UNITED STATES
SECURITIES AND EXCHANGE COMMISSION
FORM 8-K
CURRENT REPORT
PURSUANT TO SECTION 13 OR 15(D) OF THE
SECURITIES EXCHANGE ACT OF 1934
March 2, 2011
|
Date of Report (Date of earliest event reported)
|
INDUSTRIAL MINERALS, INC
|
(Exact name of registrant as specified in its charter)
|
Delaware
|
11-3763974
|
(State or other jurisdiction of incorporation or organization)
|
(I.R.S. Employer Identification Number)
|
Suite 201, 290 Picton Avenue, Ottawa, Ontario, Canada K1Z 8P8
(Address of Principal Executive Offices) (Zip Code)
(613) 241-9959
(Registrant's telephone number, including area code)
Check the appropriate box below if the Form 8-K filing is intended to simultaneously satisfy the filing obligation of the registrant under any of the following provisions (see General Instruction A.2. below):
o Written communications pursuant to Rule 425 under the Securities Act (17 CFR 230.425)
o Soliciting material pursuant to Rule 14a-12 under the Exchange Act (17 CFR 240.14a-12)
o Pre-commencement communications pursuant to Rule 14d-2(b)under the Exchange Act (17 CFR 240.14d-2(b))
o Pre-commencement communications pursuant to Rule 13e-4(c)under the Exchange Act (17 CFR 240.13e-4(c))
Item 7.01 Regulation FD Disclosure.
Technical Disclosure relating to Bissett Creek Project
On May 22, 2007, the Company signed a contract with Geostat International Inc. ("Geostat") to prepare a technical report on the Bissett Creek property in compliance with the requirements of Canadian National Instrument 43-101 (the “2007 Technical Report”). The Geostat work program included a site visit, an independent estimation, classification and certification of resources, certification and validation of the database, verification and validation of the interpretation of ore zones, an assessment of mining and processing procedures, and an estimation of the capital and operating costs to build and operate a mine at Bissett Creek. The process included the drilling of an additional six holes in order to assist in verification of previously obtained data and provide independent assay results and material to carry out independent metallurgical testing and validation.
On September 15, 2008, the Company was designated a reporting issuer in British Columbia by the British Columbia Securities Commission (the “BCSC”) pursuant to British Columbia Instrument 51-509 – Issuers Quoted in the U.S. Over-the-Counter Markets. On August 18, 2009, the Company was advised by the BCSC that the BCSC had issued a cease trade order against it for failure to file a NI 43-101 compliant technical report in connection with the November 2007 announcement by the Company of a mineral resource estimate and the results of a preliminary assessment for the Bissett Creek Project and subsequent similar disclosure. Due to financial difficulties experienced by the Company, the 2007 Technical Report was not finalized and filed with applicable Canadian securities regulatory authorities and accordingly, the Company did not include the results thereof in its 10k filing or its AIF filing in Canada. The cease trade order remains in effect and in connection with the proposed initial public offering by Northern Graphite Corporation (“Northern Graphite” or the “Corporation”), the Company has applied to have the cease trade order revoked. The BCSC has requested, and the Company has agreed, to amend and refile its AIFs for the 2008 and 2009 calendar years to provide certain additional disclosure relating to the Bissett Creek Project. The Company is filing this 8k to bring its US disclosure in line with its Canadian disclosure.
Subsequent to the completion of the 2007 Technical Report, Geostat, now renamed SGS Canada Inc. (“SGS”), prepared an updated technical report on the Bissett Creek Project dated July 16, 2010 (the “2010 Technical Report”), including 2010 price and cost estimates, which was filed on SEDAR by Northern Graphite and the Company in September 2010. Following a review of the 2010 Technical Report by the BCSC, the report has been amended and restated as of February 2, 2011 and has been refiled and is available for review under the SEDAR profiles of the Company and Northern Graphite at www.sedar.com.
There are no material differences between the recommendations and conclusions contained in the 2007 Technical Report and those in the original 2010 Technical Report or the amended and restated 2010 Technical Report. As a result of comments by the BCSC, the Company added additional disclosure relating to historical drilling results, assay procedures and the conversion of double LOI assay results to LECO assay equivalents for about 20 per cent of the drill database, independent verification of the graphite prices used, and corrected areas of identified technical non-compliance with NI 43-101. Investors and shareholders should rely only on the amended and restated 2010 Technical Report and are cautioned that they should not place undue reliance on the 2007 Technical Report or the original 2010 Technical Report. The following information is extracted and summarized from the amended and restated 2010 Technical Report.
RESERVE INFORMATION
Mineral resources (“resources”) have been calculated as at February 2, 2011 in accordance with National Instrument 43-101 – Standards of Disclosure for Mineral Projects of the Canadian Securities Administrators (“NI 43-101”), as required by Canadian securities regulatory authorities. While the terms “measured”, “indicated” and “inferred” mineral resources are required pursuant to NI43-101, the SEC does not recognize such terms. Canadian standards differ significantly from the requirements of the SEC, and mineral resource information contained herein is not comparable to similar information regarding mineral resources disclosed in accordance with the requirements of the SEC. Investors should understand that
-2-
“inferred” mineral resources have a great amount of uncertainty as to their existence and as to their economic and legal feasibility. In addition, investors are cautioned not to assume that any part or all of the Company’s mineral resources constitute or will be converted into reserves.
THE BISSETT CREEK PROJECT
The Bissett Creek Project is the subject of the amended and restated 2010 Technical Report, which was prepared for the Corporation by Gilbert Rousseau P.Eng and Claude Duplessis P.Eng of SGS, each of whom is an independent qualified person pursuant to NI 43-101. The following summary has been prepared with the consent of Messrs. Duplessis and Rousseau and is largely a direct extract of the disclosure contained in the Technical Report.
Prospective investors should be aware that certain historical technical disclosure regarding the Bissett Creek Project by Industrial Minerals did not comply with NI 43-101 and should not be relied upon. Prospective investors should rely only on the information contained in this prospectus and the amended and restated 2010 Technical Report.
Project Description and Location
The Company’s subsidiary, Northern Graphite, holds a 100% interest in the Bissett Creek Project, which contains large crystal graphite flakes in a graphitic gneiss deposit south of the Trans-Canada Highway (Highway 17) and 53 kilometres east of Mattawa, Ontario. The Bissett Creek Project is located in the United Townships of Head, Clara and Maria, in the County of Renfrew, Province of Ontario, approximately 300 km north-northeast of Toronto.
The Bissett Creek Project consists of the Mining Claims, being a group of six unpatented mineral claims covering approximately 624 hectares, and the Mining Lease, being Ontario mining lease number 106693 issued in 1993 for 21 years covering 564.6 hectares. The total property area is approximately 1,189 hectares, and the well explored area is less than 60 hectares. The Bissett Creek Project is centred on UTM coordinates 727170 E and 5112025N (NAD 83) on the topographic map (NTS 31L/01). Northern Graphite owns sufficient ground rights for the development of the Bissett Creek Project. Operational permits and environmental authorization certificates are required for the mining of the open pit but it is expected that these approvals will be obtained normally when needed.
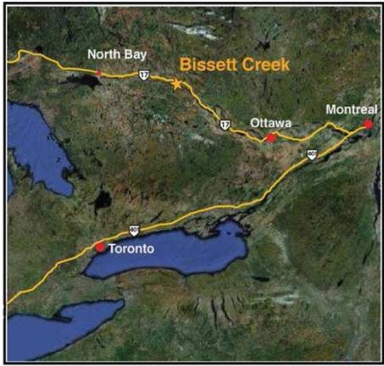
-3-
Royalties on the Bissett Creek Project include an annual advance payment of $27,000 to the three original prospectors that discovered the property which will be credited against a royalty of $20 per ton of concentrate on net sales once the mine is operational, and a 2.5% NSR on any other minerals derived from the property payable to the same parties.
SGS was retained by Industrial Minerals in May 2007 to prepare a NI 43-101 compliant technical report on the Bissett Creek Project with a preliminary assessment in order to evaluate the economic potential of the Bissett Creek Project. This preliminary assessment was updated in the Technical Report and is preliminary in nature and includes Inferred Resources that are considered too speculative geologically to have economic considerations applied to them that would enable them to be categorized as Mineral Reserves. As well, there is no certainty that the results of this preliminary assessment will be realized by Northern.
The preliminary assessment in the Technical Report covers the scientific and financial aspects of the Bissett Creek Project, the technical aspect of the mining and the construction and operation of milling facilities capable of processing 870,000 tonnes per year of graphite bearing rock. Annual production should be in the range of 18,500 tonnes of graphitic flakes, spread more or less in the three following size ranges: 30% +35mesh, 40% -35 to +48 mesh and 30% -48 mesh. The pre-production scenario envisaged by Northern requires the stripping of the open pit, a tailings pond, a waste dump site, a polishing pond, a 2,500 tpd concentrator and the construction of a power line from Highway 17 to the mine site.
Accessibility, Climate, Local Resources, Infrastructure and Physiography
Accessibility
The property is accessible by the Trans-Canada Highway (Highway 17), approximately 53 km east of the town of Mattawa. The Trans-Canada Highway in this area connects the cities of North Bay and Ottawa. The Bissett Creek road intersects Highway 17 two km east of the village of Bissett Creek. Access from Highway 17 to the property is by way of a well maintained gravel forestry road on a distance of 13 km and then east on a winding road on a distance of 4 km.
Climate
The nearest town to the Bissett Creek Project with the most complete data on the climate is Petawawa, which hosts a military camp. In Ontario, the climate is generally continental, although modified by the Great Lakes to the south, and precipitation increases from NW to SE. Annual runoff is from 200 to 600 mm.
Local Resources
The local resources in terms of labour force, supplies and equipment are not sufficient. However, the area is well served by regional geological and mining service firms in North Bay, which is situated 110 km to the northwest. The nearest town, Mattawa, may also provide some workers for minor services, lodging and living support.
Buildings at the site installed in 2002 by Industrial Minerals provide shelter facilities for small groups, core logging, splitting facilities and some storage. All major services are available in North Bay, while minor ones may be available in Mattawa.
Infrastructure
The access road, the mobile house and stripping of the overburden in certain areas were completed by North Coast Industries Ltd. (“North Coast”), a previous optionee of the project, between 1987 and 1992. The dry process pilot plant building was completed by Industrial Minerals in 2005. All of these are kept in good condition. Presently there are not sufficient catering and sleeping facilities to accommodate more than two workers during a stay at the site.
Sand and gravel are available within the Bissett Creek Project, if additional material should be required.
Presently, there is a no electrical power from Ontario Hydro at the site and electrical power at the site is provided by a small power generator. The Corporation contemplates bringing a power line from Highway 17 to the property in the near future.
-4-
In the past, the MNDM and Ontario government have encouraged natural resource development through the granting of permits, title security and financial incentives. Politically, the Ontario government and local Northern Ontario governments are very supportive of mining activities.
Physiography
The Bissett Creek Project is located in rolling hilly terrain. The elevation above sea level ranges from 270 to 320 metres. The property is covered by a mixed forest of conifers and hardwoods. Merchantable red and white pine occurs near the western margin of the property. Soil cover is variable. Rock exposures are found in road cuts and ridge crests. Soil cover is normally sandy, glaciofluvial deposits over ridge areas and glacial lake and stream sediments at lower elevations. Lower lying areas tend to be swampy and covered by moderately thick growth of stunted cedar and swamp grasses. Recognized overburden depth on the property is variable, ranging from zero metres to ten metres thick in the swampy areas.
History
The Bissett Creek Project was first staked by Frank Tagliamonti and associates in 1980. The same year, Donegal Resources Ltd. optioned the Bissett Creek Project but limited work was performed prior to its decision to abandon the property.
In 1981, Hartford Resources Inc. (“Hartford”) optioned the Bissett Creek Project and staked an additional 24 claims. In 1984, Princeton Resources Corp. (“Princeton”) acquired a 100% interest in the Bissett Creek Project through the acquisition of Hartford. Hartford had held the claims since 1981 and had conducted some exploration work including line cutting, surveying, and trenching. During the latter part of 1984 through 1986, Princeton carried out a program of mapping, trenching, surveying, drilling, sampling, and testing with the result that 10 million tonnes of approximately 3% graphite were defined. Historical information is provided for informational purposes only. This resource estimate was not completed in accordance with NI 43-101 and therefore should not be relied upon. Subsequent work identified areas ranging from 3% to 6% graphite. In 1985, Princeton set up a base camp and constructed a batch testing plant.
In November 1986, North Coast entered into an option agreement with Princeton whereby North Coast would be awarded a 58% interest in the Bissett Creek Project upon the completion of a batch testing plant, bulk sampling and the production of graphite flake for end user tests. North Coast was awarded its 58% interest in the property in June of 1987 and subsequently acquired Princeton’s remaining 42% interest on February 6, 1989.
In 1986, North Coast hired KHD Canada Inc. (“KHD”) to review the test plant and make process recommendations. In 1987, the results of these recommendations indicated that the Bissett Creek graphite deposit could be concentrated into high grade and high value graphite flakes. A full feasibility study was undertaken and completed in 1989 which deemed the Bissett Creek Project to be viable with a potential +40% IRR. Kilborn Engineering Ltd., KHD, Bacon Donaldson and Associates Ltd. and Cominco Engineering Services Limited determined that the Bissett Creek Project had a minimum of 20 million tonnes of graphitic material grading higher than 3.18% C. Historical information is provided for informational purposes only. The feasibility study and resource estimate were not completed in accordance with NI 43-101 and therefore should not be relied upon. North Coast undertook extensive exploration and evaluation work on the Bissett Creek Project. Exploration work included detailed geologic mapping on a scale of 1:100, 700m of trenching and 2,100m of diamond drilling for a total of 7,232m in 160 holes. Percussion drilling totalling 1,207m in 82 holes was also done. This drilling was carried out on a 64m x 46m grid spacing with infill drilling at 23m x 23m. In addition to the Princeton 3,630 tonne bulk sample, North Coast collected a number of smaller bulk samples for bench test work by KHD and a large 6,668 tonne bulk sample for pilot testing by EKOF Flotation GmbH (“EKOF”) and KHD.
World graphite prices underwent a significant decline in the late 1980’s as China aggressively entered the graphite market, and the Bissett Creek Project was put on hold. North Coast continued to maintain the leases up until 1997 but graphite prices did not recover sufficiently to warrant proceeding with a mine/mill development at Bissett Creek.
In 2002, Industrial Minerals, through the Corporation, took over the Bissett Creek Project and attempted to develop a dry process flow sheet for the recovery of the graphite flakes. A poorly engineered and flawed design resulted in very little product being produced and continuous or commercial operation was never achieved.
-5-
In April 2007, Industrial Minerals, through a new management group, proceeded to review the past documentation and determined that there was sufficient data to proceed with a preliminary assessment study. Graphite prices had recovered significantly as the future for graphite in some applications is increasing at double digit rates. SGS was contracted in May 2007 to produce a NI 43-101 compliant technical report on the Bissett Creek Project.
Industrial |Minerals planned to install a one tonne per hour pilot plant on the property in the spring of 2008 and a full size 2,500 tonne per day commercial plant producing approximately 20,000 tonnes per year of high grade, high quality graphite flakes in 2010. Industrial Minerals also extended its claims by adding an additional 950 acres (380 hectares) in the spring of 2007 bringing the total property area to 3,250 acres (1,304 hectares). For various reasons, Industrial Minerals did not pursue the development of the Bissett Creek Project.
The Corporation changed its name from “Industrial Minerals Canada Inc.” to “Northern Graphite Corporation” in December 2009 and has to date operated as a subsidiary of Industrial Minerals.
Geological Setting
The Bissett Creek Project lies within the Ontario Gneiss Segment of the Grenville Structural Province of the Canadian Shield. This area is characterized by quartzofeldspathic gneisses which have undergone upper amphibolite facies grade of regional metamorphism with metamorphic temperatures estimated to have reached the 600 to 700 degrees Celsius range. The Ontario Gneiss Segment is distinguished from other areas of the same belt by having northwesterly dominant foliation and structural trends.
Mapping by S.B. Lumbers, 1976, of the Ontario Department of Mines, indicates that the property and surrounding area are underlain by Middle Precambrian metasedimentary rocks. These are coarse and medium grained, biotite-K-feldspar quartz-plagioclase gneisses which are high grade metamorphic equivalents of pure sandstone, arkose and argillite. These highly deformed and recrystallized rocks have been folded into northwest trending, northeast dipping recumbent folds which are refolded by large broad open folds. Greater than 10 % of the rocks are composed of remobilized quartz and feldspar migmatite.
The Bissett Creek Project is predominantly underlain by Middle Precambrian age meta-sedimentary rocks. These are divided into graphite gneiss, transitional graphitic gneiss, and barren gneiss for mapping purposes. The graphitic gneiss is a distinctive recessive weathering unit, commonly exposed along rock cuts, hill tops and occasional cliff faces. It is a calcareous, biotite-amphibole-quartzofelspathic gneiss (generally red-brown to pale yellow-brown weathering). Graphite, pyrite and pyrrhotite occur throughout. Graphite occurs in concentrations visually estimated to be from 1 to 10 %. Sulphides occur in concentrations from 1 to 5 %. In its unweathered state, the rock unit is pale to medium grey in colour.
This graphite gneiss has a moderate 5 to 20 degree dip to the east and the high grade layer dips 20 to 30 degrees to the south on the property. This unit is sandwiched between the upper barren non-calcareous gneiss, which forms the hanging wall of the deposit and a similar lower barren gneiss which forms the footwall. A total thickness of 75m of graphitic gneiss was intersected by drilling.
The barren gneiss is a pale to dark grey-green non-calcareous unit. Black biotite, dark green amphiboles and red garnets distinguish the units from the graphite bearing varieties.
An intermediate unit is present, typically a biotite-muscovite-garnet-quartzofeldspathic gneiss. Muscovite is the distinguishing mica variety and the garnets are mauve in color. This unit may contain variable amounts of graphite and occurs below and within the graphitic gneiss. Two intrusive units have been observed on surface; dykes and sills of coarse grained biotite-muscovite-quartz-feldspar pegmatites and a dark green lamprophyre.
The deposit may be classified as a sedimentary type origin. However metamorphism has transformed the original organic content of the mother sedimentary rock into graphitic carbon flakes. The actual appellation of the deposit is graphitic gneiss. The Bissett Creek Project main zone area is composed of sub-horizontal 5 to 10 degrees undulating layers. The actual well recognized higher grade layer is dipping 15 to 20 degrees to the south.
-6-
Exploration
In 1984, Princeton completed geological mapping, line cutting, surveying, trenching, sampling and diamond drilling. A total of 1,041 ft. (317 m) of BQ diameter core was drilled in 7 holes. Forty trench samples were taken along 5 new trenches. A 15 ton bulk sample was taken from a previously known surface high grade outcrop. A higher grade graphite horizon in the Northeast Zone was identified with a thickness of about 30 meters.
In 1985, Princeton completed geological grid mapping, a magnetic survey, diamond drilling and bulk sampling. A pilot test plant was constructed on site. 99 vertical BQ diamond drill holes were completed for a total footage drilled of 16,836 (3,131 m). Mineralization occurs in gently southeast dipping horizons within an envelope of lower grade graphitic gneiss. The higher grade sections occur in up to 3 horizons. In cross-section, true thicknesses range from 15 to 30 meters. Commonly, a second horizon with a thickness ranging from 3 to 6 meters occurs in the same section. The larger horizons are traceable over a 350 meter strike length. Grade and thickness decrease in the southwest, northeast and down dip directions.
In late 1986, North Coast optioned a 58% interest in the property and became the operator. As part of this agreement North Coast operated the pilot plant processing some 4,900 tons of ore and producing approx. 36 tons of graphite concentrate.
In 1987 North Coast completed geological mapping at 1”=100’ and outcrop sampling completed in the “NE”, “A”, “B”, and “C” zones. Trench sampling was also completed in 5 trenches (T-87-1 to 5). 67 percussion holes were drilled to 60’ where possible and the whole length was sampled in 10’ lengths, strictly for assay. A total of 976.9 ft. of N-DBGM diameter core was drilled in 6 holes. An additional 5,707 ft. of BQ diameter core was drilled in 34 holes. North Coast collected a number of smaller bulk samples for bench test work by KHD and a large 60 tonne bulk sample for pilot testing by EKOF and KHD. Further detailed exploration and evaluation consisted of ore reserve calculations, mine planning, estimates of associated capital and operating costs, extensive metallurgical evaluation, process design, environmental assessment, graphite flake quality evaluation, flake concentrate end user testing and market analysis. North Coast engaged KHD to review the pilot plant flow sheet and equipment, to make process recommendations, and to perform test work on samples and concentrate from the pilot plant. Based on the positive conclusions of the “Prefeasibility Study for the Bissett Creek Graphite Project” issued in December 1987 by KHD, a full feasibility study was completed by KHD in April 1989 for operation of a graphite beneficiation plant with mining facilities and necessary infrastructure. This work had determined that the property had a minimum of 20 million tons of graphitic material grading 3.18%. Historical information is presented for informational purposes only. The resource estimation was not completed in accordance with NI 43-101 and therefore should not be relied upon.
Exploration work indicated that the property, predominantly underlain by Middle Precambrian aged meta-sedimentary rocks, could be divided for mapping purposes into three subunits; 1aG, graphitic gneiss; 1aBT, transitional gneiss and 1aB, barren gneiss. The graphitic gneiss unit hosting the Bissett Creek deposit forms an irregular area with a north-south length of 2.1 km and east-west dimensions reach a maximum of 1.2 km. The graphitic gneiss exposures taper toward the north and south before being lost through structural displacement or erosion. It is a distinctive recessive weathering unit, sometimes calcareous, and generally red-brown to pale yellow-brown weathering biotite-amphibole-quartzo-feldspathic gneiss. Graphite, pyrite and pyrrhotite occur throughout. Graphite occurs in concentrations from 1 to 10% by volume and a flake size range of 1 to 6 mm in diameter. Pyrite and pyrrhotite occur in concentrations ranging from 1 to 5%. In the unweathered state, the rock unit is a pale to medium grey color. This distinct, well mineralized unit, occurs as a gently to moderately east dipping unit, sandwiched between an underlying and overlying barren, non-calcareous gneiss (unit laB). The western edge of the graphitic gneiss is truncated by erosion. The eastern limit of graphite is determined by the overlying barren gneiss contact. A total thickness of at least 76 m has been demonstrated by drilling. Unit laG is uniformly mineralized by low grade flake graphite in the range of 1 to 2% and higher grades occur within and near the structural base of the unit. These bands range in thickness from 10 to 98 feet (3 to 30 meters). On a smaller scale, broad open folds are recognized and vertical faults have been recognized and inferred from drill core. These faults have easterly and east-northeasterly strikes and occur at intervals of 200 to 250 meters. Their effect has been to rotate uniformly dipping blocks around vertical axes. Displacement across the faults appears to be minor.
-7-
SGS’s geological and mining-metallurgical engineers visited the site on June 6 and 7, 2007 and the geological engineer visited again on August 6 and 7, 2007. In addition, the phase 1 independent drilling campaign was carried out and supervised by SGS personnel from the beginning to the end.
No additional work was done on the Bissett Creek Project between the summer and fall of 2007 leading up to the completion of a report by SGS in November 2007, and the completion of the Technical Report in July 2010 (subsequently revised in February 2011). Since the original completion of the Technical Report in July 2010 9and prior to its revision in February 2011), the Corporation has started to implement the recommendations in the Technical Report and has completed a 2,900m infill and exploration drilling program and initiated a metallurgical testing program, a pre-feasibility study and the environmental and permitting review process, all with the objective of positioning the Corporation to make a construction decision on the Bissett Creek Project in 2011. A construction decision is contingent on the positive results of the pre-feasibility study and subject to the availability of financing. There is no guarantee the results of the pre-feasibility study will be positive or will support a construction decision. In addition, there are risks associated with going into production without completing a full feasibility study in that the capital and operating costs estimates, the degree of engineering that has been applied to the various parameters and the extent of testing contained in a pre-feasibility study are not as formal, detailed and reliable as those contained in a feasibility study.
Mineralization
The Bissett Creek mineralization is relatively simple when looked at it from a deposit scale, on local scale it is structurally complex with pegmatite and diabase dykes cutting through it.
The actual sub-horizontal graphitic gneiss was probably an impure greywacke including organic materials. It was metamorphosed under high pressure and temperature and the carbon has been transformed into crystal flakes. As they were formed from sedimentary origin, the graphite flakes are well distributed and occur in successions of low to high density within the graphitic gneiss rock. As in any sedimentary rock, the grade varies less laterally and more across the beds which may be compared to the metasediment graphitic gneiss layers. It is not possible to associate polarity to the gneiss. However, a higher grade layer within the 70m thick graphitic gneiss was observed at the base of the actual arrangement. This creates layers in the order of 20 meters thick which gently dip south in the western part of the deposit.
Graphite flakes occur disseminated in the gneiss and in variable concentration in the transitional gneiss. The graphite flakes are present as oval to sub rounded particles from 1 to 6 millimetres in diameter. The flake sizes measured in the core samples taken in 2007 show a general distribution that is not associated with the percentage of total graphitic carbon. This means the whole deposit can be considered of interest since large flakes are generally present no matter the percentage grade of the graphite. Below the top soil, for the first one to two meters in thickness, the rock is weathered and thus friable. At least the first meter of rock should allow very high recovery of large flakes with little communition.
Drilling
In 1984, Princeton completed a total of 1,041 ft. (317 m) of BQ diameter core drilling in 7 holes. 2 holes drill tested the South Zone, 1 hole tested the North Zone, and 4 holes were drilled in the Northeast Zone.
In 1985, Princeton completed 99 vertical BQ diamond drill holes for a total footage drilled of 16,836 (3,131 m). This total included about 30 shallow unnamed test holes which were drilled to outline surface sample sites. The shallow hole footage totaled 348 ft. (106m). The combined 1985-86 drilling totals 17,881 ft. (5450 m) in 106 holes. Ninety-three holes were drilled in the northeast zone. The majority were drilled at a 64 meter by 46 meter spacing. A detail grid spacing of 23 m by 23 m was used in one area and one fence of holes was drilled at a 10 m spacing to determine the continuity of the graphite horizons. Percussion drill sampling was carried out in 5 areas and 4,000 tons were mined from 3 sites. A total of 3.8 million tons of flake graphite bearing gneiss grading an average of 3.05% graphitic carbon was outlined by diamond drilling in the western and northeast zones. Historical information is presented for informational purposes only. The resource calculation was not completed in accordance with NI 43-101 and therefore should not be relied upon. A cutoff grade of 2.5% C(g) (graphitic carbon) was applied. Resource calculations were based on blocks measuring 70 x 70 x 10 meters. Close to 3 million of the 3.8 million tons are within 34 meters of the bedrock surface. This figure has not been
-8-
evaluated in terms of mining feasibility and no mining dilution or stripping ratio had been calculated. Complete data on the relationship of graphitic carbon assays to full scale flotation was not available and further information was also needed to be gathered on the physical properties of the final product.
In 1987, North Coast drilled 67 percussion holes to 60’ where possible and the whole length was sampled in 10’ lengths, strictly for assay. A total of 976.9 ft. of N-DBGM diameter core was drilled in 6 holes. An additional 5,707 ft. of BQ diameter core was drilled in 34 holes.
158 of the 160 historical diamond drill holes were retained for the present resource calculation. Two historical diamond drill holes located north of the conceptual pit were not used. The percussion holes were excluded from the resource calculation because their methodology description was not thorough enough. None of the trench data or pit results was utilized in the present resource calculation.
In the summer of 2007, following SGS’s recommendation, Northern undertook an independent validation drilling program. The program permitted the development of independent assay results and has also provided material to carry out metallurgical testing and validation. Six vertical NQ size diamond drill holes were drilled in the eastern part of the deposit for a total of 246.43 meters (808.5 ft) around the location of pit # 1. The last drill hole (DDH-07-06) was drilled in an area of the Bissett Creek Project previously named the “pencil zone”. Drilling was done by George Downing Estate Drilling Ltd., from August 1 to August 9, 2007. The results obtained from these six holes were consistent with previous drilling done on the Bissett Creek Project.
SGS’s geological and mining-metallurgical engineers visited the site on June 6 and 7, 2007 and the geological engineer visited again on August 6 and 7, 2007. In addition, the phase 1 independent drilling campaign was carried out and supervised by SGS personnel from the beginning to the end.
No additional work was done on the Bissett Creek Project between the summer and fall of 2007 leading up to the completion of a report by SGS in November 2007, and the completion of the Technical Report in July 2010. Since the completion of the Technical Report, the Corporation has started to implement the recommendations in the Technical Report and has completed a 2,900m infill and exploration drilling program. Results of the program are being compiled and evaluated and QA/QC results verified.
Historical drilling has showed that graphite flakes appear to be evenly distributed throughout the main graphitic unit, regardless of grade. Minor pegmatite and lamprophyre dykes with no grade were also intersected. Higher grade sections of economic interest within the graphitic unit generally consist of an upper zone and a lower basal zone. In a significant majority of the holes both of these zones were present or they coalesced into one thicker zone. In a small number of holes economic mineralization only occurred in the basal zone. Rarely was just the upper zone present.
Potentially economic mineralization is often bounded by transitional mineralization that is treated as waste in the economic analysis but it is not far below cut off. As the grade is high enough to cover incremental milling costs, it will be stored in a low grade stockpile and processed at the end of the mine life.
The graphitic unit as well as the upper and basal zones shows very good correlation and consistency from drill hole to drill hole. As a result, there is a relatively high degree of confidence that the inferred resources can upgraded to a higher category with additional drilling. Furthermore, the deposit remains open north/south along strike and to the east. There are a number of obvious opportunities to increase the current resources around the pit and to the north, with additional drilling. Drill holes located to the north of the current conceptual pit, and which are not included in the resource calculation, intersected the same style and tenor of mineralization.
All 6 holes of the 2007 drill program intersected mineralized gneiss. There was no overburden at drill site locations. The graphitic gneiss foliation being sub horizontal, the vertical holes cut mineralized thicknesses from 30 meters up to 49 meters.
-9-
Sampling and Analysis
The majority of samples taken during the 1980’s drilling programs were prepared on site. Early on, drill core and channel samples prepared for LECO analysis used a 4 to 5 kg sample split in 10 ft intervals on average for drill core and then crushed to one-half inch size. Later on, a detailed procedure was prepared for site sample preparation.
Historically, the carbon content determination of graphite was done using two methods: the double loss of ignition, (double LOI) approach; and a more specific LECO analysis. The double LOI method was and is still being accepted as an industry standard and this method was the basis for much of the original resource analysis done on Bissett Creek. A limited range of results were also tested using the LECO methodology. In both cases, the majority of samples were prepared and analyzed at the site facility. Regular checks were also conducted at SGS Lakefield Research in Lakefield, Ontario, and KHD’s facilities in West Germany.
QA/QC procedures with respect to historical data are not the same as those currently in force. However, extensive testing was done on site, check assays by well known labs were used and the results were reviewed and used at the time by a number of reputable engineering firms including Kilborn, Cominco, KHD, Bacon Donaldson and Pincock Allen & Holt. Furthermore, SGS had access to all the original assay sheets and the results of check sampling at SGS Lakefield. Also, SGS was able to reproduce similar grades and thicknesses to those intersected by historical holes. Therefore results are considered reliable for the purposes of the Technical Report. The observed ranges in values gave a certain level of confidence with respect to the use of historical data. In order to reflect the level of uncertainty in the use of historical results, no resources are categorized as measured.
During the 2007 drill campaign, every core box was photographed prior to splitting. Core from drill holes was first stored in boxes containing each 15 ft in length. After being logged and measured, the core was cut in two parts on its longitudinal direction with a rock saw. One half of the core was sampled for analysis in a laboratory and the other half of the core was stored back in core boxes. Each sample measured approximately 5 ft. A total of 162 samples have been retrieved and kept for analysis. The boxes were numbered and tagged for each drill holes. The boxes were left in a warehouse on site.
During the summer of 2007, in addition to the independent drill program, SGS carried out validation tests on the recovery of graphite and especially the large flakes. This was first done at CFP, a processing laboratory in Val d’Or, Quebec and then assays were done at the COREM facilities in Quebec City. The tests were done on graphitic gneiss rock samples taken from the pit #1 location and acquired during SGS’s first site visit in June 2007. A second battery of tests was also performed at Ortech, with assays at Activation Laboratories Ltd. in Ontario, to further validate the results. The samples came from parts of the witness core samples housed at the mine site.
These additional tests have allowed SGS to conclude that large flakes were present evenly in the various grades and locations drilled in 2007. The actual proven graphitic carbon recovery is in the 95% range. The actual flake size distribution before optimization showed approximately 30% in the +35 mesh size, 40% in the -35 to +48 mesh fraction and 30% in the – 48 mesh portion.
In 2007, SGS did not carry out an extensive QA/QC program during the independent drilling campaign. The main goal of the drilling was to confirm the graphitic gneiss mineralization grade and thickness. However, since samples from the deposit were prepared and assayed at different laboratories and the results were very similar, in SGS’s opinion, the results are considered reliable and reproducible.
In the proposed (July 2010) definition drilling and exploration program on the Bissett Creek Project, a standard procedure of QA/QC will have to be put in place and be followed with repeats and double lab controls. This should include in addition to internal laboratory standards and controls, the inclusion of standards and a 5 to 10% re-assay in a second laboratory. The HC1 leach of pulp prior to LOI and LECO should be run on at least 100 samples and if results prove to be significantly different, all the sample pulps should be run with the HC1 carbonate leach prior to graphitic determination.
-10-
Security of Samples
Review of the sampling preparation, security and analytical procedures used on the Bissett Creek Project in the past were judged to be adequate, though SGS did not have access to the original assay certificates to verify the accuracy of the data. Historically, the carbon content determination of graphite was done using two methods: the double loss of ignition, (double LOI) approach; and a more specific LECO analysis.
The double LOI method was and is still being accepted as an industry standard and this method was the basis for much of the original resource analysis done on the Bissett Creek Project. A limited range of results were also tested using the LECO methodology. In both cases, the majority of samples were prepared and analyzed at the site facility. Regular checks were also conducted at SGS Lakefield Research in Lakefield, Ontario, and KHD’s facilities in West Germany.
For the 2007 campaign, sampling preparation, security and analytical procedures were judged to be adequate. The possibility of tampering is almost nil since the core was split bagged and sealed. The sample bags were under witness of SGS staff until being shipped to the laboratory for preparation and analysis.
Mineral Resource Estimate
In order to be able to properly estimate the Bissett Creek graphite resources, SGS carried out extensive computer modeling of the historical data on the Bissett Creek Project. It should be noted that even if the original data had been computerized in the late1980’s, it was not possible to retrieve it. Requests to SNC-Lavalin (which acquired Kilborn) confirmed that they only had hard copies of the Kilborn reports in their archives. Moreover, the data was done in imperial measures and had to be converted over to metric units. As a result, SGS had to manually enter all of the data to create its resource models.
This process started with computerization of the cross-sections done by the original driller, as well as data from the assay sheets retrieved from the archived records which were available on the Bissett Creek Project. Because of the tremendous amount of historical data in different coordinate systems, the work was tedious, and somewhat complicated by the graphitic carbon assay methods used at that time.
In 2007, SGS’s review of the original results of the two assay methods confirmed that the LOI results were designed more as a graphitic indicator, while the LECO methodology provides a more specific assessment of the graphitic carbon content. It is important to mention that the LOI method of analysis should not be used to measure graphite content since pyrite and calcite (carbonate) content which are present in the deposit may distort the appropriate % graphitic carbon values. 1,791 assays were compiled from the 1980’s drilling, 1,433 of which (80% of the historical dataset) had Double LOI and LECO assay values. Linear regression calculations from these data pairs lead to establishing the following predictive equation: predicted LECO = 0.665*LOI + 0.004. The linear regression was applied to the 358 samples (20% of the historical dataset) that were not assayed for LECO, allowing the results to be more effectively extrapolated across the deposit and compared to the 2007 drill program.
These efforts mean that SGS has carried out modern measurements of the graphitic carbon, which in turn have resulted in a more specific analysis of the graphitic carbon. In doing so, SGS was able to confirm that the LECO grades were consistently 66% of the original LOI grades established for the Bissett Creek Project. It also confirmed that the original LECO results were the more accurate assays of the Bissett Creek graphitic grades.
Within the historical data, only the diamond drill holes were used. In SGS’s opinion, the percussion holes did not have enough description on their methodology to ensure they were as reliable as the drill holes. Drill hole positions from maps were digitized in imperial and converted to metric units. Two conversions occur since they were first transformed into UTM based on a georeference satellite image. Another map from KHD with holes locations was digitized again and converted to the NAD 83 UTM system. Relative positions from one hole to another is maintained. However, SGS believes the exact hole locations in the new coordinate system to be within a 3 to 5 meter radius. The diamond drill hole database has a total of 164 usable holes, i.e. 6 new holes and 158 historical holes.
-11-
SGS designed envelopes around the composites of the estimated mineralized zones according to the geological interpretation between the sections and its knowledge of the deposit. The correlation with the rock types was not validated for the graphitic gneiss as the core description need to be standardized according to the new geological model and also to the lack of information regarding the geology in the database. Because of the presence of graphitic gneiss with inclusions of pegmatites and mafic dykes that cross the deposit at various locations, decision was made to define the mineralized zone with inclusion of barren material at zero grade. In SGS’s opinion some of the barren material will go to the process while some other will be large enough to be taken apart from the graphitic gneiss. In the modeling of the mineralized zone, definition starts from overburden rock contact to the bottom contact.
The resources are estimated between the overburden surface and graphitic gneiss interpreted floor on cross section. A block model of 10mN x10mE x 5mZ is employed and a fixed specific gravity of 2.63 is used. The Indicated Resources are within a well drilled perimeter of approximately 64m x 46m while the Inferred Resources are within the surrounding of this perimeter with limited extension because of lack of drilling. However, outcrops show graphitic gneiss in those extensions.
The first NI 43-101 compliant resources statement is summarized in the table below:
Bissett Creek - Classified resources for public disclosure
Indicated
|
Inferred
|
|||||||||
% Graph C
|
Tonnage
|
LOI
|
Graph C-LECO
|
In Situ Graphite
|
Tonnage
|
LOI
|
Graph C-LECO
|
In Situ Graphite
|
||
Cut-Off
|
metric
|
%
|
%
|
(metric tonnes)
|
metric
|
%
|
%
|
(metric tonnes)
|
||
1
|
20,448,900
|
2.87
|
1.97
|
402,200
|
26,232,000
|
2.82
|
1.90
|
499,700
|
||
1.5
|
14,641,000
|
3.19
|
2.24
|
327,700
|
18,027,000
|
3.19
|
2.21
|
397,900
|
||
2
|
8,779,000
|
3.57
|
2.58
|
226,000
|
10,682,000
|
3.59
|
2.51
|
268,000
|
||
2.5
|
4,562,000
|
3.95
|
2.88
|
131,600
|
4,621,000
|
4.17
|
2.89
|
133,400
|
||
2.7
|
3,077,000
|
4.10
|
3.02
|
93,000
|
3,210,000
|
4.23
|
3.00
|
96,400
|
||
2.8
|
2,374,000
|
4.18
|
3.10
|
73,700
|
2,314,000
|
4.30
|
3.10
|
71,800
|
||
3
|
1,316,000
|
4.34
|
3.27
|
43,100
|
1,402,000
|
4.34
|
3.24
|
45,400
|
||
3.3
|
469,000
|
4.59
|
3.52
|
16,500
|
353,000
|
4.41
|
3.52
|
12,400
|
||
SG:2.63
|
||||||||||
Undiluted
|
Rounded numbers
|
Mineral Resources that are not Mineral Reserves do not have demonstrated economic viability.
The base case represents resources above a 1.5% cut-off. Because the average selling price of the graphite is around $1,700 per tonne, the in situ cut-off is about $25.50 per tonne, which is suitable for open pit operations. The effective cut-off used in the preliminary assessment is 1.58%.
The above resources do not include the graphitic gneiss intersected in the holes north of the actual known deposit. SGS recommends that more drilling be done between sections with a detailed topographical survey to support Measured Resources. In SGS’s opinion, a QA/QC program must be put in place for the next drilling campaign. Actual quality control with different metallurgical testing by SGS is considered sufficient to proceed with the next stage of economic analysis.
-12-
Mining Operations
General
Economics permitting, Northern plans to mine and mill 2,500 tonnes of graphitic material per day from the Bissett Creek Project. Because the mineralized rock comes to the surface, an open-cast operation is described in the Technical Report. Proposed mining operations are conceptual in nature and could change substantially depending on the results of the pre-feasibility study.
The mineralized and waste material within the deposit is mainly gneissic. This material is normally competent with only minor weathering near the surface. The overburden material which accounts for the majority of the waste material to be removed in a rather short time varies from 0 to 10 meters with an average thickness of more or less 4 meters.
Firstly, the overburden will have to be removed on an area exceeding some 5 meters of the pit contour at an angle of 30º. No rock mechanic was undertaken; however because of the characteristics of the host rock an overall slope of 45º is believed to be conservative. The bench will have 5 meters in height whereas the berms shall have a width of 5 meters. However 10m bench height is envisage where 10m thick mineralized material is present, the 5m bench height will be applicable for the bottom contact to reduce dilution.
Apart from the overburden, for the purpose of the Technical Report, a 3 phase pit development is proposed in order to have a waste to mineralized material ratio from 0.05 to1.15 tonne of waste to 1 tonne of mineralized material. Thus for the entire operation of the mine, for every tonne of mineralized material mined out, about half a tonne of waste will have to be stockpiled somewhere on the property.
A 2 m³ backhoe type shovel backed by a D-8 bulldozer and a couple of 10 wheeler trucks may be used to remove the overburden that will be stockpiled in a specific designated area. At the end of the mining operation this overburden will be used to cover the waste stockpile and if necessary the mill tailings. The overburden removal will be subcontracted. A budget proposal from Norascon for a turnkey mining operation was obtained and this proposal is used in the economic assessment.
The gneissic rock will be drilled and blasted. Two hydraulic percussion drills capable of drilling up to 127 mm holes to a depth of 7 meters will be used. The selected drills will have sufficiently high masts to drill holes in a single pass without having to couple and uncouple drill rods. Blastholes will be charge with ammonium nitrate - fuel oil mixtures (ANFO) by means of a truck mounted ANFO loading unit. Where water is encountered, water gel explosives will be used. Loaded blastholes will be detonated by nonelectric caps linked with primacord.
The primary loading equipment will be two hydraulic excavators equipped with 4.6 m³ bucket. A wheeled front end loader having a 4.3 m³ bucket capacity will be provided for backup when the shovels are not available and for loading scattered material. The haulage equipment will consist of a fleet of 36-tonne capacity off highway trucks. The mineralized material will be hauled over a distance of approximately 0.5 km to the mill crusher hopper while the barren rock will be hauled to a nearby stockpile.
Because of a somewhat erratic contamination of mineralized material by small dykes and pegmatite delimitation within the host rock, coupled to the difficulty of distinguishing at the pit face what is graphite from what is biotite, a geologist or at least a good geological technician will have to be hired to follow the day to day mining operation.
The necessary manpower to smoothly mine some 14,000 tpd of graphitic material from the Bissett Creek deposit shall minimally be 34. Apart from the geologist and the security guards, all other employees will be supplied by and at the discretion of the mining contractor. Along with its work force, the mining contractor will supply a garage large enough to accommodate the repair of two trucks at the same time and two explosive shelters (one for the explosives and one for the non-electric fuses and detonators). Finally, the Corporation will install a guardhouse at the entry of the property.
-13-
The mining capital expenditures will be only for the purchase of a field trailer to lodge the guard house and the installation of a fence around the openings since the entrepreneur will supply all of the mining equipment, machinery and shelters.
The authors of the report have substantial experience in the mining industry and have acquired through preparing a number of NI 43-101 reports knowledge of detailed mining costs for open-pit operations in flat lying deposits of similar tonnage. Based on this experience, the mining costs provided by Norascon were considered to be reliable for an operation of this size and type. Norascon has provided the following average cost per tonne in $ CDN for the excavation and the mining of the overburden, the waste and mineralized material.
Mining cost overburden: | $ 2.20/tonne |
Mining cost waste rock: | $ 3.81/tonne |
Mining cost mineralized rock: | $ 4.11/tonne |
Conceptual Mining Sequence
The open pit design in the preliminary assessment contained in the Technical Report is based on a cut-off grade calculation determined from processing costs developed in the cost model of SGS plus an internal model prepared by Northern. SGS believes these costs to be reasonable for use in the preliminary assessment and that they are comparable with other similar operations in analogous conditions with respect to equipment, supply and support. For the purpose of this preliminary assessment, all Mineral Resources including Indicated Resource and Inferred Resource categories were used in the final pit to support the proposed 45 years of operation on the property. Three detailed imbricated pit designs were done in order to derive a higher grade at the beginning of the operation with the smallest waste to ore ratio. The final pit is the final whittle pit which will probably change with additional drilling.
The starter pit (#1) is 230m x 150m, the second phase pit (#2) is 340m x 370m, and the third phase pit (#3) is 900m x 500m. Total pit depth is 80m with bottom at elevation 210 metres. A 45 degree maximum overall slope in rock is used while a 3H to 1V is used in the overburden. No geotechnical investigations have been completed as yet to support the pit design and are recommended in the next phase of work. It is SGS’s opinion that a 45 degree overall slope is conservative having seen the rock quality in the test pit. The ramp declines at a maximum of 10% with a width of 3 times the width of the haulage trucks i.e. 15 metres.
The proposed graphite producing operation will constitute a small to medium scale operation using conventional drill, blast, load and haul process to mine an average of 870,000 tonnes of graphitic material and 450,000 tonnes of waste per year. If economics warrant, the mine production rate could range from 2,500 to 5,000 tonnes of mineralized material per day.
The initial production scenario was a complete mining fleet. However the idea of using a mining contractor has been retained in the preliminary assessment contained in the Technical Report. SGS has received a turnkey quotation from a mining contractor for the excavation and mining of the overburden and rock on the property. A mining contractor for the first 10 years is proposed. A mining dilution of 10% is taken into account. Main mining bench height is 10 meters while five metres will be used near the bottom contact.
If feasible, SGS proposes to use the overburden removed from the proposed pit #1 to build the tailings dam resulting in an optimization of the earth movement and lowering the dam construction costs. The rest should be stockpiled, to cover the waste pile at the end of the mining operation.
Within the conceptual scenario, the stripping over time is variable. In the first two years of operation, a waste to mineralized rock ratio of 0.05 to 1 will be achieved, in the third to eleventh years of operation a ratio of 0.55 to 1 is scheduled and afterward it will decrease to 0.23 to 1 in year 19 and will increase to 1.15 to 1 from year 20 to year 27. In years 28 to 31 it should be 0.06 to 1 and drop to zero for the rest of the fourteen years of operation as the mill will process the low grade stockpile. The average cut-off grade for the whole open pit is 1.58 % graphitic carbon and the average waste to mineralized rock ratio is 0.66 tonnes of waste for one tonne of processed rock.
-14-
The start-up pit contains a total of 1,570,000 tonnes of Indicated Resources at 3.66% total carbon and 2.71% graphitic carbon. Fully diluted, the pit has 1,727,000 tonnes of Indicated Resources at an average graphitic carbon grade of 2.55%. The second phase pit has a total of 3,235,000 tonnes of Indicated Resources at 3.21% total carbon and 2.34% graphitic carbon. Fully diluted, the pit has 3,558,000 tonnes of Indicated Resources at an average graphitic carbon grade of 2.22%.
The third phase pit has a total 6,263,000 tonnes of Indicated Resources at 3.38% total carbon and 2.32% graphitic carbon and 3,762,000 tonnes of Inferred Resources at 3.43% total carbon and 2.42% graphitic carbon. Fully diluted, the pit has 6,889,300 tonnes of Indicated Resources at an average graphitic carbon grade of 2.20% and 4,138,200 tonnes of Inferred Resources at an average graphitic carbon grade of 2.29%.
75% of the resources in the above three mining phases are in the Indicated Resources category over the first 19 years of operation.
The fourth phase pit has a total of 1,903,990 tonnes of Indicated Resources at 2.45% graphitic carbon and 9,596,260 tonnes of Inferred Resources at 2.32% graphitic carbon. Fully diluted, the pit has 2,094,490 tonnes of Indicated Resources at an average graphitic carbon grade of 2.27% and 10,555,880 tonnes of Inferred Resources at an average graphitic carbon grade of 2.16%.
The actual fifth phase plans to process the low grade stockpile. However, this may change after exploration diamond drilling takes place to secure better head grades. There are 4,419,800 tonnes of diluted Indicated Resources at 1.22% graphitic carbon grade and 5,520,900 tonnes of diluted Inferred Resources at 1.15% graphitic carbon in the low grade stockpile.
To keep a safe distance between the quarry and the mill, the run of mine graphitic material will be hauled over a distance of approximately 0.5 km to the mill site. Whenever possible the graphitic material should be dumped directly in the jaw crusher feed hopper. If for some reason it will be impossible to dump the incoming graphitic material directly in the jaw crusher feeder hopper, it will be stockpiled nearby to be retrieved at a later time.
Waste should be trucked to a principal waste dump located to the north or west of the actual deposit. However validation, that is, condemnation drilling, will be required prior to waste disposal. Opportunities for in-pit waste backfilling should come available in mined out areas after seven years of mining; details have not yet been developed.
Processing Plant
A 2,500 tpd mill is proposed in the preliminary assessment contained in the Technical Report. The mill process should be very conventional. Operation should rely on the operators’ experience and skill supported by electronics and instrumentation. Mill design criteria are the one used in some mines in Canada where, apart from the run of mine grizzly and hopper, the ore bins, the thickener and the water tanks, the entire mill services and operations are under the same roof. Whenever possible, mill equipment will be chosen on the base of recovering a maximum of the larger flakes.
The Technical Report is based on the following assumptions:
●
|
A good mill design will have a good overall graphite grade and recovery
|
●
|
A Butler type building has been selected for its versatility, low cost and ease of construction
|
●
|
If available and in good working conditions, Northern will buy second hand milling equipment
|
●
|
The mine will be able to feed the mill at a rate of 2,500 tpd, 7 days per week
|
-15-
●
|
No major setback will be encountered with the federal and provincial environmental agencies, trade unions and/or indigenous people
|
●
|
3-Phases electrical power will be available on site
|
●
|
Approximately 5 hectares of a more or less flat site will have to be prepared at a reasonable cost for the mill and its dependencies
|
●
|
It will be possible to discard the tailings without jeopardizing the small streams crossing the property
|
●
|
It is assumed that approximately 40.0 % of the graphitic carbon is in the + 35 mesh fraction while some 70 % is coarser than 48 mesh. The run of mine has a 2.55 to 2.18 % diluted graphitic carbon grade and the mill overall recovery will be better than 90.0 %.
|
●
|
The Work Index is in the order of 12 kWh/tonne
|
●
|
The liberation size is no finer than 80 % minus 20 mesh.
|
●
|
No provisions were made for the recovery of other minerals (silica, biotite, etc)
|
Laboratory and pilot plant test work done late in the 1980’s and early 1990’s by such prestigious companies as KHD, Cominco Engineering Services Ltd. and Bacon, Donaldson & Associates Ltd. have shown that a well designed mill could produce three concentrate grades (+48 mesh, -48 to +100 mesh and –100 mesh) having an average grade of 92.7 % C with an overall mill recovery of 94.4%. However, SGS is of the opinion that once a clean +48 mesh graphite material is produced it is only a matter of installing a three deck screen at the end of the circuit instead of a two deck to produce, at the same time, a discrete +35 mesh grade.
The run of mine material should be crushed and conveyed to a SAG mill and then to a bank of flash flotation cells followed by a +48 mesh circuit, a -48 to 100 mesh circuit and finally a finer than 100 mesh circuit. The three graphite concentrates will be allowed to settle in a thickener and then filtered and dried. The dryer product will be fed to a set of three deck screens and then conveyed to their respective bins. Dust control will be provided by a dust collector system comprising a cyclone and a bag house. Dust collector product is discarded or allowed to report to the -100 mesh bin.
From a series of tests made in the 1980’s, the concentrate grades should be in the +90% range while, after the necessary break in period, overall recovery should be in the 95% bracket.
The graphitic material and the waste are potentially acidic generators so the tailings should have to be stored under water while the waste dump should have to include some dolomitic or calcareous aggregates to neutralize the acid potential with the addition of 10 to 20kg of carbonate material per tonne of waste. Permits and environmental issues are currently being addressed by another consulting group (Knight Piesold Consulting).
In the past, Industrial Minerals has done extensive work to determine the crushing-milling costs. Based on the softness/hardness of the mineralized material, the low electrical power requirement, the ease of graphite concentration and mill control and instrumentation, SGS is of the opinion that the cost of approximately $7.00 per tonne as defined in 2007 by Industrial Minerals was in the correct range. However, because of the increase in the cost of living since 2007, a milling cost of $7.50 per tonne is anticipated.
Mill reagents and other chemicals consumption will be for all practical purpose limited to an alcohol or and hydrocarbon type of collector-frother (EKOF or pure kerosene). Crushing and grinding wear parts as well as grinding media consumption will be minimal by the use of a SAG mill. After the break in period, for an efficient operation of the mill, a work force of 40 employees will be required.
-16-
Today, a rule of thumb for the cost of a new mill plant is approximately $20,000 per tonne milled per day or in the case of the Bissett Creek mill approximately $50,000,000. This cost is for a very conventional mill with new equipment. However, SGS is of the opinion that some $5,000,000 could easily be saved by buying good second hand equipment.
SGS is of the opinion that it will take up to one year for Northern to obtain all the necessary permits before proceeding to the construction of the mill. In the case the Corporation prefers to wait for all the permits to come in before buying a first piece of equipment, another period ranging from nine months to one year will be required before the mill start up. However, in the meantime, because of the many unknowns especially as to which milling equipment will work best, Northern would be well inspired to have the flow sheet validated at the pilot plant level.
Markets
In 2007, the Corporation investigated specific prices for the graphite concentrates by flake size category. Noting that pricing in the graphite market place is often established on a “fully negotiated” basis and that final prices may be subject to change based on market conditions at the time final contracts are established, the Corporation determined that sales prices range from $2,200, to $1,800 to $850 per tonne for the three basic graphite flake ranges it expected to produce.
Since that determination, the Corporation has further considered that it should attract premium pricing since almost 90% of Bissett Creek Project production is expected to be 80% +48 mesh, 94%C. There is no quoted price for this larger flake material as it is uncommon, but the Corporation expects to be able to sell its graphite for significantly higher than US$2,000 per tonne.
In addition, graphite prices have increased substantially over the last couple of years due to the effect of the ongoing industrialization of China, India and other emerging economies on traditional demand in the steel and automotive industries. This trend is expected to continue. Moreover, the growing use of lithium-ion batteries in hybrid and all-electric vehicles is expected to create significant incremental demand for graphite in the future, which will have a positive influence on prices.
Accordingly, the Corporation considers $1,700 per tonne to be a conservative, long term average blended price for the products that should be produced from the Bissett Creek Project and is suitable for use in the preliminary assessment in the Technical Report.
It should also be noted that the actual preliminary assessment study does not take into account the potential production of high purity graphite products that the Corporation ultimately expects to sell.
The average selling price used in the Technical Report has been verified and is considered reasonable based on independent verifications consisting of published prices in Industrial Minerals magazine and review of an independent market intelligence and research report. The average price provided by the Corporation was also reviewed by industrial minerals and graphite expert, Mr. George C. Hawley, prior to being provided to SGS.
Financial Analysis
SGS independently prepared a set of Excel spreadsheets “the economic model” to examine the economic viability of the proposed scenario with a sensitivity analysis. At this stage, SGS has conducted the financial analysis on the basis of pre-tax results.
Assumptions are:
Mining cost overburden: | $ 2.20/tonne |
Mining cost waste rock: | $ 3.81/tonne |
Mining cost mineralized rock: | $ 4.11/tonne |
-17-
Mining cost overburden: | $ 7.50/tonne |
Mine administration costs: | $ 1.12/tonne |
Contingency on processing costs: | $ 1.50/tonne |
General administration costs: | $3.57/tonne |
Total processing cost: | $13.69/tonne |
Mill recovery: | 93 to 96% |
Recovery mining: | 100% |
Mining dilution: | 10% |
Because of the availability of experienced mining contractors, the decision has been made to use a mining contractor rather than an owner operated mining fleet. Stripping can be done in a short period of time (within a three month period) from the starter pit, so it is considered an operating rather than a capital cost. Accordingly, there is no capital cost estimate for the pit exploitation itself. All capital costs relate to the mill construction, engineering and design, infrastructure and tailings rehabilitation and mine closure and reclamation.
CAPEX
|
$
|
Metallurgical testing
|
100,000
|
Mill construction + Equipment
|
45,650,000
|
Mining construction
|
166,000
|
Tailings pond study & construction
|
1,575,000
|
Mine closure provision
|
709,000
|
Powerline and Connection
|
2,152,500
|
Preproduction head office
|
2,100,000
|
Contingency (20%)
|
10,490,500
|
Total CAPEX
|
$62,943,000
|
SGS’s conclusion is that the potential development of Bissett Creek appears to be economically attractive. A discount rate of 10% yields a NPV of approximately $77.6 million, and a corresponding projected IRR of approximately 24% before taxes. The payback period in the base case is six years.
It should also be noted that in 2007 SGS carried out a detailed economic sensitivity analysis that modifies prices, costs and graphite recoveries over a +/- 25% range, producing corresponding IRR ranges varying from 13% to 42%.
Since the price of graphite in the long run should parallel the overall mining costs, SGS is confident that its 2007 detailed economic sensitivity analysis is still valid with IRR range from 13% to 42%. The 2010 updated IRR ranges between 10 and 37%.
-18-
The preliminary assessment is preliminary in nature and includes Inferred Resources that are considered too speculative geologically to have economic considerations applied to them that would enable them to be categorized as Mineral Reserves. Furthermore, there is no certainty that the results projected in the preliminary assessment will be realized and actual results may vary substantially.
The Corporation’s proposed mining operation is conceptual and the Corporation’s methods and projections could change significantly based on the results and recommendations of the pre-feasibility study.
Interpretation and Conclusions
A great deal of the work done in the past was performed on less than 10% of the Bissett Creek Project, with several important studies by major engineering companies. All of those studies were based on resource models using the LOI assay methodology, which seems to have been accepted at the time as a key indicator of graphitic content in the rock.
Based on the 2007 independent drilling program, and a review of the available LOI versus LECO assay results, SGS is confident that the need for an accurate assessment of the graphitic content has been achieved (it should also be noted that only those sections of the previous reports that were considered reliable were used in SGS’s updated assessment). Accordingly, SGS has reduced the average grades of the deposit from the figures stated in the original feasibility studies. This is based on the observation that the original LOI results did not fully represent the actual graphitic carbon values in the rock because of the carbonaceous nature of the gneiss in some areas and the small amount of disseminated pyrite which affected the LOI readings.
With the actual resource estimate of graphitic carbon (% graphitic carbon by LECO), the project is healthier than twenty years ago. Moreover, aside from grade considerations, SGS has confirmed that the flake size is well distributed in the deposit and is not related to the grade.
In 2007, SGS provided the following services to Northern which are still valid for the purpose of the preliminary assessment:
·
|
Independent sampling;
|
·
|
Independent laboratory tests to validate grade, flake recovery and graphitic carbon assay;
|
·
|
Independent diamond drilling and sampling of six drill holes;
|
·
|
Differential GPS survey of the new holes and a sector of the topography;
|
·
|
Acid generation tests; and
|
·
|
Metallurgical testing and assaying.
|
The proposed mining operation by Northern could be one of the largest graphitic crystal flake hard rock mining operations in Canada and certainly the nearest in terms of a supplier to potential North American markets.
The Bissett Creek Project has a Mineral Resources inventory that could sustain production for more than 40 years and potentially a larger scale operation if market conditions warrant.
SGS believes that the capital and operating costs assumptions considered in the preliminary assessment contained in the Technical Report are of the correct magnitude for the project and within the accuracy required for this level of study.
-19-
SGS believes that drilling, sampling and testwork as well as site investigation work are adequate for this stage of the project; development concepts are viable, however, more diamond drilling is recommended to increase the level of confidence in the resources and better define the real size of the deposit.
Metallurgical testing will be needed for the selection of machinery and to increase the recovery of the larger size fraction, which in turn will yield higher market prices.
Based on drill results from less than 10% of the overall Bissett Creek Project area (total area = 3,250 acres), the Indicated and Inferred Resources provide a solid base with a recovery of approximately 658,000 tonnes of graphite in this preliminary assessment. Average grades within this resource range between 2.2 to 3.1% C. Using a plant capacity of approximately 2,500 tonnes per day, the projected mine life at these grades is approximately 40+ years, before allowing for any additional resources derived from further drilling on the Bissett Creek Project.
In addition, the Bissett Creek deposit is characterized by its structure as a large flake, crystalline graphite deposit and has been found to be free of many of the chemicals or contaminants often present in such deposits. This profile will assist in improving recoveries and reducing overall processing costs. Accordingly, based on the actual resource estimation and current market fundamentals, SGS concludes that Bissett Creek may prove to be economically attractive. Applying a discount rate of 10% yields an NPV of approximately $77.6 million before taxes and a corresponding projected IRR of approximately 24%. Given this economic profile, SGS’s recommendation is to proceed with a pre-feasibility study.
75% of the Mineral Resource estimate is in the Indicated Resources category for the first 19 years of operation, thus the preliminary assessment results and conclusions would change little if Inferred Resources were excluded entirely. Furthermore, drill spacing represents a key feature differentiating Inferred Resource and Indicated Resource classifications because the Bissett Creek deposit is relatively thick and flat lying with good continuity of mineralization between drill holes. It is also open along strike and down dip. The preliminary assessment recommends additional drilling as part of the pre-feasibility study. There is a relatively high probability that additional drilling will upgrade Inferred Resources into Indicated Resources.
During the feasibility study process in the 1980s, a number of well known and reputable engineering companies completed metallurgical test work, pilot plant testing and bulk sampling of the Bissett Creek deposit and therefore it was thoroughly tested. While this work predated NI 43-101, it is the opinion of SGS that this work has significant value in making the decision to proceed with a pre-feasibility study. Furthermore, the pre-feasibility study will allow SGS to validate the metallurgical testing done in the past and develop and optimize a flow sheet for a wet process.
The preliminary assessment is preliminary in nature and it includes Inferred Resources that are considered too speculative geologically to have economic considerations applied to them that would enable them to be categorized as Mineral Reserves, and there is no certainty that the results projected in the preliminary assessment will be realized and actual results may vary substantially.
Recommendations
Following the positive results of the estimated cash-flow, SGS recommends to advance the Bissett Creek Project in the direction of a commercial production. SGS also recommends that Northern proceed with a pre-feasibility study in order to confirm its recommendations. As part of the next prefeasibility phase, SGS recommends that Northern prepare the following:
-
|
Clear cut the area of the first 5 year pit
|
-
|
Carry a detailed survey of the topography of the whole site with differential GPS
|
-
|
Carry out metallurgical testing at pilot plant level
|
-
|
Carry out infill of 10 to 12 holes of 50 to 100 meters in the initial pit area
|
-
|
Carry out exploration drilling within 5 km of the actual known deposit
|
-
|
Review environmental aspects and secure all required permit and authorization
|
-
|
Prepare a GIS including all magnetic surveys, available mapping for exploration
|
-20-
The budget for the next phase of work is as follows:
Bench scale pilot plant testing | $ 100,000 | |
Exploration and infill diamond drilling | $ 400,000 | |
Pre-feasibility study | $ 250,000 | |
Environmental and permitting | $ 500,000 | |
TOTAL | $ 1,250,000 |
Exploration and Development
Since the original completion of the Technical Report in July 2010 (and prior to its revision in February 2011), the Corporation has completed a 2,900 meter infill and expansion drill program. The results of QA/QC assaying and analysis are still being awaiting and once received, the results will be compiled, analysed and released.
The Corporation has also retained SGS to complete a pre-feasibility study as well as metallurgical testing and this work is underway with completion scheduled for the second quarter of 2011. It is expected that metallurgical testing will be followed by pilot plant testing at SGS Lakefield in the third quarter of 2011.
Knight Piesold has been retained to manage the environmental and mine permitting process which is also underway and is expected to be completed by the end of 2011.
In accordance with General Instruction B.2 of Form 8-K, the information in this report, including the exhibit attached hereto, shall not be deemed “filed” for purposes of Section 18 of the Securities Exchange Act of 1934, as amended (the “Exchange Act”), nor shall such information be deemed incorporated by reference in any filing under the Securities Act of 1933, as amended, or the Exchange Act, except as shall be expressly set forth by specific reference in such a filing.
SIGNATURES
Pursuant to the requirements of the Securities Exchange Act of 1934, the registrant has duly caused this report to be signed on its behalf by the undersigned hereunto duly authorized.
Industrial Minerals, Inc.
|
|||
Dated March 3, 2011
|
By:
|
![]() |
|
Gregory B. Bowes
|
|||
Chief Executive Officer and Chief Financial Officer
|
-21-