Attached files
file | filename |
---|---|
8-K - 8-K - Smart Sand, Inc. | snd-20200909.htm |

September 2020 Barclays Presentation

Disclaimer Forward-Looking Statements This presentation contains forward-looking statements within the meaning of the federal securities laws. Statements that are predictive in nature, that depend upon or refer to future events or conditions or that include the words “believe,” “expect,” “anticipate,” “intend,” “estimate” and other expressions that are predictions of or indicate future events and trends and that do not relate to historical matters identify forward-looking statements. Our forward-looking statements include statements about our business strategy, our industry, our future profitability, our expected capital expenditures and the impact of such expenditures on our performance, the costs of being a publicly traded corporation and our capital programs. A forward-looking statement may include a statement of the assumptions or bases underlying the forward-looking statement. We believe that we have chosen these assumptions or bases in good faith and that they are reasonable. Factors that could cause our actual results to differ materially from the results contemplated by such forward-looking statements include, but are not limited to (i) large or multiple customer defaults, including defaults resulting from actual or potential insolvencies, (ii) the level of production of crude oil, natural gas and other hydrocarbons and the resultant market prices of crude oil, natural gas, natural gas liquids and other hydrocarbons, (iii) changes in general economic and geopolitical conditions; (iv) competitive conditions in our industry (including the adoption of regional sand), (v) changes in the long-term supply of and demand for oil and natural gas, (vi) actions taken by our customers, competitors and third-party operators, (vii) changes in the availability and cost of capital, (viii) our ability to successfully implement our business plan, (ix) our ability to complete growth projects on time and on budget, (x) the price and availability of debt and equity financing (including changes in interest rates), (xi) changes in our tax status, (xii) technological changes, (xiii) operating hazards, natural disasters, pandemics, weather-related delays, casualty losses and other matters beyond our control, (xiv) the effects of existing and future laws and governmental regulations (or the interpretation thereof), (xv) failure to secure or maintain contracts with our largest customers or non-performance of any of those customers under the applicable contract, (xvi) our ability to collect our accounts receivable, (xvii) the effects of current and future litigation, and such other factors discussed or referenced in the “Risk Factors” and "Management's Discussion and Analysis of Financial Condition and Results of Operations“ sections of the Form 10- K and the Form 10-Q filed by the Company with U.S Securities and Exchange Commission (the “SEC”) on February 26, 2020 and August 5, 2020, respectively. You should not place undue reliance on our forward-looking statements. Although forward-looking statements reflect our good faith beliefs at the time they are made, forward-looking statements involve known and unknown risks, uncertainties and other factors, including the factors described in the preceding paragraph, which may cause our actual results, performance or achievements to differ materially from anticipated future results, performance or achievements expressed or implied by such forward-looking statements. You should also carefully consider the statements under the heading “Note About Forward-Looking Statements” in the Annual Report on Form 10-K for the year ended December 31, 2019. Any forward-looking statement speaks only as of the date on which such statement is made, and we undertake no obligation to publicly update or revise any forward-looking statement, whether as a result of new information, future events, changed circumstances or otherwise, unless required by law. In this presentation, assumptions were made with respect to industry performance, general business and economic conditions and other matters. Any estimates contained in these analyses, whether expressed or implied, are based on estimates and are not necessarily indicative of actual values or predictive of future results or values, which may be significantly more or less favorable than as set forth herein. The Company reserves the right to change any or all of the estimates included herein whether as a result of any changes in the above referenced information, market factors or otherwise. Industry and Market Data This presentation has been prepared by the Company and includes market data and other statistical information from third-party sources, including independent industry publications, or other published independent sources. Although the Company believes these third-party sources are reliable as of their respective dates, the Company has not independently verified the accuracy or completeness of this information. 1

Disclaimer (cont’d) Reserves Mineral resources and reserves are typically classified by confidence (reliability) levels based on the level of exploration, consistency and assurance of geologic knowledge of the deposit. This classification system considers different levels of geoscientific knowledge and varying degrees of technical and economic evaluation. Mineral reserves are derived from in situ resources through application of modifying factors, such as mining, analytical, economic, marketing, legal, environmental, social and governmental factors, relative to mining methods, processing techniques, economics and markets. In estimating our reserves, our independent reserve engineer does not classify a resource as a reserve unless that resource can be demonstrated to have reasonable certainty to be recovered economically in accordance with the modifying factors listed above. “Reserves” are defined by SEC Industry Guide 7 as that part of a mineral deposit that could be economically and legally extracted or produced at the time of the reserve determination. Industry Guide 7 defines “proven (measured) reserves” as reserves for which (a) quantity is computed from dimensions revealed in outcrops, trenches, workings or drill holes; grade and/or quality are computed from the results of detailed sampling and (b) the sites for inspection, sampling and measurement are spaced so closely and the geologic character is so well defined that size, shape, depth and mineral content of reserves are well-established. Industry Guide 7 defines “probable (indicated) reserves” as reserves for which quantity and grade and/or quality are computed from information similar to that used for proven (measured) reserves, but the sites for inspection, sampling, and measurement are farther apart or are otherwise less adequately spaced. The degree of assurance, although lower than that for proven (measured) reserves, is high enough to assume continuity between points of observation. Non-GAAP Information This presentation also contains information about the Company’s EBITDA, Adjusted EBITDA, and contribution margin, which are not measures derived in accordance with U.S. generally accepted accounting principles (“GAAP”) and which exclude components that are important to understanding the Company’s financial performance. We define EBITDA as our net income, plus (i) depreciation, depletion, and amortization expense; (ii) income tax expense (benefit); (iii) interest expense and (iv) franchise taxes. We define Adjusted EBITDA as EBITDA, plus (i) gain or loss on sale of fixed assets or discontinued operations, (ii) integration and transition costs associated with specified transactions, (iii) equity compensation, (iv) acquisition and development costs, (v) non-recurring cash charges related to restructuring, retention and other similar actions, (vi) earn-out, contingent consideration obligations and other acquisition and development costs, (vii) non-cash charges and unusual or non-recurring charges. We believe that our presentation of EBITDA and Adjusted EBITDA will provide useful information to investors in assessing our financial condition and results of operations. Net income is the GAAP measure most directly comparable to EBITDA and Adjusted EBITDA. EBITDA and Adjusted EBITDA should not be considered alternatives to net income presented in accordance with GAAP. Because EBITDA and Adjusted EBITDA may be defined differently by other companies in our industry, our definition of EBITDA and Adjusted EBITDA may not be comparable to similarly titled measures of other companies, thereby diminishing its utility. We also use contribution margin, which we define as total revenues less costs of goods sold excluding depreciation, depletion and accretion of asset retirement obligations, to measure our financial and operating performance. Contribution margin excludes other operating expenses and income, including costs not directly associated with the operations of our business such as accounting, human resources, information technology, legal, sales and other administrative activities. We believe contribution margin is a meaningful measure because it provides an operating and financial measure of our ability to generate margin in excess of our operating cost base. 2

Company Highlights The Right Operating Model ▪ Oakdale is one of the largest single operating Northern White raw frac mines in United States ▪ 300+ million tons of high quality fine mesh reserves with 5.5 million tons current operating capacity ▪ 14+ miles of rail track servicing Oakdale from two Class I rail lines ▪ Multi-unit train capable with access to all operating basins ▪ Low operating cost structure ▪ Mining, processing, and shipping all done at one location ▪ Large single mine sites on rail dominate other bulk commodity business models ▪ Sustainable long-term supply and logistics advantage ▪ Combination of large, high quality reserve base, low cost operations, and ability to ship large quantities of sand efficiently and sustainably to all operating basins ▪ Mine to Wellsite Solutions Capabilities ▪ Through our Van Hook Terminal, our network of third party terminal partners, and our SmartSystemsTM wellsite storage solutions, we can offer sustainable, efficient sand supply chain support for our customers The Right Sand ▪ ~80% of Oakdale’s reserves are fine mesh (40/70 and 100 Mesh) ▪ Fine mesh raw frac sand represents over 80% of the current demand for raw frac sand currently ▪ Quality Matters ▪ Northern White sand vs regional sand is a higher quality product that we believe can lead to better long-term well results for oil and gas producers ▪ Higher crush strength ▪ Better conductivity ▪ Cleaner / less turbidity The Right Capital Structure ▪ Prudent capital structure with lowest leverage levels in the proppant industry (0.2x Net Debt / EBITDA) ▪ High insider ownership that aligns management with investors (~15% owned by CEO, ~50% owned by insiders) 3

Vertical Integration – A Key Differentiator Smart Sand’s Business Offerings Premium Northern White Reserve Gigantic Rail Capacity Terminal & Forward Staging Management Last Mile Logistics Wellsite Storage Solutions Large Finer Mesh Northern White Reserve Dual-served (CP & UP) Planning ahead reduces risks Safe and reliable Wellsite storage Consistent high-quality proppant Over 14 miles of track space Redundancy in the supply chain Helps eliminate demurrage Direct to the blender delivery 5.5mm tons annual production capability Unit train capable Avoid trucking congestion Smaller fleet and more turns per day Realtime inventory control 4
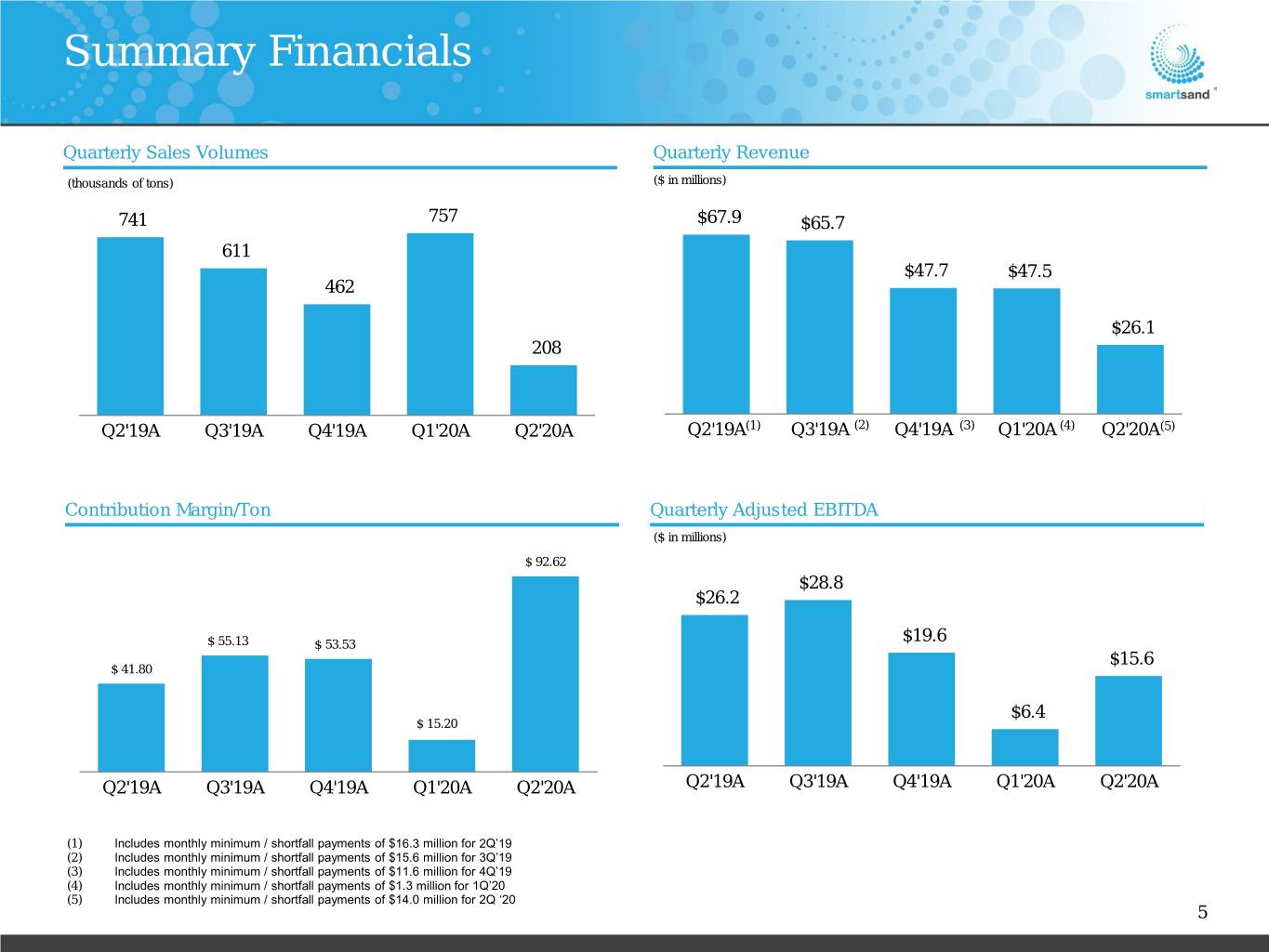
Summary Financials Quarterly Sales Volumes Quarterly Revenue (thousands of tons) ($ in millions) 741 757 $67.9 $65.7 611 $47.7 $47.5 462 $26.1 208 Q2'19A Q3'19A Q4'19A Q1'20A Q2'20A Q2'19A(1) Q3'19A (2) Q4'19A (3) Q1'20A (4) Q2'20A(5) Contribution Margin/Ton Quarterly Adjusted EBITDA ($ in millions) $ 92.62 $28.8 $26.2 $19.6 $ 55.13 $ 53.53 $15.6 $ 41.80 $6.4 $ 15.20 Q2'19A Q3'19A Q4'19A Q1'20A Q2'20A Q2'19A Q3'19A Q4'19A Q1'20A Q2'20A (1) Includes monthly minimum / shortfall payments of $16.3 million for 2Q’19 (2) Includes monthly minimum / shortfall payments of $15.6 million for 3Q’19 (3) Includes monthly minimum / shortfall payments of $11.6 million for 4Q’19 (4) Includes monthly minimum / shortfall payments of $1.3 million for 1Q’20 (5) Includes monthly minimum / shortfall payments of $14.0 million for 2Q ‘20 5
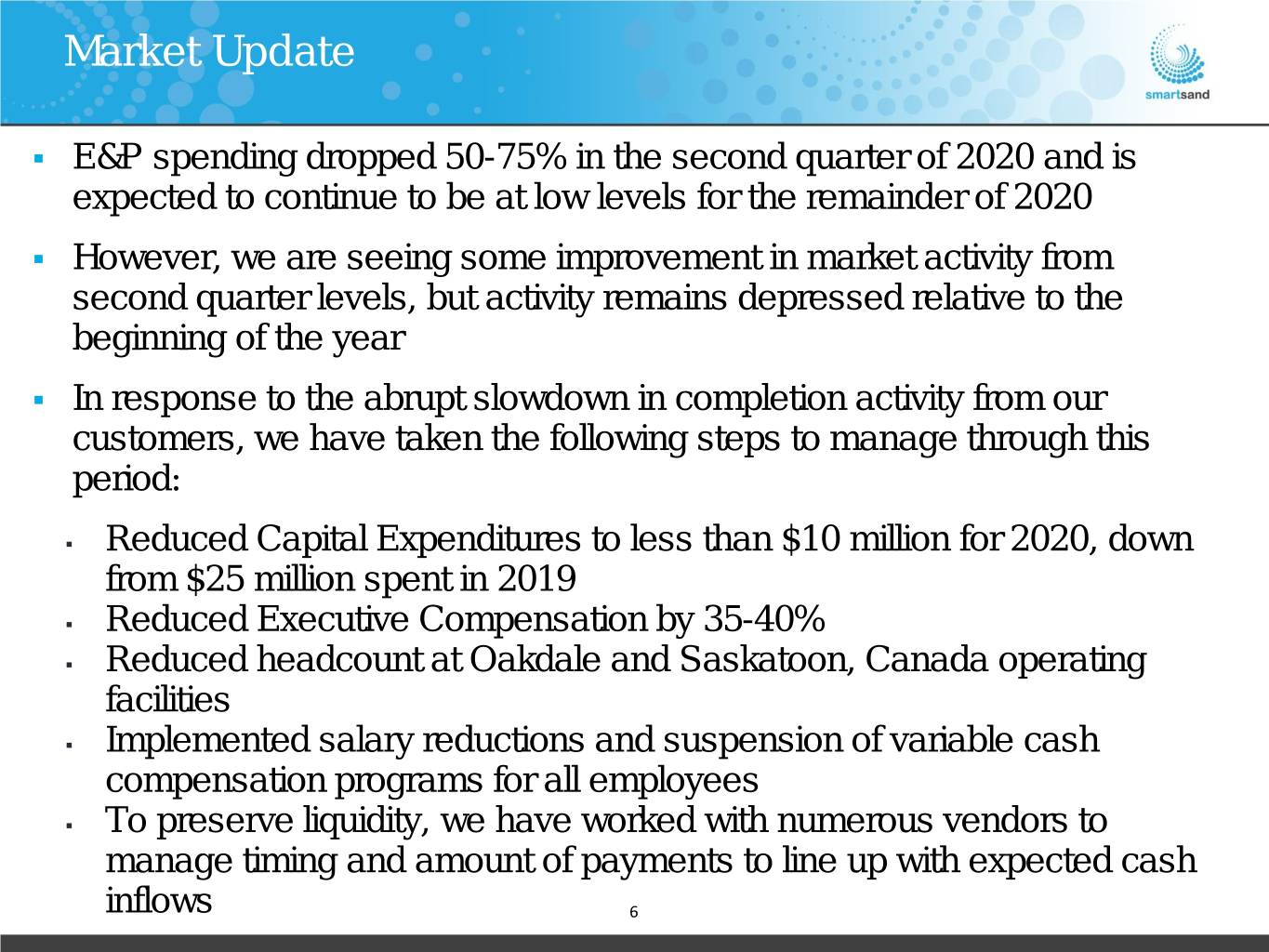
Market Update ▪ E&P spending dropped 50-75% in the second quarter of 2020 and is expected to continue to be at low levels for the remainder of 2020 ▪ However, we are seeing some improvement in market activity from second quarter levels, but activity remains depressed relative to the beginning of the year ▪ In response to the abrupt slowdown in completion activity from our customers, we have taken the following steps to manage through this period: ▪ Reduced Capital Expenditures to less than $10 million for 2020, down from $25 million spent in 2019 ▪ Reduced Executive Compensation by 35-40% ▪ Reduced headcount at Oakdale and Saskatoon, Canada operating facilities ▪ Implemented salary reductions and suspension of variable cash compensation programs for all employees ▪ To preserve liquidity, we have worked with numerous vendors to manage timing and amount of payments to line up with expected cash inflows 6

The Value of Northern White Sand ▪ A recent study by Rystad Energy has linked proppant type to decreased production and profitability – while local sand has been cheaper to deliver to the wellsite than northern white sand, the loss in cash flow from lower production as a result of using the inferior product is exceeding the cost savings ▪ The recent study examined 800 wells across 7 operators in the Permian basin ▪ 50% of operators have seen a negative economic impact as compared to wells completed with northern white sand and up to 85% are on the verge of seeing a negative economic impact on wells with less than one year of production ▪ The impact has been seen in both the Midland and Delaware basins from using lower cost and lower quality in-basin sand rather than northern white sand on cash flows assuming oil prices remain at $40/bbl 7
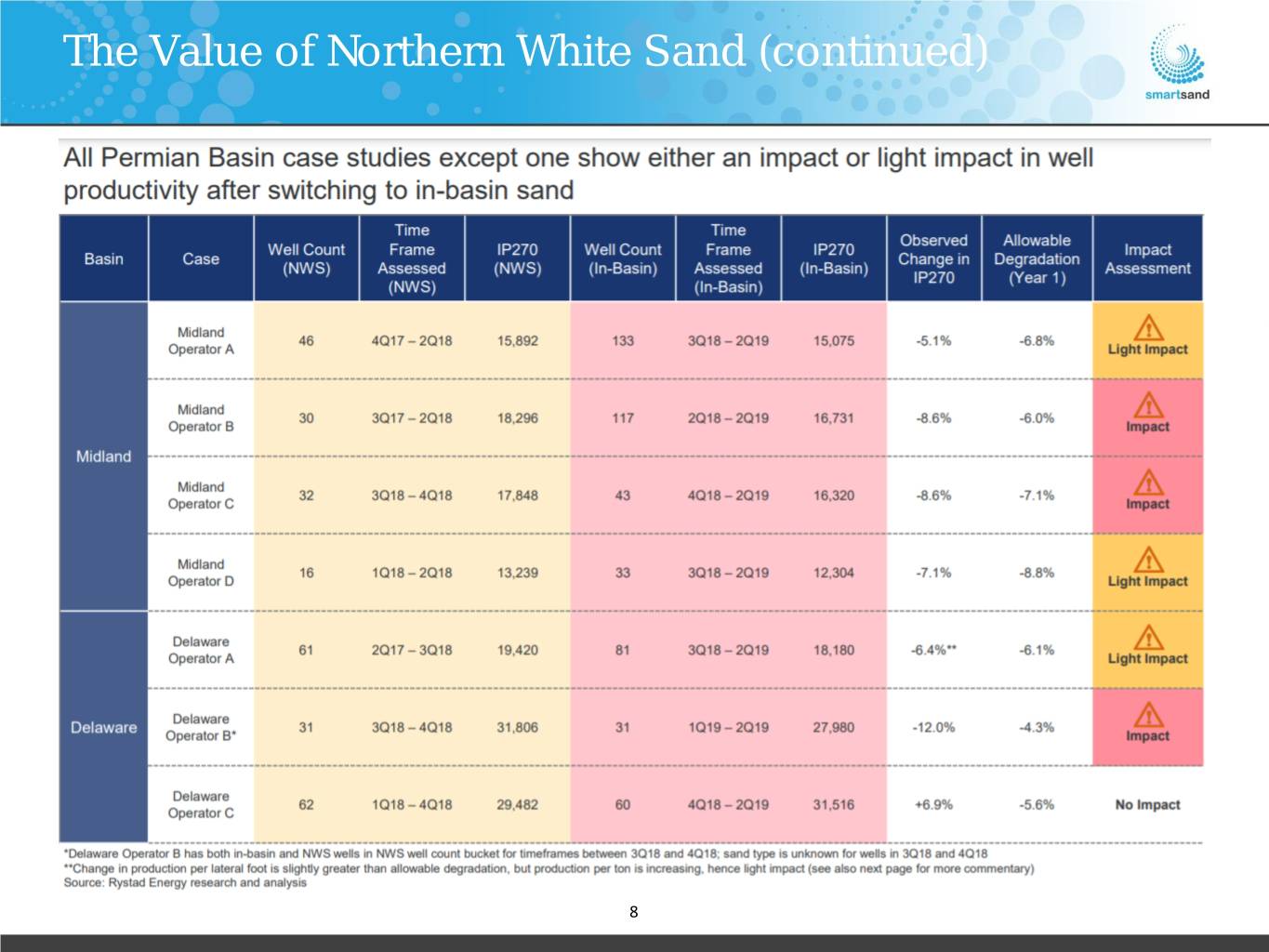
The Value of Northern White Sand (continued) 8
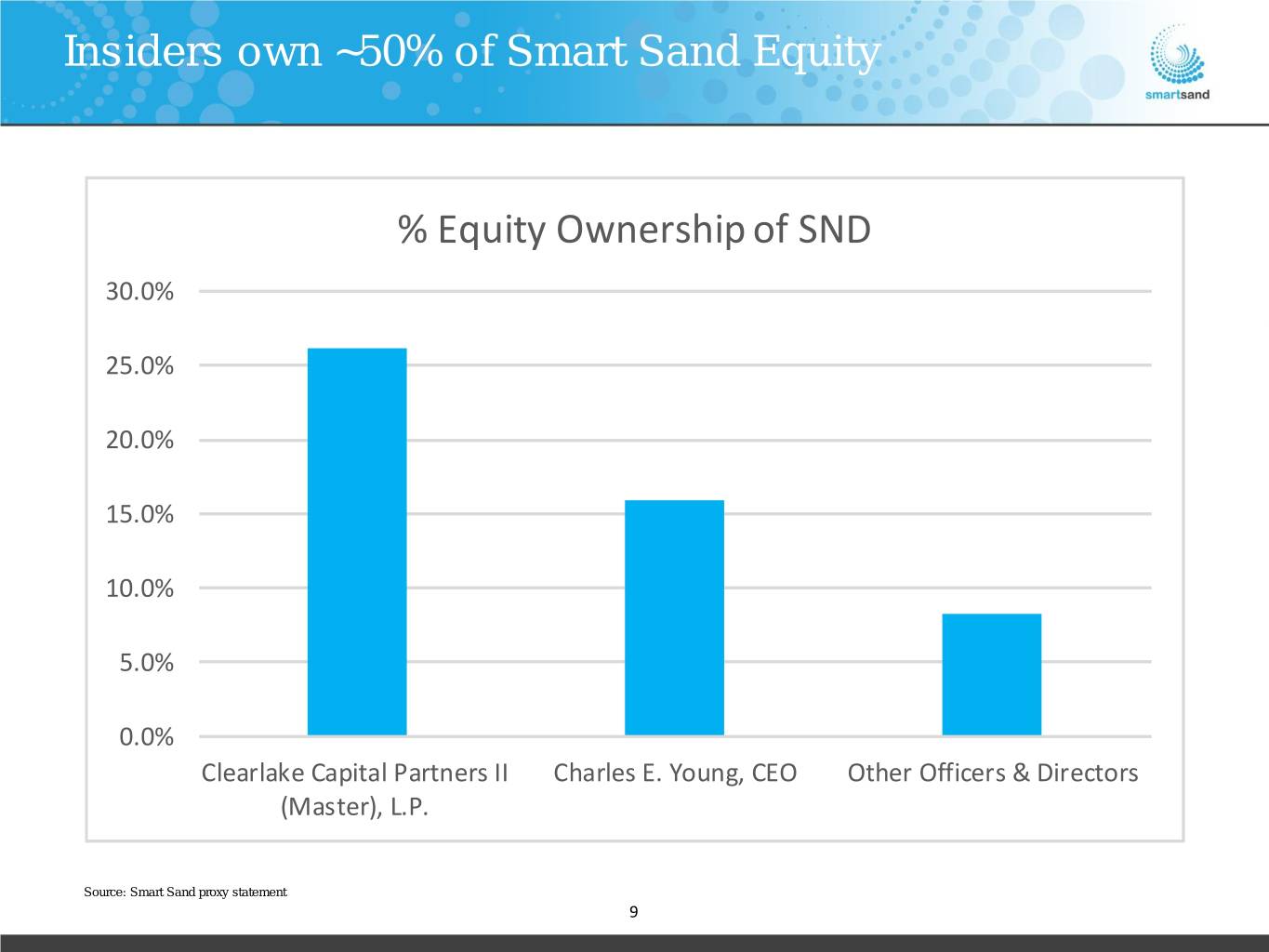
Insiders own ~50% of Smart Sand Equity % Equity Ownership of SND 30.0% 25.0% 20.0% 15.0% 10.0% 5.0% 0.0% Clearlake Capital Partners II Charles E. Young, CEO Other Officers & Directors (Master), L.P. Source: Smart Sand proxy statement 9

Industry Overview 10

Industry Trends Continue to Support Increasing Use of Frac Sand per Well Source: Spears and Associates 2Q 2020 Proppant Market Report. 11

Industry Trends Continue to Support Increasing Use of Frac Sand per Well Lateral lengths continue to get longer Source: Spears and Associates 2Q 2020 Proppant Market Report. 12
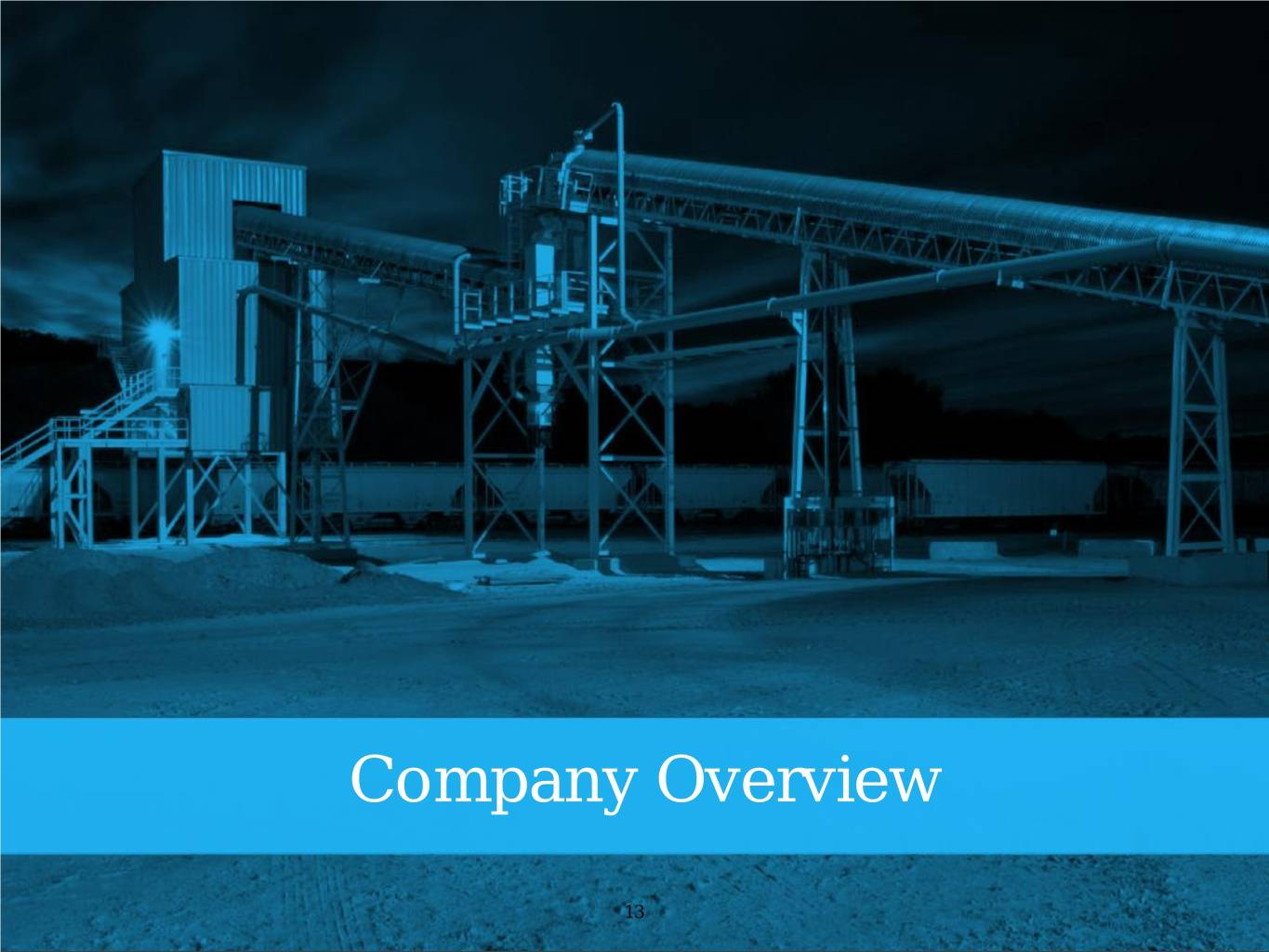
Company Overview 13
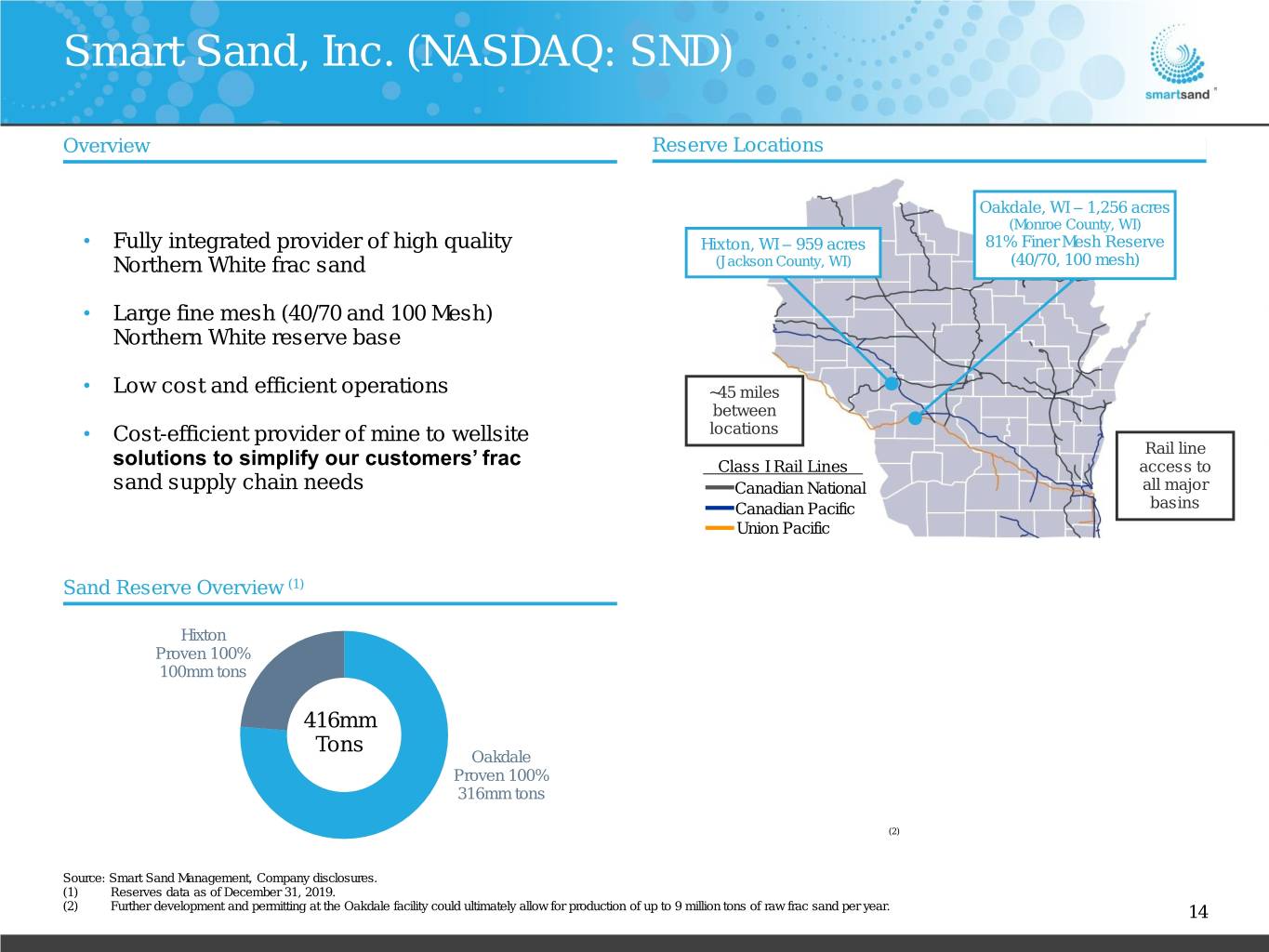
Smart Sand, Inc. (NASDAQ: SND) Overview Reserve Locations Oakdale, WI – 1,256 acres (Monroe County, WI) • Fully integrated provider of high quality Hixton, WI – 959 acres 81% Finer Mesh Reserve Northern White frac sand (Jackson County, WI) (40/70, 100 mesh) • Large fine mesh (40/70 and 100 Mesh) Northern White reserve base • Low cost and efficient operations ~45 miles between • Cost-efficient provider of mine to wellsite locations Rail line solutions to simplify our customers’ frac Class I Rail Lines access to sand supply chain needs Canadian National all major Canadian Pacific basins Union Pacific Sand Reserve Overview (1) Hixton Proven 100% 100mm tons 416mm Tons Oakdale Proven 100% 316mm tons (2) Source: Smart Sand Management, Company disclosures. (1) Reserves data as of December 31, 2019. (2) Further development and permitting at the Oakdale facility could ultimately allow for production of up to 9 million tons of raw frac sand per year. 14
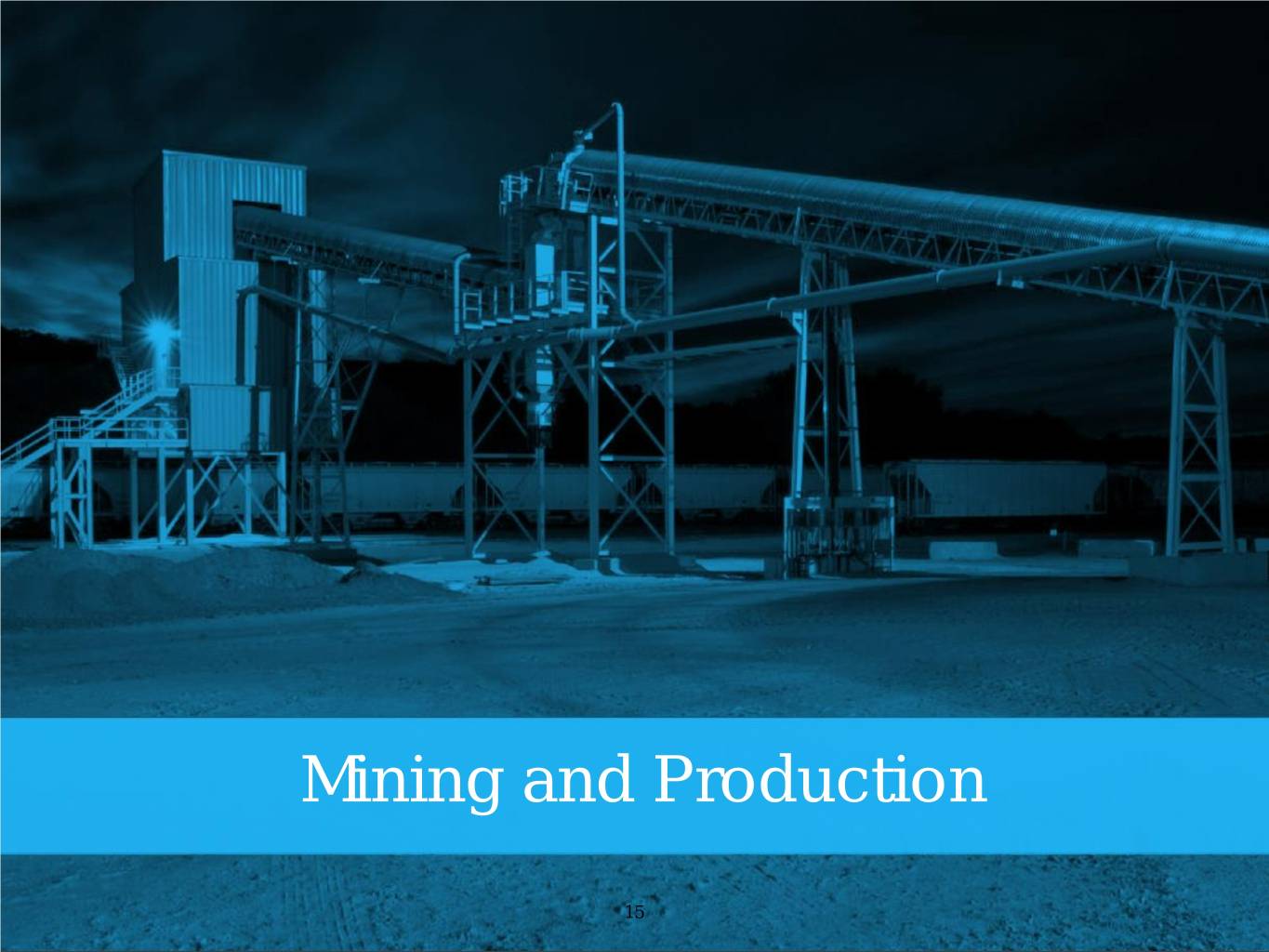
Mining and Production 15

Cost-Effective, Differentiated Process On-site Mining / Excavation Conveyer Belt to On-site Wet Plant Wet Plant Cleans and Sorts Product Dry Plant Dries and Sorts Product Unit Trains Deliver Dry Sand to Basins ◼ Low Cost Structure Due to Several Key Attributes: − Low royalty rates ($0.50 per ton sold on 20/70 sand) − Higher mining yields due to balance of coarse and fine mineral reserve deposits − Minimal trucking required; reserves, processing plants, and rail facilities are centralized ◼ Evaluating Other Initiatives to Reduce Mining and Operating Costs 16

Oakdale Facility: High Quality Northern White Raw Frac Sand in an Efficient Configuration 17
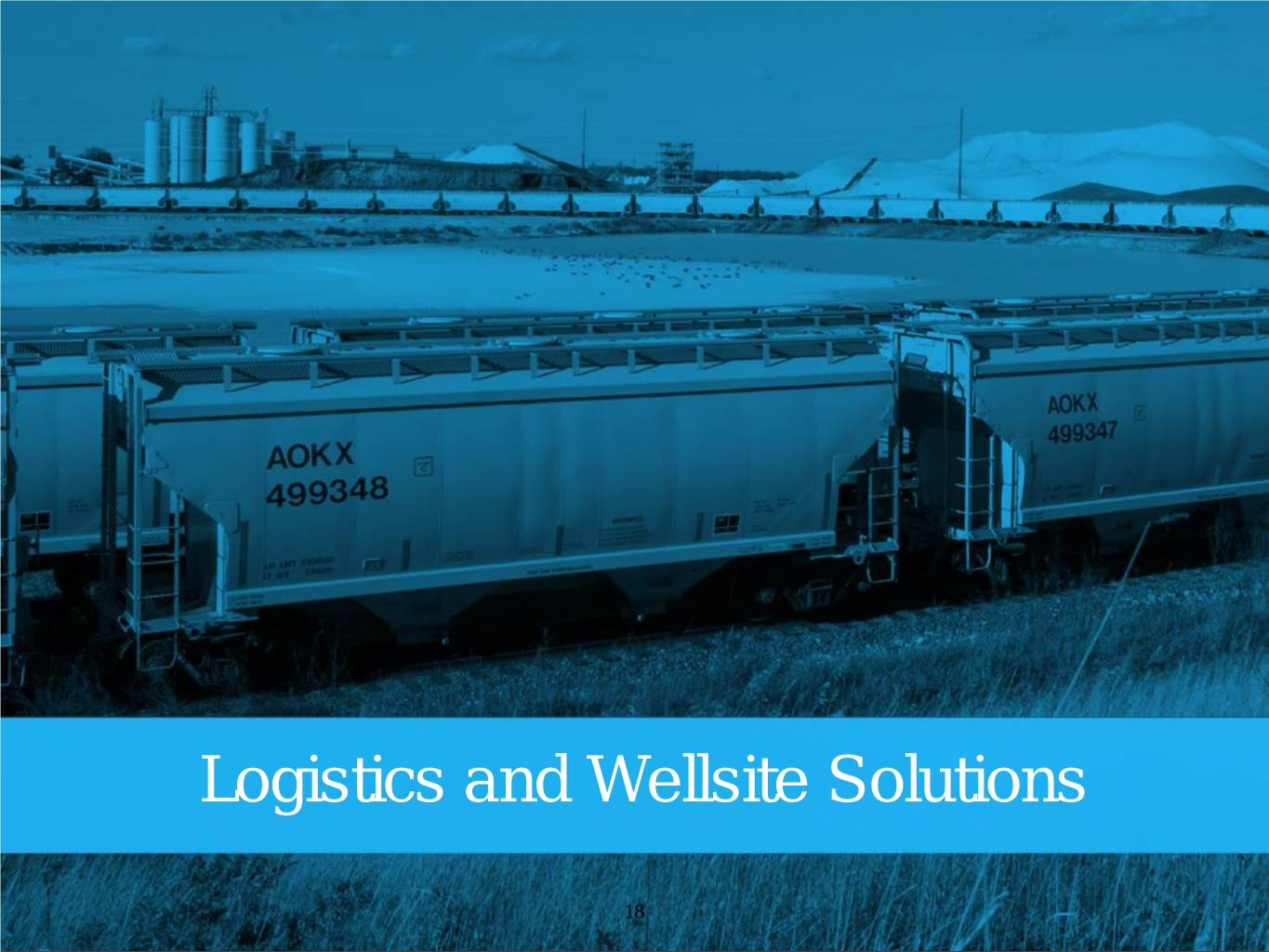
Logistics and Wellsite Solutions 18

Expansive Logistics Capabilities Key Logistical Advantages Highly Competitive Delivery Capabilities ◼ Dual Served Class I Rail Access – onsite service on Canadian Pacific rail line coupled with nearby terminal on Union Pacific rail line Van Hook allows access to multiple oil and gas plays, avoids interchange fees Terminal on local short-hauls and allows opportunity to reduce freight costs through competition ◼ Unit Train Capability – Reduces customer product delivery time and costs (see below) ◼ In Basin Terminal – Van Hook terminal in North Dakota provides competitive advantage for delivery of frac sand into the Bakken ◼ Wellsite Storage Solutions - Portable wellsite storage solutions provide customers with a proppant management system designed to help control demurrage, drive down costs and improve safety Manifest Route vs. Unit Train Route Benefits Manifest Route Unit Train Route Certain other Stop Stop Stop Basin Basin Competitors 1 2 3 Generally 14+ days Generally <5 days Increased landed cost and time Better utilization of railcars, predictable Unit Trains Require Approximately One-third of the Time of Manifest Trains and Significantly Improve Reliability 19

Van Hook Terminal ◼ Location: Van Hook, ND ◼ Commenced operations in April 2018 ◼ We shipped 46% of our volumes year to date in 2020 through this terminal as customers recognized the value of Van Hook’s strategic location and efficient logistics solutions Van Hook Terminal 20

SmartSystemsTM Wellsite Storage Solutions Features • Transported using specialized trailer for unassisted setup in five minutes. • Tri-axle trailer design with reinforced steel frame and remote control operation. • Direct to blender delivery, controls dust, stops and starts proppant flow. • Passive & Active onboard positive dust collection. • Five chute positions offering unparalleled site layout options. • Up to five SmartDepotTM silos delivering ~1,000 tons direct to the blender hopper. • Service platforms for safe access to service areas. • Six external pneumatic fill pipes for simultaneous loading. • The system is self-powered and requires no generator. • Hydraulic stabilizers to maintain stability. Focus on Providing Safety and Logistics A Proven & Environmental and Last Mile Tested Product Stewardship Advantages 21

Our SmartSystemsTM Storage vs. the Competition Competitive Options SmartSystemsTM Storage Equipment Smart Sand: Silos: • Multiple Size Options With Custom • Belts Required, No Direct To Configurations Blender Offload • Engineered and Designed Specifically • Dust Can Be a Concern For Sand Storage on the Well Site • Large Footprint • Smallest Footprint in the Industry • Not Fully Integrated • Fast Mobilization and Demobilization Times • Direct to Blender Offload • Dust Control Box Design: • Single & Dual Blender Designs • Limited Tonnage Per Truck • No Moving Parts Resulting In Poor Optimization • Moving Equipment Causing Safety Concerns • Forklifts and Safe Spaces Required • Extremely Large Footprint Hybrid: • Completion Conveyor Design With Inefficient Delivery System To The Blender • Dust Can Be a Concern • Large Footprint • Not Fully Integrated 22

SmartPathTM Proppant Handling System ▪ SmartPathtm is a patent-pending mobile transloading system, designed to work with bottom dump trailers, featuring a drive over conveyor, surge bin, dust collection system, on-board generator, and redundant conveyance circuits for transferring proppant into SmartDepottm silos ▪ The SmartPath coupled with our Smart Depot portable silos will provide pressure pumpers and E&Ps a very efficient and flexible proppant delivery and storage system at the wellsite ▪ Key Features: ▪ Self-contained - requires no external equipment in order to deploy or operate ▪ Drive over conveyor is capable to unloading at a rate of up to 5 tons per minute, pneumatic to the silos at a rate of up to 2 tons per minute ▪ Double tank discharge system for longer life than traditional rotary airlocks ▪ Generator meets EPA Tier 4 emissions standard ▪ OSHA/OHS ladders and platforms for service and maintenance ▪ Controls and wiring rated for all weather operation, -40°F to 100°F temperatures ▪ DOT/TC approved axles, abs brakes, running lights, and rear bumper 23

Smart Sand Summary Sustainable Operating Model ▪ Large, high quality reserve base ▪ Low cost operations ▪ Efficient and sustainable logistics capabilities with access to all operating basins Prudent Capital Structure ▪ Low leverage levels (0.2x Net Debt / TTM EBITDA) allow Company the ability to manage through all operating cycles ▪ Well positioned to participate in consolidation opportunities should they present themselves Committed Management / Ownership ▪ High insider ownership that aligns management with investors (~15% owned by CEO, ~50% owned by insiders) to focus on long-term value creation 24

Appendix 25

Committed to Highest Corporate Standards ◼ Management maintains close dialogue with customers regarding the oil and gas industry’s rigorous regulatory environment Legal & ◼ ISO registered Quality System and Environmental Management System in Regulatory place ◼ Minimal environmental and community impact: on-site rail, careful mine design, moderated trucking and extensive use of conveyors ◼ A member of the Wisconsin Industrial Sand Association (WISA), a selective industry group promoting high standards for safety, Environmental sustainability and environmental performance ◼ Participant in Wisconsin’s Green Tier program, demonstrating voluntary commitment to high environmental performance through projects that improve the environment and promote good community relations ◼ Our first priority is a safe work environment. Dedicated safety staff, continual Safety training and daily inspections are part of our MSHA approved safety plan Smart Sand is committed to providing a safe working environment and upholding the highest levels of environmental stewardship 26

EBITDA Reconciliation Year ended December 31, ($ in thousands) 2015 2016 2017 2018 2019 Net income (loss) $4,990 $10,379 $21,526 $18,688 $31,623 Depreciation, depletion, accretion and amortization 5,318 6,445 7,300 18,165 27,135 Income tax (benefit) expense 4,129 9,394 (2,809) 5,122 7,809 Interest expense 7,826 8,436 700 2,320 3,626 Franchise taxes 35 21 339 442 285 EBITDA $22,298 $34,675 $27,056 $44,737 $70,478 (Gain) Loss on sale of fixed assets 39 (59) 253 321 (42) Integration and transition costs – – 16 – – Initial public offering related costs (1) 221 725 – – – Equity compensation (2) 792 1,426 1,652 2,670 2,755 Acquisition and development costs (3) 76 – 845 (218) (3,047) Non-cash impairment of goodwill and other intangible asset (4) – – – 17,835 15,542 Cash charges related to restructuring and retention – – 279 674 137 Non-cash charges (5) 469 21 514 (26) 687 Loss on extinguishment of debt – 1,051 – – 561 Adjusted EBITDA $23,881 $37,839 $30,615 $65,993 $87,071 (1) For the year ended December 31, 2016, represents IPO-related bonuses. For the year ended December 31, 2015, represents expenses related to previous IPO activities. (2) Represents the non-cash expenses for stock-based awards issued to our employees and employee stock purchase plan compensation expense. (3) Represents costs incurred related to the business combinations and current development project activities. The year ended December 31, 2019 includes $3,272 decrease in the estimated fair value of our contingent consideration related to the acquisition of Quickthree and $225 related to development project activities. The year ended December 31, 2018 includes $1,858 decrease in the estimated fair value of our contingent consideration related to the acquisition of Quickthree, partially offset by $1,146 of costs related to the acquisition of Quickthree and $494 related to development project activities. (4)The $17.8mm charge in 2018 relates primarily to the decline in our stock price in 2018 and the relationship between the resulting market capitalization and the equity recorded on our balance sheet. During the year ended December 31, 2019, we recorded impairment loss of $15.5 million, of which $7.6 million relates to our finite-lived developed technology intangible assets and $7.9 million relates to our Hixton, Wisconsin property. The impairment of the finite-lived intangible assets is from our developed technology allocated to the Quickload acquired in connection with the acquisition of Quickthree in 2018. We are developing and testing a new transload technology and no longer plan to actively market the Quickload and as such, all developed technology intangible assets related to the Quickload were fully impaired during the third quarter of 2019. In the fourth quarter of 2019, we determined that the full amount recorded on the balance sheet which relate to the Hixton, Wisconsin property may not be recoverable as we have no current plans to further develop the site. (5) Represents accretion of asset retirement obligations and loss on derivatives. 27

EBITDA Reconciliation Quarter ended ($ in thousands) 6/30/2019 9/30/2019 12/31/2019 3/31/2020 6/30/2020 Net income (loss) $14,276 $10,887 $2,388 ($84) $4,640 Depreciation, depletion, accretion and amortization 6,590 6,992 7,250 5,487 5,450 Income tax expense (benefit) 3,973 2,608 294 165 3,470 Interest expense 997 969 679 480 619 Franchise taxes 93 56 51 56 94 EBITDA $25,929 $21,512 $10,662 $6,104 $14,273 Gain (loss) on sale of fixed assets (1) (15) (1) – 275 Equity compensation (1) 685 663 708 926 842 Acquisition and development costs (2) (577) (1,208) (315) (822) 144 Non-cash impairment of goodwill and other intangible asset (3) – 7,628 7,914 – – Cash charges related to restructuring and retention 41 – 55 82 – Accretion of asset retirement obligations 166 178 64 75 76 Loss on extinguishment of debt – – 561 – – Adjusted EBITDA $26,243 $28,758 $19,648 $6,365 $15,610 (1) Represents the non-cash expenses for stock-based awards issued to our employees and employee stock purchase plan compensation expense. (2) Represents costs incurred related to the business combinations and current development project activities. (3) The charge in the quarter ending 9/30/19 related to specific developed technology allocated to the Quickload - The Company is developing and testing a new SmartPathTM transload technology and no longer plans to actively market the Quickload system and as such, all developed technology intangible assets related to the Quickload have been impaired. In the fourth quarter of 2019, we determined that the full amount recorded on the balance sheet which relate to the Hixton, Wisconsin property may not be recoverable as we have no current plans to further develop the site. 28

Contribution Margin Reconciliation Quarter ended ($ in thousands) 6/30/2019 9/30/2019 12/31/2019 3/31/2020 6/30/2020 Revenue $67,941 $65,690 $47,667 $47,488 $26,106 Cost of goods sold 43,068 38,555 29,793 41,089 11,906 Gross profit 24,873 27,135 17,874 6,399 14,200 Depreciation, depletion, and accretion of asset retirment obligations 6,101 6,547 6,858 5,109 5,065 Contribution margin $30,974 $33,682 $24,732 $11,508 $19,265 Contribution margin per ton $41.80 $55.13 $53.53 $15.20 $92.62 Note: Figures may not tie due to rounding. 29