Attached files
file | filename |
---|---|
EX-32 - EXHIBIT 32 - Northrop Grumman Innovation Systems, Inc. | oa-ex32x20171231.htm |
EX-31.2 - EXHIBIT 31.2 - Northrop Grumman Innovation Systems, Inc. | oa-ex312x20171231.htm |
EX-31.1 - EXHIBIT 31.1 - Northrop Grumman Innovation Systems, Inc. | oa-ex311x20171231.htm |
EX-23.2 - EXHIBIT 23.2 - Northrop Grumman Innovation Systems, Inc. | oa-ex232x20171231.htm |
EX-23.1 - EXHIBIT 23.1 - Northrop Grumman Innovation Systems, Inc. | oa-ex231x20171231.htm |
EX-21 - EXHIBIT 21 - Northrop Grumman Innovation Systems, Inc. | oa-ex21x20171231.htm |
EX-10.14.7 - EXHIBIT 10.14.7 - Northrop Grumman Innovation Systems, Inc. | oa-ex10147x20171231.htm |
EX-10.13.7 - EXHIBIT 10.13.7 - Northrop Grumman Innovation Systems, Inc. | oa-ex10137x20171231.htm |
EX-10.13.5 - EXHIBIT 10.13.5 - Northrop Grumman Innovation Systems, Inc. | oa-ex10135x20171231.htm |
UNITED STATES
SECURITIES AND EXCHANGE COMMISSION
Washington, D.C. 20549
FORM 10-K
ý | ANNUAL REPORT PURSUANT TO SECTION 13 OR 15(d) OF THE SECURITIES EXCHANGE ACT OF 1934 | |
For the year ended December 31, 2017 | ||
OR | ||
o | TRANSITION REPORT PURSUANT TO SECTION 13 OR 15(d) OF THE SECURITIES EXCHANGE ACT OF 1934 | |
Commission file number 1-10582
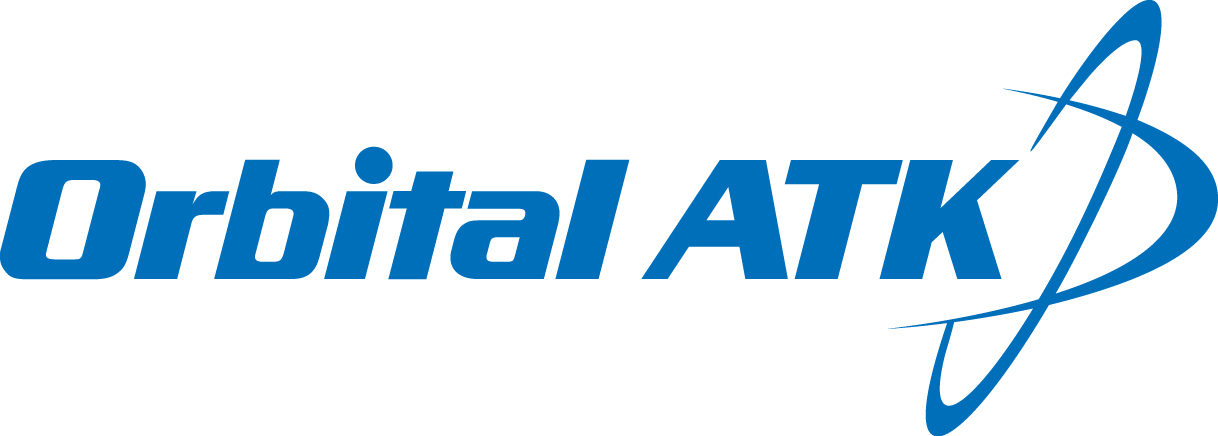
ORBITAL ATK, INC.
(Exact name of Registrant as specified in its charter)
Delaware (State or other jurisdiction of incorporation or organization) | 41-1672694 (I.R.S. Employer Identification No.) | |
45101 Warp Drive | ||
Dulles, Virginia | 20166 | |
(Address of principal executive offices) | (Zip Code) |
Registrant's telephone number, including area code: (703) 406-5000
Securities registered pursuant to Section 12(b) of the Act:
Title of each class | Name of each exchange on which registered | |
Common Stock, par value $.01 | New York Stock Exchange |
Securities registered pursuant to Section 12(g) of the Act: None.
____________________________________________________________________________
Indicate by check mark if the registrant is a well-known seasoned issuer, as defined in Rule 405 of the Securities Act. Yes o No ý
Indicate by check mark if the registrant is not required to file reports pursuant to Section 13 or Section 15(d) of the Act. Yes o No ý
Indicate by check mark whether the registrant: (1) has filed all reports required to be filed by Section 13 or 15(d) of the Securities Exchange Act of 1934 during the preceding 12 months (or for such shorter period that the registrant was required to file such reports), and (2) has been subject to such filing requirements for the past 90 days. Yes ý No o
Indicate by check mark whether the registrant has submitted electronically and posted on its corporate Web site, if any, every Interactive Data File required to be submitted and posted pursuant to Rule 405 of Regulation S-T (§232.405 of this chapter) during the preceding 12 months (or for such shorter period that the registrant was required to submit and post such files). Yes ý No o
Indicate by check mark if disclosure of delinquent filers pursuant to Item 405 of Regulation S-K is not contained herein, and will not be contained, to the best of registrant's knowledge, in definitive proxy or information statements incorporated by reference in Part III of this Form 10-K or any amendment to this Form 10-K. o
Indicate by check mark whether the registrant is a large accelerated filer, an accelerated filer, a non-accelerated filer, a smaller reporting company, or an emerging growth company. See the definitions of "large accelerated filer," "accelerated filer," "smaller reporting company" and "emerging growth company" in Rule 12b-2 of the Exchange Act.
Large Accelerated Filer ý | Accelerated Filer o | Non-Accelerated Filer o (Do not check if a smaller reporting company) | Smaller Reporting Company o | Emerging Growth Company o |
If an emerging growth company, indicate by check mark if the registrant has elected not to use the extended transition period for complying with any new or revised financial accounting standards provided pursuant to Section 13(a) of the Exchange Act. o
Indicate by check mark whether the registrant is a shell company (as defined in Rule 12b-2 of the Exchange Act). Yes o No ý
At June 30, 2017, the aggregate market value of the registrant's voting common stock held by non-affiliates was approximately $5.611 billion (based upon the closing price of the common stock on the New York Stock Exchange on June 30, 2017).
At February 15, 2018, there were 57,798,076 shares of the registrant's voting common stock outstanding.
TABLE OF CONTENTS
Page | ||
PART I
EXPLANATORY NOTE REGARDING THIS ANNUAL REPORT
In March 2015, we changed our fiscal year from the period beginning on April 1 and ending on March 31 to the period beginning on January 1 and ending on December 31. We refer in this report to the nine-month period beginning on April 1, 2015 and ending on December 31, 2015 as the "2015 transition period." All fiscal years after December 31, 2015 are for the calendar year ended December 31. We sometimes refer in this report to the period beginning January 1, 2017 and ending on December 31, 2017 as "calendar 2017" or "2017" and the period beginning on January 1, 2016 and ending on December 31, 2016 as "calendar 2016" or "2016." We refer in this report to the period beginning on April 1, 2014 and ending on March 31, 2015 as “fiscal 2015” and the period beginning on April 1, 2013 and ending on March 31, 2014 as “fiscal 2014.”
ITEM 1. BUSINESS
Orbital ATK, Inc. (the "Company," "we," "us" or "our") is an aerospace and defense systems company and supplier of related products to the U.S. Government, allied nations, prime contractors and other customers. Our main products include launch vehicles and related propulsion systems; satellites and associated components and services; composite aerospace structures; tactical missiles, subsystems and defense electronics; and precision weapons, armament systems and ammunition. We are headquartered in Dulles, Virginia and have operating locations throughout the United States. We were incorporated in Delaware in 1990.
On September 17, 2017, the Company entered into an Agreement and Plan of Merger (the "Merger Agreement") with Northrop Grumman Corporation ("Northrop Grumman") and Neptune Merger, Inc., a wholly owned subsidiary of Northrop Grumman ("Sub"), pursuant to which Northrop Grumman will acquire the Company for a purchase price of $134.50 per share in cash (the "Merger").
Closing of the Merger is expected to occur during the first half of 2018, subject to customary closing conditions and obtaining required regulatory approvals. At the effective time of the Merger, each outstanding share of the Company’s common stock, other than shares owned by the Company, Northrop Grumman or Sub (which will be canceled) and appraisal shares, will be converted into the right to receive $134.50 in cash, without interest and less any applicable withholding taxes.
On February 9, 2015, we completed the spin-off and distribution (the "Distribution") of our former Sporting Group to our stockholders as a new public company called Vista Outdoor Inc. ("Vista Outdoor"). Immediately following the Distribution of our former Sporting Group, we combined with Orbital Sciences Corporation ("Orbital") through the merger of a company subsidiary with Orbital (the "Orbital-ATK Merger").
We conduct business in three segments: Flight Systems Group, Defense Systems Group and Space Systems Group, which are described in greater detail below. These Groups are further comprised of smaller operating units that we refer to as "divisions."
Flight Systems Group is well-positioned in its markets, as follows:
• | leading provider of small- and medium-class space launch vehicles for civil, military and commercial missions, |
• | major supplier of interceptor boosters and target vehicles for missile defense applications, |
• | premier producer of solid rocket propulsion systems and specialty energetic products, and |
• | manufacturer of composite structures for commercial and military aircraft and launch vehicles. |
Defense Systems Group is also well-positioned in its markets, as follows:
• | leader in propulsion and controls for air-, sea- and land-based tactical missiles and missile defense interceptors, as well as fuzing and warheads for tactical missiles and munitions, |
• | supplier of advanced defense electronics for next-generation strike weapon systems, missile-warning and aircraft survivability systems and special-mission aircraft, |
1
• | leading producer of medium- and large-caliber ammunition, medium-caliber gun systems and precision munitions guidance kits, and |
• | leading U.S. producer of small-caliber ammunition. |
Space Systems Group is also well-positioned in its markets, as follows:
• | leading provider of small- and medium-class commercial satellites used for global communications and high-resolution earth imaging, |
• | leading provider of small- and medium-class spacecraft that perform scientific research and national security missions for government customers, |
• | provider of commercial cargo delivery to the International Space Station ("ISS") and developer of advanced space systems, and |
• | premier provider of spacecraft components and subsystems and specialized technical services. |
Sales; income from continuing operations, before interest, income taxes and noncontrolling interest; and other financial data for each segment for the year ended December 31, 2017, the year ended December 31, 2016 and the nine months ended December 31, 2015, respectively, are set forth in Note 18, Operating Segment Information, to the consolidated financial statements included in Part II, Item 8, "Financial Statements and Supplementary Data" of this report.
Flight Systems Group
Flight Systems Group develops launch vehicles that are used as small- and medium-class space launch vehicles to place satellites into earth orbit and escape trajectories, interceptor and target vehicles for missile defense systems and suborbital launch vehicles that place payloads into a variety of high-altitude trajectories. The Group also develops and produces medium- and large-class rocket propulsion systems for human and cargo launch vehicles, strategic missiles, missile defense interceptors and target vehicles. Additionally, the Group operates in the military and commercial aircraft and launch structures markets.
The following is a description of the divisions within Flight Systems Group:
Launch Vehicles Division
The Launch Vehicles division includes both small- and medium-class rockets for government, civil and commercial payloads. Our innovative Pegasus® rocket is launched from our "Stargazer" L-1011 carrier aircraft and has proven to be the small space-launch workhorse for U.S. Government and commercial customers. Our Taurus launch vehicle combines our Pegasus upper-stage motors with a commercially-provided first stage propulsion system for increased performance. Our Minotaur I, IV and V rockets combine decommissioned Minuteman and Peacekeeper rocket motors with our proven upper stage motors, avionics and fairings to provide increased lifting capacity for government-sponsored payloads.
The division's Antares rocket is a two-stage vehicle (with optional third stage) that provides low-earth orbit launch capability for payloads weighing up to 7,000 kg. The Antares rocket has been used in the execution of our Commercial Resupply Services ("CRS") contract with the National Aeronautics and Space Administration ("NASA") to deliver cargo to the ISS. The Antares design has been upgraded with RD-181 first stage engines to provide greater payload performance and increased reliability, and the reconfigured Antares rocket successfully flew in 2016 and 2017, with two launches scheduled in 2018, both in connection with the CRS-1 contract. Additional missions through 2024 under the CRS-1 contract and the follow-on CRS-2 contract are planned.
The division also is an industry-leading provider of suborbital launch vehicles for the nation's missile defense systems for the U.S. Missile Defense Agency, the U.S. Air Force, Army and Navy, and allied nations. Additionally, the division is the sole provider of interceptor boosters for the U.S. Missile Defense Agency's Ground-based Midcourse Defense ("GMD") system designed to intercept and destroy long-range enemy missiles. We are also a primary supplier of highly-reliable target vehicles that serve as "threat simulators" to provide high-fidelity facsimiles of enemy missile threats in the testing and verification of missile defense systems.
2
Propulsion Systems Division
The Propulsion Systems division is the development and production center for solid rocket motors for NASA's current and planned human spaceflight programs, including the Space Launch System ("SLS") heavy lift vehicle and the launch abort system motor for the Orion® crew capsule that is designed to safely pull the crew capsule away from the launch vehicle in the event of an emergency during launch.
The division also produces medium-class solid rocket motors for the U.S. Navy's Trident II Fleet Ballistic Missile program and conducts solid rocket propulsion sustainment activities for the U.S. Air Force's Minuteman III Intercontinental Ballistic Missile. These two programs provide the backbone of the United States' strategic deterrence program. Additional solid rocket motors being produced by the division include Graphite Epoxy Motors for the Delta IV, Atlas and Vulcan, Orion motors for our Pegasus and Minotaur launch vehicles and U.S. Missile Defense Agency targets, and CASTOR® motors for our Antares rocket and Taurus rocket. The division supplies Orion motors for all three stages of the GMD system, as well as other Orbital ATK launch vehicles and is in the process of developing the Next Generation Launcher for the U.S. Government. In addition, the division produces advanced flares and decoys that provide illumination for search and rescue missions and countermeasures against missile attacks.
Aerospace Structures Division
The Aerospace Structures division is a provider of advanced composite aircraft structures for military and commercial aircraft manufacturers, using highly automated composite fabrication techniques, including automated fiber placement and stiffener forming processes. The division provides a wide variety of composite parts for the F-35 Lightning II Joint Strike Fighter, a fifth-generation fighter aircraft for the U.S. military and its allies. It also provides composite radomes and apertures for a number of military aircraft and provides wing stiffeners for the A400M military transport aircraft. The division provides very large fiber-placed and hand lay-up structures for the Antares, Atlas and Delta launch vehicles, and filament-wound composite cases for solid rocket motors and composite overwrapped pressure vessels.
The division has a commercial aerospace composites center of excellence facility in Clearfield, Utah to support its commercial aerospace customers, including Airbus, Rolls Royce and Boeing. The division is under contract to produce the majority of the composite fuselage stringers and frames for the Airbus A350 XWB wide-body passenger jetliner. Additional major commercial programs include a contract with Rolls Royce to produce the aft fan case for the Trent XWB engine, which is used to power the Airbus A350 aircraft, and a contract to produce composite frames for the Boeing 787-9 and 787-10 commercial aircraft.
Defense Systems Group
Defense Systems Group develops and produces small-, medium- and large-caliber ammunition, precision weapons and munitions, high-performance gun systems, and propellant and energetic materials. It operates the Lake City Army Ammunition Plant in Independence, Missouri and a Naval Sea Systems Command facility in Rocket Center, West Virginia. Defense Systems Group is also a leader in tactical solid rocket motor development and production for a variety of air-, sea- and land-based missile systems. The Group serves a variety of domestic and international customers in the defense and security markets in a prime contractor, partner or supplier role. Defense Systems Group also provides propulsion control systems that support U.S. Missile Defense Agency and NASA programs, airborne missile warning systems, advanced fuzes and defense electronics. The Group produces the U.S. Navy's Advanced Anti-Radiation Guided Missile ("AARGM") and has developed advanced air-breathing propulsion systems and special-mission aircraft for defense applications.
The following is a description of the divisions within Defense Systems Group:
Missile Products Division
The Missile Products division provides customers with high-performance tactical solid rocket motor propulsion for a variety of surface- and air-launched missile systems including Hellfire, Maverick, Advanced Medium-Range Air-to-Air Missile and Sidewinder. The division also produces warheads, fuzing and sensors for various artillery, mortar, grenade and air-dropped weapons, including the Hard Target Void Sensing Fuze. The division produces metal components for various medium-caliber ammunition and 120mm tank ammunition, and also produces specialty composite and ceramic structures used on military platforms. The division provides customers with the third-stage
3
propulsion on the Standard Missile defense interceptor. Additional capabilities include the STAR™ family of satellite orbit insertion motors, high performance rocket boosters and advanced air-breathing propulsion for platforms designed for Mach 3+ flight. It also continues to operate our New River Energetics facility located on the Radford Army Ammunition Plant in Radford, Virginia, which provides load, assembly and pack of medium caliber munitions; and propellants and powders for the canister and commercial markets, individual re-loaders and ammunition manufacturers.
Armament Systems Division
The Armament Systems division is home to our precision weapons and medium- and large-caliber ammunition programs, including advanced precision munition programs. The division is under contract to develop the U.S. Army's new multi-purpose tank round and currently produces the Precision Guidance Kit for 155mm artillery. The division also produces the family of medium-caliber Bushmaster® chain guns and is a global systems designer and producer of medium-caliber ammunition for integrated gun systems. These gun systems are used on a variety of ground combat vehicles, helicopters and naval vessels, including the Bradley Fighting Vehicle, the Light Armored Vehicle, coastal patrol craft and Apache helicopters. New products include a link-fed variant of the Apache gun system for ground and naval applications. Armament Systems also leads Defense Systems Group's international co-production efforts and provides munitions support to allied nations.
Defense Electronics Division
The Defense Electronics division provides customers with advanced capabilities for offensive and defensive electronic warfare and specializes in weaponized airborne intelligence, surveillance and reconnaissance platforms and advanced anti-radiation homing missile systems, special-mission aircraft, missile warning systems and mission support equipment. Key programs include the AARGM missile used by the U.S. Navy and North Atlantic Treaty Organization militaries, and the AAR-47 missile warning system used by U.S. and allied fixed- and rotor-wing aircraft to defeat incoming missile threats. The division also provides special-mission aircraft that integrate sensors, fire control software, gun systems and air-to-ground weapons capability for use in counterinsurgency, border/coastal surveillance and security missions.
Small Caliber Systems Division
The Small Caliber Systems division via operating the Lake City Army Ammunition Plant is the largest producer of small-caliber ammunition in the U.S., covering 5.56, 7.62 and .50 caliber rounds. The division also provides non-NATO ammunition to the U.S. Army for use by allied forces. The division also provides commercial ammunition to Vista Outdoor. Since 2000, the Company has operated and modernized the Lake City Army Ammunition Plant.
Space Systems Group
Space Systems Group offers a broad portfolio of products for commercial, military, scientific and international customers. The Group develops and produces small- and medium- class satellites that are used to enable global and regional communications and broadcasting, conduct space-related scientific research and perform activities related to national security. In addition, the Space Systems Group develops and produces human-rated space systems for earth orbit and deep-space exploration, including delivering cargo to the ISS. This Group is also a provider of spacecraft components and subsystems as well as specialized engineering and operations services to U.S. Government agencies.
The following is a description of the divisions within Space Systems Group:
Satellite Systems Division
The Satellite Systems division designs and produces small- and medium- class satellites used for various activities including: national security space programs, geosynchronous ("GEO") satellites used for global and regional communications/broadcasting, commercial imaging and remote sensing satellites. The division also conducts space-related scientific research, including astrophysics, earth science/remote sensing and heliophysics, interplanetary and other deep-space exploration missions, including the demonstration of new space technologies. In addition, the division designs and manufacturers satellite buses tailored to accommodate a variety of payloads and hosted payloads for various orbits or interplanetary missions.
4
Advanced Programs Division
The Advanced Programs division consists of two main business areas: human space systems and space robotics and logistics. In the human space systems business area, the division provides human-rated space systems for low-earth orbit and deep-space exploration, including cargo missions to the ISS under the CRS-1 and CRS-2 programs using the Cygnus spacecraft. The division is also working in partnership with NASA on various programs, including the Deep Space Gateway, Power Propulsion Element, as well as NextSTEP-2 which focuses on the development of deep space habitat prototypes. In the space robotics and logistics business area, the division is working to develop and build Mission Extension Vehicles to provide in-orbit GEO satellite life extension. Additional areas of focus include space robotics capabilities development to support areas such as in-orbit satellite assembly and repair.
Space Components Division
The Space Components division is a major supplier of satellite mechanical components and structural assemblies for a wide variety of commercial, civil and defense spacecraft. As a leader in the industry, we believe that products manufactured by the division have flown aboard virtually every U.S. satellite built in the last 20 years. The division has strong market positions in spacecraft composite primary and secondary structures, satellite fuel and oxidizer tanks, precision payload structures, solar power arrays, deployable structures and thermal control systems.
Technical Services Division
The Technical Services division provides a full spectrum of cost-effective engineering, manufacturing and program management services to NASA and other civil government and military space agencies. The division also manages high-profile NASA science programs, including its scientific sounding rocket and high altitude balloon activities.
Customers
Our sales have come primarily from contracts with agencies of the U.S. Government and its prime contractors and subcontractors, and from major domestic and international commercial satellite operators, international customers including foreign military sales contracted through the U.S. Government and aircraft manufacturers. As the various U.S. Government customers, including the U.S. Navy, U.S. Army, NASA and the U.S. Air Force, make independent purchasing decisions, we do not generally regard the U.S. Government as one customer. Instead, we view each agency as a separate customer.
5
Sales by customer, as a percentage of total sales, were as follows:
Percentage of Sales | ||||||||
Year Ended | Year Ended | Nine Months Ended | ||||||
December 31, 2017 | December 31, 2016 | December 31, 2015 | ||||||
Sales to: | ||||||||
U.S. Army | 15 | % | 17 | % | 15 | % | ||
U.S. Navy | 11 | 12 | 11 | |||||
U.S. Air Force | 4 | 4 | 4 | |||||
NASA | 22 | 27 | 23 | |||||
Other U.S. Government customers | 21 | 16 | 17 | |||||
Total U.S. Government customers | 73 | 76 | 70 | |||||
Commercial and foreign customers | 27 | 24 | 30 | |||||
Total | 100 | % | 100 | % | 100 | % |
Sales to the U.S. Government and its prime contractors were as follows (in millions):
U.S. Government Sales | Percentage of Sales | |||||
Year ended December 31, 2017 | $ | 3,489 | 73 | % | ||
Year ended December 31, 2016 | $ | 3,368 | 76 | % | ||
Nine months ended December 31, 2015 | $ | 2,359 | 70 | % |
The Company's CRS contracts with NASA, which are reported within its Flight Systems Group and Space Systems Group, comprised 9%, 13% and 10% of total sales in the years ended December 31, 2017 and 2016 and in the 2015 transition period, respectively. No other single contract accounted for more than 10% of the Company's sales in the years ended December 31, 2017 and 2016 or in the 2015 transition period.
Other than the U.S. Government customers listed above, no single customer accounted for more than 10% of our sales in the year ended December 31, 2017, the year ended December 31, 2016 or in the 2015 transition period.
International sales were as follows (in millions):
International Sales | Percentage of Sales | |||||
Year ended December 31, 2017 | $ | 878 | 18 | % | ||
Year ended December 31, 2016 | $ | 778 | 17 | % | ||
Nine months ended December 31, 2015 | $ | 766 | 23 | % |
Sales to foreign governments and other international customers may require approval by the U.S. Department of Defense ("DoD") and the U.S. Department of State or the U.S. Department of Commerce. Our products are sold to U.S. allies directly, as well as through the U.S. Government. During the year ended December 31, 2017, approximately 20% of these sales were in Flight Systems Group, 66% were in Defense Systems Group, and 14% were in Space Systems Group. No sales to an individual country outside the United States accounted for more than 5% of our sales in the year ended December 31, 2017.
Backlog
Firm backlog is the estimated value of contracts for which orders have been recorded, but for which revenue has not yet been recognized. The total amount of firm backlog was approximately $10.2 billion at December 31, 2017 and $9.3 billion at December 31, 2016. Approximately $3.4 billion of firm backlog was not yet funded at December 31, 2017. We expect that approximately 43% of the December 31, 2017 firm backlog will be recognized as revenue in calendar year 2018.
6
Total backlog, which includes firm backlog plus the value of unexercised options, was approximately $16.0 billion at December 31, 2017 and $14.4 billion at December 31, 2016.
Seasonality
Our business is not seasonal.
Competition
We compete against other U.S. and foreign prime contractors and subcontractors, many of which have substantially more resources to deploy than we do in the pursuit of government and industry contracts. Our ability to compete successfully in this environment depends on a number of factors, including the creativity and effectiveness of research and development programs, our ability to offer better program performance than our competitors and/or at a lower cost, our readiness with respect to facilities, equipment and personnel to undertake the programs for which we compete, and our past performance and demonstrated capabilities.
Additional information on the risks related to competition can be found in Item 1A, "Risk Factors" of this report.
We generally face competition from a number of competitors in each business area, although no single competitor competes along all of our segments. Our principal competitors in each of our segments are as follows:
Flight Systems Group: Aerojet-Rocketdyne Holdings, Inc.; Arianespace SA; Coleman Aerospace, a division of Aerojet-Rocketdyne Holdings, Inc.; GKN Aerospace Company; Lockheed Martin Corporation; Space Exploration Technologies Corporation; Spirit Aerosystems Company; United Launch Alliance (a joint venture between Lockheed Martin Corporation and The Boeing Company); and Vought Aircraft, a division of Triumph Aerostructures.
Defense Systems Group: Aerojet-Rocketdyne Holdings, Inc.; BAE Systems; Chemring Group; General Dynamics Corporation; Lockheed Martin Corporation; Nammo AS; Nexter SA; Winchester Ammunition Division of Olin Corporation; Raytheon Company; Rheinmetall AG; and various other international competitors.
Space Systems Group: Airbus Defense and Space; Ball Aerospace and Technologies Corp.; Lockheed Martin Corporation; Maxar Technologies; Millenium Space Systems; Sierra Nevada Corporation; Space Exploration Technologies Corporation; Thales Alenia Space; and The Boeing Company.
Research and Development
We conduct extensive research and development ("R&D") activities. Company-funded R&D is primarily for the improvement of current products and for development of next-generation technology. Customer-funded R&D is comprised primarily of activities we conduct under contracts with the U.S. Government and its prime contractors. R&D expenditures were as follows (in millions):
Company-funded | Customer-funded | ||||||
Year ended December 31, 2017 | $ | 115 | $ | 536 | |||
Year ended December 31, 2016 | $ | 116 | $ | 429 | |||
Nine months ended December 31, 2015 | $ | 83 | $ | 376 |
Raw Materials and Components
We use a broad range of raw materials in manufacturing our products, including aluminum, steel, copper, lead, ammonium perchlorate, graphite fiber, epoxy resins, zinc and adhesives. We monitor the sources from which we purchase raw materials in an attempt to ensure there are adequate supplies to support our operations. We monitor the price of materials, particularly commodity metals like copper, which have fluctuated dramatically over the past several years.
We also use sub-assemblies and instruments in our products and obtain parts and equipment that are used in the production of our products or in the provision of our services from domestic and foreign suppliers and the U.S. Government. Generally, we have not experienced material difficulty in obtaining product components or necessary parts and equipment, and we believe that alternatives to our existing sources of supply are available in most cases.
7
We procure materials and components from a variety of sources. In the case of our U.S. Government contracts, we are often required to purchase from sources approved by the DoD. When our suppliers choose to eliminate certain materials or components we require from their product offering, we attempt to qualify other suppliers or replacement materials to ensure there are no disruptions to our operations.
We rely upon sole-source suppliers for many of our satellite and launch vehicle components, including our liquid-propellant rocket engines and cores. The inability of our current suppliers to provide us with key components could result in significant contract delays, cost increases and loss of revenues due to the time, resources and effort that would be required to develop or adapt other engines or components for use in our products.
Additional information on the risks related to raw materials and components can be found in Item 1A, "Risk Factors" of this report.
Intellectual Property
Although we manufacture various products covered by patents, we do not believe that any single existing patent, license or group of patents is material to our success. We believe that unpatented research, development and engineering skills also make an important contribution to our business. The U.S. Government typically receives royalty-free licenses to inventions made under U.S. Government contracts. Consistent with our policy to protect proprietary information from unauthorized disclosure, we ordinarily require employees to sign confidentiality agreements as a condition of employment.
As many of our products are complex and involve patented and other proprietary technologies, we face a risk of claims alleging that we have infringed upon third-party intellectual property rights. Such claims could result in costly and time-consuming litigation, the invalidation of our intellectual property rights and/or increased licensing costs.
Regulatory Matters
U.S. Governmental Contracts
We are subject to the procurement policies and procedures set forth in the Federal Acquisition Regulation ("FAR"). The FAR governs all aspects of government contracting, including competition and acquisition planning; contracting methods and contract types; contractor qualifications; and acquisition procedures. Every U.S. Government contract contains a list of FAR provisions that must be complied with in order for the contract to be awarded. The FAR provides for regular audits and reviews of contract procurement, performance and administration. Failure to comply with the provisions of the FAR could result in contract termination.
The U.S. Government may terminate its contracts with its suppliers, either for convenience or in the event of a default as a result of our failure to perform under the applicable contract. If a cost-plus contract is terminated for convenience, we are entitled to reimbursement of our approved costs and payment of a total fee proportionate to the percentage of the work completed under the contract. If a fixed-price contract is terminated for convenience, we are entitled to payment for items delivered to and accepted by the U.S. Government, and fair compensation for work performed plus the costs of settling and paying claims by terminated subcontractors, other settlement expenses and a reasonable profit on the costs incurred or committed. If a contract termination is for default, we are paid an amount agreed upon for completed and partially completed products and services accepted by the U.S. Government, and may be liable to the U.S. Government for repayment of any advance payments and progress payments related to the terminated portions of the contract, as well as excess costs incurred by the U.S. Government in procuring undelivered items from another source.
Additional information on the risks related to government contracts can be found in Item 1A,"Risk Factors" of this report.
Laws Relating to Import-Export
We also must comply with U.S. and foreign laws governing the export of munitions and other controlled products and commodities. These include regulations relating to import-export control, exchange controls, the Foreign Corrupt Practices Act and the anti-boycott provisions of the U.S. Export Administration Act.
8
U.S. Government Contract Security Restrictions
Certain programs with the U.S. Government are prohibited by the customer from being publicly discussed. The consolidated financial statements and financial information in this Annual Report on Form 10-K reflect the operating results of our entire company, including restricted programs, under accounting principles generally accepted in the United States of America (GAAP).
Environmental
Our operations are subject to a number of federal, state and local environmental laws and regulations, as well as applicable foreign laws and regulations that govern the discharge, treatment, storage, remediation and disposal of certain materials and wastes, and restoration of damages to the environment. Compliance with these laws and regulations is a responsibility we take seriously. We believe that forward-looking, proper and cost-effective management of air, land and water resources is vital to the long-term success of our business. Our environmental policy identifies key objectives for implementing this commitment throughout our operations. Additional information on the risks related to environmental matters can be found in Item 1A, "Risk Factors" of this report.
Employees
At December 31, 2017, we had approximately 13,900 employees. We have union-represented employees at five locations, comprising less than 20% of our total workforce. One location has two separate bargaining units, each with its own collective bargaining agreement (“CBA”). The Company’s current CBAs expire in 2018, 2019, 2021, and 2022.
Executive Officers
The following table sets forth certain information with respect to our executive officers at December 31, 2017:
Name | Age | Title | ||
David W. Thompson | 63 | President and Chief Executive Officer | ||
Blake E. Larson | 58 | Chief Operating Officer | ||
Garrett E. Pierce | 73 | Chief Financial Officer | ||
Antonio L. Elias | 68 | Executive Vice President and Chief Technical Officer | ||
Frank L. Culbertson, Jr. | 68 | Executive Vice President and President, Space Systems Group | ||
Michael A. Kahn | 58 | Executive Vice President and President, Defense Systems Group | ||
Scott L. Lehr | 57 | Executive Vice President and President, Flight Systems Group | ||
Thomas E. McCabe | 63 | Senior Vice President, General Counsel and Secretary | ||
Christine A. Wolf | 57 | Senior Vice President, Human Resources |
Each of the above individuals serves at the pleasure of the Board of Directors. No family relationship exists among any of the executive officers or among any of them and our directors. There are no outstanding loans from our company to any of these individuals. Information regarding the employment history (in each case with our Company unless otherwise indicated) of each of the executive officers is set forth below.
David W. Thompson has served in his present position since the Orbital-ATK Merger on February 9, 2015. Mr. Thompson has also been a director of our Company since the Orbital-ATK Merger. He co-founded Orbital and served as Chairman of the Board and Chief Executive Officer of Orbital from 1982 until the Orbital-ATK Merger. From 1982 until October 1999, he also served as President of Orbital, a role he resumed in mid-2011. Prior to founding Orbital, Mr. Thompson was employed by Hughes Electronics Corporation as special assistant to the President of its Missile Systems Group and by NASA at the Marshall Space Flight Center as a project manager and engineer, and also worked on the Space Shuttle's autopilot design at the Charles Stark Draper Laboratory. Mr. Thompson is an Honorary Fellow of the American Institute of Aeronautics and Astronautics, a Fellow of the American Astronautical Society and the Royal Aeronautical Society, and is a member of the U.S. National Academy
9
of Engineering. He also serves as a member of the Board of Trustees of the California Institute of Technology and the Carnegie Institution for Science.
Blake E. Larson has served in his present position since the Orbital-ATK Merger on February 9, 2015. From April 2010 until February 9, 2015, he served as our Senior Vice President and President, Aerospace Group. From 2009 to March 2010, he was Senior Vice President and President, Space Systems. From 2008 to 2009, he was Executive Vice President, Space Systems, and also General Manager, Spacecraft Systems from August 2008 to January 2009. From 2006 to 2008, he was Executive Vice President of Mission Systems Group. Prior to that, Mr. Larson held a variety of key leadership positions in operations of several businesses within our aerospace and defense portfolio.
Garrett E. Pierce has served in his present position since the Orbital-ATK Merger on February 9, 2015. He was Vice Chairman and Chief Financial Officer of Orbital from 2002 until the Orbital-ATK Merger, and was Executive Vice President and Chief Financial Officer of Orbital from 2000 to 2002. From 1996 until 2000, he was Executive Vice President and Chief Financial Officer of Sensormatic Electronics Corp., a supplier of electronic security systems, where he was also named Chief Administrative Officer in July 1998. Prior to joining Sensormatic, Mr. Pierce was the Executive Vice President and Chief Financial Officer of California Microwave, Inc., a supplier of microwave, radio frequency, and satellite systems and products for communications and wireless networks. From 1980 to 1993, Mr. Pierce was employed by Materials Research Corporation, a provider of thin film equipment and high purity materials to the semiconductor, telecommunications and media storage industries, where he progressed from Chief Financial Officer to President and Chief Executive Officer. Materials Research Corporation was acquired by Sony Corporation in 1989. From 1972 to 1980, Mr. Pierce held various management positions with The Signal Companies. Mr. Pierce is a Director of Kulicke and Soffa Industries, Inc.
Antonio L. Elias has served in his present position since the Orbital-ATK Merger on February 9, 2015. He was Executive Vice President and Chief Technical Officer of Orbital from September 2012 until the Orbital-ATK Merger. From October 2001 to September 2012, he served as Orbital's Executive Vice President and General Manager, Advanced Programs Group, and was Orbital's Senior Vice President and General Manager, Advanced Programs Group from 1997 to 2001. From 1996 until 1997, Dr. Elias served as Senior Vice President and Chief Technical Officer of Orbital. From 1993 through 1995, he was Orbital's Senior Vice President for Advanced Projects, and was Orbital's Senior Vice President, Space Systems Division from 1990 to 1993. He was Vice President, Engineering of Orbital from 1989 to 1990 and was Orbital's Chief Engineer from 1986 to 1989. From 1980 to 1986, Dr. Elias was an Assistant Professor of Aeronautics and Astronautics at Massachusetts Institute of Technology. He was elected to the National Academy of Engineering in 2001.
Frank L. Culbertson, Jr. has served in his present position since the Orbital-ATK Merger on February 9, 2015. He was Orbital's Executive Vice President and General Manager, Advanced Programs Group from September 2012 until the Orbital-ATK Merger. From 2008 to 2012, he served as a Senior Vice President in Orbital's Advanced Program Group, where he headed human space systems efforts. Prior to joining Orbital, Mr. Culbertson was a Senior Vice President at Science Applications International Corporation from 2002 to 2008. Before entering the private sector, Mr. Culbertson served as a NASA astronaut for 18 years, flying three Space Shuttle missions, and began his career as a pilot in the U.S. Navy.
Michael A. Kahn has served in his present position since the Orbital-ATK Merger on February 9, 2015. From April 2012 until February 9, 2015, he served as our Senior Vice President and President, Defense Group. From August 2010 through March 2012, he was Senior Vice President and President, Missile Products Group. From 2009 to August 2010, he was Executive Vice President, Aerospace Systems. From 2008 to 2009, he was Vice President and General Manager, Launch Systems, and from 2001 to 2008, he was Vice President, Space Launch Systems. From 1997 to 2001, he was Vice President, Operations, and played a key role in the integration of Thiokol and ATK. From 1989 to 1997, he held a number of senior leadership positions across a variety of programs and operations of our company. Prior to that he was with Rockwell International, Rocketdyne Division, and held a number of positions across engineering, quality and reliability assurance, launch site operations and rocket engine testing.
10
Scott L. Lehr has held his present position since July 1, 2015. From April 2015 through June 2015, he was Senior Vice President, Flight Systems Group. From April 2009 through March 2015, he served as Vice President and General Manager of Defense and Commercial Systems in the Aerospace Group. From 2007 to 2009, he was Vice President, Operations, and from 2004 to 2007, he was Vice President, Air Force Programs within the Launch Systems Group. Prior to that, he held a number of senior leadership positions in engineering and program management as part of our propulsion business. He joined the company in 1984 and has more than 30 years of experience in the aerospace industry.
Thomas E. McCabe has served in his present position since the Orbital-ATK Merger on February 9, 2015. He was Senior Vice President, General Counsel and Corporate Secretary of Orbital from January 2014 until the Orbital-ATK Merger. Before joining Orbital, he served from 2010 to 2014 as Senior Vice President, General Counsel and Secretary of Alion Science and Technology Corporation, a provider of advanced engineering and technology solutions. From 2008 to 2010, he served as Executive Vice President and General Counsel, and President of the Federal business of Braintech, Inc., which provided automated vision systems for industrial and military robots. Earlier in his career, he was Vice President and Deputy General Counsel of XM Satellite Radio from 2005 through its merger with Sirius Satellite Radio in 2008. He also served as President, CEO and a director of software provider MicroBanx Systems from 2001 to 2005, and President, CEO and a director of its parent company, COBIS Corporation, from 2004 to 2005. From 1992 to 2000, he was a senior executive at GRC International, Inc., a provider of advanced software and technology solutions, serving as Senior Vice President, General Counsel, Secretary and Director of Corporate Development through its sale to AT&T in 2000. He was an attorney in private practice from 1982 to 1991. He began his career as judicial clerk for Judge Charles R. Richey at the United States District Court for the District of Columbia from 1981 to 1982.
Christine A. Wolf has held her present position since joining the company in March 2011. She has more than 30 years of experience in the Human Resources field. Prior to joining the company, she was the Senior Vice President and Chief Human Resources Officer for Fannie Mae from 2008 to March 2011. Prior to that, she was the Chief Human Resources Officer for E*Trade from 2004 to 2008.
Available Information
Our reports filed with the Securities and Exchange Commission ("SEC") can be found on our Internet site at www.orbitalatk.com under the "Investors" heading free of charge. These include our annual report on Form 10-K, quarterly reports on Form 10-Q, current reports on Form 8-K, and any amendments to those reports filed or furnished pursuant to Section 13(a) or 15(d) of the Securities Exchange Act of 1934. We make these reports available as soon as reasonably practicable after they are electronically filed with, or furnished to, the SEC.
You can also obtain these reports from the SEC's Public Reference Room, which is located at 100 F Street, NE, Washington, D.C. 20549. Information on the operation of the Public Reference Room is available by phone (1-800-SEC-0330) or on the Internet (www.sec.gov). This site contains reports, proxy and information statements, and other information regarding issuers that file electronically with the SEC.
The content on any website referred to in this Form 10-K is not incorporated by reference into this Form 10-K unless expressly noted.
11
ITEM 1A. RISK FACTORS
We are subject to a number of risks, including those related to the proposed Northrop Grumman acquisition, to those related to being a U.S. Government contractor and those related to domestic and international commercial sales. The material risks we are subject to are discussed below.
Failure to complete the Merger could negatively impact the price of our common stock, as well as our future business and financial results.
On September 17, 2017, we entered into an Agreement and Plan of Merger with Northrop Grumman and Neptune Merger, Inc., a wholly owned subsidiary of Northrop Grumman, pursuant to which Northrop Grumman will acquire us.
The Merger Agreement contains a number of conditions that must be satisfied or waived prior to the completion of the Merger. We cannot assure you that all of the conditions to the Merger will be so satisfied or waived on a timely basis. If the conditions to the Merger are not satisfied or waived on a timely basis, we may be unable to complete the Merger as quickly as expected or at all.
If the Merger is not completed, our ongoing business may be adversely affected as follows: (i) we may experience negative reactions from the financial markets, including negative impacts on the market price of our common stock; (ii) some of management's attention will have been directed to the Merger instead of being directed to our own operations and the pursuit of other opportunities that could have been beneficial to us; (iii) the manner in which customers, suppliers and other third parties perceive us may be negatively impacted, which in turn could affect our ability to compete for business; (iv) we may experience negative reactions from employees; (v) we will have expended time and resources that could otherwise have been spent on our business; and (vi) we may be required, in certain circumstances, to pay a termination fee of $275 million, as provided in the Merger Agreement. In addition, any significant delay in consummating the Merger could have a material adverse effect on our operating results and adversely affect our relationships with customers and suppliers and would likely lead to a significant diversion of management and employee attention.
Additionally, in approving the Merger Agreement, the Board of Directors considered a number of factors and potential benefits, including the fact that the Merger consideration to be received by holders of our common stock represented a 22.2% premium to the closing price of our common stock on September 15, 2017. If the Merger is not completed, neither the Company nor the holders of our common stock will realize this benefit of the Merger. Moreover, we would also have nevertheless incurred substantial transaction-related fees and costs and the loss of management time and resources.
Expenses related to the pending Merger are significant and will adversely affect our operating results.
We have incurred and expect to continue to incur significant expenses in connection with the pending Merger, including legal and investment banking fees. We expect these costs to have an adverse effect on our operating results. If the Merger is not consummated, we may under certain circumstances be required to pay to Northrop Grumman a termination fee of $275 million. Our financial position and results of operations would be adversely affected if we were required to pay the termination fee to Northrop Grumman.
We are subject to business uncertainties and contractual restrictions while the Merger is pending, which could adversely affect our business.
The Merger Agreement requires us to act in the ordinary course of business and restricts us, without the consent of Northrop Grumman, from taking certain specified actions until the pending Merger occurs or the Merger Agreement terminates. These restrictions may prevent us from pursuing otherwise attractive business opportunities and making other changes to our business before completion of the Merger or, if the Merger is not completed, termination of the Merger Agreement.
Uncertainties associated with the Merger may cause a loss of management and other key employees and disrupt our business relationships, which could adversely affect our business.
Uncertainty about the effect of the Merger on our employees, customers and suppliers may have an adverse effect on our business. These uncertainties may impair our ability to attract, retain and motivate key personnel until the Merger is completed and for a period of time thereafter. Employee retention may be particularly challenging during the pendency of the Merger. If key employees depart and as we face additional uncertainties relating to the Merger, our business relationships may be subject to disruption as customers, suppliers and other third parties attempt to
12
negotiate changes in existing business relationships or consider entering into business relationships with parties other than the Company. If key employees depart or if our existing business relationships suffer, our results of operations may be adversely affected. The adverse effects of such disruptions could be further exacerbated by any delay in the completion of the Merger.
Our business could be adversely impacted by reductions or changes in U.S. Government military or NASA spending.
We depend on contracts with the U.S. Government and its prime contractors for a substantial portion of our sales. In addition, a significant portion of such sales come from a small number of contracts. Our CRS contracts with NASA, which are reported within Flight Systems Group and Space Systems Group, comprised 9%, 13% and 10% of our sales in calendar year 2017, calendar year 2016 and the 2015 transition period, respectively. Our small-caliber ammunition contract with the U.S. Army, which is reported within Defense Systems Group, comprised 5%, 6%, and 6% of our sales in calendar 2017, calendar 2016 and the 2015 transition period, respectively. The loss or significant reduction of a material U.S. Government program in which we participate could have a material adverse effect on our operating results, financial condition or cash flows.
U.S. Government contracts are dependent on the continuing availability of Congressional appropriations. Congress usually appropriates funds for a given program on a fiscal year basis even though contract performance may take more than one year. As a result, at the outset of a major program, the contract is usually incrementally funded, and additional monies are normally committed to the contract by the procuring agency only as Congress makes appropriations for future fiscal years. In addition, most U.S. Government contracts are subject to modification if funding is changed. Key programs in which we participate must compete with other programs for consideration during the federal budgeting and appropriation process, and support and funding for any U.S. Government program may be influenced by general economic conditions, political considerations and other factors. A decline in U.S. Government support and funding for programs in which we participate could result in contract terminations, delays in contract awards, the failure to exercise contract options, the cancellation of planned procurements and fewer new business opportunities, any of which could have a material adverse effect on our operating results, financial condition or cash flows.
We are subject to intense competition for U.S. Government contracts and programs and therefore may not be able to compete successfully.
We encounter competition for many contracts and programs, including in particular, U.S. Government contracts. Some of our competitors have substantially greater financial, technical, marketing, manufacturing, distribution and other resources. Our ability to compete for these contracts depends to a large extent upon:
• | the creativity and effectiveness of our research and development programs, |
• | our ability to offer better program performance and/or at a lower cost than our competitors, |
• | the readiness of our facilities, equipment and personnel to undertake the programs for which we compete, and |
• | our past performance and demonstrated capabilities. |
In some instances, the U.S. Government directs a program to a single supplier. In these cases, there may be other suppliers who have the capability to compete for the programs involved, but they can only enter or reenter the market if the U.S. Government chooses to open the particular program to competition and, as such, these types of programs are subject to risk of the U.S. Government providing new awards to other suppliers. Our sole-source contracts accounted for 47% of our U.S. Government sales in the year ended December 31, 2017.
We may not be able to react to increases in our costs due to the nature of our U.S. Government contracts.
Our U.S. Government contracts can be categorized as either "cost-plus" or "fixed-price."
Cost-Plus Contracts. Cost-plus contracts are cost-plus-fixed-fee, cost-plus-incentive-fee or cost-plus-award-fee contracts. Cost-plus-fixed-fee contracts allow us to recover approved costs plus a fixed fee. Cost-plus-incentive-fee contracts and cost-plus-award-fee contracts allow us to recover approved costs plus a fee that can fluctuate based on actual results as compared to contractual targets for factors such as cost, quality, schedule and performance. The award or incentive fees that are typically associated with these programs are subject to uncertainty and may be earned over extended periods. In these cases, the associated financial risks for cost-plus contracts are primarily in lower profit rates or program cancellation if cost, schedule or technical performance issues arise.
13
Fixed-Price Contracts. Fixed-price contracts are firm-fixed-price, fixed-price-incentive or fixed-price-level-of-effort contracts. Under firm-fixed-price contracts, we agree to perform certain work for a fixed price and absorb any cost overruns. Fixed-price-incentive contracts are fixed-price contracts under which the final contract price may be adjusted based on total final costs compared to total target cost, and may be affected by schedule and performance. Fixed-price-level-of-effort contracts allow for a fixed price per labor hour, subject to a contract cap. All fixed-price contracts present the inherent risk of unreimbursed cost overruns. If the initial estimates used to calculate the contract price and the cost to perform the work prove to be incorrect, there could be a material adverse effect on operating results, financial condition or cash flows. The Lake City Army Ammunition Plant ammunition contract is a fixed-price contract and is expected to result in a net loss over the term of the contract. In addition, some contracts have specific provisions relating to cost, schedule and performance. If we fail to meet the terms specified in those contracts, the cost to perform the work could increase or our price could be reduced, which would adversely affect our financial condition. The U.S. Government also regulates the accounting methods under which costs are allocated to U.S. Government contracts.
The following table identifies the amount contributed to our U.S. Government business by contract type in the year ended December 31, 2017:
Cost-plus contracts | 36 | % |
Fixed-price contracts | 64 | % |
Total | 100 | % |
We use estimates in accounting for our programs. Changes in estimates have affected our financial results and could affect them in the future.
Contract accounting requires judgment relative to assessing risks, estimating contract revenues, including the impact of scope change negotiations, estimating program costs, and making assumptions for schedule and technical issues. Due to the size and nature of many of our contracts, the estimation of total revenues and cost at completion is complex and subject to many variables. Assumptions are made regarding the length of time to complete the contract because costs also include expected increases in wages and prices for materials. Similarly, many assumptions are made regarding the future impact of such things as the business base, efficiency initiatives, cost reduction efforts, contract changes and claim recovery. Incentives or penalties related to performance on contracts are considered in estimating revenue and profit rates, and are recorded when there is sufficient information to assess anticipated performance. Estimates of award and incentive fees are also used in estimating revenue and profit rates based on actual and anticipated awards.
Because of the significance of the judgments and estimation processes described above, it is possible that materially different amounts could be recorded if we used different assumptions or if the underlying circumstances were to change. For example, we have concluded that the Company’s costs will exceed expected revenues under its long-term contract with the U.S. Army to manufacture and supply small-caliber ammunition at the Lake City Army Ammunition Plant, resulting in a material net loss over the contract's term. Changes in underlying assumptions, circumstances or estimates may adversely affect future period financial performance. Additional information on our accounting policies for revenue recognition can be found in Item 7, "Management's Discussion and Analysis of Financial Condition and Results of Operations" in the section titled "Critical Accounting Policies" of this report.
Our U.S. Government contracts are subject to termination at any time, with or without cause.
Our direct and indirect contracts with the U.S. Government or its prime contractors may be terminated or suspended at any time, with or without cause, for the convenience of the U.S. Government or in the event of a default by the contractor. If a cost-plus contract is terminated, the contractor is entitled to reimbursement of its approved costs. If the contractor would have incurred a loss had the entire contract been performed, then no profit is allowed by the U.S. Government.
If the termination is for convenience, the contractor is also entitled to receive payment of a total fee proportionate to the percentage of the work completed under the contract. If a fixed-price contract is terminated, the contractor is entitled to receive payment for items delivered to and accepted by the U.S. Government. If the termination is for convenience, the contractor is also entitled to receive fair compensation for work performed plus the costs of settling and paying claims by terminated subcontractors, other settlement expenses and a reasonable profit on the costs incurred or committed. While the contractor is entitled to these claims under either type of contract, there can be no assurance that these amounts will be recovered.
14
If a contract termination is for default:
• | the contractor is paid an amount agreed upon for completed and partially completed products and services accepted by the U.S. Government, |
• | the U.S. Government is not liable for the contractor's costs for unaccepted items, and is entitled to repayment of any advance payments and progress payments related to the terminated portions of the contract, and |
• | the contractor may be liable for excess costs incurred by the U.S. Government in procuring undelivered items from another source. |
One of our major programs is as the provider of solid rocket motors for NASA's SLS program. In the event NASA were to cancel the SLS program, we believe that we will be reimbursed for certain amounts previously incurred by us, as well as amounts to be incurred by us, as part of that termination, (e.g., severance, environmental liabilities and termination administration). There can be no assurance, however, that we would be successful in collecting reimbursement of any termination liability costs.
Our contracts with NASA to deliver cargo to the ISS are a significant part of our business within Flight Systems Group and Space Systems Group. NASA could cancel these contracts for any reason, including as a result of reductions in appropriations or our failure to achieve milestones due to technical issues or delays similar to those that occurred when we experienced an Antares launch failure in 2014. A cancellation of our NASA contracts could have a material adverse effect on our operating results, financial condition and cash flows.
Our small-caliber ammunition operations for the U.S. military and U.S. allies are conducted at the Lake City Army Ammunition Plant in Independence, Missouri. The Lake City Army Ammunition Plant is the U.S. Army's principal small-caliber ammunition production facility and is the primary supplier of the U.S. military's small-caliber ammunition needs. We took over operation of this facility in 2000 and are responsible for the operation and management. In September 2012, we were awarded new contracts for the continued production of ammunition and continued operation and maintenance of the Lake City Army Ammunition Plant. The production contract has an initial term of seven years. The contract also had the possibility of an award term extension of an additional three years, but the Company provided written notice of rejection of the extension to the U.S. Army in 2017, which we believe will result in materially lower sales for the Company should we not win the re-compete.
Other risks associated with U.S. Government contracts may expose us to adverse consequences.
Like all U.S. Government contractors, we are subject to possible losses on contracts due to risks associated with uncertain cost factors related to:
• | scarce technological skills and components, |
• | the frequent need to bid on programs in advance of design completion, which may result in unforeseen technological difficulties and/or cost overruns, |
• | the substantial time and effort required for design and development, |
• | design complexity, |
• | rapid obsolescence, and |
• | the potential need for design improvement. |
Such factors can increase the costs associated with a program and delay performance, reducing our profitability and adversely impacting our customer relationships.
We manufacture and provide commercial aircraft components which could subject us to exposure unique to the commercial aircraft industry.
Airbus and Boeing have the contractual right to cancel their contracts with us for convenience, which could include the termination of one or more aircraft models or programs for which we supply products. Although Airbus and Boeing would be required to reimburse us in certain situations for expenses, there can be no assurance these payments would adequately cover our expenses or lost profits resulting from the termination. Furthermore, if Airbus or Boeing experiences a decrease in requirements for the products which we supply to it, a major disruption in its business, such as a strike, work stoppage or slowdown, fails to perform on its contractual obligations under its
15
agreements with us or we cannot meet the expected production rate increases, our business, results of operations, financial position and cash flows could be materially adversely affected.
We are subject to procurement and other related laws and regulations, and non-compliance may expose us to adverse consequences.
We are subject to extensive and complex U.S. Government procurement laws and regulations, along with ongoing U.S. Government audits and reviews of contract procurement, performance and administration. As a result, U.S. Government agencies, including the Defense Contract Audit Agency, various agency Inspectors General and the U.S. Department of Justice ("DoJ"), routinely audit and investigate government contractors. In particular, these agencies often investigate our launch vehicle failures and other material occurrences relating to our products, including an ongoing DoJ/NASA investigation of the 2009 OCO and 2011 Glory failures involving the Taurus XL launch vehicle. These agencies review a contractor's performance under its contracts, cost structure and compliance with applicable laws, regulations and standards, including procurement integrity laws and the False Claims Act.
Charging practices relating to labor, research and development, and other costs that may be charged directly or indirectly to U.S. Government contracts are often scrutinized to determine that such costs are allowable under U.S. Government contracts and furthermore that such costs are reasonable. Any costs determined to be unallowable or unreasonable may not be reimbursed, and such costs already reimbursed may be subject to repayment. If the amount of such costs were significant, our results of operations, financial condition and cash flow could be materially adversely affected. We expect to recover a significant portion of our research and development expenses through billings under certain of our U.S. Government contracts in accordance with applicable regulations, but such billings could be reversed or rejected by the U.S. Government. Our inability to recover a significant portion of such expenses could materially adversely affect our operating results, financial condition or cash flows.
U.S. Government agencies also review the adequacy of, and a contractor's compliance with, its internal control systems and policies, including the contractor's purchasing, property, estimating, earned value, material management and accounting systems. Adverse findings relating to our systems could result in the U.S. Government customer withholding a percentage of payments and also could impact our ability to win new U.S. Government contracts or exercise contract options.
Responding to government audits, inquiries or investigations may involve significant expense and divert management attention. Also, if an audit or investigation were to uncover improper or illegal activities, we could be subject to civil and criminal penalties and administrative sanctions, including termination of contracts, forfeiture of profits, suspension of payments, fines and suspension or prohibition from doing business with the U.S. Government. In addition, we could suffer serious harm to our reputation if allegations of impropriety were to be made against us.
Changes in demand for military and commercial ammunition could adversely affect our financial performance.
We sell military ammunition to the DoD and commercial ammunition to Vista Outdoor under an ammunition supply agreement. Both the commercial and military markets for ammunition are subject to a number of risks and uncertainties that can cause demand to fluctuate unpredictably. Decreases in the demand for ammunition in either market could result in excess manufacturing capacity and increased overhead rates as a result, which could have a negative impact on our operating results. Further, since our Lake City Ammunition Contract with the U.S. Army is in a loss position, increases in demand by the DoD could adversely affect our financial performance, including profitability and cash flow. In addition, manufacturing costs for ammunition could rise as a result of a number of factors, including increases in commodity prices and other raw materials and increases in labor costs at the Lake City Army Ammunition Plant, which could also have an adverse effect on our operating results and further increase our net loss under that contract.
We manufacture and sell products that create exposure to potential product liability, warranty liability or personal injury claims and litigation.
Our products may expose us to potential product liability, warranty liability or personal injury claims relating to the use of those products. Our reputation may be adversely affected by such claims, whether or not successful, including potential negative publicity about our products.
16
We are exposed to risks associated with expansion into new and adjacent commercial markets.
Our long-term business growth strategy includes further expansion into new and adjacent markets. For example, we currently are investing in several new growth initiatives, including new cutting-edge satellite servicing technologies. Such efforts involve a number of risks, including increased capital expenditures, market uncertainties, market acceptance of new technologies, schedule delays, performance risk, extended payment terms, diversion of management attention, additional credit risk associated with new customers, and costs incurred in competing with companies with strong brand names and market positions. An unfavorable event or trend in any one or more of these factors could adversely affect our operating results, financial condition or cash flows.
International sales are subject to greater risks that sometimes are associated with doing business in foreign countries.
A portion of our business is derived from international markets. In the year ended December 31, 2017, approximately 18% of our sales were to foreign customers, compared to 17% in the year ended December 31, 2016. We also procure certain key components from non-U.S. vendors. Our international business may pose greater risks than our business in the United States due to changes in economic, legal and political environments, as well as foreign government priorities and budgets. International transactions frequently involve increased financial and legal risks arising from differing legal systems and customs in other countries. In addition, some international customers require contractors to agree to offset programs that may require in-country purchases or manufacturing or financial support arrangements as a condition to awarding contracts. The contracts may include penalties in the event a company fails to perform in accordance with the offset requirements. Furthermore, international business may create difficulties and risks with respect to the maintenance of an integrated supply chain network. An unfavorable event or trend in any one or more of these factors could adversely affect our operating results, financial condition or cash flows. Foreign sales subject us to numerous stringent U.S. and foreign laws and regulations, including Congressional review and approval of certain foreign arms sales, regulations relating to import-export control, exchange controls, the Foreign Corrupt Practices Act and certain other anti-corruption laws, and the anti-boycott provisions of the U.S. Export Administration Act. Failure to comply with these laws and regulations could result in material adverse consequences to us.
Our products are subject to extensive regulation.
We are required to comply with extensive regulation of our products, including those rules and regulations administered by the Bureau of Alcohol, Tobacco, Firearms and Explosives, the U.S. Department of Homeland Security, the U.S. Department of State and the U.S. Department of Commerce. These laws include, but are not limited to, the Foreign Corrupt Practices Act, International Traffic in Arms Regulations, and the Chemical Facility Anti-Terrorism Standards. Compliance with these laws is costly and time consuming. A violation of these laws could result in significant fines and penalties and could have a material adverse effect on our business.
We are exposed to market risk from changes in foreign currency exchange rates which could negatively impact profitability.
Sales and purchases in currencies other than the U.S. dollar expose us to fluctuations in foreign currencies relative to the U.S. dollar and may adversely affect our results of operations. Currency fluctuations may affect product demand and prices we pay for materials and, as a result, our operating margins may be negatively impacted. Fluctuations in exchange rates may give rise to translation gains or losses when financial statements of our non-U.S. businesses are translated into U.S. dollars. While we monitor our exchange rate exposures and seek to reduce the risk of volatility through hedging activities, such activities bear a financial cost and are not always available or successful in mitigating such volatility.
We have restated our prior consolidated financial statements twice recently, which may lead to adverse determinations in legal proceedings, additional risks and uncertainties, including loss of investor confidence and negative impacts on our stock price.
As a result of our recent restatements, we have become subject to a number of additional costs and risks, including unanticipated costs for accounting and legal fees in connection with or related to the restatements and the remediation of our ineffective disclosure controls and procedures and material weaknesses in internal control over financial reporting. We are also the subject of a non-public investigation by the SEC, securities class action litigation and shareholder demands and potentially other actions as a result of the restatements. We could be subject to additional shareholder, governmental, or other actions in connection with the restatements and related matters. Any current or future legal proceedings will, regardless of the outcome, continue to consume a significant amount of management's time and attention and may result in additional legal, accounting, insurance and other costs. While
17
we cannot estimate our potential exposure in these proceedings at this time, we expect to expend significant amounts defending the litigation and responding to the SEC investigation. If we do not prevail in any such proceedings, we could be required to pay substantial damages or settlement costs. In addition, the restatements and related matters could impair our reputation or could cause our counterparties to lose confidence in us. Any of these occurrences could have a material adverse effect on our business, results of operations, financial condition and stock price.
We have a substantial amount of debt, and the cost of servicing that debt could adversely affect our business and hinder our ability to make payments on our debt.
At December 31, 2017, we had total debt of $1,410 million. In addition, we had $240 million of outstanding but undrawn letters of credit and, taking into account these letters of credit, an additional $760 million of availability under our revolving credit facility. Additional information on our debt can be found in Item 7, "Management's Discussion and Analysis of Financial Condition and Results of Operations" in the section titled "Liquidity and Capital Resources" of this report.
We have demands on our cash resources in addition to interest and principal payments on our debt including, among others, operating expenses. These significant demands on our cash resources could:
• | make it more difficult for us to satisfy obligations, |
• | require us to dedicate a substantial portion of our cash flow from operations to payments on our debt, thereby reducing the amount of cash flow available for working capital, capital expenditures, acquisitions, share repurchases, dividends and other general corporate purposes, |
• | limit our flexibility in planning for, or reacting to, changes in the defense and aerospace industries, |
• | place us at a competitive disadvantage compared to competitors that have lower debt service obligations and significantly greater operating and financing flexibility, |
• | limit, along with the financial and other restrictive covenants applicable to our indebtedness, among other things, our ability to borrow additional funds, |
• | increase our vulnerability to general adverse economic and industry conditions, and |
• | result in a default event upon a failure to comply with financial covenants contained in our senior credit facilities which, if not cured or waived, could have a material adverse effect on our business, financial condition or results of operations. |
Our ability to pay interest on and repay our long-term debt and to satisfy our other liabilities will depend upon future operating performance and our ability to refinance our debt as it becomes due. Our future operating performance and ability to refinance will be affected by prevailing economic conditions at that time and financial, business and other factors, many of which are beyond our control.
If we are unable to service our indebtedness and fund operating costs, we will be forced to adopt alternative strategies that may include:
• | reducing or delaying expenditures for capital equipment and/or share repurchases, |
• | seeking additional debt financing or equity capital, |
• | foregoing attractive acquisition opportunities, |
• | selling assets, or |
• | restructuring or refinancing debt. |
There can be no assurance that any such strategies could be implemented on satisfactory terms, if at all.
The level of returns on pension and postretirement plan assets, changes in interest rates and other factors could affect our earnings and cash flows.
Our earnings may be impacted by the amount of expense or income recorded for employee benefit plans, primarily pension plans and other postretirement plans. U.S. GAAP requires us to calculate income or expense for the plans using actuarial valuations. These valuations are based on assumptions made relating to financial market and other
18
economic conditions. Changes in key economic indicators can result in changes in these assumptions. The key year-end assumptions used to estimate pension and postretirement benefit expense or income for the following year are the discount rate, the expected long-term rate of return on plan assets, the rate of increase in future compensation levels, mortality rates and the health care cost trend rate. We are required to remeasure our plan assets and benefit obligations annually, which may result in a significant change to equity through other comprehensive income (loss). Our pension and other postretirement benefit income or expense can also be affected by legislation or other regulatory actions. Additional information on how our financial statements can be affected by pension plan accounting policies can be found in Item 7, "Management's Discussion and Analysis of Financial Condition and Results of Operations" in the section titled "Critical Accounting Policies" of this report.
Our business could be negatively impacted by security threats, including cyber security and other industrial, insider and physical security threats, and other disruptions.
As a U.S. defense contractor, we face cyber security threats, threats to the physical security of our facilities and employees, and terrorist acts, as well as the potential for business disruptions associated with information technology failures, natural disasters or public health crises. We also face the risk of economic espionage, which involves the targeting or acquisition of sensitive financial, trade, proprietary or technological information.
We routinely experience cyber security threats, threats to our information technology infrastructure and attempts to gain access to sensitive information, as do our customers, suppliers, subcontractors and joint venture partners. We may experience similar security threats at customer sites that we operate and manage.
Prior cyber attacks directed at us have not had a material impact on our financial results, and we believe that our threat detection and mitigation processes and procedures are generally adequate. The threats we face vary from attacks common to most industries to more advanced and persistent threats from highly-organized adversaries who target us because we protect national security information. If we are unable to protect sensitive information, our customers or governmental authorities could question the adequacy of our threat mitigation and detection processes and procedures and, as a result, our present and future business could be negatively impacted.
Although we work cooperatively with our customers, suppliers, subcontractors and joint venture partners to minimize the impact of cyber threats, other security threats or business disruptions, we must rely on the safeguards put in place by these entities, which may in turn affect the security of our own information and that of other parties. The entities we work with have varying levels of cyber security expertise and safeguards and their relationships with government contractors, such as us, may increase the likelihood that they are targeted by the same cyber threats we face.
The costs related to cyber or other security threats or disruptions may not be fully insured or indemnified by other means. Occurrence of any of these events could adversely affect our internal operations, the services we provide to customers, loss of competitive advantages derived from our research and development efforts or other intellectual property, the obsolescence of our products and services, our financial results, our reputation and our stock price.
Disruptions in the supply of key raw materials or components and difficulties in the supplier qualification process, as well as increases in prices of raw materials, could adversely impact us.
Key raw materials used in our operations include aluminum, steel, steel alloys, copper, zinc, lead, graphite fiber, prepreg, hydroxy terminated polybutadiene, epoxy resins and adhesives, ethylene propylene diene monomer rubbers, diethylether, x-ray film, plasticizers and nitrate esters, impregnated ablative materials, various natural and synthetic rubber compounds, polybutadiene, acrylonitrile and ammonium perchlorate. We also purchase chemicals; electronic, electro-mechanical and mechanical components; subassemblies; and subsystems that are integrated with the manufactured parts for final assembly into finished products and systems.
We monitor sources of supply to attempt to assure that adequate raw materials and other supplies needed in manufacturing processes are available. As a U.S. Government contractor, we are frequently limited to procuring materials and components from sources of supply approved by the DoD. In addition, as changes occur in business conditions, the DoD budget and Congressional allocations, suppliers of specialty chemicals and materials sometimes consider dropping low volume items from their product lines, which may require, as it has in the past, qualification of new suppliers for raw materials on key programs. The supply of ammonium perchlorate, a principal raw material used in our operations, is limited to a single source that supplies the entire domestic solid propellant industry. This single source, however, maintains two separate manufacturing lines a reasonable distance apart, which mitigates the likelihood of a fire, explosion or other problem impacting all production.
19
We also rely on sole-source suppliers for a number of key components, including the rocket motors and engines we use on our launch vehicles. If we are unable to obtain such components in the future, due to a supplier's financial difficulties or a supplier's failure to perform as expected, we could have difficulty procuring such components in a timely or cost effective manner. Although other suppliers of the same materials may exist, the addition of a new supplier may require us to qualify the new source for use. The qualification process may impact our profitability or ability to meet contract deliveries. A disruption in the procurement of key components could result in substantial cost increases, significant delays in the execution of certain contracts or our inability to complete certain contracts, any of which could result in a materially adverse impact on our financial results.
For example, as a result of the failure of our Antares launch vehicle in October 2014 and prior engine test failures, we ceased using the AJ-26 rocket engine in our Antares product line and transitioned to a sole-sourced replacement engine, the RD-181. The time, expense and effort associated with our recovery plan resulted in additional costs and delays.
Certain suppliers of materials used in the manufacturing of rocket motors have discontinued the production of some materials. These materials include certain insulation and resin materials for rocket motor cases and aerospace-grade rayon for nozzles. We have qualified new replacement materials for some programs. For other programs, we or our customers have procured sufficient inventory to cover current program requirements and are in the process of qualifying new replacement materials to be qualified in time to meet future production needs. Our profitability may be affected if unforeseen difficulties in developing and qualifying replacement materials occur.
We are also impacted by increases in the prices of raw materials used in production on commercial and fixed-price business. We have seen a significant fluctuation in the prices of commodity metals, including copper, lead, steel and zinc. The fluctuating costs of natural gas and electricity also have an impact on the cost of operating our factories.
Prolonged disruptions in the supply of any of our key raw materials or components, difficulty completing qualification of new sources of supply, implementing use of replacement materials, components or new sources of supply, or a continuing increase in the prices of raw materials, energy or components could have a material adverse effect on our operating results, financial condition or cash flows.
Failure of our subcontractors to perform their contractual obligations could materially and adversely impact our prime contract performance and ability to obtain future business.
We rely on subcontracts with other companies to perform a portion of the services we provide our customers on many of our contracts. There is a risk that we may have disputes with our subcontractors, including disputes regarding the quality and timeliness of work performed by the subcontractor, customer concerns about the subcontract, our failure to extend existing task orders or issue new task orders under a subcontract or our hiring of personnel of a subcontractor. A failure by one or more of our subcontractors to satisfactorily provide on a timely basis the agreed-upon supplies or perform the agreed-upon services may materially and adversely impact our ability to perform our obligations as the prime contractor. Subcontractor performance deficiencies could result in a customer limiting payments or terminating a contract for default. A default termination could expose us to liability and have a material adverse effect on the ability to compete for future contracts and orders.
Failure to successfully negotiate or renew collective bargaining agreements, or strikes, slow-downs or other labor-related disruptions, could adversely affect our operations and could result in increased costs that impair our financial performance.
A significant number of our employees are covered by collective bargaining agreements, which expire on various dates. Strikes, slow-downs or other labor-related disruptions could occur if we are unable to either negotiate or renew these agreements on satisfactory terms, which could adversely impact our operating results. The terms and conditions of new or renegotiated agreements could also increase our costs or otherwise affect our ability to fully implement future operational changes to enhance our efficiency. In certain instances, we may not be able to pass increased costs from new or renegotiated agreements on to our customers due to the fixed-price nature of many of our contracts, including our small-caliber ammunition contract with the U.S. Army that is performed at the Lake City Army Ammunition Plant.
20
Our future success and growth will depend significantly on our ability to develop new technologies and products that achieve market acceptance within acceptable margins while maintaining a qualified workforce to meet the needs of our customers.
Virtually all of the products produced and sold by us are highly engineered and require sophisticated manufacturing and system integration techniques and capabilities. Our commercial and government businesses both operate in global markets that are characterized by rapidly changing technologies, industry standards, market trends and customer demands. The product and program needs of our government and commercial customers change and evolve regularly. Accordingly, our future performance depends on our ability to identify emerging technological trends, develop and manufacture competitive products, enhance our products by adding innovative features that differentiate our products from those of our competitors, and bring those products to market quickly at cost-effective prices.
Our ability to develop new products based on technological innovation can affect our competitive position and requires the investment of significant resources. These development efforts divert resources from other potential investments in our businesses, and they may not lead to the development of new technologies or products on a timely basis or meets the needs of our customers as fully as other competitive offerings. In addition, the markets for our products may not develop or grow as we anticipate. The failure of our technologies or products to gain market acceptance due to more attractive offerings by our competitors could significantly reduce our revenues and adversely affect our competitive standing and prospects.
In addition, because of the highly specialized nature of our business, we must be able to hire and retain the skilled and appropriately qualified personnel necessary to perform the services required by our customers. Our operating results, financial condition or cash flows may be adversely affected if we are unable to develop new products that meet customers' changing needs or successfully attract and retain qualified personnel.
There can be no assurance that our products will be successfully developed or manufactured or that they will perform as intended.
Most of the products we develop and manufacture are technologically advanced and sometimes include novel systems that must function under highly demanding operating conditions. From time to time, we experience product failures, cost overruns in developing and manufacturing our products, delays in delivery and other operational problems. We have experienced product and service failures, schedule delays and other problems in connection with certain of our launch vehicles, including the Antares launch vehicle, satellites, advanced space systems and other products. We may have similar occurrences in the future.
Some of our satellite and launch services contracts impose monetary penalties on us for delays and for performance failures, which penalties could be significant. In addition to any costs resulting from product warranties or required remedial action, product failures or significant delays may result in increased costs or loss of revenues due to the postponement or cancellation of subsequently scheduled operations or product deliveries and may have a material adverse effect on our operating results, financial condition or cash flows. Negative publicity from a product failure could damage our reputation and impair our ability to win new contracts.
Due to the volatile and flammable nature of our products, fires or explosions may disrupt our business.
Many of our products involve the manufacture and/or handling of a variety of explosive and flammable materials. From time to time, these activities have resulted in incidents, such as an explosion at the Lake City Army Ammunition Plant in 2017, that have caused workplace injuries and fatalities, the temporary shut down or other disruption of our manufacturing process, production delays, and related expense, fines and liability to third parties. We have safety and loss prevention programs which require detailed pre-construction reviews of process changes and new operations, along with routine safety audits of operations involving explosive materials, to mitigate such incidents, as well as insurance coverage for such incidents. We may experience similar or more serious incidents in the future which could result in production delays or otherwise have a material adverse effect on our operating results, financial condition or cash flows.
We are subject to environmental laws and regulations that govern both past practices and current compliance which may expose us to adverse consequences.
Our operations and ownership or use of real property are subject to a number of federal, state and local environmental laws and regulations, as well as applicable foreign laws and regulations, including those for discharge of hazardous materials, remediation of contaminated sites and restoration of damage to the environment. At certain sites that we own or operate or formerly owned or operated, there is known or potential contamination
21
that we are required to investigate, remediate or provide resource restoration. We could incur substantial costs, including remediation costs, resource restoration costs, fines and penalties, or third party property damage or personal injury claims, as a result of liabilities associated with past practices or violations of environmental laws or non-compliance with environmental permits.
We expect that a portion of our environmental compliance and remediation costs will be recoverable under U.S. Government contracts. Some of the remediation costs that are not recoverable from the U.S. Government that are associated with facilities purchased in a business acquisition may be covered by indemnification agreements.
Although we have environmental management programs in place to mitigate risks, and environmental laws and regulations have not had a material adverse effect on our operating results, financial condition or cash flows in the past, it is difficult to predict whether they will have a material impact in the future.
Capital market volatility could adversely impact our earnings because of our capital structure.
We are exposed to the risk of fluctuation in interest rates. If interest rates increase, we may incur increased interest expense on variable interest-rate debt or short-term borrowings, which could have an adverse impact on our operating results and cash flows.
Our profitability could be impacted by unanticipated changes in our tax provisions or exposure to additional income tax liabilities.
Our business operates in many locations under government jurisdictions that impose income taxes. Changes in domestic or foreign income tax laws and regulations, or their interpretation, could result in higher or lower income tax rates assessed or changes in the taxability of certain revenues or the deductibility of certain expenses, thereby affecting income tax expense and profitability. In addition, audits by income tax authorities could result in unanticipated increases in income tax expense.
In connection with the Tax Cuts and Jobs Act (the "Tax Act") signed into law on December 22, 2017, the U.S. Treasury is expected to issue rules, regulations and guidance in connection with the Tax Act which may alter interpretations of its provisions and change our preliminary analysis and conclusions. Any Treasury rules, regulations and guidance may materially impact the company's operating results, including our provision for income taxes, the amount of our net deferred tax assets and our estimated effective tax rate. We cannot currently predict the overall impact of the Tax Act on our business and results of operations. There could be unforeseen adverse tax consequences that arise as a result of the Tax Act. In addition, further changes in the tax laws of foreign jurisdictions could arise. These contemplated changes could increase tax uncertainty and may adversely affect our provision for income taxes.
We are involved in a number of legal proceedings. We cannot predict the outcome of litigation and other contingencies with certainty.
We are subject to lawsuits, investigations and disputes (some involving substantial amounts) that arise out of the conduct of our business including matters relating to commercial transactions, government contracts, product liability, prior acquisitions and divestitures, employment, employee benefits plans, intellectual property, import and export matters, and environmental, health and safety matters. As noted in Part I, Item 3, "Legal Proceedings" of this Form 10-K, we are also subject to various claims related to the restatements. Resolution of these matters can be prolonged and costly, and our business may be adversely affected by the ultimate outcome of these matters that cannot be predicted with certainty. Moreover, our potential liabilities are subject to change over time due to new developments, changes in settlement strategy or the impact of evidentiary issues, and we may become subject to or be required to pay damage awards or settlements that could have a material adverse effect on our operating results, financial condition or cash flows.
22
If the Distribution does not qualify as a tax-free spin-off under Section 355 of the Internal Revenue Code (the "Code"), including as a result of subsequent acquisitions of our stock or Vista Outdoor, then we or our stockholders immediately prior to the Distribution may be required to pay substantial U.S. federal income taxes and we may be obligated to indemnify Vista Outdoor for such taxes imposed on Vista Outdoor.
The Distribution and the Orbital-ATK Merger are intended to qualify as tax-free to us, our stockholders, Vista Outdoor and Orbital for U.S. federal income tax purposes. However, there can be no assurance that the IRS or the courts will agree with the conclusion of the parties and their counsel regarding the tax treatment of the Distribution and Orbital-ATK Merger. If the Distribution or certain related transactions were taxable, our stockholders would recognize income on their receipt of Vista Outdoor stock in the Distribution, and we would be considered to have made a taxable sale of certain of our assets to Vista Outdoor.
The Distribution will be taxable to us pursuant to Section 355(e) of the Code if there is a 50% or more change in ownership of either us or Vista Outdoor, directly or indirectly, as part of a plan or series of related transactions that include the Distribution. Because our stockholders collectively owned more than 50% of our common stock following the Orbital-ATK Merger, the Orbital-ATK Merger alone will not cause the Distribution to be taxable to us under Section 355(e). However, Section 355(e) could apply if other acquisitions of our stock before or after the Orbital-ATK Merger, or of Vista Outdoor after the Orbital-ATK Merger, are considered to be part of a plan or series of related transactions that include the Distribution. If Section 355(e) were to apply, we would be considered to have made a taxable sale of certain assets to Vista Outdoor and could recognize a substantial taxable gain.
Under the tax matters agreement between us and Vista Outdoor (the "Tax Matters Agreement"), in certain circumstances, and subject to certain limitations, Vista Outdoor is required to indemnify us against taxes on the Distribution that arise as a result of actions or failures to act by Vista Outdoor, or as a result of Section 355(e) applying due to acquisitions of Vista Outdoor stock after the Distribution. In other cases, however, we might recognize taxable gain on the Distribution without being entitled to an indemnification payment under the Tax Matters Agreement. If such tax is imposed on Vista Outdoor, then we generally will be required to indemnify Vista Outdoor for that tax.
ITEM 1B. UNRESOLVED STAFF COMMENTS
There are no unresolved staff comments at the date of this report.
ITEM 2. PROPERTIES
Facilities. At December 31, 2017, we occupied research, development, manufacturing, assembly, test, warehouse and office facilities having a total floor space of approximately 17.5 million square feet. These facilities are either owned or leased, or are occupied under facilities-use contracts with the U.S. Government.
At December 31, 2017, our operating segments had significant operations at the following locations(1):
Flight Systems Group | Brigham City/Promontory, UT; Clearfield, UT; Magna, UT; Chandler, AZ; Dulles, VA; Iuka, MS; Dayton, OH; Vandenberg Air Force Base, CA; Wallops Island, VA; Huntsville, AL | |
Defense Systems Group | Mesa, AZ; Northridge, CA; Elkton, MD; Elk River, MN; Plymouth, MN; Independence, MO; Fort Worth, TX; Radford, VA; Rocket Center, WV | |
Space Systems Group | Dulles, VA; Beltsville, MD; Gilbert, AZ; Greenbelt, MD; Commerce, CA; Goleta, CA; San Diego, CA; Wallops Island, VA; Palestine, TX; Pasadena, CA | |
Corporate | Dulles, VA; Plymouth, MN; Minnetonka, MN |
(1) We occupy a number of small facilities in countries around the world which are not included above.
Land. We also use land that we own or lease for assembly, test and evaluation in Brigham City, Corrine and Magna, UT, which is used by Flight Systems Group; and in Elk River, MN, and Socorro, NM, which is used by Defense Systems Group.
Our personnel operate in certain other facilities that are not owned or operated by us, including: Kennedy Space Center, Cape Canaveral, FL and Picatinny Arsenal, Picatinny, NJ. The square footage of these facilities is not included in the table below.
Our properties are well maintained and in good operating condition and are sufficient to meet our near-term operating requirements.
23
The following table summarizes the floor space, in thousands of square feet, occupied by each operating segment as of December 31, 2017:
Owned | Leased | Government Owned (1) | Total | ||||||||
Flight Systems Group | 5,237 | 3,609 | 536 | 9,382 | |||||||
Defense Systems Group | 655 | 1,175 | 4,766 | 6,596 | |||||||
Space Systems Group | 270 | 1,141 | 23 | 1,434 | |||||||
Corporate | — | 46 | — | 46 | |||||||
Total | 6,162 | 5,971 | 5,325 | 17,458 | |||||||
Percentage of total | 35 | % | 34 | % | 31 | % | 100 | % |
(1) These facilities are occupied under facilities contracts that generally require us to pay for all utilities, services and maintenance costs.
ITEM 3. LEGAL PROCEEDINGS
From time to time, we are subject to various legal proceedings, including lawsuits, which arise out of, and are incidental to, the conduct of our business. We do not consider any of such proceedings that are currently pending, individually or in the aggregate, to be material to our business or likely to result in a material adverse effect on our future operating results, financial condition or cash flows, notwithstanding that the unfavorable resolution of any matter may have a material effect on our net earnings in any particular quarter.
On April 29, 2016, US Space LLC filed a complaint against the Company and its subsidiary, ATK Space Systems Inc. in New York Supreme Court, alleging breach of contract and various other claims, and seeking unspecified damages, all related to ViviSat LLC, a former joint venture between the parties. The Company believes US Space’s claims are without merit. On May 27, 2016, the Company filed a countersuit in Loudoun County Circuit Court in the Commonwealth of Virginia (ATK Space Systems, Inc. and Orbital ATK, Inc. v. U.S. Space LLC, Case No. CL-101847) asserting claims for declaratory and injunctive relief against US Space LLC relating to ViviSat. The Company’s Virginia complaint alleged a failure of US Space to perform contractual obligations relating to obtaining financing for ViviSat, triggering certain rights of the Company that led to the dissolution of the venture. On November 11, 2016, the New York Supreme Court dismissed US Space’s New York case in its entirety. On January 6, 2017, US Space filed counterclaims against the Company, similar to its previous claims in its now-dismissed New York lawsuit. US Space’s initial counterclaims in the Virginia case sought damages of at least $125 million, but increased its damages demand to $385 million in the fourth quarter of 2017. A jury trial is currently ongoing. While the Company continues to believe that US Space’s counterclaims are without merit, the amount of the damages sought, if ever awarded, could be material to our cash flows and results of operations.
Securities Class Action. Seven purported class actions challenging the Merger were filed in the United States District Court for the Eastern District of Virginia, captioned Lickteig v. Orbital ATK, Inc., et al., filed October 11, 2017 (the "Lickteig Action"), Ayzin v. Orbital ATK, Inc., et al., filed October 13, 2017 (the "Ayzin Action"), Sedon v. Orbital ATK, Inc., et al., filed October 16, 2017 (the "Sedon Action"), Berg v. Orbital ATK, Inc., et al., filed October 16, 2017 (the "Berg Action"), Simnowitz v. Orbital ATK, Inc., et al., filed October 18, 2017 (the "Simnowitz Action"), Cramer v. Orbital ATK, Inc., et al., filed October 25, 2017 (the "Cramer Action"), and Donato v. Orbital ATK, Inc., et al., filed on November 7, 2017 (the "Donato Action" and collectively with the Lickteig Action, Ayzin Action, Sedon Action, Berg Action, Simnowitz Action and Cramer Action, the "Actions"). The Actions alleged certain violations of the Securities and Exchange Act of 1934 (the "Exchange Act"), as amended, and sought, among other things, damages, attorneys' fees and injunctive relief to prevent the Merger from closing. While the Company believed that the Actions lacked merit and that the disclosures set forth in the proxy statement complied fully with applicable law, in order to moot plaintiffs' unmeritorious disclosure claims, avoid nuisance and possible expense and provide additional information to our stockholders, the Company determined to voluntarily supplement the proxy statement, as set forth in the Company's Schedule 14A filed with the SEC on November 20, 2017. On November 20, 2017, the Ayzin Action, Sedon Action, Berg Action, Cramer Action and Donato Action were each voluntarily dismissed with prejudice as to the plaintiffs. On December 8, 2017, the Simnowitz Action was voluntarily dismissed with prejudice as to the plaintiff and on January 12, 2018, the Lickteig Action was voluntarily dismissed with prejudice as to the plaintiff. While each of the Actions have been voluntarily dismissed with prejudice as to the plaintiffs, additional plaintiffs may file lawsuits against the Company and/or its directors and officers in connection with the Merger.
24
On August 12, 2016, a putative class action complaint, naming the Company, our Chief Executive Officer and our Chief Financial Officer as defendants, was filed in the United States District Court for the Eastern District of Virginia (Steven Knurr, et al. v. Orbital ATK, Inc., No. 16-cv-01031 (TSE-MSN)). The class action complaint asserts claims on behalf of purchasers of Orbital ATK securities for violations of Sections 10(b) and 20(a) of the Exchange Act and Rule 10b-5 thereunder, arising out of allegedly false and misleading statements and the failure to disclose that: (i) the Company lacked effective control over financial reporting; and (ii) as a result, the Company failed to record an anticipated loss on its long-term contract with the U.S. Army to manufacture and supply small-caliber ammunition at the U.S. Army's Lake City Army Ammunition Plant. On April 24, 2017 and October 10, 2017, the plaintiffs filed amended complaints naming additional defendants and asserting claims for violations of additional sections of the Exchange Act and alleged false and misleading statements in the Company’s Form S-4 filed with the SEC relating to the Orbital-ATK Merger. The complaint seeks an award of damages, an award of reasonable costs and expenses at trial, including counsel and expert fees, and an award of such other relief as deemed appropriate by the Court.
SEC Investigation. The SEC is conducting a non-public investigation relating to our historical accounting practices as a result of the prior restatement of the Company's unaudited condensed consolidated financial statements for the quarterly periods ended July 5, 2015 and October 4, 2015 as described in the Company's Amendment to the Transition Report on Form 10-K for the nine-month transition period ending December 31, 2015 filed with the SEC on March 15, 2016. The Company has also voluntarily self-reported to the SEC regarding matters pertaining to the Restatement described in the Company's Amendment to the Transition Report on Form 10-K for the nine-month transition period ending December 31, 2015 filed on February 24, 2017. The Company is cooperating fully with the SEC in connection with these matters.
Other U.S. Government Investigations. We are also subject to U.S. Government investigations from which civil, criminal or administrative proceedings could result. Such proceedings could involve claims by the U.S. Government for fines, penalties, compensatory and treble damages, restitution and/or forfeitures. Under government regulations, a company, or one or more of its operating divisions or subdivisions, can also be suspended or debarred from government contracts, or lose its export privileges, based on the results of investigations. We believe, based upon all available information, that the outcome of any such pending government investigations will not have a material adverse effect on our operating results, financial condition or cash flows.
Environmental Liabilities. Our operations and ownership or use of real property are subject to a number of federal, state and local laws and regulations, including those for discharge of hazardous materials, remediation of contaminated sites and restoration of damage to the environment. Due in part to their complexity and pervasiveness, such laws and regulations have resulted in our being involved with a number of related legal proceedings, claims and remediation obligations. We routinely assess, based on in-depth studies, expert analyses and legal reviews, our contingencies, obligations and commitments for remediation of contaminated sites and past practices, including assessments of ranges and probabilities of recoveries from other responsible parties. Our policy is to accrue and charge to expense in the current period any identified exposures related to environmental liabilities based on estimates of investigation, cleanup, monitoring and resource restoration costs to be incurred.
We have been identified as a potentially responsible party ("PRP"), along with other parties, in several regulatory agency actions associated with hazardous waste sites. As a PRP, we may be required to pay a share of the costs of the investigation and clean-up of these sites. While uncertainties exist with respect to the amounts and timing of the ultimate environmental liabilities, based on currently available information, we have concluded that these matters, individually or in the aggregate, will not have a material adverse effect on our operating results, financial condition or cash flows.
We could incur substantial costs, including cleanup costs, resource restoration, fines and penalties or third-party property damage or personal injury claims, as a result of violations or liabilities under environmental laws or non-compliance with environmental permits. While environmental laws and regulations have not had a material adverse effect on our operating results, financial condition or cash flows in the past, and we have environmental management programs in place to mitigate these risks, it is difficult to predict whether they will have a material impact in the future.
The description of certain environmental matters contained in Part II, Item 7, "Management's Discussion and Analysis of Financial Condition and Results of Operations" under the heading "Contingencies" is incorporated herein by reference.
25
ITEM 4. MINE SAFETY DISCLOSURES
Not applicable.
26
PART II
ITEM 5. MARKET FOR REGISTRANT'S COMMON EQUITY, RELATED STOCKHOLDER MATTERS AND ISSUER PURCHASES OF EQUITY SECURITIES
Our common stock is listed and traded on the New York Stock Exchange under the symbol "OA." The following table presents the high and low sales prices of the common stock for the periods indicated:
Period | High | Low | ||||||
Year ended December 31, 2017 | ||||||||
Quarter ended December 31, 2017 | $ | 134.57 | $ | 131.50 | ||||
Quarter ended October 1, 2017 | $ | 133.16 | $ | 99.79 | ||||
Quarter ended July 2, 2017 | $ | 104.32 | $ | 95.31 | ||||
Quarter ended April 2, 2017 | $ | 102.11 | $ | 86.82 | ||||
Year ended December 31, 2016 | ||||||||
Quarter ended December 31, 2016 | $ | 89.39 | $ | 71.52 | ||||
Quarter ended October 2, 2016 | $ | 89.43 | $ | 67.04 | ||||
Quarter ended July 3, 2016 | $ | 90.98 | $ | 82.11 | ||||
Quarter ended April 3, 2016 | $ | 94.92 | $ | 74.31 |
The number of holders of record of our common stock at February 16, 2018 was 4,596.
During the year ended December 31, 2017, the Company paid four quarterly dividends of $0.32 per share, totaling approximately $74 million. In January 2018, our Board of Directors approved a quarterly dividend to be paid in the first quarter of 2018 of $0.32 per share, totaling approximately $18 million. During the year ended December 31, 2016, the Company paid four quarterly dividends of $0.30 per share, totaling approximately $70 million. Under the terms of the Merger Agreement, we are permitted to, and intend to, continue paying a $0.32 per share quarterly cash dividend until the closing of the transaction. However, we are not permitted to increase the per share dividend amount under the terms of the Merger Agreement.
We cannot be certain that we will continue to declare dividends in the future and, as such, the amount and timing of any future dividends are not determinable. Our dividend policy is reviewed by our Board of Directors in light of relevant factors, including our earnings, liquidity position, financial condition, capital requirements and credit ratings, as well as the extent to which the payment of cash dividends may be restricted by covenants contained in our instruments, including our 5.25% Senior Notes due 2021, 5.50% Senior Notes due 2023 and Senior Credit Facility (as described under "Liquidity and Capital Resources" in Part II, Item 7, "Management's Discussion and Analysis of Financial Condition and Results of Operations" of this report).
The discussion of limitations upon the payment of dividends as a result of the indentures governing our debt instruments as discussed in Part II, Item 7, "Management's Discussion and Analysis of Financial Condition and Results of Operations" under the heading "Long-term Debt and Credit Facilities" is incorporated herein by reference.
27
Equity Compensation Plan Information
The following table gives information about our common stock that may be issued upon the exercise of options, warrants and rights under each of our existing equity compensation plans at December 31, 2017:
Plan category | Number of securities to be issued upon exercise of outstanding options, warrants and rights (a) | Weighted-average exercise price of outstanding options, warrants and rights (b) | Number of securities remaining available for future issuance under equity compensation plans (excluding securities reflected in column (a)) (c) | |||||||
Equity compensation plans approved by security holders: | ||||||||||
1990 Equity Incentive Plan (1) | ||||||||||
Deferred Compensation (2) | 13,269 | |||||||||
Non-Employee Director Restricted Stock Plan (1) | ||||||||||
Deferred Compensation (2) | 6,924 | |||||||||
2005 Stock Incentive Plan (1) | ||||||||||
Stock Options | 116,405 | $ | 57.86 | |||||||
Performance Awards (4) | 151,656 | |||||||||
Deferred Compensation (2) | 55,309 | |||||||||
2015 Stock Incentive Plan (3) | 2,084,273 | |||||||||
Stock Options | 129,464 | $ | 85.79 | |||||||
Performance Awards (4) | 265,974 | |||||||||
Deferred Compensation (2) | 17,774 | |||||||||
2016 Employee Stock Purchase Plan (5) | 1,781,318 | |||||||||
Total | 756,775 | $ | 72.56 | 3,865,591 |
_________________________________________
(1) | No additional awards may be granted under this plan. |
(2) | Shares reserved for payment of deferred stock units in accordance with the terms of the plan. |
(3) | Under the 2015 Stock Incentive Plan, a total of 3,750,000 shares were authorized for awards. However, the plan includes a fungible share counting provision, under which "full-value awards" (i.e., awards other than stock options and stock appreciation rights) are counted against the reserve of shares available for issuance under the plan as 2.5 shares for every one share actually issued in connection with the award. No more than 5% of the shares available for awards under the plan may be granted to our non-employee directors in the aggregate. |
(4) | Shares reserved for issuance in connection with outstanding performance awards. The amount shown assumes the maximum payout of the performance shares based on achievement of the highest level of performance. The actual number of shares to be issued depends on the performance levels achieved for the respective performance periods. |
(5) | Under the 2016 Employee Stock Purchase Plan ("ESPP"), a total of 2,000,000 shares were authorized for issuance. In connection with the Merger, the ESPP was suspended as of October 1, 2017. |
28
ISSUER PURCHASES OF EQUITY SECURITIES
Period | Total Number of Shares Purchased (1) | Average Price Paid per Share | Total Number of Shares Purchased as Part of Publicly Announced Program (2) | Amount Available for Future Share Repurchases Under the Plans or Programs (in millions) | |||||||||
October 2 - October 29 | 319 | $ | 133.21 | — | |||||||||
October 30 - November 26 | 196 | $ | 132.93 | — | |||||||||
November 27 - December 31 | — | $ | — | — | |||||||||
Quarter ended December 31, 2017 | 515 | $ | 133.10 | — | $ | 227 |
_________________________________________
(1) | Represents shares withheld to pay taxes upon vesting of shares of restricted stock and restricted stock units or payment of performance shares that were granted under our incentive compensation plans. |
(2) | During 2015, the Board of Directors approved a stock repurchase program that authorized the repurchase of up to the lesser of $250 million or 3.25 million shares through December 31, 2016, which was subsequently increased during 2016 to the lesser of $300 million or 4.0 million shares through March 2017. In February 2017, the Board of Directors further increased the amount authorized for repurchase to $450 million, removed the share quantity limitation and extended the repurchase period through March 31, 2018. We repurchased 230,918 shares for $23 million during the year ended December 31, 2017. In connection with the Merger, the Company halted its share repurchase program. |
29
STOCKHOLDER RETURN PERFORMANCE GRAPH
The graph below compares the cumulative total stockholder return on the Company's common stock during the period from March 31, 2013 through December 31, 2017, with the Standard & Poor's Composite 500 Index, (a broad equity market index) and the Dow Jones U.S. Aerospace and Defense Index (a published industry index) for the same period.
The comparison assumes that on April 1, 2013, $100 was invested in the Company's common stock (at the closing price on the previous trading day) and in each of the indexes. The comparison assumes that all cash dividends were reinvested and takes into account the value of the Vista Outdoor shares distributed to stockholders in the Distribution as if it occurred prior to March 31, 2013. The graph indicates the dollar value of each hypothetical $100 investment at March 31, 2014 and 2015, and at December 31, 2015, 2016 and 2017.
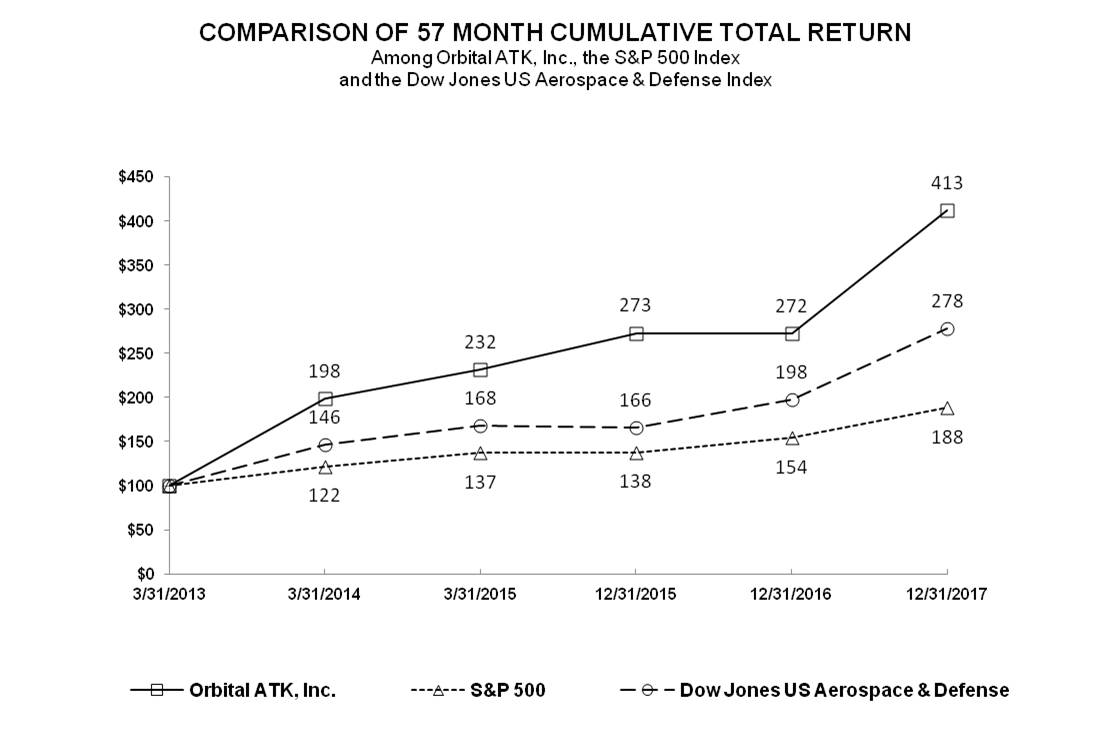
30
ITEM 6. SELECTED FINANCIAL DATA
Results for the periods after fiscal 2014 are not comparable to fiscal 2014 due to the Orbital-ATK Merger and Distribution, as described in Note 4, Mergers and Divestiture, to the accompanying consolidated financial statements in Part II, Item 8.
Year Ended December 31, | Nine Months Ended | Year Ended March 31, | |||||||||||||||||
(in millions, except per share data) | 2017 | 2016 | December 31, 2015 | 2015 | 2014 | ||||||||||||||
(1) | (2) | (3) | (4) | ||||||||||||||||
Results of Operations: | |||||||||||||||||||
Sales | $ | 4,764 | $ | 4,455 | $ | 3,391 | $ | 3,113 | $ | 2,891 | |||||||||
Gross profit | 1,065 | 985 | 674 | 701 | 290 | ||||||||||||||
Income (loss) from continuing operations, before interest, income taxes and noncontrolling interest | 529 | 472 | 333 | 223 | (59 | ) | |||||||||||||
Income (loss) from continuing operations of Orbital ATK, Inc. | 310 | 293 | 185 | 70 | (64 | ) | |||||||||||||
Income from discontinued operations | — | — | 1 | 125 | 181 | ||||||||||||||
Net income attributable to Orbital ATK, Inc. | $ | 310 | $ | 293 | $ | 186 | $ | 195 | $ | 117 | |||||||||
Earnings per common share attributable to Orbital ATK, Inc.: | |||||||||||||||||||
Basic: | |||||||||||||||||||
Income (loss) from continuing operations | $ | 5.39 | $ | 5.05 | $ | 3.12 | $ | 1.96 | $ | (2.03 | ) | ||||||||
Income from discontinued operations | $ | — | $ | — | $ | 0.02 | $ | 3.53 | $ | 5.73 | |||||||||
Diluted: | |||||||||||||||||||
Income (loss) from continuing operations | $ | 5.34 | $ | 5.01 | $ | 3.09 | $ | 1.93 | $ | (1.97 | ) | ||||||||
Income from discontinued operations | $ | — | $ | — | $ | 0.02 | $ | 3.46 | $ | 5.55 | |||||||||
Cash dividends per common share | $ | 1.28 | $ | 1.20 | $ | 0.78 | $ | 1.28 | $ | 1.10 | |||||||||
Consolidated Balance Sheet Data: | |||||||||||||||||||
Total assets | $ | 5,666 | $ | 5,418 | $ | 5,324 | $ | 5,478 | $ | 5,925 | |||||||||
Long-term debt (including current portion) | $ | 1,401 | $ | 1,438 | $ | 1,476 | $ | 1,572 | $ | 2,069 |
(1) | Calendar 2017 results included $10 million of acquisition transaction expenses related to the pending acquisition by Northrop Grumman. |
(2) | The nine month period ended December 31, 2015 results include a $50 million gain on settlement of a dispute with a supplier pertaining to the Antares rocket used in the CRS-1 contract. |
(3) | Fiscal 2015 results include $35 million of transaction fees for advisory, legal and accounting services in connection with the Distribution and the Orbital-ATK Merger and a $25 million litigation charge pertaining to a Raytheon lawsuit settlement. |
(4) | Fiscal 2014 results include a $342 million forward loss contract reserve recorded in the second quarter related to our long-term contract (the "Lake City Contract") with the U.S. Army to manufacture and supply small-caliber ammunition at the U.S. Army’s Lake City Army Ammunition Plant. |
31
ITEM 7. MANAGEMENT'S DISCUSSION AND ANALYSIS OF FINANCIAL CONDITION AND RESULTS OF OPERATIONS
(amounts in millions except share and per share data or unless otherwise indicated)
Forward-Looking Information is Subject to Risk and Uncertainty
Some of the statements made and information contained in this report, excluding historical information, are "forward-looking statements" as defined in the Private Securities Litigation Reform Act of 1995. Forward-looking statements give our current expectations or forecasts of future events. Words such as "may," "will," "expected," "intend," "estimate," "anticipate," "believe," "project" or "continue," and similar expressions are used to identify forward-looking statements. From time to time, we also may provide oral or written forward-looking statements in other materials released to the public. Any or all forward-looking statements in this report and in any public statements we make could be materially different. They can be affected by assumptions used or by known or unknown risks or uncertainties. Consequently, no forward-looking statements can be guaranteed. Actual results may vary materially. You are cautioned not to place undue reliance on any forward-looking statements. You should also understand that it is not possible to predict or identify all such factors and you should not consider the following list to be a complete statement of all potential risks and uncertainties. Any change in the following factors may impact the achievement of results:
• | the risk that the pending acquisition by Northrop Grumman may not be completed in a timely manner or at all, which may adversely affect our business and the price of our common stock, |
• | the failure to satisfy any of the conditions to the consummation of the pending acquisition on a timely basis, including the receipt of certain governmental and regulatory approvals, |
• | the occurrence of any circumstance that could give rise to the termination of the Merger Agreement, |
• | reductions or changes in programs administered by the National Aeronautics and Space Administration ("NASA") or in U.S. Government military spending, timing of payments and budgetary policies, including impacts of sequestration under the Budget Control Act of 2011, and sourcing strategies, |
• | intense competition for U.S. Government contracts and programs, |
• | increases in costs, which we may not be able to react to due to the nature of our U.S. Government contracts, |
• | changes in cost and revenue estimates and/or timing of programs, |
• | the potential termination of U.S. Government contracts and the potential inability to recover termination costs, |
• | other risks associated with U.S. Government contracts that might expose us to adverse consequences, |
• | laws, rules and regulations applicable to us, including procurement and import-export control, |
• | reduction or change in demand and manufacturing costs for ammunition, |
• | the manufacture and sale of products that create exposure to potential product liability, warranty liability or personal injury claims and litigation, |
• | risks associated with expansion into new and adjacent markets, |
• | greater risk associated with international business, including foreign currency exchange rates and fluctuations in those rates, |
• | federal and state regulation of defense products and ammunition, |
• | costs of servicing our debt, including cash requirements and interest rate fluctuations, |
• | actual pension and other postretirement plan asset returns and assumptions regarding future returns, discount rates, service costs, mortality rates and health care cost trend rates, |
• | security threats, including cybersecurity and other industrial and physical security threats, and other disruptions, |
32
• | supply, availability and costs of raw materials and components, including commodity price fluctuations, |
• | performance of our subcontractors, |
• | development of key technologies and retention of a qualified workforce, |
• | the performance of our products, |
• | fires or explosions at any of our facilities, |
• | government investigations and audits, |
• | environmental laws that govern current and past practices and rules and regulations, noncompliance with which may expose us to adverse consequences, |
• | impacts of financial market disruptions or volatility to our customers and vendors, |
• | unanticipated changes in the tax provision or exposure to additional tax liabilities, including as a result of the recent tax law legislation, the Tax Cuts and Jobs Act (the "Tax Act") signed into law in December 2017 and |
• | the costs and ultimate outcome of litigation matters, government investigations and other legal proceedings, including those related to the restatement of our previously issued financial results. |
This list of factors is not exhaustive, and new factors may emerge or changes to the foregoing factors may occur that would impact our business. Additional information regarding these and other factors is contained in Part I, Item 1A, "Risk Factors," of this report and may also be contained in our filings with the Securities and Exchange Commission on Forms 10-Q and 8-K. All such risk factors are difficult to predict, contain material uncertainties that may affect actual results and may be beyond our control.
Executive Summary
We are an aerospace and defense products company and supplier of products to the U.S. Government, allied nations, prime contractors and other customers. Our main products include launch vehicles and related propulsion systems, satellites and associated components and services, composite aerospace structures, tactical missiles, subsystems and defense electronics and precision weapons, armament systems and ammunition. We are headquartered in Dulles, Virginia and have operating locations throughout the United States.
On September 17, 2017, we entered into an Agreement and Plan of Merger (the "Merger Agreement") with Northrop Grumman Corporation ("Northrop Grumman") and Neptune Merger, Inc., a wholly owned subsidiary of Northrop Grumman ("Sub"), pursuant to which Northrop Grumman will acquire the Company for a purchase price of $134.50 per share in cash (the "Merger").
Closing of the Merger is expected to occur during the first half of 2018, subject to customary closing conditions and obtaining required regulatory approvals. The stockholders of the Company voted in favor of approving the Merger Agreement at a special meeting held on November 29, 2017. In February 2018, the European Commission informed the parties that it would not oppose the Merger and declared it compatible with the European Union internal market under the applicable regulation. This is one of two required regulatory approvals.
The other required regulatory approval is the expiration or termination of the waiting period under the Hart-Scott-Rodino Antitrust Improvements Act (the "HSR Act"). On December 6, 2017, the Company received a request for additional information (the "second request") from the Federal Trade Commission ("FTC"). The effect of the second request is to extend the waiting period imposed by the HSR Act until 30 days after both the Company and Northrop Grumman have substantially complied with the request, unless that period is extended voluntarily by the parties or terminated sooner by the FTC.
At the effective time of the Merger, each outstanding share of the Company's common stock, other than shares owned by the Company, Northrop Grumman or Sub (which will be canceled) and appraisal shares, will be converted into the right to receive $134.50 in cash, without interest and less any applicable withholding taxes.
On February 9, 2015, we completed the spin-off and distribution (the "Distribution") of our former Sporting Group to our stockholders as a new public company called Vista Outdoor Inc. ("Vista Outdoor"). As a result, the Sporting Group is reported as discontinued operations. Immediately following the distribution of our former Sporting Group, we combined with Orbital through the merger of a company subsidiary with Orbital.
33
We conduct business in three segments:
• | Flight Systems Group develops launch vehicles that are used as small- and medium-class space launch vehicles to place satellites into earth orbit and escape trajectories, interceptor and target vehicles for missile defense systems and suborbital launch vehicles that place payloads into a variety of high-altitude trajectories. The group also develops and produces medium- and large-class rocket propulsion systems for human and cargo launch vehicles, strategic missiles, missile defense interceptors and target vehicles. Additionally, Flight Systems Group operates in the military and commercial aircraft and launch structures markets. |
• | Defense Systems Group develops and produces small-, medium- and large-caliber military ammunition, propulsion systems for tactical missiles and missile defense applications, strike weapons, precision weapons and munitions, high-performance gun systems, aircraft survivability systems, fuzes and warheads, energetic materials and special mission aircraft. |
• | Space Systems Group develops and produces small- and medium-class satellites that are used to enable global and regional communications and broadcasting, conduct space-related scientific research and perform activities related to national security. In addition, Space Systems Group develops and produces human-rated space systems for earth orbit and deep space exploration, including cargo delivery to the International Space Station. This group is also a provider of spacecraft components and subsystems as well as specialized engineering and operations services to U.S. government agencies. |
Below is a table that represents each segment's earnings and respective operating margins that contribute to the overall performance of the Company:
Year Ended December 31, 2017 | |||||||||||
Flight Systems Group | Defense Systems Group | Space Systems Group | |||||||||
Sales(1) | $ | 1,681 | $ | 1,968 | $ | 1,284 | |||||
Income From Operations Before Interest, Income Taxes and Noncontrolling Interest(1) | $ | 211 | $ | 193 | $ | 142 | |||||
Operating Margin | 13 | % | 10 | % | 11 | % | |||||
(1) Sales and total income from operations before interest, income taxes and noncontrolling interest listed above does not include the corporate segment intercompany elimination of sales of ($169) million and intercompany profit elimination and certain costs including unallowables retained in the corporate segment of ($17) million. |
Operating margins differ among the Company's three operating segments due to several factors, including, but not limited to, the mix of contract types, competitive positioning and pricing, complexity of our deliverables and the impact of program execution. The operating margin in our Defense Systems Group is lower than the operating margins of the Space Systems Group and Flight Systems Group primarily due to the Company's small-caliber ammunition contract with the U.S. Army which operates in a forward loss position. As a result, this contract has no margin, which, given the size of the contract, lowers the overall Defense Systems Group's margin.
Fiscal Year
In March 2015, we changed our fiscal year from the period beginning on April 1 and ending on March 31 to the period beginning on January 1 and ending on December 31. We refer in this report to the nine-month period beginning on April 1, 2015 and ending on December 31, 2015 as the "2015 transition period." All fiscal years after December 31, 2015 are for the calendar twelve months ended December 31. We refer in this report to the period beginning on January 1, 2017 and ending on December 31, 2017 as "calendar 2017" or "2017" and the period beginning on January 1, 2016 and ending on December 31, 2016 as "calendar 2016" or "2016."
34
Outlook
U.S Government Business — Our business with the U.S. Government comprised approximately 73% of our sales in 2017. U.S. Government contracts are dependent on the continuing availability of Congressional appropriations. Congress usually appropriates funds for a given program on a government fiscal year ("GFY") basis even though contract performance may take more than one year. As a result, at the outset of a major program, the contract is usually incrementally funded, and additional monies are normally committed to the contract by the procuring agency only as Congress makes appropriations for future GFYs. In addition, most U.S. Government contracts are subject to modification if funding is changed. Any failure by Congress to appropriate additional funds to any program in which we participate, or any contract modification as a result of funding changes, could materially delay or terminate the program. This could have a material adverse effect on our operating results, financial condition or cash flows.
The government budget structure has been constrained by the 2011 Budget Control Act, which provided for a reduction of the U.S. Department of Defense ("DoD") topline budget by approximately $490 billion over 10 years starting in GFY 2012, and subsequent amendments that continue to limit DoD spending. Over the past few years, including during the current fiscal year, the U.S. Government frequently has been operating under continuing resolutions rather than approved budgets. During such periods when regular appropriation bills have not yet been passed, we could experience delays in orders due to reduced funding; however, our key programs have continued to be supported and funded.
The recent agreement in Congress and President Trump’s Administration on a two-year budget package is expected to lift caps on defense spending for GFY 2018 and 2019 and provide a significant increase in defense spending during that period, which could present opportunities for the Company. NASA budgets in the near term may include material cuts to proposed earth science programs but we expect support for existing programs and that NASA's commitment to the International Space Station and related CRS programs will continue. We also expect funding for the Space Launch System and Orion Programs to be maintained.
Commercial and International Business — Our commercial businesses, consisting primarily of communication satellite and aircraft structure sales, as well as ammunition sales to Vista Outdoor, were mixed in 2017, with ammunition sales and commercial satellites continuing a downward trend and aircraft structures sales up. Industry-wide, new orders for geosynchronous satellites continued to be soft in 2017, a trend that is expected to persist in the near term. This weakness, however, continues to be offset to a large extent by demand in the NASA and DoD satellite markets. We continue to emphasize international business as a key element of growth in our Defense Systems segment, as defense spending by U.S. allies continues to present opportunities for us.
The U.S. aerospace and defense industry has experienced significant changes over recent years. Our management believes that the key to our continued success is to focus on providing innovative, reliable and affordable space, defense and aviation systems. We continue to position ourselves where management believes there will be strong defense and civil government funding and commercial interest, including an emphasis on international defense business and other potential growth areas.
Critical Accounting Policies
Our discussion and analysis of our financial condition and results of operations are based upon our consolidated financial statements, which have been prepared in accordance with accounting principles generally accepted in the United States of America ("GAAP"). In preparing the consolidated financial statements, we make estimates and judgments that affect the reported amounts of assets, liabilities, sales, expenses, and related disclosure of contingent assets and liabilities. We re-evaluate our estimates on an on-going basis. Our estimates are based on historical experience and on various other assumptions that are believed to be reasonable under the circumstances. Actual results may differ from these estimates under different assumptions or conditions.
We believe the following are our critical accounting policies that affect our more significant judgments and estimates used in the preparation of our consolidated financial statements.
35
Revenue Recognition
A substantial portion of our sales come from contracts with agencies of the U.S. Government and its prime contractors and subcontractors. As the various U.S. Government customers, including the U.S. Navy, U.S. Army, NASA and the U.S. Air Force make independent purchasing decisions, we do not generally regard the U.S. Government as one customer. Instead, we view each agency as a separate customer.
Long-term Contracts — The majority of our sales are from long-term contracts, which are accounted for using the percentage-of-completion method. Accounting for contracts under the percentage-of-completion method requires judgment relative to assessing risks and estimating contract revenues and costs. Profits expected to be realized on contracts are based on management's estimates of total contract value and costs at completion. Changes in estimates of contract sales, costs or profits are recognized using the cumulative catch-up method of accounting. The cumulative effect of a change in estimate is recognized in the period a change in estimate occurs. The effect of the changes on future periods of contract performance is recognized as if the revised estimate had been used since contract inception or, in the case of contracts acquired in business combinations, from the date of acquisition. In the period in which it is determined that a loss will be incurred on a contract, the entire amount of the estimated loss, based on gross profit along with general and administrative costs, is charged to cost of sales.
Changes in contract estimates occur for a variety of reasons, including changes in contract scope, unforeseen changes in contract cost estimates due to unanticipated cost growth or risks affecting contract costs and/or the resolution of contract risks at lower costs than anticipated, as well as changes in contract overhead costs over the performance period. Changes in estimates could have a material effect on the Company's consolidated financial position or results of operations.
Generally, favorable changes in contract estimates recognized using the cumulative catch-up method of accounting represent margin improvement on programs where either estimated cost at completion was lower than previously estimated or a change in contract scope on a program caused a higher profit rate. Conversely, the unfavorable changes in contract estimates represent margin declines on programs where either estimated cost at completion was higher than previously estimated or a change in contract scope on a program caused a lower profit rate.
The favorable and unfavorable changes in contract estimates recognized using the cumulative catch-up method of accounting are as follows (in millions):
Year Ended | Nine Months Ended | |||||||||||
December 31, 2017 | December 31, 2016 | December 31, 2015 | ||||||||||
Gross favorable adjustments | $ | 250 | $ | 247 | $ | 136 | ||||||
Gross unfavorable adjustments | (145 | ) | (166 | ) | (98 | ) | ||||||
Net adjustments | $ | 105 | $ | 81 | $ | 38 |
For the year ended December 31, 2017, the Company recognized favorable cumulative catch-up adjustments due to higher profit expectations on programs in the Aerospace Structures division, the Propulsion Systems division and the Launch Vehicles division, within our Flight Systems Group; the Space Components division, the Satellite Systems division and the Advanced Programs division, within our Space Systems Group; and the Armament Systems division and the Missile Products division, within our Defense Systems Group, due to better performance resulting from risk retirement and lower cost than had previously been estimated. The Company recognized unfavorable cumulative catch-up adjustments in the Aerospace Structures division and the Propulsion Systems division, within our Flight Systems Group; the Satellite Systems division, within our Space Systems Group; and the Armament Systems division within our Defense Systems Group, primarily due to higher costs than had previously been estimated.
For the year ended December 31, 2016, the Company recognized favorable cumulative catch-up adjustments due to higher profit expectations on programs in the Launch Vehicles division, within our Flight Systems Group, and the Advanced Programs division, within our Space Systems Group, due to better performance resulting from risk retirement and lower costs than had previously been estimated. The Company recognized unfavorable cumulative catch-up adjustments primarily due to (i) in the Aerospace Structures division, within our Flight Systems Group, an increase in estimated costs at completion, (ii) in the Satellite Systems division, within our Space Systems Group, higher costs than had previously been estimated, and (iii) in the Defense Electronics division, within our Defense Systems Group, a reduction in a program's estimated revenue.
36
For the nine months ended December 31, 2015, the Company recognized favorable cumulative catch-up adjustments due to higher profit expectations on programs in the Aerospace Structures and Propulsion Systems divisions, within our Flight Systems Group, and the Armament Systems and Missile Products divisions, within our Defense Systems Group, due to better performance resulting from risk retirement and lower costs than had previously been estimated. The Company recognized unfavorable cumulative catch-up adjustments in the Aerospace Structures division, within our Flight Systems Group, and the Armament Systems, Missile Products and Defense Electronics divisions, within our Defense Systems Group, due to higher costs than had previously been estimated.
Contracts may contain provisions to earn incentive and award fees if specified targets are achieved as well as penalty provisions related to performance. Incentive and award fees and penalties that can be reasonably estimated and are probable are recorded over the performance period of the contract. Incentive and award fees that cannot be reasonably estimated are recorded when awarded.
Other — Sales not recognized under the long-term contract method are recognized when persuasive evidence of an arrangement exists, the product has been delivered and legal title and all risks of ownership have been transferred, written contract and sales terms are complete, customer acceptance has occurred and payment is reasonably assured. Sales are reduced for allowances and price discounts.
Employee Benefit Plans
Defined Benefit Pension Plans. Our noncontributory defined benefit pension plans include the following legacy Alliant Techsystems Inc. plans: "Alliant Techsystems Inc. Pension and Retirement Plan" and "Thiokol Propulsion Pension Plan" (the "ATK Plans") and the legacy Orbital plans: "Fairchild Bargained Plan" and "Fairchild Space and Defense Plan" (the "Orbital Plans"). The Orbital Plans were merged into the Alliant Techsystems Inc. Pension and Retirement Plan on December 31, 2015 and the combined plan's name was changed to the Orbital ATK, Inc. Pension and Retirement Plan. The Company's ongoing defined benefit pension plans are the "Orbital ATK, Inc. Pension and Retirement Plan" and the "Thiokol Propulsion Pension Plan" (the "Orbital ATK Plans").
ATK Plans — The ATK Plans are noncontributory defined benefit pension plans that cover substantially all legacy ATK employees hired prior to January 1, 2007. Eligible legacy ATK non-union employees hired on or after January 1, 2007 and certain union employees are not covered by a defined benefit plan but receive an employer contribution through a defined contribution plan. Prior to July 1, 2013 (January 1, 2014, January 1, 2015 and April 1, 2016 for certain union groups), the ATK Plans provided either pension benefits based on employee annual pay levels and years of credited service or stated amounts for each year of credited service. Effective July 1, 2013 and at later dates for certain collective bargaining agreements, pension benefits were frozen and a new cash balance formula applicable to pay and service was implemented. The cash balance formula provides each impacted employee with pay credits based on the sum of that employee's age plus years of pension service as of December 31 of each calendar year, plus 4% annual interest credits. The Orbital Plans were frozen in 1994 and no pension benefits are being accrued by those employees. The Company funds the Orbital ATK Plans in accordance with federal requirements calculated using appropriate actuarial methods. Depending on the plan they are covered by, employees generally vest after three or five years. Plan assets are held in a trust and are invested in a diversified portfolio of equity investments, fixed income investments, real estate, timber, energy investments, hedge funds, private equity and cash. For certain plan assets where the fair market value is not readily determinable, estimates of the fair value are determined using the best available information including the most recent audited financial statements.
We also sponsor nonqualified supplemental executive retirement plans which provide certain executives and highly compensated employees the opportunity to receive pension benefits in excess of those payable through tax-qualified pension plans. We implemented similar changes as those noted above to our nonqualified supplemental executive retirement plans for certain highly compensated employees.
We recorded pension expense for the Orbital ATK Plans of $69 million for the year ended December 31, 2017, compared to $64 million for the year ended December 31, 2016, an increase of $5 million. The expense related to these Orbital ATK Plans is calculated based upon a number of actuarial assumptions, including the expected long-term rate of return on plan assets, the discount rate and the rate of compensation increase. The following table sets forth our assumptions used in determining pension expense:
37
Projected 2018 | Year Ended December 31, 2017 | Year Ended December 31, 2016 | Nine Months Ended December 31, 2015 | ||||||||
Expected long-term rate of return on plan assets | 7.00 | % | 7.00 | % | 7.25 | % | 7.25 | % | |||
Discount rate | 3.65 | % | 4.14 | % | 4.40 | % | 3.90 | % | |||
Rate of compensation increase: | |||||||||||
Union | 2.90 | % | 3.11 | % | 3.13 | % | 3.66 | % | |||
Salaried | 3.51 | % | 3.56 | % | 3.60 | % | 3.14 | % |
In developing the expected long-term rate of return assumption, we consider input from our actuaries and other advisors, annualized returns of various major indices over a long-term time horizon and our own historical 5-year and 10-year compounded investment returns. The expected long-term rate of return of 7.00% used in the year ended December 31, 2017 for the Orbital ATK Plans was based on an asset allocation range of 20 - 45% in public equity investments, 35 - 50% in fixed income investments, 0 - 10% in real estate investments,15 - 30% collectively in hedge fund and private investments and 0 - 6% in cash investments. The actual return in any fiscal year will likely differ from our assumption, but our estimate of its return is based on long-term projections and historical results. Therefore, any variance in a given year does not necessarily indicate that the assumption should be changed.
We calculate the equivalent weighted average discount rate as the singular interest rate that results in the same total present value from the stream of future cash flows as the projected benefit obligation ("PBO") at December 31, 2017. The weighted average discount rate was 3.65%, 4.14% and 4.40% at December 31, 2017, December 31, 2016 and December 31, 2015, respectively, for the qualified plans, and 3.33%, 3.63% and 3.85% for the nonqualified supplemental executive retirement plan. The yield curve used to determine the PBO at year end impacts the following year's pension expense, through the calculation of interest cost and service cost items.
Future actual pension expense could vary significantly depending on future investment performance, changes in future discount rates, legally required plan changes and various other factors related to the populations participating in the Orbital ATK Plans. If the assumptions of the discount rate, compensation increase and/or expected rate of return for 2018 were different, the impact on 2018 expense would be as follows: each 0.25% change in the discount rate would change 2018 pension expense by approximately $6 million; each 0.25% change in the rate of compensation increase would change 2018 pension expense by an immaterial amount; and each 0.25% change in the expected rate of return on plan assets would change 2018 pension expense by approximately $6 million.
We base our determination of pension expense or income on a market-related valuation of assets, which reduces year-to-year volatility. This market-related valuation recognizes investment gains or losses over a five-year period from the year in which they occur. Investment gains or losses for this purpose are the difference between the expected return calculated using the market-related value of assets and the actual return based on the market-related value of assets. Since the market-related value of assets recognizes gains or losses over a five-year period, the future value of assets will be impacted as previously deferred gains or losses are recorded.
Effective January 1, 2016, the Company changed the approach used to measure service and interest costs for pension and other postretirement benefits. Prior to January 1, 2016, the Company measured service and interest costs utilizing a single weighted-average discount rate derived from the yield curve used to measure the plan obligations. The Company elected to measure service and interest costs by applying the specific spot rates along that yield curve to the plans' liability cash flows. The Company believes this approach provides a more precise measurement of service and interest costs by aligning the timing of the plans' forecasted cash flows to the corresponding spot rates on the yield curve. This change does not affect the measurement of plan obligations. The Company accounted for this change on a prospective basis as a change in accounting estimate, resulting in lower pension expense compared to the method used prior to January 1, 2016.
We made contributions to the qualified pension trust of $115 million during the year ended December 31, 2017. We are not required to make any contributions to meet the legally required minimum for 2018. We distributed $3 million under our supplemental executive retirement plans during the year ended December 31, 2017, and expect to make distributions directly to retirees of $4 million in 2018. A substantial portion of our plan contributions are recoverable from the U.S. Government as allowable indirect contract costs at amounts generally equal to the pension plan contributions, although not necessarily in the same year the contribution is made. Our funded pension status was approximately 78% at December 31, 2017.
38
Other Postretirement Benefits. We also provide postretirement health care benefits and life insurance coverage to certain employees and retirees. During the year ending December 31, 2016, the Company amended its retiree health care plan to provide coverage through a private exchange effective January 1, 2017. The exchange offers the retiree a broad choice of health care plans from which to choose. The Company will contribute fixed payments to a Health Retirement Account (HRA), when applicable, for those retirees that previously had subsidized health care coverage through the Company. The Company's contributions to the HRAs are retirees' funds to be spent on qualified health care premiums and eligible out-of-pocket expenses. This plan amendment caused a remeasurement that increased the Company's funded status by $39 million at December 31, 2016 and will reduce expenses recorded in future periods.
The following table sets forth our assumptions used to determine net periodic benefit cost for other postretirement benefit ("PRB") plans:
Projected 2018 | Year Ended December 31, 2017 | Year Ended December 31, 2016 | Nine Months Ended December 31, 2015 | ||||||||
Expected long-term rate of return on Plan assets: | |||||||||||
Held solely in fixed income investments | 4.00 | % | 4.00 | % | 4.00 | % | 5.00% / 6.25% | ||||
Held in pension master trust and fixed income investments | 6.00 | % | 6.00 | % | 6.00 | % | 6.25 | % | |||
Discount rate | 3.36 | % | 3.63 | % | 3.98 | % | 3.55 | % | |||
Weighted-average initial health care cost trend rate | N/A | N/A | 6.10 | % | 6.10 | % |
Health care cost trend rates are set specifically for each benefit plan and design. Health care cost trend rates used to determine the net periodic benefit cost for employees during the year ended December 31, 2017, and health care cost ultimate trend rates used to determine future expense calculations, do not apply since we contribute fixed payments to the retiree HRA.
In developing the expected long-term rate of return assumption for other PRB plans, we consider input from actuaries, historical returns and annualized returns of various major indices over long periods. At December 31, 2017, approximately 52% of the assets were held in a 401(h) account held within the pension master trust and are invested in the same manner as the pension assets. The expected long-term rates of returns are based on the weighted average asset allocation between the assets held within the 401(h) and those held in fixed income investments.
We made other PRB plan contributions of $3 million in the year ended December 31, 2017 and expect to make contributions of approximately $4 million in 2018. A substantial portion of our PRB plan contributions are recoverable from the U.S. Government as allowable indirect costs at amounts generally equal to the plan contributions, although not necessarily in the same year the contribution is made.
The Medicare Prescription Drug, Improvement and Modernization Act of 2003 (the "Act") reduced our accumulated projected benefit obligation ("APBO") measured at December 31, 2005. One of our other PRB plans is actuarially equivalent to Medicare, but we do not believe that the subsidies it will receive under the Act will be significant. Because we believe that participation levels in our other PRB plans will decline, the impact to our results of operations in any period has not been and is not expected to be significant.
Income Taxes
Provisions for federal, state and foreign income taxes are calculated based on reported pre-tax earnings and current tax law. Such provisions differ from the amounts currently receivable or payable because certain items of income and expense are recognized in different time periods for financial reporting purposes than for income tax purposes. Significant judgment is required in determining income tax provisions and evaluating tax positions. We periodically assess our liabilities and contingencies for all periods that are currently open to examination or have not been effectively settled based on the most current available information. Where it is not more likely than not that our tax position will be sustained, we record the entire resulting tax liability and when it is more likely than not of being sustained, we record our best estimate of the resulting tax liability. Any applicable interest and penalties related to these positions are also recorded in the consolidated financial statements. To the extent our assessment of the tax outcome of these matters changes, such change in estimate will impact the income tax provision in the period of the change. It is our policy to record any interest and penalties related to income taxes as part of the income tax
39
expense for financial reporting purposes. Deferred tax assets related to carryforwards are reduced by a valuation allowance when it is not more likely than not that the amount will be realized before expiration of the carryforward period. As part of this analysis, we take into account the amount and character to determine if the carryforwards will be realized. Significant estimates are required for this analysis. Changes in the amounts of valuation allowance are recorded in the tax provision in the period when the change occurs. For information on the effect of the Tax Act, see Note 14, Income Taxes, to the consolidated financial statements included in Part II, Item 8, "Financial Statements and Supplementary Data" of this report.
Accounting for Goodwill
We test goodwill for impairment on the first day of the fourth quarter and upon the occurrence of events or changes in circumstances that indicate that the asset might be impaired. We determined that the reporting units for our goodwill impairment review are our operating segments, or components of an operating segment, that constitute a business for which discrete financial information is available, and for which segment management regularly reviews the operating results. We aggregate certain components or reporting units based upon an evaluation of the facts and circumstances, including the nature of products and services and the extent of shared assets and resources. As a result, we have seven reporting units.
The goodwill impairment test is performed using a two-step process. In the first step, we determine the estimated fair value of each reporting unit and compare it to the carrying value of the reporting unit, including goodwill. If the carrying amount of a reporting unit is higher than its estimated fair value, an indication of impairment exists and the second step must be performed in order to determine the amount of the impairment. In the second step, we must determine the implied fair value of the reporting unit's goodwill which is determined by allocating the fair value of the reporting unit in a manner similar to a purchase price allocation. The implied fair value is compared to the carrying amount and if the carrying amount of the reporting unit's goodwill exceeds the implied fair value of its goodwill, an impairment loss must be recognized for the excess.
The estimated fair value of each reporting unit was determined using both an income and market approach. The value estimated using a discounted cash flow model was generally weighted equally against the estimated value derived from a market approach that considers the guideline company and transaction methods if recent transactions were available for one of our seven reporting units. These market approach methods estimate the price reasonably expected to be realized from the sale of the company based on comparable companies and recent transactional data. The estimated fair value for each reporting unit substantially exceeded its respective carrying value.
In developing a discounted cash flow analysis, our assumptions about future revenues and expenses, capital expenditures and changes in working capital are based on our three-year plan, as approved by our Board of Directors, and assumes a terminal growth rate thereafter. A separate discount rate is determined for each reporting unit and these cash flows are then discounted to determine the fair value of the reporting unit.
Projecting discounted future cash flows requires us to make significant estimates regarding future revenues and expenses, projected capital expenditures, changes in working capital and the appropriate discount rate. The projections also take into account several factors including current and estimated economic trends and outlook, costs of raw materials, consideration of our market capitalization in comparison to the estimated fair values of our reporting units and other factors which are beyond our control. If the current economic conditions were to deteriorate, or if we were to lose a significant contract or business, causing a reduction in estimated discounted cash flows, it is possible that the estimated fair value of certain reporting units could fall below their carrying value resulting in the necessity to conduct additional goodwill impairment tests in future periods. We continually monitor the reporting units for impairment indicators and update assumptions used in the most recent calculation of the estimated fair value of a reporting unit as appropriate.
Results of Operations
In March 2015, we changed our fiscal year from the period beginning on April 1 and ending on March 31 to the period beginning on January 1 and ending on December 31. We believe that a reader’s understanding of our results of operations will be enhanced by review of a comparison between our audited results for the fiscal year ended December 31, 2016, referred to as calendar year 2016, and our unaudited results for the fiscal year ended December 31, 2015, referred to as calendar year 2015. Accordingly, we present our discussion and analysis under "Results of Operations" below based on comparisons of the results for such periods.
40
The following information should be read in conjunction with our consolidated financial statements. The key performance indicators that management uses in managing the business are sales, income before interest and income taxes, and cash flows.
Group Sales and Cost of Sales include intergroup sales and profit. Corporate and Eliminations includes intergroup sales and profit eliminations and corporate expenses.
The information presented in the Results of Operations compares the audited results for the calendar year ended December 31, 2017 to the audited results for the calendar year ended December 31, 2016, and compares the audited results for the calendar year ended December 31, 2016 to the unaudited results for the calendar year ended December 31, 2015.
Calendar Year Ended December 31, 2017 Compared to Calendar Year Ended December 31, 2016
Sales
Year Ended December 31, | |||||||||||||||
2017 | 2016 | $ Change | % Change | ||||||||||||
Flight Systems Group | $ | 1,681 | $ | 1,496 | $ | 185 | 12.4 | % | |||||||
Defense Systems Group | 1,968 | 1,823 | 145 | 8.0 | |||||||||||
Space Systems Group | 1,284 | 1,238 | 46 | 3.7 | |||||||||||
Corporate and Eliminations | (169 | ) | (102 | ) | (67 | ) | (65.7 | ) | |||||||
Total sales | $ | 4,764 | $ | 4,455 | $ | 309 | 6.9 | % |
The fluctuation in sales was driven by the program-related changes within the operating segments as described below.
Flight Systems Group. The increase in sales was driven by higher sales of $126 million in Aerospace Structures due to increased production on composite aircraft structures. The increase was also driven by higher sales in Launch Vehicles of $57 million due to a new medium range ballistic target program and increased activity on small space launch programs.
Defense Systems Group. The increase in sales was due to an increase of $75 million in Armament Systems driven by international sales, $57 million in Defense Electronics due to higher strike weapons and light attack aircraft production, and $37 million in Missile Products due to higher production level on tactical propulsion and missile defense. These increases were partially offset by a decrease of $25 million in Small Caliber Systems primarily attributable to production delays resulting from an industrial accident that occurred in April 2017 at our Lake City Army Ammunition Plant.
Space Systems Group. The increase was due to higher sales of $130 million in Satellite Systems driven by an increase of $162 million on new and existing programs in defense satellites and $38 million in higher product sales for scientific and environmental satellites, partially offset by a decrease of $71 million in commercial satellites. The increase was also due to higher sales of $12 million in Space Components as a result of increased activity on existing programs and $3 million in Technical Services driven by activities on our U.S. Navy contracts. These increases were offset by a decrease of $99 million in Advanced Programs driven by a decrease of $169 million for Commercial Resupply Services ("CRS") activity partially offset by a $70 million increase in Mission Extension Vehicles ("MEV") activity.
Corporate and Eliminations. The change in Corporate and Eliminations was primarily due to an increase in intercompany activity, which are eliminated in consolidation.
Cost of Sales
Year Ended December 31, | |||||||||||||||
2017 | 2016 | $ Change | % Change | ||||||||||||
Flight Systems Group | $ | 1,292 | $ | 1,117 | $ | 175 | 15.7 | % | |||||||
Defense Systems Group | 1,571 | 1,471 | 100 | 6.8 | |||||||||||
Space Systems Group | 1,048 | 1,010 | 38 | 3.8 | |||||||||||
Corporate and Eliminations | (212 | ) | (128 | ) | (84 | ) | (65.6 | ) | |||||||
Total cost of sales | $ | 3,699 | $ | 3,470 | $ | 229 | 6.6 | % |
41
The fluctuation in cost of sales was driven by the program-related changes within the operating segments as described below.
Flight Systems Group. The increase was due to higher cost of sales of $103 million in Aerospace Structures due to increased production on composite aircraft structures. The increase was also driven by higher cost of sales in Launch Vehicles of $62 million due to a new medium range ballistic target program and activity related to additional missions on Antares, offset by reduced production on existing missile defense programs. Cost of sales also increased $11 million in Propulsion Systems due to production timing on existing programs.
Defense Systems Group. The increase was due to higher cost of sales of $54 million in Armament Systems due to increased international sales, $42 million in Defense Electronics due to higher volume of strike weapons and light attack aircraft production and $16 million in Missile Products due to increased tactical propulsion production and missile defense. These increases were partially offset by a decrease of $14 million in Small Caliber Systems primarily attributable to production delays resulting from an industrial accident that occurred in the Lake City Army Ammunition Plant in April 2017.
Space Systems Group. The increase was due to higher cost of sales of $91 million in Satellite Systems driven by increased activity in defense satellites and scientific and environmental satellites, partially offset by decreases in commercial satellites. In addition, Space Components increased $13 million due to increased activity on existing programs. These increases were offset by a decrease of $66 million in Advanced Programs due to decreased CRS activity, offset by increased MEV activity.
Corporate and Eliminations. The change in Corporate and Eliminations was primarily due to an increase in intercompany activity, which are eliminated in consolidation.
Operating Expenses
Year Ended December 31, | ||||||||||||||||||
2017 | As a % of Sales | 2016 | As a % of Sales | Change | ||||||||||||||
Research and development | $ | 115 | 2.4 | % | $ | 116 | 2.6 | % | $ | (1 | ) | |||||||
Selling | 115 | 2.4 | 107 | 2.4 | 8 | |||||||||||||
General and administrative | 306 | 6.4 | 290 | 6.5 | 16 | |||||||||||||
Total | $ | 536 | 11.2 | % | $ | 513 | 11.5 | % | $ | 23 |
Operating expenses increased $23 million primarily due to increased general and administrative costs to support our growth initiatives, mainly in our Defense Systems Group, and incremental costs for acquisition transaction expenses offset by lower expenses in the current year for legal and audit fees related to the restatement of our financial statements. Additionally, selling expenses increased due to higher bid and proposal expenses in Flight Systems Group and Defense Systems Group.
Net Interest Expense
Net interest expense for the year ended December 31, 2017 was $67 million, which was relatively flat compared to $68 million during the year ended December 31, 2016.
Income Taxes (from Continuing Operations)
Year Ended December 31, | ||||||||||||||||||
2017 | Effective Rate | 2016 | Effective Rate | Change | ||||||||||||||
Income taxes | $ | 152 | 33.0 | % | $ | 111 | 27.5 | % | $ | 41 |
The increase in the current year tax rate is due to tax expense increases as a result of the Tax Act and state taxes, decreased benefits from the Domestic Manufacturing Deduction ("DMD") and the research and development ("R&D") tax credit, partially offset by increased benefits from the true-up of prior year taxes and a decrease in valuation allowance.
Our provision for income taxes includes both federal and state income taxes. The effective tax rate for the year ended December 31, 2017 of 33.0% differs from the federal statutory rate of 35.0% due to the write-down of net deferred tax assets as a result of the Tax Act, the DMD, the R&D tax credit, true-up of prior year taxes, partially offset by the change in valuation allowance and state income taxes, which increased the rate.
42
The effective tax rate for December 31, 2016 of 27.5% differs from the federal statutory rate of 35.0% due to the DMD, the R&D tax credit, true-up of prior year taxes and the settlement of the examination by the IRS of the fiscal 2013 and 2014 tax returns, partially offset by the change in valuation allowance and state income taxes, which increased the tax rate.
Calendar Year Ended December 31, 2016 Compared to Calendar Year Ended December 31, 2015 (Unaudited)
Sales
Year Ended December 31, | |||||||||||||||
2016 | 2015 | $ Change | % Change | ||||||||||||
(Unaudited) | |||||||||||||||
Flight Systems Group | $ | 1,496 | $ | 1,470 | $ | 26 | 1.8 | % | |||||||
Defense Systems Group | 1,823 | 1,820 | 3 | 0.2 | |||||||||||
Space Systems Group | 1,238 | 1,165 | 73 | 6.3 | |||||||||||
Corporate and Eliminations | (102 | ) | (92 | ) | (10 | ) | (10.9 | ) | |||||||
Total sales | $ | 4,455 | $ | 4,363 | $ | 92 | 2.1 | % |
The fluctuation in sales was driven by the program-related changes within the operating segments as described below.
Flight Systems Group. The increase in sales was primarily due to the Antares return to flight, added missions, and inclusion of a full year of Orbital's results in the year ended December 31, 2016, whereas the year ended December 31, 2015 only included Orbital's results after February 9, 2015 (the date of the Orbital-ATK Merger). Additionally, growth in Aerospace Structures programs was partly offset by a decrease in tactical missile volume and a favorable contract close out adjustment in the year ended December 31, 2015 that did not reoccur in the year ended December 31, 2016.
Defense Systems Group. Sales were relatively flat for the year ended December 31, 2016 compared to the year ended December 31, 2015. Missile Product's contracts experienced an increase in activity, which was offset by a decline in non-standard ammunition sales during the year within Small Caliber Systems.
Space Systems Group. The increase in sales for the year ended December 31, 2016 was primarily due to including a full year of Orbital's results whereas the year ended December 31, 2015 only included Orbital's results after the date of the Orbital-ATK Merger. Additionally, the year ended December 31, 2015 included unfavorable profit adjustments related to Satellite Systems that did not reoccur in the year ended December 31, 2016.
Corporate and Eliminations. The change in Corporate and Eliminations was primarily due to an increase in intercompany activity, which are eliminated in consolidation.
Cost of Sales
Year Ended December 31, | |||||||||||||||
2016 | 2015 | $ Change | % Change | ||||||||||||
(unaudited) | |||||||||||||||
Flight Systems Group | $ | 1,117 | $ | 1,119 | $ | (2 | ) | (0.2 | )% | ||||||
Defense Systems Group | 1,471 | 1,460 | 11 | 0.8 | |||||||||||
Space Systems Group | 1,010 | 969 | 41 | 4.2 | |||||||||||
Corporate and Eliminations | (128 | ) | (83 | ) | (45 | ) | (54.2 | ) | |||||||
Total cost of sales | $ | 3,470 | $ | 3,465 | $ | 5 | 0.1 | % |
The fluctuation in cost of sales was driven by the program-related changes within the operating segments as described below.
Flight Systems Group. Cost of sales remained relatively flat.
Defense Systems Group. The slight increase for the year ended December 31, 2016 was primarily driven by higher costs associated with certain Armament Systems and Missile Products contracts.
43
Space Systems Group. The increase in cost of sales for the year ended December 31, 2016 was primarily due to including a full year of activity of the Orbital business.
Corporate and Eliminations. The change in Corporate and Eliminations was primarily due to an increase in intercompany activity, which are eliminated in consolidation.
Operating Expenses
Year Ended December 31, | ||||||||||||||||||
2016 | As a % of Sales | 2015 | As a % of Sales | Change | ||||||||||||||
(Unaudited) | ||||||||||||||||||
Research and development | $ | 116 | 2.6 | % | $ | 109 | 2.5 | % | $ | 7 | ||||||||
Selling | 107 | 2.4 | 109 | 2.5 | (2 | ) | ||||||||||||
General and administrative | 290 | 6.5 | 359 | 8.2 | (69 | ) | ||||||||||||
Goodwill impairment | — | — | 34 | 0.8 | (34 | ) | ||||||||||||
Total | $ | 513 | 11.5 | % | $ | 611 | 14.0 | % | $ | (98 | ) |
Operating expenses decreased $98 million primarily due to transaction fees for advisory, legal and accounting services in connection with the Distribution and Orbital-ATK Merger during the year ended December 31, 2015 that did not reoccur in the year ended December 31, 2016. During the first quarter of calendar 2015, we recorded a goodwill impairment charge of $34 million pertaining to Space Components in our Space Systems Group, in connection with our annual goodwill impairment test. Additional reductions in general and administrative costs in Propulsion Systems lowered general and administrative costs overall, as a percentage of revenue.
Net Interest Expense
Net interest expense for the year ended December 31, 2016 was $68 million, a decrease of $13 million compared to $81 million during the year ended December 31, 2015. The decrease was primarily due to accelerated amortization of deferred debt issuance costs related to refinancing our debt during the year ended December 31, 2015 that did not reoccur in the year ended December 31, 2016.
Income Taxes (from Continuing Operations)
Year Ended December 31, | ||||||||||||||||||
2016 | Effective Rate | 2015 | Effective Rate | Change | ||||||||||||||
(Unaudited) | ||||||||||||||||||
Income taxes | $ | 111 | 27.5 | % | $ | 83 | 36.4 | % | $ | 28 |
The decrease in the current year tax rate is due to increased benefits from the DMD and the R&D tax credit, the true-up of prior year taxes, the settlement of the examination by the IRS of the fiscal 2013 and 2014 tax returns and the absence of goodwill impairment and non-deductible transaction costs which increased the tax rate in the prior period, partially offset by an increase in valuation allowance.
Our provision for income taxes includes both federal and state income taxes. The effective tax rate for December 31, 2016 of 27.5% differs from the federal statutory rate of 35.0% due to the DMD, the R&D tax credit, true-up of prior year taxes and the settlement of the examination by the IRS of the fiscal 2013 and 2014 tax returns, partially offset by the change in valuation allowance and state income taxes, which increased the tax rate.
The effective tax rate for the year ended December 31, 2015 of 36.4% differs from the federal statutory rate of 35.0% due to the impact of goodwill impairment, non-deductible transaction costs, and state income taxes offset by the DMD, the R&D tax credit and true-up of prior year taxes.
Liquidity and Capital Resources
We manage our business to maximize operating cash flows as the primary source of liquidity. In addition to cash on hand and cash generated by operations, sources of liquidity include a credit facility, long-term borrowings, and access to the public debt and equity markets. We use our cash to fund investments in our existing core businesses and for debt repayment, cash dividends, share repurchases and acquisition or other activities.
44
Cash Flows Summary
Our cash flows from continuing operations for operating, investing and financing activities, as reflected in the Consolidated Statements of Cash Flows are summarized as follows:
Year Ended December 31, | ||||||||||||
2017 | 2016 | 2015 | ||||||||||
(unaudited) | ||||||||||||
Cash provided by operating activities of continuing operations | $ | 520 | $ | 519 | $ | 450 | ||||||
Cash (used in) provided by investing activities of continuing operations | (245 | ) | (183 | ) | 280 | |||||||
Cash used in financing activities of continuing operations | (129 | ) | (240 | ) | (748 | ) | ||||||
Net cash flows provided by (used in) continuing operations | $ | 146 | $ | 96 | $ | (18 | ) |
Operating Activities
Net cash provided by operating activities of continuing operations during the year ended December 31, 2017 was consistent with 2016. The positive drivers of the changes in cash flows were net earnings, deferred taxes and changes in other assets and liabilities ($97 million). These changes were partially offset by an increase in the use of working capital ($103 million).
Net cash provided by operating activities of continuing operations increased during the year ended December 31, 2016 resulting primarily from the net effect of a $147 million improvement in income from continuing operations partially offset by positive non-cash net income adjustments in the prior year for goodwill impairment and loss on extinguishment of debt that did not occur in the year ended December 31, 2016 and changes in working capital and other assets and liabilities ($4 million increase in the use of cash).
Investing Activities
Cash used in investing activities of continuing operations was $245 million during the year ended December 31, 2017 an increase of $62 million from $183 million for the year ended December 31, 2016. This increase was driven by higher capital expenditures during the year ended December 31, 2017 related to our self-constructed Mission Extension Vehicles, which will provide in-orbit satellite life extension services when completed. We expended $101 million in the current year for these assets.
Investing activities of continuing operations used cash of $183 million during the year ended December 31, 2016 compared to cash provided by investing activities of continuing operations of $280 million during the year ended December 31, 2015. This decrease was driven by the receipt of cash acquired in the Orbital-ATK Merger of $254 million and a cash dividend of $214 million paid by Vista Outdoor to us, less cash distributed to Vista Outdoor of $32 million in connection with the Distribution during the year ended December 31, 2015. The decrease was also driven by higher capital expenditures of $31 million in the year ended December 31, 2016 offset by proceeds of $4 million from the sale of land during the year ended December 31, 2016.
Financing Activities
Net cash used in financing activities of continuing operations during the year ended December 31, 2017 decreased by $111 million primarily due to lower share repurchases of $102 million and higher proceeds from employee stock compensation plans of $13 million. In connection with the Merger, the Company halted its share repurchase program.
Net cash used in financing activities of continuing operations during the year ended December 31, 2016 decreased $508 million primarily due to higher debt payments, net of $1,761 million related to our credit facility offset by proceeds of $1,200 million from the issuance of long-term debt in the year ended December 31, 2015, partially offset by higher dividends paid and share repurchases during the year ended December 31, 2016 of $13 million and $45 million, respectively.
Liquidity
In addition to our normal operating cash requirements, our principal future cash requirements will be to fund capital expenditures, repay debt, satisfy employee benefit obligations and pay dividends. As a result of the pending Merger, we halted our share repurchase program and do not expect to complete any strategic acquisitions. If the Merger
45
were not completed for any reason, we would expect to consider resuming our share repurchase program and exploring possible strategic acquisitions. Our short-term cash requirements for operations are expected to consist mainly of capital expenditures to maintain and expand production facilities and working capital requirements. Our debt service requirements over the next two years consist of principal payments due under the Term Loan A of the Senior Credit Facility, as discussed further below. Our other debt service requirements consist of interest expense on outstanding debt.
During the year ended December 31, 2017, we paid quarterly dividends of $0.32 per share for all four quarters totaling approximately $74 million. On January 31, 2018, the Board of Directors declared a quarterly cash dividend of $0.32 per share. The payment and amount of any future dividends are at the discretion of the Board of Directors and will be based on a number of factors, including our earnings, liquidity position, financial condition, capital requirements, credit ratings and the availability and cost of obtaining new debt. Under the terms of the Merger Agreement, we are permitted to, and intend to, continue paying a $0.32 per share quarterly cash dividend until the closing of the transaction. However, we are not permitted to increase the per share dividend amount under the terms of the Merger Agreement.
In September 2015, we issued $400 million aggregate principal amount of 5.50% Senior Notes due 2023 and we refinanced our then-existing senior credit facility (the "Former Credit Facility") with a new senior credit facility (the "Senior Credit Facility"), extending debt maturities and increasing our revolving debt capacity, which increased our liquidity. Based on our current financial condition, management believes that our cash position, combined with anticipated generation of cash flows and the availability of funding, if needed, through our revolving credit facilities, as well as potential future sources of funding, including additional bank financing and debt markets, will be adequate to fund future growth as well as to service our currently anticipated long-term debt and pension obligations, make capital expenditures and payment of dividends over the next 12 months.
We do not expect that our access to liquidity sources will be materially impacted in the near future. There can be no assurance, however, that the cost or availability of future borrowings, if any, will not be materially impacted by capital market conditions.
Long-term Debt and Credit Facilities
At December 31, 2017, we had actual total indebtedness of $1,410 million, and a $1,000 million revolving credit facility that provided for the potential of additional borrowings up to $760 million reduced by outstanding letters of credit of $240 million. There were no outstanding borrowings under the revolving credit facility at December 31, 2017.
Our indebtedness consisted of the following:
December 31, 2017 | December 31, 2016 | |||||||
Senior Credit Facility: | ||||||||
Term Loan A due 2020 | $ | 710 | $ | 750 | ||||
Revolving Credit Facility due 2020 | — | — | ||||||
5.25% Senior Notes due 2021 | 300 | 300 | ||||||
5.50% Senior Notes due 2023 | 400 | 400 | ||||||
Carrying amount of long-term debt | 1,410 | 1,450 | ||||||
Unamortized debt issuance costs: | ||||||||
Senior Credit Facility | 4 | 5 | ||||||
5.25% Senior Notes due 2021 | 1 | 2 | ||||||
5.50% Senior Notes due 2023 | 4 | 5 | ||||||
Unamortized debt issuance costs | 9 | 12 | ||||||
Long-term debt less unamortized debt issuance costs | 1,401 | 1,438 | ||||||
Less: Current portion of long-term debt | 40 | 40 | ||||||
Long-term debt | $ | 1,361 | $ | 1,398 |
See Note 10, Long-term Debt, to the consolidated financial statements in Part II, Item 8, "Financial Statements and Supplementary Data" for a detailed discussion of these borrowings.
46
Covenants
Our Senior Credit Facility imposes restrictions on us, including limitations on our ability to incur additional debt, enter into capital leases, grant liens, pay dividends and make certain other payments, sell assets, or merge or consolidate with or into another entity. In addition, the Senior Credit Facility limits our ability to enter into sale-and-leaseback transactions. The Senior Credit Facility also requires that we meet and maintain the following financial ratios:
Total Leverage Ratio (1) | Interest Coverage Ratio (2) | |||||
Requirement | 4.00 | 3.00 | ||||
Actual at December 31, 2017 | 1.86 | 11.92 |
_________________________________________
(1) | Not to exceed the required financial ratio. |
(2) | Not to be below the required financial ratio. |
The Total Leverage Ratio is the sum of our total debt plus financial letters of credit, net of up to $100 million of cash, divided by Covenant Earnings Before Interest, Taxes, Depreciation and Amortization ("EBITDA") (which includes adjustments for items such as non-recurring or extraordinary non-cash items, non-cash charges related to stock-based compensation, and intangible asset impairment charges, as well as inclusion of EBITDA of acquired companies on a pro forma basis) for the past four fiscal quarters.
The Interest Coverage Ratio is Covenant EBITDA divided by cash payments for interest expense.
Our debt agreements contain cross-default provisions so that non-compliance with the covenants within one debt agreement that would give rise to the right to accelerate repayment of any outstanding indebtedness could cause a default under other debt agreements as well. Our ability to comply with these covenants and to meet and maintain the requisite financial ratios may be affected by events beyond our control. Borrowings under the Senior Credit Facility are subject to compliance with these covenants. The indentures governing the 5.25% Notes and the 5.50% Notes impose restrictions on us, including limitations on our ability to incur additional debt, enter into capital leases, grant liens, pay dividends and make certain other payments, sell assets, or merge or consolidate with or into another entity.
At December 31, 2017, we were in compliance with the covenants in all of our debt agreements.
Share Repurchases
During 2016, the Board of Directors authorized an increase to the amount for repurchase of the Company's common stock to the lesser of $300 million or 4 million shares through March 31, 2017. On February 27, 2017, the Board of Directors further increased the amount authorized for repurchase to $450 million, removed the share quantity limitation and extended the repurchase period through March 31, 2018. Under the authorized repurchase program, shares of our common stock may be purchased from time to time in the open market, subject to compliance with applicable laws and regulations and our debt covenants, depending upon market conditions and other factors. We repurchased 230,918 shares for $23 million during the year ended December 31, 2017, 1,570,333 shares for $124 million in the year ended December 31, 2016, and 1,008,445 shares for $76 million in the 2015 transition period. In connection with the Merger, the Company halted its share repurchase program.
Authorized repurchases of our shares are also subject to market conditions, our compliance with our debt covenants and the limitations imposed by the Merger Agreement. Our 5.25% Senior Notes and 5.50% Senior Notes limit the aggregate sum of dividends, share repurchases and other designated restricted payments to an amount based on our net income, stock issuance proceeds and certain other items since April 1, 2001, less restricted payments made since that date. At December 31, 2017, the Senior Credit Facility allows us to make unlimited "restricted payments" (as defined in the Credit Agreement), which, among other items, allows payments for future share repurchases, as long as we maintain a certain amount of liquidity and maintain certain senior secured debt limits. When those requirements are not met, the limit is equal to $250 million plus proceeds of any equity issuances plus 50% of net income since October 7, 2010. The Credit Agreement also prohibits dividend payments if loan defaults exist or the financial covenants contained in the agreement are not met, subject to certain limited exceptions.
47
Contractual Obligations and Commercial Commitments
The following table summarizes our contractual obligations and commercial commitments at December 31, 2017:
Total | 1 Year | 2 - 3 Years | 4 - 5 Years | More than 5 Years | |||||||||||||||
Contractual obligations - by payment period: | |||||||||||||||||||
Long-term debt | $ | 1,410 | $ | 40 | $ | 670 | $ | 300 | $ | 400 | |||||||||
Interest on debt (1) | 219 | 47 | 90 | 60 | 22 | ||||||||||||||
Operating leases | 400 | 85 | 148 | 107 | 60 | ||||||||||||||
Environmental remediation costs, net | 20 | 2 | 1 | 4 | 13 | ||||||||||||||
Purchase obligations (2) | 75 | 40 | 34 | 1 | — | ||||||||||||||
Pension and other postretirement plan contributions | 302 | 11 | 152 | 92 | 47 | ||||||||||||||
Total contractual obligations, net | $ | 2,426 | $ | 225 | $ | 1,095 | $ | 564 | $ | 542 | |||||||||
Other commercial commitments - by expiration period: | |||||||||||||||||||
Letters of credit (3) | $ | 240 | $ | 74 | $ | 116 | $ | 40 | $ | 10 |
(1) | Includes interest on variable rate debt calculated based on the minimum required rate for LIBOR based loans under the Credit Agreement as of December 31, 2017. Variable rate debt was 50% of our total debt at December 31, 2017. |
(2) | Purchase obligations are comprised primarily of open purchase order commitments to suppliers, primarily for materials, in which the commitment is binding and specifies all the significant terms including fixed or minimum quantities to be purchased. |
(3) | Approximately $24 million of standby letters of credit in the "1 Year" category are expected to renew for additional periods until completion of the contractual obligation. |
The total liability for unrecognized tax benefits at December 31, 2017 was $137 million (see Note 14, Income Taxes) and it is reasonably possible that a $30 million reduction of the unrecognized tax benefit will occur in the next 12 months. We are not able to provide a reasonably reliable estimate of the timing of future payments relating to the noncurrent unrecognized tax benefits and therefore this amount is not included in the table above.
Pension plan contributions are an estimate of our minimum funding requirements through 2027 to provide pension benefits for employees based on expected actuarial estimated service accruals through 2027 pursuant to the Employee Retirement Income Security Act, although we may make additional discretionary contributions. These estimates may change significantly depending on the actual rate of return on plan assets, discount rates, discretionary pension contributions and regulations. A substantial portion of our Plan contributions are recoverable from the U.S. Government as allowable indirect contract costs at amounts generally equal to the pension plan contributions, although not necessarily in the same year the contribution is made.
Contingencies
Litigation. From time to time, we are subject to various legal proceedings, including lawsuits, which arise out of, and are incidental to, the conduct of our business. We do not consider any of such proceedings that are currently pending, individually or in the aggregate, notwithstanding that the unfavorable resolution of any matter may have a material effect on our net earnings in any particular quarter, to be material to our business or likely to result in a material adverse effect on our future operating results, financial condition or cash flows. See Item 3, "Legal Proceedings" and Note 16, Contingencies, to the consolidated financial statements in Item 8, "Financial Statements and Supplementary Data" of this report for additional information.
Environmental Liabilities. Our operations and ownership or use of real property are subject to a number of federal, state, and local environmental laws and regulations, as well as applicable foreign laws and regulations, including those for discharge of hazardous materials, remediation of contaminated sites and restoration of damage to the environment. At certain sites that we own or operate or formerly owned or operated, there is known or potential
48
contamination that we are required to investigate or remediate. We could incur substantial costs, including remediation costs, resource restoration costs, fines and penalties, or third party property damage or personal injury claims, as a result of liabilities associated with past practices or violations of environmental laws or non-compliance with environmental permits.
The liability for environmental remediation represents management's best estimate of the probable and reasonably estimable costs related to known remediation obligations. The receivable represents the amount that we expect to recover. We expect that a portion of the environmental compliance and remediation costs will be recoverable under U.S. Government contracts. Some of the remediation costs that are not recoverable from the U.S. Government that are associated with facilities purchased in a business acquisition may be covered by various indemnification agreements. There were no material insurance recoveries related to environmental remediation during any of the periods presented.
Factors that could significantly change the estimates on environmental liabilities include:
• | the adoption, implementation and interpretation of new laws, regulations or cleanup standards, |
• | advances in technologies, |
• | outcomes of negotiations or litigation with regulatory authorities and other parties, |
• | additional information about the ultimate remedy selected at new and existing sites, |
• | adjustment of our share of the cost of such remedies, |
• | changes in the extent and type of site utilization, |
• | the discovery of new contamination, |
• | the number of parties found liable at each site and their ability to pay, |
• | more current estimates of liabilities for these contingencies, or |
• | liabilities associated with resource restoration as a result of contamination from past practices. |
See Note 16, Contingencies, to the consolidated financial statements in Item 8, "Financial Statements and Supplementary Data" of this report for additional information.
New Accounting Pronouncements
See Note 1, Summary of Significant Accounting Policies, to the consolidated financial statements in Item 8, "Financial Statements and Supplementary Data" of this report for discussion of new accounting pronouncements.
Inflation
In management's opinion, inflation has not had a significant impact upon the results of our operations. The selling prices under contracts, the majority of which are long term, generally include estimated costs to be incurred in future periods. These cost projections can generally be negotiated into new buys under fixed-price government contracts, while actual cost increases are recoverable on cost-type contracts.
49
ITEM 7A. QUANTITATIVE AND QUALITATIVE DISCLOSURES ABOUT MARKET RISK
Our market risk exposure primarily relates to changes in interest rates, foreign currency exchange rates and certain commodity prices. To mitigate the risks from interest rate exposure, we occasionally enter into hedging transactions, mainly interest rate swaps, through derivative financial instruments that have been authorized pursuant to corporate policies. We also use derivatives to hedge foreign currency exchange rates and commodity price risks, but do not use derivative financial instruments for trading or other speculative purposes, and we are not a party to leveraged financial instruments. Additional information regarding financial instruments is contained in Note 1, Summary of Significant Accounting Policies and Note 3, Derivative Financial Instruments, to the consolidated financial statements.
Currently, our primary interest rate exposures relate to variable rate debt. We measure market risk related to changes in interest rates utilizing a sensitivity analysis. The sensitivity analysis measures the potential loss in fair values, cash flows and earnings based on a hypothetical change (increase and decrease) in interest rates. We use current market rates on our debt portfolio to perform the sensitivity analysis. The potential change in fair values is based on an assumed immediate change in the net present values of interest rate-sensitive exposures resulting from a 100 basis point change in interest rates. The potential change in cash flows and earnings is based on the change in the net interest income/expense over a one-year period due to the change in rates. Based on our analysis, a 100 basis point change in interest rates would not have a material impact on the fair values or our results of operations or cash flows at December 31, 2017.
We use derivatives to hedge our exposure to market risks from changes in foreign currency exchange rates. We transact business globally and are subject to risks associated with changing foreign currency exchange rates. Based on our analysis, a 10 percent unfavorable foreign exchange rate movement would not have a material impact on our financial positions, results of operations or cash flows at December 31, 2017.
With respect to our ammunition business, we have a strategic sourcing and price strategy to mitigate risk from commodity price fluctuation. We will continue to evaluate the need for future price changes in light of these trends, our competitive landscape and our financial results. If commodity costs increase, and if we are unable to offset these increases with ongoing manufacturing efficiencies and price increases, our future results from operations and cash flows could be materially impacted.
Significant increases in commodities prices can negatively impact operating results with respect to our firm fixed-price contract to supply the DoD's small-caliber ammunition needs and our sales within commercial ammunition. Accordingly, we have entered into futures contracts in order to reduce the impact of metal price fluctuations. The majority of the impact has been mitigated on the contract with the U.S. Army by the terms within that contract. We have entered into futures contracts and purchase orders for the current expected production requirements for both the small-caliber ammunition supply contract and the production of commercial ammunition, thereby mitigating near term market risk; however, if metal prices exceed pre-determined levels, Defense Systems Group's operating results could be adversely impacted.
50
ITEM 8. FINANCIAL STATEMENTS AND SUPPLEMENTARY DATA
REPORT OF INDEPENDENT REGISTERED PUBLIC ACCOUNTING FIRM
To the Board of Directors and Stockholders of Orbital ATK, Inc.
Opinions on the Financial Statements and Internal Control over Financial Reporting
We have audited the accompanying consolidated balance sheet of Orbital ATK, Inc. and subsidiaries (the "Company") as of December 31, 2017, the related consolidated statements of operations, comprehensive income, equity, and cash flows, for the year ended December 31, 2017, and the related notes (collectively referred to as the "financial statements"). We also have audited the Company’s internal control over financial reporting as of December 31, 2017, based on criteria established in Internal Control - Integrated Framework (2013) issued by the Committee of Sponsoring Organizations of the Treadway Commission (COSO).
In our opinion, the financial statements referred to above present fairly, in all material respects, the financial position of the Company as of December 31, 2017, and the results of its operations and its cash flows for the period ended December 31, 2017, in conformity with accounting principles generally accepted in the United States of America. Also, in our opinion, the Company maintained, in all material respects, effective internal control over financial reporting as of December 31, 2017, based on criteria established in Internal Control - Integrated Framework (2013) issued by COSO.
Basis for Opinions
The Company's management is responsible for these financial statements, for maintaining effective internal control over financial reporting, and for its assessment of the effectiveness of internal control over financial reporting, included in the accompanying Management's Report on Internal Control over Financial Reporting. Our responsibility is to express an opinion on these financial statements and an opinion on the Company's internal control over financial reporting based on our audit. We are a public accounting firm registered with the Public Company Accounting Oversight Board (United States) ("PCAOB") and are required to be independent with respect to the Company in accordance with the U.S. federal securities laws and the applicable rules and regulations of the Securities and Exchange Commission and the PCAOB.
We conducted our audit in accordance with the standards of the PCAOB. Those standards require that we plan and perform the audit to obtain reasonable assurance about whether the financial statements are free of material misstatement, whether due to error or fraud, and whether effective internal control over financial reporting was maintained in all material respects.
Our audit of the financial statements included performing procedures to assess the risks of material misstatement of the financial statements, whether due to error or fraud, and performing procedures to respond to those risks. Such procedures included examining, on a test basis, evidence regarding the amounts and disclosures in the financial statements. Our audit also included evaluating the accounting principles used and significant estimates made by management, as well as evaluating the overall presentation of the financial statements. Our audit of internal control over financial reporting included obtaining an understanding of internal control over financial reporting, assessing the risk that a material weakness exists, and testing and evaluating the design and operating effectiveness of internal control based on the assessed risk. Our audit also included performing such other procedures as we considered necessary in the circumstances. We believe that our audit provides a reasonable basis for our opinions.
Definition and Limitations of Internal Control over Financial Reporting
A company's internal control over financial reporting is a process designed to provide reasonable assurance regarding the reliability of financial reporting and the preparation of financial statements for external purposes in accordance with generally accepted accounting principles. A company's internal control over financial reporting includes those policies and procedures that (1) pertain to the maintenance of records that, in reasonable detail, accurately and fairly reflect the transactions and dispositions of the assets of the company; (2) provide reasonable assurance that transactions are recorded as necessary to permit preparation of financial statements in accordance with generally accepted accounting principles, and that receipts and expenditures of the company are being made only in accordance with authorizations of management and directors of the company; and (3) provide reasonable
51
assurance regarding prevention or timely detection of unauthorized acquisition, use, or disposition of the company's assets that could have a material effect on the financial statements.
Because of its inherent limitations, internal control over financial reporting may not prevent or detect misstatements. Also, projections of any evaluation of effectiveness to future periods are subject to the risk that controls may become inadequate because of changes in conditions, or that the degree of compliance with the policies or procedures may deteriorate.
/s/ DELOITTE & TOUCHE LLP
McLean, Virginia
February 21, 2018
We have served as the Company's auditor since 2017.
52
REPORT OF INDEPENDENT REGISTERED PUBLIC ACCOUNTING FIRM
To the Board of Directors and Stockholders of Orbital ATK, Inc.
In our opinion, the consolidated balance sheet as of December 31, 2016 and the related consolidated statements of operations, of comprehensive income, of equity, and of cash flows for the year ended December 31, 2016 and for the nine months ended December 31, 2015 present fairly, in all material respects, the financial position of Orbital ATK, Inc. and its subsidiaries as of December 31, 2016, and the results of their operations and their cash flows for the year ended December 31, 2016 and for the nine months ended December 31, 2015, in conformity with accounting principles generally accepted in the United States of America. These financial statements are the responsibility of the Company's management. Our responsibility is to express an opinion on these financial statements based on our audits. We conducted our audits of these financial statements in accordance with the standards of the Public Company Accounting Oversight Board (United States). Those standards require that we plan and perform the audit to obtain reasonable assurance about whether the financial statements are free of material misstatement. An audit includes examining, on a test basis, evidence supporting the amounts and disclosures in the financial statements, assessing the accounting principles used and significant estimates made by management, and evaluating the overall financial statement presentation. We believe that our audits provide a reasonable basis for our opinion.
/s/ PricewaterhouseCoopers LLP
McLean, Virginia
April 28, 2017
53
ORBITAL ATK, INC.
CONSOLIDATED BALANCE SHEETS
As of December 31, | ||||||||
(Amounts in millions, except share data) | 2017 | 2016 | ||||||
ASSETS | ||||||||
Current assets: | ||||||||
Cash and cash equivalents | $ | 346 | $ | 200 | ||||
Net receivables | 1,893 | 1,741 | ||||||
Net inventories | 221 | 215 | ||||||
Other current assets | 82 | 79 | ||||||
Total current assets | 2,542 | 2,235 | ||||||
Net property, plant and equipment | 934 | 816 | ||||||
Goodwill | 1,832 | 1,832 | ||||||
Net intangibles | 61 | 98 | ||||||
Deferred income taxes | 155 | 254 | ||||||
Other noncurrent assets | 142 | 183 | ||||||
Total assets | $ | 5,666 | $ | 5,418 | ||||
LIABILITIES AND EQUITY | ||||||||
Current liabilities: | ||||||||
Current portion of long-term debt | $ | 40 | $ | 40 | ||||
Accounts payable | 216 | 175 | ||||||
Contract-related liabilities | 375 | 394 | ||||||
Contract loss reserve | 152 | 197 | ||||||
Contract advances and allowances | 330 | 233 | ||||||
Accrued compensation | 137 | 120 | ||||||
Other current liabilities | 210 | 183 | ||||||
Total current liabilities | 1,460 | 1,342 | ||||||
Long-term debt | 1,361 | 1,398 | ||||||
Pension and postemployment benefits | 693 | 744 | ||||||
Other noncurrent liabilities | 107 | 117 | ||||||
Total liabilities | 3,621 | 3,601 | ||||||
Commitments and contingencies (Notes 13, 15 and 16) | ||||||||
Stockholders' Equity | ||||||||
Common stock—$.01 par value: authorized—180,000,000 shares; issued and outstanding— 57,686,214 shares held at December 31, 2017 and 57,487,466 shares held at December 31, 2016 | 1 | 1 | ||||||
Additional paid-in-capital | 2,175 | 2,175 | ||||||
Retained earnings | 1,502 | 1,266 | ||||||
Accumulated other comprehensive loss | (780 | ) | (764 | ) | ||||
Common stock in treasury, at cost— 11,248,810 shares held at December 31, 2017 and 11,447,558 shares held at December 31, 2016 | (864 | ) | (872 | ) | ||||
Total Orbital ATK, Inc. stockholders' equity | 2,034 | 1,806 | ||||||
Noncontrolling interest | 11 | 11 | ||||||
Total equity | 2,045 | 1,817 | ||||||
Total liabilities and equity | $ | 5,666 | $ | 5,418 |
See Notes to the Consolidated Financial Statements.
54
ORBITAL ATK, INC.
CONSOLIDATED STATEMENTS OF OPERATIONS
(Amounts in millions, except per share data) | Year Ended December 31, 2017 | Year Ended December 31, 2016 | Nine Months Ended December 31, 2015 | |||||||||
Sales | $ | 4,764 | $ | 4,455 | $ | 3,391 | ||||||
Cost of sales | 3,699 | 3,470 | 2,717 | |||||||||
Gross profit | 1,065 | 985 | 674 | |||||||||
Operating expenses: | ||||||||||||
Research and development | 115 | 116 | 83 | |||||||||
Selling | 115 | 107 | 88 | |||||||||
General and administrative | 306 | 290 | 220 | |||||||||
Gain on settlement | — | — | 50 | |||||||||
Income from continuing operations, before interest, income taxes and noncontrolling interest | 529 | 472 | 333 | |||||||||
Interest expense, net | (67 | ) | (68 | ) | (61 | ) | ||||||
Income from continuing operations, before income taxes and noncontrolling interest | 462 | 404 | 272 | |||||||||
Income taxes | 152 | 111 | 87 | |||||||||
Income from continuing operations, before noncontrolling interest | 310 | 293 | 185 | |||||||||
Less net income attributable to noncontrolling interest | — | — | — | |||||||||
Income from continuing operations of Orbital ATK, Inc. | 310 | 293 | 185 | |||||||||
Discontinued operations: | ||||||||||||
Income from discontinued operations, before income taxes | — | — | — | |||||||||
Income taxes | — | — | (1 | ) | ||||||||
Income from discontinued operations | — | — | 1 | |||||||||
Net income attributable to Orbital ATK, Inc. | $ | 310 | $ | 293 | $ | 186 | ||||||
Basic earnings per common share from: | ||||||||||||
Continuing operations | $ | 5.39 | $ | 5.05 | $ | 3.12 | ||||||
Discontinued operations | — | — | 0.02 | |||||||||
Net income attributable to Orbital ATK, Inc. | $ | 5.39 | $ | 5.05 | $ | 3.14 | ||||||
Weighted-average number of common shares outstanding | 57 | 58 | 59 | |||||||||
Diluted earnings per common share from: | ||||||||||||
Continuing operations | $ | 5.34 | $ | 5.01 | $ | 3.09 | ||||||
Discontinued operations | — | — | 0.02 | |||||||||
Net income attributable to Orbital ATK, Inc. | $ | 5.34 | $ | 5.01 | $ | 3.11 | ||||||
Weighted-average number of diluted common shares outstanding | 58 | 58 | 60 | |||||||||
Cash dividends per common share | $ | 1.28 | $ | 1.20 | $ | 0.78 |
Note: earnings per share amounts may not recalculate due to rounding.
See Notes to the Consolidated Financial Statements.
55
ORBITAL ATK, INC.
CONSOLIDATED STATEMENT OF COMPREHENSIVE INCOME
(Amounts in millions) | Year Ended December 31, 2017 | Year Ended December 31, 2016 | Nine Months Ended December 31, 2015 | |||||||||
Net income | $ | 310 | $ | 293 | $ | 186 | ||||||
Other comprehensive (loss) income | ||||||||||||
Pension and other postretirement benefits: | ||||||||||||
Prior service credits for pension and postretirement benefit plans recorded to net income, net of taxes of $10, $10 and $8, respectively | (17 | ) | (17 | ) | (13 | ) | ||||||
Net actuarial loss for pension and postretirement benefit plans recorded to net income, net of taxes of$(51), $(48) and $(44), respectively | 82 | 79 | 70 | |||||||||
Valuation adjustment for pension and postretirement benefit plans, net of taxes of $28, $30 and $(3), respectively | (83 | ) | (49 | ) | 5 | |||||||
Change in derivatives, net of taxes of $(1), $(4) and $1, respectively | 2 | 8 | (1 | ) | ||||||||
Other, net of taxes of $0, $(1) and $0, respectively | — | 1 | 1 | |||||||||
Other comprehensive (loss) income, net of tax | (16 | ) | 22 | 62 | ||||||||
Comprehensive income attributable to Orbital ATK, Inc. | 294 | 315 | 248 |
56
ORBITAL ATK, INC.
CONSOLIDATED STATEMENTS OF CASH FLOWS
Year Ended | Year Ended | Nine Months Ended | ||||||||||
(Amounts in millions) | December 31, 2017 | December 31, 2016 | December 31, 2015 | |||||||||
Operating Activities | ||||||||||||
Continuing operations: | ||||||||||||
Net income | $ | 310 | $ | 293 | $ | 186 | ||||||
Net income from discontinued operations | — | — | (1 | ) | ||||||||
Income from continuing operations | 310 | 293 | 185 | |||||||||
Adjustments to reconcile income from continuing operations to cash provided by operating activities of continuing operations: | ||||||||||||
Depreciation | 118 | 116 | 89 | |||||||||
Amortization of intangible assets | 37 | 43 | 33 | |||||||||
Amortization and write-off of deferred financing costs | 2 | 2 | 13 | |||||||||
Fixed asset impairment | 8 | 10 | 8 | |||||||||
Deferred income taxes | 68 | 42 | 58 | |||||||||
Loss on disposal of property | 2 | 6 | 11 | |||||||||
Share-based plans expense | 23 | 21 | 19 | |||||||||
Excess tax benefits from share-based plans | — | — | (5 | ) | ||||||||
Other | 5 | 4 | — | |||||||||
Changes in assets and liabilities: | ||||||||||||
Net receivables | (122 | ) | (88 | ) | 17 | |||||||
Net inventories | 18 | (9 | ) | (16 | ) | |||||||
Income taxes receivable | — | 50 | (19 | ) | ||||||||
Accounts payable | 10 | 38 | (29 | ) | ||||||||
Contract advances and allowances | 97 | 61 | (1 | ) | ||||||||
Contract loss reserve | (45 | ) | (26 | ) | (27 | ) | ||||||
Accrued compensation | 18 | (5 | ) | (10 | ) | |||||||
Contract-related liabilities | (19 | ) | 39 | (19 | ) | |||||||
Pension and postemployment benefits | (57 | ) | (71 | ) | (4 | ) | ||||||
Other assets and liabilities | 47 | (7 | ) | — | ||||||||
Cash provided by operating activities of continuing operations | 520 | 519 | 303 | |||||||||
Cash provided by operating activities of discontinued operations | — | — | — | |||||||||
Cash provided by operating activities | 520 | 519 | 303 | |||||||||
Investing Activities | ||||||||||||
Capital expenditures | (245 | ) | (187 | ) | (105 | ) | ||||||
Cash dividend (refunded to) Vista Outdoor, net of cash transferred to Vista Outdoor in conjunction with the Distribution of Sporting Group | — | — | (6 | ) | ||||||||
Proceeds from the disposition of property, plant and equipment | — | 4 | — | |||||||||
Cash used in investing activities | (245 | ) | (183 | ) | (111 | ) | ||||||
Financing Activities | ||||||||||||
Credit facility borrowings | 505 | 930 | 745 | |||||||||
Credit facility payments | (505 | ) | (930 | ) | (745 | ) | ||||||
Payments made on bank debt | (40 | ) | (40 | ) | (25 | ) | ||||||
Payments made to extinguish debt | — | — | (1,274 | ) | ||||||||
Proceeds from issuance of long-term debt | — | — | 1,200 | |||||||||
Payments made for debt issuance costs | — | — | (10 | ) | ||||||||
Purchase of treasury shares | (32 | ) | (134 | ) | (81 | ) | ||||||
Dividends paid | (74 | ) | (70 | ) | (46 | ) | ||||||
Proceeds from employee stock compensation plans | 17 | 4 | 4 | |||||||||
Excess tax benefits from share-based plans | — | — | 5 | |||||||||
Cash used in financing activities | (129 | ) | (240 | ) | (227 | ) |
57
Increase (decrease) in cash and cash equivalents | 146 | 96 | (35 | ) | ||||||||
Cash and cash equivalents at beginning of period | 200 | 104 | 139 | |||||||||
Cash and cash equivalents at end of period | $ | 346 | $ | 200 | $ | 104 | ||||||
Supplemental Cash Flow Disclosures | ||||||||||||
Cash paid for interest, net | $ | 60 | $ | 62 | $ | 41 | ||||||
Cash paid for income taxes, net | $ | 24 | $ | 36 | $ | 26 | ||||||
Noncash investing activity: | ||||||||||||
Capital expenditures included in accounts payable of continuing operations | $ | 12 | $ | 7 | $ | 5 |
See Notes to the Consolidated Financial Statements.
58
ORBITAL ATK, INC.
CONSOLIDATED STATEMENTS OF EQUITY
(Amounts in millions except share data) | Common Stock $.01 Par Value | Additional Paid-in-capital | Retained Earnings | Accumulated Other Comprehensive Loss | Treasury Stock | Noncontrolling Interest | Total Equity | ||||||||||||||||||||||||
Shares | Amount | ||||||||||||||||||||||||||||||
Balance, March 31, 2015 | 59,427,942 | $ | 1 | $ | 2,182 | $ | 894 | $ | (848 | ) | $ | (719 | ) | $ | 11 | $ | 1,521 | ||||||||||||||
Comprehensive income | — | — | — | 186 | 62 | — | — | 248 | |||||||||||||||||||||||
Exercise of stock options | 121,477 | — | (5 | ) | — | — | 9 | — | 4 | ||||||||||||||||||||||
Restricted stock grants | 67,529 | — | (7 | ) | — | — | 7 | — | — | ||||||||||||||||||||||
Share-based compensation | — | — | 20 | — | — | — | — | 20 | |||||||||||||||||||||||
Treasury stock purchased | (1,008,445 | ) | — | — | — | — | (76 | ) | — | (76 | ) | ||||||||||||||||||||
Shares issued net of treasury stock withheld | 125,717 | — | (15 | ) | — | — | 10 | — | (5 | ) | |||||||||||||||||||||
Tax benefit related to share based plans and other | — | — | 11 | — | — | — | — | 11 | |||||||||||||||||||||||
Distribution of Sporting Group | (6 | ) | (6 | ) | |||||||||||||||||||||||||||
Dividends | — | — | — | (31 | ) | — | — | — | (31 | ) | |||||||||||||||||||||
Employee benefit plans and other | (4,225 | ) | — | 2 | — | — | (2 | ) | — | — | |||||||||||||||||||||
Balance, December 31, 2015 | 58,729,995 | 1 | 2,188 | 1,043 | (786 | ) | (771 | ) | 11 | 1,686 | |||||||||||||||||||||
Comprehensive income | — | — | — | 293 | 22 | — | — | 315 | |||||||||||||||||||||||
Exercise of stock options | 32,175 | — | (2 | ) | — | — | 2 | — | — | ||||||||||||||||||||||
Restricted stock grants | 176,800 | — | (13 | ) | — | — | 13 | — | — | ||||||||||||||||||||||
Share-based compensation | — | — | 21 | — | — | — | — | 21 | |||||||||||||||||||||||
Treasury stock purchased | (1,570,333 | ) | — | — | — | — | (124 | ) | — | (124 | ) | ||||||||||||||||||||
Shares issued net of treasury stock withheld | 172,582 | — | (16 | ) | — | — | 12 | — | (4 | ) | |||||||||||||||||||||
Tax benefit related to share based plans and other | — | — | (4 | ) | — | — | — | — | (4 | ) | |||||||||||||||||||||
Dividends | — | — | — | (70 | ) | — | — | — | (70 | ) | |||||||||||||||||||||
Employee benefit plans and other | (53,753 | ) | — | 1 | — | — | (4 | ) | — | (3 | ) | ||||||||||||||||||||
Balance, December 31, 2016 | 57,487,466 | 1 | 2,175 | 1,266 | (764 | ) | (872 | ) | 11 | 1,817 | |||||||||||||||||||||
Comprehensive income | — | — | — | 310 | (16 | ) | — | — | 294 | ||||||||||||||||||||||
Exercise of stock options | 84,544 | — | (3 | ) | — | — | 6 | — | 3 | ||||||||||||||||||||||
Restricted stock grants | 156,675 | — | (12 | ) | — | — | 12 | — | — | ||||||||||||||||||||||
Share-based compensation | — | — | 23 | — | — | — | — | 23 | |||||||||||||||||||||||
Treasury stock purchased | (230,918 | ) | — | — | — | — | (23 | ) | — | (23 | ) | ||||||||||||||||||||
Shares issued net of treasury stock withheld | 247,977 | — | (8 | ) | — | — | 18 | — | 10 | ||||||||||||||||||||||
Dividends | — | — | — | (74 | ) | — | — | — | (74 | ) | |||||||||||||||||||||
Employee benefit plans and other | (59,530 | ) | — | — | — | — | (5 | ) | — | (5 | ) | ||||||||||||||||||||
Balance, December 31, 2017 | 57,686,214 | $ | 1 | $ | 2,175 | $ | 1,502 | $ | (780 | ) | $ | (864 | ) | $ | 11 | $ | 2,045 |
See Notes to the Consolidated Financial Statements.
59
NOTES TO THE CONSOLIDATED FINANCIAL STATEMENTS
(Amounts in millions except share and per share data and unless otherwise indicated)
1. Summary of Significant Accounting Policies
Nature of Operations. Orbital ATK, Inc. (the "Company") is an aerospace and defense systems company and supplier of related products to the U.S. Government, allied nations and prime contractors. The Company is headquartered in Dulles, Virginia and has operating locations throughout the United States. The Company was incorporated in Delaware in 1990.
On February 9, 2015, the Company completed a tax-free spin-off of and distribution (the "Distribution") of its former Sporting Group to its stockholders as a new public company called Vista Outdoor Inc. ("Vista Outdoor"). Immediately following the Distribution, the Company combined with Orbital Sciences Corporation ("Orbital") through the merger of a company subsidiary with Orbital (the "Orbital-ATK Merger"). As a result of the Distribution, the Sporting Group is reported as a discontinued operation for all prior periods presented.
Basis of Presentation. The consolidated financial statements of the Company include all majority-owned affiliates. Intercompany transactions and accounts have been eliminated.
Fiscal Year. Beginning January 1, 2016, the Company changed its fiscal year from the period beginning on April 1 and ending on March 31 to the period beginning on January 1 and ending on December 31. As a result, for the fiscal period ended December 31, 2015, in these consolidated statements, including the notes thereto, the financial results are for a nine-month transition period ended December 31, 2015 ("2015 transition period"). Audited results for the year ended December 31, 2017 and 2016 are for a twelve-month period.
Use of Estimates. The preparation of consolidated financial statements in conformity with U.S. generally accepted accounting principles requires ("GAAP") management to make estimates and assumptions that affect amounts reported therein. Due to the inherent uncertainty involved in making estimates, actual results reported in future periods may differ from those estimates.
Revenue Recognition. The Company's sales come primarily from contracts with agencies of the U.S. Government and its prime contractors and subcontractors. The various U.S. Government customers, including the U.S. Navy, U.S. Army, NASA and the U.S. Air Force, make independent purchasing decisions. Consequently, each agency is regarded as a separate customer.
Contracts — Substantially all of the Company's sales are accounted for as long-term contracts. Sales under long-term contracts are accounted for under the percentage-of-completion method and include cost-plus and fixed-price contracts. Sales under cost-plus contracts are recognized as costs are incurred. Sales under fixed-price contracts are either recognized as the actual cost of work performed relates to the estimate at completion ("cost-to-cost") or based on results achieved, which usually coincides with customer acceptance ("units-of-delivery"). The majority of the Company's total revenue is accounted for using the cost-to-cost method of accounting.
Profits expected to be realized on contracts are based on management's estimates of total contract sales value and costs at completion. Estimated amounts for contract changes, including scope and claims, are included in contract sales only when realization is estimated to be probable. Assumptions used for recording sales and earnings are adjusted in the period of change to reflect revisions in contract value and estimated costs that include an allocation of overhead costs. In the period in which it is determined that a loss will be incurred on a contract, the entire amount of the estimated loss, based on gross profit along with general and administrative costs, is charged to cost of sales. Changes in estimates of contract sales, costs or profits are recognized using the cumulative catch-up method of accounting. The cumulative effect of a change in estimate is recognized in the period a change in estimate occurs. The effect of the changes on future periods of contract performance is recognized as if the revised estimate had been used since contract inception or, in the case of contracts acquired in business combinations, from the date of acquisition.
Changes in contract estimates occur for a variety of reasons including changes in contract scope, unforeseen changes in contract cost estimates due to unanticipated cost growth or risks affecting contract costs and/or the resolution of contract risks at lower costs than anticipated, termination of commercial contracts in the event of a lack of end user demand, as well as changes in contract overhead costs over the performance period. Changes in estimates could have a material effect on the Company's consolidated financial position or results of operations.
Generally, favorable changes in contract estimates recognized using the cumulative catch-up method of accounting represent margin improvement on programs where either estimated cost at completion was lower than previously
60
estimated or a change in contract scope on a program caused a higher profit rate. Conversely, the unfavorable changes in contract estimates represent margin declines on programs where either estimated cost at completion was higher than previously estimated or a change in contract scope on a program caused a lower profit rate.
Aggregate net changes in contract estimates recognized increased income before income taxes and noncontrolling interest by approximately $105 million ($1.22 per diluted share) for the year ended December 31, 2017, approximately $81 million ($1.00 per diluted share) for the year ended December 31, 2016, and approximately $38 million ($0.43 per diluted share) in the 2015 transition period. Estimated costs to complete on loss contracts at December 31, 2017 and 2016 are $1,108 million and $1,333 million, respectively.
Contracts may contain provisions to earn incentive and award fees if specified targets are achieved as well as penalty provisions related to performance. Incentive and award fees and penalties that can be reasonably estimated and are probable are recorded over the performance period of the contract. Incentive and award fees that cannot be reasonably estimated are recorded when awarded.
Other — Sales not recognized under the long-term contract method are recognized when persuasive evidence of an arrangement exists, the product has been delivered and legal title and all risks of ownership have been transferred, written contract and sales terms are complete, customer acceptance has occurred and payment is reasonably assured. Sales are reduced for allowances and price discounts.
Operating Expenses. Research and development, selling and general and administrative costs are expensed in the period incurred. Research and development ("R&D") costs include costs incurred for experimentation and design testing. Company-funded R&D is primarily for the improvement of current products and for development of next-generation technology. Customer-funded R&D is comprised primarily of activities we conduct under contracts with the U.S. Government and its prime contractors. Selling costs include bid and proposal efforts related to products and services. Costs that are incurred pursuant to contractual arrangements are recorded over the period that revenue is recognized, consistent with the Company's contract accounting policy.
Environmental Remediation and Compliance. Costs associated with environmental compliance, restoration and preventing future contamination that are estimable and probable are accrued and expensed, or capitalized as appropriate. Expected remediation, restoration and monitoring costs relating to an existing condition caused by past operations, and which do not contribute to current or future revenue generation, are accrued and expensed in the period that such costs become estimable. Liabilities are recognized for remedial and resource restoration activities when they are probable and the cost can be reasonably estimated. The Company expects that a portion of its environmental remediation costs will be recoverable under U.S. Government contracts and has recorded a receivable equal to the amounts the Company expects to recover.
The Company's engineering, financial and legal specialists estimate, based on current law and existing technologies, the cost of each environmental liability. Such estimates are based primarily upon the estimated cost of investigation and remediation required and the likelihood that other potentially responsible parties ("PRPs") will be able to fulfill their commitments at the sites where the Company may be jointly and severally liable. The Company's estimates for environmental obligations are dependent on, and affected by, the nature and extent of historical information and physical data relating to a contaminated site, the complexity of the site, methods of remediation available, the technology that will be required, the outcome of discussions with regulatory agencies and other PRPs at multi-party sites, the number and financial viability of other PRPs, changes in environmental laws and regulations, future technological developments, and the timing of expenditures; accordingly, the Company periodically evaluates and revises such estimates based on expenditures against established reserves and the availability of additional information.
Cash Equivalents. Cash equivalents are all highly liquid cash investments purchased with original maturities of three months or less.
Marketable Securities. Investments in a common collective trust that primarily invests in fixed income securities are classified as available-for-sale securities and are recorded at fair value within other noncurrent assets on the consolidated balance sheet. Unrealized gains and losses are recorded in other comprehensive income ("OCI"). When such investments are sold, the unrealized gains or losses are reversed from OCI and recognized in the consolidated income statement.
61
Net Inventories. Inventories are stated at the lower of cost or market. Inventoried costs relating to contracts in progress are stated at actual production costs, including factory overhead, initial tooling and other related costs incurred to date, reduced by amounts associated with recognized sales. Recorded amounts for raw materials, work in process and finished goods are generally determined using the average cost method.
Net Property, Plant and Equipment. Property, plant and equipment is stated at cost and depreciated over estimated useful lives. Machinery and equipment is depreciated using the double declining balance method at most of the Company's facilities, and using the straight-line method at other Company facilities. Other depreciable property is depreciated using the straight-line method. Machinery and equipment is depreciated over 1 to 30 years and buildings and improvements is depreciated over 1 to 45 years. Leasehold improvements are depreciated over the shorter of the useful life of the asset or the length of the lease.
Property, plant and equipment is reviewed for impairment when indicators of potential impairment are present. When such impairment is identified, it is recorded as a loss in that period. Maintenance and repairs are charged to expense as incurred. Major improvements that extend useful lives are capitalized and depreciated. The cost and accumulated depreciation of property, plant and equipment retired or otherwise disposed of are removed from the related accounts, and any residual values are charged or credited to income.
Accounting for Goodwill and Identifiable Intangible Assets.
Goodwill — Historically, the Company has tested goodwill for impairment on January 1 or upon the occurrence of events or changes in circumstances that indicate that the asset might be impaired. During 2015, the Company changed its fiscal year end to December 31st and as a result, has changed the timing of impairment testing, primarily in order to better align the timing with our annual operating plan, forecasting and budgeting process, to the first day of the fourth quarter and whenever events or circumstances indicate that the carrying value of goodwill may not be recoverable. The 2017 impairment analysis date was on October 2nd and the 2016 impairment analysis was October 3rd. The Company determined that the reporting units for its goodwill impairment review are its operating segments, or components of an operating segment, that constitute a business for which discrete financial information is available, and for which segment management regularly reviews the operating results.
The impairment test is performed using a two-step process. In the first step, the Company estimates the fair value of each reporting unit and compares it to the carrying value of the reporting unit, including goodwill. If the carrying amount of a reporting unit is higher than its fair value, an indication of goodwill impairment exists and the second step is performed in order to determine the amount of the goodwill impairment. In the second step, the Company determines the implied fair value of the reporting unit's goodwill which it determines by allocating the estimated fair value of the reporting unit in a manner similar to a purchase price allocation. The implied fair value is compared to the carrying amount and if the carrying amount of the reporting unit's goodwill exceeds the implied fair value of its goodwill, an impairment loss is recognized for the excess.
Identifiable Intangible Assets — The Company's primary identifiable intangible assets consist of contract backlog intangible assets recorded as part of the Orbital-ATK Merger. Identifiable intangible assets with finite lives are amortized and evaluated for impairment whenever events or changes in circumstances indicate that the carrying amount may not be recoverable. Identifiable intangibles with indefinite lives are not amortized, if applicable, and are tested for impairment annually on the first day of the fourth quarter, or more frequently if events warrant.
Treasury Stock. Shares of Company common stock repurchased under the Company’s share repurchase program are held as treasury stock. Treasury stock is accounted for using the cost method. Shares held in treasury may be reissued to satisfy (i) the vesting of performance awards, total stockholder return performance awards ("TSR awards") and restricted stock units, (ii) the grant of restricted stock and (iii) the exercise of stock options. When treasury stock is reissued, the value is determined using a weighted-average basis.
Stock-based Compensation. The Company's stock-based compensation plans, which are described more fully in Note 17, Stock Based Compensation, provide for the grant of various types of stock-based incentive awards, including performance awards, total stockholder return performance awards ("TSR awards"), restricted stock and options to purchase common stock. The types and mix of stock-based incentive awards are evaluated on an ongoing basis and may vary based on the Company's overall strategy regarding compensation, including consideration of the impact of expensing stock awards on the Company's results of operations.
62
Performance awards are valued at the fair value of the Company stock at the grant date and expense is recognized based on the number of shares expected to vest under the terms of the award under which they are granted. The Company uses an integrated Monte Carlo simulation model to determine the fair value of the TSR awards and the calculated fair value is recognized in income over the vesting period, which approximates the service period. Restricted stock issued vests over periods ranging from one to three years and is valued based on the market value of the Company stock on the grant date. The estimated grant date fair value of stock options is recognized in income on a straight-line basis over the requisite service period, generally one to three years. The estimated fair value of each option is calculated using the Black-Scholes option-pricing model.
Restructuring Costs. In fiscal 2015 and during the 2015 transition period, the Company executed business restructuring initiatives aimed at reducing the Company's fixed cost structure. The remaining restructuring liability for these actions relates primarily to lease losses on terminated leases and was $16 million at December 31, 2017 and $20 million at December 31, 2016. The change in the liability was primarily due to cash payments. No additional charges are expected for these actions.
Income Taxes. Provisions for federal, state and foreign income taxes are calculated based on reported pre-tax earnings and current tax law. Such provisions differ from the amounts currently receivable or payable because certain items of income and expense are recognized in different time periods for financial reporting purposes than for income tax purposes. Significant judgment is required in determining income taxes and evaluating tax positions. The Company periodically assesses its liabilities and contingencies for all periods that are currently open to examination or have not been effectively settled based on the most current available information. Where it is not more likely than not that the Company's tax position will be sustained, the Company records the entire resulting tax liability and when it is more likely than not of being sustained, the Company records its best estimate of the resulting tax liability. Any applicable interest and penalties related to those positions are also recorded in the consolidated financial statements. To the extent the Company's assessment of the tax outcome of these matters changes, such change in estimate will impact income taxes in the period of the change. It is the Company's policy to record any interest and penalties related to income taxes as part of the income taxes for financial reporting purposes. Deferred tax assets related to carryforwards are reduced by a valuation allowance when it is not more likely than not that the amount will be realized before expiration of the carryforward period. As part of this analysis, the Company takes into account the amount and character of the income to determine if the carryforwards will be realized. Significant estimates and judgments are required for this analysis. Changes in the amounts of valuation allowance are recorded in tax expense in the period when the change occurs. For information on the effect of the Tax Cuts and Jobs Act (the "Tax Act") that was signed into law in December 2017, see Note 14, Income Taxes.
Derivative Instruments and Hedging Activities. From time to time, the Company uses derivative instruments, consisting mainly of commodity forward contracts to hedge forecasted purchases of certain commodities, foreign currency exchange contracts to hedge forecasted transactions denominated in a foreign currency and interest rate swaps to manage interest rate risk on debt. The Company does not hold or issue derivatives for trading purposes. At the inception of each derivative instrument, the Company documents the relationship between the derivative instrument and the hedged item, as well as its risk-management objectives and strategy for undertaking the hedge transaction. The Company assesses, both at the derivative's inception and on an ongoing basis, whether the derivative instrument is highly effective in offsetting changes in the fair value of the hedged item. Derivatives are recognized on the balance sheet at fair value. The effective portion of changes in fair value of derivatives designated as cash flow hedges are recorded to accumulated OCI and recognized in earnings in the same account in which the hedged item is recognized when the hedged item impacts earnings, and the cash flows from the effective portion of cash flow hedges are classified in the same section of the cash flows as the hedged item. The ineffective portion of derivatives designated as cash flow hedges and changes in fair value of derivative instruments not designated in a qualifying hedging relationship are reflected in current earnings, and the cash flows from the ineffective portion of cash flow hedges are classified as investing activities. The Company's current derivatives are designated as cash flow hedges. See Note 3, Derivative Financial Instruments for further details.
Earnings Per Share Data. Basic earnings per share ("EPS") is computed based upon the weighted-average number of common shares outstanding for each period. Diluted EPS is computed based on the weighted-average number of common shares and common equivalent shares outstanding for each period. Common equivalent shares represent the effect of stock-based awards (see Note 17, Stock-Based Compensation) during each period presented, which, if exercised or earned, would have a dilutive effect on earnings per share.
63
Fair Value of Non-financial Instruments. The carrying amounts of receivables, inventory, accounts payable, accrued liabilities and other current assets and liabilities, approximate fair values due to the short maturity of these instruments. See Note 2, Fair Value of Financial Instruments, for additional disclosure regarding fair value of financial instruments.
Accounting Standards Updates Adopted. During the year ended December 31, 2017, the Company adopted the following Accounting Standard Updates:
In October 2016, the Financial Accounting Standards Board ("FASB") issued Accounting Standards Update ("ASU") 2016-17, Consolidation (Topic 810), Interests Held through Related Parties That Are under Common Control ("ASU 2016-17"). This ASU amends the consolidation guidance issued under ASU 2015-02, Consolidation (Topic 810) Amendments to the Consolidation Analysis, for those entities that are the single decision maker of a variable interest entity ("VIE") such that a single decision maker is not required to consider indirect interests held through related parties that are under common control with the single decision maker to be the equivalent of direct interest in their entirety. Instead, they are required to include those interests on a proportionate basis consistent with indirect interests held through other related parties. The amendments in this ASU were effective for annual reporting periods beginning after December 15, 2016, and interim periods within that reporting period. The adoption of this standard did not have a material impact on the Company’s consolidated financial statements.
Accounting Standards Updates Issued But Not Yet Adopted.
In August 2017, the FASB issued ASU 2017-12, Targeted Improvements to Accounting for Hedging Activities ("ASU 2017-12"). The ASU amends Accounting Standard Codification ("ASC") Topic 815, Derivatives and Hedging, in order to simplify hedge accounting by better aligning an entity's financial reporting for hedging relationships with its risk management activities. The ASU also simplifies the application of the hedge accounting guidance. ASU 2017-12 is effective for annual periods beginning after December 15, 2018, and interim periods therein. The ASU will be applied utilizing a modified retrospective approach to existing hedging relationships as of the adoption date. The Company does not expect the provisions of ASU 2017-12 to have a material impact on the Company's consolidated financial position, results of operations and cash flows.
In May 2017, the FASB issued ASU 2017-09, Modification Accounting for Share-Based Payment Arrangements ("ASU 2017-09"), which identifies and provides guidance on the types of changes to share-based payment awards that an entity would be required to apply modification accounting under ASU 2016-09, Stock Compensation (Topic 718). Specifically, an entity would not apply modification accounting if the fair value, vesting conditions and classification of the awards are the same immediately before and after the modification. ASU 2017-09 is effective for annual periods beginning after December 15, 2017 and will be applied prospectively to awards modified on or after the effective date. The Company does not expect the provisions of ASU 2017-09 to have a material impact on the Company's consolidated financial position, results of operations and cash flows.
In March 2017, the FASB issued ASU 2017-07, Improving the Presentation of Net Periodic Pension Cost and Net Periodic Postretirement Benefit Cost ("ASU 2017-07"). The ASU amends ASC Topic 715, Compensation—Retirement Benefits, to require employers that present a measure of operating income in their statement of income to include only the service cost component of net periodic pension costs and net periodic postretirement benefit cost in operating expenses. The ASU also stipulates that only the service cost component of net benefit cost is eligible for capitalization. This guidance is effective for fiscal years beginning after December 15, 2017. Early adoption is permitted as of the beginning of an annual period for which financial statements have not been issued or made available for issuance. Disclosures of the nature of and reason for the change in accounting principle are required in the first interim and annual periods of adoption. The Company is currently evaluating the provisions of ASU 2017-07 and its impact on the Company's consolidated financial position, results of operations and cash flows.
In February 2017, the FASB issued ASU 2017-06, Plan Accounting: Defined Benefit Pension Plans (Topic 960), Defined Contribution Pension Plans (Topic 962), Health and Welfare Benefit Plans (Topic 965), Employee Benefit Plan Master Trust Reporting (“ASU 2017-06”). The ASU relates primarily to the reporting by an employee benefit plan for its interest in a master trust. The amendments in ASU 2017-06 are effective for fiscal years beginning after December 15, 2018. Early adoption is permitted. An entity should apply the amendments in ASU 2017-06 retrospectively to each period for which financial statements are presented. The Company does not expect the provisions of ASU 2017-06 to have a material impact on the Company's consolidated financial position, results of operations and cash flows.
64
In January 2017, the FASB issued ASU 2017-04, Simplifying the Test for Goodwill Impairment ("ASU 2017-04"), which simplifies the accounting for goodwill impairments by eliminating Step 2 from the goodwill impairment test. If the carrying amount of a reporting unit exceeds its fair value, an impairment loss shall be recognized in an amount equal to that excess, versus determining an implied fair value in Step 2 to measure the impairment loss. ASU 2017-04 is effective for annual periods beginning after December 15, 2019. The Company does not expect the provisions of ASU 2017-04 to have a material impact on the Company's consolidated financial position, results of operations and cash flows.
In February 2016, the FASB issued ASU 2016-02, Leases (Topic 842), which requires recognition of lease assets and lease liabilities for those leases classified as operating leases under previous U.S. GAAP. The new standard is effective for annual reporting periods beginning after December 15, 2018 with early adoption permitted. The Company currently is evaluating the potential changes from this ASU to its future financial reporting and disclosures.
During 2016, the FASB issued ASU 2016-15, Statement of Cash Flows (Topic 230), Classification of Certain Cash Receipts and Cash Payments and ASU 2016-18, Statement of Cash Flows (Topic 230), Restricted Cash. These ASUs clarify how entities should classify certain cash receipts and cash payments on the statement of cash flows and requires that the statement of cash flows explain the change during the period in the total cash, cash equivalents and amounts generally described as restricted cash or restricted cash equivalents. These standards will be adopted on January 1, 2018 and are not expected to have a material impact on the Company's consolidated statement of cash flows.
In May 2014, the FASB issued ASU 2014-09, Revenue from Contracts with Customers (Topic 606), which will replace numerous requirements in U.S. GAAP, including industry-specific requirements, and provide companies with a single revenue recognition model for recognizing revenue from contracts with customers. The new standard is effective for annual reporting periods beginning after December 15, 2017. The core principle of the new standard is that a company should recognize revenue to depict the transfer of promised goods or services to customers in an amount that reflects the consideration to which such company expects to be entitled in exchange for those goods or services. The two permitted transition methods under the new standard are the full retrospective method, in which case the standard would be applied to each prior reporting period presented, or the modified retrospective method, in which case the cumulative effect of applying the standard would be recognized at the date of initial application.
The Company will adopt the standard on January 1, 2018 and apply the modified retrospective method. The Company has completed its analysis of ASU 2014-09, and the associated impact on the Company's business processes, systems and internal controls. As part of this analysis, the Company compared existing policies and procedures to the requirements of the standard and prepared modifications to ensure appropriate application of the standard. Additionally, the Company has designed and implemented specific controls over the adoption of the new standard. The Company did not experience significant changes to current controls. The Company is finalizing its assessment of the quantitative impact of adopting ASU 2014-09. The current anticipated financial impact of adoption is a reduction to retained earnings of approximately $325 million, a reduction to unbilled accounts receivable of approximately $475 million and increases in inventory and other current assets of approximately $150 million. The primary area of anticipated change relates to the determination of performance obligations in a contract. While not impacting the total amount of revenue recognized over the life of a contract, this determination will alter the timing of revenue recognition for certain contracts in the Company's portfolio. In addition, the Company will present expanded disclosures related to revenues and contracts with customers as required by ASU 2014-09.
Under ASU 2014-09, revenue is recognized as the Company satisfies a performance obligation by transferring control to the customer. For performance obligations satisfied over time, the objective is to measure progress in a manner which depicts the performance of transferring control to the customer. As such, the Company expects contract revenue will generally be recognized over time using a cost incurred input measure. This is consistent with the percentage of completion cost-to-cost revenue recognition model currently used for the majority of the Company's contracts.
Other new pronouncements issued but not effective for the Company until after December 31, 2017 are not expected to have a material impact on the Company's continuing financial position, results of operations and cash flows.
2. Fair Value of Financial Instruments
The current authoritative guidance on fair value clarifies the definition of fair value, prescribes a framework for measuring fair value, establishes a fair value hierarchy based on the inputs used to measure fair value, and expands disclosures about the use of fair value measurements. Fair value is defined as the price that would be
65
received to sell an asset or paid to transfer a liability (an exit price) in the principal or most advantageous market for the asset or liability in an orderly transaction between market participants on the measurement date.
The valuation techniques required by the current authoritative literature are based upon observable and unobservable inputs. Observable inputs reflect market data obtained from independent sources, while unobservable inputs reflect internal market assumptions. These two types of inputs create the following fair value hierarchy:
Level 1—Quoted prices for identical instruments in active markets.
Level 2—Quoted prices for similar instruments in active markets; quoted prices for identical or similar instruments in markets that are not active; and model-derived valuations whose inputs are observable or whose significant value drivers are observable.
Level 3—Significant inputs to the valuation model are unobservable.
The following section describes the valuation methodologies used by the Company to measure its financial instruments at fair value.
Derivative financial instruments and hedging activities — In order to manage its exposure to commodity pricing and foreign currency risk, the Company periodically utilizes commodity and foreign currency derivatives, which are considered Level 2 instruments. As discussed further in Note 3, Derivative Financial Instruments, the Company has outstanding commodity forward contracts that were entered into to hedge forecasted purchases of copper and zinc, as well as outstanding foreign currency forward contracts that were entered into to hedge forecasted transactions denominated in a foreign currency. Commodity derivatives are valued based on prices of futures exchanges and recently reported transactions in the marketplace. The Company currently holds one interest rate swap with a total notional value of $100 million. The swap is valued based on future LIBOR, and the established fixed rate is based primarily on quotes from banks. Foreign currency derivatives are valued based on observable market transactions of spot currency rates and forward currency prices.
Long-term Debt — The fair value of the variable rate long-term debt is calculated based on current market rates for debt of the same risk and maturities. The fair value of the fixed rate debt is based on market quotes for each issuance. The Company considers these to be Level 2 instruments.
The Company's non-financial instruments measured at fair value on a non-recurring basis include goodwill, indefinite-lived intangible assets and long-lived tangible assets. The valuation methods used to determine fair value require a significant degree of management judgment to determine the key assumptions. As such, the Company generally classifies non-financial instruments as either Level 2 or Level 3 fair value measurements. At December 31, 2017 and 2016, the Company did not have any non-financial instruments measured at fair value on a non-recurring basis.
66
The following tables set forth, by level within the fair value hierarchy, the Company's financial assets and liabilities that are measured at fair value on a recurring basis (in millions):
December 31, 2017 | ||||||||||||
Fair Value Measurements Using Inputs Considered as | ||||||||||||
Level 1 | Level 2 | Level 3 | ||||||||||
Assets: | ||||||||||||
Derivatives | $ | — | $ | 13 | $ | — | ||||||
Liabilities: | ||||||||||||
Derivatives | $ | — | $ | 2 | $ | — |
December 31, 2016 | ||||||||||||
Fair Value Measurements Using Inputs Considered as | ||||||||||||
Level 1 | Level 2 | Level 3 | ||||||||||
Assets: | ||||||||||||
Derivatives | $ | — | $ | 9 | $ | — | ||||||
Liabilities: | ||||||||||||
Derivatives | $ | — | $ | 1 | $ | — |
Recorded carrying amount and fair value of debt was as follows (in millions):
December 31, 2017 | December 31, 2016 | ||||||||||||||
Carrying Amount | Fair Value | Carrying Amount | Fair Value | ||||||||||||
Fixed rate debt | $ | 700 | $ | 732 | $ | 700 | $ | 727 | |||||||
Variable rate debt | $ | 710 | $ | 706 | $ | 750 | $ | 746 |
Investments in marketable securities — The Company has investments in marketable securities held in a common collective trust ("CCT") that are primarily fixed income securities used to pay benefits under a nonqualified supplemental executive retirement plan for certain executives and highly compensated employees. Investments in a collective investment vehicle are valued by multiplying the investee company's net asset value per share, as determined by the investee company, with the number of units or shares owned at the valuation date. Net asset value per share is determined by the investee company's custodian or fund administrator by deducting from the value of the assets of the investee company all its liabilities and the resulting number is divided by the outstanding number of shares or units. Investments held by the CCT, including collateral invested for securities on loan, are valued on the basis of valuations furnished by a pricing service approved by the CCT's investment manager, which determines valuations using methods based on market transactions for comparable securities and various relationships between securities which are generally recognized by institutional traders, or at fair value as determined in good faith by the CCT's investment manager. The fair value of these securities, not subject to leveling, is included within other noncurrent assets on the Company's consolidated balance sheet. The fair value of these securities is measured on a recurring basis and was $15 million and $13 million at December 31, 2017 and 2016, respectively.
3. Derivative Financial Instruments
The Company is exposed to market risks arising from adverse changes in commodity prices affecting the cost of raw materials and energy, interest rates and foreign exchange risks. In the normal course of business, these risks are managed through a variety of strategies, including the use of derivative instruments.
Cash Flow Hedges
The Company periodically uses interest rate swaps to hedge forecasted interest payments and the risk associated with variable interest rates on long-term debt.
67
The Company entered into interest rate swaps during fiscal 2014 requiring fixed rate payments on a total notional amount of $400 million, of which $100 million remains outstanding, and receives one-month LIBOR. The fair value of interest rate swap agreements approximates the amount at which they could be settled, based on future LIBOR, and the established fixed rate is based primarily on quotes from banks.
Interest rate swap agreements entered into to manage interest costs and risk associated with variable interest rates outstanding at December 31, 2017 were as follows (in millions):
Notional | Fair Value | Pay Fixed | Receive Floating | Maturity Date | ||||||||||||
Non-amortizing swap | $ | 100 | $ | — | 1.69 | % | 1.57 | % | August 2018 |
The amount to be paid or received under these swaps is recorded as an adjustment to interest expense.
The counterparties to the interest rate swap agreements expose the Company to credit risk in the event of nonperformance. However, at December 31, 2017, the outstanding swap agreements were in a net liability position which would require the Company to make the net settlement payments to the counterparties if the agreements were settled as of that date. The Company does not anticipate nonperformance by counterparties and does not hold or issue derivative financial instruments for trading purposes.
Commodity forward contracts are periodically used to hedge forecasted purchases of certain commodities. The contracts essentially establish a fixed price for the underlying commodity and are designated and qualify as effective cash flow hedges of purchases of the commodity. Ineffectiveness is calculated as the amount by which the change in the fair value of the derivatives exceeds the change in the fair value of the anticipated commodity purchases.
Commodity forward contracts outstanding that hedge forecasted commodity purchases were as follows:
(Amounts in millions of pounds) | December 31, | |||||
2017 | 2016 | |||||
Copper | 17 | 10 | ||||
Zinc | 6 | 3 |
Due to the customer contract requirements, the benefits associated with the commodity contracts may be passed on to the customer and not realized by the Company.
The Company enters into foreign currency forward contracts to hedge forecasted transactions, denominated in foreign currencies. These transactions qualify as effective cash flow hedges and are designated as such.
Ineffectiveness with respect to forecasted transactions is calculated based on changes in the forward rate until the anticipated purchase or cash receipt occurs; ineffectiveness of the hedge of the accounts payable is evaluated based on the change in fair value of its anticipated settlement.
As of December 31, 2017, the Company had the following outstanding Euro currency forward contracts in place:
(Amounts in millions of Euros) | December 31, | |||||||
2017 | 2016 | |||||||
Euros Sold | € | 7 | € | 33 | ||||
Euros Purchased | 36 | 45 |
The gains or losses on the commodity forward contracts are recorded in inventory as the commodities are purchased and in cost of sales when the related inventory is sold. The gains or losses on the foreign currency forward contracts are recorded in earnings when the related inventory is sold or customer cash receipts are received.
The fair values of the commodity and foreign currency forward contracts are recorded in other assets or liabilities, as appropriate, and the effective portion is reflected in accumulated other comprehensive income (loss) in the financial statements.
68
Fair values in the consolidated balance sheets related to derivative instruments designated as hedging instruments were as follows (in millions):
Asset Derivatives Fair Value | Liability Derivatives Fair Value | |||||||||||||||
December 31, 2017 | December 31, 2016 | December 31, 2017 | December 31, 2016 | |||||||||||||
Commodity forward contracts(1) | $ | 11 | $ | 5 | $ | — | $ | — | ||||||||
Foreign currency forward contracts(1) | 2 | 3 | 2 | — | ||||||||||||
Foreign currency forward contracts(2) | — | 1 | — | — | ||||||||||||
Interest rate swap contracts(2) | — | — | — | 1 | ||||||||||||
Total | $ | 13 | $ | 9 | $ | 2 | $ | 1 |
____________________________________________________________
(1) Location - Other current assets/Other current liabilities
(2) Location - Other noncurrent assets/Other noncurrent liabilities
Gains and (losses) reclassified from Accumulated Other Comprehensive Loss to the consolidated statements of comprehensive income related to derivative instruments were as follows (in millions):
Location | Year Ended December 31, 2017 | Year Ended December 31, 2016 | ||||||||
Commodity forward contracts | Cost of sales | $ | 2 | $ | (3 | ) | ||||
Interest rate swap contracts | Interest expense | (1 | ) | (3 | ) | |||||
Foreign currency forward contracts | Cost of sales | 4 | — |
The Company expects the remaining unrealized losses will be realized and reported in cost of sales or interest expense depending on the type of contract consistent with realized gains and losses noted in the table above. Estimated and actual gains or losses will change as market prices change.
The Company performs assessments of the effectiveness of hedge instruments on a quarterly basis and determined the hedges to be highly effective.
There was no ineffective portion of derivative instruments and no derivatives were excluded from effectiveness testing during the years ended December 31, 2017 and December 31, 2016; accordingly, the Company did not recognize any related gains or losses in the income statement.
All derivatives used by the Company during the periods presented were designated as hedging instruments for accounting purposes.
4. Mergers and Divestiture
Northrop Grumman. On September 17, 2017, the Company entered into an Agreement and Plan of Merger (the “Merger Agreement”) with Northrop Grumman Corporation (“Northrop Grumman”) and Neptune Merger, Inc., a wholly owned subsidiary of Northrop Grumman (“Sub”), under which Sub will merge with and into the Company,
with the Company continuing as the surviving corporation and a wholly-owned subsidiary of Northrop Grumman (the “Merger”).
Upon the closing of the Merger, each outstanding share of Company common stock, other than shares owned by the Company, Northrop Grumman or Sub (which will be canceled) and appraisal shares, will automatically be converted into the right to receive $134.50 in cash, without interest and less any applicable withholding taxes.
The stockholders of the Company voted in favor of approving the Merger Agreement at a special meeting held on November 29, 2017. Closing remains subject to customary closing conditions, including obtaining required regulatory approvals. The Company received a request for additional information from the Federal Trade Commission ("FTC") on December 6, 2017.
Orbital. On February 9, 2015, the Company completed the spin-off and Distribution of its former Sporting Group to its stockholders and merged with Orbital pursuant to a transaction agreement dated April 28, 2014 (the "Transaction Agreement"). Both the Distribution and Orbital-ATK Merger were structured to be tax-free to U.S. stockholders for U.S. federal income tax purposes. Under the Transaction Agreement, a subsidiary of the Company merged with and into Orbital, with Orbital continuing as a wholly-owned subsidiary of the Company.
Ongoing Business with Vista Outdoor
In conjunction with the Distribution of the Company's former Sporting Group, the Company entered into two supply agreements and one Transition Services Agreement ("TSA") with Vista Outdoor. The supply agreements call for Vista Outdoor to purchase certain minimum quantities of ammunition and gun powder from the Company through 2018 or 2017, as applicable. The supply agreements, which are priced at arms-length, expire in 2018 for the ammunition agreement with the gun powder agreement expiring in 2017. The supply agreements had an option to be extended in one-to-three year increments. The agreements were not extended and expired or will expire according to their original terms. Under the terms of the TSA, the Company provided Vista Outdoor with administrative services for 12 months following the Distribution and provided tax-related services for 18 months following the Distribution, extendable to 30 months. At the option of Vista Outdoor, the Company is currently providing tax-audit related services. Fees for services under the TSA are charged to Vista Outdoor.
Sales to Vista Outdoor under the two supply agreements, reported within Defense Systems Group, were $181 million for the year ended December 31, 2017, $238 million for the year ended December 31, 2016 and $138 million for the 2015 transition period.
5. Net Receivables
Net receivables, including amounts due under long-term contracts, consisted of the following:
December 31, | ||||||||
2017 | 2016 | |||||||
(in millions) | ||||||||
Billed receivables | ||||||||
U.S. Government contracts | $ | 159 | $ | 132 | ||||
Commercial and other | 92 | 112 | ||||||
Unbilled receivables | ||||||||
U.S. Government contracts | 850 | 806 | ||||||
Commercial and other | 793 | 691 | ||||||
Less allowance for doubtful accounts | (1 | ) | — | |||||
Net receivables | $ | 1,893 | $ | 1,741 |
Receivable balances are shown net of customer progress payments received of $697 million at December 31, 2017 and $601 million at December 31, 2016.
Unbilled receivables represent the balance of recoverable costs and accrued profit, comprised principally of revenue recognized on contracts for which billings have not been presented to the customer because the amounts were earned but not contractually billable at the balance sheet date. These amounts include expected additional billable general overhead costs and fees on flexibly priced contracts awaiting final rate negotiations.
Progress payments received from customers relating to the uncompleted portions of contracts are offset against unbilled receivable balances or applicable inventories. Any remaining progress payment balances are classified as contract advances.
At December 31, 2017 and 2016, the aggregate amount of contract-related unbilled receivables the Company does not expect to collect within the next 12 months was $275 million and $287 million, respectively.
The Company records an allowance for doubtful accounts, reducing the receivables balance to an amount the Company estimates is collectible from customers. Estimates used in determining the allowance for doubtful accounts are based on current trends, aging of accounts receivable, periodic credit evaluations of customers' financial condition and historical collection experience.
6. Net Inventories
Net inventories consisted of the following:
December 31, | ||||||||
2017 | 2016 | |||||||
(in millions) | ||||||||
Raw materials | $ | 89 | $ | 93 | ||||
Work/contracts in process | 113 | 121 | ||||||
Finished goods | 19 | 1 | ||||||
Net inventories | $ | 221 | $ | 215 |
7. Net Property, Plant and Equipment
Net property, plant and equipment consisted of the following:
December 31, | ||||||||
2017 | 2016 | |||||||
(in millions) | ||||||||
Land | $ | 29 | $ | 29 | ||||
Buildings and other improvements | 412 | 383 | ||||||
Machinery, equipment and other | 1,432 | 1,313 | ||||||
Property not yet in service | 280 | 212 | ||||||
Gross property, plant and equipment | 2,153 | 1,937 | ||||||
Less accumulated depreciation | (1,219 | ) | (1,121 | ) | ||||
Net property, plant and equipment | $ | 934 | $ | 816 |
Depreciation expense was $118 million for the year ended December 31, 2017, $116 million in the year ended December 31, 2016 and $89 million in the 2015 transition period.
8. Goodwill and Net Intangibles
Changes in goodwill by segment were as follows:
Flight Systems Group | Defense Systems Group | Space Systems Group | Total | |||||||||||||
(in millions) | ||||||||||||||||
Balance, December 31, 2015 | $ | 923 | $ | 363 | $ | 542 | $ | 1,828 | ||||||||
Measurement period adjustments | 6 | — | (2 | ) | 4 | |||||||||||
Balance, December 31, 2016 | 929 | 363 | 540 | 1,832 | ||||||||||||
Adjustments | — | — | — | — | ||||||||||||
Balance at December 31, 2017 | $ | 929 | $ | 363 | $ | 540 | $ | 1,832 |
The goodwill impairment analysis conducted for the years ended December 31, 2017 and 2016 and for the 2015 transition period concluded there were no impairments.
Goodwill recorded within Defense Systems Group and Space Systems Group is presented net of accumulated impairment losses totaling $4 million and $143 million, respectively, at December 31, 2017.
Net intangibles consisted of the following amortizing intangibles:
69
December 31, 2017 | December 31, 2016 | ||||||||||||||||||||||
Gross Carrying Amount | Accumulated Amortization | Total | Gross Carrying Amount | Accumulated Amortization | Total | ||||||||||||||||||
(in millions) | |||||||||||||||||||||||
Contract backlog | $ | 173 | $ | (115 | ) | $ | 58 | $ | 173 | $ | (79 | ) | $ | 94 | |||||||||
Patented technology | 11 | (8 | ) | 3 | 11 | (7 | ) | 4 | |||||||||||||||
Customer relationships and other | — | — | — | 2 | (2 | ) | — | ||||||||||||||||
Net intangibles | $ | 184 | $ | (123 | ) | $ | 61 | $ | 186 | $ | (88 | ) | $ | 98 |
The contract backlog asset in the table above is being amortized as underlying costs are recognized under the contract. The other assets in the table above are being amortized using a straight-line method. Amortization expense related to these assets was $37 million for the year ended December 31, 2017, $43 million for the year ended December 31, 2016 and $33 million in the 2015 transition period.
Scheduled amortization is as follows:
Contract Backlog | Patented Technology | Total | ||||||||||
(in millions) | ||||||||||||
2018 | $ | 25 | $ | 1 | $ | 26 | ||||||
2019 | 22 | 1 | 23 | |||||||||
2020 | 11 | 1 | 12 | |||||||||
2021 | — | — | — | |||||||||
2022 | — | — | — | |||||||||
Total | $ | 58 | $ | 3 | $ | 61 |
9. Other Current Liabilities
Other current liabilities consisted of the following:
December 31, | ||||||||
2017 | 2016 | |||||||
(in millions) | ||||||||
Employee benefits and insurance | $ | 81 | $ | 74 | ||||
Deferred lease obligation | 2 | 2 | ||||||
Interest | 10 | 10 | ||||||
Accrued tax liabilities | 26 | 28 | ||||||
Environmental liability | 5 | 6 | ||||||
Other | 86 | 63 | ||||||
Total other current liabilities | $ | 210 | $ | 183 |
70
10. Long-term Debt
Long-term debt, including the current portion, consisted of the following:
December 31, | ||||||||
2017 | 2016 | |||||||
(in millions) | ||||||||
Senior Credit Facility: | ||||||||
Term Loan A due 2020 | $ | 710 | $ | 750 | ||||
Revolving Credit Facility due 2020 | — | — | ||||||
5.25% Senior Notes due 2021 | 300 | 300 | ||||||
5.50% Senior Notes due 2023 | 400 | 400 | ||||||
Carrying amount of long-term debt | 1,410 | 1,450 | ||||||
Unamortized debt issuance costs: | ||||||||
Senior Credit Facility | 4 | 5 | ||||||
5.25% Senior Notes due 2021 | 1 | 2 | ||||||
5.50% Senior Notes due 2023 | 4 | 5 | ||||||
Unamortized debt issuance costs | 9 | 12 | ||||||
Long-term debt less unamortized debt issuance costs | 1,401 | 1,438 | ||||||
Less: Current portion of long-term debt | 40 | 40 | ||||||
Long-term debt | $ | 1,361 | $ | 1,398 |
Senior Credit Facility
In September 2015, the Company refinanced its former senior credit facility (the "Former Senior Credit Facility") with a new senior credit facility (the "Senior Credit Facility"), which is comprised of a term loan of $800 million (the "Term Loan A") and a revolving credit facility of $1,000 million (the "Revolving Credit Facility"), both of which mature in 2020. The Term Loan A is subject to quarterly principal payments of $10 million, with the remaining balance due at maturity. Substantially all tangible and intangible assets of the Company and certain domestic subsidiaries, excluding real property, are pledged as collateral under the Senior Credit Facility. Borrowings under the Senior Credit Facility bear interest at a per annum rate equal to either the sum of a base rate plus a margin or the sum of a LIBOR rate plus a margin. Borrowings under the Former Senior Credit Facility were charged interest at a rate equal to either the sum of a base rate plus a margin or the sum of a Eurodollar rate plus a margin. Each margin is based on the Company's total leverage ratio. In compliance with the terms of the Senior Credit Facility, the current base rate margin is 0.25% and the current LIBOR margin is 1.25%. The weighted-average interest rate for the Term Loan A, after taking into account the interest rate swaps discussed below, was 2.84% at December 31, 2017. The Company pays a quarterly commitment fee on the unused portion of the Revolving Credit Facility based on its total leverage ratio. Based on the Company's current total leverage ratio, this current fee is 0.20%. At December 31, 2017, the Company had no borrowings outstanding on the Revolving Credit Facility and had outstanding letters of credit of $240 million, which reduced amounts available on the Revolving Credit Facility to $760 million.
As a result of the refinancing in September 2015, the Company recorded a charge of $10 million, reported in net interest expense, to write off a portion of the unamortized debt issuance costs associated with the Former Senior Credit Facility. There are debt issuance costs totaling $6 million associated with the Former Senior Credit Facility in addition to debt issuance costs incurred related to the new Senior Credit Facility that are being amortized to interest expense over five years, the term of the Senior Credit Facility.
5.25% Senior Notes
In fiscal 2014, the Company issued $300 million aggregate principal amount of 5.25% Senior Notes (the "5.25% Notes") that mature on October 1, 2021. These notes are general unsecured obligations. Interest on these notes is payable on April 1 and October 1 of each year. The Company has the right to redeem some or all of these notes on or after October 1, 2016, at specified redemption prices. Debt issuance costs of $3 million related to these notes are being amortized to interest expense over eight years, the term of the notes.
71
5.50% Senior Notes
In September 2015, the Company issued $400 million aggregate principal amount of 5.50% Senior Notes (the "5.50% Notes") that mature on October 1, 2023. These notes are general unsecured obligations. Interest on these notes is payable on April 1 and October 1 of each year. The Company has the right to redeem some or all of these notes from time to time on or after October 1, 2018, at specified redemption prices. Debt issuance costs of $6 million related to these notes are being amortized to interest expense over eight years, the term of the notes.
Interest Rate Swaps
In fiscal 2014, the Company entered into floating-to-fixed interest rate swap agreements in order to hedge the Company's forecasted interest payments on its outstanding variable rate debt, which has included the term loans associated with the Senior Credit Facility and Former Senior Credit Facility.
At December 31, 2017, the Company had the following cash flow hedge interest rate swaps in place:
Notional | Fair Value | Pay Fixed | Receive Floating | Maturity Date | ||||||||||||
(in millions) | ||||||||||||||||
Non-amortizing swap | $ | 100 | $ | — | 1.69 | % | 1.57 | % | August 2018 |
The amount to be paid or received under these swaps is recorded as an adjustment to interest expense.
Rank and Guarantees
The 5.25% Notes and the 5.50% Notes are the Company's general unsecured and unsubordinated obligations and rank equally in right of payment with all of the Company's existing and future unsecured and unsubordinated indebtedness, rank senior in right of payment to all of the Company's existing and future subordinated indebtedness, and are effectively subordinated to all existing and future senior secured indebtedness, including the Senior Credit Facility, to the extent of the collateral. The 5.25% Notes and the 5.50% Notes are guaranteed on an unsecured basis, jointly and severally and fully and unconditionally, by substantially all of the Company's domestic subsidiaries. The Senior Credit Facility obligations are guaranteed on a secured basis, jointly and severally and fully and unconditionally, by substantially all of the Company's domestic subsidiaries. All of these guarantor subsidiaries are 100% owned by the Company. The Company, exclusive of these guarantor subsidiaries, has no independent operations or material assets.
Scheduled Minimum Loan Payments
Scheduled minimum loan payments are as follows:
(in millions) | |||
2018 | $ | 40 | |
2019 | 40 | ||
2020 | 630 | ||
2021 | 300 | ||
2022 | — | ||
Thereafter | 400 | ||
Total | $ | 1,410 |
Covenants and Default Provisions
The Company's Senior Credit Facility and the indentures governing the 5.25% Notes and the 5.50% Notes impose restrictions on the Company, including limitations on its ability to incur additional debt, enter into capital leases, grant liens, pay dividends and make certain other payments, sell assets, or merge or consolidate with or into another entity. In addition, the Senior Credit Facility limits the Company's ability to enter into sale-and-leaseback transactions. The 5.25% Notes and 5.50% Notes limit the aggregate sum of dividends, share repurchases and other designated restricted payments. The Senior Credit Facility also requires the Company to meet and maintain
72
specified financial ratios, including a minimum interest coverage ratio and a maximum consolidated total leverage ratio. The Company's debt agreements contain cross-default provisions so that noncompliance with the covenants within one debt agreement that would give rise to the right to accelerate repayment of any outstanding indebtedness could cause a default under other debt agreements as well. The Company's ability to comply with these covenants and to meet and maintain the financial ratios may be affected by events beyond its control. Borrowings under the Senior Credit Facility are subject to compliance with these covenants. The Company is in compliance with its credit agreement covenants as of December 31, 2017.
11. Accumulated Other Comprehensive Loss
Changes in Accumulated Other Comprehensive Income (Loss) ("AOCI"), net of income taxes, were as follows:
Year Ended December 31, 2017 | Year Ended December 31, 2016 | ||||||||||||||||||||||||||||||
Derivatives | Pension and Other Post- retirement Benefits | Available-for-sale Securities | Total | Derivatives | Pension and Other Post- retirement Benefits | Available-for-sale Securities | Total | ||||||||||||||||||||||||
(in millions) | |||||||||||||||||||||||||||||||
Beginning of period unrealized gain (loss) in AOCI | $ | 5 | $ | (771 | ) | $ | 2 | $ | (764 | ) | $ | (3 | ) | $ | (784 | ) | $ | 1 | $ | (786 | ) | ||||||||||
Net increase in fair value of derivatives | 5 | — | — | 5 | 4 | — | — | 4 | |||||||||||||||||||||||
Net (gains) losses reclassified from AOCI, offsetting the price paid to suppliers(1) | (3 | ) | — | — | (3 | ) | 4 | — | — | 4 | |||||||||||||||||||||
Net actuarial losses reclassified from AOCI(2) | — | 82 | — | 82 | — | 79 | — | 79 | |||||||||||||||||||||||
Prior service costs reclassified from AOCI(2) | — | (17 | ) | — | (17 | ) | — | (17 | ) | — | (17 | ) | |||||||||||||||||||
Valuation adjustment for pension and postretirement benefit plans | — | (83 | ) | — | (83 | ) | — | (49 | ) | — | (49 | ) | |||||||||||||||||||
Other | — | — | — | — | — | — | 1 | 1 | |||||||||||||||||||||||
End of period unrealized gain (loss) in AOCI | $ | 7 | $ | (789 | ) | $ | 2 | $ | (780 | ) | $ | 5 | $ | (771 | ) | $ | 2 | $ | (764 | ) |
_________________________________________
(1) | Amounts related to derivative instruments that were reclassified from AOCI and recorded as a component of cost of sales or interest expense for each period presented. |
(2) | Amounts related to pension and other postretirement benefits that were reclassified from AOCI and recorded as a component of net periodic benefit cost for each period presented (Note 13, Employee Benefit Plans). |
73
12. Earnings per Share
The following is a reconciliation of the numerator and denominator used in the basic and diluted earnings per share ("EPS") calculations, with amounts in millions, except per share data:
Year Ended December 31, 2017 | Year Ended December 31, 2016 | Nine Months Ended December 31, 2015 | |||||||||
Numerator: | |||||||||||
Income from continuing operations of Orbital ATK, Inc. | $ | 310 | $ | 293 | $ | 185 | |||||
Income from discontinued operations | — | — | 1 | ||||||||
Net income attributable to Orbital ATK, Inc. | 310 | 293 | 186 | ||||||||
Earnings allocated to participating securities | — | — | — | ||||||||
Income available to common stockholders | $ | 310 | $ | 293 | $ | 186 | |||||
Denominator: | |||||||||||
Weighted-average shares of common stock | 57.38 | 57.99 | 59.36 | ||||||||
Dilutive effect of stock-based awards | 0.53 | 0.47 | 0.56 | ||||||||
Diluted weighted-average shares of common stock | 57.91 | 58.46 | 59.92 | ||||||||
Anti-dilutive stock options and other stock awards excluded from the calculation of diluted earnings per share | 0.10 | 0.31 | 0.10 | ||||||||
Net income per common share from: | |||||||||||
Basic: | |||||||||||
Continuing operations | $ | 5.39 | $ | 5.05 | $ | 3.12 | |||||
Discontinued operations | — | — | 0.02 | ||||||||
Net income attributable to Orbital ATK, Inc. | $ | 5.39 | $ | 5.05 | $ | 3.14 | |||||
Diluted: | |||||||||||
Continuing operations | $ | 5.34 | $ | 5.01 | $ | 3.09 | |||||
Discontinued operations | — | — | 0.02 | ||||||||
Net income attributable to Orbital ATK, Inc. | $ | 5.34 | $ | 5.01 | $ | 3.11 |
Diluted earnings per share is calculated using net income available to common stockholders divided by the diluted weighted average number of common shares outstanding during each period determined using the treasury stock method.
13. Employee Benefit Plans
The Company provides defined benefit pension plans and defined contribution plans for its employees. The Company has tax-qualified defined benefit plans, a supplemental (nonqualified) defined benefit pension plan, a defined contribution plan and a supplemental (non-qualified) defined contribution plan. A qualified plan meets the requirements of certain sections of the Internal Revenue Code and, generally, contributions to qualified plans are tax deductible. A qualified plan typically provides benefits to a broad group of employees and may not discriminate in favor of highly compensated employees in coverage, benefits or contributions. In addition, the Company provides medical and life insurance benefits to certain retirees and their eligible dependents through its postretirement plans.
Defined Benefit Plans
The Company's noncontributory defined benefit pension plans include the following legacy Alliant Techsystems Inc. plans: "Alliant Techsystems Inc. Pension and Retirement Plan" and "Thiokol Propulsion Pension Plan" (the "ATK Plans") and the legacy Orbital Sciences plans: "Fairchild Bargained Plan" and "Fairchild Space and Defense Plan" (the "Orbital Plans"). The Orbital Plans were merged into the Alliant Techsystems Inc. Pension and Retirement Plan on December 31, 2015 and the combined plan's name was changed to the "Orbital ATK, Inc. Pension and Retirement Plan." The Company's ongoing defined benefit pension plans are the Orbital ATK Inc. Pension and Retirement Plan and the Thiokol Propulsion Pension Plan (the "Orbital ATK Plans").
74
The Company is required to reflect the funded status of the pension and other postretirement benefit ("PRB") plans on the consolidated balance sheet. The funded status of the plans is measured as the difference between the plan assets at fair value and the projected benefit obligation. The Company has recognized the aggregate of all underfunded plans within the accrued pension liability and postretirement and postemployment benefits liabilities. The Company has recognized the aggregate of all overfunded plans within other noncurrent assets. The portion of the amount by which the actuarial present value of benefits included in the projected benefit obligation exceeds the fair value of plan assets, payable in the next 12 months, is reflected in other accrued liabilities.
Previously unrecognized differences between actual amounts and estimates based on actuarial assumptions are included in accumulated other comprehensive loss in the consolidated balance sheet and the difference between actual amounts and estimates based on actuarial assumptions has been recognized in other comprehensive income in the period in which they occur.
The Company's measurement date for remeasuring its plan assets and benefit obligations is December 31.
Pension Plans. The ATK Plans are qualified noncontributory defined benefit pension plans that cover substantially all legacy ATK employees hired prior to January 1, 2007. Eligible legacy ATK non-union employees hired on or after January 1, 2007 and certain union employees are not covered by a defined benefit plan but receive an employer contribution through a defined contribution plan, discussed below. Prior to July 1, 2013 (January 1, 2014, January 1, 2015 and April 1, 2016 for certain union groups), the ATK Plans provided either pension benefits based on employee annual pay levels and years of credited service or stated amounts for each year of credited service. Effective July 1, 2013 and with certain collective bargaining agreements, pension benefits were frozen and a new cash balance formula applicable to pay and service was implemented. The cash balance formula provides each impacted employee with pay credits based on the sum of that employee's age plus years of pension service at December 31 of each calendar year, plus 4% annual interest credits. The Orbital Plans were frozen in 1994 and no pension benefits are being accrued by those employees. The Company funds the Orbital ATK Plans in accordance with federal requirements calculated using appropriate actuarial methods. Depending on the plan they are covered by, employees generally vest after three or five years.
The Company also sponsors a nonqualified supplemental executive retirement plan which provides certain executives and highly compensated employees the opportunity to receive pension benefits in excess of those payable through tax-qualified pension plans. The benefit obligation of these plans is included in the pension information below.
Other Postretirement Benefit Plans. Generally, employees who terminated employment from the Company on or before January 1, 2004 and were at least age 50 or 55 with at least five or ten years of service, depending on the provisions of the pension plan they are eligible for, are entitled to a pre- and/or post-65 health care company subsidy and retiree life insurance coverage. Employees who terminated employment after January 1, 2004, but before January 1, 2006, are eligible only for a pre-65 Company subsidy. The portion of the health care premium cost borne by the Company for such benefits is based on the pension plan the employees are eligible for, years of service and age at termination.
During the year ending December 31, 2016, the Company amended its retiree health care plan to provide coverage through a private exchange effective January 1, 2017. The exchange offers the retiree a broad choice of health care plans from which to choose. The Company will contribute fixed payments to a Health Retirement Account (HRA), when applicable, for those retirees that previously had subsidized health care coverage through the Company. The Company's contributions to the HRAs are retirees' funds to be spent on qualified health care premiums and eligible out-of-pocket expenses. This plan amendment caused a remeasurement that increased the Company's funded status by $39 million and will reduce expenses recorded in future periods.
75
The following table shows changes in the benefit obligation, plan assets and funded status of the Company's qualified and non-qualified pension plans and other PRB plans, including Orbital Plans. Benefit obligation balances presented below reflect the projected benefit obligation ("PBO") for pension plans and Accumulated PRB obligations ("APBO") or other PRB plans.
Pension Benefits | Other Postretirement Benefits | |||||||||||||||
Year Ended December 31, 2017 | Year Ended December 31, 2016 | Year Ended December 31, 2017 | Year Ended December 31, 2016 | |||||||||||||
(in millions) | ||||||||||||||||
Change in benefit obligation: | ||||||||||||||||
Benefit obligation at beginning of period | $ | 2,926 | $ | 2,953 | $ | 69 | $ | 114 | ||||||||
Service cost | 17 | 18 | — | — | ||||||||||||
Interest cost | 98 | 101 | 2 | 3 | ||||||||||||
Plan amendments | — | — | — | (39 | ) | |||||||||||
Actuarial loss (gain) | 229 | 87 | 3 | 1 | ||||||||||||
Retiree contributions | — | — | — | 5 | ||||||||||||
Benefits paid | (218 | ) | (233 | ) | (7 | ) | (15 | ) | ||||||||
Benefit obligation at end of period | 3,052 | 2,926 | 67 | 69 | ||||||||||||
Change in plan assets: | ||||||||||||||||
Fair value of plan assets at beginning of period | 2,208 | 2,190 | 61 | 60 | ||||||||||||
Actual return on plan assets | 277 | 131 | 4 | 4 | ||||||||||||
Retiree contributions | — | — | — | 5 | ||||||||||||
Employer contributions | 118 | 120 | 3 | 7 | ||||||||||||
Benefits paid | (218 | ) | (233 | ) | (7 | ) | (15 | ) | ||||||||
Fair value of plan assets at end of period | 2,385 | 2,208 | 61 | 61 | ||||||||||||
Unfunded status | $ | (667 | ) | $ | (718 | ) | $ | (6 | ) | $ | (8 | ) |
Pension Benefits | Other Postretirement Benefits | |||||||||||||||
December 31, 2017 | December 31, 2016 | December 31, 2017 | December 31, 2016 | |||||||||||||
(in millions) | ||||||||||||||||
Noncurrent assets | $ | — | $ | — | $ | 19 | $ | 17 | ||||||||
Other current liabilities | (4 | ) | (3 | ) | (3 | ) | (3 | ) | ||||||||
Postretirement benefit liabilities | — | — | (22 | ) | (22 | ) | ||||||||||
Pension liabilities | (663 | ) | (715 | ) | — | — | ||||||||||
Net amount recognized | $ | (667 | ) | $ | (718 | ) | $ | (6 | ) | $ | (8 | ) | ||||
Accumulated other comprehensive loss (income) related to: | ||||||||||||||||
Unrecognized net actuarial losses | $ | 1,376 | $ | 1,398 | $ | 16 | $ | 15 | ||||||||
Unrecognized prior service benefits | (90 | ) | (110 | ) | (36 | ) | (43 | ) | ||||||||
Accumulated other comprehensive loss (income) | $ | 1,286 | $ | 1,288 | $ | (20 | ) | $ | (28 | ) |
76
The estimated amount that will be amortized from AOCI into net periodic benefit cost in 2018 is as follows:
Pension | Other Postretirement Benefits | |||||||
(in millions) | ||||||||
Recognized net actuarial losses | $ | 147 | $ | 2 | ||||
Amortization of prior service benefits | (20 | ) | (5 | ) | ||||
Total | $ | 127 | $ | (3 | ) |
The accumulated benefit obligation for all defined benefit pension plans was $3,052 million at December 31, 2017 and $2,926 million at December 31, 2016.
December 31, | ||||||||
2017 | 2016 | |||||||
(in millions) | ||||||||
Information for pension plans with an accumulated benefit obligation in excess of plan assets: | ||||||||
Projected benefit obligation | $ | 3,052 | $ | 2,926 | ||||
Accumulated benefit obligation | $ | 3,052 | $ | 2,926 | ||||
Fair value of plan assets | $ | 2,385 | $ | 2,208 |
Components of net periodic benefit cost were as follows (in millions):
Pension Benefits | Other Postretirement Benefits | ||||||||||||||||||||||
Year Ended December 31, 2017 | Year Ended December 31, 2016 | Nine Months Ended December 31, 2015 | Year Ended December 31, 2017 | Year Ended December 31, 2016 | Nine Months Ended December 31, 2015 | ||||||||||||||||||
Components of net periodic benefit cost: | |||||||||||||||||||||||
Service cost | $ | 17 | $ | 18 | $ | 14 | $ | — | $ | — | $ | — | |||||||||||
Interest cost | 98 | 101 | 91 | 2 | 3 | 3 | |||||||||||||||||
Expected return on plan assets | (157 | ) | (162 | ) | (120 | ) | (3 | ) | (3 | ) | (3 | ) | |||||||||||
Amortization of unrecognized net loss | 131 | 126 | 113 | 2 | 1 | 2 | |||||||||||||||||
Amortization of unrecognized prior service benefit | (20 | ) | (21 | ) | (16 | ) | (7 | ) | (6 | ) | (5 | ) | |||||||||||
Net periodic benefit cost before special termination benefits cost/curtailment | 69 | 62 | 82 | (6 | ) | (5 | ) | (3 | ) | ||||||||||||||
Special termination benefits cost/curtailment | — | 2 | — | — | — | — | |||||||||||||||||
Net periodic benefit cost | $ | 69 | $ | 64 | $ | 82 | $ | (6 | ) | $ | (5 | ) | $ | (3 | ) |
The special termination benefits cost/curtailment cost in the table above represents a settlement expense to recognize the impact of lump sum benefit payments made in the non-qualified supplemental executive retirement plan.
At the end of the 2015 transition period, the Company changed the approach used to measure service and interest costs for pension and other postretirement benefits. For the 2015 transition period, the Company measured service and interest costs utilizing a single weighted-average discount rate derived from the yield curve used to measure the plan obligations. For 2016 and 2017, the Company elected to measure service and interest costs by applying the specific spot rates along that yield curve to the plans' liability cash flows. The Company believes this approach provides a more precise measurement of service and interest costs by aligning the timing of the plans' liability cash
77
flows to the corresponding spot rates on the yield curve. This change does not affect the measurement of our plan obligations. The Company accounted for this change as a change in accounting estimate and, accordingly, has accounted for it on a prospective basis.
Assumptions
Pension Benefits | Other Postretirement Benefits | ||||||||||||||||
Year Ended December 31, 2017 | Year Ended December 31, 2016 | Nine Months Ended December 31, 2015 | Year Ended December 31, 2017 | Year Ended December 31, 2016 | Nine Months Ended December 31, 2015 | ||||||||||||
Weighted-average assumptions used to determine benefit obligations at the end of each period | |||||||||||||||||
Discount rate | 3.65 | % | 4.14 | % | 4.40 | % | 3.36 | % | 3.62 | % | 3.98 | % | |||||
Rate of compensation increase: | |||||||||||||||||
Union | 2.90 | % | 3.11 | % | 3.13 | % | |||||||||||
Salaried | 3.51 | % | 3.56 | % | 3.62 | % |
Pension Benefits | Other Postretirement Benefits | ||||||||||||||||
Year Ended December 31, 2017 | Year Ended December 31, 2016 | Nine Months Ended December 31, 2015 | Year Ended December 31, 2017 | Year Ended December 31, 2016 | Nine Months Ended December 31, 2015 | ||||||||||||
Weighted-average assumptions used to determine net periodic benefit cost for each period | |||||||||||||||||
Discount rate | 4.14 | % | 4.40 | % | 3.90 | % | 3.63 | % | 3.98 | % | 3.55 | % | |||||
Expected long-term rate of return on plan assets | 7.00 | % | 7.25 | % | 7.25 | % | 4.00% / 6.00% | 4.00% / 6.00% | 5.00% / 6.25% | ||||||||
Rate of compensation increase: | |||||||||||||||||
Union | 3.11 | % | 3.13 | % | 3.66 | % | |||||||||||
Salaried | 3.56 | % | 3.60 | % | 3.14 | % |
In developing the expected long-term rate of return assumption, the Company considers input from its actuaries and other advisors, annualized returns of various major indices over a long-term time horizon and the Company's own historical 5-year and 10-year compounded investment returns. The expected long-term rate of return of 7.00% used in the year ended December 31, 2017 for the plans was based on an asset allocation range of 20 - 45% in public equity investments, 35 - 50% in fixed income investments, 0 - 10% in real estate investments, 15 - 30% collectively in hedge fund and private investments and 0 - 6% in cash investments. The actual return in any fiscal year will likely differ from the Company's assumption, but the Company's estimate of its return is based on long-term projections and historical results. Therefore, any variance in a given year does not necessarily indicate that the assumption should be changed.
In developing the expected long-term rate of return assumption for other PRB plans, the Company considers input from actuaries, historical returns and annualized returns of various major indices over long periods. The expected long-term rates of returns are based on the weighted average asset allocation between the assets held within the 401(h) and those held in fixed income investments.
The Company amended its retiree health care plan to provide coverage through a private exchange effective January 1, 2017. The Company will contribute fixed payments to an HRA for those retirees who previously had subsidized health care coverage through the Company. As such, health care cost trend rates have no effect on the amounts reported for health care plans. A one percentage point increase or decrease in the assumed health care cost trend rates would have no effect.
78
Plan Assets
Pension. Pension plan weighted-average asset allocations:
Anticipated 2018 | Actual | |||||||||||
Low | High | December 31, 2017 | December 31, 2016 | |||||||||
Asset category: | ||||||||||||
Domestic equity | 10.0 | % | 20.0 | % | 15.7 | % | 12.5 | % | ||||
International equity | 10.0 | % | 20.0 | % | 14.6 | % | 18.4 | % | ||||
Fixed income | 35.0 | % | 50.0 | % | 34.2 | % | 38.2 | % | ||||
Real estate | 2.0 | % | 6.0 | % | 3.6 | % | 3.5 | % | ||||
Hedge funds/private equity | 15.0 | % | 30.0 | % | 24.6 | % | 21.1 | % | ||||
Other investments/cash | 2.0 | % | 8.0 | % | 7.3 | % | 6.3 | % |
The Company has a committee which, assisted by outside consultants, evaluates the objectives and investment policies concerning its long-term investment goals and asset allocation strategies. Plan assets are invested in various asset classes that are expected to produce a sufficient level of diversification and investment return over the long term. The investment goals are (1) to meet or exceed the assumed actuarial rate of return over the long term within reasonable and prudent levels of risk, and (2) to preserve the real purchasing power of assets to meet future obligations. The nature and duration of benefit obligations, along with assumptions concerning asset class returns and return correlations, are considered when determining an appropriate asset allocation to achieve the investment objectives. Pension plan assets for the Company's qualified pension plans are held in a trust for the benefit of the plan participants and are invested in a diversified portfolio of equity investments, fixed income investments, real asset investments, hedge funds, private equity and cash. Risk targets are established and monitored against acceptable ranges. All investment policies and procedures are designed to ensure that the plans' investments are in compliance with the Employee Retirement Income Security Act. Guidelines are established defining permitted investments within each asset class.
During the 2015 transition period, the Company implemented an investment strategy derived from the asset-liability study conducted during fiscal 2013. The results of the asset-liability study reinforced the emphasis on managing the volatility of pension assets relative to pension liabilities while still achieving a competitive investment return, achieving diversification between and within various asset classes and managing other risks. In order to manage the volatility between the value of pension assets and liabilities, the Company has maintained an allocation to long-duration fixed income investments. The Company regularly reviews its actual asset allocation and periodically rebalances its investments to the targeted allocation when considered appropriate. Target allocation ranges are guidelines, not limitations, and occasionally due to market conditions and other factors actual asset allocation may vary above or below a target.
The implementation of the investment strategy discussed above is executed through a variety of investment structures such as: direct share or bond ownership, common/collective trusts or registered investment companies. Valuation methodologies differ for each of these structures. The valuation methodologies used for these investment structures are as follows:
U.S. Government Securities, Corporate Debt, Common Stock and Registered Investment Companies: Investments are valued at the closing price reported on the active market on which the individual securities are traded.
Common/Collective Trusts: Investments in a collective investment vehicle are valued by multiplying the investee company's net asset value per share with the number of units or shares owned at the valuation date as determined by the investee company. Net asset value per share is determined by the investee company's custodian or fund administrator by deducting from the value of the assets of the investee company all of its liabilities and the resulting number is divided by the outstanding number of shares or units. Investments held by the common/collective trusts ("CCT"), including collateral invested for securities on loan, are valued on the basis of valuations furnished by a pricing service approved by the CCT's investment manager, which determines valuations using methods based on market transactions for comparable securities and various relationships between securities which are generally recognized by institutional traders, or at fair value as determined in good faith by the CCT's investment manager.
79
Partnership/Joint Venture Interests: Given the inherent illiquidity of many partnership/joint venture investments, these investments are generally valued based on unobservable inputs that reflect the reporting entity's own assumptions about the assumptions that market participants would use pricing the asset. While the valuation methodologies may differ among each entity, the method for valuing these assets is primarily net asset values; other methods may include, but are not limited to, discounted cash flow analysis and comparable trading data for similar investments. The General Partner or Account Manager for these investments aggregates the values of underlying account securities and assets, then determines a final net asset value at the overall fund or account level and apportions that among the various investors by percentage of partnership or account ownership percentages.
Funds in Insurance Company Accounts: These investments are valued at fair value by discounting the related cash flows based on current yields of similar instruments with comparable durations considering the credit-worthiness of the issuer.
The methods described above may produce a fair value calculation that may not be indicative of net realizable value or reflective of future fair values. Furthermore, while the Company believes its valuation methods are appropriate and consistent with other market participants, the use of different methodologies or assumptions to determine the fair value of certain financial instruments could result in a different fair value measurement at the reporting date.
Fair Value: Pension plan investments using the fair value hierarchy consisted of the following:
December 31, 2017 | Quoted Prices in Active Markets for Identical Assets (Level 1) | Significant Other Observable Inputs (Level 2) | Significant Unobservable Inputs (Level 3) | Total | ||||||||||||
(in millions) | ||||||||||||||||
Interest-bearing cash | $ | — | $ | 2 | $ | — | $ | 2 | ||||||||
U.S. Government securities | 4 | — | — | 4 | ||||||||||||
Corporate debt | — | 147 | — | 147 | ||||||||||||
Common stock | 83 | — | — | 83 | ||||||||||||
Registered investment companies | 28 | — | — | 28 | ||||||||||||
Value of funds in insurance company accounts | — | 40 | — | 40 | ||||||||||||
Total assets in the fair value hierarchy | $ | 115 | $ | 189 | $ | — | $ | 304 | ||||||||
Investments measured at NAV | 2,081 | |||||||||||||||
Total investments | $ | 2,385 |
Pension plan investments using the fair value hierarchy consisted of the following:
December 31, 2016 | Quoted Prices in Active Markets for Identical Assets (Level 1) | Significant Other Observable Inputs (Level 2) | Significant Unobservable Inputs (Level 3) | Total | ||||||||||||
(in millions) | ||||||||||||||||
Interest-bearing cash | $ | — | $ | 2 | $ | — | $ | 2 | ||||||||
U.S. Government securities | 3 | — | — | 3 | ||||||||||||
Corporate debt | — | 138 | — | 138 | ||||||||||||
Common stock | 62 | 1 | — | 63 | ||||||||||||
Registered investment companies | 56 | — | — | 56 | ||||||||||||
Value of funds in insurance company accounts | — | 39 | 1 | 40 | ||||||||||||
Total assets in the fair value hierarchy | $ | 121 | $ | 180 | $ | 1 | $ | 302 | ||||||||
Investments measured at NAV | 1,906 | |||||||||||||||
Total investments | $ | 2,208 |
80
There were no material changes in Level 3 assets during the year ended December 31, 2017 or the year ended December 31, 2016.
There was no direct ownership of the Company's common stock included in plan assets at any of the periods presented.
Other Postretirement Benefits. The Company's other PRB obligations were 91.0% and 88.4% pre-funded at December 31, 2017 and December 31, 2016, respectively.
Portions of the assets are held in a 401(h) account held within the pension master trust and are invested in the same manner as the pension assets. Approximately 52% and 47% of the assets were held in the 401(h) account at December 31, 2017 and December 31, 2016, respectively. The remaining assets are in fixed income investments. The Company's investment objective for the other PRB plan assets is the preservation and safety of capital.
Contributions
During the year ended December 31, 2017, the Company contributed $115 million directly to the Orbital ATK pension plans. The Company distributed $3 million directly to retirees under its supplemental (nonqualified) executive retirement plan and $3 million to its other PRB plans during the year ended December 31, 2017. The Company is not required to make any contributions to the Orbital ATK pension plans to meet its legally required minimum for 2018. The Company also expects to distribute approximately $4 million directly to retirees under its supplemental executive retirement plans and to distribute approximately $4 million to its other postretirement benefit plans in 2018.
Expected Future Benefit Payments
The following benefit payments, which reflect expected future service, are expected to be paid in the years ending December 31. The pension benefits will be paid primarily out of the pension trust.
Pension Benefits | Other Postretirement Benefits | |||||||
(in millions) | ||||||||
2018 | $ | 225 | $ | 8 | ||||
2019 | 197 | 7 | ||||||
2020 | 200 | 7 | ||||||
2021 | 203 | 7 | ||||||
2022 | 203 | 6 | ||||||
2023 through 2027 | 994 | 24 |
Termination
In the event the Company terminates any of the plans under conditions in which the plan's assets exceed that plan's obligations, U.S. Government regulations require that a fair allocation of any of the plan's assets based on plan contributions that were reimbursed under U.S. Government contracts will be returned to the U.S. Government.
Defined Contribution Plan
Through December 31, 2015, the Company also sponsored two defined contribution plans - the Alliant Techsystems Inc. 401(k) Plan and the Deferred Salary and Profit Sharing Plan for Employees of Orbital Sciences Corporation (the "Orbital Sciences 401(k) Plan"). Participation in these plans was available to substantially all U.S. employees. Effective January 1, 2016, the Orbital Sciences 401(k) Plan merged into the Alliant Techsystems Inc. 401(k) Plan, and the combined plan's name was changed to the Orbital ATK, Inc. 401(k) Plan.
The Orbital ATK, Inc. 401(k) Plan is a 401(k) plan, with an employee stock ownership ("ESOP") feature. Employees may contribute up to 50% of their pay (highly compensated employees are subject to limitations). Employee contributions are invested, at the employees' direction, among a variety of investment alternatives including a Company common stock fund. Participants may transfer amounts into and out of the investment alternatives at any time, except for the Company common stock fund. Effective January 1, 2013, employees no longer had the option to invest in the Company common stock fund, other than for the reinvestment of dividends paid on the Company
81
common stock in participants' accounts. Balances in the fund prior to January 1, 2013 remain in the fund unless distributed or transferred. Any dividends declared on the Company common stock can be either reinvested within the Company common stock fund or provided as a cash payment.
The Company matching contributions and non-elective contribution to this plan are summarized below:
• | a matching contribution of 100% of the first 3% of the participant's contributed pay plus 50% of the next 3% of the participant's contributed pay for most employees (subject to one-year vesting), or |
• | a matching contribution of 100% of the first 6% of the participant's contributed pay for Technical Services Division employees (subject to one-year vesting), or |
• | a non-elective contribution based on the recognized compensation, age and service for most employees who are not earning a pension benefit (subject to three-year vesting). |
The Company's contributions to the 401(K) plan were $73 million in the year ended December 31, 2017, $56 million in the year ended December 31, 2016 and $41 million in the 2015 transition period. The Company also made a contribution to the 401(k) plan of $4 million in fiscal 2016 for a prior Orbital Sciences 401(k) Plan annual discretionary profit sharing contribution based on the participant's compensation earned prior to the merger.
14. Income Taxes
On December 22, 2017, the Tax Act was signed into law. The Tax Act changes existing United States tax law and includes numerous provisions that will impact the Company, including reducing the corporate tax rate to 21% from 35% for years beginning after December 31, 2017. The Tax Act also introduces prospective changes beginning in 2018, including repeal of the domestic manufacturing deduction, acceleration of tax revenue recognition and additional limitations on executive compensation. The Company is continuing to evaluate the impact of the Tax Act on our business and results of operations.
In accordance with Staff Accounting Bulletin No. 118 ("SAB 118"), which provides SEC staff guidance for the application of ASC Topic 740, Income Taxes, in the reporting period in which the Tax Act was signed into law, the Company recognized the income tax effects of the Tax Act in its 2017 financial statements. The income tax effects of the Tax Act that have been accounted for in 2017 are based on reasonable estimates. If the Company was able to make reasonable estimates for the effects of the Tax Act for which the Company's analysis was not complete, the Company recorded provisional adjustments in accordance with SAB 118.
The Company believes the reduction of the U.S. corporate income tax rate as a result of the Tax Act will have the most significant impact on the Company’s federal income taxes. The Company measures deferred tax assets and liabilities using enacted tax rates that will apply in the years in which the temporary differences are expected to be recovered or paid. The company recognized income tax expense of $39 million for the year ended December 31, 2017 and a corresponding $39 million decrease in net deferred tax assets as of December 31, 2017 related to the remeasurement of deferred tax assets and liabilities to reflect the reduction in the U.S. corporate income tax rate from 35% to 21%, both which are complete under SAB 118.
The Company’s accounting for the following effects of the Tax Act are not complete: (1) cost recovery, (2) limitation on the deductibility of certain executive compensation, (3) recovery of Alternative Minimum Tax credits and (4) valuation allowances against state tax attribute carryforwards. The Company was able to make reasonable estimates of certain effects and, therefore recorded provisional adjustments for such effects, none of which were material. The Company expects to finalize all provisional and non-estimable amounts within the measurement period as described in SAB 118.
82
Income Tax Expense
Substantially all of the Company’s income from continuing operations before income taxes for the three years ended December 31, 2017 was earned in the United States. The provision for income taxes related to continuing operations for each of the three years ended December 31, 2017 included the following:
Year Ended December 31, 2017 | Year Ended December 31, 2016 | Nine Months Ended December 31, 2015 | ||||||||||
(in millions) | ||||||||||||
Current: | ||||||||||||
Federal | $ | 75 | $ | 63 | $ | 28 | ||||||
State | 9 | 2 | 2 | |||||||||
Non-US | — | 4 | — | |||||||||
Deferred: | ||||||||||||
Federal | 72 | 39 | 55 | |||||||||
State | (4 | ) | 3 | 2 | ||||||||
Income taxes | $ | 152 | $ | 111 | $ | 87 |
Differences between the federal statutory rate and the Company's effective rate related to the following:
Year Ended December 31, 2017 | Year Ended December 31, 2016 | Nine Months Ended December 31, 2015 | |||||||
Statutory federal income tax rate | 35.0 | % | 35.0 | % | 35.0 | % | |||
State income taxes, net of federal impact | 3.3 | 2.8 | 2.1 | ||||||
Domestic manufacturing deduction | (1.9 | ) | (2.3 | ) | (1.5 | ) | |||
True-up of prior year taxes | (3.2 | ) | (2.6 | ) | 0.1 | ||||
Research and development tax credit | (9.3 | ) | (12.6 | ) | (5.2 | ) | |||
Change in prior year contingent tax liabilities | (1.3 | ) | 0.1 | 1.0 | |||||
Impacts related to the 2017 Tax Act | 8.4 | — | — | ||||||
Other, net | (0.1 | ) | 0.1 | (1.2 | ) | ||||
Change in valuation allowance | 2.1 | 7.0 | 1.6 | ||||||
Income tax provision | 33.0 | % | 27.5 | % | 31.9 | % |
Deferred Income Taxes
Deferred income taxes arise because of temporary differences in the timing of the recognition of income and expense items for financial statement reporting and income tax purposes. The net effect of these temporary differences are classified in the consolidated financial statements of financial position as noncurrent assets or liabilities.
83
Deferred income tax assets and liabilities resulting from temporary differences related to the following:
December 31, | ||||||||
2017 | 2016 | |||||||
(in millions) | ||||||||
Deferred income tax assets: | ||||||||
Retirement benefits | $ | 169 | $ | 271 | ||||
Federal carryforwards | 31 | 13 | ||||||
State carryforwards | 73 | 50 | ||||||
Other | 8 | 19 | ||||||
Other reserves | 10 | 21 | ||||||
Accruals for employee benefits | 25 | 40 | ||||||
Inventory | 13 | 25 | ||||||
Contract method of revenue recognition | 42 | 80 | ||||||
Total deferred income tax assets before valuation allowance | 371 | 519 | ||||||
Valuation allowance | (62 | ) | (42 | ) | ||||
Total deferred income tax assets | 309 | 477 | ||||||
Deferred income tax liabilities: | ||||||||
Intangible assets | (47 | ) | (86 | ) | ||||
Property, plant and equipment | (104 | ) | (127 | ) | ||||
Debt-related | (3 | ) | (10 | ) | ||||
Total deferred income tax liabilities | (154 | ) | (223 | ) | ||||
Net deferred income tax assets | $ | 155 | $ | 254 |
The Company believes it is more likely than not that the recorded deferred benefits will be realized through the reduction of future taxable income. The Company's recorded valuation allowance of $62 million at December 31, 2017 relates to certain capital loss, tax credits and net operating losses that are not expected to be realized before their expiration.
Included in the net deferred tax asset are net operating loss and credit carryovers of $35 million, net of valuation allowances, which expire in years ending from December 31, 2018 through December 31, 2038, and a $9 million federal AMT tax credit that will be utilized or fully refunded prior to 2022.
The following summarizes activity related to valuation allowances for deferred tax assets:
Year Ended December 31, 2017 | Year Ended December 31, 2016 | Nine Months Ended December 31, 2015 | |||||||||
(in millions) | |||||||||||
Beginning Balance | $ | 42 | $ | 13 | $ | 9 | |||||
Additions, charged to expense | 21 | 37 | 5 | ||||||||
Deductions | (1 | ) | (8 | ) | (1 | ) | |||||
Ending Balance | $ | 62 | $ | 42 | $ | 13 |
The Company has significant deferred tax assets in the U.S. against which valuation allowances have been established to reduce such deferred tax assets to an amount that is more likely than not to be realized. The establishment of valuation allowances requires significant judgment and is impacted by various estimates. Both positive and negative evidence, as well as the objectivity and verifiability of that evidence, is considered in determining the appropriateness of recording a valuation allowance on deferred tax assets. While the Company believes positive evidence exists with regard to the realizability of these deferred tax assets, it is not considered sufficient to outweigh the objectively verifiable negative evidence.
84
Unrecognized Tax Benefits
Unrecognized tax benefits consist of the carrying value of the Company's recorded uncertain tax positions as well as the potential tax benefits that could result from other tax positions that have not been recognized in the financial statements under current authoritative guidance. At December 31, 2017 and December 31, 2016, unrecognized tax benefits that have not been recognized in the financial statements amounted to $137 million and $121 million, respectively, of which $125 million and $106 million, respectively, would affect the effective tax rate, if recognized. The remaining balance is related to deferred tax items which only impact the timing of tax payments. Although the timing and outcome of audit settlements are uncertain, it is reasonably possible that a $30 million reduction of the uncertain tax benefits will occur in the next 12 months. The settlement of these unrecognized tax benefits could result in earnings from $0 million to $27 million.
Changes in unrecognized tax benefits, excluding interest and penalties, were as follows:
Year Ended December 31, 2017 | Year Ended December 31, 2016 | Nine Months Ended December 31, 2015 | ||||||||||
(in millions) | ||||||||||||
Unrecognized tax benefits, beginning of period | $ | 119 | $ | 81 | $ | 34 | ||||||
Gross increases—tax positions in prior periods | 6 | 30 | 42 | |||||||||
Gross decreases—tax positions in prior periods | (2 | ) | (4 | ) | (1 | ) | ||||||
Gross increases—current-period tax positions | 21 | 18 | 6 | |||||||||
Settlements | — | (5 | ) | — | ||||||||
Lapse of statute of limitations | (10 | ) | (1 | ) | — | |||||||
Unrecognized tax benefits, end of period | $ | 134 | $ | 119 | $ | 81 |
The Company reports income tax-related interest income within income taxes. Penalties and tax-related interest expense are also reported as a component of income taxes. At December 31, 2017 and December 31, 2016, $3 million and $2 million of income tax-related interest and an immaterial amount of penalties were included in accrued income taxes, respectively.
The Company or one of its subsidiaries files income tax returns in the U.S. federal, various U.S. state and foreign jurisdictions. With few exceptions, the Company is no longer subject to U.S. federal, state and local, or foreign income tax examinations by tax authorities for years prior to 2011. The IRS has completed the audits of the Company through fiscal 2014 and is currently auditing the Company's income tax returns for fiscal year 2015 and calendar year 2015. The Company believes appropriate provisions for all outstanding issues have been made for all remaining open years in all jurisdictions.
15. Commitments
The Company leases land, buildings and equipment under various operating leases, which generally have renewal options of one to five years. Rent expense was $95 million in the year ended December 31, 2017, $88 million in the year ended December 31, 2016, and $69 million in the 2015 transition period.
Scheduled operating lease payments are as follows:
(in millions) | |||
2018 | $ | 85 | |
2019 | 81 | ||
2020 | 67 | ||
2021 | 59 | ||
2022 | 48 | ||
Thereafter | 60 | ||
Total | $ | 400 |
85
As part of the Company's restructuring activities in connection with the Orbital-ATK Merger, certain leased spaces were vacated by the Company. The Company has subleased most of this space and sublease income was not material for the year ended December 31, 2017.
The Company currently leases land from a private party for its facility in Magna, Utah. This facility is used in the production and testing of some of the Company's rocket motors. The current lease extends through September 2022. The lease requires the Company to surrender the property back to its owner in its original condition. While the Company currently anticipates operating this facility indefinitely, the Company could incur significant costs if the Company were to terminate this lease.
The Company has known conditional asset retirement obligations, such as contractual lease restoration obligations, to be performed in the future, that are not reasonably estimable due to insufficient information about the timing and method of settlement of the obligation. Accordingly, these obligations have not been recorded in the consolidated financial statements. A liability for these obligations will be recorded in the period when sufficient information regarding timing and method of settlement becomes available to make a reasonable estimate of the liability's fair value.
16. Contingencies
Litigation
From time to time, the Company is subject to various legal proceedings, including lawsuits, which arise out of, and are incidental to, the conduct of the Company's business. The Company does not consider any of such proceedings that are currently pending, individually or in the aggregate to be material to its business or likely to result in a material adverse effect on its operating results, financial condition or cash flows, notwithstanding that the unfavorable resolution of any matter may have a material effect on net earnings in any particular quarter.
On April 29, 2016, US Space LLC filed a complaint against the Company and its subsidiary, ATK Space Systems Inc. in New York Supreme Court, alleging breach of contract and various other claims, and seeking unspecified damages, all related to ViviSat LLC, a former joint venture between the parties. The Company believes US Space’s claims are without merit. On May 27, 2016, the Company filed a countersuit in Loudoun County Circuit Court in the Commonwealth of Virginia (ATK Space Systems, Inc. and Orbital ATK, Inc. v. U.S. Space LLC, Case No. CL-101847) asserting claims for declaratory and injunctive relief against US Space LLC relating to ViviSat. The Company’s Virginia complaint alleged a failure of US Space to perform contractual obligations relating to obtaining financing for ViviSat, triggering certain rights of the Company that led to the dissolution of the venture. On November 11, 2016, the New York Supreme Court dismissed US Space’s New York case in its entirety. On January 6, 2017, US Space filed counterclaims against the Company, similar to its previous claims in its now-dismissed New York lawsuit. US Space’s initial counterclaims in the Virginia case sought damages of at least $125 million, but increased its damages demand to $385 million in the fourth quarter of 2017. A jury trial is currently ongoing. While the Company continues to believe that US Space’s counterclaims are without merit, the amount of the damages sought, if ever awarded, could be material to our cash flows and results of operations.
Securities Class Action
Seven purported class actions challenging the Merger were filed in the United States District Court for the Eastern District of Virginia, captioned Lickteig v. Orbital ATK, Inc., et al., filed October 11, 2017 (the "Lickteig Action"), Ayzin v. Orbital ATK, Inc., et al., filed October 13, 2017 (the "Ayzin Action"), Sedon v. Orbital ATK, Inc., et al., filed October 16, 2017 (the "Sedon Action"), Berg v. Orbital ATK, Inc., et al., filed October 16, 2017 (the "Berg Action"), Simnowitz v. Orbital ATK, Inc., et al., filed October 18, 2017 (the "Simnowitz Action"), Cramer v. Orbital ATK, Inc., et al., filed October 25, 2017 (the "Cramer Action"), and Donato v. Orbital ATK, Inc., et al., filed on November 7, 2017 (the "Donato Action" and collectively with the Lickteig Action, Ayzin Action, Sedon Action, Berg Action, Simnowitz Action and Cramer Action, the "Actions"). The Actions alleged certain violations of the Securities and Exchange Act of 1934 (the "Exchange Act"), as amended, and sought, among other things, damages, attorneys' fees and injunctive relief to prevent the Merger from closing. While the Company believed that the Actions lacked merit and that the disclosures set forth in the proxy statement complied fully with applicable law, in order to moot plaintiffs' unmeritorious disclosure claims, avoid nuisance and possible expense and provide additional information to our stockholders, the Company determined to voluntarily supplement the proxy statement, as set forth in the Company's Schedule 14A filed with the SEC on November 20, 2017. On November 20, 2017, the Ayzin Action, Sedon Action, Berg Action, Cramer Action and Donato Action were each voluntarily dismissed with prejudice as to the plaintiffs. On
86
December 8, 2017, the Simnowitz Action was voluntarily dismissed with prejudice as to the plaintiff and on January 12, 2018, the Lickteig Action was voluntarily dismissed with prejudice as to the plaintiff. While each of the Actions have been voluntarily dismissed with prejudice as to the plaintiffs, additional plaintiffs may file lawsuits against the Company and/or its directors and officers in connection with the Merger.
On August 12, 2016, a putative class action complaint, naming the Company, our Chief Executive Officer and our Chief Financial Officer as defendants, was filed in the United States District Court for the Eastern District of Virginia (Steven Knurr, et al. v. Orbital ATK, Inc., No. 16-cv-01031 (TSE-MSN)). The class action complaint asserts claims on behalf of purchasers of Orbital ATK securities for violations of Sections 10(b) and 20(a) of the Exchange Act and Rule 10b-5 thereunder, arising out of allegedly false and misleading statements and the failure to disclose that: (i) the Company lacked effective control over financial reporting; and (ii) as a result, the Company failed to record an anticipated loss on its long-term contract with the U.S. Army to manufacture and supply small caliber ammunition at the U.S. Army's Lake City Army Ammunition Plant. On April 24, 2017 and October 10, 2017, the plaintiffs filed amended complaints naming additional defendants and asserting claims for violations of additional sections of the Exchange Act and alleged false and misleading statements in the Company's Form S-4 filed with the SEC relating to the Orbital-ATK Merger. The complaint seeks an award of damages, an award of reasonable costs and expenses at trial, including counsel and expert fees, and an award of such other relief as deemed appropriate by the Court.
SEC Investigation
The SEC is conducting a non-public investigation relating to our historical accounting practices as a result of the prior restatement of the Company's unaudited condensed consolidated financial statements for the quarterly periods ended July 5, 2015 and October 4, 2015 as described in the Company's Amendment to the Transition Report on Form 10-K for the nine-month transition period ending December 31, 2015 filed with the SEC on March 15, 2016. The Company has also voluntarily self-reported to the SEC regarding matters pertaining to the Restatement described in the Company's Amendment to the Transition Report on Form 10-K for the nine-month transition period ending December 31, 2015 filed on February 24, 2017. The Company is cooperating fully with the SEC in connection with these matters.
U.S. Government Investigations
The Company is also subject to U.S. Government investigations from which civil, criminal or administrative proceedings could result. Such proceedings could involve claims by the U.S. Government for fines, penalties, compensatory and treble damages, restitution and/or forfeitures. Under government regulations, a company, or one or more of its operating divisions or subdivisions, can also be suspended or debarred from government contracts, or lose its export privileges, based on the results of investigations. The Company believes, based upon all available information, that the outcome of any such pending government investigations will not have a material adverse effect on its operating results, financial condition or cash flows.
Claim Recovery
Profits expected to be realized on contracts are based on management's estimates of total contract sales value and costs at completion. Estimated amounts for contract changes and claims are included in contract sales only when realization is estimated to be probable. Unbilled receivables included $17 million and $18 million as of December 31, 2017 and December 31, 2016, respectively, for contract claims based on progress to date on certain contracts.
Environmental Liabilities
The Company's operations and ownership or use of real property are subject to a number of federal, state and local environmental laws and regulations, as well as applicable foreign laws and regulations, including those for discharge of hazardous materials, remediation of contaminated sites and restoration of damage to the environment. At certain sites that the Company owns or operates or formerly owned or operated, there is known or potential contamination that the Company is required to investigate or remediate. The Company could incur substantial costs, including remediation costs, resource restoration costs, fines and penalties, or third party property damage or personal injury claims, as a result of liabilities associated with past practices or violations of environmental laws or non-compliance with environmental permits.
87
The Company has been identified as a potentially responsible party ("PRP"), along with other parties, in several regulatory agency actions associated with hazardous waste sites. As a PRP, the Company may be required to pay a share of the costs of the investigation and clean-up of these sites. While uncertainties exist with respect to the amounts and timing of the ultimate environmental liabilities, based on currently available information, the Company has concluded that these matters, individually or in the aggregate, will not have a material adverse effect on operating results, financial condition or cash flows.
The Company could incur substantial costs, including cleanup costs, resource restoration, fines and penalties or third-party property damage or personal injury claims, as a result of violations or liabilities under environmental laws or non-compliance with environmental permits. While environmental laws and regulations have not had a material adverse effect on the Company's operating results, financial condition or cash flows in the past, and the Company has environmental management programs in place to mitigate these risks, it is difficult to predict whether they will have a material impact in the future.
The liability for environmental remediation represents management's best estimate of the probable and reasonably estimable costs related to known remediation obligations. The receivable represents the amount that the Company expects to recover, as discussed below.
The following is a summary of the amounts recorded for environmental remediation:
December 31, 2017 | December 31, 2016 | |||||||||||||||
Liability | Receivable | Liability | Receivable | |||||||||||||
(in millions) | ||||||||||||||||
Current | $ | 5 | $ | 3 | $ | 6 | $ | 3 | ||||||||
Noncurrent | 28 | 10 | 35 | 15 | ||||||||||||
Total | $ | 33 | $ | 13 | $ | 41 | $ | 18 |
At December 31, 2017, the estimated range of reasonably possible costs of environmental remediation was $33 million to $59 million.
The Company expects that a portion of its environmental compliance and remediation costs will be recoverable under U.S. Government contracts. Some of the remediation costs that are not recoverable from the U.S. Government that are associated with facilities purchased in a business acquisition may be covered by various indemnification agreements, as described below.
• | As part of its acquisition of the Hercules Aerospace Company in fiscal 1995, the Company generally assumed responsibility for environmental compliance at the facilities acquired from Hercules ("the Hercules Facilities"). The Company believes that a portion of the compliance and remediation costs associated with the Hercules Facilities will be recoverable under U.S. Government contracts. If the Company were unable to recover those environmental remediation costs under these contracts, the Company believes that these costs will be covered by Hercules Incorporated, a subsidiary of Ashland Inc., ("Hercules") under environmental agreements entered into in connection with the Hercules acquisition. Under these agreements, Hercules has agreed to indemnify the Company for environmental conditions relating to releases or hazardous waste activities occurring prior to the Company's purchase of the Hercules Facilities as long as they were identified in accordance with the terms of the agreement; fines relating to pre-acquisition environmental compliance; and environmental claims arising out of breaches of Hercules' representations and warranties. Hercules is not required to indemnify the Company for any individual claims below $50 thousand. Hercules is obligated to indemnify the Company for the lowest cost response of remediation required at the facility that is acceptable to the applicable regulatory agencies. The Company is not responsible for conducting any remedial activities with respect to the Clearwater, FL facility. In accordance with its agreement with Hercules, the Company notified Hercules of all known contamination on non-federal lands on or before March 31, 2000, and on federal lands on or before March 31, 2005. |
• | The Company generally assumed responsibility for environmental compliance at the Thiokol Facilities acquired from Alcoa Inc. ("Alcoa") in fiscal 2002. The Company expects that a portion of the compliance and remediation costs associated with the acquired Thiokol Facilities will be recoverable under U.S. |
88
Government contracts. In accordance with its agreement with Alcoa, the Company notified Alcoa of all known environmental remediation issues at January 30, 2004. Of these known issues, the Company is responsible for any costs not recovered through U.S. Government contracts at the Thiokol Facilities up to $14 million, the Company and Alcoa have agreed to split evenly any amounts between $14 million and $34 million, and the Company is responsible for any payments in excess of $34 million. At this time, the Company believes that costs not recovered through U.S. Government contracts will be immaterial.
The Company cannot ensure that the U.S. Government, Hercules, Alcoa, or other third parties will reimburse it for any particular environmental costs or reimburse the Company in a timely manner or that any claims for indemnification will not be disputed. U.S. Government reimbursements for cleanups are financed out of a particular agency's operating budget and the ability of a particular governmental agency to make timely reimbursements for cleanup costs will be subject to national budgetary constraints. The Company's failure to obtain full or timely reimbursement from the U.S. Government, Hercules, Alcoa, or other third parties could have a material adverse effect on its operating results, financial condition or cash flows. While the Company has environmental management programs in place to mitigate these risks, and environmental laws and regulations have not had a material adverse effect on the Company's operating results, financial condition or cash flows in the past, it is difficult to predict whether they will have a material impact in the future.
In December 2001, the Company received notice from the State of Utah of a potential claim against the Company under Section 107(f) of the Comprehensive Environmental Response, Compensation, and Liability Act ("CERCLA") for natural resource damages at Bacchus, one of the Hercules Facilities, in Magna, Utah. The notice letter, which was issued to preserve the State's rights under CERCLA, also expressly acknowledged the State's willingness to allow the Company to go forward with its currently-planned monitoring and remediation program. The State's preliminary estimate of damages contained in this claim was $139 million, which is based on known and alleged groundwater contamination at and near Bacchus and is related to Hercules' manufacturing operations at the site. The Company received similar notices related to the Promontory facility that was acquired from Alcoa in the acquisition of Thiokol and Kennecott’s Section 21 Well Field due to the presence of perchlorate. Although the Company has previously made accruals for its best estimate of the probable and reasonably estimable costs related to the remediation obligations known to the Company with respect to the affected areas, the Company cannot yet predict if or when a suit may be filed against it, nor can the Company determine any additional costs that may be incurred in connection with this matter.
Expected aggregate undiscounted environmental remediation payments, net of expected recoveries, are as follows:
(in millions) | |||
2018 | $ | 2 | |
2019 | 1 | ||
2020 | — | ||
2021 | 2 | ||
2022 | 2 | ||
Thereafter | 13 | ||
Total | $ | 20 |
There were no material insurance recoveries related to environmental remediation during any of the periods presented.
17. Stock-Based Compensation
The Company has authorized 5,000,000 shares of preferred stock, par value $1.00, none of which has been issued.
During the year ended December 31, 2017, the Company sponsored five stock-based incentive plans, including: the Orbital ATK, Inc. 2015 Stock Incentive Plan (the "2015 Stock Incentive Plan"); three legacy ATK plans (the Alliant Techsystems Inc. 2005 Stock Incentive Plan, the Non-Employee Director Restricted Stock Plan and the 1990 Equity Incentive Plan); and one legacy Orbital plan, under which the Company assumed the obligation to issue Company common stock pursuant to the terms of the transaction agreement ("the Transaction Agreement") relating to the Orbital-ATK Merger (the Orbital Sciences Corporation 2005 Amended and Restated Stock Incentive Plan). At December 31, 2017, the Company has authorized up to 3,750,000 common shares under the 2015 Stock Incentive
89
Plan, of which 2,084,273 common shares are available to be granted. No new grants will be made out of the other four plans.
During the year ended December 31, 2016, the Company adopted an Employee Stock Purchase Plan ("ESPP") whereby eligible employees may purchase shares of the Company's common stock at the lesser of 85% of the fair market value of a share of common stock at the beginning or at the end of the quarterly offering period. The ESPP is compensatory and the fair value of the shares purchased is determined using the Black-Scholes option pricing model. As of December 31, 2017, the Company had authorized up to 2,000,000 common shares, of which 1,781,318 shares of common shares were available for purchase under the ESPP. The Company recognized $2 million and $1 million of ESPP expense during the year ended December 31, 2017 and 2016, respectively. In connection with the Merger, the ESPP has been suspended as of October 1, 2017.
There are four types of awards outstanding under the Company's stock incentive plans: performance awards, total stockholder return performance awards ("TSR awards"), restricted stock and stock options. The Company issues treasury shares upon (i) the vesting of performance awards, TSR awards and restricted stock units, (ii) the grant of restricted stock, and (iii) the exercise of stock options.
The Company's nonvested stock-based compensation awards activity was as follows:
Performance Share and TSR Awards | Restricted Stock Units | Restricted Stock Awards | Combined Weighted Average Grant Date Fair Value | ||||||||||
Nonvested, March 31, 2015 | 160,530 | 500,939 | 212,635 | $ | 77.02 | ||||||||
Granted | 2,976 | — | 86,108 | 74.88 | |||||||||
Canceled/forfeited | (5,374 | ) | (10,908 | ) | (9,914 | ) | 80.88 | ||||||
Vested | (333 | ) | (191,084 | ) | (17,806 | ) | 43.87 | ||||||
Nonvested, December 31, 2015 | 157,799 | 298,947 | 271,023 | $ | 75.57 | ||||||||
Granted | 153,888 | — | 176,800 | 80.14 | |||||||||
Canceled/forfeited | (706 | ) | (2,933 | ) | (7,720 | ) | 78.73 | ||||||
Vested | — | (193,687 | ) | (128,854 | ) | 64.68 | |||||||
Nonvested, December 31, 2016 | 310,981 | 102,327 | 311,249 | $ | 82.31 | ||||||||
Granted | 118,786 | — | 161,207 | 99.55 | |||||||||
Canceled/forfeited | (12,137 | ) | (1,016 | ) | (9,356 | ) | 84.74 | ||||||
Vested | — | (101,311 | ) | (156,190 | ) | 92.80 | |||||||
Nonvested, December 31, 2017 | 417,630 | — | 306,910 | $ | 88.54 |
In the table above, the fair value of vested stock awards was $26 million, $28 million and $15 million for shares that vested during the year ended December 31, 2017, the year ended December 31, 2016 and the 2015 transition period, respectively.
Performance Awards. There were performance shares reserved for executive officers and key employees. Performance shares are valued at the fair value of the Company's stock as of the grant date and expense is recognized based on the number of shares expected to vest according to the terms of the awards under which they are granted. Of these performance shares outstanding:
• | up to 58,506 will become payable upon achievement of financial performance goals relating to absolute sales growth and return on investment of capital for the performance period beginning January 1, 2017 and ending December 31, 2019; and |
• | up to 71,074 will become payable upon achievement of financial performance goals relating to absolute sales growth and return on investment of capital for the performance period beginning January 1, 2016 and ending December 31, 2018; and |
• | up to 79,235 will become payable upon achievement of financial performance goals relating to absolute earnings per share growth and absolute sales growth for the performance period beginning April 1, 2015 and ending December 31, 2017. |
90
TSR Awards. There were 208,815 shares outstanding reserved for executive officers and key employees for the fiscal year 2017-2019, 2016-2018 and 2015-2017 performance periods. The Company used an integrated Monte Carlo simulation model to determine the fair value of the TSR awards. The Monte Carlo model calculates the probability of satisfying the market conditions stipulated in the award. This probability is an input into the trinomial lattice model used to determine the fair value of the awards as well as the assumptions of other variables, including the risk-free interest rate and expected volatility of the peer average and the Company's stock price in future periods. The risk-free rate is based on the zero-coupon U.S. Treasury bill with a remaining term that approximates the life assumed at the date of grant.
Weighted-average assumptions used in estimating the value of the TSR award were as follows:
Year Ended December 31, 2017 | Year Ended December 31, 2016 | Nine Months Ended December 31, 2015 | ||||||||||
Risk-free rate | 1.42 | % | 1.00 | % | 1.02 | % | ||||||
Expected volatility | 26.77 | % | 25.39 | % | 22.81 | % | ||||||
Expected dividend yield | 1.28 | % | 1.51 | % | 1.78 | % | ||||||
Expected award life | 2.8 years | 2.8 years | 2.8 years | |||||||||
Weighted average grant date fair value | $ | 115.26 | $ | 87.85 | $ | 94.93 |
Restricted Stock Units. Pursuant to the terms of the Transaction Agreement and under the terms of the ATK 2005 Stock Incentive Plan, all of the performance awards and TSR awards outstanding at February 9, 2015 were converted into time-vesting restricted stock units in connection with the Distribution, with vesting periods corresponding to the respective performance periods. During the year ended December 31, 2017, 53,449 shares of restricted stock units vested for the performance period ending March 31, 2017. Pursuant to the terms of the Transaction Agreement, the Company also assumed the obligation to issue Company common stock from the legacy Orbital plan. At December 31, 2017, there were no restricted stock units outstanding under the legacy Orbital plan as 47,862 shares of restricted stock units vested and 1,016 shares were forfeited during the year ended December 31, 2017.
Restricted Stock Awards. Restricted stock granted to non-employee directors and certain key employees vests over periods generally ranging from one to three years from the date of award and is valued at the fair value of the Company's common stock at the grant date.
Stock Options. Stock options may be granted periodically, with an exercise price equal to the fair market value of the Company's common stock on the date of grant, and generally vest from one to three years from the date of grant. Options are generally granted with seven-year or ten-year terms.
91
The Company's stock option activity was as follows:
Shares | Weighted Average Exercise Price | Weighted Average Remaining Contractual Life (in years) | Aggregate Intrinsic Value (per option) | ||||||||||
Outstanding, March 31, 2015 | 354,730 | $ | 41.83 | 7.8 | $ | 34.80 | |||||||
Granted | 1,443 | 73.13 | |||||||||||
Exercised | (122,893 | ) | 30.90 | ||||||||||
Outstanding, December 31, 2015 | 233,280 | $ | 47.79 | 7.7 | $ | 41.55 | |||||||
Granted | 72,328 | 79.43 | |||||||||||
Exercised | (33,629 | ) | 29.93 | ||||||||||
Outstanding, December 31, 2016 | 271,979 | $ | 58.41 | 7.6 | $ | 29.32 | |||||||
Granted | 58,434 | 93.51 | |||||||||||
Exercised | (84,544 | ) | 41.52 | ||||||||||
Outstanding, December 31, 2017 | 245,869 | $ | 72.56 | 7.6 | $ | 58.94 | |||||||
Options exercisable at: | |||||||||||||
December 31, 2017 | 114,364 | $ | 59.07 | 6.6 | $ | 72.43 | |||||||
Options expected to vest: | |||||||||||||
December 31, 2017 | 131,505 | $ | 84.30 | 8.4 | $ | 47.20 |
The weighted-average fair value of each option grant is estimated on the date of grant using the Black-Scholes option pricing model. The option pricing model requires the Company to make assumptions. The risk-free rate is based on U.S. Treasury securities with a remaining term that approximates the expected life assumed at the date of grant. Expected volatility is based on the historical volatility of peer companies' stock over the past six years. The expected option life was derived based on the "simplified" method under Staff Accounting Bulletins No. 107, "Share-Based Payment," as amended by Staff Accounting Bulletin No. 110 because of the Company's short history since the Orbital-ATK Merger and Distribution. The weighted-average fair value of options granted was $24.47, $20.53 and $20.80 during the year ended December 31, 2017, the year ended December 31, 2016 and the 2015 transition period, respectively.
Weighted-average assumptions used in estimating the value of the stock option grants were as follows:
Year Ended December 31, 2017 | Year Ended December 31, 2016 | Nine Months Ended December 31, 2015 | ||||
Risk-free rate | 1.96% | 1.62% | 1.99% | |||
Expected volatility | 28.19% | 26.89% | 27.91% | |||
Expected dividend yield | 1.35% | 1.36% | 1.17% | |||
Expected option life | 6 years | 7 years | 7 years |
The total intrinsic value of options exercised was $6 million, $2 million and $5 million during the year ended December 31, 2017, the year ended December 31, 2016, and the 2015 transition period, respectively. The tax benefit realized from stock options exercised was $1 million for the year ended December 31, 2017 and was immaterial for the year ended December 31, 2016 and the 2015 transition period. Total cash received from options exercised during the year ended December 31, 2017, the year ended December 31, 2016 and the 2015 transition period was $4 million, $1 million, and $4 million, respectively.
92
Total pre-tax stock-based compensation expense of $21 million, $20 million and $19 million was recognized during the year ended December 31, 2017, the year ended December 31, 2016 and the 2015 transition period, respectively. The total income tax benefit recognized in the statement of operations for share-based compensation was $8 million, $7 million and $8 million during the year ended December 31, 2017, the year ended December 31, 2016 and the 2015 transition period, respectively.
At December 31, 2017, the total unrecognized compensation cost related to nonvested stock-based compensation awards was $25 million and is expected to be realized over a weighted average period of 1.7 years.
Share Repurchases
Shares of the Company's common stock may be purchased in the open market, subject to compliance with applicable laws and regulations and the Company's debt covenants, depending upon market conditions and other factors. During 2016, the Board of Directors authorized an increase to the amount for repurchase of the Company's common stock to the lesser of $300 million or 4 million shares and extended the repurchase period through March 31, 2017. In February 2017, the Board of Directors further increased the amount authorized for repurchase to $450 million, removed the share quantity limitation, and extended the repurchase period through March 31, 2018. In connection with the Merger, the Company halted its share repurchase program.
The Company repurchased 230,918 shares for $23 million during the year ended December 31, 2017, 1,570,333 shares for $124 million in the year ended December 31, 2016, and 1,008,445 shares for $76 million in the 2015 transition period.
18. Operating Segment Information
The Company operates its business structure within three operating segments. These operating segments ("Groups") are defined based on the reporting and review process used by the Company's chief executive officer and other management. The operating structure aligns the Company's capabilities and resources with its customers and markets and positions the Company for long-term growth and improved profitability. At December 31, 2017, the Company's three operating groups were:
• | Flight Systems Group develops launch vehicles that are used as small- and medium-class space launch vehicles to place satellites into earth orbit and escape trajectories, interceptor and target vehicles for missile defense systems and suborbital launch vehicles that place payloads into a variety of high-altitude trajectories. The Group also develops and produces medium- and large-class rocket propulsion systems for human and cargo launch vehicles, strategic missiles, missile defense interceptors and target vehicles. Additionally, Flight Systems Group operates in the military and commercial aircraft and launch structures markets. |
• | Defense Systems Group develops and produces military small-, medium- and large-caliber ammunition, propulsion systems for tactical missiles and missile defense applications, strike weapons, precision weapons and munitions, high-performance gun systems, aircraft survivability systems, fuzes and warheads, energetic materials and special mission aircraft. |
• | Space Systems Group develops and produces small- and medium-class satellites that are used to enable global and regional communications and broadcasting, conduct space-related scientific research, and perform activities related to national security. In addition, Space Systems Group develops and produces human-rated space systems for earth orbit and deep space exploration, including cargo delivery to the International Space Station. This group is also a provider of spacecraft components and subsystems as well as specialized engineering and operations services to U.S. Government agencies. |
93
The Company derives the majority of its sales from contracts with, and prime contractors to, the U.S. Government. Sales to the U.S. Government and U.S. Government prime contractors were as follows:
U.S. Government Sales | Percentage of sales | ||||||
(in millions) | |||||||
Year ended December 31, 2017 | $ | 3,489 | 73 | % | |||
Year ended December 31, 2016 | $ | 3,368 | 76 | % | |||
Nine months ended December 31, 2015 | $ | 2,359 | 70 | % |
The CRS contracts with NASA, which are reported within Flight Systems Group and Space Systems Group, comprised 9%, 13% and 10% of total sales in the year ended December 31, 2017, the year ended December 31, 2016 and the 2015 transition period, respectively.
The Company's small-caliber ammunition contract with the U.S. Army, which is reported within Defense Systems Group, comprised 5%, 6% and 6% of total sales in the year ended December 31, 2017, the year ended December 31, 2016 and the 2015 transition period, respectively.
No single commercial customer accounted for more than 10% of the Company's sales in the year ended December 31, 2017, the year ended December 31, 2016 or the 2015 transition period, respectively.
The Company's international sales were $878 million in the year ended December 31, 2017, $778 million in the year ended December 31, 2016, and $766 million in the 2015 transition period. Sales to no individual country outside the United States accounted for more than 5%, 4% or 4% of the Company's sales in the year ended December 31, 2017, the year ended December 31, 2016 and the 2015 transition period, respectively. Substantially all of the Company's assets are held in the United States.
Operating results and total assets by segment were as follows:
Year Ended December 31, 2017 | ||||||||||||||||||||
Flight Systems Group | Defense Systems Group | Space Systems Group | Corporate | Total | ||||||||||||||||
(in millions) | ||||||||||||||||||||
Sales: | ||||||||||||||||||||
External customers | $ | 1,669 | $ | 1,952 | $ | 1,143 | $ | — | $ | 4,764 | ||||||||||
Intercompany | 12 | 16 | 141 | (169 | ) | — | ||||||||||||||
Total | $ | 1,681 | $ | 1,968 | $ | 1,284 | $ | (169 | ) | $ | 4,764 | |||||||||
Income (loss) before interest, income taxes and noncontrolling interest | $ | 211 | $ | 193 | $ | 142 | $ | (17 | ) | $ | 529 | |||||||||
Capital expenditures | $ | 73 | $ | 34 | $ | 34 | $ | 104 | $ | 245 | ||||||||||
Depreciation | $ | 59 | $ | 18 | $ | 36 | $ | 5 | $ | 118 | ||||||||||
Amortization of intangibles | $ | — | $ | 1 | $ | — | $ | 36 | $ | 37 | ||||||||||
Total assets | $ | 2,262 | $ | 1,337 | $ | 1,256 | $ | 811 | $ | 5,666 |
94
Year Ended December 31, 2016 | ||||||||||||||||||||
Flight Systems Group | Defense Systems Group | Space Systems Group | Corporate | Total | ||||||||||||||||
(in millions) | ||||||||||||||||||||
Sales: | ||||||||||||||||||||
External customers | $ | 1,483 | $ | 1,804 | $ | 1,168 | $ | — | $ | 4,455 | ||||||||||
Intercompany | 13 | 19 | 70 | (102 | ) | — | ||||||||||||||
Total | $ | 1,496 | $ | 1,823 | $ | 1,238 | $ | (102 | ) | $ | 4,455 | |||||||||
Income (loss) before interest, income taxes and noncontrolling interest | $ | 204 | $ | 172 | $ | 129 | $ | (33 | ) | $ | 472 | |||||||||
Capital expenditures | $ | 78 | $ | 44 | $ | 56 | $ | 9 | $ | 187 | ||||||||||
Depreciation | $ | 54 | $ | 18 | $ | 31 | $ | 13 | $ | 116 | ||||||||||
Amortization of intangibles | $ | — | $ | 1 | $ | — | $ | 42 | $ | 43 | ||||||||||
Total assets | $ | 2,208 | $ | 1,228 | $ | 1,280 | $ | 702 | $ | 5,418 |
Nine Months Ended December 31, 2015 | ||||||||||||||||||||
Flight Systems Group | Defense Systems Group | Space Systems Group | Corporate | Total | ||||||||||||||||
(in millions) | ||||||||||||||||||||
Sales: | ||||||||||||||||||||
External customers | $ | 1,115 | $ | 1,314 | $ | 962 | $ | — | $ | 3,391 | ||||||||||
Intercompany | 27 | 6 | 15 | (48 | ) | — | ||||||||||||||
Total | $ | 1,142 | $ | 1,320 | $ | 977 | $ | (48 | ) | $ | 3,391 | |||||||||
Income (loss) from continuing operations, before interest, income taxes and noncontrolling interest | $ | 197 | $ | 126 | $ | 67 | $ | (57 | ) | $ | 333 | |||||||||
Capital expenditures | $ | 48 | $ | 23 | $ | 31 | $ | 3 | $ | 105 | ||||||||||
Depreciation | $ | 39 | $ | 15 | $ | 24 | $ | 11 | $ | 89 | ||||||||||
Amortization of intangibles | $ | — | $ | 1 | $ | — | $ | 32 | $ | 33 | ||||||||||
Total assets | $ | 2,224 | $ | 1,184 | $ | 1,273 | $ | 643 | $ | 5,324 |
Certain administrative functions are primarily managed by the Company at the corporate headquarters ("Corporate"). Some examples of such functions are human resources, pension and postretirement benefits, corporate accounting, legal, tax, treasury and certain strategic growth initiatives. Significant assets and liabilities managed at Corporate include those associated with debt, restructuring, pension and postretirement benefits, environmental liabilities, litigation liabilities, strategic growth costs and income taxes.
Costs related to the administrative functions managed by Corporate are either recorded at Corporate or allocated to the segments based on the nature of the expense. The difference between pension and postretirement benefit expense calculated under U.S. GAAP and the expense calculated under U.S. Cost Accounting Standards is recorded at the corporate level which provides for greater clarity on the operating results of the business segments. Administrative expenses such as corporate accounting, legal and treasury costs are allocated out to the business segments. Transactions between segments are recorded at the segment level, consistent with the Company's financial accounting policies. Intercompany balances and transactions involving different segments are eliminated at the Company's consolidated financial statements level and are shown above in Corporate. The amortization expense related to purchase accounting attributed to the acquisition of Orbital is also recorded in Corporate.
95
19. Transition Period Comparative Data
The following table presents certain financial information for the nine months ended December 31, 2015 and December 28, 2014 respectively:
Nine Months Ended | |||||||
(in millions, except per share data) | December 31, 2015 | December 28, 2014 | |||||
(unaudited) | |||||||
Sales | $ | 3,391 | $ | 2,142 | |||
Gross profit | $ | 674 | $ | 478 | |||
Income from continuing operations | $ | 185 | $ | 109 | |||
Income from discontinued operations | $ | 1 | $ | 108 | |||
Net income attributable to Orbital ATK, Inc. | $ | 186 | $ | 217 | |||
Basic earnings per common share | |||||||
Income from continuing operations | $ | 3.12 | $ | 3.44 | |||
Income from discontinued operations | 0.02 | 3.42 | |||||
Net income attributable to Orbital ATK, Inc. | $ | 3.14 | $ | 6.86 | |||
Diluted earnings per common share | |||||||
Income from continuing operations | $ | 3.09 | $ | 3.37 | |||
Income from discontinued operations | 0.02 | 3.34 | |||||
Net income attributable to Orbital ATK, Inc. | $ | 3.11 | $ | 6.71 |
Note: earnings per share amounts may not recalculate due to rounding.
20. Quarterly Financial Data (unaudited)
For the Year Ended December 31, 2017 | ||||||||||||||||
Quarter Ended | ||||||||||||||||
(in millions, except per share data) | April 2, | July 2, | October 1, | December 31, | ||||||||||||
Sales | $ | 1,085 | $ | 1,115 | $ | 1,216 | $ | 1,348 | ||||||||
Gross profit | $ | 229 | $ | 267 | $ | 275 | $ | 294 | ||||||||
Net income attributable to Orbital ATK, Inc. | $ | 66 | $ | 88 | $ | 94 | $ | 62 | ||||||||
Basic earnings per common share (1) | $ | 1.16 | $ | 1.52 | $ | 1.65 | $ | 1.07 | ||||||||
Diluted earnings per common share (1) | $ | 1.15 | $ | 1.51 | $ | 1.64 | $ | 1.06 | ||||||||
Weighted-average common shares outstanding | 57.33 | 57.41 | 57.31 | 57.38 | ||||||||||||
Weighted-average diluted shares outstanding | 57.78 | 57.73 | 57.76 | 57.97 | ||||||||||||
Cash dividends per common share: | ||||||||||||||||
Declared | $ | 0.32 | $ | 0.32 | $ | 0.32 | $ | 0.32 | ||||||||
Paid | $ | 0.32 | $ | 0.32 | $ | 0.32 | $ | 0.32 |
96
For the Year Ended December 31, 2016 | ||||||||||||||||
Quarter Ended | ||||||||||||||||
(in millions, except per share data) | April 3, | July 3, | October 2, | December 31, | ||||||||||||
Sales | $ | 1,056 | $ | 1,084 | $ | 1,043 | $ | 1,272 | ||||||||
Gross profit | $ | 227 | $ | 280 | $ | 210 | $ | 268 | ||||||||
Net income attributable to Orbital ATK, Inc. | $ | 77 | $ | 91 | $ | 60 | $ | 65 | ||||||||
Basic earnings per common share(1) | $ | 1.33 | $ | 1.56 | $ | 1.04 | $ | 1.12 | ||||||||
Diluted earnings per common share(1) | $ | 1.31 | $ | 1.55 | $ | 1.04 | $ | 1.11 | ||||||||
Weighted-average common shares outstanding | 58.30 | 58.19 | 57.93 | 57.30 | ||||||||||||
Weighted-average diluted shares outstanding | 58.88 | 58.64 | 58.26 | 57.69 | ||||||||||||
Cash dividends per common share: | ||||||||||||||||
Declared | $ | 0.30 | $ | 0.30 | $ | 0.30 | $ | 0.30 | ||||||||
Paid | $ | 0.30 | $ | 0.30 | $ | 0.30 | $ | 0.30 |
(1) Quarterly earnings per common share amounts may not total to annual earnings per common share amounts because quarterly and annual earnings per share are calculated separately based on earnings and basic and diluted weighted-average common shares outstanding during the respective periods.
ITEM 9. CHANGES IN AND DISAGREEMENTS WITH ACCOUNTANTS ON ACCOUNTING AND FINANCIAL DISCLOSURE
None.
ITEM 9A. CONTROLS AND PROCEDURES
Disclosure Controls and Procedures
The Company has established disclosure controls and procedures (as defined in Rule 13a-15(e) under the Securities Exchange Act of 1934) to ensure that information required to be disclosed by the Company in reports that the Company files or submits under the Securities Exchange Act of 1934 is accurately recorded, processed, summarized, and reported within the time periods specified in the SEC's rules and forms. These disclosure controls and procedures include, without limitation, controls and procedures designed to ensure that information required to be disclosed in the reports the Company files or submits is accumulated and communicated to management, including the Chief Executive Officer and Chief Financial Officer, as appropriate to allow timely decisions regarding required disclosure.
Management of the Company, with the participation of its Chief Executive Officer and Chief Financial Officer, evaluated the effectiveness of the Company's disclosure controls and procedures as of December 31, 2017. Based upon this evaluation, the Company's Chief Executive Officer and Chief Financial Officer have concluded that the Company's disclosure controls and procedures were effective as of December 31, 2017.
Management's Report on Internal Control over Financial Reporting
Management is responsible for establishing and maintaining adequate internal control over financial reporting, as such term is defined in Rule 13a-15(f) under the Securities Exchange Act of 1934. The Company's internal control over financial reporting was designed to provide reasonable assurance regarding the reliability of financial reporting and the preparation of financial statements for external purposes in accordance with accounting principles generally accepted in the United States of America. The assessment of the effectiveness of the Company's internal control over financial reporting was based on criteria established in Internal Control-Integrated Framework (2013) issued by the Committee of Sponsoring Organizations of the Treadway Commission. Because of its inherent limitations, internal control over financial reporting can provide only reasonable assurance and may not prevent or detect misstatements. Management of the Company has assessed the effectiveness of the Company's internal control
97
over financial reporting as of December 31, 2017 and concluded that the Company's internal control over financial reporting was effective as of December 31, 2017.
Deloitte & Touche LLP issued an attestation report dated February 21, 2018, concerning the Company’s internal control over financial reporting, which is contained in this Annual Report.
Changes in Internal Control over Financial Reporting
During the quarter ended December 31, 2017, there were no changes in the Company's internal control over financial reporting (as defined in Rule 13a-15(f) under the Securities Exchange Act of 1934) other than changes related to the remediation of the material weakness below, that have materially affected, or are reasonably likely to materially affect, the Company's internal control over financial reporting.
Remediation Efforts to Address Material Weakness
Management previously identified and disclosed a material weakness in internal control over financial reporting related to designing and maintaining controls associated with the preparation, review and approval of costs incurred and contract estimates used to determine revenue at the Small Caliber Systems division. During the quarter ended December 31, 2017, the Company completed the remediation of this material weakness.
ITEM 9B. OTHER INFORMATION
None.
98
PART III
ITEM 10. DIRECTORS, EXECUTIVE OFFICERS AND CORPORATE GOVERNANCE
Board of Directors
Kevin P. Chilton, 63, has been a director of the Company since 2015. General Chilton retired as General from the U.S. Air Force in 2011 after more than three decades of service. He served as Commander, U.S. Strategic Command, from 2007 through 2011, overseeing operations for Department of Defense nuclear, space and cyberspace operations. From 2006 to 2007, General Chilton served as Commander of Air Force Space Command, where he was responsible for all U.S. Air Force space operations. He previously served in the U.S. Air Force in a variety of command positions and as a pilot. General Chilton also served as a NASA astronaut from 1987 to 1996, including on three Space Shuttle flights. He is also a director of CenturyLink, Inc. He was a director of Level 3 Communications, Inc. from 2012 until its acquisition by CenturyLink in November 2017, and served as a director of Anadarko Petroleum Corporation from 2011 to 2017. From 2012 until the merger of the Company and Orbital Sciences Corporation ("Orbital") on February 9, 2015 (the "Orbital-ATK Merger"), he was a director of Orbital.
Roxanne J. Decyk, 65, has been a director of the Company since 2010. Ms. Decyk served as the Executive Vice President of Global Government Affairs for Royal Dutch Shell plc, a global group of energy and petrochemicals companies, from 2009 to 2010. She joined Royal Dutch Shell plc in 1999, where, prior to her most recent position, she was Corporate Affairs Director from 2005 to 2009, Senior Vice President, Corporate Affairs and Human Resources, Shell US from 2002 to 2005, and Vice President, Corporate Strategy from 1999 to 2002. She is also a director of Ensco plc and Weatherford International plc. She was also a director of Snap-on Incorporated from 1993 to 2014, Petrofac Limited from 2011 to 2015, and DigitalGlobe, Inc. from 2014 to 2017.
Lennard A. Fisk, 74, has been a director of the Company since 2015. Dr. Fisk has been a Distinguished University Professor of Space Science at the University of Michigan since 2006. He joined the faculty of the University of Michigan in 1993, where he leads a group that conducts theoretical and experimental space science research. From 1987 to 1993, Dr. Fisk was the NASA Associate Administrator for Space Science and Applications, where he was responsible for the planning and direction of all NASA programs concerned with space science and applications, and for the institutional management of the Goddard Space Flight Center and the Jet Propulsion Laboratory. He has served on numerous advisory committees including the Space Studies Board of the U.S. National Academy of Sciences, which he chaired from 2003 to 2008. From 1993 until the Orbital-ATK Merger in February 2015, he was a director of Orbital Sciences Corporation.
Ronald R. Fogleman, 76, has been a director of the Company since 2004. General Fogleman has been the non-executive Chairman of Orbital ATK's Board of Directors since November 2009. He has been President of B Bar J Cattle and Consulting Company, a consulting firm, since 1997. Prior to retiring from the U.S Air Force in 1997 after 34 years of active service, he was the Commander of the Air Mobility Command, Commander-In-Chief of the US Transportation Command and the Air Force’s 15th Chief of Staff. Since his military retirement he served as a member of the Defense Policy Board, the NASA Advisory Council, the Jet Propulsion Laboratory Advisory Council and two Congressional Commissions associated with the organization of national security assets in space. He has been on the boards of directors of numerous public companies. He served as a director of AAR CORP. from 2001 to 2017, including as AAR’s Lead Director from 2013 to 2017.
Ronald T. Kadish, 69, has been a director of the Company since 2015. General Kadish served as Executive Vice President of Booz Allen Hamilton, a global strategy and technology consulting firm, from 2005 to 2015. In September 2004, he retired as Lieutenant General from the U.S. Air Force after serving for 34 years. From 1999 until his retirement, General Kadish served as Director of the U.S. Missile Defense Agency. From August 1996 to June 1999, General Kadish served as the Commander of the Electronic Systems Center at Hanscom Air Force Base. Prior to that time, he served in numerous assignments with the U.S. Air Force, including Program Director for several major military aircraft platforms. He is also a director of Spirit AeroSystems Holdings, Inc. From 2005 until the Orbital-ATK Merger in February 2015, he was a director of Orbital Sciences Corporation.
Tig H. Krekel, 64, has been a director of the Company since 2010. Mr. Krekel is Chairman and Founding Partner of Hudson Group, a South Carolina advisory services firm. He was the Vice Chairman and a partner of J.F. Lehman & Company, a New York private-equity investment bank, from 2003 to 2012. Before joining J.F. Lehman, Mr. Krekel served as President and Chief Executive Officer of Hughes Space and Communications and President of Boeing Satellite Systems, the world's largest manufacturer of commercial and military communications satellites. He is also a director of Vista Outdoor Inc.
99
Douglas L. Maine, 69, has been a director of the Company since 2006. Mr. Maine joined International Business Machines in 1998 as Chief Financial Officer following a 20-year career with MCI, a telecommunications firm, where he was Chief Financial Officer from 1992-1998. He was named General Manager of ibm.com in 2000 and General Manager, Consumer Products Industry in 2003 and retired in 2005. Mr. Maine is currently a Limited Partner and Senior Advisor to Brown Brothers Harriman & Co., a financial services firm. He is also a director of Albemarle, Inc. and BroadSoft, Inc. He was also a director of Rockwood Holdings, Inc. from 2005 until January 2015, when Albemarle acquired Rockwood.
Roman Martinez IV, 70, has been a director of the Company since 2004. Mr. Martinez has been a private investor since 2003. He retired as Managing Director of Lehman Brothers, an investment banking firm, in 2003, following a 31-year career with the firm. He is also a director of Cigna Corporation. From 2008 to 2014, he was also a director of Bacardi Limited.
Janice I. Obuchowski, 66, has been a director of the Company since 2015. Ms. Obuchowski has been President of Freedom Technologies, Incorporated, a telecommunications research and consulting firm, since 1992. Ms. Obuchowski also served as Ambassador and U.S. Representative to the 2003 World Radiocommunication Conference. From 1989 to 1992, she served as Assistant Secretary for Communications and Information at the U.S. Department of Commerce and Administrator of the National Telecommunications and Information Agency. From 1980 to 1987, she served in a variety of positions at the U.S. Federal Communications Commission, including Senior Adviser to the Chairman. Ms. Obuchowski is a director of CSG Systems International, Inc. and Inmarsat plc. She has also served as a director of QUALCOMM, and of Stratos Global, as well as a representative to several United States government advisory committees. From 1996 until the Orbital-ATK Merger in February 2015, she was a director of Orbital Sciences Corporation.
James G. Roche, 78, has been a director of the Company since 2015. Dr. Roche served as the Secretary of the U.S. Air Force from 2001 to 2005. From 1984 to 2001, he held several executive positions with Northrop Grumman Corporation, a global defense company, including Corporate Vice President and President of its Electronic Sensors and Systems Sector. From 1983 to 1984, Dr. Roche was Democratic Staff Director of the U.S. Senate Committee on Armed Services. He served in the U.S. Navy for 23 years and retired with the rank of captain in 1983. Between 2006 and 2009, Dr. Roche served as a director of TechTeam Global, Inc. From 2005 until the Orbital-ATK Merger in February 2015, he was a director of Orbital Sciences Corporation.
Harrison H. Schmitt, 82, has been a director of the Company since 2015. Dr. Schmitt has served in various capacities as an aerospace and earth science consultant since 1983. From 1977 to 1983, Dr. Schmitt was a U.S. Senator from New Mexico, during which time he chaired the Senate Science, Technology and Space Subcommittee, which oversaw all non-military space-related research and development programs of the U.S. Government. During 1981 to 1983, Schmitt served on the Senate Appropriations Committee. From 1974 to 1975, he was Assistant Administrator for Energy Programs for NASA. From 1965 to 1973, he was a NASA astronaut and pilot. As Lunar Module Pilot and geologist on Apollo 17 in 1972, the last Apollo mission to the Moon, he explored the Moon's surface. Dr. Schmitt chaired the NASA Advisory Council from 2005 to 2008. From 1983 until the Orbital-ATK Merger in February 2015, he was a director of Orbital Sciences Corporation and served as Lead Director during the year leading to the Orbital-ATK Merger.
David W. Thompson, 63, has been a director of the Company since 2015. Mr. Thompson has been President and Chief Executive Officer of Orbital ATK since the Orbital-ATK Merger in February 2015. He co-founded Orbital Sciences Corporation and served as Chairman of the Board and Chief Executive Officer of Orbital from 1982 until the Orbital-ATK Merger. From 1982 to 1999, he also served as President of Orbital, a role he resumed in mid-2011. Prior to founding Orbital, Mr. Thompson was employed by Hughes Electronics Corporation as special assistant to the President of its Missile Systems Group and by NASA at the Marshall Space Flight Center as a project manager and engineer, and also worked on the Space Shuttle's autopilot design at the Charles Stark Draper Laboratory.
Scott L. Webster, 65, has been a director of the Company since 2015. He is currently the Chairman of the Board of Cobham Advanced Electronic Solutions, the U.S. subsidiary of Cobham plc, a multinational defense technology company. Mr. Webster was Chairman of the Board of MBDA Incorporated, the U.S. subsidiary of MBDA, a multinational developer and manufacturer of missiles and missile systems, from 2013 to January 2017. He served as interim CEO of MBDA Incorporated from 2013 to 2014. Mr. Webster is a co-founder of Orbital Sciences Corporation. From 1998 to 2001, he served as Chairman of the Board and Chief Executive Officer of ORBCOMM Global, L.P., a satellite services company formerly affiliated with Orbital. Mr. Webster previously served for over ten years in executive leadership positions and then in various consulting capacities with Orbital through 1997. From 1982 until the Orbital-ATK Merger in February 2015, he was a director of Orbital Sciences Corporation.
100
Executive Officers
Information regarding the Company's executive officers is set forth under the heading "Executive Officers" in Item 1, "Business" of Part I of this Form 10-K and is incorporated by reference in this Item 10, "Directors, Executive Officers and Corporate Governance".
Section 16(a) Beneficial Ownership Reporting Compliance
Section 16(a) of the Securities Exchange Act of 1934 requires our directors and certain officers, as well as beneficial owners of more than 10% of the Company's common stock, to file initial reports of ownership and reports of changes in ownership of securities with the Securities and Exchange Commission. Such persons are required to furnish us with copies of these reports. Based solely on a review of these reports, written representations from our directors and officers, and applicable regulations, we believe that all required reports for the fiscal year ended December 31, 2017 were timely filed, except that the Company filed a late Form 4 on August 15, 2017 on behalf of Frank L. Culbertson, relating to his sale on August 10, 2017 of three shares held through the Orbital ATK Stock Fund in the Company's 401(k) plan and intra-plan transfer into other investments. In addition, the Company filed a Form 5 on February 6, 2018 on behalf of Ronald T. Kadish, to report a gift transfer of directly-held shares of common stock to his trust on August 17, 2016. The Company previously disclosed in a Form 4 report relating to a different transaction that the nature of Mr. Kadish’s beneficial ownership of the shares transferred to his trust had changed from direct to indirect. However, the Company subsequently determined that the transfer was not merely a change in the form of Mr. Kadish’s ownership, exempt from the reporting requirements of Section 16(a), but rather was reportable on Form 5 as a gift.
Code of Ethics and Business Conduct
We have a written code of business ethics and conduct which applies to all directors, officers and employees. Our Corporate Governance Guidelines provide that the Board will not permit any waiver of our Code of Ethics and Business Conduct. Our Code of Ethics and Business Conduct is available on our website at www.orbitalatk.com by selecting Investors and then Corporate Governance. We intend to satisfy the disclosure requirements under the Securities Exchange Act of 1934, as amended, regarding an amendment to, or a waiver from, our Code of Ethics and Business Conduct by posting such information on our website at www.orbitalatk.com.
Stockholders may request a free printed copy of our Code of Ethics and Business Conduct from our investor relations department by contacting them by telephone at 703-406-5960 or by email at investor.relations@orbitalatk.com.
Audit Committee
Members: | Douglas L. Maine, Chair | Ronald T. Kadish | ||
Kevin P. Chilton | Roman Martinez IV |
The Audit Committee is responsible for assisting the Board of Directors in monitoring the integrity of the Company's financial statements, the Company's compliance with legal and regulatory requirements and aspects of the Company's Code of Ethics and Business Conduct, the independent auditor's qualifications and independence, and the performance of the Company's internal audit function and the independent auditor. The Audit Committee has the sole authority to retain and terminate the independent auditor and is directly responsible for the compensation and oversight of the work of the independent auditor. The independent auditor reports directly to the Audit Committee. The Audit Committee reviews and discusses with management and the independent auditor the annual audited and quarterly financial statements (including the specific disclosures under the "Management's Discussion and Analysis of Financial Condition and Results of Operations"), critical accounting policies and practices used by the Company, the Company's internal control over financial reporting, and the Company's major financial risk exposures.
All of the Audit Committee members meet the independence and experience requirements of the NYSE and the Securities and Exchange Commission. The Board has identified Mr. Maine and Mr. Martinez as audit committee financial experts under the rules of the Securities and Exchange Commission. The Audit Committee held 20 meetings during 2017, five of which were regularly-scheduled meetings and 15 of which were special meetings. Generally, the Audit Committee meets separately with the independent auditors and the Company's internal auditors at regularly-scheduled meetings and periodically meets separately with management.
101
ITEM 11. EXECUTIVE COMPENSATION
EXECUTIVE COMPENSATION
COMPENSATION DISCUSSION AND ANALYSIS
Executive Summary
The following discussion describes Orbital ATK's executive compensation program for 2017 and certain compensation decisions made for 2018.
The Compensation Discussion and Analysis describes the objectives and elements of our executive compensation program and explains the compensation decisions of the Company's Compensation and Human Resources Committee (the "Committee") with respect to our named executive officers ("NEOs"). As of December 31, 2017, our NEOs were:
• | David W. Thompson, President and Chief Executive Officer |
• | Blake E. Larson, Chief Operating Officer |
• | Garrett E. Pierce, Chief Financial Officer |
• | Frank L. Culbertson, Executive Vice President and President, Space Systems Group |
• | Michael A. Kahn, Executive Vice President and President, Defense Systems Group |
2017 Overview
The Company achieved strong financial and operational results in 2017, with revenue, operating income, earnings per share and free cash flow meeting or exceeding our annual guidance. In addition, in early 2017, the Company completed its filing with the Securities and Exchange Commission of a previously disclosed multi-year restatement of its financial statements and remediated all material weaknesses in its internal financial controls that were identified during the restatement process. Most significantly, the Company entered into a definitive agreement with Northrop Grumman Corporation under which Northrop Grumman will acquire all outstanding shares of the Company's common stock for $134.50 per share. The transaction consideration represents a substantial premium over the market price for the Company’s common stock, and the pending acquisition reflects the significant value the Company has generated for its customers, shareholders, and employees in recent years.
In 2017, Orbital ATK generated solid operational results and received significant contract awards in a number of its product markets as we continued providing innovative and reliable products with best-in-class safety and quality. The Company’s operational successes in 2017 included the following highlights:
• | In the Flight Systems Group, we completed a successful launch of our Antares rocket, which carried the Company’s Cygnus spacecraft on a resupply mission to the International Space Station (“ISS”), a Taurus rocket carrying ten commercial spacecraft, and a Minotaur IV rocket carrying a US Air Force satellite. The Company also conducted successful tests of its IRBM and Patriot target vehicles, and supported a number of additional rocket launches with its propulsion and composite structures products. |
• | In the Defense Systems Group, Orbital ATK delivered its 100,000th Hellfire tactical missile motor and delivered over 1.3 billion small- and medium-caliber ammunition rounds. |
• | In the Space Systems Group, we continued to meet our commitments to NASA for International Space Station cargo delivery, completing two Cygnus missions during the year, made progress on the development of the Company’s Mission Extension Vehicle, which will provide satellite extension services to customers, and delivered 20 Iridium NEXT satellites and its first GEOStar-3 commercial satellite, which was successfully launched in January 2018. |
Overall, the Company achieved new business awards of $7.6 billion in 2017 increasing total contract backlog (including options, indefinite quantity contracts and undefinitized orders) approximately 12% to $16.0 billion at the end of 2017, including $10.2 billion of firm contract backlog. The Company won key business in a number of important areas, including the following:
• | Flight Systems booked approximately $2.2 billion of orders and options, highlighted by major contracts for military aircraft structures, including for the F-35 fighter. |
• | Defense Systems received approximately $3.7 billion of new contracts and options, including a significant contract to continue full-rate production of the advanced anti-radiation guided missile (AARGM), long-term |
102
agreements with multiple commercial ammunition suppliers, providing flexibility to optimize operations at the Lake City Army Ammunition Plant, and a number of foreign and domestic awards for medium- and large-caliber ammunition.
• | Space Systems won nearly $1.7 billion in new business, with contracts for government spacecraft and the Company’s second mission extension vehicle. |
The Company also continued its balanced cash deployment program in 2017, repurchasing approximately $23 million of its common stock and declaring quarterly dividends totaling $74 million. Share repurchases were limited in 2017 due to trading blackouts associated with the Company’s restatement of its financial statements, completed in mid-2017, and subsequent restrictions imposed by the merger agreement with Northrop Grumman. The Company however continued its practice of annual increases to its quarterly dividend in 2017, increasing the amount from $0.30 per share to $0.32 per share at the start of 2017. In the aggregate, the Company’s return to investors totaled $97 million for the year.
Overview of 2017 Pay Decisions
• | Modest Salary Increases. Increases in 2017 salaries ranged from 1.50% to 4.65% for three of our NEOs, with salaries unchanged for two of our NEOs. The increases were designed to maintain market competitiveness and recognize individual performance and criticality to the Company. |
• | Target Incentive Opportunity Adjustments. Target annual cash incentive opportunities, expressed as a percentage of base salary were not increased in 2017 compared to 2016 levels. Target long-term incentive opportunities were increased for Messrs. Thompson and Larson and decreased for Messrs. Culbertson and Kahn. |
• | Above Target Payout of Annual Incentive Program. The 2017 annual cash incentive plan was based on earnings before interest and taxes (“EBIT”), revenue, free cash flow, orders, and operations and integration milestones. Group presidents were assessed on performance at both the corporate and group level, and corporate executives were assessed on performance at the corporate level. Due to solid financial and operational performance, corporate executives achieved 150% of target performance, the Space Systems Group President achieved 154% of target performance, and the Defense Systems Group President achieved 154% of target performance. |
Results of 2017 Stockholder "Say on Pay" Vote
At the 2017 annual meeting of stockholders, the Company received a 95% vote in favor of the compensation paid to executive officers, indicating a strong endorsement of the Company's executive compensation program. The Committee continues to be mindful of stockholder interests in making compensation decisions.
Overview of Executive Compensation Program and Key Practices
The primary components of our executive compensation program are base salary, an annual incentive opportunity, and a long-term incentive ("LTI") opportunity consisting of grants of performance shares, restricted stock and stock options. Significant elements of our executive officers' compensation are tied to financial and operating performance and are intended to drive sustained long-term stockholder value. The metrics for the annual and long-term incentives are described in detail later in this Compensation Discussion and Analysis. Annually, the Committee reviews and approves the metrics for our annual- and long-term incentives. The metrics for our annual incentive normally are measured based on a 12-month performance period, and our long-term incentive performance shares are based on a three-year period. Details regarding our annual incentive awards are provided in the "Grants of Plan-Based Awards" table below.
The two charts immediately below show the general allocation of 2017 compensation for our executive officers, including by type of award, the percentage of total compensation that is tied to the achievement of financial and operational performance metrics and to stock performance, and the percentage of total compensation that is "at risk." The value of each type of incentive-based compensation assumes achievement of the target value for each type of incentive. Since these awards have both upside opportunity and downside risk, these percentages may not reflect the actual amounts realized.
103
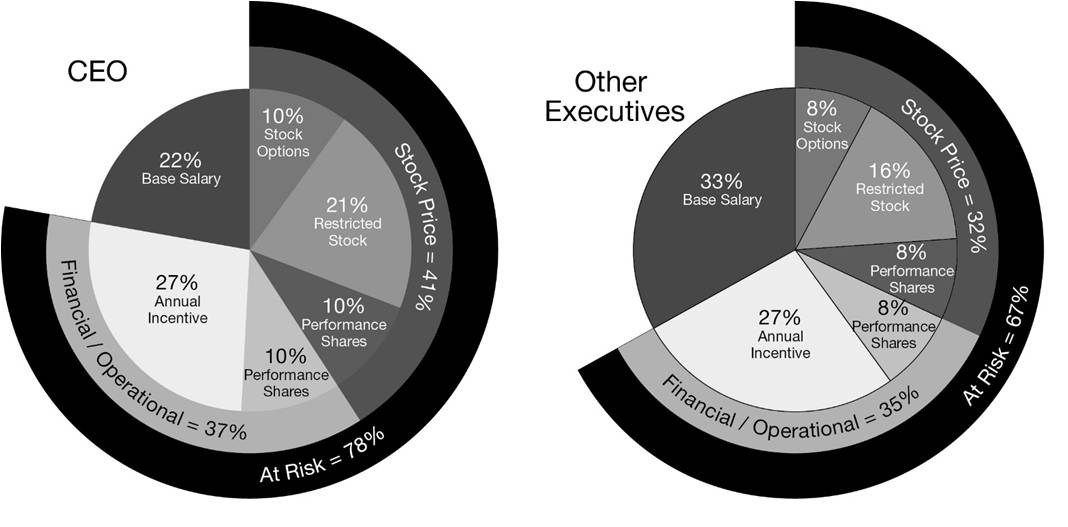
Our compensation program includes the following important pay governance and other policies and practices:
• | A stock holding requirement for executive officers |
• | A policy prohibiting hedging and pledging of Company stock by our directors and officers |
• | No stock options granted with an exercise price below market value on the date of grant |
• | No repricing or buybacks of stock options |
• | Caps on annual and long-term incentives |
• | Limited perquisites |
• | Double-trigger provisions for a change in control |
• | A recoupment (clawback) policy |
• | Use of an independent compensation consultant to provide third-party advice on executive compensation |
Executive Compensation Philosophy
The overall objective of the Company's executive compensation program is to create long-term stockholder value. The program seeks to achieve this goal by providing a competitive compensation package to our executives in order to attract, motivate and retain a talented executive leadership group that is dedicated to the long-term interests of our stockholders.
Both management and the Committee realize the importance of maintaining sound principles for the development and administration of executive compensation and benefit programs. Executive compensation decisions are based on three fundamental principles:
1. | Performance-Based - Incentive compensation is designed to motivate behavior that will drive strong financial performance and create stockholder value. Executive compensation varies in relation to the Company's financial performance and stock price performance. The Committee sets target performance levels in line with the Company's annual and long-term business and strategic plans and, accordingly, the Company must achieve superior performance in order for executive officers to receive payments in excess of the target amounts. |
2. | Aligned with Stockholder Interests - The Company will achieve the best results for its stockholders when its executives act and are rewarded as owners of the business. |
• | On an ongoing basis, a significant portion of our total direct compensation is provided through equity-based incentives - generally, over half of the total opportunity for our Chief Executive Officer and, on average, approximately 40% of the total opportunity for our other executive officers. |
104
• | Executive officers are required to retain at least 50% of the net shares (remaining after payment of withholding taxes and, in the case of options, exercise price) received as compensation and to hold such shares until the executive leaves the Company. |
3. | Quality of Talent - Orbital ATK requires highly-skilled executives to drive long-term success - executives whose abilities are essential to the creation of long-term value for stockholders. To ensure we remain competitive in attracting and retaining talented executives, we conduct an annual market analysis for both direct and indirect compensation. |
• | Total direct compensation (base salary, annual incentive, long-term incentive) is benchmarked against a peer group of industry companies of comparable size. In addition, the Committee references survey-reported information from the aerospace and defense industry and manufacturing industries to obtain a broader market perspective. The determination of compensation is described in more detail below. |
Indirect compensation programs (benefits) are evaluated separately from direct compensation through the Company's regular benefit review and benchmarking process. For all employees, the Company considers general market data from companies in relevant industries and of relevant revenue size.
Elements of Orbital ATK's Executive Compensation Program
The primary elements of the Company's executive compensation program are shown in the following table:
Compensation Element | Objective |
Base salary | To provide a fixed level of cash compensation for sustained individual performance based on level of responsibility, experience and performance. |
Annual incentive | To focus executives' attention on annual performance goals and reward executives for their contributions to the Company's short-term financial and operational performance. |
Long-term compensation | To align management's interests with those of the Company's stockholders through the use of stock incentive programs designed to reward financial performance that creates stockholder value over time, link awards to stock-price performance, and serve as a retention vehicle for top executive talent. |
Benefits | To provide a competitive total compensation program and support the attraction and retention of highly-skilled executives. |
The various elements afford flexibility in designing an executive compensation package and allow the Committee to focus executive officers' efforts on both short-term and long-term business objectives.
Determination of Compensation
The Committee is responsible for setting the Company's compensation policies and approving the compensation paid to executive officers. The Committee also receives advice on compensation matters from Semler Brossy Consulting Group, LLC, the Committee's independent compensation consultant. Semler Brossy has served as the Committee's compensation consultant since September 2013.
Compensation Benchmarking
Each year, before the Committee approves executive officer compensation for the upcoming fiscal year, we review our executive compensation program to (1) assess ongoing market competitiveness and (2) consider both Company and individual performance. The Committee benchmarks executive compensation for the Company's officers against officers in similar positions at comparable companies. In addition, the Committee also reviews compensation survey data from the aerospace and defense industry and manufacturing industries to provide a broader view of compensation practices in the market. The benchmarking data is not applied in a formulaic manner, but rather the Committee members consider the information in exercising their business judgment to make compensation decisions.
For 2017, with input from Semler Brossy, the Committee made several changes to the Company’s peer group of aerospace and defense companies with revenue between $1 billion and $15 billion that it had employed in the prior fiscal year. The Committee removed SPX Corporation, due to a significant spin-off transaction, as well as AMETEK, Inc. and Timken Company, replacing them with Aerojet Rocketdyne and Huntington Ingalls to increase the emphasis on aerospace and defense companies.
105
For 2017, our peer group consisted of the following 16 companies:
Textron Inc. | Triumph Group, Inc. |
L-3 Communications Holdings, Inc. | Huntington Ingalls Industries |
Spirit AeroSystems Holdings, Inc. | Moog Inc. |
Rockwell Automation, Inc. | Teledyne Technologies Incorporated |
Oshkosh Corporation | Curtiss-Wright Corporation |
Rockwell Collins, Inc. | Esterline Technologies Corporation |
Harris Corporation | Hexcel Corporation |
Aerojet Rocketdyne | Kaman Corporation |
In late 2017, the Committee reevaluated this peer group and determined to continue it unchanged for 2018.
Compensation Decision-Making Process
Each year, the Committee meets at a regularly scheduled meeting to establish base salary and annual and long-term incentive compensation levels for the Company's executive officers for the upcoming fiscal year. In establishing executive compensation for 2017, the Committee reviewed multiple market reference points for each executive officer as a guide to establish a targeted level of total direct compensation (base salary, annual incentive, and long-term incentives) for each executive officer position. The data for base salary, annual incentive compensation, and long-term incentive compensation for each position were compared to the current compensation levels of the respective executive officers, and the Company's CEO then made recommendations to the Committee on the pay levels for officers (other than himself) based on the CEO's assessment of the officer's performance and experience level and applicable retention considerations. The Committee retains discretion to make adjustments such that the compensation of individual executive officers may be above or below the market references. The level of compensation for the Company's CEO is determined solely by the Committee, with assistance from the Committee's compensation consultant. The Committee approves all grants of long-term incentive equity awards to executive officers, and the Company does not backdate, reprice or grant equity awards retroactively. Payments of equity and cash compensation are audited for conformity to amounts authorized by the Committee and for compliance with applicable processes and procedures.
2017 Base Salaries
In late 2016, the Committee’s compensation consultant, Semler Brossy, presented an assessment of executive pay levels based on a review of peer group proxy materials, general industry compensation data, and specific industry data. The Committee conducted its review and approval of executive officers' base salaries for 2017 at the Committee's February 2017 meeting. The Committee approved a base salary increase effective March 2017 for three of the named executive officers as summarized below.
The decision to give an executive officer a base salary increase and the amount of that increase was made by considering competitive salary levels as presented to the Committee by Semler Brossy, the officer's specific responsibilities and experience level, and recommendations on individual performance and retention considerations by our CEO for each officer other than himself.
For 2017, the Committee approved the following increases to each named executive officer's base salary:
Percent Increase | |
Mr. Thompson | 0.00% |
Mr. Pierce | 1.50% |
Mr. Larson | 4.65% |
Mr. Culbertson | 4.16% |
Mr. Kahn | 0.00% |
Mr. Thompson’s 2017 base salary remained unchanged from 2016, and his 2017 base salary continued to place him below the median of the CEO salary comparative benchmarks presented by Semler Brossy.
106
2017 Annual Incentive Compensation
Philosophy and Decision-Making Process
The primary purpose of the Company's annual incentive opportunity is to motivate executives to achieve objectives that will enhance the value of the Company and reward them commensurate with their success. This goal is achieved by making a large portion of the Company's cash compensation variable and dependent upon annual Company and business group financial goals and by setting challenging but achievable target levels of performance.
The goal-setting process for the Company's annual incentive compensation program begins with the CEO working with the Committee to establish performance measures that will provide the appropriate incentives to management to achieve the Company's annual financial and non-financial goals. The Committee determines the weighting of the performance measures, the annual incentive opportunity for each executive, expressed as a percentage of annual base salary and, with input from management, the performance levels to be achieved at the threshold, target and maximum incentive payout levels within such payout range.
Performance Measure Determination and Weighting
In early 2017, the Committee approved the overall annual incentive plan design, including the financial metrics and weighting to be used for 2017 under the Company's Executive Officer Incentive Plan.
The approved metrics consisted of both financial and non-financial operational metrics. The financial annual incentive performance metrics established by the Committee included EBIT, sales, free cash flow and orders. Free cash flow is defined as cash provided by operations less capital expenditures plus asset sales. The non-financial performance metrics for the annual incentive program consist of operational goals measured based on the achievement of specified milestones. For 2017, the Committee determined to retain the same overall annual incentive design, including the same financial metrics, weightings and payout ranges that were in effect for 2016. The Committee also determined to continue the practice of capping the actual incentive payout to Corporate Staff at the highest achievement percentage attained at the business group level. The weightings of the metrics approved by the Committee for 2017 are summarized in the following table. "Corporate Staff" includes Messrs. Thompson, Pierce and Larson and "Group Presidents" includes Messrs. Culbertson and Kahn.
107
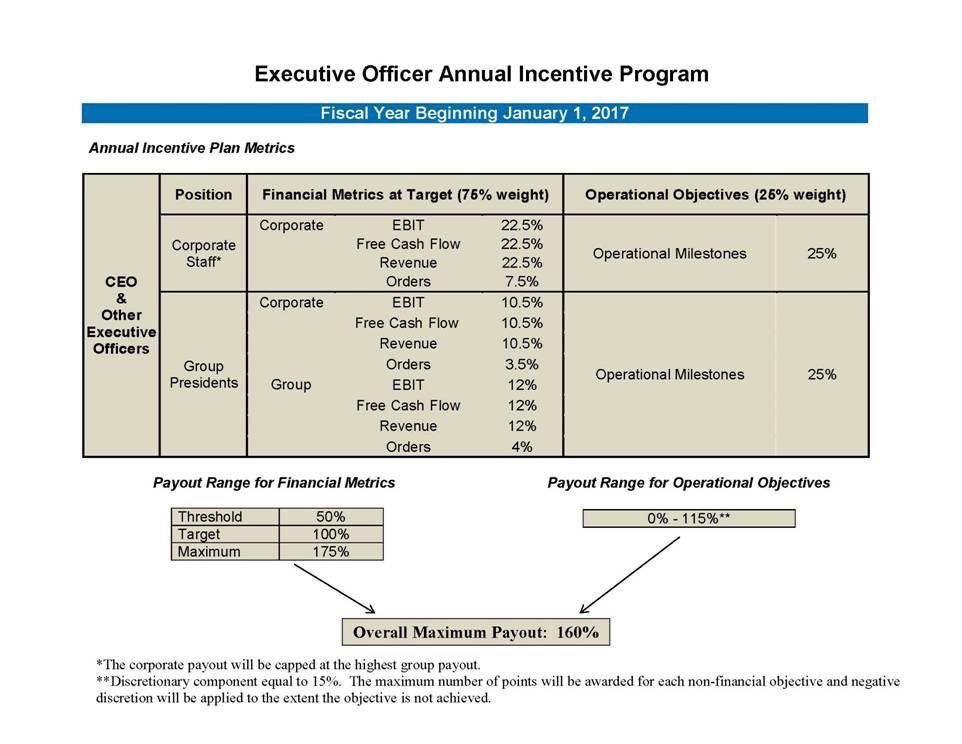
For 2018, the Committee has determined to retain the same overall annual incentive design, including the same financial metrics, weightings and payout ranges that were in effect for 2017.
Annual Incentive Opportunity
As part of its annual review of individual executive officer compensation levels in February 2017, the Committee reviewed and established the annual incentive payment opportunity (expressed as a percentage of base salary) for threshold, target and maximum performance levels for each executive officer. For 2017, the Committee decided to retain the existing target annual incentive opportunity for each named executive officer. As a result, the target performance level, the annual incentive payment opportunity for our CEO was 120% of annual base salary and ranged from 80% to 90% of base salary for the other NEOs.
The Committee established the maximum payout opportunity at 160% of target with no payment earned unless performance met the threshold level. The percentages for each named executive officer were as follows:
Annual Cash Incentive Targets (% of Base Salary) | |||||||||
Threshold | Target | Maximum | |||||||
Mr. Thompson | 45 | % | 120 | % | 192 | % | |||
Mr. Pierce | 33.8 | % | 90 | % | 144 | % | |||
Mr. Larson | 33.8 | % | 90 | % | 144 | % | |||
Mr. Culbertson | 30 | % | 80 | % | 128 | % | |||
Mr. Kahn | 30 | % | 80 | % | 128 | % |
108
Performance Goals
In February 2017, the Committee established the specific performance goals at threshold, target and maximum for each financial performance metric. Performance goals were also established for each of the Company's three business groups and are applicable to the Group Presidents. The target levels of performance were considered by the Committee and management to be challenging but achievable.
When setting the goals, the Committee also specified that, in determining and calculating the financial performance results at the end of 2017, mandatory adjustments would be made (in accordance with the provisions of the Company's Executive Officer Incentive Plan and the requirements of Section 162(m) of the Internal Revenue Code) to eliminate the negative or positive effects of certain items, including for example, litigation or claim judgments or settlements, charges relating to restructurings, discontinued operations, severance and contract termination and other costs incurred in rationalizing certain business activities and extraordinary items and other unusual and non-recurring items of loss or gain. The adjustment factors (specified pursuant to the Company's Executive Officer Incentive Plan) are intended in part to mitigate inappropriate influence in the management decision-making process.
Multiple operational objectives were selected for 2017 for each of the three business groups and their divisions, as well as the Corporate Group and its departments. For the business groups, these objectives included the successful completion of key Company missions, successful execution of product testing, winning key new business, and maintaining schedule and cost performance on various programs. The Corporate Group operational objectives included completion of the Company’s restatement of its financial statements for prior periods and remediating material weaknesses in its accounting controls, improving select Company processes and business systems and achieving certain cost reductions, and providing strong support to business group initiatives.
Actual performance is measured following the end of the performance period, as described below. The Committee retains the discretion to further adjust incentive payment amounts after the adjusted results have been calculated.
Annual Incentive Performance Results
In February 2018, the Committee evaluated the Company's results on each of the performance goals established as described above and applied the applicable adjustment factors in calculating the financial results. Based on the final results, as adjusted, the Company achieved approximately 146% of the target incentive amount for EBIT, 162% of the target incentive amount for revenue, 175% of the target amount for free cash flow and 175% of the target incentive amount for orders. Adjustments were made to the EBIT and free cash flow results to remove the impacts of costs associated with the Company’s restatement of its financial statements for certain prior periods, transaction expenses relating to the pending acquisition by Northrop Grumman, and the acceleration of a payment to a third party into 2017 that was due in 2018.
The Committee has the ability to adjust an officer's payment upward or downward based on individual performance or other factors determined by the Committee to be appropriate in its discretion. While the Committee determines and approves all annual incentive awards and payments for the executive officers, it considers the CEO's assessment of the individual performance of each of the executive officers other than himself. The Committee assesses the performance of the CEO in making any discretionary adjustment to the CEO's annual incentive payment.
The overall Company financial results for 2017 were:
Goals (in millions) | Threshold Performance Goal | Target Performance Goal | Maximum Performance Goal | Reported Results | Adjusted Results | ||||||||||||||||
Company EBIT | $ | 472 | $ | 526 | $ | 579 | $ | 529 | $ | 558 | |||||||||||
Company Revenue | $ | 4,343 | $ | 4,575 | $ | 4,804 | $ | 4,764 | $ | 4,764 | |||||||||||
Company Free Cash Flow* | $ | 234 | $ | 275 | $ | 316 | $ | 275 | $ | 395 | |||||||||||
Company Orders | $ | 4,026 | $ | 4,739 | $ | 5,453 | $ | 5,767 | $ | 5,767 | |||||||||||
*As described above, free cash flow is defined to as cash provided from operations less capital expenditures plus asset sales. |
The table below shows the performance measures and respective weightings and the adjusted performance levels achieved under the annual incentive program at the corporate level for Messrs. Thompson, Larson and Pierce,
109
whose incentive payout is based solely on the financial performance of the Company as a whole, in addition to corporate-level operational factors.
Financial and Operational Measures | Weightings | Overall Target Incentive Achieved | ||
Company EBIT | 22.5 | % | 146% | |
Company Revenue | 22.5 | % | 162% | |
Company Free Cash Flow | 22.5 | % | 175% | |
Company Orders | 7.5 | % | 175% | |
Operational Milestones | 25.0 | % | 113% | |
Overall Performance Level Achieved | 150% |
The table below shows the performance measures and respective weightings and the adjusted performance levels achieved under the annual incentive program for Messrs. Culbertson and Kahn, whose incentive payouts are based both on Company financial results and the results of their respective business group, in addition to group-level operational factors.
Financial and Operational Measures | Weightings | Overall Target Incentive Achieved (Mr. Culbertson) | Overall Target Incentive Achieved (Mr. Kahn) | ||
Company EBIT | 10.5% | 146 | % | 146 | % |
Company Revenue | 10.5% | 162 | % | 162 | % |
Company Free Cash Flow | 10.5% | 175 | % | 175 | % |
Company Orders | 3.5% | 175 | % | 175 | % |
Business Group EBIT | 12% | 175 | % | 175 | % |
Business Group Revenue | 12% | 172 | % | 170 | % |
Business Group Free Cash Flow | 12% | 175 | % | 175 | % |
Business Group Orders | 4% | 175 | % | 175 | % |
Operational Milestones | 25% | 111 | % | 112 | % |
Overall Performance Level Achieved | 154 | % | 154 | % |
The following table sets forth the threshold, target and maximum annual incentive compensation amounts established by the Committee in 2017 and the actual cash incentive paid to each of the named executive officers.
Annual Cash Incentive Amounts | Actual | |||||||||||||||||||||||||||
Threshold | Target | Maximum | Incentive | |||||||||||||||||||||||||
Mr. Thompson | $ | 405,006 | $ | 1,080,017 | $ | 1,728,028 | $ | 1,619,054 | ||||||||||||||||||||
Mr. Pierce | $ | 227,813 | $ | 607,500 | $ | 972,000 | $ | 910,703 | ||||||||||||||||||||
Mr. Larson | $ | 227,813 | $ | 607,500 | $ | 972,000 | $ | 910,703 | ||||||||||||||||||||
Mr. Culbertson | $ | 150,000 | $ | 400,000 | $ | 640,000 | $ | 616,680 | ||||||||||||||||||||
Mr. Kahn | $ | 156,000 | $ | 416,000 | $ | 665,600 | $ | 641,306 |
2017 Long-Term Incentive Compensation
The Committee determines the framework and goals for the Company's long-term incentive compensation program. When considering the long-term incentive program design for this performance period, the Committee reviewed the current construct of compensation being delivered through restricted stock, stock options and other performance-based awards. The Committee determined to retain the mix of long-term awards utilized for the Company's executive officers in prior years, consisting of restricted stock, stock options and performance shares measured over a three-year performance period. The Committee also retained the performance goals and weightings used for the prior period - relative total stockholder return, absolute revenue growth and return on invested capital.
The key elements and objectives of the long-term incentive program for the Company's executive officers are shown below.
110
Executive Officer Long-Term Incentive Program | |||
Type of Award | Value* | Objectives | Key Terms |
Performance Shares (to be paid out in shares of Orbital ATK common stock upon the achievement of pre-determined metrics) | 40% of long-term incentive opportunity | Aligned with long-term stockholder interests by focusing on total shareholder return, top-line growth, profitability, and capital | Measured over a three fiscal-year period: (1) relative total stockholder return: relative three-year return compared to aerospace and defense companies with revenue >$1 billion in the S&P Composite 1500 Index (50% weighting); (2) absolute revenue growth (25% weighting); (3) return on invested capital (25% weighting) |
Restricted Stock | 40% of long-term incentive opportunity | Retention, with underlying value based on stock-price performance | Equal annual installment vesting over a three-year period |
Stock Options | 20% of long-term incentive opportunity | Long-term stock price appreciation | Exercise price equal to fair market value of Orbital ATK stock on the date of grant; equal annual installment vesting over a three-year period; 10-year term |
* The value of the performance shares and restricted stock was determined using the closing sale price of Orbital ATK common stock on the grant date of the award. The value of the stock options was determined using the Black-Scholes option pricing model on the grant date of the award.
The potential payout for a performance share grant ranges from 25% of target to 200% of target. For all measures, no payout will be made if performance falls short of threshold, and the actual amounts payable will be interpolated on a straight line basis between the threshold and target or between the target and maximum, as applicable.
In February 2018, as part of its planning for long-term incentive grants to be made during fiscal 2018, the Committee determined to retain the same overall long-term incentive plan design, for the same reasons described above with respect to annual incentives.
Long-Term Incentive Opportunity
In February 2017, the Committee approved the amount of each executive officer's long-term incentive award opportunity based on the Committee's review and assessment of the market competitiveness of the officers' target level of total direct compensation, including long-term incentive compensation. The target long-term incentive compensation amount for each of the named executive officers was set at or near the market median for officers in similar positions at companies in our peer group or the survey data from the aerospace and defense industry. The long-term incentive award opportunity is divided 40%-40%-20% between awards of restricted stock, performance shares and options, respectively, as shown below. In light of the proposed transaction with Northrop Grumman, the Committee determined that options would not be an appropriate incentive award type for 2018. Consequently, the weighting for 2018 grants is 60%-40% restricted stock and performance shares.
Restricted Stock (40% of Total) | Performance Shares (40% of Total) | Options (20% of Total) | Total | |
Mr. Thompson | $840,000 | $840,000 | $420,000 | $2,100,000 |
Mr. Pierce | $400,000 | $400,000 | $200,000 | $1,000,000 |
Mr. Larson | $500,000 | $500,000 | $250,000 | $1,250,000 |
Mr. Culbertson | $200,000 | $200,000 | $100,000 | $500,000 |
Mr. Kahn | $200,000 | $200,000 | $100,000 | $500,000 |
Performance Measure Levels
The Committee established the specific levels for each performance measure applicable to the grant of performance shares. When setting the levels, the Committee also specified that in determining and calculating the performance results at the end of the performance period, adjustments would be made to eliminate the negative or positive effects of certain items, including, for example, litigation or claim judgments or settlements, charges relating to restructurings, discontinued operations, severance and contract termination and other costs incurred in rationalizing certain business activities and extraordinary items and other unusual and non-recurring items of loss or gain. Actual performance will be measured following the end of the performance period. The Committee retains
111
the discretion to further adjust incentive payment amounts downward after the adjusted results have been calculated.
Long-Term Incentive Compensation Payouts
On December 31, 2017, the fiscal year 2015-2017 period for performance share grants ended. Based on the audited financial results for 2017 and, after the adjustment factors were applied, in February 2018, the Committee determined, for the performance metrics applicable to this performance period, that the Company achieved 65% of the target incentive goal for revenue growth and 134% of target for earnings per share growth. The Committee also determined that the Company achieved 200% for the relative total stockholder return goal by performing at the 86th percentile within the designated peer group. Overall, the Company achieved a payout of approximately 150%. The payout of the performance shares is shown in the Option Exercises and Stock Vested table further below.
In addition to the vesting of performance-based shares, during 2017, our named executive officers received shares of stock as a result of the time-based vesting of standard restricted stock grants made to them in prior periods. Our named executive officers also received shares of Company stock as a result of the time-based vesting of restricted stock units (“RSU”s) granted to them under two circumstances. Officers who were employed by Orbital prior to the Orbital-ATK Merger (Messrs. Thompson, Pierce and Culbertson) received annual RSU grants as part of the standard compensation program for that company. The final tranche of a grant made to these executives in 2014 vested in July 2017. Officers who were employed by ATK prior to the Orbital-ATK Merger had performance awards from periods prior to the Orbital-ATK Merger converted into time-based vesting RSUs pursuant to the terms of the Orbital-ATK Merger transaction agreement between ATK and Orbital. For the then-outstanding FY14-16 and FY15-17 performance awards, the Committee determined that the number of RSUs issued in lieu of an executive’s performance award would be based on the target level of performance. This determination was based on the conclusion that a reasonable determination of actual performance could not be made for these grants given the length of time remaining in the performance periods and the resulting uncertainty regarding the measurement of the applicable performance metrics. As a result of the conversions, these awards are no longer subject to the performance-based vesting conditions of the original performance shares. Consequently, the RSUs for the FY15-17 period time-vested on March 31, 2017. The vesting of RSUs in 2017 for our named executive officers is provided in the Option Exercises and Stock Vested table in this Form 10-K.
Other Compensation Design Elements
Recoupment and Forfeiture
The Company has a recoupment policy that reserves the right of the Committee to recoup any incentive awards from an executive officer if there is a material restatement of the Company's financial results. If the Committee determines a recoupment is appropriate in the exercise of its discretion, considering all the facts and circumstances, the executive officer shall forfeit and pay back a portion, or all, of the outstanding or previously granted awards as determined by the Committee. This includes awards that are deferred into a Company Nonqualified Deferred Compensation Plan. The recoupment policy applies to all awards granted after December 31, 2009, and includes any form of cash or equity compensation other than base salaries.
Benefit, Retirement and Perquisite Programs
Orbital ATK provides certain benefits to our executive officers, including health, welfare, and retirement benefits. We do so to support the attraction and retention of highly-skilled executives. The Company's benefits programs offer flexibility and choice. Under our benefit programs, employees have the opportunity to choose which benefits fit their personal family and financial needs.
Health and Welfare Benefits. Our executive officers participate in the same health and welfare programs as other Company employees.
Retirement Benefits. In general, our executive officers participate in the standard employee retirement programs. Supplemental executive retirement plans are also provided. See the discussion in this Form 10-K under the headings "Pension Benefits" and "Nonqualified Deferred Compensation."
Nonqualified Deferred Compensation. We offer a nonqualified deferred compensation plan as a tool for our key employees to plan for their financial future. This plan is designed to allow for retirement savings above the limits imposed by the Internal Revenue Service for 401(k) plans on a tax-deferred basis. In general, beyond the potential for a 401(k) make-up match included in the Summary Compensation Table, amounts credited to an employee's account under the plan reflect the employee's voluntary deferral of compensation. All accounts are credited with
112
earnings and investment gains and losses by assuming that deferred amounts were invested in one or more investment alternatives selected by the participant under the terms of the plan. These investment choices are generally the same as those offered to all Company employees through the Company's 401(k) Plan. Following the Orbital-ATK Merger, legacy Orbital executives, including Messrs. Thompson, Pierce, and Culbertson, continued to participate in an Orbital non-qualified deferred compensation plan, which was frozen to future contributions for plan years commencing January 1, 2016.
Severance. From time to time, we need to offer an executive officer a severance package in connection with a termination of employment. Generally, the package is aligned with the benefits outlined in the Company's Executive Severance Plan. In certain circumstances, we may offer additional severance benefits to facilitate successful organizational transitions. The Executive Severance Plan is in line with competitive norms and it is regularly benchmarked against market practices. Payments made under this plan are described below under the heading "Potential Payments Upon Termination or Change in Control."
Change-in-Control. Executive officers participate in our Income Security Plan, which provides for severance payments under certain circumstances following a change-in-control of the Company. We believe this plan helps ensure that our officers will remain focused on the best interests of our stockholders during periods of uncertainty regarding the officers' future employment prospects. Payments under this plan are not triggered solely by a change-in-control, but rather by termination of employment (that meets certain conditions specified in the plan) following a change-in-control. The plan does not include a tax gross-up provision and caps the benefits provided under the plan at the limit established under Section 280G of the Internal Revenue Code in order to avoid both the loss of tax deductions and the imposition of the excise tax pursuant to the Internal Revenue Code. The plan also includes a "sunset" provision applicable to the chief executive officer, the chief financial officer, the chief operating officer, and general counsel of the Company such that after five years of service with the Company in that position the amount payable would gradually be reduced from three times compensation to two times compensation at a rate of two-tenths per year (after a total of nine years of service in that position, the amount payable would be two times compensation). None of Messrs. Thompson, Larson or Pierce has served in their current positions for more than five years and, accordingly, no reduction has been made to their compensation multiple.
The Income Security Plan remained in effect until February 9, 2018 (the third anniversary of the merger of Orbital Sciences and Alliant Techsystems), and no other officers or employees were eligible to participate in that plan. In May 2015, the Committee adopted a new Income Security Plan (the "2015 ISP") applicable to any new executive officers and other employees who became eligible to participate after the May 5, 2015 adoption date. Payments under the 2015 ISP are not triggered solely by a change-in-control, but rather by a termination of employment (that meets certain conditions specified in the plan) following a change-in-control. After February 9, 2018, all executive officers who participated in the prior Income Security Plan became participants in the 2015 ISP. The Committee continues to monitor the design of the 2015 ISP against market competitive practices for such plans.
Limited Perquisites. In recent years, the Committee eliminated most of the Company’s executive perquisites. The Committee believes that it continues to deliver a competitive total compensation package to our executives and therefore does not need to offer extensive perquisites.
Perquisites represent a small portion of any executive officer's total direct compensation. Perquisites paid to our named executive officers are disclosed in the Summary Compensation Table under the "All Other Compensation" column.
Compensation Outside the Standard Program
In certain circumstances, such as hiring a new executive, we may provide compensation outside our standard executive compensation program.
When we offer employment to a new executive, we follow the guidelines in our executive compensation philosophy, unless individual circumstances, combined with competitive market practices, require us to include additional compensation (e.g., signing bonus or special equity grant) to attract and retain the executive talent we need. In general, we do not pay our executives additional compensation for special projects or program results. We believe that we provide a fair and competitive total compensation package to our executives for delivering business results that are expected and subsumed under our pay-for-performance philosophy.
Stock Holding Requirement
Each executive officer is required to retain at least 50% of the net shares (remaining after payment of withholding taxes and, in the case of options, exercise price) of Orbital ATK common stock acquired as compensation to ensure
113
that executives' interests and actions are aligned with the interests of Orbital ATK's stockholders. These shares must be held until the executive leaves the Company or is no longer an executive officer. This approach underscores an ownership mentality for our executives, which is one of the fundamental principles of our executive compensation program.
The Committee annually reviews the holdings of executives to ensure compliance with the stock holding requirement.
No Hedging or Pledging of Company Stock
The Company has a policy and procedures for transactions in Orbital ATK securities for its directors and Section 16 reporting officers. This policy requires all directors and executive officers of the Company to pre-clear any proposed transactions in Orbital ATK securities. In 2015, the Board adopted a policy explicitly prohibiting hedging or pledging of Company securities by directors and executive officers. In addition, the Company's executive officers and directors have provided written representations to the Company that they do not hedge the economic risk of ownership of Company common stock, have not hedged any of their shares of Company stock and have not pledged any shares of Company common stock as collateral for a loan or otherwise.
Tax Deductibility of Compensation
Under Section 162(m) of the Internal Revenue Code, a publicly held corporation generally is limited to a $1 million annual tax deduction for compensation paid to each of its “covered employees.” Prior to the enactment of the Tax Act, which was signed into law on December 22, 2017, a publicly held corporation’s covered employees included its chief executive officer and three other most highly compensated executive officers (other than the chief financial officer), and certain “qualified performance-based compensation” was excluded from the $1 million deduction limit. The Tax Act made certain changes to Section 162(m), effective for taxable years beginning after December 31, 2017. These changes include, among others, expanding the definition of “covered employee” to include a publicly held corporation’s chief financial officer and repealing the qualified performance-based compensation exception, subject to a transition rule for remuneration provided pursuant to a written binding contract which was in effect on November 2, 2017, and which was not modified in any material respect on or after that date.
While compensation decisions for our executive officers in 2017 were made with consideration of the implications of Section 162(m), the Committee does not believe that tax considerations will be material to its future compensation decisions for the named executive officers as a result of the changes to Section 162(m) in the Tax Act. The Committee may decide to pay amounts outside of our stockholder approved plans that are nondeductible if it determines that such payments are consistent with our pay-for-performance philosophy and are in the best interests of the Company.
Compensation Risk Assessment
The Company has reviewed and assessed its incentive compensation plans and programs and concluded that the Company's compensation policies and practices for its employees are not reasonably likely to have a material adverse effect on the Company. During the last fiscal year, the Committee reviewed the Company's assessment process and discussed with management the impact of the Company’s compensation policies and practices on risk taking within the Company.
114
COMPENSATION AND HUMAN RESOURCES COMMITTEE REPORT
The Compensation and Human Resources Committee of the Board of Directors has reviewed and discussed with the Company's management the Compensation Discussion and Analysis. Based on this review and these discussions with management, the Compensation and Human Resources Committee recommended to the Board of Directors that the Compensation Discussion and Analysis be included in Orbital ATK’s annual report on Form 10-K.
This report is provided by the Compensation and Human Resources Committee:
Roxanne J. Decyk, Chair
Lennard A. Fisk
Tig H. Krekel
Douglas L. Maine
Janice I. Obuchowski
115
CEO PAY RATIO
The following pay ratio and supporting information compares the annual total compensation of our employees other than our CEO (including full-time, part-time and temporary employees) and the annual total compensation of our CEO, as required by Section 953(b) of the Dodd-Frank Act. The pay ratio is a reasonable estimate calculated in a manner consistent with Item 402(u) of Regulation S-K.
For 2017, our last completed fiscal year:
• | The median of the annual total compensation of all employees of our Company other than the CEO was $86,079; and |
• | The annual total compensation of our CEO, as reported in the Summary Compensation Table included in Item 11 of Part III of this Form 10-K, was $4,963,326. |
Based on this information, the ratio of the annual total compensation of our CEO to the median of the annual total compensation of all other employees was 58:1.
To determine the pay ratio, we took the steps outlined below.
We determined that as of December 31, 2017, the determination date, our employee population consisted of 13,958 individuals, almost all of whom were located in the United States. This population consists of our full-time, part-time and temporary employees. We did not have any seasonal employees. Included in this total population are eight non-U.S. employees: five in Saudi Arabia and one each in Canada, Singapore, and the United Arab Emirates. Excluding these non-U.S. employees, our employee population that was used to calculate the pay ratio consisted of 13,950 individuals.
To identify the median employee, we compared, over a period of one year, each employee’s compensation derived from base pay, overtime pay, shift premium or shift differential pay, lump sum merit pay, paid actual time-off, pre-tax deferrals (including 401(k) plan and flexible spending account contributions), and any cash incentives paid to the employee in 2017 for performance during the prior year. In making this determination, we did not annualize the compensation of any employees who did not work for us for the entire year. However, for 2,093 full-time and part-time permanent employees who were hired in 2017 and were not paid cash incentives for performance during the prior year, we included their projected cash incentives to be paid in 2018 assuming performance at the target level in 2017.
Once we identified our median employee, we calculated that employee’s annual total compensation for 2017 in accordance with the requirements of Item 402(c)(2)(x) of Regulation S-K, resulting in annual total compensation of $86,079. The median employee’s annual total compensation includes regular pay, paid time-off, a performance recognition award, a cash incentive to be paid in 2018 for performance in 2017, and company contributions to the 401(k) plan.
With respect to our CEO, we used the amount reported as total compensation in the Summary Compensation Table included in Item 11 of Part III of this Form 10-K. Any adjustments, estimates and assumptions used to calculate total annual compensation are described in footnotes to the Summary Compensation Table.
116
References in columns of the tables below to "2015T" refer to the 2015 transition period, which was the nine-month period from April 1, 2015 through December 31, 2015.
SUMMARY COMPENSATION TABLE
The following table shows the cash and non-cash compensation awarded to or earned by the Chief Executive Officer, Chief Financial Officer, and each of our three other most highly compensated executive officers during 2017. The materially lower total compensation amounts reported for the earliest two periods in the Summary Compensation Table below are due to two non-recurring features of those periods: First, in connection with the Orbital-ATK Merger, Mr. Thompson, and Mr. Pierce became the Company’s Chief Executive Officer and Chief Financial Officer, respectively, on February 9, 2015, less than two months before the end of the Company’s fiscal year ended March 31, 2015 (fiscal year 2015). As a result, no non-equity incentive compensation is reported for this period for legacy Orbital named executive officers and their salaries are calculated based on the last six weeks of the fiscal year. Second, the 2015T fiscal period was a shortened nine-month period resulting from the Company’s change from a March 31 fiscal year-end to a December 31 fiscal year-end. Consequently, equity grants made to the named executive officers for calendar year 2015 were made, and are reported, in the fiscal year 2015 period.
Name and Principal Position | Year (1) | Salary ($)(2) | Bonus ($) | Stock Awards ($)(3)(4)(5) | Option Awards ($)(6) | Non-equity Incentive Plan Compensation ($)(7) | Change in Pension Value and Nonqualified Deferred Compensation Earnings ($)(8) | All Other Compensation ($)(9) | Total ($) | ||||||||||||||||
David W. Thompson | 2017 | $ | 934,630 | $ | — | $ | 1,777,044 | $ | 419,979 | $ | 1,619,054 | $ | — | $ | 212,619 | $ | 4,963,326 | ||||||||
President & | 2016 | $ | 945,688 | $ | — | $ | 1,970,864 | $ | 479,991 | $ | 1,246,016 | $ | — | $ | 226,673 | $ | 4,869,232 | ||||||||
Chief Executive Officer | 2015T | $ | 669,049 | $ | — | $ | — | $ | — | $ | 1,485,669 | $ | — | $ | 44,064 | $ | 2,198,782 | ||||||||
FY2015 | $ | 111,539 | $ | — | $ | 2,072,304 | $ | 480,004 | $ | — | $ | — | $ | 14,187 | $ | 2,678,034 | |||||||||
Garrett E. Pierce | 2017 | $ | 698,655 | $ | — | $ | 846,183 | $ | 199,993 | $ | 910,703 | $ | — | $ | 129,172 | $ | 2,784,706 | ||||||||
Chief Financial Officer | 2016 | $ | 702,121 | $ | — | $ | 821,057 | $ | 199,983 | $ | 690,494 | $ | — | $ | 138,488 | $ | 2,552,143 | ||||||||
2015T | $ | 509,262 | $ | — | $ | — | $ | — | $ | 840,457 | $ | — | $ | 28,678 | $ | 1,378,397 | |||||||||
FY2015 | $ | 96,925 | $ | — | $ | 863,330 | $ | 200,008 | $ | — | $ | — | $ | 10,976 | $ | 1,171,239 | |||||||||
Blake E. Larson | 2017 | $ | 681,635 | $ | — | $ | 1,057,877 | $ | 249,986 | $ | 910,703 | $ | 254,873 | $ | 77,689 | $ | 3,232,763 | ||||||||
Chief Operating Officer | 2016 | $ | 654,231 | $ | 286,808 | $ | 944,338 | $ | 229,998 | $ | 703,209 | $ | 225,798 | $ | 67,615 | $ | 3,111,997 | ||||||||
2015T | $ | 489,836 | $ | — | $ | — | $ | — | $ | 604,434 | $ | 108,714 | $ | 119,939 | $ | 1,322,923 | |||||||||
FY2015 | $ | 467,659 | $ | 286,808 | $ | 992,908 | $ | 230,009 | $ | 465,737 | $ | 1,772,466 | $ | 125,926 | $ | 4,341,513 | |||||||||
Frank L. Culbertson | 2017 | $ | 514,235 | $ | — | $ | 422,992 | $ | 99,984 | $ | 616,680 | $ | — | $ | 89,932 | $ | 1,743,823 | ||||||||
Executive Vice President & | 2016 | $ | 495,980 | $ | — | $ | 472,088 | $ | 114,989 | $ | 477,330 | $ | — | $ | 91,322 | $ | 1,651,709 | ||||||||
President, Space Systems Group | 2015T | $ | 359,667 | $ | — | $ | — | $ | — | $ | 532,022 | $ | — | $ | 16,190 | $ | 907,879 | ||||||||
Michael A. Kahn | 2017 | $ | 530,000 | $ | — | $ | 422,992 | $ | 99,984 | $ | 641,306 | $ | 369,772 | $ | 39,163 | $ | 2,103,217 | ||||||||
Executive Vice President & | 2016 | $ | 527,885 | $ | — | $ | 472,088 | $ | 114,989 | $ | 187,221 | $ | 202,130 | $ | 44,649 | $ | 1,548,962 | ||||||||
President, Defense Systems | 2015T | $ | 392,459 | $ | — | $ | — | $ | — | $ | 347,759 | $ | 12,073 | $ | 41,057 | $ | 793,348 | ||||||||
FY2015 | $ | 455,496 | $ | 156,435 | $ | 496,376 | $ | 114,994 | $ | 362,484 | $ | 379,887 | $ | 82,255 | $ | 2,047,927 | |||||||||
(1) | The years reported are the Company's fiscal year ending December 31, 2017, the Company's fiscal year ending December 31, 2016, the nine-month transition period ending December 31, 2015, and the fiscal year ending March 31, 2015. |
(2) | Includes amounts, if any, deferred at the direction of the executive officer pursuant to the Company's 401(k) Plan or Nonqualified Deferred Compensation Plan. Also includes payments to executive officers for vacation sold under the Company's vacation buy/sell benefit program: Mr. Thompson, $34,616, Mr. Pierce, $25,577, Mr. Larson, $12,404, Mr. Culbertson, $18,462, and Mr. Kahn, $10,000. |
(3) | This column shows the aggregate grant date fair value computed in accordance with generally accepted accounting principles in the United States. For 2017, the amounts in this column for restricted stock awards and the component of the performance share awards subject to financial performance measures are calculated based on the number of shares awarded multiplied by the closing price of Orbital ATK common stock on the date of grant. The number of performance shares used to determine this aggregate fair value of |
117
the component of the award subject to revenue and return on invested capital financial metrics (50% of the total award) is based on the target payout level for the award. The fair value of the component of the awards of performance shares subject to a relative total stockholder return ("relative TSR") measure (50% of the total award) is determined by an integrated Monte Carlo simulation model. The number of performance shares used to determine the aggregate fair value of the relative TSR component of the award is based on the target payout level (amounts do not reflect the actual amounts that may vest or be earned by the executive officer). The assumptions used in calculating the aggregate grant date fair value of the awards are disclosed in Note 17 to the consolidated financial statements in this Form 10-K.
The value of the restricted stock and the value for the 2017-2019 performance shares (at target and maximum) awarded to the named executive officers during 2017 are shown separately in the table below:
2017 - 2019 Performance Shares | |||||||||||
Name | Restricted Stock | At Target | At Maximum | ||||||||
Mr. Thompson | $ | 839,907 | $ | 937,137 | $ | 1,874,274 | |||||
Mr. Pierce | $ | 399,942 | $ | 446,241 | $ | 892,482 | |||||
Mr. Larson | $ | 499,998 | $ | 557,879 | $ | 1,115,758 | |||||
Mr. Culbertson | $ | 199,924 | $ | 223,068 | $ | 446,136 | |||||
Mr. Kahn | $ | 199,924 | $ | 223,068 | $ | 446,136 |
(4) | For fiscal year 2016, the amounts in this column were calculated as noted above in footnote 3. |
The value of the restricted stock and the value for the 2016-2018 performance shares (at target and maximum) awarded to the named executive officers during 2016 are shown separately in the table below:
2016 - 2018 Performance Shares | |||||||||||
Name | Restricted Stock | At Target | At Maximum | ||||||||
Mr. Thompson | $ | 959,991 | $ | 1,010,873 | $ | 2,021,746 | |||||
Mr. Pierce | $ | 399,930 | $ | 421,127 | $ | 842,255 | |||||
Mr. Larson | $ | 459,979 | $ | 484,359 | $ | 968,718 | |||||
Mr. Culbertson | $ | 229,950 | $ | 242,138 | $ | 484,276 | |||||
Mr. Kahn | $ | 229,950 | $ | 242,138 | $ | 484,276 |
(5) | For fiscal year 2015 (FY2015), the amounts in this column were calculated as noted above in footnote 3. |
The value of the restricted stock awards and the target value for the April 1, 2015 - December 31, 2017 performance shares (at target and maximum) awarded to each of the named executive officers in fiscal year 2015 are shown separately in the table below:
2015 - 2017 Performance Shares | |||||||||||
Name | Restricted Stock | At Target | At Maximum | ||||||||
Mr. Thompson | $ | 959,983 | $ | 1,112,320 | $ | 2,224,641 | |||||
Mr. Pierce | $ | 399,933 | $ | 463,397 | $ | 926,795 | |||||
Mr. Larson | $ | 459,959 | $ | 532,949 | $ | 1,065,897 | |||||
Mr. Kahn | $ | 229,943 | $ | 266,433 | $ | 532,865 |
(6) | The amount in this column shows the aggregate grant date fair value computed in accordance with generally accepted accounting principles in the United States. The amount is based on the fair value of the stock option award as estimated using the Black-Scholes option-pricing model multiplied by the number of shares subject to the option award. The assumptions used to arrive at the Black-Scholes value are disclosed in Note 17 to the consolidated financial statements in this Form 10-K. |
(7) | The amounts in this column represent payment of annual incentive compensation for the periods noted. The annual incentive compensation program and payments for 2017 are described in the "Compensation Discussion and Analysis" in this Form 10-K. Includes amounts, if any, deferred at the direction of the executive officer pursuant to the Company's 401(k) Plan or Nonqualified Deferred Compensation Plan. |
118
(8) | The amounts in this column represent the aggregate change in the actuarial present value of the officer's accumulated retirement benefits under the Company's Pension and Retirement Plan and Defined Benefit Supplemental Executive Retirement Plan. Mr. Thompson, Mr. Pierce, and Mr. Culbertson do not participate in a defined benefit retirement plan. See the "Pension Benefits" section in this Form 10-K for additional information. No above-market or preferential earnings on any nonqualified deferred compensation was paid to the officers during the last fiscal year and, accordingly, no such amounts are reflected above. |
(9) | "All Other Compensation" amounts for 2017 consist of the following: |
Name | Dividends (1) | 401(k) Plan Contributions | DC SERP Plan Allocations | ||||||
Mr. Thompson | $ | 30,206 | $ | 22,950 | $ | 159,463 | |||
Mr. Pierce | $ | 13,268 | $ | 22,950 | $ | 92,954 | |||
Mr. Larson | $ | 15,929 | $ | 12,150 | $ | 49,610 | |||
Mr. Culbertson | $ | 7,218 | $ | 22,950 | $ | 59,764 | |||
Mr. Kahn | $ | 7,338 | $ | 12,150 | $ | 19,675 |
(1) | This amount represents cash dividend payments made to the named executive officers on unvested restricted stock awards. |
119
GRANTS OF PLAN-BASED AWARDS
The following table summarizes the grants of equity and non-equity plan-based awards made to the executive officers named in the Summary Compensation Table during the fiscal year ended December 31, 2017. The non-equity awards were granted under our Executive Officer Incentive Plan, which was approved by stockholders in 2016, and the equity awards were granted under our Stock Incentive Plan, which was approved by stockholders in 2015.
Estimated Future Payouts Under Non-Equity Incentive Plan Awards | Estimated Future Payouts Under Equity Incentive Plan Awards | All Other Stock Awards: Number of Shares of Stock or Units (#) | All Other Option Awards: Number of Securities Underlying Options (#) | Grant Date Fair Value of Stock and Option Awards ($)(6) | ||||||||||||||||||||||||
Exercise or Base Price of Option Awards ($/Share) | ||||||||||||||||||||||||||||
Name | Grant Date (1) | Incentive Award Type | Threshold ($) | Target ($) | Maximum ($) | Threshold (#) | Target (#) | Maximum (#) | ||||||||||||||||||||
David W. Thompson | 2/27/2017 | Annual (2) | $ | 405,006 | $ | 1,080,017 | $ | 1,728,028 | ||||||||||||||||||||
2/27/2017 | Long-Term Stock (3) | 2,245 | 8,982 | 17,964 | $ | 937,137 | ||||||||||||||||||||||
2/27/2017 | Restricted Stock (4) | 8,982 | $ | 839,907 | ||||||||||||||||||||||||
2/27/2017 | Stock Options (5) | 17,163 | $ | 93.51 | $ | 419,979 | ||||||||||||||||||||||
Garrett E. Pierce | 2/27/2017 | Annual (2) | $ | 227,813 | $ | 607,500 | $ | 972,000 | ||||||||||||||||||||
2/27/2017 | Long-Term Stock (3) | 1,069 | 4,277 | 8,554 | $ | 446,241 | ||||||||||||||||||||||
2/27/2017 | Restricted Stock (4) | 4,277 | $ | 399,942 | ||||||||||||||||||||||||
2/27/2017 | Stock Options (5) | 8,173 | $ | 93.51 | $ | 199,993 | ||||||||||||||||||||||
Blake E. Larson | 2/27/2017 | Annual (2) | $ | 227,813 | $ | 607,500 | $ | 972,000 | ||||||||||||||||||||
2/27/2017 | Long-Term Stock (3) | 1,336 | 5,347 | 10,694 | $ | 557,879 | ||||||||||||||||||||||
2/27/2017 | Restricted Stock (4) | 5,347 | $ | 499,998 | ||||||||||||||||||||||||
2/27/2017 | Stock Options (5) | 10,216 | $ | 93.51 | $ | 249,986 | ||||||||||||||||||||||
Frank L. Culbertson | 2/27/2017 | Annual (2) | $ | 150,000 | $ | 400,000 | $ | 640,000 | ||||||||||||||||||||
2/27/2017 | Long-Term Stock (3) | 534 | 2,138 | 4,276 | $ | 223,068 | ||||||||||||||||||||||
2/27/2017 | Restricted Stock (4) | 2,138 | $ | 199,924 | ||||||||||||||||||||||||
2/27/2017 | Stock Options (5) | 4,086 | $ | 93.51 | $ | 99,984 | ||||||||||||||||||||||
Michael A. Kahn | 2/27/2017 | Annual (2) | $ | 156,000 | $ | 416,000 | $ | 665,600 | ||||||||||||||||||||
2/27/2017 | Long-Term Stock (3) | 534 | 2,138 | 4,276 | $ | 223,068 | ||||||||||||||||||||||
2/27/2017 | Restricted Stock (4) | 2,138 | $ | 199,924 | ||||||||||||||||||||||||
2/27/2017 | Stock Options (5) | 4,086 | $ | 93.51 | $ | 99,984 | ||||||||||||||||||||||
(1) | The grant date is the date the Compensation and Human Resources Committee of the Board of Directors met and approved the awards. |
(2) | The amounts reflect the potential cash payout for the annual incentive program for the fiscal year ending December 31, 2017 if all performance measures are satisfied at the applicable level. The material terms of the award are described above in the "Compensation Discussion and Analysis" under the subheading "Annual Incentive Performance Results." See the "Non-Equity Incentive Plan Compensation" column in the Summary Compensation Table above for the amount actually earned for 2017. |
(3) | Each column in this row shows the number of shares of common stock that may be paid out for the three fiscal-year performance period beginning January 1, 2017 and ending December 31, 2019 if all performance metrics are satisfied at the applicable level. The payout will be determined after the fiscal year ending December 31, 2019. The material terms of the award are described above in the "Compensation Discussion and Analysis" under the subheading "2017 Long-Term Incentive Compensation." |
(4) | The number of shares of restricted stock shown in this row represents the actual number of shares of restricted stock granted to the named executive officers on February 27, 2017. The restricted stock shown in this row vests in three equal annual installments beginning on the first anniversary of the grant date. |
120
The shares of restricted stock shown in this row may also vest upon death, disability, involuntary termination without cause or a qualifying termination of employment following a change in control of the Company. Dividends are payable on the shares at the same rate as dividends paid on all outstanding shares of Orbital ATK common stock.
(5) | The number of stock options shown in this row represents the actual number of options granted to the named executive officers on February 27, 2017. The option exercise price is the closing sale price of a share of Orbital ATK common stock on the NYSE on the date of grant. The stock options vest in three equal annual installments starting on the first anniversary of the grant date. The options may also vest in the event of a qualifying termination of employment following a change in control of the Company. |
(6) | This column shows the full grant date fair value of the equity awards under FASB ASC Topic 718. Generally, for the long-term stock incentive awards relating to performance metrics, the full grant date fair value is the amount the Company could expense in its financial statements over the awards' performance period assuming performance is achieved at the target level. Assumptions made in the calculations of these amounts may be found in Note 17 to the consolidated financial statements in this Form 10-K. |
121
OUTSTANDING EQUITY AWARDS AT FISCAL YEAR-END
The following table shows the unexercised stock options, unvested restricted stock awards and restricted stock units, and unearned performance share awards as of December 31, 2017 by the executive officers named in the Summary Compensation Table.
Option Awards | Stock Awards | ||||||||||||||||||
Name | Grant Date (1) | Number of Securities Underlying Unexercised Options (#) Exercisable (2) | Number of Securities Underlying Unexercised Options (#) Unexercisable (2) | Equity Incentive Plan Awards: Number of Securities Underlying Unexercised Unearned Options (#) | Option Exercise Price ($) | Option Expiration Date | Number of Shares or Units of Stock That Have Not Vested (#)(3) | Market Value of Shares or Units of Stock That Have Not Vested ($)(4) | Equity Incentive Plan Awards: Number of Unearned Shares, Units or Other Rights That Have Not Vested (#)(5) | Equity Incentive Plan Awards: Market or Payout Value of Unearned Shares, Units or Other Rights That Have Not Vested ($)(4)(5) | |||||||||
David W. Thompson | 3/10/2015 | 15,594 | 7,798 | — | $ | 72.06 | 3/10/2025 | 4,441 | $583,992 | — | — | ||||||||
3/17/2016 | 7,793 | 15,587 | — | $ | 79.43 | 3/17/2026 | 8,058 | $1,059,627 | 24,172 | (6) | $ | 3,178,618 | |||||||
2/27/2017 | — | 17,163 | — | $ | 93.51 | 2/27/2027 | 8,982 | $1,181,133 | 17,964 | (7) | $ | 2,362,266 | |||||||
Garrett E. Pierce | 3/10/2015 | 6,498 | 3,249 | — | $ | 72.06 | 3/10/2025 | 1,850 | $243,275 | — | — | ||||||||
3/17/2016 | 3,247 | 6,494 | — | $ | 79.43 | 3/17/2026 | 3,357 | $441,446 | 10,070 | (6) | $ | 1,324,205 | |||||||
2/27/2017 | — | 8,173 | — | $ | 93.51 | 2/27/2027 | 4,277 | $562,426 | 8,554 | (7) | $ | 1,124,851 | |||||||
Blake E. Larson | 3/6/2012 | 7,597 | — | — | $ | 26.25 | 3/6/2022 | — | — | — | — | ||||||||
3/5/2013 | 6,094 | — | — | $ | 30.40 | 3/5/2023 | — | — | — | — | |||||||||
3/11/2014 | 2,764 | — | — | $ | 61.65 | 3/11/2024 | — | — | — | — | |||||||||
3/10/2015 | 7,472 | 3,737 | — | $ | 72.06 | 3/10/2025 | 2,128 | $279,832 | — | — | |||||||||
3/17/2016 | 3,734 | 7,469 | — | $ | 79.43 | 3/17/2026 | 3,861 | $507,722 | 11,582 | (6) | $ | 1,523,033 | |||||||
2/27/2017 | — | 10,216 | — | $ | 93.51 | 2/27/2027 | 5,347 | $703,131 | 10,694 | (7) | $ | 1,406,261 | |||||||
Frank L. Culbertson | 3/10/2015 | 3,736 | 1,868 | — | $ | 72.06 | 3/10/2025 | 1,064 | $139,916 | — | — | ||||||||
3/17/2016 | 1,867 | 3,734 | — | $ | 79.43 | 3/17/2026 | 1,930 | $253,795 | 5,790 | (6) | $ | 761,385 | |||||||
2/27/2017 | — | 4,086 | — | $ | 93.51 | 2/27/2027 | 2,138 | $281,147 | 4,276 | (7) | $ | 562,294 | |||||||
Michael A. Kahn | 3/6/2012 | 6,822 | — | — | $ | 26.25 | 3/6/2022 | — | — | — | — | ||||||||
3/5/2013 | 6,094 | — | — | $ | 30.40 | 3/5/2023 | — | — | — | — | |||||||||
3/11/2014 | 2,764 | — | — | $ | 61.65 | 3/11/2024 | — | — | — | — | |||||||||
3/10/2015 | 3,736 | 1,868 | — | $ | 72.06 | 3/10/2025 | 1,064 | $139,916 | — | — | |||||||||
3/17/2016 | 1,867 | 3,734 | — | $ | 79.43 | 3/17/2026 | 1,930 | $253,795 | 5,790 | (6) | $ | 761,385 | |||||||
2/27/2017 | — | 4,086 | — | $ | 93.51 | 2/27/2027 | 2,138 | $281,147 | 4,276 | (7) | $ | 562,294 | |||||||
(1) | For a better understanding of this table, we have included an additional column showing the grant dates of stock options, restricted stock awards, and performance share awards. |
(2) | Stock option grants vest in three equal annual installments beginning on the first anniversary of the grant date. |
(3) | Restricted stock awards vest in three equal annual installments beginning on the first anniversary of the grant date. |
(4) | The amounts in this column were calculated using a per share value of $131.50, the closing price of Company common stock as reported on the NYSE on December 29, 2017, the last trading day of the fiscal year. |
(5) | The amounts shown reflect the payout of the performance shares based on achievement at the maximum level of performance. The vesting and payout of any performance shares for the respective performance periods ending on December 31 will be determined, based on the actual achievement of specified performance goals. |
122
(6) | These shares correspond to a long-term incentive award relating to performance growth measures (relative TSR, absolute revenue growth, and return on invested capital) for the period of January 1, 2016 through December 31, 2018. |
(7) | These shares correspond to a long-term incentive award relating to performance growth measures (relative TSR, absolute revenue growth, and return on invested capital) for the period of January 1, 2017 through December 31, 2019. |
123
OPTION EXERCISES AND STOCK VESTED
The following table provides information for the executive officers named in the Summary Compensation Table regarding the exercise of stock options and the vesting of restricted stock awards, restricted stock units, and performance shares during the fiscal year ended December 31, 2017.
Option Awards | Stock Awards | ||||||||||||
Name | Number of Shares Acquired on Exercise (#) | Value Realized on Exercise ($) | Number of Shares Acquired on Vesting (#)(1)(2) | Value Realized on Vesting ($)(1)(2) | |||||||||
David W. Thompson | — | — | 35,139 | $ | 4,175,867 | ||||||||
Garrett E. Pierce | — | — | 16,323 | $ | 1,913,552 | ||||||||
Blake E. Larson | — | — | 18,037 | $ | 2,102,062 | ||||||||
Frank L. Culbertson | — | — | 9,797 | $ | 1,142,744 | ||||||||
Michael A. Kahn | — | — | 11,232 | $ | 1,268,212 |
(1) | Includes the vesting of restricted stock awards and restricted stock units. Value realized was determined by multiplying the number of vested shares or units by the closing market price of the Company's common stock on the date of vesting. If the vesting date fell on a weekend or holiday, the closing market price of the common stock on the business day immediately preceding the vesting date was used to determine the value realized. The number of shares of restricted stock awards and restricted stock units that vested for each of the officers is as follows: |
Name | Vesting Date | Number of Shares | |
Mr. Thompson | 3/10/2017 | 4,441 | |
3/17/2017 | 4,028 | ||
7/21/2017 | 6,735 | ||
Mr. Pierce | 3/10/2017 | 1,850 | |
3/17/2017 | 1,678 | ||
7/21/2017 | 4,490 | ||
Mr. Larson | 3/10/2017 | 2,128 | |
3/11/2017 | 375 | ||
3/17/2017 | 1,930 | ||
3/31/2017 | 4,053 | ||
Mr. Culbertson | 3/10/2017 | 1,064 | |
3/17/2017 | 965 | ||
7/21/2017 | 2,993 | ||
Mr. Kahn | 3/10/2017 | 1,064 | |
3/11/2017 | 375 | ||
3/17/2017 | 965 | ||
3/31/2017 | 4,053 | ||
Upon vesting of each award, the Company withheld shares of Company common stock from each officer having a value equal to the applicable tax withholding requirement.
(2) | Includes the payment of performance shares which vested on December 31, 2017 upon subsequent confirmation of the Compensation and Human Resources Committee that performance goals had been achieved, as described in the “Compensation Discussion and Analysis” section of this Form 10-K under the subheading “Long-Term Incentive Compensation Payouts.” The value realized was determined by multiplying the number of vested shares by the closing market price of Orbital ATK common stock on February 21, 2018, the payment date, which was $131.80. The number of performance shares that vested for each of the officers is as follows: |
124
Name | Number of Shares | |
Mr. Thompson | 19,935 | |
Mr. Pierce | 8,305 | |
Mr. Larson | 9,551 | |
Mr. Culbertson | 4,775 | |
Mr. Kahn | 4,775 | |
Mr. Thompson deferred 40% of his performance shares that were earned. As a result of the deferral, and in lieu of payment of the shares, Mr. Thompson’s account under Orbital ATK’s Nonqualified Deferred Compensation Plan was credited with deferred stock units. The number of units credited to the account was determined on a one-for-one basis equal to the number of shares that would otherwise have been paid, reduced by the number of shares having a value equal to Orbital ATK’s Medicare tax withholding obligation as a result of the deferral of payment of the shares. The deferred stock units will be settled 100% in Orbital ATK common stock following termination of employment or such other date specified by the officer under the terms of the Nonqualified Deferred Compensation Plan.
125
PENSION BENEFITS
Orbital ATK maintains two tax-qualified defined benefit retirement plans covering fewer than half of our employees. These plans were closed to new participants as of January 1, 2007 (and at later dates for certain employees covered by collective bargaining agreements). Of the named executive officers, two participated in a defined benefit plan during the fiscal year ended December 31, 2017: Mr. Larson and Mr. Kahn. Their benefits are described below. The named executive officers who do not participate in a defined benefit plan (Mr. Thompson, Mr. Pierce, and Mr. Culbertson) instead participated in the Orbital ATK defined contribution plan. The Company’s contributions for these named executive officers are included in the Summary Compensation Table under the column "All Other Compensation."
The Internal Revenue Code limits the benefits that may be paid from such tax-qualified plans. The Orbital ATK, Inc. Defined Benefit Supplemental Executive Retirement Plan (the "DB SERP") was established to provide benefits for highly compensated employees whose tax-qualified defined benefit plan benefits are reduced by certain IRS limits or by their participation in the Company's Nonqualified Deferred Compensation Plan. A grantor trust was established under which certain funds have been set aside to satisfy some of the obligations under the DB SERP. If the funds in the trust are insufficient to pay amounts payable under the DB SERP, the Company will pay the deficiency. Mr. Larson and Mr. Kahn participate in the DB SERP. The Company also sponsors the Orbital ATK, Inc. Defined Contribution Supplemental Executive Retirement Plan (the "DC SERP"). All of the named executive officers participated in the DC SERP during 2017. Amounts allocated by the Company under the DC SERP are included in the Summary Compensation Table under the column "All Other Compensation" and are also shown in the table under the heading "Nonqualified Deferred Compensation" in this Form 10-K.
Orbital ATK, Inc. Pension and Retirement Plan and Thiokol Propulsion Pension Plan
Due to acquisitions and benefit plan mergers, the Orbital ATK, Inc. Pension and Retirement Plan (the "Pension Plan"), and the Thiokol Propulsion Pension Plan (the "Thiokol Plan") contain various benefit formulas that apply to certain groups of employees. The benefit formulas that applied prior to July 1, 2013 to the two named executive officers who were participants in a defined benefit plan at that time were the following:
• | Mr. Larson - the old Cash Balance formula under the Pension Plan, |
• | Mr. Kahn - the Thiokol Pension Plan formula under the Thiokol Plan. |
Since July 1, 2013, the pension benefit is calculated in two pieces: the benefit earned as of June 30, 2013 under the prior formula and the benefit earned under a new Cash Balance formula for service and earnings beginning July 1, 2013. Mr. Larson and Mr. Kahn began earning benefits under the new Cash Balance formula effective July 1, 2013.
Each portion of the pension benefit will be payable separately. Different payment forms and commencement dates may be elected for the different pieces of the benefit. The elements of compensation used in applying the various payment and benefit formulas generally include base salary plus annual incentive payments (actually paid through the month of termination of employment, or June 30, 2013, in the case of benefits under the frozen formulas), up to the applicable IRS maximum compensation limit. Historically, employees were vested after five years of vesting service. On January 1, 2008, vesting under the old Cash Balance formula changed to three years of vesting service. Effective July 1, 2013, all impacted employees who transitioned to the new Cash Balance formula became 100% vested in their entire pension benefit regardless of their years of vesting service. Mr. Larson and Mr. Kahn participated in a defined benefit plan during 2017 and are vested in their respective Pension Plan or Thiokol Plan benefits. The normal retirement age for the plan is defined in the Pension Plan as age 65. The normal retirement age is defined in the Thiokol Plan as age 67.
New Cash Balance Formula - Effective for All Participants as of July 1, 2013
Effective July 1, 2013, the pension plan formulas were amended to provide benefits based on a new Cash Balance formula. The new Cash Balance formula provides pay and interest credits to all eligible participants. The pay credit is based on a percentage of eligible earnings received after July 1, 2013. The pay credit percentage is based on age plus Pension Service. Pension Service includes prior formula service to June 30, 2013 and service after July 1, 2013 (measured in whole years) at the end of each calendar year.
126
Age Plus Years of Pension Service | Percentage of Eligible Pay |
Less than 40 | 2.5% |
From 40 to 59 | 3.0% |
60 or more | 4.0% |
Cash Balance accounts are credited annually with pay and interest credits. The annual interest crediting rate is 4% and applies to the beginning of year account balance. Interest credits after termination continue to apply until benefit commencement date.
After termination of employment, a participant's vested account balance may be distributed immediately to a participant regardless of age in a variety of actuarially equivalent monthly annuity payment forms or as a lump sum payment. The interest rate and mortality table used to convert the cash balance account to a monthly annuity are based on the IRS prescribed assumptions for lump sum benefits (Section 417(e) of the Internal Revenue Code) in effect at the time the benefit commences.
Defined Benefit Plan Formulas Prior to July 1, 2013
Old Cash Balance Formula (Mr. Larson)
Effective April 1, 1992, the pension plan formula then in effect was amended to provide benefits based upon a Cash Balance formula (referred to as the "old" Cash Balance formula). The old Cash Balance formula continued through June 30, 2013 to apply to employees who were participants in the pension plan as of April 1, 1992, or were hired after April 1, 1992 and not covered by one of the subsequently acquired plan formulas, but who had at least 15 years of credited service as of December 31, 2003. Effective June 30, 2013, pay credits under this old Cash Balance Formula ended. Mr. Larson's initial cash balance account was equal to the lump sum value as of April 1, 1992 of his accrued benefit under the prior pension plan formula at that time. Mr. Larson's cash balance account was credited monthly with a percentage of pension earnings that increased with length of service as follows:
Years of Service | Percentage of Pension Earnings | Additional Percentage for Earnings in Excess of Social Security Wage Base | ||
Less than 5 | 3.5% | 3.5% | ||
5 to 9 | 4.5% | 4.5% | ||
10 to 14 | 5.5% | 5.5% | ||
15 to 19 | 6.5% | 5.5% | ||
20 to 24 | 7.5% | 5.5% | ||
25 or more | 8.5% | 5.5% |
The pay credits applied to the old cash balance accounts ended on June 30, 2013. The account balances continue to be credited monthly with interest credits equal to one-twelfth of the average one-year U.S. Treasury Bill rate during the 12 months ending September 30 of the prior calendar year. The minimum annual interest crediting rate is 3.06%. For calendar year 2017, the interest crediting rate is 3.06%.
The old Cash Balance formula benefit (frozen as of June 30, 2013) is not less than the lump sum equivalent of a monthly benefit of $47.50 multiplied by years of credited service as of June 30, 2013 payable at age 65.
At retirement, which may occur at or after age 55, a participant's vested old Cash Balance account may be payable as a monthly annuity or an annuity with a lump sum payment at age 62 or, if commencement of benefits occurs at or after age 62, as an optional lump sum payment. The interest rate and mortality table used to convert the old cash balance account to a monthly annuity are based on the IRS prescribed assumptions for lump sum benefits (Section 417(e) of the Internal Revenue Code) in effect at the time the benefit commences and early or late retirement age adjustment factors as specified in the plan. Participants who terminate employment before age 55 may receive a lump sum payment at age 65.
127
Thiokol Pension Plan Formula (Mr. Kahn)
The Thiokol Plan formula covers employees who had at least 15 years of credited service as of December 31, 2003 and who joined the Company in connection with the acquisition of Thiokol from Alcoa or began employment in a location offering this formula.
The Thiokol Plan provides an annuity benefit determined based on final average earnings and the participant’s years of credited service. Effective June 30, 2013, benefit accruals under this formula were frozen for the impacted participants. The frozen benefit is equal to:
• | 1.23% of final average earnings multiplied by years of credited service; plus |
• | 0.75% of final average earnings in excess of social security covered compensation, multiplied by years of credited service (up to a maximum of 35 years). |
Final average earnings, social security covered compensation and credited service are all frozen as of June 30, 2013. Final average earnings as of June 30, 2013 is determined as the greater of the final average earnings determined as of December 31, 2012 (using actual calendar year earnings) or the amount determined using actual earnings for the 60 month period from July 1, 2008 to June 30, 2013.
Benefits are paid in a variety of actuarially equivalent monthly annuity options at retirement.
Participants with at least five years of credited service may retire early with a reduced benefit on or after age 55. The benefits of participants electing early retirement are reduced according to plan factors for benefit commencement prior to age 67 (6.67% for each of the first five years, 3.33% for each of the next five years, 4.13% for the next year, and 3.74% for the year after that). As it relates to the frozen benefit, service with the Company after July 1, 2013 will be included when determining eligibility for early retirement.
Defined Benefit Supplemental Executive Retirement Plan
The DB SERP provides benefits for highly compensated employees whose tax-qualified defined benefit plan benefits are reduced by certain IRS limits or by their participation in the Company's Nonqualified Deferred Compensation Plan. The IRS annual salary limitation (Section 401(a)(17) of the Internal Revenue Code) and certain other IRS requirements restrict pension benefits from tax-qualified pension plans for certain highly compensated employees. The DB SERP is designed to offset these limitations.
The applicable benefits from the DB SERP are generally based on the same benefit formula and provisions as the underlying qualified plan formula that applies to the participant. Effective July 1, 2013, the benefit formula for future accruals under the DB SERP changed to the new Cash Balance formula. The DB SERP benefit after July 1, 2013 consists of the frozen SERP benefit earned under the prior formula as of June 30, 2013 and the SERP benefit earned under the new Cash Balance formula after that date. The DB SERP benefits are paid in a lump sum the later of six months or February 1 following the calendar year of termination of employment or separation of service (as defined by Section 409A of the Internal Revenue Code), including interest (at the greater of 6% or the rate specified in the qualified pension plan for determining lump sum payments) from the first day of the month following termination to the actual payment date. The DB SERP benefit is converted to a lump sum payment based on an annual interest rate that is the greater of 6% or the rate specified in the qualified pension plan for determining lump sum payments, except for formulas which already determine the benefit as a lump sum amount.
Employees vest in the DB SERP benefits at the same time their benefits vest under the qualified pension plan.
The DB SERP provides certain executives covered by the old Cash Balance formula with the right to receive a benefit based on the greater of the Pension Equity Plan (“PEP”) formula or the old Cash Balance formula through June 30, 2013 provided they remain employed until at least age 55 and receive a benefit under the new Cash Balance formula in effect July 1, 2013. This provision applies to Mr. Larson since he has attained age 55 and the benefit amount is reflected in the table below. The PEP formula is included in the Pension Plan. The frozen PEP formula calculates benefits as a lump sum amount equal to 5.5% of final average earnings up to one-half of the social security wage base, plus 11% of final average earnings in excess of one-half of the social security wage base multiplied by years of credited service. Final average earnings for the PEP formula is equal to the average of the highest 60 consecutive months out of the last 120 months of earnings as of June 30, 2013. The social security wage base as of June 30, 2013 was $113,700. The June 30, 2013 frozen PEP amount is increased on a monthly basis by interest at a rate of 4% (compounded annually) until the benefit commencement date.
128
Pension Benefits
The following table provides information concerning each defined benefit plan of the Company that provides for payments or benefits to any of the named executive officers.
Name | Plan Name | Number of Years Pension Service (1) | Present Value of Accumulated Benefits ($) | Payments During Last Fiscal Year ($) | ||
Blake E. Larson | Pension Plan | 36.500 | 680,347 | — | ||
DB SERP | 36.500 | 2,837,997 | — | |||
Michael A. Kahn | Thiokol Plan | 29.167 | 1,088,474 | — | ||
DB SERP | 29.167 | 1,976,035 | — |
(1)Pension Service is determined in years and months as of December 31, 2017.
Assumptions
The "Present Value of Accumulated Benefits" is based on the same assumptions as those used for the valuation of the plan liabilities in this Form 10-K. The assumptions made in the calculations of these amounts may be found in Note 13 to the audited financial statements in this Form 10-K.
The old Cash Balance formula benefits are projected from the current account value to age 65 assuming that the interest crediting rate is 3.5% for years after 2017. Retirement age is assumed to be age 65, except for Mr. Kahn’s benefits. For Mr. Kahn, age 67 is used since this is the unreduced retirement age for the Thiokol Plan formula. The assumption is made that there is no probability of pre-retirement death or termination by any other cause.
All SERP benefits are assumed to be paid as a lump sum in accordance with the plan document.
"Pension Service" includes only service with the Company (or certain acquired employers). In general, the Company does not grant extra years of pension service.
129
NONQUALIFIED DEFERRED COMPENSATION
The following table provides information for the executive officers named in the Summary Compensation Table regarding contributions, earnings, distributions and year-end account balances with respect to the contributions to the Orbital ATK, Inc. Nonqualified Deferred Compensation Plan (the "Deferred Compensation Plan"), the Orbital Sciences Corporation Nonqualified Management Deferred Compensation Plan (the "Orbital Deferred Compensation Plan"), and the Orbital ATK Inc. Defined Contribution Supplemental Executive Retirement Plan (the "DC SERP").
Name | Plan Name | Executive Contributions in Last Fiscal Year ($)(1) | Registrant Contributions in Last Fiscal Year ($) | Aggregate Earnings in Last Fiscal Year ($) | Aggregate Withdrawals/ Distributions in Last Fiscal Year ($) | Aggregate Balance at Last Fiscal Year End ($)(2) | ||||||||||
David W. Thompson | Deferred Compensation Plan | $ | 588,408 | $ | — | $ | 72,414 | $ | — | $ | 850,702 | |||||
Orbital Deferred Compensation Plan | $ | — | $ | — | $ | 596,544 | $ | — | $ | 6,094,449 | ||||||
DC SERP | $ | — | $ | 159,463 | $ | 17,185 | $ | — | $ | 357,928 | ||||||
Garrett E. Pierce | Deferred Compensation Plan | $ | — | $ | — | $ | — | $ | — | $ | — | |||||
Orbital Deferred Compensation Plan | $ | — | $ | — | $ | 29,030 | $ | — | $ | 195,244 | ||||||
DC SERP | $ | — | $ | 92,954 | $ | 8,136 | $ | — | $ | 207,526 | ||||||
Blake E. Larson | Deferred Compensation Plan | $ | — | $ | — | $ | 87,012 | $ | — | $ | 909,509 | |||||
DC SERP | $ | — | $ | 49,610 | $ | 17,577 | $ | — | $ | 193,743 | ||||||
Frank L. Culbertson | Deferred Compensation Plan | $ | — | $ | — | $ | — | $ | — | $ | — | |||||
Orbital Deferred Compensation Plan | $ | — | $ | — | $ | 2,221 | $ | — | $ | 22,686 | ||||||
DC SERP | $ | — | $ | 59,764 | $ | 4,840 | $ | — | $ | 127,923 | ||||||
Michael A. Kahn | Deferred Compensation Plan | $ | — | $ | — | $ | 62,817 | $ | — | $ | 845,352 | |||||
DC SERP | $ | — | $ | 19,675 | $ | 13,928 | $ | — | $ | 131,474 |
(1) | This column does not include the deferral by Mr. Thompson of the portion of his performance award earned for the 2015-2017 performance period ended December 31, 2017 because that amount was not actually credited to his account until fiscal year 2018. |
(2) | For Messrs. Larson and Kahn, the amounts in the following table represent aggregate contributions made by the executive officer or by the Company for the benefit of the executive officer, since the officer's commencement of participation in the plan(s) through December 31, 2017. Deferrals and contributions in prior years were previously reported as compensation in the Summary Compensation Table in the Company's proxy statement for the applicable years for those officers who were named in the Summary Compensation Table in those years. For Messrs. Thompson, Pierce and Culbertson, amounts in the following table represent aggregate contributions since the beginning of their employment with the Company on February 9, 2015. The aggregate earnings represent the cumulative earnings on the original deferred amounts. There have been no distributions/withdrawals made to the named executive officers through December 31, 2017. |
Detail of Aggregate Balances at Last Fiscal Year End
Executive Contributions | Registrant Contributions | ||||||||||||||||||||||||
Name | Salary Deferrals ($) | Annual Cash Incentive Deferrals ($) | Performance Share Deferrals ($) | Allocations to Orbital Deferred Compensation Plan ($) | Allocations to DC SERP ($) | Aggregate Earnings ($) | Withdrawals ($) | Balance ($) | |||||||||||||||||
Mr. Thompson | $ | 770,815 | $ | — | $ | — | $ | 23,882 | $ | 340,742 | $ | 1,242,248 | $ | — | $ | 7,303,079 | |||||||||
Mr. Pierce | $ | — | $ | — | $ | — | $ | 16,964 | $ | 199,390 | $ | 47,755 | $ | — | $ | 402,770 | |||||||||
Mr. Larson | $ | — | $ | 308,888 | $ | — | $ | — | $ | 174,994 | $ | 619,370 | $ | — | $ | 1,103,252 | |||||||||
Mr. Culbertson | $ | — | $ | — | $ | — | $ | 4,269 | $ | 123,082 | $ | 7,704 | $ | — | $ | 150,609 | |||||||||
Mr. Kahn | $ | 10,209 | $ | 363,269 | $ | — | $ | — | $ | 113,132 | $ | 490,216 | $ | — | $ | 976,826 |
Deferred Compensation Plan
All of the named executive officers are eligible to participate in the Deferred Compensation Plan. Participants in the plan generally may elect to defer up to 70% of salary and 100% of cash or equity incentive compensation.
130
The Company may credit to participants' accounts under the plan certain additional amounts relating to foregone matching contributions under the Company's 401(k) Plan. Under the Deferred Compensation Plan, the Company may also make additional discretionary contributions to participants' accounts.
The plan is an unfunded plan, meaning that participants' accounts are bookkeeping entries only and do not entitle them to ownership of any actual assets. The accounts represent an unsecured promise by the Company to pay participants benefits in the future. However, the Company has established a nonqualified grantor trust commonly known as a "Rabbi Trust." The assets of the Rabbi Trust will be used to pay benefits, but the assets of the Trust remain subject to the claims of the Company's general creditors.
Participants' account balances are credited with earnings and investment gains and losses by assuming that the deferred amounts were invested in one or more investment funds made available by the Company from time to time under the plan. The investment alternatives include funds with different degrees of risk and, for amounts credited before January 1, 2005, include Company common stock as an investment alternative. Participants select their measuring investments from among the investment alternatives provided and may reallocate amounts among the various investment alternatives at any time, except for amounts credited to the Company common stock investment alternative. After January 1, 2005, only deferrals of equity performance awards may be credited to, and must remain credited to, the Orbital ATK common stock investment alternative. Amounts allocated to the Orbital ATK common stock investment alternative are credited with dividend equivalents in the form of additional deferred stock units, based on the closing sale price of Orbital ATK common stock as reported on the NYSE on the dividend payment dates. Dividend equivalents are credited at the same rate as cash dividends paid on Orbital ATK's common stock.
The investment alternatives during 2017 were based on funds which generally corresponded to the investment funds made available under the Company's 401(k) Plan.
Generally, payouts from the plan cannot be made until the participant terminates employment, becomes totally and permanently disabled, has an unforeseeable financial emergency or reaches the date of a scheduled distribution elected by the participant under rules specified in the plan. A participant may request a distribution of amounts deferred before January 1, 2005, subject to the forfeiture of 10% of the amount withdrawn. Payouts may commence as soon as practicable following the occurrence of a distribution event; however, for amounts deferred after 2004, a payout cannot begin until six months after termination or separation of service (as defined by Section 409A of the Internal Revenue Code) for certain participants. Payouts are made in cash, except with respect to deferrals of equity performance awards after January 1, 2005, which are paid in shares of Orbital ATK common stock equal to the number of shares that were deferred, plus additional deferred stock units credited to the participants' accounts as a result of the deemed reinvestment of dividend equivalents with respect to the deferred shares. In addition, any Vista Outdoor Inc. ("Vista") deferred stock units that have been credited to a participant's account will be settled in shares of Vista common stock on a one-for-one basis. Vista phantom stock units will be paid in cash. For deferrals made on or after January 1, 2005, payouts are made in a lump sum or, in the case of retirement, in either a lump sum or in annual installments of up to 15 years as elected by the participant.
Orbital Deferred Compensation Plan
The Orbital Deferred Compensation Plan was assumed by the Company in connection with the Orbital-ATK Merger and is applicable to eligible legacy Orbital employees, including Mr. Thompson, Mr. Pierce and Mr. Culbertson. The plan was frozen to future contributions for plan years commencing January 1, 2016. The plan provided executive officers and other key management and highly compensated employees with the ability to set aside compensation on a tax-deferred basis. This compensation consisted of amounts a participant elected to defer and/or discretionary contributions by the Company. Under the plan, the participants deferred up to 100% of their cash base salaries and up to 100% of their cash bonuses.
The participants have the right to allocate amounts credited to their plan account to one or more measuring investments made available by the plan administrator. The participants may change these allocations on a daily basis by contacting the plan administrator by phone or accessing their plan account online through the plan administrator's website.
Benefits under the plan will be distributed under the terms elected by the employee. For each deferral year and type of deferral, the participant elected either a future in-service withdrawal date or a distribution upon a voluntary or involuntary termination of employment. The participant also elected to receive the distributions either as a lump sum payment or in annual installments. In the event a participant dies while employed by Orbital ATK, benefits will be
131
paid to the participant's beneficiaries in the same manner as elected by such participant. Additionally, upon a showing of an unforeseen financial hardship and with appropriate approval from the Compensation and Human Resources Committee, a participant may be allowed to access funds in the participant's plan account earlier than the elected distribution date. Mr. Thompson Mr. Pierce and Mr. Culbertson are fully vested in their account balances under the plan.
Defined Contribution Supplemental Executive Retirement Plan
The DC SERP is a nonqualified defined contribution plan under which the Company and its subsidiaries that sponsor the DC SERP may credit pre-tax contributions to a participant's account. Participation in the DC SERP is limited to (1) employees who are eligible for a non-elective contribution ("NEC") under the 401(k) Plan and (2) beginning July 1, 2013, employees who receive eligible compensation in excess of the IRS annual compensation limit and make the maximum allowable before-tax or Roth 401(k) contributions to the 401(k) Plan. An annual NEC allocation of 2.5% to 4.0% of compensation in excess of the IRS limits for a plan year will be made to a participant's account if: (i) the employee is a participant in the 401(k) Plan and the employee's NEC to the 401(k) Plan for the plan year is reduced by the annual compensation limit imposed by the Internal Revenue Code or (ii) the employee is a participant in both the 401(k) Plan and the Nonqualified Deferred Compensation Plan and the employee's NEC to the 401(k) Plan for the plan year is reduced due to the employee's deferrals to the Nonqualified Deferred Compensation Plan. Additionally, an annual match allocation of 4.5% of compensation in excess of the IRS compensation limit will be made to a participant's account if the participant has made the maximum allowable before-tax or Roth 401(k) contributions to the 401(k) Plan for the calendar year.
Vesting for the NEC allocation under the DC SERP occurs following three years of vesting service and vesting for the match allocation under the DC SERP occurs following one year of vesting service. A participant becomes fully vested upon death, attainment of age 65, total disability while employed by the Company, or upon a change in control.
The DC SERP is an unfunded plan, meaning that participants' accounts are bookkeeping entries only and do not entitle them to ownership of any actual assets. The accounts represent an unsecured promise by the Company to pay participants benefits in the future.
Participants' account balances are credited with earnings and investment gains and losses by assuming that the allocations were invested in one or more investment funds made available by the Company from time to time under the plan. The measuring investments have different degrees of risk. Participants select their measuring investments from among the investment alternatives provided and may reallocate amounts among the various investment alternatives at any time. The investment alternatives corresponded to the investment funds made available under the Company's 401(k) Plan.
The DC SERP benefit is paid as a lump sum on the later of the first day of the seventh month following termination of employment or February 1st of the calendar year following the calendar year of termination of employment.
132
POTENTIAL PAYMENTS UPON TERMINATION OR CHANGE IN CONTROL
Payments Made Upon Voluntary or Involuntary Termination
If the employment of any of the named executive officers is voluntarily or involuntarily terminated (other than retirement or involuntary termination without cause, as described below), no additional payments or benefits will accrue or be paid to the individual, other than what has been accrued and vested in the benefit plans discussed above in this Form 10-K under the headings "Summary Compensation Table," "Pension Benefits," and "Nonqualified Deferred Compensation." A voluntary or involuntary termination will not trigger an acceleration of the vesting of any stock options.
Payments Made Upon Retirement
Upon retirement of a named executive officer, the officer would be eligible for:
• | A prorated amount of the executive officer's annual incentive award, payable at the end of the performance period. The payment would be based on actual performance measured following the end of the performance period and would be prorated for the period of employment, provided the officer completed at least 90 days of employment in the performance period. |
• | Stock options generally are exercisable for three years to the extent exercisable on the date of retirement, but may not be exercised later than the expiration date of the stock options. |
• | Any outstanding performance share awards would be paid at the end of the performance period based on the actual performance measured following the end of the performance period and would be prorated for the period of active service during the performance period. |
• | Shares of restricted stock and restricted stock units would be forfeited. |
If a named executive officer covered under the Company's Defined Benefit Supplemental Executive Retirement Plan (the "DB SERP") or the Company's Defined Contribution Supplemental Executive Retirement Plan (the "DC SERP") engages in certain specific activities before payment of the supplemental executive retirement plan benefit, the executive will forfeit the benefit provided under the Plan. The DB SERP is described above in this Form 10-K under the heading "Pension Benefits" and the DC SERP is described above in this Form 10-K under the heading "Nonqualified Deferred Compensation."
Payments Made Upon Involuntary Termination Without Cause
If the employment of any of the named executive officers is terminated by Orbital ATK for convenience or a reduction in force due to lack of business or reorganization, the officer would be eligible for:
• | A lump sum payout equal to 12 months base salary. |
• | A prorated amount of the executive officer's annual incentive award, payable at the end of the performance period. The payment would be based on actual performance measured following the end of the performance period and would be prorated for the period of employment, provided the officer completed at least 90 days of employment in the performance period. |
• | An additional $25,000 to defray health care costs. |
In return, the officer is required to execute a general release of claims against Orbital ATK and agree to confidentiality, non-compete, non-solicitation and non-disparagement provisions for the one-year severance period. If a breach of any of these post-employment restrictions occurs, Orbital ATK is entitled to stop payment on the severance benefit and recover payments already made.
In the event of an involuntary termination without cause, of any of the named executive officers, our standard award agreements provide as follows:
• | Stock options generally are exercisable for three years following such termination of employment to the extent exercisable on the date of termination, but may not be exercised later than the expiration date of the stock options. |
• | Shares of restricted stock and restricted stock units would immediately vest. |
• | Any outstanding performance share awards would be paid at the end of the performance period based on the actual performance measured following the end of the performance period and would be prorated for the period of active service during the performance period. |
133
The amounts of these payments are shown in the table below titled "Potential Payments Upon Termination."
Payments Made Upon Disability
If the employment of any of the named executive officers is terminated due to disability, the following provisions would apply:
• | A prorated amount of the executive officer's annual incentive award, payable at the end of the performance period would be paid based on actual performance measured following the end of the performance period and prorated for the period of employment, provided the officer completed at least 90 days of employment in the performance period. |
• | Stock options generally are exercisable for three years following such termination of employment to the extent exercisable on the date of termination, but may not be exercised later than the expiration date of the stock options. |
• | Shares of restricted stock and restricted stock units would immediately vest. |
• | Any outstanding performance share awards would be paid at the end of the performance period based on the actual performance measured following the end of the performance period and would be prorated for the period of active service during the performance period. |
The amounts of these payments are shown in the table below titled "Potential Payments Upon Termination."
Payments Made Upon Death
If any of the named executive officers dies, the treatment of awards is similar to that outlined above for termination due to disability, except with respect to any outstanding performance share awards. Outstanding performance share awards would be paid to the officer's estate as soon as administratively possible at the threshold performance level for the applicable performance period. The payment would be prorated for the period of active service during the performance period.
The amounts of these payments are shown in the table below titled "Potential Payments Upon Termination."
Potential Payments Upon Termination Following a Change in Control
The purpose of the Company's Income Security Plan is to provide income security protection to certain executives of Orbital ATK in the event of a "qualifying termination" following a change in control of Orbital ATK. Generally, a "qualifying termination" is an involuntary termination of employment without "cause" or a voluntary termination of employment for "good reason." For purposes of the Income Security Plan, a "change in control" includes:
• | An acquisition of 40% or more of the voting power of securities entitled to vote in the election of directors; |
• | The consummation of a reorganization, merger, asset sale, or other transaction that results in existing stockholders owning less than 60% of the Company's outstanding voting securities; |
• | A change in a majority of the incumbent directors (including directors approved by a majority of the incumbents); |
• | Approval by the stockholders of a complete liquidation or dissolution of the Company; or |
• | Any other circumstance which the Board determines to be a change in control for purposes of this plan after giving due consideration to the nature of the circumstances then presented. |
On May 5, 2015, the Company adopted the Orbital ATK, Inc. Income Security Plan ("2015 ISP"), freezing the Company's former plan ("2013 ISP) to new participants. The 2013 ISP terminated on February 9, 2018. As of December 31, 2017, all of the named executive officers were covered under the 2013 ISP.
The amounts of the payments that would be made to the current executive officers named in the Summary Compensation Table if a "qualifying termination" occurred on December 31, 2017 are shown in the table below titled "Potential Payments Upon Termination."
Plan Provisions under the 2013 ISP
Participation in the plan was limited to "executive officers" of Orbital ATK (as that term is defined in Rule 3b-7 under the Securities Exchange Act of 1934) and any employee selected by the Compensation and Human Resources
134
Committee prior to May 5, 2015. Within the plan, participants were divided into two tiers with different levels of payments and benefits:
• | "Tier 1 Participants," who, as of December 31, 2017, were Orbital ATK's President and Chief Executive Officer, Chief Financial Officer, Chief Operating Officer, and Senior Vice President and General Counsel; and |
• | "Tier 2 Participants," who, as of December 31, 2017, were all other "executive officers" and any employee selected by the Committee to participate in the plan for the fiscal year. |
The plan did not have a tax gross-up provision, and the plan capped the benefits provided under the plan at the limit established under Section 280G of the Internal Revenue Code in order to avoid the imposition of the excise tax provided by Section 4999 of the Code.
In the event of a "qualifying termination," as defined in the Income Security Plan, each participant in the plan would have received:
• | Base salary and other compensation earned through the date of termination to the extent not already paid; |
• | A prorated portion of the annual cash incentive payment for which the participant was eligible for the fiscal year in which the termination occurred, calculated based on (a) the target level of performance if the termination occurred within the first three quarters of the fiscal year or (b) the greater of projected performance or target performance if the termination occurred within the fourth quarter of the fiscal year; |
• | Immediate full vesting of any outstanding stock awards, other than performance vesting stock awards; |
• | Payment of outstanding performance vesting stock awards and long-term cash incentive plan awards at the target level of performance; and |
• | Payment for reasonable legal fees and expenses incurred in good faith by the participant to obtain benefits if Orbital ATK does not pay benefits under the plan. |
In the event a Tier 1 Participant had a "qualifying termination" within the first five years of service in his or her specific Tier 1 officer position, the Tier 1 Participant would have also received:
• | A cash payment equal to three times the participant's annual base salary and current annual cash incentive opportunity for which the participant was eligible, assuming the target level of performance had been achieved; |
• | A cash payment equal to three times the maximum 401(k) Plan match the participant would have received for the calendar year in which the termination occurs; |
• | A cash payment equal to the value of benefits that Orbital ATK would have provided to the participant under Orbital ATK's group health plan for a period of three years following termination; and |
• | An additional supplemental retirement benefit equal to the increased benefit that the participant would have received under the DB SERP and/or DC SERP that would have occurred if: (1) the additional age and service would have been credited during the three-year period following the date of the termination, based on the current base salary and payments received under any annual incentive plan during the year preceding termination for the purpose of calculating recognizable compensation, and (2) the participant had contributed the maximum amounts allowable for before-tax or Roth 401(k) contributions to the 401(k) Plan during the three-year period following the date of termination. |
After five years of service in the specific Tier 1 officer position, each element of compensation payable to a Tier 1 Participant that was multiplied by three, as described above, would have been reduced by an increment of 0.2 on each of the fifth through ninth anniversaries of the date of service in that position, for a total decrease from three times compensation to two times compensation over that five-year period. Effective December 31, 2017, the multiple for each of Mr. Thompson, Mr. Pierce and Mr. Larson was three.
Tier 2 Participants would have also received:
• | A cash payment equal to two times the participant's annual base salary and current annual cash incentive amount opportunity for which the participant is eligible, assuming the target level of performance had been achieved; |
135
• | A cash payment equal to two times the maximum 401(k) Plan match the participant would have received for the calendar year in which the termination occurs; |
• | A cash payment equal to the value of benefits that Orbital ATK would have provided to the participant under Orbital ATK's group health plan for a period of two years following termination; and |
An additional supplemental retirement benefit equal to the increased benefit that the participant would have received under the DB SERP and/or DC SERP that would have occurred if: (1) the additional age and service would have been credited during the two-year period following the date of termination, based on the current base salary and payments received under any annual incentive plan during the year preceding termination for the purpose of calculating recognizable compensation, and (2) the participant had contributed the maximum amounts allowable for before-tax or Roth 401(k) contributions to the 401(k) Plan during the two-year period following the date of termination.
Plan Provisions under the 2015 ISP
Participation in the plan is limited to "executive officers" of Orbital ATK (as that term is defined in Rule 3b-7 under the Securities Exchange Act of 1934) and any employee selected by the Compensation and Human Resources Committee since May 5, 2015.
• | A cash payment equal to two times the participant's annual base salary and current annual cash incentive amount opportunity for which the participant is eligible, assuming the target level of performance had been achieved; |
• | A prorated portion of the annual cash incentive payment for which the participant is eligible for the fiscal year in which the termination occurs, calculated based on the target level of performance; |
• | A cash payment equal to the cash amount the participant would receive under any Long-Term Cash Incentive Plan assuming target performance had been achieved; |
• | Immediate full vesting of any outstanding stock awards, other than performance vesting stock awards; |
• | Payment of outstanding performance vesting stock awards and long-term cash incentive plan awards at the target level of performance; and |
• | A cash payment equal to the value of benefits that Orbital ATK would have provided to the participant under Orbital ATK's group health plan for a period of two years following termination. |
All cash payments described in the 2015 ISP above will be paid in a lump sum not later than the 15th day of the third calendar month following the date of a participant's "qualifying termination." The supplemental retirement benefit is paid the later of (a) six months following termination of employment or separation of service (as defined by Section 409A of the Internal Revenue Code) or (b) February 1 of the following calendar year. A participant is entitled to such benefits under the Income Security Plan in consideration of his or her execution of a separation agreement and general release of claims (the "Release"). The obligation to provide benefits to a participant will be conditioned on the participant's continuing compliance with the confidentiality and non-disparagement, non-competition and non-solicitation covenants set forth in the Release and the covenants to provide services to the Company set forth in the Release. The obligations of the participants have a duration of three years for Tier 1 participants and two years for Tier 2 participants. If a breach of these post-employment restrictions occurs, Orbital ATK is entitled to injunctive relief and any other legal or equitable remedies.
Potential Payments Upon Termination
The following table shows potential payments to the named executive officers upon death, disability, termination without cause and termination of employment following a change in control of the Company. The amounts shown assume that the termination was effective December 31, 2017, the last day of the Company's fiscal year, and are estimates of the amounts that would be paid to the executive officers upon termination, in addition to the base salary, annual incentive and long-term incentive earned during fiscal year 2017 and any applicable retirement amounts payable to the executive officers discussed above under the heading "Pension Benefits" and "Nonqualified Deferred Compensation" in this Form 10-K. The actual amounts to be paid can only be determined at the actual time of an officer's termination. No tax gross-ups are paid to the executive officers upon termination of employment.
136
David W. Thompson | Garrett E. Pierce | Blake E. Larson | Frank L. Culbertson | Michael A. Kahn | |||||||||||||||||
Payments Upon Death | |||||||||||||||||||||
Cash Payment | $ | — | $ | — | $ | — | $ | — | $ | — | |||||||||||
Equity | |||||||||||||||||||||
Stock Options | $ | — | $ | — | $ | — | $ | — | $ | — | |||||||||||
Restricted Stock | $ | 2,824,752 | (1) | $ | 1,247,146 | (1) | $ | 1,490,684 | (1) | $ | 674,858 | (1) | $ | 674,858 | (1) | ||||||
Performance Awards | $ | 363,203 | (2) | $ | 157,011 | (2) | $ | 185,284 | (2) | $ | 86,790 | (2) | $ | 86,790 | (2) | ||||||
Retirement (401(k), DB SERP and/or DC SERP benefit) | $ | — | $ | — | $ | — | $ | — | $ | — | |||||||||||
Total | $ | 3,187,955 | $ | 1,404,157 | $ | 1,675,968 | $ | 761,648 | $ | 761,648 | |||||||||||
Payments Upon Disability | |||||||||||||||||||||
Cash Payment | $ | — | $ | — | $ | — | $ | — | $ | — | |||||||||||
Equity | |||||||||||||||||||||
Stock Options | $ | — | $ | — | $ | — | $ | — | $ | — | |||||||||||
Restricted Stock | $ | 2,824,752 | (1) | $ | 1,247,146 | (1) | $ | 1,490,684 | (1) | $ | 674,858 | (1) | $ | 674,858 | (1) | ||||||
Performance Awards | $ | 2,906,413 | (3) | $ | 1,257,666 | (3) | $ | 1,483,978 | (3) | $ | 694,978 | (3) | $ | 694,978 | (3) | ||||||
Retirement (401(k), DB SERP and/or DC SERP benefit) | $ | — | $ | — | $ | — | $ | — | $ | — | |||||||||||
Total | $ | 5,731,165 | $ | 2,504,812 | $ | 2,974,662 | $ | 1,369,836 | $ | 1,369,836 | |||||||||||
Payments Upon Termination Without Cause - Layoff | |||||||||||||||||||||
Cash Payment | $ | 925,014 | (4) | $ | 700,000 | (4) | $ | 700,000 | (4) | $ | 525,000 | (4) | $ | 545,000 | (4) | ||||||
Equity | |||||||||||||||||||||
Stock Options | $ | — | $ | — | $ | — | $ | — | $ | — | |||||||||||
Restricted Stock | $ | 2,824,752 | (1) | $ | 1,247,146 | (1) | $ | 1,490,684 | (1) | $ | 674,858 | (1) | $ | 674,858 | (1) | ||||||
Performance Awards | $ | 2,906,413 | (3) | $ | 1,257,666 | (3) | $ | 1,483,978 | (3) | $ | 694,978 | (3) | $ | 694,978 | (3) | ||||||
Retirement (401(k), DB SERP and/or DC SERP benefit) | $ | — | $ | — | $ | — | $ | — | $ | — | |||||||||||
Total | $ | 6,656,179 | $ | 3,204,812 | $ | 3,674,662 | $ | 1,894,836 | $ | 1,914,836 | |||||||||||
Payments Upon Termination following a Change in Control | |||||||||||||||||||||
Severance Payment | $ | 5,940,095 | $ | 3,847,500 | $ | 3,847,500 | $ | 1,800,000 | $ | 1,872,000 | |||||||||||
Payment Reduction | $ | (324,235 | ) | (5) | $ | — | $ | — | $ | — | $ | — | |||||||||
Equity | |||||||||||||||||||||
Stock Options | $ | 1,927,151 | (6) | $ | 841,755 | (6) | $ | 999,144 | (6) | $ | 460,690 | (6) | $ | 460,690 | (6) | ||||||
Restricted Stock | $ | 2,824,752 | (1) | $ | 1,247,146 | (1) | $ | 1,490,684 | (1) | $ | 674,858 | (1) | $ | 674,858 | (1) | ||||||
Performance Awards | $ | 2,770,442 | (7) | $ | 1,224,528 | (7) | $ | 1,464,647 | (7) | $ | 661,840 | (7) | $ | 661,840 | (7) | ||||||
Health and Welfare Benefits | $ | 47,021 | (8) | $ | 33,341 | (8) | $ | 33,341 | (8) | $ | 1,109 | (8) | $ | 31,348 | (8) | ||||||
Retirement (401(k), DB SERP and/or DC SERP benefit) | $ | 514,838 | $ | 315,801 | $ | 390,334 | $ | 144,546 | $ | 421,714 | |||||||||||
Total | $ | 13,700,064 | $ | 7,510,071 | $ | 8,225,650 | $ | 3,743,043 | $ | 4,122,450 |
(1) | Values are determined by multiplying the number of shares of restricted stock by $131.50, the closing market price of Company common stock as reported on the NYSE on December 29, 2017, the last trading day of the fiscal year. |
(2) | Estimates for the performance awards for the fiscal year 2016-2018 and fiscal year 2017-2019 performance periods assume payout at the threshold performance level consistent with the terms of the Award Agreements. The value represents a prorated number of shares based on the period of active employment during the respective performance periods. The value was determined by multiplying the number of shares payable by $131.50, the closing market price of Company common stock as reported on the NYSE on December 29, 2017, the last trading day of the fiscal year. |
137
(3) | Estimates for the performance awards for the fiscal year 2016-2018 and fiscal year 2017-2019 performance periods assume payout at the maximum performance level and are prorated based on the period of active employment during the respective performance periods. The value was determined by multiplying the number of shares payable by $131.50, the closing market price of Company common stock as reported on the NYSE on December 29, 2017, the last trading day of the fiscal year. The prorated performance awards would be paid at the end of the performance period based on the actual performance measured following the end of the performance period. |
(4) | The cash payment includes 12 months of base salary and an additional $25,000 to defray health care costs. |
(5) | Under the terms of the Income Security Plan, benefits in excess of the limit established under Section 280G of the Internal Revenue Code are reduced such that the total severance benefit equals the Section 280G limit, beginning with the cash severance payment. |
(6) | Values are determined by multiplying the number of unvested options by the spread between the option price and $131.50, the closing market price of a share of Company common stock as reported on the NYSE on December 29, 2017, the last trading day of the fiscal year. |
(7) | Estimates for the performance awards for the fiscal year 2016-2018 and 2017-2019 performance periods assume payout at the target performance level, consistent with the terms of the Income Security Plan. The value was determined by multiplying the number of shares payable by $131.50, the closing market price of a share of Company common stock as reported on the NYSE on December 29, 2017, the last trading day of the fiscal year. |
(8) | For purposes of quantifying health and welfare benefits, Orbital ATK's annual premium cost was multiplied by three for each of Mr. Thompson, Mr. Pierce and Mr. Larson and by two for each of the other named executive officers. |
Executive Severance Agreement with Mr. Pierce
Mr. Pierce has a preexisting executive severance agreement with Orbital. The Company assumed this agreement in connection with the Orbital-ATK Merger. The agreement provides that Mr. Pierce would receive severance payments and benefits from the Company if his employment is terminated other than in the event of a change in control.
Under his agreement, Mr. Pierce will be entitled to the following payments and benefits upon the occurrence of the following termination events:
Disability. If Mr. Pierce's employment is terminated by the Company for disability (generally defined as incapacity due to physical or mental illness), then (1) his benefits shall be determined in accordance with the insurance and benefits programs then in effect and (2) his equity grants shall continue to vest as scheduled for a 24-month period following such termination and his stock options shall remain exercisable for the remainder of the originally scheduled term. Assuming a December 31, 2017 termination event for disability, Mr. Pierce would receive (a) short-term disability payments of 80% of his base salary for six months, paid biweekly for a total of $270,000, followed by (b) monthly long-term disability payments of $25,000 for 12 months, for an aggregate potential amount of $570,000; and a total of 9,484 shares of restricted stock and 9,312 performance shares would continue to vest as scheduled for a 24-month period. As of December 31, 2017, the value of these awards was $2,471,674 based on the $131.50 closing price of Company common stock on December 29, 2017. Therefore, the aggregate amount of compensation Mr. Pierce might receive if his employment was terminated due to his disability is $3,041,674.
Cause. If Mr. Pierce's employment is terminated by the Company for "cause" (as defined in the agreement), Mr. Pierce would only be permitted to exercise vested stock options for 60 days after the date of termination. As of December 31, 2017, Mr. Pierce is vested in 9,745 stock options.
Good Reason or Without Cause. If Mr. Pierce's employment is terminated by the Company for any reason other than for disability or cause, or by Mr. Pierce for "good reason" (as defined in the agreement), then Mr. Pierce would receive a lump sum payment equal to two times the sum of (1) his annual base salary and (2) the higher of (a) the sum of any bonuses paid or payable to him for the 12-month period immediately preceding the month of such termination or (b) the target bonus for the year of termination based on 80% of his annual base salary. He would also be reimbursed for all reasonable legal fees and expenses incurred by him as a result of such termination. Also, Mr. Pierce's outstanding equity grants would continue to vest as scheduled for a 24-month period and vested stock
138
options would remain exercisable for the remainder of their originally scheduled terms. In addition, his insurance benefits would continue for a 24-month period following such termination.
If Mr. Pierce's employment is terminated by the Company without cause or by him for good reason, and assuming a December 31, 2017 termination event for either of these reasons, payments would be as follows:
Salary | Bonus | Insurance Benefits(1) | Equity Awards(2) | Total(3) |
$1,350,000 | $1,821,406 | $46,615 | $3,765,219 | $6,983,240 |
(1) | Reflects the gross premiums to be paid to provide Mr. Pierce with life, disability, accident and health insurance benefits substantially similar to those he was receiving as of December 31, 2017 for the next 24-month period. |
(2) | Reflects the value of 9,484 shares of restricted stock and 9,312 performance shares, which would continue to vest as scheduled for the next 24-month period, based on the $131.50 closing price of Company common stock on December 29, 2017. Also includes the value of (i) 9,747 stock options, determined based on the difference between the closing price of $131.50 and the exercise price for the options of $72.06, (ii) 9,741 stock options, determined based on the difference between the closing price of $131.50 and the exercise price for the options of $79.43, and (iii) 5,448 stock options, determined based on the difference between the closing price of $131.50 and the exercise price for the options of $93.51. |
(3) | Estimated legal fees and expenses incurred by Mr. Pierce in connection with a termination are not included in the total. |
139
DIRECTOR COMPENSATION
Summary Compensation Information
Only non-employee directors receive compensation for service on the Board of Directors. On August 10, 2017, the Board of Directors approved the following non-employee director compensation, effective immediately as of the election of directors to the Board at the annual meeting of stockholders on that date:
• | an award of restricted stock valued at $120,000 at the time of grant upon initial election to the Board and upon re-election at each subsequent annual meeting of stockholders (increased from $100,000); |
• | an annual cash retainer of $75,000, with no additional fees paid for Board and committee meetings attended; |
• | an annual cash retainer of $100,000 for the independent non-executive Chairman of the Board (Ronald R. Fogleman; increased from $90,000); |
• | an annual cash retainer of $25,000 for the chair of the Audit Committee (increased from $18,500); |
• | an annual cash retainer of $15,000 for the chair of the Compensation and Human Resources Committee, $15,000 for the chair of the Governance Committee and $15,000 for the chair of the Markets and Technology Committee (each retainer increased from $12,500); and |
• | an annual cash retainer of $13,500 for each member of the Audit Committee, $7,500 for each member of the Compensation and Human Resources Committee, $7,500 for each member of the Governance Committee, $7,500 for each member of the Markets and Technology Committee and $2,500 for each member of the special subcommittee of the Markets and Technology Committee. |
Cash amounts are paid annually in a lump sum following election or re-election at the annual meeting of stockholders.
Directors who spend a significant part of a day on Company business issues beyond the normal scope of board member responsibilities receive an additional $1,000 per diem payment, plus expenses. The per diem is paid at the discretion of the Chairman or Chief Executive Officer. Non-employee directors are also reimbursed for tuition and related expenses for continuing director education courses.
Director Compensation
The following table shows the annual retainer and fees earned by the directors for 2017 and either paid in cash or deferred at the election of the director. The Board's Deferred Fee Plan is described below. The table also shows the aggregate grant date fair value of stock awards computed in accordance with generally accepted accounting principles in the United States. The Non-Employee Director Stock Program is described below. Additional information regarding the restricted stock awards and deferred stock units is described in footnote 1 below.
The amounts shown below consist of cash retainer payments and restricted stock awards made in August 2017 for expected service as a Company director, plus all other compensation.
140
Name | Fees Earned or Paid in Cash ($) | Stock Awards(1) ($) | All Other Compensation(2) ($) | Total ($) | ||||||||||||||
Kevin P. Chilton | $ | 98,500 | $ | 119,917 | $ | 3,528 | $ | 221,945 | ||||||||||
Roxanne J. Decyk | $ | 105,000 | $ | 119,917 | $ | 9,741 | $ | 234,658 | ||||||||||
Lennard A. Fisk | $ | 97,500 | $ | 119,917 | $ | 1,092 | $ | 218,509 | ||||||||||
Ronald R. Fogleman | $ | 185,000 | $ | 119,917 | $ | 18,098 | $ | 323,015 | ||||||||||
Ronald T. Kadish | $ | 98,500 | $ | 119,917 | $ | 1,092 | $ | 219,509 | ||||||||||
Tig H. Krekel | $ | 90,000 | $ | 119,917 | $ | 11,356 | $ | 221,273 | ||||||||||
Douglas L. Maine | $ | 121,000 | $ | 119,917 | $ | 1,092 | $ | 242,009 | ||||||||||
Roman Martinez IV | $ | 88,500 | $ | 119,917 | $ | 19,199 | $ | 227,616 | ||||||||||
Janice I. Obuchowski | $ | 97,500 | $ | 119,917 | $ | 1,092 | $ | 218,509 | ||||||||||
James G. Roche | $ | 100,000 | $ | 119,917 | $ | 1,092 | $ | 221,009 | ||||||||||
Harrison H. Schmitt | $ | 100,000 | $ | 119,917 | $ | 1,092 | $ | 221,009 | ||||||||||
Scott L. Webster | $ | 90,000 | $ | 119,917 | $ | 27,528 | $ | 237,445 | ||||||||||
Martin C. Faga (former director) | $ | — | $ | — | $ | 6,001 | $ | 6,001 | ||||||||||
Robert M. Hanisee (former director) | $ | — | $ | — | $ | 367 | $ | 367 |
(1) | This column shows the grant date fair value computed in accordance with generally accepted accounting principles in the United States. The amounts represent restricted stock awards and grants of deferred stock units that are paid in shares of Company common stock and calculated based on the number of shares granted multiplied by the closing price per share of common stock on the date of grant (the amounts do not reflect the actual amounts that may be realized by the directors). A discussion of the assumptions used in calculating these values may be found in Note 17 to the audited financial statements in this Form 10-K. |
The following table shows the number of shares of restricted stock or deferred stock units (to be settled in shares of Company common stock) granted to each non-employee director during 2017 and the closing price per share of common stock on the date of grant.
Name | Grant Date | Number of Shares of Stock or Units | Closing Price on Grant Date | |||||
Kevin P. Chilton | 8/10/2017 | 1,133 | $105.84 | |||||
Roxanne J. Decyk | 8/10/2017 | 1,133 | $105.84 | |||||
Lennard A. Fisk | 8/10/2017 | 1,133 | $105.84 | |||||
Ronald R. Fogleman | 8/10/2017 | 1,133 | $105.84 | |||||
Ronald T. Kadish | 8/10/2017 | 1,133 | $105.84 | |||||
Tig H. Krekel | 8/10/2017 | 1,133 | $105.84 | |||||
Douglas L. Maine | 8/10/2017 | 1,133 | $105.84 | |||||
Roman Martinez IV | 8/10/2017 | 1,133 | $105.84 | |||||
Janice I. Obuchowski | 8/10/2017 | 1,133 | $105.84 | |||||
James G. Roche | 8/10/2017 | 1,133 | $105.84 | |||||
Harrison H. Schmitt | 8/10/2017 | 1,133 | $105.84 | |||||
Scott L. Webster | 8/10/2017 | 1,133 | $105.84 |
The aggregate numbers of shares of restricted common stock, deferred stock units (to be settled in shares of Company common stock) and phantom stock units (to be settled in cash) held by each non-employee director as of December 31, 2017 were as follows:
141
Name | Shares of Restricted Stock (#) | Deferred Stock Units (#) | Phantom Stock Units (#) | ||||||
Kevin P. Chilton | — | 3,323 | — | ||||||
Roxanne J. Decyk | — | 8,177 | — | ||||||
Lennard A. Fisk | 1,133 | — | — | ||||||
Ronald R. Fogleman | 1,133 | 13,286 | 1,845 | ||||||
Ronald T. Kadish | 1,133 | — | — | ||||||
Tig H. Krekel | — | 9,438 | — | ||||||
Douglas L. Maine | 1,133 | — | — | ||||||
Roman Martinez IV | — | 15,566 | 7,597 | ||||||
Janice I. Obuchowski | 1,133 | — | — | ||||||
James G. Roche | 1,133 | — | — | ||||||
Harrison H. Schmitt | 1,133 | — | — | ||||||
Scott L. Webster | 1,133 | 2,190 | — |
(2) | Except for Mr. Webster, the "All Other Compensation" column consists solely of the aggregate amount of: cash dividends paid on unvested restricted stock awarded under the Non-Employee Director Stock Program under the Company's 2015 Stock Incentive Plan or the Non-Employee Director Restricted Stock (the "2015 Director Stock Program"); dividend equivalents paid in cash on deferred stock units under the 2015 Director Stock Program and its predecessor plans (the Non-Employee Director Restricted Stock Award and Stock Deferral Program under the Company's 2005 Stock Incentive Plan and the non-Employee Director Restricted Stock Plan); and the dollar value of dividend equivalents credited in the form of additional phantom stock units under the Company's Deferred Fee Plan for Non-Employee Directors. Dividend equivalents are paid or credited at the same rate as cash dividends paid on the Company's common stock. For Mr. Webster, "All Other Compensation" also includes total payments of $24,000 for the creation of leadership and honorary awards for Company employees and directors. |
Deferred Fee Plan for Non-Employee Directors
The Deferred Fee Plan for Non-Employee Directors permits a director to defer receipt of all or part of the director's cash retainer. In general, directors must make elections to defer fees payable during any calendar year by the end of the preceding calendar year. Newly elected directors have up to 30 days to elect to defer future fees. A director can elect to have deferred amounts credited to either a "cash account" or a "share account" as phantom stock units (based on the market price of Orbital ATK common stock). Cash accounts are credited with interest quarterly at the Company's one-year borrowing rate and share accounts will be credited with additional units if dividends are paid on Orbital ATK common stock. Payment of deferred amounts is made in cash following the director's termination of Board service. Phantom stock units credited to share accounts are paid out based on the market price of Orbital ATK common stock at the time of payout. A director may elect to receive payments either in a lump sum or in up to 10 annual installments.
Currently, two directors hold phantom stock units in this plan. Neither director deferred cash retainer fees during the year ended December 31, 2017. The following table shows how those directors currently have their deferred fees credited and how many common stock units (to be settled in cash) were credited to their share accounts as of December 31, 2017, including additional stock units acquired as a result of dividend equivalents credited on those common stock units.
Name | Annual Retainer | Units as of December 31, 2017 | ||
Ronald R. Fogleman | Cash account-50% | N/A | ||
Share account-50% | 1,845 | |||
Roman Martinez IV | Share account-100% | 7,597 |
142
Non-Employee Director Stock Program
Each non-employee director receives automatic awards of restricted common stock under the Non-Employee Stock Program under the Company's 2015 Stock Incentive Plan upon first being elected to the Board of Directors and upon re-election at each subsequent annual meeting of stockholders. The stock awards have a market value of $120,000, as determined by the closing market price of our common stock on the date of grant.
Common stock issued under this program entitles participating directors to all of the rights of a stockholder, including the right to vote the shares and receive any cash dividends. All shares are, however, subject to certain restrictions against sale or transfer for a period, which we refer to as the restricted period, starting on the award date and ending on the earliest to occur of the following:
• | the first anniversary of the award date; |
• | the retirement of the director from the Board in compliance with the Board's retirement policy as then in effect; |
• | the termination of the director's service on the Board because of disability or death; or |
• | the termination of the director's service on the Board following a change in control of Orbital ATK. |
All restrictions on the restricted common stock are removed on the expiration of the restricted period.
The program permits the directors to elect to defer receipt of the restricted stock in exchange for a credit, in stock units, to a deferred stock unit account. In general, directors must make these deferral elections by the end of the calendar year preceding the date of the grant of restricted stock. Directors who make a deferral election will have no rights as stockholders of Orbital ATK with respect to amounts credited to their deferred stock unit account. If cash dividends are paid on Orbital ATK common stock, the Company will pay each director an amount equal to the cash dividends that would be paid on the number of shares equal to the number of stock units credited to the director's deferred stock unit account. Payment of stock units credited to the deferred stock unit account will be made in a lump sum in an equal number of shares of unrestricted common stock at the time specified in the director's deferral election, but no later than as soon as administratively feasible following the director's termination of Board service.
If a director ceases to be a member of the Board for any reason prior to the expiration of the restricted period, the director forfeits all rights in shares or deferred stock units, as applicable, for which the restricted period has not expired.
2018 Director Compensation Changes
The Company’s usual practice is to pay directors upon election or re-election at each annual meeting of stockholders. However, the Company does not presently anticipate holding an annual meeting of stockholders in 2018 as the Merger is currently expected to close in the first half of 2018.
As a result, if the Company does not hold the 2018 annual meeting of stockholders, the Company intends to compensate directors on a quarterly basis (rather than annually) beginning the time that that annual meeting otherwise would have been held. Each quarterly payment will be paid in cash and no restricted stock shall be issued. The amount of the payment to each non-employee director will approximate 25% of the cash value of the total applicable compensation such director would have received after a regular annual meeting of stockholders.
Expense Reimbursement
Non-employee directors are reimbursed for travel and other expenses incurred in the performance of their duties. Non-employee directors are also reimbursed for tuition and related expenses for continuing director education courses.
Indemnification Agreements
Orbital ATK has entered into indemnification agreements with its directors. These agreements require the Company to:
• | indemnify the directors to the fullest extent permitted by law; |
• | advance to the directors all related expenses, subject to reimbursement if it is subsequently determined that indemnification is not permitted; |
143
• | indemnify and advance all expenses incurred by directors seeking to enforce their rights under the indemnification agreements; and |
• | cover directors under our directors' and officers' liability insurance. |
Compensation Committee Interlocks and Insider Participation
None of the members of the Compensation and Human Resources Committee has ever served as an officer or employee of Orbital ATK or has any relationships with Orbital ATK requiring disclosure below under the heading "Certain Relationships and Related Transactions." Since the beginning of the last fiscal year, no executive officer of Orbital ATK has served on the compensation committee or board of any company that employs a director of Orbital ATK.
Stock Ownership Guideline for Non-Employee Directors
The Board has established a stock ownership guideline for non-employee directors of 5,000 shares of Orbital ATK common stock, to be achieved within five years following a director's election to the Board. The Governance Committee of the Board reviews the stock ownership of each incumbent director annually prior to the Committee's recommendation to the Board of the nominees for election as directors at the annual meeting of stockholders. The following are counted for the purpose of meeting the stock ownership guideline: shares of Orbital ATK common stock owned outright, restricted stock and deferred stock units granted under our Non-Employee Director Stock Program under the Company's 2015 Stock Incentive Plan and predecessor plans (the Non-Employee Director Restricted Stock Award and Stock Deferral Program under the Company's 2005 Stock Incentive Plan or the Non-Employee Director Restricted Stock Plan), and phantom stock units granted under our Deferred Fee Plan for Non-Employee Directors.
The following table shows the securities holdings of incumbent non-employee director nominees as of February 16, 2018 that are counted for the purpose of meeting this guideline.
Name | Date First Elected to Board | Common Stock | Restricted Common Stock | Deferred Stock Units(1) | Phantom Stock Units(2) | Total Securities | |||||||||||||||||||||
Kevin P. Chilton | 2/9/2015 | 3,023 | — | 3,323 | — | 6,346 | |||||||||||||||||||||
Roxanne J. Decyk | 8/3/2010 | 1,261 | — | 8,177 | — | 9,438 | |||||||||||||||||||||
Lennard A. Fisk | 2/9/2015 | 17,300 | 1,133 | — | — | 18,433 | |||||||||||||||||||||
Ronald R. Fogleman | 5/4/2004 | 1,147 | 1,133 | 13,286 | 1,845 | 17,411 | |||||||||||||||||||||
Ronald T. Kadish | 2/9/2015 | 15,932 | 1,133 | — | — | 17,065 | |||||||||||||||||||||
Tig H. Krekel | 3/1/2010 | 1,054 | — | 9,438 | — | 10,492 | |||||||||||||||||||||
Douglas L. Maine | 1/1/2006 | 15,125 | 1,133 | — | — | 16,258 | |||||||||||||||||||||
Roman Martinez IV | 5/4/2004 | 4,000 | (3) | — | 15,566 | 7,597 | 27,163 | (3) | |||||||||||||||||||
Janice I. Obuchowski | 2/9/2015 | 13,150 | 1,133 | — | — | 14,283 | |||||||||||||||||||||
James G. Roche | 2/9/2015 | 15,291 | 1,133 | — | — | 16,424 | |||||||||||||||||||||
Harrison H. Schmitt | 2/9/2015 | 10,452 | 1,133 | — | — | 11,585 | |||||||||||||||||||||
Scott L. Webster | 2/9/2015 | 13,177 | 1,133 | 2,190 | — | 16,500 |
(1) | Deferred stock units are settled in shares of Orbital ATK common stock. |
(2) | Phantom stock units are settled in cash based on the share price of Orbital ATK common stock at the time of payment. |
(3) | Mr. Martinez disclaims ownership of 1,000 shares of common stock owned by his spouse. |
144
ITEM 12. SECURITY OWNERSHIP OF CERTAIN BENEFICIAL OWNERS AND MANAGEMENT AND RELATED STOCKHOLDER MATTERS
The following table shows the number of shares of our common stock beneficially owned (as defined by the Securities and Exchange Commission) as of February 16, 2018 by (1) each person known by the Company to beneficially own more than 5% of the Company's common stock, (2) each of our directors and nominees, (3) each executive officer named in the Summary Compensation Table included in this Form 10-K, and (4) all of the directors and executive officers as a group. Unless otherwise noted, the persons listed in the table have sole voting and investment powers with respect to the shares of common stock owned by them.
Name of Beneficial Owner | Amount and Nature of Beneficial Ownership(1)(2)(3) | Percent of Shares Outstanding(4) | Total Shares, Options, DSUs, and PSUs Owned (5) | |||||||||
BlackRock, Inc. (6) | 5,567,694 | 9.6 | % | 5,567,694 | ||||||||
The Vanguard Group, Inc. (7) | 4,882,579 | 8.4 | % | 4,882,579 | ||||||||
First Eagle Investment Management, LLC (8) | 4,512,118 | 7.8 | % | 4,512,118 | ||||||||
FMR LLC (9) | 3,934,558 | 6.8 | % | 3,934,558 | ||||||||
Kevin P. Chilton | 3,023 | * | 6,346 | |||||||||
Frank L. Culbertson | 33,622 | * | 38,213 | |||||||||
Roxanne J. Decyk | 1,261 | * | 9,438 | |||||||||
Lennard A. Fisk | 18,433 | * | 18,433 | |||||||||
Ronald R. Fogleman | 2,280 | * | 17,411 | |||||||||
Ronald T. Kadish | 17,065 | * | 17,065 | |||||||||
Michael A. Kahn | 76,134 | * | 81,990 | |||||||||
Tig H. Krekel | 1,054 | * | 10,492 | |||||||||
Blake E. Larson | 104,203 | * | 114,749 | |||||||||
Douglas L. Maine | 16,258 | * | 16,258 | |||||||||
Roman Martinez IV | 4,000 | (10) | * | 27,163 | ||||||||
Janice I. Obuchowski | 14,283 | * | 14,283 | |||||||||
Garrett E. Pierce | 99,196 | * | 107,892 | |||||||||
James G. Roche | 16,424 | * | 16,424 | |||||||||
Harrison H. Schmitt | 11,585 | * | 11,585 | |||||||||
David W. Thompson | 152,923 | * | 172,159 | |||||||||
Scott L. Webster | 14,310 | * | 16,500 | |||||||||
All directors and executive officers as a group (21 persons) | 744,208 | 1.3 | % | 870,446 | ||||||||
* | Less than 1%. | |||||||||||
(1) | Includes shares subject to stock options exercisable on February 16, 2018, or within 60 days thereafter, for the following beneficial owners: Frank L. Culbertson, 10,700 shares; Michael A. Kahn, 26,380 shares; Blake E. Larson, 38,537 shares; Garrett E. Pierce, 18,965 shares; David W. Thompson, 44,699 shares; and all directors and executive officers as a group (21 persons), 171,364 shares. | |||||||||||
(2) | Includes shares of restricted common stock with voting rights held by certain directors and executive officers. Excludes deferred stock units without voting rights under our Non-Employee Director Stock Program under the Company's 2015 Stock Incentive Plan, or its predecessor plans (the Non-Employee Director Restricted Stock Award and Stock Deferral Program under the Company's 2005 Stock Incentive Plan and the Non-Employee Director Restricted Stock Plan). Additional information regarding Orbital ATK securities held by each director is shown in the table under the heading Stock Ownership Guideline for Non-Employee Directors in Item 11, “Executive Compensation” of Part III of this Form 10-K. As of February 16, 2018, all directors and executive officers as a group (21 persons) held 111,163 shares of restricted stock. Excludes deferred stock units without voting rights under our Nonqualified Deferred Compensation Plan because none of the executive officers has a payment scheduled within 60 days. Includes shares allocated, as of February 16, 2018, under a 401(k) plan to the accounts of the following beneficial owners: Mr. Kahn, 417 shares; Mr. Pierce, 2,204 shares; Mr. Thompson, 2,374 shares; and all directors and executive officers as a group (21 persons), 8,188 shares. |
145
(3) | Excludes phantom stock units to be settled in cash that are credited to the accounts of directors who participate in our Deferred Fee Plan for Non-Employee Directors (which are shown in the table under the heading Stock Ownership Guideline for Non-Employee Directors in Item 11, “Executive Compensation” of Part III of this Form 10-K) or were credited prior to January 1, 2005 to the accounts of officers who participate in our Nonqualified Deferred Compensation Plan (described under the heading "Executive Compensation" in this Form 10-K). | |||||||||||
(4) | Assumes the issuance of the shares covered by the exercisable stock options and restricted stock units scheduled to vest within 60 days that are held by each person or the group, as applicable. | |||||||||||
(5) | Sets forth the total amount of Company stock-based holdings for the person or entity, including shares beneficially owned and reported on this table and the following stock-based holdings that will not vest or be payable within 60 days following February 16, 2018 (and therefore are not required to be reported in the table): stock options, deferred stock units and phantom stock units. This supplemental information is being provided for our current Named Executive Officers to provide additional information regarding their equity holdings, and is described in greater detail under "Executive Compensation" below. Additional information regarding Orbital ATK securities held by each director is shown in the table under the heading Stock Ownership Guideline for Non-Employee Directors in Item 11, “Executive Compensation” of Part III of this Form 10-K. | |||||||||||
(6) | Based on a Schedule 13G/A filed with the Securities and Exchange Commission on January 23, 2018, reporting beneficial ownership as of December 31, 2017. The amended Schedule 13G reported that BlackRock, Inc. ("BlackRock") has sole voting power over 5,415,168 shares and sole dispositive power over 5,567,694 shares. The shares beneficially owned by BlackRock, a parent holding company, were acquired by various BlackRock subsidiaries, none of which beneficially owns more than 5% of the outstanding shares of Orbital ATK common stock. The address of BlackRock is 55 East 52nd Street, New York, New York 10055. | |||||||||||
(7) | Based on a Schedule 13 G/A filed with the Securities and Exchange Commission on February 9, 2018, reporting beneficial ownership as of December 31, 2017. The amended Schedule 13G reported that the Vanguard Group ("Vanguard"), an investment adviser, has sole voting power over 30,491 shares, shared voting power over 3,835 shares, sole dispositive power over 4,852,773 shares, and shared dispositive power over 29,806 shares. Vanguard Fiduciary Trust Company, a wholly-owned subsidiary of Vanguard, beneficially owns 25,971 shares as a result of its serving as investment manager of collective trust accounts. Vanguard Investments Australia, Ltd., a wholly-owned subsidiary of Vanguard, beneficially owns 8,355 shares as a result of its serving as investment manager of Australian investment offerings. The address of Vanguard is 100 Vanguard Blvd., Malvern, Pennsylvania 19355. | |||||||||||
(8) | Based on a Schedule 13G/A filed with the Securities and Exchange Commission on February 8, 2018, reporting beneficial ownership as of December 31, 2017. The amended Schedule 13G reported that First Eagle Investment Management, LLC ("FEIM"), a registered investment adviser, has sole voting power over 4,279,168 shares and sole dispositive power over 4,512,118 shares. FEIM is deemed to be the beneficial owner of the 4,512,118 shares as a result of acting as investment adviser to various clients. The address of FEIM is 1345 Avenue of the Americas, New York, New York 10105. | |||||||||||
(9) | Based on a Schedule 13G filed with the Securities and Exchange Commission on February 13, 2018, reporting beneficial ownership as of December 31, 2017. The Schedule 13G reported that FMR LLC, a parent holding company, has sole voting power over 3,361,625 shares and sole dispositive power over 3,934,558 shares. Members of the Johnson family, including Abigail P. Johnson (a Director, the Chairman and the President of FMR LLC), are the predominant owners, directly or through trusts, of Series B voting common shares of FMR LLC, representing 49% of the voting power of FMR LLC. The Johnson family group and all other Series B shareholders have entered into a shareholders' voting agreement, under which all Series B voting common shares will be voted in accordance with the majority vote of the Series B voting common shares. Accordingly, through their ownership of voting common shares and the execution of the shareholders' voting agreement, members of the Johnson family may be deemed to form a controlling group with respect to FMR LLC. Neither FMR LLC nor Ms. Johnson has the sole power to vote or direct the voting of the shares owned directly by the various investment companies registered under the Investment Company Act (the "Fidelity Funds") advised by Fidelity Management & Research Company ("FMR Co"), a wholly owned subsidiary of FMR LLC, which power resides with the Fidelity Funds' Boards of Trustees. FMR Co carries out the voting of the shares under written guidelines established by the Fidelity Funds' Boards of Trustees. The address of FMR LLC is 245 Summer Street, Boston, Massachusetts 02210. | |||||||||||
(10) | Includes 1,000 shares owned by Mr. Martinez's wife. Mr. Martinez disclaims beneficial ownership of these 1,000 shares. |
Information regarding securities authorized for issuance under equity compensation plans is set forth under the heading Equity Compensation Plan Information in Item 5, "Market for Registrant's Common Equity, Related Stockholder Matters, and Issuer Purchases of Equity Securities" of Part II of this Form 10-K and is incorporated by reference in this Item 12, "Security Ownership of Certain Beneficial Owners and Management and Related Stockholder Matters".
146
ITEM 13. CERTAIN RELATIONSHIPS AND RELATED TRANSACTIONS, AND DIRECTOR INDEPENDENCE
Certain Relationships and Related Transactions
The Company has a written policy and procedures for the review, approval or ratification of certain transactions, arrangements or relationships involving Orbital ATK and its directors, executive officers, their immediate family members and entities with which they have a position or relationship, or 5% stockholders. Annually, each director and executive officer is required to complete a questionnaire which requires disclosure of any such related person transaction.
Our Governance Committee annually reviews and approves or ratifies all transactions with related persons disclosed in these questionnaires as well as all known transactions and relationships involving our 5% stockholders that are required to be disclosed by the Company pursuant to SEC rules.
The Governance Committee considers the relevant facts and circumstances available to it regarding the matter, including the material facts as to the director's or officer's relationship to or interest in the transaction. The committee approves or ratifies, as the case may be, a transaction if it determines, in good faith, that the terms of the transaction are fair to Orbital ATK and that the transaction is in, or is not inconsistent with, the best interests of the Company and its stockholders.
Any member of the Governance Committee who has an interest in the matter under consideration must abstain from voting on the approval or ratification of the transaction, but may, if so requested by the Chair of the Committee, participate in all or some of the Governance Committee's discussions of the transaction.
Director Independence
Under applicable rules of the New York Stock Exchange (“NYSE”), a majority of our Board of Directors must be independent. Our Board of Directors has affirmatively determined that each of the current directors, other than David W. Thompson, has no material relationship with Orbital ATK and is independent. Each of our Audit, Governance, and Compensation and Human Resources Committees is composed only of independent directors.
In order to qualify as independent, a director must meet each of the New York Stock Exchange's five objective independence standards and our Board of Directors must also affirmatively determine, in its business judgment and in consideration of all relevant facts and circumstances, that the director has no material relationship with Orbital ATK. The Board has reviewed the transactions and relationships between Orbital ATK and our directors, their immediate family members, and entities with which they are affiliated and has determined that other than Mr. Thompson, each director satisfies the five NYSE independence standards and does not have a material relationship with the Company that would impair his or her independence from management.
147
ITEM 14. PRINCIPAL ACCOUNTANT FEES AND SERVICES
Deloitte & Touche LLP ("Deloitte") acted as Orbital ATK's independent registered public accounting firm and also provided certain other services for the fiscal year ended December 31, 2017. PricewaterhouseCoopers LLP (“PwC”) acted as Orbital ATK's independent registered public accounting firm and also provided certain other services for the fiscal year ended December 31, 2016.
Annually, the Audit Committee reviews and pre-approves the audit services to be provided by our independent registered public accounting firm (independent auditor) for the fiscal year, including the financial plan for the audit fees and services. In addition, the Audit Committee annually provides pre-approval for designated types of services that may be provided by the independent auditor without obtaining specific pre-approval from the Audit Committee, subject to an annual dollar limitation and other terms specified by the Committee in its pre-approval policy. Any other service to be provided by the independent auditor requires specific pre-approval by the Audit Committee. In accordance with the pre-approval policy, the specific services provided by the independent auditor and the dollar amounts of fees paid for such services are reported to the Committee. The Audit Committee has delegated to the Chair of the Committee the authority to grant pre-approvals subject to a dollar limitation. Any pre-approval by the Chair of the Audit Committee is summarized for the full Committee at its next scheduled meeting.
The following table sets forth the amount of audit fees, audit-related fees, tax fees, and all other fees billed for services by Deloitte for the fiscal year ended December 31, 2017 and by PwC for the fiscal year ended December 31, 2016. All fees were pre-approved by the Audit Committee or the Chair of the Audit Committee.
Fiscal Year Ended 12/31/2017 | Fiscal Year Ended 12/31/2016 | ||||||||
Audit Fees | $ | 5,016,750 | $ | 8,037,450 | |||||
Audit-Related Fees | 50,000 | 5,000 | |||||||
Tax Fees | 527,376 | 1,475,457 | |||||||
All Other Fees | 3,790 | 3,832 | |||||||
Total Fees | $ | 5,597,916 | $ | 9,521,739 |
The Audit Fees billed or to be billed for the fiscal years ended December 31, 2017 and 2016 were for professional services rendered for audits of the Company's annual consolidated financial statements and internal control over financial reporting in accordance with Section 404 of the Sarbanes-Oxley Act of 2002 and reviews of the Company's quarterly financial statements.
The Audit-Related Fees billed for the fiscal year ended December 31, 2017 were for services relating to the Merger. The amount for the fiscal year ended December 31, 2016 was for services relating to benefit plan consents.
The Tax Fees billed for each of the fiscal years ended December 31, 2017 and 2016 were for services related to tax compliance, advice and planning, as well as services related to research and development tax credit studies.
All Other Fees billed for each of the fiscal years ended December 31, 2017 and 2016 were for accounting research tool annual licenses.
148
PART IV
ITEM 15. EXHIBITS AND FINANCIAL STATEMENT SCHEDULES
(a) Documents filed as part of this Report
1. Financial Statements
The following is a list of all of the Consolidated Financial Statements included in Item 8, "Financial Statements and Supplementary Data" of Part II.
2. Financial Statement Schedules
All schedules for which provision is made in the applicable accounting regulations of the Securities and Exchange Commission have been omitted because of the absence of the conditions under which they are required or because the information required is shown in the financial statements or notes thereto.
3. Exhibits
ORBITAL ATK, INC.
FORM 10-K FOR THE YEAR ENDED DECEMBER 31, 2017
EXHIBIT INDEX
The following exhibits are filed electronically with this report unless the exhibit number is followed by an asterisk (*), in which case the exhibit is incorporated by reference from the document listed. The applicable Securities and Exchange Commission File Number is 1-10582 unless otherwise indicated. Exhibit numbers followed by a pound sign (#) identify exhibits that are either a management contract or compensatory plan or arrangement required to be filed as an exhibit to this Form 10-K. Excluded from this list of exhibits, pursuant to Paragraph (b) (4) (iii) (A) of Item 601 of Regulation S-K, may be one or more instruments defining the rights of holders of long-term debt of the Registrant. The Registrant hereby agrees that it will, upon request of the Securities and Exchange Commission, furnish to the Commission a copy of any such instrument.
Exhibit Number | Description of Exhibit (and document from which incorporated by reference, if applicable) | |
2.1* | ||
2.2* | ||
3(i).1* | ||
3(ii).1* | ||
4.1.1* | ||
4.1.2* |
149
Exhibit Number | Description of Exhibit (and document from which incorporated by reference, if applicable) | |
4.1.3* | ||
4.1.4* | ||
4.1.5* | ||
4.2.1* | ||
4.2.2* | ||
4.2.3* | ||
10.1* | ||
10.2* | ||
10.3* | ||
10.4.1* | Purchase and Sale Agreement, dated at October 28, 1994, between the Registrant and Hercules Incorporated (the "Purchase Agreement"), including certain exhibits and certain schedules and a list of schedules and exhibits omitted (Exhibit 2 to Form 8-K dated October 28, 1994). | |
10.4.2* | Master Amendment to Purchase Agreement, dated at March 15, 1995, between the Registrant and Hercules Incorporated, including exhibits (Exhibit 2.2 to Form 8-K dated March 15, 1995). | |
10.5.1* | ||
10.5.2* | ||
10.6*# | ||
10.7*# | ||
150
Exhibit Number | Description of Exhibit (and document from which incorporated by reference, if applicable) | |
10.8*# | ||
10.9.1*# | ||
10.9.2*# | ||
10.10*# | ||
10.11*# | ||
10.12*# | ||
10.13.1*# | ||
10.13.2*# | ||
10.13.3*# | ||
10.13.4*# | ||
10.13.5# | ||
10.13.6*# | ||
10.13.7# | ||
10.14.1*# | ||
10.14.2*# | ||
10.14.3*# | ||
10.14.4*# | ||
10.14.5*# | ||
10.14.6*# | ||
151
Exhibit Number | Description of Exhibit (and document from which incorporated by reference, if applicable) | |
10.14.7# | ||
10.15.1*# | ||
10.15.2*# | ||
10.15.3*# | ||
10.15.4*# | ||
10.15.5*# | ||
10.16.1*# | ||
10.16.2*# | ||
10.17*# | ||
10.18*# | ||
10.19.1*# | ||
10.19.2*# | ||
10.20*# | ||
10.21*# | ||
10.22.1*# | ||
10.22.2*# | ||
10.23*# | ||
10.24.1*# | ||
10.24.2*# | ||
21 | ||
23.1 | ||
23.2 | ||
152
Exhibit Number | Description of Exhibit (and document from which incorporated by reference, if applicable) | |
31.1 | ||
31.2 | ||
32 | ||
101.INS | XBRL Instance Document. | |
101.SCH | XBRL Taxonomy Extension Schema Document. | |
101.CAL | XBRL Taxonomy Extension Calculation Linkbase Document. | |
101.LAB | XBRL Taxonomy Extension Labels Linkbase Document. | |
101.DEF | XBRL Taxonomy Extension Definition Linkbase Document. | |
101.PRE | XBRL Taxonomy Extension Presentation Linkbase Document. |
153
ITEM 16. FORM 10-K SUMMARY
None.
SIGNATURES
Pursuant to the requirements of Section 13 or 15(d) of the Securities Exchange Act of 1934, the registrant has duly caused this report to be signed on its behalf by the undersigned, thereunto duly authorized, on February 21, 2018.
ORBITAL ATK, INC. | ||||||
By: | /s/ David W. Thompson | |||||
Name: | David W. Thompson | |||||
Title: | President and Chief Executive Officer | |||||
(duly authorized and principal executive officer) |
154
Pursuant to the requirements of the Securities Exchange Act of 1934, this report is signed below by the following persons on behalf of the registrant and in the capacities indicated on February 21, 2018.
Signature | Title | |
/s/ David W. Thompson | ||
David W. Thompson | President and Chief Executive Officer, Director (Principal Executive Officer) | |
/s/ Garrett E. Pierce | ||
Garrett E. Pierce | Chief Financial Officer (Principal Financial Officer) | |
/s/ Kenneth P. Sharp | ||
Kenneth P. Sharp | Senior Vice President, Finance | |
/s/ Christopher A. Voci | ||
Christopher A. Voci | Vice President and Controller (Principal Accounting Officer) | |
/s/ Kevin P. Chilton | ||
Kevin P. Chilton | Director | |
/s/ Roxanne J. Decyk | ||
Roxanne J. Decyk | Director | |
/s/ Lennard A. Fisk | ||
Lennard A. Fisk | Director | |
/s/ Ronald R. Fogleman | ||
Ronald R. Fogleman | Chairman of the Board | |
/s/ Ronald T. Kadish | ||
Ronald T. Kadish | Director | |
/s/ Tig H. Krekel | ||
Tig H. Krekel | Director | |
/s/ Douglas L. Maine | ||
Douglas L. Maine | Director | |
/s/ Roman Martinez IV | ||
Roman Martinez IV | Director | |
/s/ Janice I. Obuchowski | ||
Janice I. Obuchowski | Director | |
/s/ James G. Roche | ||
James G. Roche | Director | |
/s/ Harrison H. Schmitt | ||
Harrison H. Schmitt | Director | |
/s/ Scott L. Webster | ||
Scott L. Webster | Director |
155