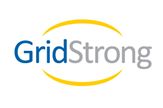
As a natural extension of our proven EnSync power electronics platform, we have engineered GridStrong technology to improve power quality, integrate Conservation Voltage Reduction (“CVR”) and improve Volt/Var Optimization (“VVO”) at “edge of the grid” distribution networks. With the ever-increasing deployment of smart meters, and penetration of distributed renewables, utilities require better control of their distribution system.
GridStrong technology supplies the aforementioned benefits, and offers a smart meter function to provide the utility with real time feedback, insight and high resolution of local events. This capability can be integrated into the existing customer supervisory control and data acquisition (“SCADA”) telemetry, or as a stand-alone software solution such as VVO or CVR. The GridStrong technology can be controlled by a central command in various operation modes and with a local autonomous control, allowing multiple systems to be deployed in a common area without issue.
Strategic Partners
We continue to utilize strategic partners to maximize our speed to market with solutions, augment our capabilities and expand our global presence. EnSync has formalized and is executing on joint development and joint venture agreements in South Korea and China, and we will continue to evolve strategic relationships in geographic markets that offer rapid and substantial growth opportunities. These strategic partners offer numerous benefits, such as market entry and penetration, low-cost manufacturing, financial consideration, technical complement, government relationships and integration as well as support services.
Our product licensing and development agreements with Lotte Chemical in South Korea have enabled us to fund development programs and significantly reduce our development cycle time. Meineng Energy, our China joint venture, has enabled us to expand our production in a low cost region, in addition to significantly increasing our post-prototype test and characterization capability. Both partners have spread the EnSync brand to their respective regions. Additionally, in July 2015 we entered into a strategic partnership with Solar Power, Inc. In addition to receiving significant investment capital from Solar Power, Inc. (“SPI”), we also entered into a Supply Agreement under which we expect to sell products and related services with an aggregated total of at least 40 megawatt of energy storage over the course of the next four years.
Competition
As discussed elsewhere in this Business section of this Annual Report on Form 10-K, we believe our technologies and products provide us with certain competitive advantages in the markets we serve. However, even with these advantages, the market for renewable energy products and services is intensely competitive and continually impacted by evolving industry standards, rapid price changes and product obsolescence. Our competitors include many domestic and foreign companies, most of which have substantially greater financial, marketing, personnel and other resources than we do. Although we believe that the advantages described above and elsewhere in this Business section of this Annual Report on Form 10-K position us well to be competitive in our industry, as a small company, we are and will continue to be at a competitive disadvantage to most of our competitors, particularly for large utility contracts.
6
Intellectual Property
Our market position, in part, depends on our Intellectual Property (“IP”) portfolio and our ability to obtain and maintain intellectual property protection for our products, processes, technology and know-how. We seek to protect our IP by, among other methods, filing United States and foreign patent applications related to our proprietary technology, inventions and improvements that are important to the development and conduct of our business. We also rely on trademarks, trade secrets, know-how and continuing technological innovation to evolve and secure our proprietary position. When it is determined that a trade secret is the most prudent approach to IP protection, we employ confidentiality agreements with our employees, customers, prospective customers, consultants, advisors, contractors or any other entity requiring knowledge of our IP for technology development or business development reasons.
We continue to have domestic and international patents issued on our power and energy control architecture known as the “Auto-Sync” modular DC-Bus, which is utilized in our new Matrix Energy Management System and our legacy EnerSection family of products. Most recently, the original patent was issued in the European Union. We have received an additional patent, the original “Auto-Sync” patent, in the US, with patents pending internationally. Additionally, we have multiple patents pending on power conversion control concepts domestically and internationally related to renewable energy optimization. We have filed for multiple patents in areas of energy storage technology and applications and control technologies, both domestically and internationally. Our filings are intended to further our differentiation, as our ability to control complex functions in simple and economical ways is unique. Areas such as hybridized storage technologies and concurrent control of multiple applications without the requirement for complicated control schemes are breakthroughs for the commercial and industrial building market, and are foundational to our Agile Hybrid Energy Storage and Matrix Energy Management System products that were introduced at the end of fiscal year 2015. EnSync also continues to do basic research on materials and chemistries for energy storage. This is an area where know-how, in addition to IP, is critical.
EnSync views the “Internet of Energy” as a key developing market. We have critical building blocks that can enable efficient and economic deployment and control of distributed generation and storage assets throughout the grid network, delivering high value to both utility as well as distributed generation asset owners. EnSync’s control expertise and ability to leverage third-party data will be an enabling capability for a future where spot market buying and selling of electricity between asset owners and the utility is realized. We will continue to invest in the development of our control and communication technologies to that end, which we believe will allow EnSync to be the “hub” through which electricity and communication between the generating assets and the utility passes.
We use trademarks on some of our products and systems, and have added registration of our “Auto-Sync” DC-Bus, Matrix, Agile, GridStrong and other roadmap products this year in the United States and internationally.
Advanced Engineering and Development
Our key advanced engineering initiatives and achievements are:
|
·
|
Completion of the next generation zinc bromide flow battery product – Agile Flow, with successful 3rd party validation at the top grid product test and certification facility in China.
|
|
·
|
Completion of zinc bromide/Li-ion Hybrid energy storage platform – Agile Hybrid.
|
|
·
|
Completion of the next generation of power electronics platform – Matrix Energy Management System.
|
|
·
|
Completion of the next generation of dynamic var compensator – GridStrong.
|
|
·
|
Design and development our utility scale flow battery products, including the Lotte 500kWh product.
|
|
·
|
Development of a control and communication platform to link the distributed generation assets to the utility, a key enabler of the “Internet of Energy”.
|
|
·
|
Design and development of the High Power version of the Matrix Energy Management System targeted for utility scale markets.
|
|
·
|
Design and development of a high power, zinc bromide/Li-ion/Matrix integrated system incorporating PV and other renewable and advanced energy generation capability into a single large format modular system.
|
The goal of these initiatives is to deliver differentiated product and service solutions that enable the massive expansion of renewable energy generation.
Our advanced engineering and development expense and cost of engineering and development revenues totaled approximately $6.7 million and $5.5 million in the years ended June 30, 2015 and June 30, 2014, respectively. We also had engineering and development revenues of approximately $771,000 and $1.3 million in the years ended June 30, 2015 and June 30, 2014, respectively.
7
Employees
EnSync currently has a total of 59 full-time employees in the United States and China. We expect staffing numbers to increase as our business grows in accordance with our business expansion plans.
Available Information
Our Annual Report on Form 10-K, our Quarterly Reports on Form 10-Q and any Current Reports on Form 8-K that we may file or furnish to the SEC pursuant to Sections 13(a) or 15(d) of the Securities Exchange Act of 1934 as well as any amendments to any of those reports are available free of charge on or through our website as soon as reasonably practicable after we file them with or furnish them to the SEC electronically. Our website is located at www.ensync.com. In addition, you may receive a copy of any of our reports free of charge by contacting our Investor Relations department at our corporate headquarters.
Item 1A. RISK FACTORS
We operate in a rapidly changing environment that involves a number of risks, some of which are beyond our control. This discussion highlights some of the risks which may affect future operating results. These are the risks and uncertainties we believe are most important for you to consider. We cannot be certain that we will successfully address these risks. If we are unable to address these risks, our business may not grow, our stock price may suffer and we may be unable to stay in business. Additional risks and uncertainties not presently known to us, which we currently deem immaterial or which are similar to those faced by other companies in our industry or business in general, may also impair our business operations.
We have incurred losses since our inception in 1998 and anticipate incurring continuing losses.
For the fiscal year ended June 30, 2015, we had revenues of $1,763,510. During this period, we had a net loss of $12,885,807 after deducting the net loss attributable to the noncontrolling interest. There can be no assurance that we will have income from operations or net income in the future. As of June 30, 2015 we had an accumulated deficit of $102,674,048. As discussed in our financial statements our significant operating losses and operating cash flow deficits raise doubt about our ability to continue as a going concern. We anticipate that we will continue to incur losses and operating cash flow deficits until we can produce and sell, if ever, a sufficient number of our systems to be profitable. However, we cannot predict when we will operate profitably, if ever. Even if we do achieve profitability, we may be unable to sustain or increase our profitability in the future.
We may require a substantial amount of additional funds to finance our capital requirements and the growth of our business, and we may not be able to raise a sufficient amount of funds, or be able to do so on terms favorable to us and our stockholders, or at all.
We have incurred losses since our inception in 1998 and expect to continue to incur losses until we are able to significantly grow our revenues. Accordingly we may need additional financing to remain in operation and to maintain and expand our business, and such financing may not be available on favorable terms, if at all. In the event that we issue any additional equity securities, investors’ interests in the Company will be diluted and investors may suffer dilution in their net book value per share depending on the price at which such securities are sold. Further, any such issuance may result in a change in control.
If we are unable to obtain the necessary funds on acceptable terms, we may not be able to:
|
·
|
execute our growth plan;
|
|
·
|
take advantage of future opportunities;
|
|
·
|
respond to customers and competition; or
|
|
·
|
remain in operation.
|
We may issue debt and/or senior equity securities in the future which would be senior to our common stock upon liquidation. Upon liquidation, holders of our debt securities, senior equity securities and lenders with respect to other borrowings will receive distributions of our available assets prior to the holders of our common stock. As a result of the significant number of convertible preferred shares outstanding, our common stockholders may receive nothing in the case of a liquidation event.
8
Our stock price could be volatile and our trading volume may fluctuate substantially.
The price of our common stock has been and may in the future continue to be extremely volatile, with the sale price fluctuating from a low of $0.40 to a high of $30.00 since June 18, 2007, the first day our stock was traded on the NYSE MKT. Many factors could have a significant impact on the future price of our common stock, including:
|
·
|
the various risks and uncertainties discussed herein;
|
|
·
|
general domestic and international economic conditions and other external factors;
|
|
·
|
general market conditions; and
|
|
·
|
the degree of trading liquidity in our common stock.
|
In addition, the stock market has from time to time experienced extreme price and volume fluctuations. This volatility has had a significant effect on the market price of securities issued by many companies which may be unrelated to the operating performance of those particular companies. These broad market fluctuations may adversely affect our share price, notwithstanding our operating results.
For the three-month period ended June 30, 2015, the daily trading volume for shares of our common stock ranged from 59,000 to 4,224,300 shares traded per day, and the average daily trading volume during such three-month period was 446,018 shares traded per day. Accordingly, our investors who wish to dispose of their shares of common stock on any given trading day may not be able to do so or may be able to dispose of only a portion of their shares of common stock.
SPI could sell or transfer a substantial number of shares of our common stock, which could depress the price of our securities or result in a change in control of the Company.
SPI currently holds 8,000,000 shares of our common stock and convertible preferred stock and a warrant that, assuming full conversion and exercise, would result in the ownership by SPI of an additional 92,000,600 shares of our common stock. SPI has no contractual restrictions on its ability to sell or transfer our common stock on the open market, in privately negotiated transactions or otherwise, and these sales or transfers could create substantial declines in the price of our securities or, if these sales or transfers were made to a single buyer or group of buyers, could contribute to a transfer of control of the Company to a third party. Sales by SPI of a substantial number of shares, or the expectation of such sales, could cause a significant reduction in the market price of our common stock.
Our industry is highly competitive and we may be unable to successfully compete.
We compete in the market for renewable energy products and services which is intensely competitive. Evolving industry standards, rapid price changes and product obsolescence also impact the market. Our competitors include many domestic and foreign companies, most of which have substantially greater financial, marketing, personnel and other resources than we do. Our current competitors or new market entrants could introduce new or enhanced technologies, products or services with features that render our technologies, products or services obsolete or less marketable. Our success will be dependent upon our ability to develop products that are superior to existing products and products introduced in the future, and which are cost effective. In addition, we may be required to continually enhance any products that are developed as well as introduce new products that keep pace with technological change and address the increasingly sophisticated needs of the marketplace. Even if our current technologies prove to be commercially feasible, there is extensive research and development being conducted on alternative energy sources that may render our technologies and protocols obsolete or otherwise non-competitive.
There can be no assurance that we will be able to keep pace with the technological demands of the marketplace or successfully develop products that will succeed in the marketplace. As a small company, we will be at a competitive disadvantage to most of our competitors, which include larger, established companies that have substantially greater financial, technical, manufacturing, marketing, distribution and other resources than us. There can be no assurance that we will have the capital resources available to undertake the research which may be necessary to upgrade our equipment or develop new devices to meet the efficiencies of changing technologies. Our inability to adapt to technological change could have a materially adverse effect on our results of operations.
9
Our ability to achieve significant revenue growth will be dependent on the successful commercialization of our new products, including our Agile Hybrid Storage System and Matrix Energy Management System.
We anticipate that a substantial majority of our revenue in fiscal year 2016 will come from new products, including our Agile Hybrid Storage System and Matrix Energy Management System. If these new products do not meet with market acceptance, our business, financial condition and results of operations will be adversely affected. A number of factors may affect the market acceptance of our new products, including, among others:
|
·
|
the price of our products relative to other products either currently available or subsequently introduced;
|
|
·
|
the perception by potential customers and strategic partners of the effectiveness of our products for their intended purposes;
|
|
·
|
our ability to fund our manufacturing, sales and marketing efforts; and
|
|
·
|
the effectiveness of our sales and marketing efforts.
|
Our products are and will be sold in new and rapidly evolving markets. As such, we cannot accurately predict the extent to which demand for these products will increase, if at all. We do not know whether our targeted customers will accept our technology or will purchase our products in sufficient quantities to allow our business to grow. To succeed, demand for our products must increase significantly in existing markets, and there must be strong demand for products that we introduce in the future. The commercial success of our new products is also dependent on the design and development of an efficient and cost effective means to integrate such products into existing electrical systems.
To achieve profitability, we will need to lower our costs and increase our margins, which we may not be able to do.
To achieve profitability we will need to lower our costs and increase our margins. These efforts may fail due to unforeseen factors. Our failure to lower our costs could make our products less competitive and harm our ability to grow our revenues. Our inability to lower our costs and increase our margins could have a materially adverse effect on our results of operations.
If our products do not perform as planned, we could experience increased costs, lower margins and harm to our reputation.
We have developed a portfolio of new products. The failure of our products to perform as planned could result in increased costs, lower margins and harm to our reputation which could have a material adverse effect on our business and financial results. For example a substantial majority of our revenue in recent periods came from our third generation ZBB EnerStore zinc bromide flow battery and ZBB EnerSection power and energy control center; as we initially reported in August, 2014, subsequent to commercialization, installation and commissioning of units in the field we garnered meaningful insights that resulted in system design modifications and other general upgrades that improved performance, efficiency, and reliability. In the interest of enhancing customer satisfaction and market reputation, in the fourth quarter of fiscal 2014 we launched an initiative to implement these improvements at certain locations of our installed base over fiscal 2015. As a result of this initiative, results of operations for the quarter ended June 30, 2014 included a charge of $1.8 million.
We need to continue to improve the performance of our products to meet future requirements and competitive pressures.
We need to continue to improve various aspects of our technology as we move forward with larger scale production and new applications of our products. For example, through our collaboration with Lotte Chemical Corporation we are currently working to develop a 500kWh version of our zinc bromide battery. Our products are complex and there can be no assurance our development efforts will be successful. Future developments and competition may reveal additional technical issues that are not currently recognized as obstacles. If we cannot continue to improve the performance of our products in a timely manner, we may be forced to redesign or delay large scale production or possibly abandon our product development efforts altogether.
We must build quality products to ensure acceptance of our products.
The market perception of our products and related acceptance of such products is highly dependent upon the quality and reliability of the products we build. Any quality problems attributable to our product lines may substantially impair our revenue and operating results. Moreover, quality problems for our product lines could cause us to delay or cease shipments of products or have to recall or field upgrade products, thus adversely affecting our ability to meet revenue or cost targets. In addition, while we seek to limit our liability as a result of product failure or defects through warranty and other limitations, if one of our products fails, a customer could suffer a significant loss and seek to hold us responsible for that loss and our reputation with other current or potential customers would likely suffer.
10
To succeed, we will need to rapidly grow and we may not be successful in managing this rapid growth.
In order to successfully grow our revenues and become profitable as well as meet the target set forth in our Supply Agreement with SPI, we will need to grow rapidly. If we fail to effectively manage this growth, our business could be adversely affected. Rapid growth will place significant demands on our management, operational and financial infrastructure. If we do not effectively manage our growth, we may fail to timely deliver products to our customers in sufficient volume or the quality of our products could suffer, which could negatively affect our operating results. To effectively manage this growth, we will need to hire additional personnel, and we will need to continue to improve our operational, financial and management controls and our reporting systems and procedures. As we move forward in commercializing our new products, we will also need to effectively manage our manufacturing and marketing needs, which represent new areas of oversight for us. These additional employees, systems enhancements and improvements will require significant capital expenditures and management resources. Failure to successfully implement these improvements could hurt our ability to manage our growth and our financial position.
Our relationships with our strategic partners may not be successful, and we may not be successful in establishing additional partnerships, which could adversely affect our ability to commercialize our products and services.
An important element of our business strategy is to enter into strategic partnerships with partners who can assist us in achieving our business goals. We are currently a party to several strategic partnership arrangements and any disruption in these collaborations could be detrimental to our business. The most significant of these strategic partnerships is our partnership with SPI. We expect to seek additional collaborators or strategic partners due to the expense, effort and expertise required to develop market and commercialize our products and our limited resources, but we may not be successful in our efforts to establish additional strategic partnerships and arrangements. If our strategic partners do not satisfy their obligations to us, we are unable to meet our strategic partners’ expectations and demands or we are unable to reach agreements with additional suitable strategic partners, we may fail to meet our business objectives for the commercialization of our products. The terms of any additional strategic partnerships or other arrangements that we establish may not be favorable to us. Our inability to successfully implement strategic partnerships and arrangements could adversely affect our business, financial condition and results of operations.
We expect that a significant portion of our sales will be to a single customer.
On July 13, 2015, in connection with the closing of the transaction between the Company and SPI, we entered into a Supply Agreement with SPI pursuant to which we agreed to provide SPI with Products and related Services (each as defined in the Supply Agreement) that have an aggregated total of at least 40 megawatt of energy storage rated power output prior to the 48-month anniversary of the date of the Supply Agreement with certain lower megawatt thresholds being required to be met at the 12-month, 24-month and 36-month anniversaries of the Supply Agreement. While we are continually seeking to expand our customer base, we anticipate that orders under the Supply Agreement will comprise a very significant portion of our sales through at least fiscal 2019. This arrangement makes us significantly dependent on SPI. Any decline in the anticipated orders from SPI or the failure of SPI to satisfy its obligations under the Supply Agreement could have an adverse impact on our business, financial condition and results of operations. Our future success is dependent upon the anticipated purchases by SPI. In addition, our dependence on our strategic partnership with SPI exposes us to numerous other risks, including: (i) a slowdown or delay in SPI’s deployment of our products could significantly reduce demand for our products; (ii) current or future economic conditions could negatively affect SPI and cause them to significantly reduce operations, or file for bankruptcy; and (iii) concentration of accounts receivable credit risk, which could have a material adverse effect on our liquidity and financial condition if SPI declared bankruptcy or delayed payments due under the Supply Agreement. Finally, if we are unable to meet our obligations to SPI under the Supply Agreement, SPI may terminate the agreement which would have a material adverse impact on our business, financial condition and results of operations.
We depend on sole and limited source suppliers and outsource selected component manufacturing, and shortages or delay of supplies of component parts may adversely affect our operating results until alternate sources can be developed.
Our operations are dependent on the ability of suppliers to deliver quality components, devices and subassemblies in time to meet critical manufacturing and distribution schedules. If we experience any constrained supply of any such component parts, such constraints, if persistent, may adversely affect operating results until alternate sourcing can be developed. There may be an increased risk of supplier constraints in periods where we are increasing production volume to meet customer demands. Volatility in the prices of component parts, an inability to secure enough components at reasonable prices to build new products in a timely manner in the quantities and configurations demanded or, conversely, a temporary oversupply of these parts, could adversely affect our future operating results.
11
We purchase several component parts from sole source and limited source suppliers. As a result of our current production volumes, we lack significant leverage with these and other suppliers especially when compared to some of our larger competitors. If our suppliers receive excess demand for their products, we may receive a low priority for order fulfillment as large volume customers may receive priority that may result in delays in our acquiring components. If we are delayed in acquiring components for our products, the manufacture and shipment of our products could be delayed. Lead times for ordering materials and components vary significantly and depend on factors such as specific supplier requirements, contract terms, the extensive production time required and current market demand for such components. Some of these delays may be substantial. As a result, we sometimes purchase critical, long lead time or single sourced components in large quantities to help protect our ability to deliver finished products. If we overestimate our component requirements, we may have excess inventory, which will increase our costs. If we underestimate our component requirements, we will have inadequate inventory, which will delay our manufacturing and render us unable to deliver products to customers on scheduled delivery dates. Manufacturing delays could negatively impact our ability to sell our products and could damage our customer relationships.
To assure the availability of our products to our customers, we outsource the manufacturing of selected components prior to the receipt of purchase orders from customers. However, we do not recognize revenue for such products until we receive an order from a customer and the product is shipped. As demand for our products may not materialize, this product delivery method subjects us to increased risks of high inventory carrying costs, obsolescence and excess, and may increase our operating costs. In addition, we may from time to time make design changes to our products, which could lead to obsolescence of inventory.
We have no experience manufacturing our products on a large-scale basis and may be unable to do so at our manufacturing facilities.
To date, we have achieved only very limited production of our energy storage systems and have no experience manufacturing our products on a large-scale basis. In connection with our strategic partnership with SPI, we will have to increase our production of products significantly and rapidly. We believe our current facilities in Menomonee Falls, Wisconsin, are sufficient to allow us to significantly increase production of our products. However, there can be no assurance that our current facilities, even if operating at full capacity, will be adequate to enable us to produce the energy storage systems in sufficient quantities to meet potential future orders, including orders we anticipate receiving under the Supply Agreement with SPI. Our inability to manufacture a sufficient number of units on a timely basis would have a material adverse effect on our business prospects, strategic partner relationships, financial condition and results of operations. In addition, even if we are able to meet production requirements, we may not be able to achieve margins that enable us to become profitable.
We are subject to risks relating to product concentration and lack of revenue diversification.
We derive a substantial portion of our revenue from a limited number of products. These products are also an integral component of many of our other products. We expect these products to continue to account for a large percentage of our revenues in the near term. Continued market acceptance of these products is therefore critical to our future success. Our future success will also depend on our ability to reduce our dependence on these few products by developing and introducing new products and product or feature enhancements in a timely manner. Specifically, our ability to capture significant market share depends on our ability to develop and market extensions to our existing product lines at higher and lower power range offerings and as containerized solutions. We are currently investing significant amounts in our products to broaden our product portfolio. Even if we are able to develop and commercially introduce new products and enhancements, they may not achieve market acceptance and the revenue generated from these new products and enhancements may not offset the costs, which would substantially impair our revenue, profitability and overall financial prospects. Successful product development and market acceptance of our existing and future products depend on a number of factors, including:
|
·
|
changing requirements of customers;
|
|
·
|
accurate prediction of market and technical requirements;
|
|
·
|
timely completion and introduction of new designs;
|
|
·
|
quality, price and performance of our products;
|
|
·
|
availability, quality, price and performance of competing products and technologies;
|
|
·
|
our customer service and support capabilities and responsiveness;
|
|
·
|
successful development of our relationships with existing and potential customers; and
|
|
·
|
changes in technology, industry standards or end-user preferences.
|
12
SPI has significant influence over key decision making and may ultimately acquire complete control of the Company.
On July 13, 2015, in connection with the closing of the transaction between the Company and SPI, we issued SPI 8,000,000 shares of our common stock and convertible preferred stock and a warrant that, assuming full conversion and exercise, would result in the ownership by SPI of an additional 92,000,600 shares of our common stock. SPI’s 8,000,000 common shares represent approximately 17% of the outstanding common stock of the Company and, as a result, it may have the ability to exert influence over the outcome of matters submitted to our shareholders for approval. Additionally, the certificate designations, preferences, rights and limitations of SPI’s convertible preferred stock allow it to vote on an as-converted basis on amendments to the Company’s Articles of Incorporation and Bylaws. Assuming the full conversion of SPI’s convertible preferred stock (and that no other shares of common stock are issued pursuant to the exercise or conversion of outstanding derivative securities or otherwise), it would own greater than a majority of the outstanding common stock and would have the ability to exert complete control of the Company. As a shareholder, SPI is entitled to vote its shares in its own interest, which may not always be in the interests of our shareholders generally.
Additionally, the Company is party to a Governance Agreement with SPI (the “Governance Agreement”). Under the Governance Agreement, SPI is entitled to nominate one director to our board of directors for so long as SPI holds at least 10,000 convertible preferred shares or 25 million shares of common stock or common stock equivalents (the “Requisite Shares”). Additionally, for so long as SPI holds the Requisite Shares (1) following the time at which the Series C-2 Preferred Stock shall have become convertible in full, SPI shall be entitled to nominate a total of two directors and (2) following the time at which the Series C-3 Preferred Stock shall have become convertible in full, SPI shall be entitled to nominate a total of three directors. The more representation that SPI gets on our board of directors, the more it will be able to influence the direction of the Company.
The Governance Agreement also provides that for so long as SPI holds the Requisite Shares, we will not take certain actions without the affirmative vote of SPI, including the following: (a) change the number or manner of appointment of the directors on the board; (b) other than in the ordinary course of conducting the Company’s business, cause the incurrence, issuance, assumption, guarantee or refinancing of any debt if the aggregate amount of such debt and all other outstanding debt of the Company exceeds $10 million; (c) cause the acquisition of an interest in any entity or the acquisition of a substantial portion of the assets or business of any entity or any division or line of business thereof or any other acquisition of material assets, in any such case where the consideration paid exceeds $2 million, or cause the Company to engage in certain other Fundamental Transactions (as defined in the certificate of designation of preferences, rights and limitations of the Series C Convertible Preferred Stock); (d) cause the entering into by the Company of any agreement, arrangement or transaction with an affiliate that calls for aggregate payments (other than payment of salary, bonus or reimbursement of reasonable expenses) in excess of $120,000; (e) cause the commitment to capital expenditures in excess of $7 million during any fiscal year; (f) cause the selection or replacement of our auditors; (g) enter into of any partnership, consortium, joint venture or other similar enterprise involving the payment, contribution, or assignment by the Company or to the Company of money or assets greater than $5 million; (h) amend or otherwise change our Articles of Incorporation or by-laws or equivalent organizational documents of the Company or any subsidiary in any manner that materially and adversely affects any rights of SPI; or (i) grant, issue or sell any equity securities (with certain limited exceptions). These veto rights provide SPI with significant influence over the Company’s operations and strategy. SPI may choose to exert its influence in a manner that is not in the best interests of our general shareholders.
Our China joint venture could be adversely affected by the laws and regulations of the Chinese government, our lack of decision-making authority and disputes between us and the Joint Venture.
The China market has a large inherent need for advanced energy storage and power electronics and is likely to become the world’s largest market for energy storage. To take advantage of this opportunity, in November 2011, we established a joint venture to develop, produce, sell, distribute and service advanced storage batteries and power electronics in China (the “Joint Venture”).
However, achieving the anticipated benefits of the Joint Venture is subject to a number of risks and uncertainties.
The Joint Venture has (1) an exclusive royalty-free license to manufacture and distribute our third generation ZBB EnerStore zinc bromide flow battery and any other zinc bromide flow battery product developed internally by us based on the V3 EnerStore, ranging from 50kWh – 500kWh module design, and ZBB EnerSection power and energy control center (up to 250KW) (the “Products”) in mainland China in the power supply management industry and (2) a non-exclusive royalty-free license to manufacture and distribute the Products in Hong Kong and Taiwan in the power supply management industry. Although the Joint Venture partners are contractually restricted from using our intellectual property outside of the Joint Venture, there is always a general risk associated with sharing intellectual property with third parties and the possibility that such information may be used and shared without our consent. Moreover, China laws that protect intellectual property rights are not as developed and favorable to the owner of such rights as are U.S. laws. If any of our intellectual property rights are used or shared without our approval in China, we may have difficulty in prosecuting our claim in an expeditious and effective manner. Difficulties or delays in enforcing our intellectual property rights could have a material adverse effect on our business and prospects.
13
As a general matter, there are substantial uncertainties regarding the interpretation and application of China laws and regulations, including, but not limited to, the laws and regulations governing the anticipated business of the Joint Venture and the protection of intellectual property rights. These laws and regulations are sometimes vague and may be subject to future changes, and their official interpretation and enforcement may involve substantial uncertainty. The effectiveness of newly enacted laws, regulations or amendments may be delayed, resulting in detrimental reliance by foreign investors. New laws and regulations that affect existing and proposed future businesses may also be applied retroactively. The unpredictability of the interpretation and application of existing and new China laws and regulations will pose additional challenges for us as we seek to develop and grow the Joint Venture’s business in China. Our failure to understand these laws or an unforeseen change in a law or the application thereof could have an adverse effect on the Joint Venture.
The success of the Joint Venture will depend in part on continued support of “new energy” initiatives by the government of China that includes requirements for products like ours. Should the government change its policies in an unfavorable manner the anticipated demand for the Joint Venture’s products in China may fail to materialize.
The Joint Venture may have economic, tax or other business interests or goals which are inconsistent with our business interests or goals, and may be in a position to take actions contrary to our policies or objectives. Disputes between us and the Joint Venture partners may result in litigation or arbitration that could be costly and divert the attention of our management and key personnel from focusing their time and effort on our day to day business. In addition, we may, in certain circumstances, be liable for the actions of the Joint Venture.
The Joint Venture is a new business in China. As with any new business, there will be many challenges facing the Joint Venture, including establishing successful manufacturing capabilities, developing a market for the Joint Venture’s products, obtaining requisite governmental approvals and permits, implementation of an untested business plan, and securing adequate funding for working capital and growth. Failure to overcome any of these or any other challenges facing the Joint Venture could result in its failure.
Business practices in Asia may entail greater risk and dependence upon the personal relationships of senior management than is common in North America, and therefore some of our agreements with other parties in China and South Korea could be difficult or impossible to enforce.
We are increasing our business activities in Asia. The business culture in parts of Asia is, in some respects, different from the business cultures in Western countries. Personal relationships among business principals of companies and business entities in Asia are very significant in their business cultures. In some cases, because so much reliance is based upon personal relationships, written contracts among businesses in Asia may be less detailed and specific than is commonly accepted for similar written agreements in Western countries. In some cases, material terms of an understanding are not contained in the written agreement but exist only as oral agreements. In other cases, the terms of transactions which may involve material amounts of money are not documented at all. In addition, in contrast to the Western business environment where a written agreement specifically defines the terms, rights and obligations of the parties in a legally-binding and enforceable manner, the parties to a written agreement in Asia may view that agreement more as a starting point for an ongoing business relationship which will evolve and undergo ongoing modification over time. As a result, any contractual arrangements we enter into with a counterparty in Asia may be more difficult to review, understand and/or enforce.
Our success depends on our ability to retain our managerial personnel and to attract additional personnel.
Our success depends largely on our ability to attract and retain managerial personnel. Competition for desirable personnel is intense, and there can be no assurance that we will be able to attract and retain the necessary staff. The loss of members of managerial staff could have a material adverse effect on our future operations and on successful development of products for our target markets. The failure to maintain management and to attract additional key personnel could materially adversely affect our business, financial condition and results of operations.
14
We market and sell, and plan to market and sell, our products in numerous international markets. If we are unable to manage our international operations effectively, our business, financial condition and results of operations could be adversely affected.
We market and sell, and plan to market and sell, our products in a number of foreign countries, including China, Australia, South Africa, Canada, European Union countries, the United Kingdom, Italy, Chile, Brazil, India, Mexico as well as Puerto Rico, various Caribbean island nations and various southeast Asia countries, and we are therefore subject to risks associated with having international operations. Risks inherent in international operations include, but are not limited to, the following:
|
·
|
changes in general economic and political conditions in the countries in which we operate;
|
|
·
|
unexpected adverse changes in foreign laws or regulatory requirements, including those with respect to renewable energy, environmental protection, permitting, export duties and quotas;
|
|
·
|
trade barriers such as export requirements, tariffs, taxes and other restrictions and expenses, which could increase the prices of our products and make us less competitive in some countries;
|
|
·
|
fluctuations in exchange rates may affect demand for our products and may adversely affect our profitability;
|
|
·
|
difficulty of, and costs relating to compliance with, the different commercial and legal requirements of the overseas markets in which we offer and sell our products;
|
|
·
|
inability to obtain, maintain or enforce intellectual property rights; and
|
|
·
|
difficulty in enforcing agreements in foreign legal systems.
|
Our business in foreign markets requires us to respond to rapid changes in market conditions in these countries. Our overall success as a global business depends, in part, on our ability to succeed in differing legal, regulatory, economic, social and political conditions. We may not be able to develop and implement policies and strategies that will be effective in each location where we do business, which in turn could adversely affect our business, financial condition and results of operations.
Our sales cycle is lengthy and variable, which makes it difficult for us to forecast revenue and other operating results.
The sales cycle for our products is lengthy, which makes it difficult for us to accurately forecast revenue in a given period, and may cause revenue and operating results to vary significantly from period to period. Some potential customers for our products typically need to commit significant time and resources to evaluate the technology used in our products and their decision to purchase our products may be further limited by budgetary constraints and numerous layers of internal review and approval, which are beyond our control. We spend substantial time and effort assisting potential customers in evaluating our products, including providing demonstrations and validation. Even after initial approval by appropriate decision makers, the negotiation and documentation processes for the actual adoption of our products can be lengthy. As a result of these factors, based on our experience to date, our sales cycle, the time from initial contact with a prospective customer to routine commercial utilization of our products, has varied and can sometimes be several months or longer, which has made it difficult for us to accurately project revenues and other operating results. We expect that sales of power purchase agreements we enter into will also be uneven from quarter to quarter due to the need to group such agreements together for sale as well as other factors. As a result, our financial results may fluctuate on a quarterly basis which may adversely affect the price of our common stock.
Our increased emphasis on larger and more complex system solutions and customer concentration may adversely affect our ability to accurately predict the timing of revenues and to meet short-term expectations of operating results.
Our increased emphasis on larger and more complex system solutions has increased the effort and time required by us to complete sales to customers. Further, a larger portion of our quarterly revenue is derived from relatively few large transactions with relatively few customers. Any delay in completing these large sales transactions or any reduction in the number of customers or large transactions, may result in significant adverse fluctuations in our quarterly revenue. Further, we use anticipated revenues to establish our operating budgets and a large portion of our expenses, particularly rent and salaries are fixed in the short term. As a result, any shortfall or delay in revenue could result in increased losses and would likely cause our operating results to be below public expectations. The occurrence of any of these events would likely materially adversely affect our results of operations and likely cause the market price of our common stock to decline.
We recently entered into our first power purchase agreement (“PPA”) which represents a new business for us. We have very limited experience in the PPA business, which is very complex, and there can be no assurance that we will be able to successfully develop such business.
We recently entered into our first power purchase agreement (“PPA”) which represents a new business for us. We plan to continue to develop the PPA portion of our business and given our limited experience and the complex nature of this business we may encounter difficulties in doing so. When we enter into a PPA we agree to provide electricity to our customer at a fixed rate for a fixed period of time (typically 20 years). To satisfy our obligations under the PPA we need to develop a system that includes power generation capability (typically PV), and an energy management system and may also include energy storage. The development and construction of these systems can require long periods of time and substantial initial capital investments, and there are significant risks related to the development of such systems, including potential technical difficulties and regulatory difficulties, including obtaining necessary permits. There can be no assurance that we will be able to overcome these risks as we develop our PPA business. In light of the long-term nature of PPAs and the significant capital requirements associated with them, we plan to sell them to third parties rather than hold them for their full terms. The sale of PPAs is a complex endeavor that is impacted by a variety of factors including interest rates, the availability of tax and other incentives, the perceived reliability and bankability of the system and other market forces beyond our control. Even if we are able to sell our PPAs, we may retain significant exposure following the sale due to our keeping an ownership interest or because we warranty the related system or otherwise retain maintenance responsibility. Our inability to sell our PPAs on acceptable terms, or at all, could have a material adverse effect on our financial condition and results of operations. We have very limited experience in the PPA business, and there can be no assurance that we will be able to successfully develop such business.
15
We expect to rely on third-party suppliers and contractors when developing and constructing systems for our PPA business.
We expect to source the components of systems deployed in our PPA business from a wide selection of third-party suppliers and engage third-party contractors for the construction of the systems. We expect to enter into contracts with our suppliers and contractors on a project-by-project basis rather than maintaining long-term contracts with our suppliers or contractors. Therefore, we expect to be exposed to price fluctuations with respect to the components sourced from our suppliers and the construction services procured from our contractors. Increases in the prices of system components, decreases in their availability, fluctuations in construction, labor and installation costs, or changes in the terms of our relationship with our suppliers and contractors may increase the cost of procuring equipment and engaging contractors and hence materially adversely affect our financial condition and results of operations.
Furthermore, the delivery of defective products or products or construction services by our suppliers or contractors which are otherwise not in compliance with contract specifications, or the late supply of products or construction services, may cause construction delays or solar power systems that fail to adhere to our quality and safety standards, which could have a material adverse effect on our business, results of operations, financial condition and cash flow.
Businesses and consumers might not adopt alternative energy solutions as a means for obtaining their electricity and power needs, and therefore our revenues may not increase, and we may be unable to achieve and then sustain profitability.
On-site distributed power generation solutions, such as fuel cell, photovoltaic and wind turbine systems, which utilize our energy storage systems, provide an alternative means for obtaining electricity and are relatively new methods of obtaining electrical power that businesses may not adopt at levels sufficient to grow this part of our business. Traditional electricity distribution is based on the regulated industry model whereby businesses and consumers obtain their electricity from a government regulated utility. For alternative methods of distributed power to succeed, businesses and consumers must adopt new purchasing practices and must be willing to rely upon less traditional means of purchasing electricity. We cannot assure you that businesses and consumers will choose to utilize on-site distributed power at levels sufficient to sustain our business in this area. The development of a mass market for our products may be impacted by many factors which are out of our control, including:
|
·
|
market acceptance of fuel cell, photovoltaic and wind turbine systems that incorporate our products;
|
|
·
|
the cost competitiveness of these systems;
|
|
·
|
regulatory requirements; and
|
|
·
|
the emergence of newer, more competitive technologies and products.
|
If a mass market fails to develop or develops more slowly than we anticipate, our business, financial condition and results of operations could be materially adversely affected.
16
Our business depends in part on the regulatory treatment of third-party owned solar energy systems.
Retail sales of electricity by non-utilities, such as us, face regulatory hurdles in some states and jurisdictions, including states and jurisdictions that we intend to enter where the laws and regulatory policies have not historically embraced competition to the service provided by the incumbent, vertically integrated electric utility. Some of the principal challenges pertain to whether non-customer owned systems qualify for the same levels of rebates or other non-tax incentives available for customer-owned solar energy systems, whether third-party owned systems are eligible at all for these incentives and whether third-party owned systems are eligible for net metering and the associated significant cost savings. Furthermore, in some states and utility territories third parties are limited in the way that they may deliver solar to their customers. In jurisdictions such as Arizona, Florida, Georgia, Kentucky, North Carolina and Utah and in Los Angeles, California, laws have been interpreted to prohibit the sale of electricity pursuant to our standard power purchase agreement, in some cases, leading residential solar energy system providers to use leases in lieu of power purchase agreements. Changes in law, reductions in, eliminations of or additional application requirements for, these benefits could reduce demand for our systems, adversely impact our access to capital and could cause us to increase the price we charge our customers for energy.
The success of our business depends on our ability to develop and protect our intellectual property rights, which could be expensive.
Our ability to compete effectively will depend, in part, on our ability to protect our proprietary technologies, systems designs and manufacturing processes. While we have attempted to safeguard and maintain our proprietary rights, there can be no assurance we have been or will be completely successful in doing so. We rely on patents, trademarks, and policies and procedures related to confidentiality to protect our intellectual property. However, most of our intellectual property is not covered by any patents or patent applications. Moreover, there can be no assurance that any of our pending patent applications will issue or, in the case of patents issued or to be issued, that the claims allowed are or will be sufficient to protect our technology or processes. Even if all of our patent applications are issued, our patents may be challenged or invalidated. Patent applications filed in foreign countries may be subject to laws, rules and procedures that are substantially different from those of the United States, and any resulting foreign patents may be difficult and expensive to enforce.
While we take steps to protect our proprietary rights to the extent possible, there can be no assurance that third parties will not know, discover or develop independently equivalent proprietary information or techniques, that they will not gain access to our trade secrets or disclose our trade secrets to the public. Therefore, we cannot guarantee that we can maintain and protect unpatented proprietary information and trade secrets. Misappropriation of our intellectual property could have an adverse effect on our competitive position and may cause us to incur substantial litigation costs.
We may be subject to claims that we infringe the intellectual property rights of others, and unfavorable outcomes could harm our business.
Our future operations may be subject to claims, and potential litigation, arising from our alleged infringement of patents, trade secrets or copyrights owned by other third parties. We intend to fully comply with the law in avoiding such infringements. However, we may become subject to claims of infringement, including such claims or litigation initiated by existing, better-funded competitors. We could also become involved in disputes regarding the ownership of intellectual property rights that relate to our technologies. These disputes could arise out of collaboration relationships, strategic partnerships or other relationships. Any such litigation could be expensive, take significant time, and could divert management’s attention from other business concerns. Our failure to prevail in any such legal proceedings, or even the mere occurrence of such legal proceedings, could substantially affect our ability to meet our expenses and continue operations.
17
We may engage in acquisitions that could disrupt our business, cause dilution to our stockholders and reduce our financial resources.
In the future, we may enter into transactions to acquire other businesses, products or technologies. If we do identify suitable candidates, we may not be able to make such acquisitions on favorable terms or at all. Any acquisitions we make may not strengthen our competitive position, and these transactions may be viewed negatively by customers or investors. We may decide to incur debt in connection with an acquisition or issue our common stock or other securities to the stockholders of the acquired company, which would reduce the percentage ownership of our existing stockholders. We could incur losses resulting from undiscovered liabilities of the acquired business that are not covered by the indemnification we may obtain from the seller. In addition, we may not be able to successfully integrate the acquired personnel, technologies and operations into our existing business in an effective, timely and non-disruptive manner. Acquisitions may also divert management from day-to-day responsibilities, increase our expenses and reduce our cash available for operations and other uses. We cannot predict the number, timing or size of future acquisitions or the effect that any such transactions might have on our operating results.
We have never paid cash dividends and do not intend to do so.
We have never declared or paid cash dividends on our common stock. We currently plan to retain any earnings to finance the growth of our business rather than to pay cash dividends. Payments of any cash dividends in the future will depend on our financial condition, results of operations and capital requirements, as well as other factors deemed relevant by our board of directors. Additionally, so long as any shares of our preferred stock our outstanding, we are prohibited from paying dividends on our common stock.
18
Item 1B. UNRESOLVED STAFF COMMENTS
Not applicable.
Item 2. PROPERTIES
Wisconsin U.S.A. Properties
The Company’s headquarters is located at N93 W14475 Whittaker Way, Menomonee Falls, Wisconsin. The Company owns this facility which has approximately 72,000 square feet of space.
Bibra Lake, Western Australia (Leasehold)
In 2001 our Australian subsidiary moved into a new, leased, self-contained research and development facility in Bibra Lake, Western Australia after previously occupying leased laboratory and workshop facilities. This facility also provides the engineering support for Australian and Southeast Asia sales as well as a marketing base for the Company in this region. The current rent is $81,376 per year (A$101,568), subject to annual CPI adjustments expiring on October 31, 2016.
Item 3. LEGAL PROCEEDINGS
We are not currently a party to any pending legal proceedings that we believe will have a material adverse effect on our business, financial condition or results of operations. We may, however, be subject to various claims and legal actions arising from the ordinary course of business from time to time.
Item 4. MINE SAFETY DISCLOSURES
Not applicable.
19
Item 5. MARKET FOR REGISTRANT’S COMMON EQUITY, RELATED STOCKHOLDER MATTERS AND ISSUER PURCHASES OF EQUITY SECURITIES
The Common Stock of the Company has historically traded on the NYSE MKT under the name ZBB Energy Corporation (Symbol: ZBB) since June 18, 2007. As of August 17, 2015 the Common Stock of the Company is traded on the NYSE MKT under the name EnSync, Inc. (Symbol: ESNC). The following table sets forth for the periods indicated the range of high and low reported sales price per share of our common stock as reported on NYSE MKT. The share and per share information in this Form 10-K, including the following table, reflect a one-for-five reverse stock split that occurred on October 31, 2013 on a retroactive basis.
High ($)
|
Low ($)
|
|||||||
2015
|
||||||||
Fourth Quarter
|
1.25 | 0.56 | ||||||
Third Quarter
|
0.84 | 0.48 | ||||||
Second Quarter
|
0.93 | 0.41 | ||||||
First Quarter
|
1.85 | 0.54 | ||||||
2014
|
||||||||
Fourth Quarter
|
2.13 | 1.10 | ||||||
Third Quarter
|
4.75 | 0.71 | ||||||
Second Quarter
|
1.17 | 0.40 | ||||||
First Quarter
|
1.35 | 0.90 |
As of September 28, 2015, the Company had 766 shareholders of record. These shareholders of record do not include non-registered stockholders whose shares are held in “nominee” or “street name.”
We have not declared or paid cash dividends on our common stock and do not anticipate paying any cash dividends in the foreseeable future.
Securities authorized for issuance under equity compensation plans is set forth in the Company’s Definitive Proxy Statement relating to the Company’s 2015 annual meeting of shareholders to be held on November 17, 2015 and is incorporated herein by reference.
Item 6. SELECTED FINANCIAL DATA
Not applicable.
Item 7. MANAGEMENT’S DISCUSSION AND ANALYSIS OF FINANCIAL CONDITION AND RESULTS OF OPERATIONS
The following discussion and analysis should be read in conjunction with our Consolidated Financial Statements and related Notes included elsewhere in this Annual Report on Form 10-K. Some of the information contained in this Management’s Discussion and Analysis of Financial Condition and Results of Operations and elsewhere in this report includes forward-looking statements based on our current management’s expectations. There can be no assurance that actual results, outcomes or business conditions will not differ materially from those projected or suggested in such forward-looking statements as a result of various factors, including, the risks and uncertainties discussed in the Risk Factors section of this Annual Report on Form 10-K.
OVERVIEW
EnSync, Inc. and its subsidiaries (“EnSync,” “we,” “us,” “our,” or the “Company”) develop, license, and manufacture innovative energy management systems solutions serving the commercial and industrial (“C&I”) building, utility, and off-grid markets. Incorporated in 1998, EnSync is headquartered in Menomonee Falls, Wisconsin, USA with offices in San Francisco, California, Honolulu, Hawaii, Shanghai, China, and Perth, Western Australia. In August 2015, we changed our corporate name from ZBB Energy Corporation to EnSync, Inc., and we regularly use the name EnSync Energy Systems for marketing and branding purposes.
EnSync develops and commercializes application solutions for advanced energy management systems critical to the transition from a “coal-centric economy” to one reliant on renewable energy sources. EnSync synchronizes conventional utility, distributed generation and storage assets to seamlessly ensure the least expensive and most reliable electricity available, thus enabling the future of energy networks. These advanced systems directly connect wind and solar equipment to the grid and other systems that can form various levels of micro-grids as well as power quality regulation solutions. EnSync brings vital power control and energy storage solutions to problems caused by incorporation of increasingly pervasive renewable energy generating assets that are part of the grid power transmission and distribution network used in commercial, industrial, and multi-tenant buildings. The Company also develops and commercializes energy management systems for off-grid applications such as island or remote power.
The consolidated financial statements include the accounts of the Company and those of its wholly-owned subsidiaries ZBB Energy Pty Ltd. (formerly known as ZBB Technologies, Ltd.) located in Perth, Australia, Century West PNL LLC, and its sixty percent owned subsidiary ZBB PowerSav Holdings Limited located in Hong Kong which was formed in connection with the Company’s investment in a China joint venture.
20
China Joint Venture
Anhui Meineng Store Energy Co., Ltd. (“Meineng Energy”) was established in late 2011 to develop, produce, sell, distribute and service advanced storage batteries and power electronics in China. Meineng Energy assembles and manufactures certain of the Company’s products for sale in the power management industry on an exclusive basis in mainland China and on a non-exclusive basis in Hong Kong and Taiwan.
Our investment in Meineng Energy was made through ZBB PowerSav Holdings Limited (“Holdco”), a limited liability Hong Kong holding company, formed with PowerSav New Energy Holdings Limited. We own 60% of Holdco’s equity interests. We have the right to appoint a majority of the members of the Board of Directors of Holdco and Holdco has the right to appoint a majority of the members of the Board of Directors of Meineng Energy. Our indirect interest in Meineng equals approximately 30%.
Bradley L. Hansen, our President and Chief Executive Officer has served as the Chief Executive Officer of Meineng Energy since December 2011. Mr. Hansen owns an indirect 6% equity interest in Meineng Energy.
Pursuant to a management services agreement, Holdco will provide certain management services to Meineng Energy in exchange for a management services fee equal to five percent of Meineng Energy’s net sales for the subsequent three years, provided the payment of such fees will terminate upon Meineng Energy completing an initial public offering on a nationally recognized securities exchange. To date, no management service fee revenues have been recognized by Holdco.
Lotte Chemical Corporation
In April 2011, we entered into a Collaboration Agreement (the “Collaboration Agreement”) with Lotte Chemical Corporation (“Lotte”), pursuant to which we collaborated with Lotte on the technical development of our third generation zinc bromide flow battery module (the “Version 3 Battery Module”). Lotte received a fully paid-up, exclusive and royalty-free license to sell and manufacture the Version 3 Battery Module in South Korea and a non-exclusive royalty-bearing license to sell the Version 3 Battery Module in Japan, Thailand, Taiwan, Malaysia, Vietnam and Singapore.
In December 2013, we entered into a Research and Development Agreement (the “R&D Agreement”) with Lotte pursuant to which we agreed to develop and provide to Lotte a 500kWh zinc bromide flow battery system, including a zinc bromide chemical flow battery module and related software (the “Product”), on the terms and conditions set forth in the R&D Agreement (the “Project”). The Project is scheduled to continue until December 16, 2015, unless extended by the mutual agreement of the Company and Lotte. Subject to the satisfaction of certain specified milestones, Lotte is required to make payments to us under the R&D Agreement totaling $3,000,000 over the term of the Project.
Additionally, in December 2013, we entered into an Amended License Agreement with Lotte (the “Amended License Agreement”). Pursuant to the Amended License Agreement, we granted to Lotte, (1) an exclusive and royalty-free limited license in South Korea to use the Company’s zinc bromide flow battery module, Zinc Bromide flow battery stack and the technical information and know how related to the intellectual property arising from the Project (collectively, the “Technology”) to manufacture or sell a zinc bromide flow battery (the “Lotte Product”) in South Korea and (2) a non-exclusive (a) royalty-free limited license for Lotte and its affiliates to use the Technology internally in all locations other than China and South Korea to manufacture the Lotte Product and (b) royalty-bearing limited license to sell the Lotte Product in all locations other than China, the United States and South Korea. Lotte is required to pay us a total license fee of $3,000,000 under the Amended License Agreement plus up to an additional $1,000,000 if certain specific milestones are successfully achieved. In addition, Lotte is required to make ongoing royalty payments to the Company equal to a single digit percentage of Lotte’s sales of the Lotte Product outside of South Korea until December 31, 2019. The original license fees were subject to a 16.5% non-refundable Korea withholding tax.
Solar Power, Inc.
In July 2015, we entered into a Securities Purchase Agreement (the “Purchase Agreement”) with Solar Power, Inc., a California corporation (“SPI”) pursuant to which we sold to SPI for an aggregate purchase price of $33,390,000 a total of (i) 8,000,000 shares (the “Purchased Common Shares”) of common stock and (ii) 28,048 shares (the “Purchased Preferred Shares”) of Series C Convertible Preferred Stock which are convertible, subject to the completion of projects under our supply agreement with SPI (as described below), into a total of up to 42,000,600 shares of Common Stock. The aggregate purchase price for the Purchased Common Shares was based on a purchase price per share of $0.6678. The aggregate purchase price for the Purchased Preferred Shares was determined based on price of $0.6678 per common share equivalent. Pursuant to the purchase agreement, SPI was also issued a warrant to purchase 50,000,000 shares of Common Stock for an aggregate purchase price of $36,729,000 (the “Warrant”).
21
We also entered into a supply agreement with SPI pursuant to which we will sell and SPI will purchase certain products and services offered by us from time to time, including certain energy management system solutions for solar projects (the “Supply Agreement”).
The Purchased Preferred Shares were sold for $1,000 per share and are convertible at a conversion price of $0.6678 provided that (A) the first one-fourth (the “Series C-1 Preferred Stock”) of the Purchased Preferred Shares only become convertible upon the completion of five megawatts worth of solar projects in accordance with the Supply Agreement (the “Projects”), (B) the second one-fourth (the “Series C-2 Preferred Stock”) only become convertible upon the completion of 15 megawatts worth of projects, (C) the third one-fourth (the “Series C-3 Preferred Stock”) only become convertible upon the completion of 25 megawatts worth of projects, and (D) the last one-fourth (the “Series C-4 Preferred Stock”) only become convertible upon the completion of 40 megawatts worth of projects. The Warrant represents the right to acquire 50,000,000 shares of Common Stock at an exercise price equal to $0.7346. The Warrant only becomes exercisable upon the completion of 40 megawatts worth of Projects.
We also entered into a form of governance agreement with SPI (the “Governance Agreement”) pursuant to which SPI is entitled to nominate one director to our board of directors for so long as SPI holds at least 10,000 Purchased Preferred Shares or 25 million of Common Stock or Common Stock equivalents (the “Requisite Shares”). Additionally, for so long as the Purchaser holds the Requisite Shares (1) following the time at which the Series C-2 Preferred Stock shall have become convertible in full, the Purchaser shall be entitled to nominate a total of two Directors to the Board and (2) following the time at which the Series C-3 Preferred Stock shall have convertible in full, the Purchaser shall be entitled to nominate a total of three directors.
NEW ACCOUNTING PRONOUNCEMENTS
Refer to Note 1 of the Notes to Consolidated Financial Statements for a discussion of recently issued accounting pronouncements.
CRITICAL ACCOUNTING POLICIES AND ESTIMATES
The preparation of our financial statements conforms to accounting principles generally accepted in the United States of America, which requires management, in applying our accounting policies, to make estimates and assumptions that have an important impact on our reported amounts of assets, liabilities, revenue, expenses and related disclosures at the date of our financial statements. On an on-going basis, management evaluates its estimates including those related to revenue recognition, inventory valuations, warranty obligations, and income taxes. Management bases its estimates and judgments on historical experience and on various other factors that are believed to be reasonable under the circumstances, the results of which form the basis for making judgments about the carrying values of assets and liabilities that are not readily apparent from other sources. Actual results may differ from management’s estimates.
CRITICAL ACCOUNTING ESTIMATES
Revenue Recognition
Application of the accounting principles related to the measurement and recognition of revenue requires the Company to make judgments and estimates. Even for the same product, the Company has to interpret contract terms to determine the appropriate accounting treatments. When services, installation and training, etc. are rendered with product sales, the Company determines whether the deliverables should be treated as separate units of accounting. When there are multiple transactions with the same customer, significant judgments are made to determine whether separate contracts are considered as part of one arrangement according to the contract’s terms and conditions. When the installed equipment is accepted by the customer in different periods, the Company determines whether the completed project is able to be used by the customer, whether the receivable is collectible and whether revenue is recognized in stages.
Revenue recognition is also impacted by various factors, including the credit-worthiness of the customer. Estimates of these factors are evaluated periodically to assess the adequacy of the estimates. If the estimates were changed, revenue would be impacted.
22
Excess and Obsolete Inventory
We determine the amount of inventory that is excess and obsolete using estimates of future demand for individual components of raw materials and finished goods.
To determine excess and obsolete inventory, we compare listings of existing piece parts and finished goods to future product demand and usage requirements. We record a full valuation allowance for inventory quantities on hand in excess of two year’s expected usage.
We believe our accounting estimate related to excess and obsolete inventory is a critical accounting estimate because it requires us to make assumptions about future sales volumes and product mix, which can be highly uncertain. Changes in these estimates can have a material effect on our financial statements.
Accrued Expenses
Accrued expenses consist of the Company’s present obligations for various expenses incurred during the period and include a reserve for estimated contract losses, other accrued expenses, and warranty obligations. Included in accrued expenses as of June 30, 2015 is a remaining reserve of approximately $685,000 for a $1.8 million product upgrade initiative established in the fourth quarter of fiscal 2014.
Subsequent to commercialization, installation and commissioning of units in the field, the Company garnered meaningful insights that resulted in system design modifications and other general upgrades, which improved the performance, efficiency, and reliability of its systems. In the interest of enhancing customer satisfaction, the Company launched the product upgrade initiative to implement these improvements at certain locations of its installed base through fiscal year 2016.
Warranty Provision
The Company’s products are generally covered by a warranty for 12 or 18 months. The Company accrues for warranty costs as part of costs of sales based on associated material costs, technical labor costs, and associated overheads.
If the Company experiences an increase in warranty claims compared with historical experience, or if the cost of servicing warranty claims is greater than expected, the Company’s gross margin could be adversely affected.
Stock Based Compensation
The Company’s Board of Directors approves grants of stock options to employees to purchase our common stock. Stock compensation expense is recorded based upon the estimated fair value of the stock option at the date of grant. The accounting estimate related to stock-based compensation is considered a critical accounting estimate because estimates are made in calculating compensation expense including expected option lives, forfeiture rates and expected volatility. Expected option lives and forfeiture rates may be different from estimates and may result in potential future adjustments, which would impact the amount of stock-based compensation expense recorded in a particular period.
RESULTS OF OPERATIONS
Year ended June 30, 2015 compared with the year ended June 30, 2014
Revenue:
Our revenues for the years ended June 30, 2015 and June 30, 2014 were $1,763,510 and $7,851,607, respectively. The decrease of $6,088,097 in the year ended June 30, 2015 was the result of a $2,534,445 decrease in product sales revenues, $533,652 decrease in engineering and development revenue, and a $3,000,000 decrease in licensing revenue as compared to the year ended June 30, 2014.
23
Costs and Expenses:
Total costs and expenses for the years ended June 30, 2015 and June 30, 2014 were $15,320,684 and $16,648,862, respectively. This decrease of $1,328,178 in the year ended June 30, 2015 was due to the following factors:
·
|
$2,053,619 decrease in costs of product sales principally due to decreased product sales;
|
·
|
$61,025 increase in cost of engineering and development due to costs incurred in relation to the Lotte research and development agreement for the year ended June 30, 2015 compared to year ended June 30, 2014;
|
·
|
$1,175,238 increase in advanced engineering and development expenses due to $720,000 of higher salaries, related payroll taxes, and benefits resulting from increased headcount year over year, $497,000 paid for contract employees, and $469,000 of additional spending on project materials. This activity was partially offset by a $315,000 decrease in advanced engineering and development activity at the Company’s Australia location;
|
·
|
$113,035 decrease in selling, general, and administrative expenses was due to decreases of $539,000 of activity completed on the product upgrade initiative that was reserved for during fiscal year 2014, $495,000 in Korean withholding tax on Lotte license revenues and $89,000 in legal fees partially offset by increases of $352,000 in wages and benefits related to increased headcount, $301,000 in recruitment fees, $178,000 of other miscellaneous general expenses, $130,000 in travel expenses and $76,000 in advertising expense; and,
|
·
|
$397,787 decrease in depreciation and amortization expense as a result of the full recognition of amortization expense of the Company’s intangible assets during the prior fiscal year.
|
Other Income (Expense):
Total other income (expense) for the year ended June 30, 2015 increased by $1,457,566 to income of $659,110 from an expense of $798,456 for the year ended June 30, 2014 primarily as a result of the $1,257,407 gain on investment in investee company resulting from a third-party capital investment transaction with the investee company and a $162,763 decrease in equity in loss of investee company.
On August 12, 2014, Meineng Energy received a cash investment of 20,000,000 RMB (about $3.2 million) from a third party for a post-closing valuation of $42 million. During the year ended June 30, 2015, we recognized a $1,257,407 gain on the carrying value of our investment in Meineng Energy. $481,870 of this gain is attributable to the noncontrolling interest, which provided a net gain of $775,537 to the Company.
Income Taxes (Benefit):
The benefit for income taxes during the year ended June 30, 2015 increased by $4,044 to $86,455 from $82,411 for the year ended June 30, 2014. The current year benefit for income taxes was generated by a release of a reserve for an uncertain tax position related to a refundable tax credit for research and development previously received related to qualified expenditures we incurred during the year ended June 30, 2010. The tax examination period related to the 2010 credit expired at the end of the current fiscal year. The Company did not qualify for this credit during the year ended June 30, 2015.
Net Loss:
Our net loss for the year ended June 30, 2015 increased by $4,030,389 to $12,885,808 from the $8,855,418 net loss for the year ended June 30, 2014. This increase in loss was primarily the result of decreased revenues. This activity was partially offset by the recognized gain on investment in Meineng Energy as described in “Other Income (Expense)” above.
Liquidity and Capital Resources
Since our inception, our research, advanced engineering and development, and operations have been primarily financed through debt and equity financings, and engineering, government and other research and development contracts. Total capital stock and paid in capital as of June 30, 2015 was $118,204,570 compared with June 30, 2014 total capital stock of $103,251,304. We had a cumulative deficit of $102,674,048 as of June 30, 2015 compared to a cumulative deficit of $89,788,242 as of June 30, 2014. At June 30, 2015 we had net working capital of $9,352,291 compared to June 30, 2014 net working capital of $8,723,032. Our shareholders’ equity as of June 30, 2015 and June 30, 2014, exclusive of noncontrolling interests, was $13,941,036 and $11,863,187, respectively.
On September 26, 2013, the Company entered into a Securities Purchase Agreement with certain investors providing for the sale of 3,000 shares of Series B Convertible Preferred Stock (the “Preferred Stock”). Shares of Preferred Stock were sold for $1,000 per share (the “Stated Value”) and accrue dividends on the Stated Value at an annual rate of 10%. At June 30, 2015 the Preferred Stock was convertible into a total of 3,221,964 shares of common stock of the Company (“Common Stock”) at a conversion price equal to $0.95. Upon any liquidation, dissolution or winding up of the Company, holders of Preferred Stock are entitled to receive out of the assets of the Company an amount equal to two times the Stated Value, plus any accrued and unpaid dividends thereon. The net proceeds to the Company, after deducting $96,967 of offering costs, were $2,909,873. At June 30, 2015 the liquidation preference of the Preferred Stock was $5,635,866.
On March 19, 2014, the Company completed an underwritten public offering of its common stock at a price to the public of $2.25 per share. The Company sold a total of 6,325,000 shares of its common stock in the offering for aggregate proceeds of approximately $14.2 million. The Company received approximately $13.0 million of net proceeds from the offering, after deducting the underwriting discount and expenses.
24
On August 27, 2014, we completed an underwritten public offering of our common stock at a price to the public of $1.12 per share. We sold a total of 13,248,000 shares of our common stock in the offering for aggregate proceeds of approximately $14.8 million. We received approximately $13.7 million of net proceeds from the offering, after deducting the underwriting discount and expenses.
On July 13, 2015, we entered into a Securities Purchase Agreement (the “Purchase Agreement”) with Solar Power, Inc., a California corporation (“SPI”) pursuant to which we sold to SPI for an aggregate purchase price of $33,390,000 a total of (i) 8,000,000 shares (the “Purchased Common Shares”) of common stock and (ii) 28,048 shares (the “Purchased Preferred Shares”) of Series C Convertible Preferred Stock. The aggregate purchase price for the Purchased Common Shares was based on a purchase price per shares of $0.6678 and the aggregate purchase price for the Purchased Preferred Shares was determined based on price of $0.6678 per common share equivalent. Pursuant to the purchase agreement, SPI was also issued a warrant to purchase 50,000,000 shares of Common Stock for an aggregate purchase price of $36,729,000 (the “Warrant”).
At June 30, 2015, our principal sources of liquidity were our cash and cash equivalents which totaled $10,757,461, accounts receivable of $113,093, and expected collections under the Lotte R&D Agreement.
We believe that cash and cash equivalents on hand, expected collections on the Lotte R&D Agreement, the July 13, 2015 financing from SPI, and other potential sources of cash, will be sufficient to fund our current operations through the fourth quarter of fiscal year 2017. However, unless we are able to increase our revenues and achieve profitability we will likely require additional investment capital thereafter to fund our operations.
If we are unable to obtain additional required funding, we may not be able to:
|
·
|
remain in operation;
|
|
·
|
execute our growth plan;
|
|
·
|
take advantage of future opportunities; or
|
|
·
|
respond to customers and competition.
|
Operating Activities
Our operating activities used net cash of $11,167,097 for the year ended June 30, 2015. Cash used in operations resulted from a net loss of $12,811,610, which was decreased by $1,136,924 in non-cash adjustments and by $507,589 in net changes to working capital. Non-cash adjustments included a gain on investment in investee company of $1,257,407, $1,263,529 of stock compensation expense, $644,790 of depreciation expense, and $495,119 of equity in loss of investee company. Net decreases in working capital were primarily due to decreases in accounts receivable of $937,931, $154,853 in inventory, $91,191 in refundable income taxes, and $1,473,945 in accrued expenses, offset by increases in prepaids and other current assets of $145,723, $467,102 in accounts payable, $436,010 in customer deposits, and accrued compensation and benefits of $40,170.
Investing Activities
Our investing activities used net cash of $567,791 for the year ended June 30, 2015, primarily for a new note receivable in the amount of $150,000 and $427,499 for purchases of property and equipment.
Financing Activities
Our financing activities provided net cash of $12,139,606 for the year ended June 30, 2015. Net cash provided by financing activities was comprised principally of $14,837,760 in proceeds from the issuance of common stock, less common stock issuance costs of $1,148,023. During the year ended June 30, 2015 we made repayments of $1,018,062 of principal on bank loans and notes payable and paid $545,825 in financing costs related to the Solar Power, Inc. Securities Purchase agreement that closed on July 13, 2015.
Off-Balance Sheet Arrangements
We had no off-balance sheet arrangements as of June 30, 2015.
Item 7A. QUANTITATIVE AND QUALITATIVE DISCLOSURES ABOUT MARKET RISK
Not applicable.
25
Item 8. FINANCIAL STATEMENTS AND SUPPLEMENTARY DATA
INDEX TO FINANCIAL STATEMENTS
ENSYNC, INC.
TABLE OF CONTENTS
Page
|
||||
Report of Independent Registered Public Accounting Firm
|
27 | |||
Consolidated Balance Sheets as of June 30, 2015 and 2014
|
28 | |||
Consolidated Statements of Operations for the Years ended June 30, 2015 and 2014
|
29 | |||
Consolidated Statements of Comprehensive Loss for the Years ended June 30, 2015 and 2014
|
30 | |||
Consolidated Statements of Changes in Equity for the Years ended June 30, 2015 and 2014
|
31 | |||
Consolidated Statements of Cash Flows for the Years ended June 30, 2015 and 2014
|
32 | |||
Notes to Consolidated Financial Statements
|
33 |
26
REPORT OF INDEPENDENT REGISTERD PUBLIC ACCOUNTING FIRM
To the Shareholders, Audit Committee and Board of Directors
EnSync, Inc. Menomonee Falls, WI
We have audited the accompanying consolidated balance sheets of EnSync, Inc., (the Company) as of June 30, 2015 and 2014, and the related consolidated statements of operations, comprehensive loss, changes in equity and cash flows for the years then ended. These consolidated financial statements are the responsibility of the Company's management. Our responsibility is to express an opinion on these consolidated financial statements based on our audits.
We conducted our audits in accordance with the standards of the Public Company Accounting Oversight Board (United States). Those standards require that we plan and perform the audit to obtain reasonable assurance about whether the consolidated financial statements are free of material misstatement. The Company is not required to have, nor were we engaged to perform, an audit of its internal control over financial reporting. Our audits included consideration of its internal control over financial reporting as a basis for designing audit procedures that are appropriate in the circumstances, but not for the purpose of expressing an opinion on the effectiveness of the company’s internal control over financial reporting. Accordingly, we express no such opinion. An audit includes examining, on a test basis, evidence supporting the amounts and disclosures in the consolidated financial statements. An audit also includes assessing the accounting principles used and significant estimates made by management as well as evaluating the overall consolidated financial statement presentation. We believe that our audits provide a reasonable basis for our opinion.
In our opinion, the consolidated financial statements referred to above present fairly, in all material respects, the financial position of EnSync, Inc., as of June 30, 2015 and 2014 and the results of its operations and cash flows for the years then ended, in conformity with U.S. generally accepted accounting principles.
/s/ Baker Tilly Virchow Krause, LLP
Milwaukee, Wisconsin
September 28, 2015
27
EnSync, Inc.
|
||||||||
Consolidated Balance Sheets
|
||||||||
June 30, 2015
|
June 30, 2014
|
|||||||
Assets
|
||||||||
Current assets:
|
||||||||
Cash and cash equivalents
|
$ | 10,757,461 | $ | 10,360,721 | ||||
Restricted cash on deposit
|
60,193 | 69,901 | ||||||
Accounts receivable, net
|
113,093 | 1,051,024 | ||||||
Inventories, net
|
1,198,117 | 1,352,970 | ||||||
Prepaid expenses and other current assets
|
441,537 | 295,814 | ||||||
Deferred financing costs
|
545,825 | - | ||||||
Refundable income tax credit
|
- | 91,191 | ||||||
Note receivable
|
159,107 | - | ||||||
Total current assets
|
13,275,333 | 13,221,621 | ||||||
Long-term assets:
|
||||||||
Property, plant and equipment, net
|
4,164,912 | 4,382,203 | ||||||
Investment in investee company
|
2,408,528 | 1,646,240 | ||||||
Goodwill
|
803,079 | 803,079 | ||||||
Total assets
|
$ | 20,651,852 | $ | 20,053,143 | ||||
Liabilities and Equity
|
||||||||
Current liabilities:
|
||||||||
Current maturities of bank loans and notes payable
|
$ | 324,626 | $ | 351,142 | ||||
Accounts payable
|
1,056,744 | 589,642 | ||||||
Accrued expenses
|
1,129,166 | 2,621,479 | ||||||
Customer deposits
|
1,177,155 | 741,145 | ||||||
Accrued compensation and benefits
|
235,351 | 195,181 | ||||||
Total current liabilities
|
3,923,042 | 4,498,589 | ||||||
Long-term liabilities:
|
||||||||
Bank loans and notes payable, net of current maturities
|
1,053,581 | 2,045,127 | ||||||
Total liabilities
|
4,976,623 | 6,543,716 | ||||||
Commitments and contingencies (Note 13)
|
||||||||
Equity
|
||||||||
Series B redeemable convertible preferred stock ($0.01 par value,
|
||||||||
$1,000 face value) 3,000 shares authorized and issued, 2,575 shares outstanding, preference in liquidation of $5,635,866 and $5,347,994 as of June 30, 2015 and June 30, 2014, respectively
|
26 | 26 | ||||||
Common stock ($0.01 par value); 150,000,000 authorized,
|
||||||||
39,129,334 and 25,651,389 shares issued and outstanding as of June 30, 2015 and June 30, 2014, respectively
|
1,099,608 | 964,828 | ||||||
Additional paid-in capital
|
117,104,936 | 102,286,450 | ||||||
Accumulated deficit
|
(102,674,049 | ) | (89,788,242 | ) | ||||
Accumulated other comprehensive loss
|
(1,589,486 | ) | (1,599,875 | ) | ||||
Total EnSync, Inc. equity
|
13,941,035 | 11,863,187 | ||||||
Noncontrolling interest
|
1,734,194 | 1,646,240 | ||||||
Total equity
|
15,675,229 | 13,509,427 | ||||||
Total liabilities and equity
|
$ | 20,651,852 | $ | 20,053,143 |
See accompanying notes to consolidated financial statements.
28
EnSync, Inc.
|
||||||||
Consolidated Statements of Operations
|
||||||||
Year ended June 30,
|
||||||||
2015
|
2014
|
|||||||
Revenues
|
||||||||
Product sales
|
$ | 992,162 | $ | 3,526,607 | ||||
Engineering and development
|
771,348 | 1,325,000 | ||||||
License
|
- | 3,000,000 | ||||||
Total Revenues
|
1,763,510 | 7,851,607 | ||||||
Costs and Expenses
|
||||||||
Cost of product sales
|
841,928 | 2,895,547 | ||||||
Cost of engineering and development
|
267,127 | 206,102 | ||||||
Advanced engineering and development
|
6,420,191 | 5,244,953 | ||||||
Selling, general, and administrative
|
7,146,649 | 7,259,683 | ||||||
Depreciation and amortization
|
644,790 | 1,042,577 | ||||||
Total Costs and Expenses
|
15,320,685 | 16,648,862 | ||||||
Loss from Operations
|
(13,557,175 | ) | (8,797,255 | ) | ||||
Other Income (Expense)
|
||||||||
Equity in loss of investee company
|
(495,119 | ) | (657,882 | ) | ||||
Gain on investment in investee company
|
1,257,407 | - | ||||||
Interest income
|
25,108 | 5,635 | ||||||
Interest expense
|
(128,009 | ) | (147,105 | ) | ||||
Other income (expense)
|
(277 | ) | 896 | |||||
Total Other Income (Expense)
|
659,110 | (798,456 | ) | |||||
Loss before benefit for Income Taxes
|
(12,898,065 | ) | (9,595,711 | ) | ||||
Benefit for Income Taxes
|
(86,455 | ) | (82,411 | ) | ||||
Net loss
|
(12,811,610 | ) | (9,513,300 | ) | ||||
Net loss attributable to noncontrolling interest
|
407,672 | 657,882 | ||||||
Gain attributable to noncontrolling interest
|
(481,870 | ) | - | |||||
Net Income (Loss) Attributable to EnSync, Inc.
|
(12,885,808 | ) | (8,855,418 | ) | ||||
Preferred Stock Dividend
|
(266,356 | ) | (222,009 | ) | ||||
Net Loss Attributable to Common Shareholders
|
$ | (13,152,164 | ) | $ | (9,077,427 | ) | ||
Net Loss per share
|
||||||||
Basic and diluted
|
$ | (0.36 | ) | $ | (0.46 | ) | ||
Weighted average shares-basic and diluted
|
36,944,116 | 19,853,579 |
See accompanying notes to consolidated financial statements.
29
EnSync, Inc.
|
||||||||
Consolidated Statements of Comprehensive Loss
|
||||||||
Year ended June 30,
|
||||||||
2015
|
2014
|
|||||||
Net loss
|
$ | (12,811,610 | ) | $ | (9,513,300 | ) | ||
Foreign exchange translation adjustments
|
10,389 | (5,457 | ) | |||||
Comprehensive loss
|
(12,801,221 | ) | (9,518,757 | ) | ||||
Net (income) loss attributable to noncontrolling interest
|
(74,198 | ) | 657,882 | |||||
Comprehensive Income (Loss) Attributable to EnSync, Inc.
|
$ | (12,875,419 | ) | $ | (8,860,875 | ) |
See accompanying notes to consolidated financial statements.
30
EnSync, Inc.
|
||||||||||||||||||||||||||||||||
Series B Preferred Stock
|
Common Stock
|
Additional
Paid-in Capital
|
Accumulated
Deficit
|
Accumulated
Other
Comprehensive
Income (Loss)
|
Noncontrolling
Interest
|
|||||||||||||||||||||||||||
Shares
|
Amount
|
Shares
|
Amount
|
|||||||||||||||||||||||||||||
Balance: June 30, 2013
|
- | $ | - | 17,707,431 | $ | 885,389 | $ | 85,464,055 | $ | (80,932,823 | ) | $ | (1,594,418 | ) | $ | 2,304,122 | ||||||||||||||||
Net loss
|
(8,855,418 | ) | (657,882 | ) | ||||||||||||||||||||||||||||
Net currency translation adjustment
|
(5,457 | ) | ||||||||||||||||||||||||||||||
Issuance of common stock, net of
costs and underwriting fees
|
6,325,000 | 63,250 | 12,973,214 | |||||||||||||||||||||||||||||
Stock-based compensation
|
245,570 | 2,456 | 959,905 | |||||||||||||||||||||||||||||
Issuance of preferred stock, net of
costs and underwriting fees
|
3,000 | 30 | 2,388,756 | |||||||||||||||||||||||||||||
Conversion of preferred stock
|
(425 | ) | (4 | ) | 470,171 | 4,701 | (4,696 | ) | ||||||||||||||||||||||||
Issuance of warrants
|
498,793 | |||||||||||||||||||||||||||||||
Issuance of warrants to underwriter
|
15,455 | |||||||||||||||||||||||||||||||
Exercise of warrants
|
903,217 | 9,032 | (9,032 | ) | ||||||||||||||||||||||||||||
Balance: June 30, 2014
|
2,575 | 26 | 25,651,389 | 964,828 | 102,286,450 | (89,788,242 | ) | (1,599,875 | ) | 1,646,240 | ||||||||||||||||||||||
Net income (loss)
|
(12,885,808 | ) | 74,198 | |||||||||||||||||||||||||||||
Net currency translation adjustment
|
10,389 | |||||||||||||||||||||||||||||||
Issuance of common stock, net of
costs and underwriting fees
|
13,248,000 | 132,480 | 13,557,257 | |||||||||||||||||||||||||||||
Stock-based compensation
|
229,945 | 2,300 | 1,261,229 | |||||||||||||||||||||||||||||
Contribution of capital from
noncontrolling interest
|
13,756 | |||||||||||||||||||||||||||||||
Balance: June 30, 2015
|
2,575 | $ | 26 | 39,129,334 | $ | 1,099,608 | $ | 117,104,936 | $ | (102,674,049 | ) | $ | (1,589,486 | ) | $ | 1,734,194 |
See accompanying notes to consolidated financial statements.
31
EnSync, Inc.
|
||||||||
Consolidated Statements of Cash Flows
|
||||||||
|
||||||||
Year ended June 30,
|
||||||||
2015
|
2014
|
|||||||
Cash flows from operating activities
|
||||||||
Net loss
|
$ | (12,811,610 | ) | $ | (9,513,300 | ) | ||
Adjustments to reconcile net loss to net cash used in operating activities:
|
||||||||
Depreciation of property, plant and equipment
|
644,790 | 736,551 | ||||||
Amortization of intangible assets
|
- | 411,073 | ||||||
Amortization of discounts and debt issuance costs on notes payable
|
- | 14,566 | ||||||
Stock-based compensation, net
|
1,263,529 | 962,361 | ||||||
Equity in loss of investee company
|
495,119 | 657,882 | ||||||
Gain on investment in investee company
|
(1,257,407 | ) | - | |||||
Interest accreted on note receivable
|
(9,107 | ) | - | |||||
Changes in assets and liabilities
|
||||||||
Accounts receivable
|
937,931 | (604,099 | ) | |||||
Inventories
|
154,853 | 1,219,306 | ||||||
Prepaids and other current assets
|
(145,723 | ) | (85,838 | ) | ||||
Refundable income taxes
|
91,191 | 46,037 | ||||||
Accounts payable
|
467,102 | 18,710 | ||||||
Accrued expenses
|
(1,473,945 | ) | 1,872,642 | |||||
Customer deposits
|
436,010 | (1,453,117 | ) | |||||
Accrued compensation and benefits
|
40,170 | 30,744 | ||||||
Net cash used in operating activities
|
(11,167,097 | ) | (5,686,482 | ) | ||||
Cash flows from investing activities
|
||||||||
Change in restricted cash
|
9,708 | (9,901 | ) | |||||
Expenditures for property and equipment
|
(427,499 | ) | (51,543 | ) | ||||
Issuance of note receivable
|
(150,000 | ) | - | |||||
Net cash used in investing activities
|
(567,791 | ) | (61,444 | ) | ||||
Cash flows from financing activities
|
||||||||
Payment of deferred financing costs
|
(545,825 | ) | - | |||||
Repayments of bank loans and notes payable
|
(1,018,062 | ) | (929,403 | ) | ||||
Proceeds from issuance of preferred stock and warrants
|
- | 3,000,000 | ||||||
Preferred stock issuance costs
|
- | (96,967 | ) | |||||
Proceeds from issuance of common stock
|
14,837,760 | 14,231,250 | ||||||
Common stock issuance costs
|
(1,148,023 | ) | (1,194,786 | ) | ||||
Contributions of captial from noncontrolling interest
|
13,756 | - | ||||||
Net cash provided by financing activities
|
12,139,606 | 15,010,094 | ||||||
Effect of exchange rate changes on cash and cash equivalents
|
(7,978 | ) | 1,932 | |||||
Net increase in cash and cash equivalents
|
396,740 | 9,264,100 | ||||||
Cash and cash equivalents - beginning of year
|
10,360,721 | 1,096,621 | ||||||
Cash and cash equivalents - end of year
|
$ | 10,757,461 | $ | 10,360,721 | ||||
Supplemental disclosures of cash flow information:
|
||||||||
Cash paid for interest
|
$ | 114,236 | $ | 147,106 | ||||
Cash received from foreign income tax credit
|
- | 133,996 |
See accompanying notes to consolidated financial statements.
32
EnSync, Inc.
Notes to Consolidated Financial Statements
NOTE 1 - SUMMARY OF SIGNIFICANT ACCOUNTING POLICIES
Description of Business
EnSync, Inc. and its subsidiaries (“EnSync,” “we,” “us,” “our,” or the “Company”) develop, license, and manufacture innovative energy management systems solutions serving the commercial and industrial (“C&I”) building, utility and off-grid markets. Incorporated in 1998, EnSync is headquartered in Menomonee Falls, Wisconsin, USA with offices in San Francisco, California, Honolulu, Hawaii, Shanghai, China and Perth, Western Australia. In August 2015, we changed our corporate name from ZBB Energy Corporation to EnSync, Inc., and we regularly use the name EnSync Energy Systems for marketing and branding purposes.
EnSync develops and commercializes application solutions for advanced energy management systems critical to the transition from a “coal-centric economy” to one reliant on renewable energy sources. EnSync synchronizes conventional utility, distributed generation and storage assets to seamlessly ensure the least expensive and most reliable electricity available, thus enabling the future of energy networks. These advanced systems directly connect wind and solar equipment to the grid and other systems than can form various levels of micro-grids as well as power quality regulation solutions. EnSync brings vital power control and energy storage solutions to problems caused by incorporation of increasingly pervasive renewable energy generating assets that are part of the grid power transmission and distribution network used in commercial, industrial, and multi-tenant buildings. The Company also develops and commercializes energy management systems for off-grid applications such as island or remote power.
The consolidated financial statements include the accounts of the Company and those of its wholly-owned subsidiaries ZBB Energy Pty Ltd. (formerly known as ZBB Technologies, Ltd.) located in Perth, Australia, Century West PNL LLC, and its sixty percent owned subsidiary ZBB PowerSav Holdings Limited located in Hong Kong, which was formed in connection with the Company’s investment in a China joint venture.
Recent Developments
On July 13, 2015, pursuant to a Securities Purchase Agreement (the “Purchase Agreement”) with Solar Power, Inc., a California corporation (“SPI”), we issued and sold to SPI for an aggregate purchase price of $33,390,000 a total of (i) 8,000,000 shares (the “Purchased Common Shares”) of common stock and (ii) 28,048 shares (the “Purchased Preferred Shares”) of Series C Convertible Preferred Stock which are convertible, subject to the completion of projects under our supply agreement with SPI (as described below), into a total of up to 42,000,600 shares of Common Stock. The aggregate purchase price for the Purchased Common Shares was based on a purchase price per share of $0.6678, and the aggregate purchase price for the Purchased Preferred Shares was determined based on price of $0.6678 per common equivalent. Pursuant to the Purchase Agreement, the Company also issued to SPI a warrant to purchase 50,000,000 shares of Common Stock for an aggregate purchase price of $36,729,000 (the “Warrant”).
In connection with the Securities Purchase Agreement, the Company incurred $545,825 of financing related costs. As of June 30, 2015, the specific costs directly attributable to the Securities Purchase Agreement have been deferred and will be charged against the gross proceeds of the offering.
The Company also entered into a supply agreement with SPI pursuant to which the Company will sell and SPI will purchase certain products and services offered by the Company from time to time, including certain energy management system solutions for solar projects (the “Supply Agreement”).
The Purchased Preferred Shares were sold for $1,000 per share and are convertible at a conversion price of $0.6678, paid at the closing of the transaction; provided that (A) the first one-fourth (the “Series C-1 Preferred Stock”) of the Purchased Preferred Shares only become convertible upon the completion of five megawatts worth of solar projects in accordance with the Supply Agreement (the “Projects”), (B) the second one-fourth (the “Series C-2 Preferred Stock”) only become convertible upon the completion of 15 megawatts worth of Projects, (C) the third one-fourth (the “Series C-3 Preferred Stock”) only become convertible upon the completion of 25 megawatts worth of Projects, and (D) the last one fourth (the “Series C-4 Preferred Stock”) only become convertible upon the completion of 40 megawatts worth of Projects. The Warrant represents the right to acquire 50,000,000 shares of Common Stock at an exercise price equal to $0.7346. The Warrant only becomes exercisable upon the completion of 40 megawatts worth of Projects.
The Company also entered into a form of governance agreement with SPI (the “Governance Agreement”) pursuant to which SPI is entitled to nominate one director to the Company’s board of directors for so long as SPI holds at least 10,000 Purchased Preferred Shares or 25 million of Common Stock or Common Stock equivalents (the “Requisite Shares”). Additionally, for so long as the Purchaser holds the Requisite Shares (1) following the time at which the Series C-2 Preferred Stock shall have become convertible in full, the Purchaser shall be entitled to nominate a total of two Directors to the Board and (2) following the time at which the Series C-3 Preferred Stock shall have convertible in full, the Purchaser shall be entitled to nominate a total of three directors.
33
Basis of Presentation
The accompanying consolidated financial statements include the accounts of the Company and its wholly and majority-owned subsidiaries and have been prepared in accordance with US GAAP. All significant intercompany accounts and transactions have been eliminated in consolidation.
Use of Estimates
The preparation of financial statements in conformity with US GAAP requires management to make estimates and assumptions. These estimates and assumptions affect the reported amounts of assets and liabilities and disclosure of contingent assets and liabilities at the date of the financial statements and the reported amount of revenues and expenses during the reporting period. It is reasonably possible that the estimates we have made may change in the near future. Significant estimates underlying the accompanying consolidated financial statements include those related to:
·
|
the timing of revenue recognition;
|
·
|
the allowance for doubtful accounts;
|
·
|
provisions for excess and obsolete inventory;
|
·
|
the lives and recoverability of property, plant and equipment and other long-lived assets, including goodwill;
|
·
|
contract costs, losses, and reserves;
|
·
|
warranty obligations;
|
·
|
income tax valuation allowances;
|
·
|
stock-based compensation; and
|
·
|
valuation of warrants.
|
Fair Value of Financial Instruments
The Company’s financial instruments consist of cash and cash equivalents, restricted cash on deposit, accounts receivable, a note receivable, accounts payable, and bank loans and notes payable. The carrying amounts of the Company’s financial instruments approximate their respective fair values due to the relatively short-term nature of these instruments, except for the bank loans and notes payable. The carrying amount of the bank loans and notes payable approximates fair value due to the interest rate and terms approximating those available to us for similar obligations.
The Company accounts for the fair value of financial instruments in accordance with Financial Accounting Standards Board (“FASB”) Accounting Standards Codification (“ASC”) 820. Fair value is defined as the price that would be received to sell an asset or paid to transfer a liability in an orderly transaction between market participants at the measurement date. The degree of judgment utilized in measuring the fair value of assets and liabilities generally correlates to the level or pricing observability. FASB ASC 820 describes a fair value hierarchy based on the following three levels of inputs, of which the first two are considered observable and the last unobservable, that may be used to measure fair value:
Level 1 inputs are quoted prices (unadjusted) in active markets for identical assets or liabilities that the reporting entity can access at the measurement date.
Level 2 inputs are inputs other than quoted prices that are observable for the asset or liability, either directly or indirectly, for similar assets or liabilities in active markets.
Level 3 inputs are unobservable inputs for the asset or liability. As such, the prices or valuation techniques require inputs that are both significant to the fair value measurement and are unobservable.
Cash and Cash Equivalents
The Company considers all highly liquid investments with maturities of three months or less to be cash equivalents. The Company maintains its cash deposits at financial institutions predominately in the United States, Australia, and Hong Kong. The Company has not experienced any losses in such accounts.
34
Restricted Cash on Deposit
The Company had $60,193 and $69,901 in restricted cash on deposit as of June 30, 2015 and June 30, 2014, respectively, as collateral for certain credit arrangements.
Accounts Receivable
Credit is extended based on an evaluation of a customer’s financial condition. Accounts receivable are stated at the amount the Company expects to collect from outstanding balances. The Company records allowances for doubtful accounts based on customer-specific analysis and general matters such as current assessments of past due balances and economic conditions. The Company writes off accounts receivable against the allowance when they become uncollectible. Accounts receivable are stated net of an allowance for doubtful accounts of $11,074 and $10,878 as of June 30, 2015 and June 30, 2014. The composition of accounts receivable by aging category is as follows as of:
Year ended June 30,
|
||||||||
2015
|
2014
|
|||||||
Current
|
$ | 4,291 | $ | 902,545 | ||||
30-60 days
|
- | - | ||||||
60-90 days
|
3,555 | - | ||||||
Over 90 days
|
105,248 | 148,479 | ||||||
Total
|
$ | 113,093 | $ | 1,051,024 |
Inventories
Inventories are stated at the lower of cost or market. Cost is computed using standard cost, which approximates actual cost, on a first-in, first-out basis. The Company provides inventory write-downs based on excess and obsolete inventories determined primarily by future demand forecasts. The write-down is measured as the difference between the cost of the inventory and market based upon assumptions about future demand and charged to the provision for inventory, which is a component of cost of sales. At the point of the loss recognition, a new, lower cost basis for that inventory is established, and subsequent changes in facts and circumstances do not result in the restoration or increase in that newly established cost basis.
Note Receivable
The Company has one note receivable from an unrelated party. The note matures on December 15, 2015 and is classified as “Note receivable” in the financial statements. We regularly evaluate the financial condition of the borrower to determine if any reserve for uncollectible amount should be established. To date, no such reserve is required. See further discussion of the note receivable in Note 5.
Property, Plant and Equipment
Land, building, equipment, computers, furniture and fixtures are recorded at cost. Maintenance, repairs and betterments are charged to expense as incurred. Depreciation is provided for all plant and equipment on a straight-line basis over the estimated useful lives of the assets. The estimated useful lives used for each class of depreciable asset are:
Estimated Useful Lives
|
|
Manufacturing equipment
|
3 - 7 years
|
Office equipment
|
3 - 7 years
|
Building and improvements
|
7 - 40 years
|
The Company completed a review of the estimated useful lives of specific assets for the year ended June 30, 2015 and determined that there were no changes in the estimated useful lives of assets.
Impairment of Long-Lived Assets
In accordance with FASB ASC Topic 360, "Impairment or Disposal of Long-Lived Assets," the Company assesses potential impairments to its long-lived assets including property, plant, equipment and intangible assets when there is evidence that events or changes in circumstances indicate that the carrying value may not be recoverable.
If such an indication exists, the recoverable amount of the asset is compared to the asset’s carrying value. Any excess of the asset’s carrying value over its recoverable amount is expensed in the statement of operations. In assessing value in use, the estimated future cash flows are discounted to their present value using a pre-tax discount rate. Management has determined that there were no long-lived assets impaired as of June 30, 2015 and June 30, 2014.
Investment in Investee Company
Investee companies that are not consolidated, but over which the Company exercises significant influence, are accounted for under the equity method of accounting. Whether or not the Company exercises significant influence with respect to an investee depends on an evaluation of several factors including, among others, representation on the investee company’s board of directors and ownership level, which is generally a 20% to 50% interest in the voting securities of the investee company. Under the equity method of accounting, an investee company’s accounts are not reported in the Company’s consolidated balance sheets and statements of operations; however, the Company’s share of the earnings or losses of the investee company is reflected in the caption ‘‘Equity in loss of investee company” in the consolidated statements of operations. The Company’s carrying value in an equity method investee company is reported in the caption ‘‘Investment in investee company’’ in the Company’s consolidated balance sheets.
35
When the Company’s carrying value in an equity method investee company is reduced to zero, no further losses are recorded in the Company’s consolidated financial statements unless the Company guaranteed obligations of the investee company or has committed additional funding. When the investee company subsequently reports income, the Company will not record its share of such income until it equals the amount of its share of losses not previously recognized.
Goodwill
Goodwill is recognized as the excess cost of an acquired entity over the net amount assigned to assets acquired and liabilities assumed. Goodwill is not amortized but reviewed for impairment annually as of June 30 or more frequently if events or changes in circumstances indicate that its carrying value may be impaired. These conditions could include a significant change in the business climate, legal factors, operating performance indicators, competition, or sale or disposition of a significant portion of a reporting unit.
The first step of the impairment test requires the comparing of a reporting unit’s fair value to its carrying value. If the carrying value is less than the fair value, no impairment exists and the second step is not performed. If the carrying value is higher than the fair value, there is an indication that impairment may exist and the second step must be performed to compute the amount of the impairment. In the second step, the impairment is computed by estimating the fair values of all recognized and unrecognized assets and liabilities of the reporting unit and comparing the implied fair value of reporting unit goodwill with the carrying amount of that unit’s goodwill. The Company determined fair value as evidenced by market capitalization, and concluded that there was no need for an impairment charge as of June 30, 2015 and June 30, 2014.
Accrued Expenses
Accrued expenses consist of the Company’s present obligations related to various expenses incurred during the period and includes a reserve for estimated contract losses, other accrued expenses, and warranty obligations. Included in accrued expenses as of June 30, 2015 and June 30, 2014 is a reserve of approximately $685,000 and $1.7 million, respectively, for a product upgrade initiative established in the fourth quarter of fiscal 2014.
Subsequent to commercialization, installation and commissioning of units in the field, the Company garnered meaningful insights that resulted in system design modifications and other general upgrades, which improved the performance, efficiency, and reliability of its systems. In the interest of enhancing customer satisfaction, the Company launched the product upgrade initiative to implement these improvements at certain locations of its installed base through fiscal year 2016.
Warranty Obligations
The Company typically warrants its products for the shorter of twelve months after installation or eighteen months after date of shipment. Warranty costs are provided for estimated claims and charged to cost of product sales as revenue is recognized. Warranty obligations are also evaluated quarterly to determine a reasonable estimate for the replacement of potentially defective materials of all energy storage systems that have been shipped to customers.
While the Company actively engages in monitoring and improving its evolving battery and production technologies, there is only a limited product history and relatively short time frame available to test and evaluate the rate of product failure. Should actual product failure rates differ from the Company’s estimates, revisions are made to the estimated rate of product failures and resulting changes to the liability for warranty obligations. In addition, from time to time, specific warranty accruals may be made if unforeseen technical problems arise.
36
As of June 30, 2015 and June 30, 2014, included in the Company’s accrued expenses were $176,967 and $731,910, respectively, related to warranty obligations. The following is a summary of accrued warranty activity:
Year ended June 30,
|
||||||||
2015
|
2014
|
|||||||
Beginning balance
|
$ | 731,910 | $ | 479,873 | ||||
Accruals for warranties during the period
|
167,901 | 741,412 | ||||||
Settlements during the period
|
(480,683 | ) | (673,588 | ) | ||||
Adjustments relating to preexisting warranties
|
(242,161 | ) | 184,213 | |||||
Ending balance
|
$ | 176,967 | $ | 731,910 |
Revenue Recognition
Revenues are recognized when persuasive evidence of a contractual arrangement exits, delivery has occurred or services have been rendered, the seller’s price to buyer is fixed and determinable, and collectability is reasonably assured. The portion of revenue related to installation and final acceptance, is deferred until such installation and final customer acceptance are completed.
From time to time, the Company may enter into separate agreements at or near the same time with the same customer. The Company evaluates such agreements to determine whether they should be accounted for individually as distinct arrangements or whether the separate agreements are, in substance, a single multiple element arrangement. The Company evaluates whether the negotiations are conducted jointly as part of a single negotiation, whether the deliverables are interrelated or interdependent, whether the fees in one arrangement are tied to performance in another arrangement, and whether elements in one arrangement are essential to another arrangement. The Company’s evaluation involves significant judgment to determine whether a group of agreements might be so closely related that they are, in effect, part of a single arrangement.
Our collaboration agreements typically involve multiple elements or deliverables, including upfront fees, contract research and development, milestone payments, technology licenses or options to obtain technology licenses, and royalties. For these arrangements, revenues are recognized in accordance with FASB ASC 605-25, “Revenue Recognition – Multiple Element Arrangements.” The Company’s revenues associated with multiple element contracts is based on the selling price hierarchy, which utilizes vendor-specific objective evidence (“VSOE”) when available, third-party evidence (“TPE”) if VSOE is not available, and if neither is available then the best estimate of the selling price is used. The Company utilizes best estimate for its multiple deliverable transactions as VSOE and TPE do not exist. To be considered a separate element, the product or service in question must represent a separate unit under SEC Staff Accounting Bulletin 104, and fulfill the following criteria: the delivered item(s) has value to the customer on a standalone basis; there is objective and reliable evidence of the fair value of the undelivered item(s); and if the arrangement includes a general right of return relative to the delivered item(s), delivery or performance of the undelivered item(s) is considered probable and substantially in our control. For arrangements containing multiple elements, revenue from time and materials based service arrangements is recognized as the service is performed. Revenue relating to undelivered elements is deferred at the estimated fair value until delivery of the deferred elements. If the arrangement does not meet all criteria above, the entire amount of the transaction is deferred until all elements are delivered.
The portion of revenue related to engineering and development is recognized ratably upon delivery of the goods or services pertaining to the underlying contractual arrangement, or revenue is recognized as certain activities are performed by the Company over the estimated performance period.
The Company charges shipping and handling fees when products are shipped or delivered to a customer, and includes such amounts in product revenues and shipping costs in cost of sales. The Company reports its revenues net of estimated returns and allowances.
Total revenues of $1,763,510 and $7,851,607 were recognized for the years ended June 30, 2015 and June 30, 2014, respectively. Revenues for the year ended June 30, 2015 were comprised of two significant customers (59% and 22% of total revenue) and revenues for year ended June 30, 2014 were comprised of two significant customers (66% and 11% of total revenue). The Company had two significant customers with outstanding receivable balances of $77,000 and $31,000 (68% and 28% of accounts receivable, net) as of June 30, 2015. The Company had three significant customers with outstanding receivable balances of $375,000, $365,000, and $188,000 (35%, 35%, and 18% of accounts receivable, net) as of June 30, 2014.
37
Engineering, Development, and License Revenues
We assess whether a substantive milestone exists at the inception of our agreements. In evaluating if a milestone is substantive we consider whether:
·
|
Substantive uncertainty exists as to the achievement of the milestone event at the inception of the arrangement;
|
·
|
The achievement of the milestone involves substantive effort and can only be achieved based in whole or in part on our performance or the occurrence of a specific outcome resulting from our performance;
|
·
|
The amount of the milestone payment appears reasonable either in relation to the effort expended or the enhancement of the value of the delivered item(s);
|
·
|
There is no future performance required to earn the milestone; and
|
·
|
The consideration is reasonable relative to all deliverables and payment terms in the arrangement.
|
If any of these conditions are not met, we do not consider the milestone to be substantive and we defer recognition of the milestone payment and recognize it as revenue over the estimated period of performance, if any.
On December 13, 2011, the Company entered into a joint development and license agreement with a global technology company to jointly develop flow batteries. The objective of the joint development agreement was to develop low cost, high energy density grid scale flow battery stacks and systems that could lead to a significant cost reduction for grid level storage. The Company recognized revenue under this agreement upon achievement of certain performance milestones. The Company recognized $0 of revenue under this agreement for the year ended June 30, 2015 and $200,000 for the year ended June 30, 2014.
On April 8, 2011, the Company entered into a Collaboration Agreement (the “Collaboration Agreement”) with Honam Petrochemical Corporation, now known as Lotte Chemical Corporation (“Lotte”), pursuant to which the Company and Lotte collaborated on the technical development of the Company’s third generation zinc bromide flow battery module (the “Version 3 Battery Module”) and Lotte received a fully paid-up, exclusive and royalty-free license to sell and manufacture the Version 3 Battery Module in South Korea and a non-exclusive royalty-bearing license to sell the Version 3 Battery Module in Japan, Thailand, Taiwan, Malaysia, Vietnam and Singapore.
On December 16, 2013, the Company and Lotte entered into a Research and Development Agreement (the “R&D Agreement”) pursuant to which the Company has agreed to develop and provide to Lotte a zinc bromide chemical flow battery system, including a Zinc Bromide chemical flow battery module and related software (the “Product”), on the terms and conditions set forth in the R&D Agreement (the “Project”). The Project is scheduled to continue until December 16, 2015, unless extended by the mutual agreement of the Company and Lotte. Subject to the satisfaction of certain specified milestones, Lotte is required to make payments to the Company under the R&D Agreement totaling $3,000,000 over the term of the Project. We recognize revenue based upon a Performance Based Method pursuant to the model described in FASB ASC 980-605-25, where revenue is recognized based on the lesser of the amount of nonrefundable cash received or the amounts due based on the proportional amount of the total effort expected to be expended on the contract that has been provided to date as there does not exist substantial doubt that the milestones will be achieved. The Company recognized $755,000 of revenue under this agreement for the year ended June 30, 2015, and $1,125,000 of revenue under this agreement for the year ended June 30, 2014.
Additionally, on December 16, 2013, the Company and Lotte entered into an Amended License Agreement (the “Amended License”). Pursuant to the Amended License Agreement, the Company granted to Lotte, (1) an exclusive and royalty-free limited license in South Korea to use the Company’s zinc bromide flow battery module, zinc bromide flow battery stack and the technical information and know how related to the intellectual property arising from the Project (collectively, the “Technology”) to manufacture or sell a zinc bromide flow battery (the “Lotte Product”) in South Korea and (2) a non-exclusive (a) royalty-free limited license for Lotte and its affiliates to use the Technology internally in all locations other than China and South Korea to manufacture the Lotte Product and (b) royalty-bearing limited license to sell the Lotte Product in all locations other than China, the United States and South Korea. Lotte is required to pay the Company a total license fee of $3,000,000 under the Amended License Agreement plus up to an additional $1,000,000 if certain specific milestones are successfully achieved. In addition, Lotte is required to make ongoing royalty payments to the Company equal to a single digit percentage of Lotte’s sales of the Lotte Product outside of South Korea until December 31, 2019. The license fees are subject to a 16.5% non-refundable Korea withholding tax.
38
Overall since the agreement date, through June 30, 2015 there were $5,250,000 of payments received and $4,880,178 of revenue recognized under the Lotte agreements.
Included in engineering and development revenues were $755,000 and $1,325,000 for the years ended June 30, 2015 and June 30, 2014, respectively, related to collaborative agreements. Engineering and development costs related to the collaboration agreements totaled $267,000 and $206,000 for the years ended June 30, 2015 and June 20, 2014, respectively.
As of June 30, 2015 and June 30, 2014, the Company had no unbilled amounts from engineering and development contracts in process. The Company had received $370,000 and $0 in customer payments for engineering and development contracts, representing deposits in advance of performance of the contracted work, as of June 30, 2015, and June 30, 2014, respectively.
Advanced Engineering and Development Expenses
In accordance with FASB ASC Topic 730, “Research and Development,” the Company expenses advanced engineering and development costs as incurred. These costs consist primarily of materials, labor, and allocable indirect costs incurred to design, build, and test prototype units, as well as the development of manufacturing processes for these units. Advanced engineering and development costs also include consulting fees and other costs.
To the extent these costs are separately identifiable, incurred and funded by advanced engineering and development type agreements with outside parties, they are shown separately on the consolidated statements of operations as a “Cost of engineering and development.”
Stock-Based Compensation
The Company measures all “Share-Based Payments," including grants of stock options, restricted shares and restricted stock units in its consolidated statement of operations based on their fair values on the grant date, which is consistent with FASB ASC Topic 718, “Stock Compensation,” guidelines.
Accordingly, the Company measures share-based compensation cost for all share-based awards at the fair value on the grant date and recognizes share-based compensation over the service period for awards that are expected to vest. The fair value of stock options is determined based on the number of shares granted and the price of the shares at grant, and calculated based on the Black-Scholes valuation model.
The Company compensates its outside directors primarily with restricted stock units (“RSUs”) rather than cash. The grant date fair value of the restricted stock unit awards is determined using the closing stock price of the Company’s common stock on the day prior to the date of the grant, with the compensation expense amortized over the vesting period of restricted stock unit awards, net of estimated forfeitures.
The Company only recognizes expense for those options or shares that are expected ultimately to vest, using two attribution methods to record expense, the straight-line method for grants with only service-based vesting or the graded-vesting method, which considers each performance period, for all other awards. See further discussion of stock-based compensation in Note 9.
Advertising Expense
Advertising costs of $44,176 and $66,086 for the years ended June 30, 2015 and June 30, 2014, respectively, were charged to selling, general, and administrative expenses as incurred.
Income Taxes
The Company records deferred income taxes in accordance with FASB ASC Topic 740, “Accounting for Income Taxes.” FASB ASC Topic 740 requires recognition of deferred income tax assets and liabilities for temporary differences between the tax basis of assets and liabilities and the amounts at which they are carried in the financial statements, based upon the enacted tax rates in effect for the year in which the differences are expected to reverse. The Company establishes a valuation allowance when necessary to reduce deferred income tax assets to the amount expected to be realized. There were no net deferred income tax assets recorded as of June 30, 2015 and June 30, 2014.
The Company applies a more-likely-than-not recognition threshold for all tax uncertainties as required under FASB ASC Topic 740, which only allows the recognition of those tax benefits that have a greater than fifty percent likelihood of being sustained upon examination by the taxing authorities.
The Company’s U.S. Federal income tax returns for the years ended June 30, 2011 through June 30, 2014 and the Company’s Wisconsin and Australian income tax returns for the years ended June 30, 2010 through June 30, 2014 are subject to examination by taxing authorities. As of June 30, 2015, there were no examinations in progress.
39
Foreign Currency
The Company uses the United States dollar as its functional and reporting currency, while the Australian dollar and Hong Kong dollar are the functional currencies of its foreign subsidiaries. Assets and liabilities of the Company’s foreign subsidiaries are translated into United States dollars at exchange rates that are in effect at the balance sheet date while equity accounts are translated at historical exchange rates. Income and expense items are translated at average exchange rates which were applicable during the reporting period. Translation adjustments are recorded in accumulated other comprehensive loss as a separate component of equity in the consolidated balance sheets.
Loss per Share
The Company follows the FASB ASC Topic 260, “Earnings per Share,” provisions which require the reporting of both basic and diluted earnings (loss) per share. Basic earnings (loss) per share is computed by dividing net income (loss) available to common stockholders by the weighted average number of common shares outstanding for the period. Diluted earnings (net loss) per share reflect the potential dilution that could occur if securities or other contracts to issue common stock were exercised or converted into common stock. In accordance with the FASB ASC Topic 260, any anti-dilutive effects on net income (loss) per share are excluded. For the years ended June 30, 2015 and June 30, 2014 there were 9,663,729 and 8,618,574 shares of common stock underlying convertible preferred stock, options, restricted stock units and warrants that are excluded, respectively.
Concentrations of Credit Risk
Financial instruments that potentially subject the Company to concentrations of credit risk consist principally of cash and accounts receivable.
The Company maintains significant cash deposits primarily with two financial institutions. The Company has not previously experienced any losses on such deposits. Additionally, the Company performs periodic evaluations of the relative credit ratings of these institutions as part of its banking strategy.
Concentrations of credit risk with respect to accounts receivable are limited due to accelerated payment terms in current customer contracts and creditworthiness of the current customer base.
Reclassifications
Certain amounts previously reported have been reclassified to conform to the current presentation.
Segment Information
The Company has determined that it operates as one reportable segment.
Recent Accounting Pronouncements
From time to time, new accounting pronouncements are issued by the FASB or other standard setting bodies that are adopted by the Company as of the specified effective date. Unless otherwise discussed, the Company believes that the impact of recently issued standards that are not yet effective and not included below will not have a material impact on our financial position or results of operations upon adoption.
In August 2015, the FASB issued ASU 2015-14 – Revenue from Contracts with Customers (Topic 606): Deferral of the Effective Date. The amendment defers the effective date of Update 2014-09 for all entities by one year. Public business entities should apply the guidance in Update 2014-09 to annual reporting periods beginning after December 15, 2017, including interim reporting periods within that reporting period. Earlier application is permitted only as of annual reporting periods beginning after December 15, 2016, including interim reporting periods within that reporting period.
In July 2015, the FASB issued ASU 2015-11 – Inventory (Topic 330): Simplifying the Measurement of Inventory. The amendment was issued to modify the process in which entities measure inventory. The amendment does not apply to inventory measured using last-in, first-out (“LIFO”) or the retail inventory method. This amendment requires entities to measure inventory at the lower of cost and net realizable value. Net realizable value is the estimated selling prices in the ordinary course of business, less reasonably predictable costs of completion, disposal, and transportation. Subsequent measurement is unchanged for inventory measured using LIFO or the retail inventory method. The amendments are effective for fiscal years beginning after December 31, 2016, including interim periods within those fiscal years on a prospective basis with earlier application permitted as of the beginning of an interim or annual reporting period. The Company does not expect adoption of this guidance to have a significant impact on its consolidated financial statements.
In February 2015, the FASB issued ASU 2015-02 – Consolidation (Topic 810): Amendments to the Consolidation Analysis. The amendment is intended to improve certain areas of consolidation guidance for legal entities such as limited partnerships, limited liability corporations, and securitization structures. The amendment simplifies reporting requirements by placing more emphasis on risk of loss when determining a controlling financial interest, reducing the frequency of application of related-party guidance when determining a controlling financial interest in a variable interest entity (“VIE”), and changing consolidation conclusions for public companies in several industries that typically make use of limited partnerships or VIEs. The amendment is effective for fiscal years beginning after December 31, 2015. Early adoption is permitted. The Company does not expect adoption of this guidance to have a significant impact on its consolidated financial statements.
40
In January 2015, the FASB issued ASU 2015-01 – Income Statement – Extraordinary and Unusual Items (Subtopic 225-20): Simplifying Income Statement Presentation by Eliminating the Concept of Extraordinary Items. The amendment was issued to reduce complexity in the accounting standards by eliminating the concept of extraordinary items from US GAAP. The amendment is effective for annual periods ending after December 15, 2015. The change may be applied prospectively or retrospectively to all prior periods presented in the financial statements. Early adoption is permitted. The Company does not expect adoption of this guidance to have a significant impact on its consolidated financial statements.
In August 2014, the FASB issued ASU 2014-15 – Disclosure of Uncertainties about an Entity’s Ability to Continue as a Going Concern (Subtopic 205-40). The update requires management to perform a going concern assessment if there is substantial doubt about an entity’s ability to continue as a going concern within one year of the financial statement issuance date. Under the new standard, the definition of substantial doubt incorporates a likeliness threshold of “probable” that is consistent with the current use of the term defined in US GAAP for loss contingencies (Topic 450 – Contingencies). Management will need to consider conditions that are known and reasonably knowable at the financial statement issuance date and determine whether the entity will be able to meet its obligations within the one-year period. Additional disclosures are required if it is probable that the entity will be unable to meet its current obligations. The amendments in this ASU will be effective for annual periods ending after December 15, 2016. Early adoption is permitted. The Company does not expect adoption of this guidance to have a significant impact on its consolidated financial statements.
In June 2014, the FASB issued ASU 2014-12 - Compensation – Stock Compensation (Topic 718). The amendment requires that entities treat performance targets that can be met after the requisite service period of a share-based payment award as performance conditions that affect vesting and, accordingly, the performance target should not be reflected in estimating the grant-date fair value of the award. Compensation expense should be recognized in the period in which it becomes probable that the performance target will be achieved. ASU 2014-12 is effective for annual periods and interim periods within those annual periods beginning after December 15, 2015. The Company is required to adopt this standard beginning July 1, 2016. ASU 2014-12 does not contain any new disclosure requirements. The Company does not expect the adoption of ASU 2014-12 to have a material effect on our financial position, results of operations or cash flows.
In May 2014, the FASB issued ASU 2014-09 – Revenue from Contracts with Customers (Topic 606). The amendment outlines a single comprehensive model for entities to use in accounting for revenue arising from contracts with customers and supersedes most current revenue recognition guidance, including industry-specific guidance. The core principle of the revenue model is that an entity recognizes revenue to depict the transfer of promised goods or services to customers in an amount that reflects the consideration to which the entity expects to be entitled in exchange for those goods or services. In applying the revenue model to contracts within its scope, an entity identifies the contract(s) with a customer, identifies the performance obligations in the contract, determines the transaction price, allocates the transaction price to the performance obligations in the contract and recognizes revenue when the entity satisfies a performance obligation. ASU 2014-09 also includes additional disclosure requirements regarding revenue, cash flows and obligations related to contracts with customers. See ASU 2015-14 above for applicable effective date of ASU 2014-09. The guidance permits companies to either apply the requirements retrospectively to all prior periods presented, or apply the requirements in the year of adoption, through a cumulative adjustment. The Company is currently evaluating the effect that implementation of this update will have on its consolidated financial position and results of operations upon adoption.
In April 2014, the FASB issued ASU 2014-08 - Presentation of Financial Statements (Topic 205) and Property, Plant, and Equipment (Topic 360): Reporting Discontinued Operations and Disclosures of Disposals of Components of an Entity. The update changes the requirements for reporting discontinued operations in Subtopic 205-20. To be classified as a discontinued operation, the disposal of a component or group of components must represent a strategic shift that has, or will have, a major effect on an entity’s operations and financial results. Examples include a disposal of a major geographic area, a major line of business or a major equity method investment. The amendments in this ASU are effective prospectively for reporting periods beginning on or after December 15, 2014, with early adoption permitted. The adoption of this pronouncement did not have a material impact on the Company’s consolidated financial statements.
In July 2013, the FASB issued ASU 2013-11 – Presentation of an Unrecognized Tax Benefit When a Net Operating Loss Carryforward, a Similar Tax Loss, or a Tax Credit Carryforward Exists, which requires an unrecognized tax benefit to be presented in the financial statements as a reduction to a deferred tax asset for a net operating loss carryforward, similar tax loss, or a tax credit carryforward. To the extent the tax benefit is not available at the reporting date under the governing tax law or if the entity does not intend to use the deferred tax asset for such purpose, the unrecognized tax benefit should be presented as a liability and not combined with deferred tax assets. ASU 2013-11 is effective for annual periods, and interim periods within those years, beginning after December 15, 2013. The amendments are to be applied to all unrecognized tax benefits that exist as of the effective date and may be applied retrospectively to each prior reporting period presented. The adoption of this pronouncement did not have a material impact on the Company’s consolidated financial statements.
41
In April 2013, the FASB issued ASU 2013-07 – Presentation of Financial Statements (Topic 205) – Liquidation Basis of Accounting. The amendments require an entity to prepare its financial statements using the liquidation basis of accounting when liquidation is imminent. Liquidation is imminent when the likelihood is remote that the entity will return from liquidation and either (a) a plan for liquidation is approved by the person or persons with the authority to make such a plan effective and the likelihood is remote that the execution of the plan will be blocked by other parties or (b) a plan for liquidation is being imposed by other forces (for example, involuntary bankruptcy). If a plan for liquidation was specified in the entity’s governing documents from the entity’s inception (for example, limited-life entities), the entity should apply the liquidation basis of accounting only if the approved plan for liquidation differs from the plan for liquidation that was specified at the entity’s inception. The amendments require financial statements prepared using the liquidation basis of accounting to present relevant information about an entity’s expected resources in liquidation by measuring and presenting assets at the amount of the expected cash proceeds from liquidation. The entity should include in its presentation of assets any items it had not previously recognized under US GAAP but that it expects to either sell in liquidation or use in settling liabilities (for example, trademarks). The amendments are effective for entities that determine liquidation is imminent during annual reporting periods beginning after December 15, 2013, and interim reporting periods therein. Entities should apply the requirements prospectively from the day that liquidation becomes imminent. Early adoption was permitted. The adoption did not have an impact on the Company’s consolidated financial statements in its present condition.
In March 2013, the FASB issued ASU 2013-05 – Foreign Currency Matters (Topic 830) – Parent’s Accounting for the Cumulative Translation Adjustment upon derecognition of Certain Subsidiaries or Group of Assets within a Foreign Entity or of an Investment in a Foreign Entity. These amendments provide guidance on releasing cumulative translation adjustments when a reporting entity (parent) ceases to have a controlling financial interest in a subsidiary or a group of assets that is a non-profit activity or a business within a foreign entity. In addition, these amendments provide guidance on the release of cumulative translation adjustments in partial sales of equity method investments and in step acquisitions. The amendments are effective for fiscal years and interim reporting periods within those years, beginning after December 15, 2013. The amendments should be applied prospectively to derecognition events occurring after the effective date. Prior periods should not be adjusted. Early adoption was permitted. If an entity elects to early adopt the amendments, it should apply them as of the beginning of the entity’s fiscal year of adoption. The Company was required to adopt this standard beginning July 1, 2014. The adoption of this pronouncement did not have a material impact on the Company’s consolidated financial statements.
In February 2013, the FASB issued ASU 2013-04 – Liabilities (Topic 405) – Obligations Resulting from Joint and Several Liability Arrangements for Which the Total Amount of the Obligation is Fixed at the Reporting Date. The amendment provides guidance for the recognition, measurement, and disclosure of obligations resulting from joint and several liability arrangements for which the total amount of the obligation within the scope of this guidance is fixed at the reporting date, except for obligations addressed within existing guidance in US GAAP. Examples of obligations within this guidance are debt arrangements, other contractual obligations, and settled litigation and judicial rulings. The amendment is effective for fiscal years, and interim periods within those years, beginning after December 15, 2013. The amendment shall be applied retrospectively to all prior periods presented for those obligations within the scope of this Subtopic that exist at the beginning of an entity’s fiscal year of adoption. Early adoption was permitted. The adoption of this pronouncement did not have a material impact on the Company’s consolidated financial statements.
NOTE 2 - CHINA JOINT VENTURE
On August 30, 2011, the Company entered into agreements providing for establishment of a joint venture to develop, produce, sell, distribute and service advanced storage batteries and power electronics in China (the “Joint Venture”). Joint Venture partners include ZBB PowerSav Holdings Limited (“Holdco”), AnHui XinLong Electrical Co. and Wuhu Huarui Power Transmission and Transformation Engineering Co. The Joint Venture was established upon receipt of certain governmental approvals from China which were received in November 2011.
The Joint Venture operates through a jointly-owned Chinese company located in Wuhu City, Anhui Province named Anhui Meineng Store Energy Co., Ltd. (“Meineng Energy”). Meineng Energy intends to initially assemble and ultimately manufacture the Company’s products for sale in the power management industry on an exclusive basis in mainland China and on a non-exclusive basis in Hong Kong and Taiwan.
42
The Company’s President and Chief Executive Officer (“President and CEO”) has served as the Chief Executive Officer of Meineng Energy since December 2011. The President and CEO owns an indirect 6% equity interest in Meineng Energy.
In connection with the Joint Venture, on August 30, 2011 the Company and certain of its subsidiaries entered into the following agreements:
·
|
Joint Venture Agreement of Anhui Meineng Store Energy Co., Ltd. (the “China JV Agreement”) by and between ZBB PowerSav Holdings Limited, a Hong Kong limited liability company (“Holdco”), and Anhui Xinrui Investment Co., Ltd, a Chinese limited liability company; and
|
·
|
Limited Liability Company Agreement of ZBB PowerSav Holdings Limited by and between ZBB Cayman Corporation and PowerSav New Energy Holdings Limited (the “Holdco Agreement”).
|
In connection with the Joint Venture, upon establishment of Meineng Energy, the Company and certain of its subsidiaries entered into the following agreements:
·
|
Management Services Agreement by and between Meineng Energy and Holdco (the “Management Services Agreement”);
|
·
|
License Agreement by and between Holdco and Meineng Energy (the “License Agreement”); and
|
·
|
Research and Development Agreement by and between the Company and Meineng Energy (the “Research and Development Agreement”).
|
Pursuant to the China JV Agreement, Meineng Energy was capitalized with approximately $13.6 million of equity capital. The Company’s only capital contributions to the Joint Venture were the contribution of technology to Meineng Energy via the License Agreement and $200,000 in cash. The Company’s indirect interest in Meineng Energy equaled approximately 33%. On August 12, 2014, Meineng Energy received a cash investment of 20,000,000 RMB (approximately $3.2 million) from Wuhu Fuhai-Haoyan Venture Investment, L.P., a branch of Shenzhen Oriental Fortune Capital Co., Ltd., for a post-closing equity position of 8%. Required governmental approval was obtained in October 2014. This investment capital will be used to fund ongoing operations and development of the China market, and provided Meineng Energy a 250,000,000 RMB (approximately $42 million) post-closing valuation. Following this investment, the Company’s indirect investment in Meineng Energy equals approximately 30%. The Company’s indirect gain as a result of the investment was $775,537, which is net of the gain attributable to the noncontrolling interest of $481,870.
The Company’s investment in Meineng Energy was made through Holdco. Pursuant to the Holdco Agreement, the Company contributed technology to Holdco via a license agreement with an agreed upon value of approximately $4.1 million and $200,000 in cash in exchange for a 60% equity interest. PowerSav agreed to contribute to Holdco $3.3 million in cash in exchange for a 40% equity interest. The initial capital contributions (consisting of the Company’s technology contribution and one half of required cash contributions) were made in December 2011. The subsequent capital contributions (consisting of one half of the required cash contribution) were made on May 16, 2012. For financial reporting purposes, Holdco’s assets and liabilities are consolidated with those of the Company and PowerSav’s 40% interest in Holdco is included in the Company’s consolidated financial statements as a noncontrolling interest. As of June 30, 2015, the Company’s indirect investment in the China JV was $674,334.
The Company’s basis in the technology contributed to Holdco was $0 due to US GAAP requirements related to research and development expenditures. The difference between the Company’s basis in this technology and the valuation of the technology by Meineng Energy of approximately $4.1 million is accounted for by the Company through the elimination of the amortization expense recognized by Meineng Energy related to the technology.
The Company has the right to appoint a majority of the members of the Board of Directors of Holdco and Holdco has the right to appoint a majority of the members of the Board of Directors of Meineng Energy.
Pursuant to the Management Services Agreement, Holdco will provide certain management services to Meineng Energy in exchange for a management services fee equal to five percent of Meineng Energy’s net sales for the five year period beginning on the first day of the first quarter in which the JV Company achieves operational breakeven results and three percent of Meineng Energy’s net sales for the subsequent three years, provided the payment of such fees will terminate upon Meineng Energy completing an initial public offering on a nationally recognized securities exchange. To date, no management service fee revenues have been recognized by Holdco.
43
Pursuant to the License Agreement (as amended on July 1, 2014), Holdco granted to Meineng Energy (1) an exclusive royalty-free license to manufacture and distribute the Company’s ZBB EnerStore, zinc bromide flow battery, version three (V3) (50KW) (and any other zinc bromide Flow Battery product developed internally by us based on the V3 EnerStore, ranging from 50kWh - 500 kWh module design) and ZBB EnerSection, power and energy control center (up to 250KW) (the “Products”) in mainland China in the power supply management industry and (2) a non-exclusive royalty-free license to manufacture and distribute the Products in Hong Kong and Taiwan in the power supply management industry.
Pursuant to the Research and Development Agreement, Meineng Energy may request the Company to provide research and development services upon commercially reasonable terms and conditions. Meineng Energy would pay the Company’s fully-loaded costs and expenses incurred in providing such services.
The Company had product sales of $70,328 and $853,663 to Meineng Energy during the years ended June 30, 2015 and June 30, 2014, respectively. The associated costs of the product sales to Meineng Energy were $55,550 and $645,853 during the years ended June 30, 2015 and June 30, 2014, respectively. During the years ended June 30, 2015 and June 30, 2014, the Company had total product purchases from Meineng Energy of $482,161 and $143,636, respectively. As of June 30, 2015, the total amount due to Meineng Energy was $250,562.
The operating results for Meineng Energy for the years ended June 30, 2015 and June 30, 2014 are summarized as follows:
Year ended June 30,
|
||||||||
2015
|
2014
|
|||||||
Revenues
|
$ | 588,190 | $ | 285,631 | ||||
Gross Profit (loss)
|
(197,957 | ) | (309,406 | ) | ||||
Income (loss) from operations
|
(2,095,980 | ) | (3,002,192 | ) | ||||
Net Income (loss)
|
(2,046,548 | ) | (3,038,432 | ) |
NOTE 3 - MANAGEMENT’S PLANS AND FUTURE OPERATIONS
The accompanying consolidated financial statements have been prepared on the basis of a going concern which contemplates that the Company will be able to realize assets and discharge its liabilities in the normal course of business. Accordingly, they do not give effect to any adjustments that would be necessary should the Company be required to liquidate its assets. The Company incurred a net loss of $12,885,808 attributable to EnSync, Inc. for year ended June 30, 2015, and as of June 30, 2015 has an accumulated deficit of $102,674,049 and total EnSync, Inc. equity of $13,941,035. The ability of the Company to settle its total liabilities of $4,976,623 and to continue as a going concern is dependent upon increasing revenues and achieving profitability. The accompanying consolidated financial statements do not include any adjustments that might result from the outcome of these uncertainties.
We believe that cash and cash equivalents on hand at June 30, 2015, expected collections on the Lotte R&D Agreement, the July 13, 2015 financing from SPI, and other potential sources of cash, will be sufficient to fund our current operations through the fourth quarter of fiscal year 2017. However, there can be no assurances that unforeseen circumstances will not require the Company to raise additional investment capital to fund its operations. If the Company is unable to obtain additional required funding, the Company’s financial condition and results of operations may be materially adversely affected and the Company may not be able to continue operations.
NOTE 4 - INVENTORIES
Inventories are comprised of the following as of:
As of June 30,
|
||||||||
2015
|
2014
|
|||||||
Raw materials
|
$ | 1,125,251 | $ | 1,054,197 | ||||
Work in progress
|
72,866 | 298,773 | ||||||
Finished goods
|
- | - | ||||||
Total
|
$ | 1,198,117 | $ | 1,352,970 |
NOTE 5 – NOTE RECEIVABLE
On September 23, 2014, the Company was issued a $150,000 convertible promissory note from an unrelated party. The note accrues interest at 8% per annum on the outstanding principal amount. The entire outstanding principal balance and accrued interest is due and payable on December 15, 2015, the maturity date of the note. If at the maturity date the note and accrued interest has not been paid in full, the Company may convert the principal and interest outstanding into shares of its convertible preferred stock at the then-current valuation.
44
NOTE 6 - PROPERTY, PLANT & EQUIPMENT
Property, plant, and equipment are comprised of the following as of:
As of June 30,
|
||||||||
2015
|
2014
|
|||||||
Land
|
$ | 217,000 | $ | 217,000 | ||||
Building and improvements
|
3,532,375 | 3,520,872 | ||||||
Manufacturing equipment
|
3,965,750 | 3,710,127 | ||||||
Office equipment
|
407,191 | 399,583 | ||||||
Construction in process
|
35,700 | - | ||||||
Total, at cost
|
8,158,016 | 7,847,582 | ||||||
Less: accumulated depreciation
|
(3,993,104 | ) | (3,465,379 | ) | ||||
Property, plant and equipment, net
|
$ | 4,164,912 | $ | 4,382,203 |
The Company recorded depreciation expense of $644,790 and $736,551 for the years ended June 30, 2015 and June 30, 2014, respectively.
NOTE 7 - GOODWILL
The Company acquired ZBB Technologies, Inc., a former wholly-owned subsidiary, through a series of transactions in March 1996. ZBB Technologies Inc. was subsequently merged with and into EnSync, Inc. on January 1, 2012. The goodwill amount of $1.134 million, the difference between the price paid for ZBB Technologies, Inc. and the net assets of the acquisition, amortized through fiscal 2002, resulted in the net goodwill amount of $803,079 as of June 30, 2015 and June 30, 2014.
NOTE 8 - BANK LOANS AND NOTES PAYABLE
The Company’s debt consisted of the following as of:
As of June 30,
|
||||||||
2015
|
2014
|
|||||||
Bank loans and notes payable-current
|
$ | 324,626 | $ | 351,142 | ||||
Bank loans and notes payable-long term
|
1,053,581 | 2,045,127 | ||||||
Total
|
$ | 1,378,207 | $ | 2,396,269 |
Bank loans and notes payable consisted of the following as of:
As of June 30,
|
||||||||
2015
|
2014
|
|||||||
Note payable to Wisconsin Econcomic Development Corporation payable in
monthly installments of $23,685, including interest at 2%, with the final
payment due May 1, 2018; collateralized by equipment purchased with the loan
proceeds and substantially all assets of the Company not otherwise
collateralized. The Company is required to maintain and increase a specified
number of employees, and the interest rate is increased in certain cases for
failure to meet this requirement.
|
$ | 804,550 | $ | 1,069,793 | ||||
Bank loan payable in fixed monthly payments of $6,800 of principal and interest
at a rate of 0.25% below prime, as defined, subject to a floor of 5% with any
principal due at maturity on June 1, 2018; collateralized by the building and land.
|
573,657 | 624,760 | ||||||
Note payable in fixed monthly installments of $6,610 of principal and interest at
a rate of 5.5% with any principal due at maturity on May 1, 2028; collateralized
by the building and land; paid in full during fiscal year 2015.
|
- | 701,716 | ||||||
$ | 1,378,207 | $ | 2,396,269 |
45
Maximum aggregate annual principal payments for fiscal periods subsequent to June 30, 2015 are as follows:
2016
|
$ | 324,626 | ||
2017
|
332,970 | |||
2018
|
720,611 | |||
$ | 1,378,207 |
NOTE 9 - EMPLOYEE AND DIRECTOR EQUITY INCENTIVE PLANS
The Company previously adopted the 2002 Stock Option Plan (“2002 Plan”) in which a stock option committee could grant up to 1,000,000 shares to key employees or non-employee members of the board of directors. The options vest in accordance with specific terms and conditions contained in an employment agreement. If vesting terms and conditions are not defined in an employment agreement, then the options vest as determined by the stock option committee. If the vesting period is not defined in an employment agreement or by the stock option committee, then the options immediately vest in full upon death, disability, or termination of employment. Vested options expire upon the earlier of either the five year anniversary of the vesting date or termination of employment. No shares are available to be issued under the 2002 Plan.
The Company also previously adopted the 2007 Equity Incentive Plan (“2007 Plan”) that authorized the board of directors or a committee to grant up to 300,000 shares to employees and directors of the Company. Unless defined in an employment agreement or otherwise determined, the options vest ratably over a three-year period. Options expire 10 years after the date of grant. No shares are available to be issued under the 2007 Plan.
In November 2010, the Company adopted the 2010 Omnibus Long-Term Incentive Plan (“Omnibus Plan”) which authorizes a committee of the board of directors to grant stock options, stock appreciation rights, restricted stock, restricted stock units, unrestricted stock, other stock-based awards, and cash awards. The Omnibus Plan authorized up to 800,000 shares plus shares of Common Stock underlying any outstanding stock option of other awards granted by any predecessor employee stock plan of the Company that is forfeited, terminated, or cancelled without issuance of shares, to employees, officers, non-employee members of the board of directors, consultants, and advisors. Unless otherwise determined, options vest ratably over a three-year period and expire 8 years after the date of grant.
At the annual meeting of shareholders held on November 7, 2012 the Company’s shareholders approved an amendment of the Omnibus Plan which increased the number of shares of the Company’s common stock available for issuance pursuant to awards under the Omnibus Plan by 900,000 shares and the creation of the 2012 Non-Employee Director Equity Compensation Plan (“2012 Director Equity Plan”), under which the Company may issue up to 700,000 restricted stock unit (“RSU”) awards and other equity awards to our non-employee directors pursuant to the Company’s director compensation policy.
At the annual meeting of shareholders held on November 18, 2014, the Company’s shareholders approved an amendment of the Omnibus Plan which increased the number of shares of the Company’s common stock available for issuance under the Omnibus Plan by 1,250,000. The shareholders also approved an amendment of the 2012 Director Equity Plan which increased the number of shares of the Company’s common stock available for issuance under the 2012 Director Equity Plan by 1,000,000. As of June 30, 2015, there were a total of 1,704,933 shares available to be issued under the Omnibus Plan and 456,804 shares available to be issued under the 2012 Director Equity Plan.
In aggregate for all plans, at June 30, 2015 there were outstanding a total of 1,577,778 options and 1,936,035 RSUs.
The fair value of each option granted is estimated on the date of grant using the Black-Scholes option-pricing method. The Company uses historical data to estimate the expected price volatility, the expected option life and the expected forfeiture rate. The Company has not made any dividend payments nor does it have plans to pay dividends in the foreseeable future. The following assumptions were used to estimate the fair value of options granted during the years ended June 30, 2015 and June 30, 2014 using the Black-Scholes option-pricing model:
Year ended June 30,
|
||||
2015
|
2014
|
|||
Expected life of option (years)
|
4
|
4
|
||
Risk-free interest rate
|
1.07 - 1.42%
|
0.95 - 1.20%
|
||
Assumed volatility
|
99.43 - 103.90%
|
94.35 - 154.68%
|
||
Expected dividend rate
|
0%
|
0%
|
||
Expected forfeiture rate
|
5.00 - 6.32%
|
4.91 - 5.62%
|
46
Time-vested and performance-based stock awards, including stock options and RSUs are accounted for at fair value at date of grant. Compensation expense is recognized over the requisite service and performance periods.
During the years ended June 30, 2015 and June 30, 2014, the Company’s results of operations include compensation expense for stock options and RSUs granted under its various equity incentive plans. The amount recognized in the financial statements related to stock-based compensation was $1,263,529 and $962,361, based on the amortized grant date fair value of options and RSUs during the years ended June 30, 2015 and June 30, 2014, respectively.
Information with respect to stock option activity is as follows:
Number
of
Options
|
Weighted
Average
Exercise Price
|
Average
Remaining
Contractual Life
(in years)
|
||||||||||
Balance at June 30, 2013
|
785,284 | $ | 5.78 | |||||||||
Options granted
|
699,850 | 1.33 | ||||||||||
Options forfeited
|
(66,066 | ) | 13.23 | |||||||||
Balance at June 30, 2014
|
1,419,068 | 3.23 | 6.09 | |||||||||
Options granted
|
423,000 | 0.85 | ||||||||||
Options forfeited
|
(264,290 | ) | 3.22 | |||||||||
Balance at June 30, 2015
|
1,577,778 | $ | 2.60 | 5.74 |
The following table summarizes information relating to the stock options outstanding as of June 30, 2015:
Outstanding
|
Exercisable
|
|||||||||||||||||||||||||
Range of Exercise Prices
|
Number
of
Options
|
Average
Remaining
Contractual Life
(in years)
|
Weighted
Average
Exercise
Price
|
Number
of
Options
|
Average
Remaining
Contractual Life
(in years)
|
Weighted
Average
Exercise
Price
|
||||||||||||||||||||
$ | 0.48 to $1.00 | 389,500 | 6.83 | $ | 0.69 | 157,600 | 6.81 | $ | 0.68 | |||||||||||||||||
$ | 1.01 to $2.50 | 750,528 | 6.75 | 1.51 | 205,903 | 6.15 | 1.82 | |||||||||||||||||||
$ | 2.51 to $5.00 | 98,900 | 3.99 | 3.94 | 98,900 | 3.99 | 3.94 | |||||||||||||||||||
$ | 5.01 to $7.50 | 323,850 | 2.86 | 6.28 | 323,850 | 2.86 | 6.28 | |||||||||||||||||||
$ | 7.51 to $17.95 | 15,000 | 0.58 | 17.95 | 15,000 | 0.58 | 17.95 | |||||||||||||||||||
Balance at June 30, 2015
|
1,577,778 | 5.74 | $ | 2.60 | 801,253 | 4.58 | $ | 3.96 |
During the year ended June 30, 2015, options to purchase 423,000 shares were granted to employees exercisable at $0.48 to $1.67 per share based on various service-based and performance-based vesting terms from July 2014 through June 2018 and exercisable at various dates through June 2023. During the year ended June 30, 2014, options to purchase 699,850 shares were granted to employees exercisable at $0.76 to $1.90 per share based on service based vesting terms from July 2013 through June 2017 and exercisable at various dates through June 2022.
The aggregate intrinsic value of outstanding options totaled $75,425 and was based on the Company’s adjusted closing stock price of $0.88 as of June 30, 2015.
A summary of the status of unvested employee stock options as of June 30, 2015 and June 30, 2014 and changes during the years then ended is presented below:
Number
of
Options
|
Weighted
Average
Grant Date
Fair Value
Per Share
|
Average
Remaining
Contractual Life
(in years)
|
|||||||
Balance at June 30, 2013
|
262,668 | $ | 3.44 | ||||||
Options granted
|
699,850 | 1.33 | |||||||
Options vested
|
(127,586 | ) | 3.55 | ||||||
Options forfeited
|
(12,463 | ) | 3.38 | ||||||
Balance at June 30, 2014
|
822,469 | 1.63 | |||||||
Options granted
|
423,000 | 0.85 | |||||||
Options vested
|
(347,328 | ) | 1.42 | ||||||
Options forfeited
|
(121,616 | ) | 2.31 | ||||||
Balance at June 30, 2015
|
776,525 | $ | 1.19 |
6.94
|
Total fair value of options granted for the years ended June 30, 2015 and June 30, 2014 was $250,771 and $665,414, respectively. At June 30, 2015, there was $305,094 in unrecognized compensation cost related to unvested stock options, which is expected to be recognized over a weighted average period of 1.3 years.
47
The Company compensates its directors with RSUs and cash. On December 20, 2013, 455,696 RSUs were granted to the Company’s directors in partial payment of directors fees through November 2014 under the 2012 Director Equity Plan. As of June 30, 2015, 445,696 of the RSUs had vested and there were $90,000 in directors’ fees expense settled with RSUs for the year ended June 30, 2015.
On May 1, 2013, the Company’s Chief Executive Officer (“CEO”) and Chief Operating Officer (“COO”) were awarded 200,000 RSUs each which would have vested on the satisfaction of certain performance targets. The RSUs were forfeited on December 31, 2013 resulting in a credit to selling, general, and administrative expense of $406,000 during the year ended June 30, 2014.
On January 14, 2014, the Company’s CEO and COO were awarded 500,000 RSUs, of which 100,000 vested immediately upon grant, and the remaining 400,000 were cancelled prior to June 30, 2014. On April 9, 2014, the Company’s CEO was awarded 200,000 RSUs which vested immediately upon grant.
On November 18, 2014, 562,500 RSUs were granted to the Company’s directors in partial payment of directors fees through November 2015 under the 2012 Director Equity Plan. As of June 30, 2015, 421,875 of the RSUs had vested and there were $270,000 in director’s fees expense settled with RSUs for the year ended June 30, 2015.
As of June 30, 2015 there were 230,625 unvested RSUs outstanding which will vest through January 15, 2016 and $90,000 in unrecognized compensation cost related to unvested RSUs which is expected to be recognized through January 15, 2016. Generally, shares of common stock related to vested RSUs are to be issued six months after the holder’s separation from service with the Company.
The table below summarizes the activity of the restricted stock units for the years ended June 30, 2015 and June 30, 2014:
Number of
Restricted
Stock Units
|
Weighted
Average
Valuation
Price Per Unit
|
|||||||
Balance at June 30, 2013
|
1,131,687 | $ | 2.30 | |||||
RSUs granted
|
1,660,696 | 0.99 | ||||||
RSUs forfeited
|
(1,200,000 | ) | 1.10 | |||||
Shares issued
|
(245,570 | ) | 1.61 | |||||
Balance at June 30, 2014
|
1,346,813 | 1.87 | ||||||
RSUs granted
|
922,500 | 1.05 | ||||||
RSUs forfeited
|
(103,334 | ) | 1.69 | |||||
Shares issued
|
(229,944 | ) | 0.80 | |||||
Balance at June 30, 2015
|
1,936,035 | $ | 1.53 |
NOTE 10 - WARRANTS
At June 30, 2015, the following warrants to purchase the Company’s common stock were outstanding and exercisable:
|
·
|
81,579 warrants exercisable at $0.95 per share and which expire in September 2016 issued as placement agent’s compensation in connection with the sale of $3 million of preferred stock on September 27, 2013 as described in Note 12.
|
|
·
|
1,710,525 warrants exercisable at $0.95 per share and which expire in September 2016 issued in connection with Securities Purchase Agreements entered into with certain investors providing for the sale of a total of $3.0 million of preferred stock on September 27, 2013 described in Note 12. In March 2014, 1,447,369 warrants were exercised via a cashless exercise resulting in the issuance of 850,169 shares of common stock of the Company.
|
|
·
|
15,000 warrants exercisable at $2.10 per share which expire in July 2015 issued as partial payment for services.
|
|
·
|
306,902 warrants exercisable at $2.375 per share and which expire in June 2017 issued in connection with the Underwriting Agreement entered into with MDB Capital Group, LLC as part of underwriting compensation which provided for the sale of $12 million of common stock on June 19, 2012. On March 19, 2014, 272,159 warrants were exercised via a cashless exercise resulting in the issuance of 53,048 shares of common stock of the Company.
|
48
|
·
|
511,604 warrants exercisable at $2.65 per share and which expire in May 2017 issued in connection with Securities Purchase Agreements entered into with certain investors providing for the sale of a total of $2,465,000 of Zero Coupon Convertible Subordinated Notes on May 1, 2012.
|
|
·
|
6,300 warrants exercisable at $5.00 per share which expire in July 2015 issued as partial payment for services.
|
|
·
|
224,375 warrants exercisable at $5.20 per share and which expire in September 2015 issued to certain purchasers of Company shares in March 2010.
|
|
·
|
71,667 warrants exercisable at $6.65 per share and which expire in August 2015 issued to certain purchasers of Company shares in August 2009.
|
The table below summarizes warrant balances and activity for the years ended June 30, 2015 and June 30, 2014:
Number of
Warrants
|
Weighted
Average
Exercise Price
Per Share
|
|||||||
Balance at June 30, 2013
|
1,421,806 | $ | 3.15 | |||||
Warrants granted
|
3,239,474 | 0.95 | ||||||
Warrants expired
|
(8,000 | ) | 2.80 | |||||
Warrants exercised
|
(1,719,528 | ) | 1.18 | |||||
Balance at June 30, 2014
|
2,933,752 | 1.88 | ||||||
Warrants granted
|
- | - | ||||||
Warrants expired
|
(5,800 | ) | 5.00 | |||||
Warrants exercised
|
- | - | ||||||
Balance at June 30, 2015
|
2,927,952 | $ | 1.88 |
NOTE 11 – BASIC AND DILUTED NET LOSS PER SHARE
Basic net loss per common share is computed by dividing net loss attributable to common stockholders by the weighted average number of common shares outstanding for the period reported. Diluted net loss per common share is computed giving effect to all dilutive potential common shares that were outstanding for the period reported. Diluted potential common shares consist of incremental shares issuable upon exercise of stock options and warrants and conversion of preferred stock. In computing diluted net loss per share for the years ended June 30, 2015 and June 30, 2014, no adjustment has been made to the weighted average outstanding common shares as the assumed exercise of outstanding options and warrants and conversion of preferred stock is anti-dilutive.
Potential common shares not included in calculating diluted net loss per share are as follow:
As of June 30,
|
||||||||
2015
|
2014
|
|||||||
Stock options and restricted stock units
|
3,513,813 | 2,765,880 | ||||||
Stock warrants
|
2,927,952 | 2,933,752 | ||||||
Series B preferred shares
|
3,221,964 | 2,918,942 | ||||||
Total
|
9,663,729 | 8,618,574 |
NOTE 12 - EQUITY
On August 27, 2014, the Company completed an underwritten public offering of its common stock at a price to the public of $1.12 per share. The Company sold a total of 13,248,000 shares of its common stock in the offering for aggregate proceeds of approximately $14.8 million. The Company received approximately $13.7 million of net proceeds from the offering, after deducting the underwriting discount and expenses.
On March 13, 2013, the Company entered into a Common Stock Purchase Agreement (“Purchase Agreement”) with Aspire Capital Fund, LLC, an Illinois limited liability company (“Aspire Capital”), which provided that, upon the terms and subject to the conditions and limitations set forth therein, Aspire Capital was committed to purchase up to an aggregate of $10 million of shares of the Company’s common stock over the two-year term of the Purchase Agreement. On August 18, 2014, the Company provided notice to Aspire Capital electing to terminate the Purchase Agreement.
49
On March 19, 2014, the Company completed an underwritten public offering of its common stock at a price to the public of $2.25 per share. The Company sold a total of 6,325,000 shares of its common stock in the offering for aggregate proceeds of approximately $14.2 million. The Company received approximately $13.0 million of net proceeds from the offering, after deducting the underwriting discount and expenses.
On October 31, 2013, the Company effected a reverse stock split of its common stock by a ratio of 1-for-5 (the “Reverse Split”). As a result of the Reverse Split every five outstanding shares of Common Stock became one share of common stock. No fractional shares were issued in connection with the Reverse Split. A shareholder who would otherwise have been entitled to receive a fractional share of common stock received a cash payment equal to the closing sales price of the Company’s Common Stock on October 31, 2013 as reported on the NYSE MKT times the amount of the fractional share. The Reverse Split did not change the number of shares of common or preferred stock that the Company is authorized to issue, or the par value of the Company’s common or preferred stock. The Reverse Split resulted in a proportionate adjustment to the per share exercise price and the number of shares of common stock issuable upon the exercise of outstanding warrants and stock options, as well as the number of shares of common stock eligible for issuance under the Omnibus Plan and the 2012 Director Equity Plan. All of the information in these financial statements has been presented to reflect the impact of the 1-for-5 Reverse Split on a retroactive basis.
On September 26, 2013 the Company entered into a Securities Purchase Agreement with certain investors providing for the sale of 3,000 shares of Series B Convertible Preferred Stock (the “Preferred Stock”). Certain Directors of the Company purchased 500 shares.
Shares of Preferred Stock were sold for $1,000 per share (the “Stated Value”) and accrue dividends on the Stated Value at an annual rate of 10%. The net proceeds to the Company, after deducting $90,966 of offering costs, were $2,903,004. During the year ended June 30, 2014, 425 shares of Preferred Stock were converted into 470,171 shares of common stock of the Company. At June 30, 2015, 2,575 shares of Preferred Stock were convertible into 3,221,964 shares of common stock of the Company (“Common Stock”) at a conversion price equal to $0.95. Upon any liquidation, dissolution or winding up of the Company, holders of Preferred Stock are entitled to receive out of the assets of the Company an amount equal to two times the Stated Value, plus any accrued and unpaid dividends thereon. At June 30, 2015 the liquidation preference of the Preferred Stock was $5,635,866.
In connection with the purchase of the Preferred Stock, investors received warrants to purchase a total of 3,157,897 shares of Common Stock at an exercise price of $0.95. The warrants are exercisable at any time prior to September 27, 2016. During the year ended June 30, 2014, 1,447,369 warrants were exercised via a cashless exercise resulting in the issuance of 850,169 shares of common stock of the Company. In addition, the Company issued a total of 81,579 warrants to a placement agent in connection with the transaction. These warrants expire on September 27, 2016.
NOTE 13 - COMMITMENTS
Leasing Activities
The Company leases its Australian research and development facility from a non-related Australian company under the terms of a lease that expires October 31, 2016. In July of 2011, the Company renewed the lease on its Australian facility through October 2016 subject to an annual CPI adjustment. Rent expense was $87,568 and $93,434 for the years ended June 30, 2015 and June 30, 2014, respectively.
The future payments required under the terms of the leases for fiscal periods subsequent to June 30, 2015 are as follows:
2016
|
$ | 81,376 | ||
2017
|
27,125 | |||
$ | 108,502 |
The Company also leased a building from an officer of its subsidiary, Tier Electronics LLC, who is also a shareholder and was a director, under a lease agreement that was due to expire on June 30, 2015. Subsequently a lease termination agreement was entered into on October 20, 2013, which terminated the lease effective December 31, 2013 for a fee of $21,000. The rent expense was $63,000 for year ended June 30, 2014. The Company was required to pay real estate taxes and other occupancy costs related to the facility.
50
Employment Contracts
The Company has entered into employment contracts with executives and management personnel. The contracts provide for salaries, bonuses and stock option grants, along with other employee benefits. The employment contracts generally have no set term and can be terminated by either party. There is a provision for payments of up to six months of annual salary as severance if the Company terminates a contract without cause, along with the acceleration of certain unvested stock option grants.
NOTE 14 - RETIREMENT PLANS
All Australian based employees are entitled to varying degrees of benefits on retirement, disability, or death. The Company contributes to an accumulation fund on behalf of the employees under an award which is legally enforceable.
For U.S. employees, the Company has a 401(k) plan. All active participants are 100% vested immediately. Expenses under these plans were $108,044 and $134,831 for the years ended June 30, 2015 and June 30, 2014, respectively.
NOTE 15 - INCOME TAXES
The provision (benefit) for income taxes consists of the following:
Year ended June 30,
|
||||||||
2015
|
2014
|
|||||||
Current
|
$ | (86,455 | ) | $ | (82,411 | ) | ||
Deferred
|
- | - | ||||||
Provision (benefit) for income taxes
|
$ | (86,455 | ) | $ | (82,411 | ) |
The Company accounts for income taxes using an asset and liability approach which generally requires the recognition of deferred income tax assets and liabilities based on the expected future income tax consequences of events that have previously been recognized in the Company’s financial statements or tax returns. In addition, a valuation allowance is recognized if it is more likely than not that some or all of the deferred income tax assets will not be realized in the foreseeable future. Deferred income tax assets are reviewed for recoverability based on historical taxable income, the expected reversals of existing temporary differences, tax planning strategies and projections of future taxable income. As a result of this analysis, the Company has provided for a valuation allowance against its net deferred income tax assets as of June 30, 2015 and June 30, 2014.
The Company’s combined effective income tax rate differed from the U.S. federal statutory income rate as follows:
Year ended June 30,
|
||||||||
2015
|
2014
|
|||||||
Income tax expense/(benefit) computed at the U.S. federal statutory rate
|
-34 | % | -34 | % | ||||
Settlement of uncertain tax positions
|
-1 | % | 0 | % | ||||
Foreign tax expense/(benefit)
|
0 | % | -1 | % | ||||
Write-off of expired net operating loss carryforwards
|
68 | % | 0 | % | ||||
Change in valuation allowance
|
-34 | % | 34 | % | ||||
Total
|
-1 | % | -1 | % |
51
Significant components of the Company’s net deferred income tax assets as of June 30, 2015 and June 30, 2014 were as follows:
As of June 30,
|
||||||||
2015
|
2014
|
|||||||
Federal net operating loss carryforwards
|
$ | 11,780,604 | $ | 22,238,624 | ||||
Federal - other
|
2,783,304 | 2,737,404 | ||||||
Wisconsin net operating loss carryforwards
|
1,748,976 | 2,747,275 | ||||||
Australia net operating loss carryforwards
|
1,497,779 | 1,497,779 | ||||||
Deferred income tax asset valuation allowance
|
(17,810,663 | ) | (29,221,082 | ) | ||||
Total deferred income tax assets
|
$ | - | $ | - |
The Company has U.S. federal net operating loss carryforwards of approximately $34.6 million as of June 30, 2015, that expire at various dates between June 30, 2017 and 2034. The Company also has $8.2 million in other federal deferred tax assets comprised of charitable contributions carryforwards and intangible amortization. The Company has U.S. federal research and development tax credit carryforwards of approximately $247,000 as of June 30, 2015 that expire at various dates through June 30, 2033. As of June 30, 2015, the Company has approximately $36.9 million of Wisconsin net operating loss carryforwards that expire at various dates between June 30, 2015 and 2028. As of June 30, 2015, the Company also has approximately $5.0 million of Australian net operating loss carryforwards available to reduce future taxable income of its Australian subsidiaries with an indefinite carryforward period.
52
A reconciliation of the beginning and ending balance of unrecognized income tax benefits is as follows:
As of June 30,
|
||||||||
2015
|
2014
|
|||||||
Beginning balance
|
$ | 196,583 | $ | 193,097 | ||||
Lapses of statutes of limitations
|
$ | (161,344 | ) | $ | - | |||
Effect of foreign currency translation
|
(35,239 | ) | 3,486 | |||||
Ending balance
|
$ | - | $ | 196,583 |
The Company’s issuance of additional shares of common stock has constituted an ownership change under Section 382 of the Internal Revenue Code which places an annual dollar limit on the use of net operating loss (“NOL”) carryforwards and other tax attributes that may be utilized in the future. The calculation of the annual limitation of usage is based on a percentage of the equity value immediately after any ownership change. The annual amount of tax attributes that may be utilized after the change in ownership is limited. Previous issuances of additional shares of common stock also resulted in ownership changes and the annual amount of tax attributes from previous years is limited as well. The estimated U.S. federal net operating loss carryforward expected to expire due to the Section 382 limitation is $44.5 million and the estimated state net operating losses expected to expire due to the limitation is $28.2 million. The net operating loss deferred tax assets reflect this limitation.
NOTE 16 – SUBSEQUENT EVENTS
Solar Power, Inc.
On July 13, 2015, we entered into a Securities Purchase Agreement (the “Purchase Agreement”) with Solar Power, Inc., a California corporation (“SPI”) pursuant to which we sold to SPI for an aggregate purchase price of $33,390,000 a total of (i) 8,000,000 shares (the “Purchased Common Shares”) of common stock and (ii) 28,048 shares (the “Purchased Preferred Shares”) of Series C Convertible Preferred Stock which are convertible, subject to the completion of projects under our supply agreement with SPI (as described below), into a total of up to 42,000,600 shares of Common Stock. The aggregate purchase price for the Purchased Common Shares was based on a purchase price per shares of $0.6678 and the aggregate purchase price for the Purchased Preferred Shares was determined based on price of $0.6678 per common share equivalent. Pursuant to the purchase agreement, SPI was also issued a warrant to purchase 50,000,000 shares of Common Stock for an aggregate purchase price of $36,729,000 (the “Warrant”).
The Company also entered into a supply agreement with SPI pursuant to which the Company will sell and SPI will purchase certain products and services offered by the Company from time to time, including certain energy management system solutions for solar projects (the “Supply Agreement”).
The Purchased Preferred Shares were sold for $1,000 per share and are convertible at a conversion price of $0.6678 provided that (A) the first one-fourth (the “Series C-1 Preferred Stock”) of the Purchased Preferred Shares only become convertible upon the completion of five megawatts worth of solar projects in accordance with the Supply Agreement (the “Projects”), (B) the second one-fourth (the “Series C-2 Preferred Stock”) only become convertible upon the completion of 15 megawatts worth of Projects, (C) the third one-fourth (the “Series C-3 Preferred Stock”) only become convertible upon the completion of 25 megawatts worth of Projects, and (D) the last one-fourth (the “Series C-4 Preferred Stock”) only become convertible upon the completion of 40 megawatts worth of Projects. The Warrant represents the right to acquire 50,000,000 shares of Common Stock at an exercise price equal to $0.7346. The Warrant only becomes exercisable upon the completion of 40 megawatts worth of Projects.
The Company also entered into a form of governance agreement with SPI (the “Governance Agreement”) pursuant to which SPI is entitled to nominate one director to the Company’s board of directors for so long as SPI holds at least 10,000 Purchased Preferred Shares or 25 million of Common Stock or Common Stock equivalents (the “Requisite Shares”). Additionally, for so long as the Purchaser holds the Requisite Shares (1) following the time at which the Series C-2 Preferred Stock shall have become convertible in full, the Purchaser shall be entitled to nominate a total of two Directors to the Board and (2) following the time at which the Series C-3 Preferred Stock shall have convertible in full, the Purchaser shall be entitled to nominate a total of three directors.
53
Corporate Name Change
Effective August 17, 2015, ZBB Energy Corporation (NYSE MKT: ZBB) changed the company name to EnSync, Inc. (NYSE MKT: ESNC). The Company will be doing business as EnSync Energy Systems.
Holu Energy LLC
On August 17, 2015, Holu Energy LLC was established as a majority owned entity of EnSync, Inc. The entity is based in Honolulu, Hawaii and is dedicated to the development of energy projects and related equipment sales.
Item 9. CHANGES IN AND DISAGREEMENTS WITH ACCOUNTANTS ON ACCOUNTING AND FINANCIAL DISCLOSURE
Not applicable.
Item 9A. CONTROLS AND PROCEDURES
Evaluation of Disclosure Controls and Procedures
We maintain disclosure controls and procedures that are designed to ensure that information required to be disclosed in our reports filed or submitted under the Securities Exchange Act of 1934, as amended (Exchange Act), is recorded, processed, summarized and reported within the time periods specified in SEC rules and forms. Our disclosure controls and procedures include, without limitation, controls and procedures designed to ensure that information required to be disclosed in our reports filed under the Exchange Act is accumulated and communicated to management as appropriate to allow timely decisions regarding required disclosures. There are inherent limitations to the effectiveness of any system of disclosure controls and procedures, including the possibility of human error and the circumvention or overriding of the controls and procedures. Accordingly, even effective disclosure controls and procedures can only provide reasonable assurance of achieving their control objectives, and management necessarily is required to use its judgment in evaluating the cost-benefit relationship of possible controls and procedures.
An evaluation was carried out under the supervision and with the participation of the Company’s management, including the Chief Executive Officer (CEO) and Vice President of Finance, of the effectiveness of our disclosure controls and procedures as of the end of the period covered by this report as defined in Exchange Act Rule 13a-15(e) and Rule 15d-15(e). Based on that evaluation, the CEO and Vice President of Finance have concluded that, as of the end of the period covered by this report, the Company’s disclosure controls and procedures are effective in ensuring that information required to be disclosed in our Exchange Act reports is (1) recorded, processed, summarized and reported in a timely manner, and (2) accumulated and communicated to our management, including the our CEO and Vice President of Finance, as appropriate, to allow timely decisions regarding required disclosure.
Management’s Report on Internal Control over Financial Reporting
Our management is responsible for establishing and maintaining adequate internal controls over financial reporting (as defined in Exchange Act Rules 13a-15(f) and 15d-15(f)). Under the supervision and with the participation of our management, including our CEO and Vice President of Finance, we conducted an evaluation of the effectiveness of our internal controls over financial reporting based on the framework in Internal Controls – Integrated Framework issued by the Committee of Sponsoring Organizations of the Treadway Commission (2013 framework). Based on our evaluation under the framework in Internal Control – Integrated Framework, our management concluded that our internal controls over financial reporting were effective as of June 30, 2015. The Company’s internal control over financial reporting is designed to provide reasonable assurances regarding the reliability of financial reporting and the preparation of the financial statements of the Company to conform with accounting principles generally accepted in the United States of America. Because of its inherent limitations, internal control over financial reporting may not prevent or detect all misstatements of fraud. Also, projections of any evaluation of effectiveness to future periods are subject to the risk that controls may become inadequate because of changes in conditions, or because the degree of compliance with the policies or procedures may deteriorate.
This annual report does not include an attestation report of the Company’s registered public accounting firm regarding internal control over financial reporting. Management’s report was not subject to attestation by the Company’s registered public accounting firm pursuant to SEC rules adopted in conformity with the Dodd-Frank Wall Street Reform and Consumer Protection Act of 2010.
54
Changes in Internal Control over Financial Reporting
There were no changes in our internal control over financial reporting (as defined in Exchange Act Rules 13a-15(f) and 15d-15(f)) that occurred during the year ended June 30, 2015 that have materially affected, or are reasonably likely to materially affect, our internal control over financial reporting.
Item 9B. OTHER INFORMATION
Not applicable
55
Item 10. DIRECTORS, EXECUTIVE OFFICERS AND CORPORATE GOVERNANCE
The information required under this item is set forth in the Company’s Definitive Proxy Statement relating to the Company’s 2015 annual meeting of shareholders to be held on November 17, 2015 and is incorporated herein by reference.
Item 11. EXECUTIVE COMPENSATION
The information required under this item is set forth in the Company’s Definitive Proxy Statement relating to the Company’s 2015 annual meeting of shareholders to be held on November 17, 2015 and is incorporated herein by reference.
Item 12. SECURITY OWNERSHIP OF CERTAIN BENEFICIAL OWNERS AND MANAGEMENT AND RELATED STOCKHOLDER MATTERS
The information required under this item is set forth in the Company’s Definitive Proxy Statement relating to the Company’s 2015 annual meeting of shareholders to be held on November 17, 2015 and is incorporated herein by reference.
Item 13. CERTAIN RELATIONSHIPS AND RELATED TRANSACTIONS, AND DIRECTOR INDEPENDENCE
The information required under this item is set forth in the Company’s Definitive Proxy Statement relating to the Company’s 2015 annual meeting of shareholders to be held on November 17, 2015 and is incorporated herein by reference.
Item 14. PRINCIPAL ACCOUNTING FEES AND SERVICES
The information required under this item is set forth in the Company’s Definitive Proxy Statement relating to the Company’s 2015 annual meeting of shareholders to be held on November 17, 2015 and is incorporated herein by reference.
56
Item 15. EXHIBITS AND FINANCIAL STATEMENT SCHEDULES
The following financial statements are included in Item 8 of this Annual Report:
Report of Independent Registered Public Accounting Firm
Consolidated Balance Sheets as of June 30, 2015 and 2014
Consolidated Statements of Operations for the Years ended June 30, 2015 and 2014
Consolidated Statements of Comprehensive Loss for the Years ended June 30, 2015 and 2014
Consolidated Statements of Changes in Equity for the Years ended June 30, 2015 and 2014
Consolidated Statements of Cash Flows for the Years ended June 30, 2015 and 2014
Notes to the Consolidated Financial Statements
Financial Statement Schedules
Financial statement schedules have been omitted because they either are not applicable or the required information is included in the consolidated financial statements or notes thereto.
Exhibits
The Exhibit Index immediately preceding the exhibits required to be filed with this report is incorporated herein by reference.
57
Pursuant to the requirements of the Section 13 or 15(d) of the Securities Exchange Act of 1934, the registrant has duly caused this Form 10-K Annual Report to be signed on its behalf by the undersigned on September 28, 2015, thereunto duly authorized.
ENSYNC, INC. | |
By: /s/ Bradley L. Hansen
Name: Bradley L. Hansen
Title: Chief Executive Officer
and President and Director
(Principal Executive Officer)
|
|
By: /s/ Dilek Wagner
Name: Dilek Wagner
Title: Vice President of Finance
(Principal Financial Officer)
|
58
Pursuant to the requirements of the Securities Exchange Act of 1934, this Form 10-K Annual Report has been signed below by the following persons on behalf of the registrant and in the capacities and on the dates indicated.
Position | Date | |||
/s/ Bradley L. Hansen | ||||
Bradley L. Hansen |
Chief Executive Officer and President
(Principal Executive Officer) and Director
|
September 28, 2015
|
||
/s/ Dilek Wagner | ||||
Dilek Wagner |
Vice President of Finance
(Principal Financial Officer and Principal Accounting Officer)
|
September 28, 2015 | ||
/s/ Paul F. Koeppe | ||||
Paul F. Koeppe | Chairman and Director | September 28, 2015 | ||
/s/ Eric C. Apfelbach | ||||
Eric C. Apfelbach | Vice Chairman and Director | September 28, 2015 | ||
/s/ Richard A. Abdoo | ||||
Richard A. Abdoo | Director | September 28, 2015 | ||
/s/ Manfred E. Birnbaum | ||||
Manfred E. Birnbaum | Director | September 28, 2015 | ||
/s/ James H. Ozanne | ||||
James H. Ozanne | Director | September 28, 2015 | ||
/s/ Theodore Stern | ||||
Theodore Stern | Director | September 28, 2015 | ||
/s/ Hoong Khoeng Cheong | ||||
Hoong Khoeng Cheong | Director |
September 28, 2015
|
59
Exhibit No.
|
Description
|
Incorporated by Reference to
|
|
Articles of Incorporation of EnSync, Inc., as amended
|
|||
3.2
|
Certificate of Designation of Preferences, Rights and Limitations of Series B Convertible Stock
|
Incorporated by reference to Exhibit 4.1 to the Company’s Current Report on Form 8-K filed on September 27, 2013
|
|
3.3
|
Certificate of Designation of Preferences, Rights and Limitations of Series C Convertible Preferred Stock
|
Incorporated by reference to Exhibit 4.1 to the Company’s Current Report on Form 8-K filed on July 14, 2015
|
|
Amended and Restated By-laws of EnSync, Inc. (as of November 4, 2009)
|
|||
Form of Stock Certificate
|
|||
4.2
|
Form of Common Stock Purchase Warrant
|
Incorporated by reference to the Company’s Report on Form 8-K filed on August 14, 2009
|
|
4.3
|
Form of Warrant
|
Incorporated by reference to the Company’s Report on Form 8-K filed on March 9, 2010
|
|
4.4
|
Form of Underwriter Warrant
|
Incorporated by reference to the Company’s Registration Statement on Form S-1 filed on April 10, 2012
|
|
4.5
|
Form of Warrant
|
Incorporated by reference to Exhibit 10.6 to the Company’s Current Report on Form 8-K filed on May 2, 2012
|
|
4.6
|
Form of Warrant
|
Incorporated by reference to Exhibit 4.2 to the Company’s Current Report on Form 8-K filed on September 27, 2013
|
|
4.7
|
Form of Warrant
|
Incorporated by reference to Exhibit 4.2 to the Company’s Current Report on Form 8-K filed on April 17, 2015
|
|
10.1*
|
2002 Stock Option Plan of ZBB Energy Corporation
|
Incorporated by reference to the Company’s Registration Statement on Form S-8 filed on April 16, 2008
|
|
10.2*
|
2005 Employee Stock Option Scheme of ZBB Energy Corporation
|
Incorporated by reference to the Company’s Registration Statement on Form SB-2 filed on October 27, 2006
|
|
10.3*
|
2007 Equity Incentive Plan of ZBB Energy Corporation
|
Incorporated by reference to the Company’s Registration Statement on Form S-8 filed on April 16, 2008
|
|
10.4*
|
Director Nonstatutory Stock Option Agreement by and between the Company and Paul F. Koeppe dated as of November 2, 2009
|
Incorporated by reference to the Company’s Report on Form 8-K filed on November 4, 2009
|
60
10.5*
|
Nonstatutory Stock Option Agreement dated January 7, 2010 by and between the Company and Eric C. Apfelbach (performance-based)
|
Incorporated by reference to the Company’s Quarterly Report on Form 10-Q for the quarter ended December 31, 2009
|
|
10.6*
|
Nonstatutory Stock Option Agreement dated January 7, 2010 by and between the Company and Eric C. Apfelbach (time-based)
|
Incorporated by reference to the Company’s Quarterly Report on Form 10-Q for the quarter ended December 31, 2009
|
|
10.7*
|
2010 Omnibus Long-Term Incentive Plan
|
Incorporated by reference to Appendix A attached to the Company’s Definitive Proxy Statement filed on September 24, 2010
|
|
10.8
|
Amendment No. 1 to 2010 Omnibus Long-Term Incentive Plan
|
Incorporated by reference to Appendix A attached to the Company’s Definitive Proxy Statement filed on September 25, 2012
|
|
10.9*
|
2010 Omnibus Long-Term Incentive Plan Form Stock Option Award Agreement
|
Incorporated by reference to the Company’s Registration Statement on Form S-8 filed on January 31, 2010
|
|
10.10*
|
2010 Omnibus Long-Term Incentive Plan Form Restricted Stock Unit Award Agreement
|
Incorporated by reference to the Company’s Registration Statement on Form S-8 filed on January 31, 2010
|
|
10.11
|
Collaboration Agreement between the Company and Honam Petrochemical Corporation dated April 8, 2011
|
Incorporated by reference to Exhibit 10.32 to the Company’s Annual Report on Form 10-K for the year ended June 30, 2011
|
|
10.12
|
Joint Venture Agreement of Anhui Meineng Store Energy Co., Ltd. by and between ZBB PowerSav Holdings Limited and Anhui Xinrui Investment Co., Ltd, dated August 30, 2011
|
Incorporated by reference to Exhibit 10.1 to the Company’s Quarterly Report on Form 10-Q for the quarter ended September 30, 2011
|
|
10.13
|
Limited Liability Company Agreement of ZBB PowerSav Holdings Limited by and between ZBB Cayman Corporation and PowerSav, Inc., dated August 30, 2011
|
Incorporated by reference to Exhibit 10.2 to the Company’s Quarterly Report on Form 10-Q for the quarter ended September 30, 2011
|
|
10.14
|
Anhui Meineng Store Energy Co., Ltd. Supplemental Agreement to the Joint Venture Agreement by and between ZBB PowerSav Holdings Limited and Anhui Xinlong Investment Management Co., Ltd, dated November 15, 2011
|
Incorporated by reference to Exhibit 10.1 to the Company’s Quarterly Report on Form 10-Q for the quarter ended December 31, 2011
|
|
10.15
|
License Agreement by and between ZBB PowerSav Holdings Ltd. and Anhui Meineng Store Energy Co., Ltd., dated November 11, 2011
|
Incorporated by reference to Exhibit 10.2 to the Company’s Quarterly Report on Form 10-Q for the quarter ended December 31, 2011
|
|
10.16
|
Management Services Agreement by and between ZBB PowerSav Holdings Ltd. and Anhui Meineng Store Energy Co., Ltd., dated November 11, 2011
|
Incorporated by reference to Exhibit 10.3 to the Company’s Quarterly Report on Form 10-Q for the quarter ended December 31, 2011
|
61
10.17
|
Form of Securities Purchase Agreement
|
Incorporated by reference to Exhibit 10 to the Company’s Current Report on Form 8-K filed on September 27, 2013
|
|
10.18*
|
Director Compensation Policy, adopted November 6, 2013
|
Incorporated by reference to Exhibit 10.24 to the Company’s Annual Report on Form 10-K for the year ended June 30, 2014.
|
|
10.19
|
First Amendment to License Agreement between ZBB PowerSav Holdings Ltd. and Anhui Meineng Store Energy Co. Ltd., dated December 3, 2013
|
Incorporated by reference to Exhibit 10.1 to the Company’s Quarterly Report on Form 10-Q for the quarter ended March 31, 2014
|
|
10.20
|
Research and Development Agreement between the Company and Lotte Chemical Corporation, dated December 16, 2013
|
Incorporated by reference to Exhibit 10.1 to the Company’s Quarterly Report on Form 10-Q for the quarter ended December 31, 2013
|
|
10.21
|
Amended License Agreement between the Company and Lotte Chemical Corporation, dated December 16, 2013
|
Incorporated by reference to Exhibit 10.2 to the Company’s Quarterly Report on Form 10-Q for the quarter ended December 31, 2013
|
|
10.22
|
Amendment to Collaboration Agreement between the Company and Lotte Chemical Corporation, dated December 16, 2013
|
Incorporated by reference to Exhibit 10.3 to the Company’s Quarterly Report on Form 10-Q for the quarter ended December 31, 2013
|
|
10.23*
|
Professional Services Agreement between Jeff Reichard and the Company, dated February 7, 2014
|
Incorporated by reference to Exhibit 10.2 to the Company’s Quarterly Report on Form 10-Q for the quarter ended March 31, 2014
|
|
10.24*
|
Employment Agreement between the Company and Dilek Wagner, dated February 2, 2014
|
Incorporated by reference to Exhibit 10.3 to the Company’s Quarterly Report on Form 10-Q for the quarter ended March 31, 2014
|
|
10.25*
|
Employment Agreement between the Company and Bradley Hansen, dated May 19, 2014
|
Incorporated by reference to Exhibit 10.31 to the Company’s Annual Report on Form 10-K for the year ended June 30, 2014
|
|
10.26*
|
Form of Nonstatutory Option Agreement issued on May 19, 2014 to Bradley Hansen
|
Incorporated by reference to Exhibit 10.32 to the Company’s Annual Report on Form 10-K for the year ended June 30, 2014
|
62
10.27*
|
Amended Separation Agreement between the Company and Charles Stankiewicz, dated May 19, 2014
|
Incorporated by reference to Exhibit 10.33 to the Company’s Annual Report on Form 10-K for the year ended June 30, 2014
|
|
10.28*
|
Amended and Restated Employment Agreement between the Company and Eric Apfelbach, dated September 30, 2014
|
Incorporated by reference to Exhibit 10.1 to the Company’s Current Report on Form 8-K filed on October 3, 2014
|
|
10.29*
|
Amended and Restated Employment Agreement between the Company and Kevin Dennis, dated September 30, 2014
|
Incorporated by reference to Exhibit 10.2 to the Company’s Current Report on Form 8-K filed on October 3, 2014
|
|
10.30*
|
Restricted Stock Unit Award Agreement between the Company and Bradley Hansen, dated July 15, 2014
|
Incorporated by reference to Exhibit 10.1 to the Company’s Quarterly Report on Form 10-Q for the quarter ended September 30, 2014
|
|
10.31
|
Amended and Restated Management Services Agreement between Anhui Meineng Store Energy Co., Ltd. and ZBB Powersav Holdings Limited, dated July 1, 2014
|
Incorporated by reference to Exhibit 10.2 to the Company’s Quarterly Report on Form 10-Q for the quarter ended September 30, 2014
|
|
10.32*
|
Amended and Restated Employment Agreement between the Company and Daniel Nordloh, dated September 30, 2014
|
Incorporated by reference to Exhibit 10.5 to the Company’s Quarterly Report on Form 10-Q for the quarter ended September 30, 2014
|
|
10.33*
|
Amended and Restated Employment Agreement between the Company and Anthony Siebert, dated September 30, 2014
|
Incorporated by reference to Exhibit 10.6 to the Company’s Quarterly Report on Form 10-Q for the quarter ended September 30, 2014
|
|
10.34*
|
Amendment No. 2 to the 2010 Omnibus Long-Term Incentive Plan
|
Incorporated by reference to Appendix A attached to the Company’s Definitive Proxy Statement filed on October 9, 2014
|
|
10.35*
|
Amendment No. 1 to the 2012 Non-Employee Director Equity Compensation Plan
|
Incorporated by reference to Appendix B attached to the Company’s Definitive Proxy Statement filed on October 9, 2014
|
|
10.36
|
Securities Purchase Agreement between the Company and Solar Power, Inc., dated April 17, 2015
|
Incorporated by reference to Exhibit 10.1 to the Company’s Current Report on Form 8-K filed on April 17, 2015
|
|
10.37
|
Form of Supply Agreement
|
Incorporated by reference to Exhibit 10.2 to the Company’s Current Report on Form 8-K filed on April 17, 2015
|
|
10.38
|
Governance Agreement between the Company and Solar Power, Inc., dated July 13, 2015
|
Incorporated by reference to Exhibit 10.2 to the Company’s Current Report on Form 8-K filed on July 14, 2015
|
|
10.39*
|
Amendment to Employment Agreement between the Company and Bradley Hansen, dated July 13, 2015
|
Incorporated by reference to Exhibit 10.3 to the Company’s Current Report on Form 8-K filed on July 14, 2015
|
63
Subsidiaries of EnSync, Inc.
|
||
Consent of Baker Tilly Virchow Krause, LLP
|
||
Certification of Principal Executive Officer pursuant to Section 302 of the Sarbanes-Oxley Act of 2002
|
||
Certification of Principal Financial and Accounting Officer pursuant to Section 302 of the Sarbanes-Oxley Act of 2002
|
||
Certification of Principal Executive Officer pursuant to 18 U.S.C. Section 1350, as adopted pursuant to Section 906 of the Sarbanes-Oxley Act of 2002
|
||
Certification of Principal Financial Officer pursuant to 18 U.S.C. Section 1350, as adopted pursuant to Section 906 of the Sarbanes-Oxley Act of 2002
|
||
101
|
Interactive Data Files
|
64