Attached files
file | filename |
---|---|
S-1/A - S-1/A - Ameresco, Inc. | b79273a2sv1za.htm |
EX-10.5 - EX-10.5 - Ameresco, Inc. | b79273a2exv10w5.htm |
Securities and Exchange Commission. Asterisks denote omissions.
DOE Savannah River Site
Biomass Cogeneration Facility and
K and L Area Heating Plants
Submitted by:
Ameresco Federal Solutions
1820 Midpark Road, Suite C
Knoxville, TN 37921
Under DOE Contract No. DE-AM36-02NT41457
May 11, 2009
Revised Final Proposal May 11, 2009 Ameresco Federal Solutions Page i |
Biomass Cogeneration Facility and Heating Plants Savannah River Site Contract DE-AM36-02NT41457 |
EXECUTIVE SUMMARY |
1 | |||
1.0 ECM 1 DESCRIPTION |
4 | |||
1.1 ECM Summary Schedule DO-4 |
4 | |||
1.2 ECM #1: Biomass Cogeneration Facility |
4 | |||
1.2.1 Detailed Description of ECM |
4 | |||
1.2.1.1 ECM Summary |
4 | |||
1.2.1.2 ECM Design Process |
5 | |||
1.2.1.3 ECM 1 Operation |
17 | |||
1.2.2 Location Affected |
18 | |||
1.2.3 ECM 1 Interface with Government Equipment |
20 | |||
1.2.4 Proposed Equipment |
25 | |||
1.2.5 Expected Lifetime |
25 | |||
1.2.6 Physical Changes to Existing Equipment or Facilities |
25 | |||
1.2.7 Savings Proposed |
25 | |||
1.2.7.1 Annual Project Savings Overview |
25 | |||
1.2.7.2 Annual Energy Baseline Consumption & Costs |
27 | |||
1.2.7.3 Annual Energy Savings Calculations |
30 | |||
1.2.7.4 ECM 1 Performance Measurement |
30 | |||
1.2.8 Utility Interruptions |
34 | |||
1.2.9 Agency Support Required |
34 | |||
1.2.10 Potential Environmental Impact |
34 | |||
1.2.11 ECM Property Ownership |
34 | |||
1.2.12 ECM Project Schedule |
34 | |||
1.3 BAMF Project Components |
35 | |||
1.3.1 BAMF Resource |
35 | |||
1.3.1.1 BAMF Supply |
35 | |||
1.3.1.2 BAMF Pricing |
36 | |||
1.3.1.3 BAMF Acquisition |
36 | |||
1.3.2 BAMF Transportation, Metering, & Delivery |
36 | |||
1.3.2.1 BAMF Transportation & Delivery |
36 | |||
1.3.2.2 BAMF Metering |
36 | |||
1.3.3 BAMF End-Use Project |
37 | |||
1.3.3.1 BAMF End-Use Demand |
37 | |||
1.3.3.2 BAMF End-Use Operations & Maintenance |
37 | |||
2.0 ECM 2 DESCRIPTION |
38 |
Revised Final Proposal May 11, 2009 Ameresco Federal Solutions Page ii |
Biomass Cogeneration Facility and Heating Plants Savannah River Site Contract DE-AM36-02NT41457 |
2.1 ECM Summary Schedule DO-4 |
38 | |||
2.2 ECM #2: Biomass Heating Plants for K& L Areas |
38 | |||
2.2.1 Detailed Description of ECM |
38 | |||
2.2.1.1 ECM Summary |
38 | |||
2.2.1.2 ECM Process Description |
39 | |||
2.2.1.3 ECM Operation |
40 | |||
2.2.2 Location Affected |
41 | |||
2.2.3 ECM 2 Interface with Government Equipment |
42 | |||
2.2.4 Proposed Equipment |
44 | |||
2.2.5 Expected Lifetime |
44 | |||
2.2.6 Physical Changes to Existing Equipment or Facilities |
44 | |||
2.2.7 Savings Proposed |
44 | |||
2.2.7.1 Annual Energy Savings |
46 | |||
2.2.7.2 Annual Energy Baseline Consumption & Costs |
46 | |||
2.2.7.3 Annual Heating Plant Performance |
48 | |||
2.2.8 Utility Interruptions |
49 | |||
2.2.9 Agency Support Required |
49 | |||
2.2.10 Potential Environmental Impact |
49 | |||
2.2.11 ECM Property Ownership |
49 | |||
2.2.12 ECM Project Schedule |
50 | |||
3.0 ENVIRONMENTAL IMPACT OVERVIEW |
51 | |||
3.1 Overview of Environmental Benefits |
51 | |||
3.2 Overview of Environmental Permitting & Assessment |
51 | |||
4.0 ECM PERFORMANCE MEASUREMENT |
56 | |||
4.1 Overview of Proposed Annual Savings |
56 | |||
4.2 M&V Plan Executive Summary |
56 | |||
4.3 Whole Project Data / Global Assumptions |
57 | |||
4.3.1 Risk and Responsibility |
57 | |||
4.3.2 Energy, Water, and Operations and Maintenance (O&M) Rate Data |
57 | |||
4.3.3 Schedule & Reporting for Verification Activities |
58 | |||
4.3.4 Status of Utility Company Incentives |
59 | |||
4.4 ECM-Specific M&V Plan and Savings Calculation Methods |
59 | |||
4.4.1 Overview of ECM Specific M&V Plans |
59 | |||
4.4.1.1 ECM 1: Biomass Cogeneration Facility |
59 | |||
4.4.1.2 ECM 2: Biomass Heating Plants for K& L Areas |
59 |
Revised Final Proposal May 11, 2009 Ameresco Federal Solutions Page iii |
Biomass Cogeneration Facility and Heating Plants Savannah River Site Contract DE-AM36-02NT41457 |
4.4.2 Energy and Water Baseline Development |
59 | |||
4.4.3 Proposed Energy & Water Savings Calculations and Methodology |
59 | |||
4.4.4 Operations and Maintenance Cost Savings |
59 | |||
5.0 MANAGEMENT APPROACH |
60 | |||
5.1 Integrated Management Review Team (IMRT) |
60 | |||
5.2 Ameresco Management Approach |
61 | |||
5.2.1 Ameresco Corporate Management Team |
63 | |||
5.2.2 Program Manager |
65 | |||
5.2.3 Engineering |
65 | |||
5.2.4 Business Operations |
65 | |||
5.2.5 Safety and Risk Management |
65 | |||
5.2.5.1 Site Safety Management |
65 | |||
5.2.6 Construction |
66 | |||
5.2.6.1 Subcontract Management |
66 | |||
5.2.6.2 Construction Management |
66 | |||
5.2.7 Site Operations |
67 | |||
5.2.7.1 Operations and Maintenance Responsibilities |
67 | |||
5.2.7.2 Repair & Replacement Responsibilities |
71 | |||
5.3 ECM Training |
71 | |||
5.4 Risk/Responsibility Matrix |
72 | |||
6.0 PROPOSAL PRICING INFORMATION |
85 | |||
6.1 Interest Rate |
85 | |||
6.2 Finance Procurement Price |
85 | |||
6.3 Sales Tax |
86 | |||
6.4 Property Tax |
87 | |||
6.5 Insurance |
87 | |||
6.6 Payment/Term |
87 | |||
6.7 Cancellation/Termination/Buyout |
88 | |||
6.8 Prepayments/Buydowns |
89 | |||
6.9 Protection of Financiers Interest |
89 | |||
6.10 Security Interest in ECM Equipment |
90 | |||
6.11 Assignment of Claims |
90 | |||
6.12 Title to and Responsibility for Contractor-Installed Property |
90 | |||
6.13 Construction Milestones |
91 |
Revised Final Proposal May 11, 2009 Ameresco Federal Solutions Page iv |
Biomass Cogeneration Facility and Heating Plants Savannah River Site Contract DE-AM36-02NT41457 |
Appendix F is presented in Volume III.
APPENDIX A GEOTECHNICAL REPORT |
A-1 | |||
APPENDIX B FLOW DIAGRAMS FOR BIOMASS COGENERATION PLANT |
B-1 | |||
APPENDIX C EQUIPMENT LIST & MANUFACTURER INFORMATION SHEETS |
C-1 | |||
APPENDIX D DESIGN STANDARDS MATRIX |
D-1 | |||
APPENDIX E PROJECT SCHEDULE |
E-1 | |||
APPENDIX F PRELIMINARY DESIGN DRAWINGS |
F-1 | |||
APPENDIX G REVIEW COMMENTS |
G-1 |
Revised Final Proposal May 11, 2009 Ameresco Federal Solutions Page v |
Biomass Cogeneration Facility and Heating Plants Savannah River Site Contract DE-AM36-02NT41457 |
Figure 1.1: Proposed Cogeneration Facility Site Layout |
7 | |||
Figure 1.2: EPI Fluidized Bed Energy System |
10 | |||
Figure 1.3: EPI Fluidized Bed Cell |
11 | |||
Figure 1.4: Cogeneration Facility Site Location |
19 | |||
Figure 1.5: Biomass Cogeneration Facility Steam Interconnection |
21 | |||
Figure 1.6: Biomass Cogeneration Facility River Water Interconnection |
22 | |||
Figure 2.1: K Area Biomass Heating Plant Location |
42 | |||
Figure 2.2: L Area Biomass Heating Plant Location |
42 | |||
Figure 5.1: Integrated Management Review Team |
61 | |||
Figure 5.2: Amerescos SRS Biomass Project Team |
64 | |||
Figure 5.3: Proposed Operations Staffing |
70 | |||
List of Tables |
||||
Table ES.1: Project Economic Summary |
2 | |||
Table 1.1: SRS Site Projection Profile Steam Demand |
17 | |||
Table 1.2: Utility Interconnection Summary |
20 | |||
Table 1.3: ECM 1 Annual Savings Summary |
26 | |||
Table 1.4: O&M Baseline Costs for D-Area Plant |
27 | |||
Table 1.5: Baseline Energy Consumption |
29 | |||
Table 1.6: ECM 1 Post-ECM Implementation Facility Performance |
32 | |||
Table 1.7: Project Milestones |
34 | |||
Table 2.1: Utility Interconnection Summary |
42 | |||
Table 2.2: ECM 2 Annual Savings Summary |
45 | |||
Table 2.3: Baseline Operating and Maintenance Cost for K Area Plant |
47 | |||
Table 2.4: Baseline Annual Energy Consumption for K Area Plant |
48 | |||
Table 2.5: ECM 2 Post ECM Heating Plant Performance |
49 | |||
Table 2.6: ECM 2 Annual Post ECM Non-Fuel Utilities Cost & Consumption |
49 | |||
Table 3.1: Environmental Permits & Documents |
52 | |||
Table 3.2: Annual Emissions Summary for Biomass Cogeneration Facility |
54 | |||
Table 3.3: Annual Emissions Summary for K&L Heating Plants |
54 | |||
Table 4.1: M&V Plan Summary |
56 | |||
Table 4.2: Utility Cost for ECM (Post) |
57 | |||
Table 4.3: NIST Escalation Rates |
58 |
Revised Final Proposal May 11, 2009 Ameresco Federal Solutions Page vi |
Biomass Cogeneration Facility and Heating Plants Savannah River Site Contract DE-AM36-02NT41457 |
ACSR
|
Aluminum Conductor, Steel Reinforced | |
AIA
|
American Institute of Architects | |
ASG
|
Annual Steam Guarantee | |
BAMF
|
Biomass & Alternate Methane Fuel | |
BDF
|
Bio Derived Fuel | |
BFB
|
Bubbling Fluidized Bed | |
Btu
|
British Thermal Unit | |
CATEX
|
Categorical Exclusion | |
CO
|
Carbon Monoxide | |
CO2
|
Carbon dioxide | |
CY
|
Calendar Year | |
DA
|
Deaerator | |
DC
|
Direct Current | |
DDC
|
Direct Digital Control | |
DES
|
Detailed Energy Survey | |
DOE
|
Department of Energy | |
EA
|
Environmental Assessment | |
ECM
|
Energy Conservation Measure | |
EPA
|
Environmental Protection Agency | |
EPI
|
Energy Products of Idaho | |
ESPC
|
Energy Savings Performance Contract | |
°F
|
Degrees Fahrenheit | |
FAR
|
Federal Acquisition Regulation | |
FEMP
|
Federal Energy Management Program | |
FONSI
|
Finding of No Significant Impact | |
FY
|
Fiscal Year | |
gpm
|
Gallons per Minute | |
Hp
|
Horsepower | |
ID
|
Induced Draft | |
IMRT
|
Integrated Management Review Team | |
IPMVP
|
International Performance Measurement & Verification Protocol | |
kgal
|
Kilogallons | |
klbs
|
Kilopounds | |
kV
|
Kilovolts | |
KVA
|
Kilovolt Amperes |
Revised Final Proposal May 11, 2009 Ameresco Federal Solutions Page vii |
Biomass Cogeneration Facility and Heating Plants Savannah River Site Contract DE-AM36-02NT41457 |
kW
|
Kilowatt | |
kWh
|
Kilowatt hour | |
LEED
|
Leadership in Energy and Environmental Design | |
M & O
|
Management and Operations | |
M & V
|
Measurement and Verification | |
MBtu
|
Million British Thermal Units (1 x 106) | |
MOA
|
Memorandum of Agreement | |
MOU
|
Memorandum of Understanding | |
MVAR
|
Megavolt Ampere Reactive | |
MW
|
Megawatts | |
NEPA
|
National Environmental Policy Act | |
NFPA
|
National Fire Protection Association | |
NIST
|
National Institute of Standards & Technology | |
NOI
|
Notice of Intent to Award | |
NOx
|
Nitrogen Oxide | |
NPDES
|
National Pollutant Discharge Elimination System | |
O & M
|
Operations and Maintenance | |
PA
|
Public Address | |
PM
|
Particulate Matter | |
PMT
|
Project Management Team | |
POIC
|
Point of Interconnection | |
PPEF
|
Performance Period Escrow Fund | |
PPH
|
Pounds Per Hour | |
PRV
|
Pressure Reducing Valve | |
Psig
|
Pounds per square inch gauge | |
PSUP
|
Power Services Utilization Permit | |
PT
|
Potential Transformer | |
PVC
|
Polyvinyl Chloride | |
QC
|
Quality Control | |
QCM
|
Quality Control Manager | |
REC
|
Renewable Energy Credit | |
RO
|
Reverse Osmosis | |
ROW
|
Right of Way | |
SCADA
|
Supervisory Control and Data Acquisition | |
SCDHEC
|
South Carolina Department of Health & Environmental Control | |
SCDOT
|
South Carolina Department of Transportation | |
SCE&G
|
South Carolina Electric & Gas |
Revised Final Proposal May 11, 2009 Ameresco Federal Solutions Page viii |
Biomass Cogeneration Facility and Heating Plants Savannah River Site Contract DE-AM36-02NT41457 |
SNCR
|
Selective Non Catalytic Reduction | |
SO2
|
Sulfur Dioxide | |
SRS
|
Savannah River Site | |
SRNS
|
Savannah River Nuclear Solutions | |
SSM
|
Site Safety Manager | |
VAC
|
Volts Alternating Current | |
VFD
|
Variable Frequency Drive | |
VOC
|
Volatile Organic Compound | |
Yr
|
Year |
Revised Final Proposal May 11, 2009 Ameresco Federal Solutions Page 1 |
Biomass Cogeneration Facility and Heating Plants Savannah River Site Contract DE-AM36-02NT41457 |
Revised Final Proposal May 11, 2009 Ameresco Federal Solutions Page 2 |
Biomass Cogeneration Facility and Heating Plants Savannah River Site Contract DE-AM36-02NT41457 |
l | Over 2,000,000 MBtu/yr of thermal renewable energy production and a minimum generation of 77,000 mWh (264,444 MBtu) of green power. | ||
l | Annual Energy Savings of approximately 500,000 MBtu/yr | ||
l | No-cost Renewable Energy Credits (RECs) | ||
l | Decrease of water intake from the Savannah River by 1,412,000 kgal/yr, supporting water conservation efforts in the regional drought situation. | ||
l | Reduction of 400 tons/yr of Particulate Matter (PM) emissions | ||
l | Reduction of 3,500 tons/yr of Sulfur Dioxide (SO2) emissions | ||
l | Reduction of 100,000 tons/yr of Carbon Dioxide (CO2) emissions | ||
l | Support of the South Carolina Biomass Council Goals |
Project | Total Energy | |||||||||||||||||||
Implementation | Savings | O&M Savings | Water Savings | Total Savings | ||||||||||||||||
Project | Cost* | (Year 1, 2012) | (Year 1, 2012) | (Year 1, 2012) | (Year 1, 2012) | |||||||||||||||
DES Cost |
[**] | N/A | N/A | N/A | N/A | |||||||||||||||
ECM 1: Biomass
Cogeneration
Facility (D Area
Replacement Plant) |
[**] | $ | 21,053,328 | $ | 12,482,882 | $ | (355,013 | ) | $ | 33,181,197 | ||||||||||
ECM 2: Biomass
Heating Facilities
for K & L Areas |
[**] | $ | 558,208 | $ | 638,970 | $ | (25,917 | ) | $ | 1,171,260 | ||||||||||
Total |
$ | 149,172,566 | $ | 21,611,535 | $ | 13,121,852 | $ | (380,931 | ) | $ | 34,352,457 | |||||||||
* | The project Implementation Cost excludes the financial procurement costs. |
Revised Final Proposal May 11, 2009 Ameresco Federal Solutions Page 3 |
Biomass Cogeneration Facility and Heating Plants Savannah River Site Contract DE-AM36-02NT41457 |
Revised Final Proposal May 11, 2009 Ameresco Federal Solutions Page 4 |
Biomass Cogeneration Facility and Heating Plants Savannah River Site Contract DE-AM36-02NT41457 |
1) | The procurement and installation of a new skid-mounted river water pump and new pumping systems controls at the river water pump house, Building 681-3G. | ||
2) | Rework of the electrical feeder from the TNX area to the South Carolina Electric and Gas (SCE&G) utility line at the D Area. | ||
3) | Relocation of the existing L Area capacitor bank. |
Revised Final Proposal May 11, 2009 Ameresco Federal Solutions Page 5 |
Biomass Cogeneration Facility and Heating Plants Savannah River Site Contract DE-AM36-02NT41457 |
Revised Final Proposal May 11, 2009 Ameresco Federal Solutions Page 6 |
Biomass Cogeneration Facility and Heating Plants Savannah River Site Contract DE-AM36-02NT41457 |
Revised Final Proposal May 11, 2009 Ameresco Federal Solutions Page 7 |
Biomass Cogeneration Facility and Heating Plants Savannah River Site Contract DE-AM36-02NT41457 |
Revised Final Proposal May 11, 2009 | Biomass Cogeneration Facility and Heating Plants | |
Ameresco Federal Solutions | Savannah River Site | |
Page 8 | Contract DE-AM36-02NT41457 |
l | Two (2) Truck scales | ||
l | Three (3) Hydraulic truck dumps and reclaimers | ||
l | Front end loaders | ||
l | Dump trucks for site use | ||
l | Live bottom trailers for K and L Area | ||
l | One (1) Fuel hogger | ||
l | One (1) Screener for oversized product | ||
l | Two (2) Magnets for metals screening | ||
l | One (1) Stacker & Reclaimer | ||
l | One (1) Truck Reclaim for Tires |
Revised Final Proposal May 11, 2009 | Biomass Cogeneration Facility and Heating Plants | |
Ameresco Federal Solutions | Savannah River Site | |
Page 9 | Contract DE-AM36-02NT41457 |
l | One (1) Shredder for tires | ||
l | Multiple conveyors for fuel handling | ||
l | One (1) Whole Tree Chipper |
Revised Final Proposal May 11, 2009 | Biomass Cogeneration Facility and Heating Plants | |
Ameresco Federal Solutions | Savannah River Site | |
Page 10 | Contract DE-AM36-02NT41457 |
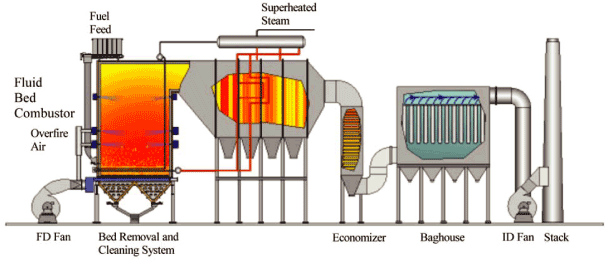
Revised Final Proposal May 11, 2009 | Biomass Cogeneration Facility and Heating Plants | |
Ameresco Federal Solutions | Savannah River Site | |
Page 11 | Contract DE-AM36-02NT41457 |
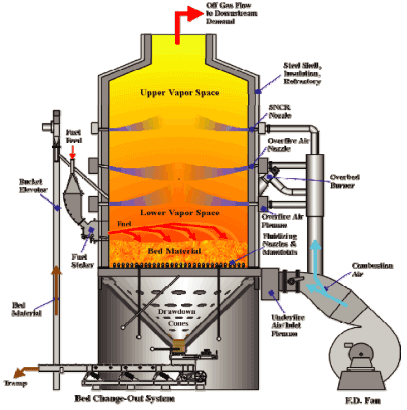
Revised Final Proposal May 11, 2009 | Biomass Cogeneration Facility and Heating Plants | |
Ameresco Federal Solutions | Savannah River Site | |
Page 12 | Contract DE-AM36-02NT41457 |
Revised Final Proposal May 11, 2009 | Biomass Cogeneration Facility and Heating Plants | |
Ameresco Federal Solutions | Savannah River Site | |
Page 13 | Contract DE-AM36-02NT41457 |
l | Two (2) 120,000 PPH biomass fluidized bed boilers, including fan systems | ||
l | Two (2) Baghouses including Penthouse | ||
l | Two (2) SNCR systems (Urea Injection) | ||
l | Boiler auxiliaries (boiler feed water pumps, DA tank, chemical treatment, and instrumentation) | ||
l | Boiler control SCADA system | ||
l | Two (2) Ash bins | ||
l | Two (2) Ash storage silos | ||
l | Two (2) Ash conveying systems (for each biomass boiler) | ||
l | Fuel Oil Storage | ||
l | Reagent Storage | ||
l | Limestone Storage |
l | Three (3) Boiler feed pumps and motors | ||
l | Two (2) DA tanks with instrumentation and trim | ||
l | Piping, valves, and controls |
Revised Final Proposal May 11, 2009 | Biomass Cogeneration Facility and Heating Plants | |
Ameresco Federal Solutions | Savannah River Site | |
Page 14 | Contract DE-AM36-02NT41457 |
l | Four (4) Carbon Filters | ||
l | Two (2) Water Softeners | ||
l | Neutralization Tank | ||
l | RO System | ||
l | Two (2) Deionized Mixed Beds | ||
l | Neutralization Skid | ||
l | Deionized Water Storage Tank |
l | Boilers |
¨ | Internal Boiler Water Treatment: Chemical feed skid(s) with injection pumps. The skid will be pre-piped, pre-wired, including necessary components and accessories for a complete functional system. Feed skid to be used with chemical totes. |
l | Circulating Water System |
¨ | Common acid chemical feed skid with injection pumps, pre-piped, pre-wired and including necessary components and accessories for a complete functional system. Feed skid to be used with chemical totes. | ||
¨ | Corrosion control chemical feed skid with injection pumps (dispersant and corrosion inhibitor), pre-piped, pre-wired and including necessary components and accessories for a complete functional system. Feed skid to be used with chemical totes. | ||
¨ | Biocide chemical feed skid with injection pumps, pre-piped, pre-wired and including necessary components and accessories for a complete functional system. Feed skid to be used with chemical totes. |
Revised Final Proposal May 11, 2009 | Biomass Cogeneration Facility and Heating Plants | |
Ameresco Federal Solutions | Savannah River Site | |
Page 15 | Contract DE-AM36-02NT41457 |
l | One (1) TGM Steam Condensing Turbine (20 MW), Model TMCE 25000A | ||
l | Electrical switchgears | ||
l | Two (2) fuel oil-fired emergency generators (1.5 MW each) | ||
l | Surface Condenser | ||
l | High Voltage, Medium Voltage Transformers |
l | One (1) two-cell Cooling Tower with variable frequency drive (VFD) Fans | ||
l | Cooling Tower pumps | ||
l | Outfall Sampling Station |
l | NFPA 850, Recommended Practice for Fire Protection for Electric Generating Plants |
¨ | Fire water loop with hydrants and post indicating valves installed in accordance with NFPA 24 Standard for the Installation of Private Fire Service Mains and Their Appurtenances |
l | International Fire Code |
¨ | Open access for emergency vehicles |
l | NFPA 850, Recommended Practice for Fire Protection for Electric Generating Plants |
¨ | Fire water loop with hydrants and post indicating valves installed in accordance with NFPA 24 Standard for the Installation of Private Fire Service Mains and Their Appurtenances |
l | International Fire Code |
¨ | Open access for emergency vehicles |
l | NFPA 850, Recommended Practice for Fire Protection for Electric Generating Plants |
¨ | Oil containment/drainage system |
Revised Final Proposal May 11, 2009 | Biomass Cogeneration Facility and Heating Plants | |
Ameresco Federal Solutions | Savannah River Site | |
Page 16 | Contract DE-AM36-02NT41457 |
¨ | A hose connection | ||
¨ | Fixed protection system, detection, and alarm system to cover, as minimum, the Turbine/Generator bearings and oil containment areas. | ||
¨ | Turbine shut down control per NFPA 850 |
l | International Building Code and International Fire Code |
¨ | Detection, alarm, and sprinkler system installed in accordance with NFPA 13 Standard for the Installation of Sprinkler Systems and NFPA 72 National Fire Alarm Code |
l | International Building Code and International Fire Code |
¨ | Detection, alarm, and sprinkler system installed in accordance with NFPA 13 Standard for the Installation of Sprinkler Systems and NFPA 72 National Fire Alarm Code |
l | NFPA 850, Recommended Practice for Fire Protection for Electric Generating Plants |
¨ | Detection and alarm system installed in accordance with NFPA 72 National Fire Alarm Code |
o | Detection, alarm, and fixed protection under raised floors. |
v | Fixed protection Dry Chemical, NFPA 17 |
l | NFPA 850, Recommended Practice for Fire Protection for Electric Generating Plants |
¨ | Protection, detection, and alarm systems are not required but are a good practice |
o | Dry type deluge system install in accordance with NFPA 13 Standard for the Installation of Sprinkler Systems |
¨ | Detection and alarm system installed in accordance with NFPA 72 National Fire Alarm Code |
¨ | Conveyor controls to be interlocked per NFPA 850 |
l | NFPA 850, Recommended Practice for Fire Protection for Electric Generating Plants |
¨ | Hydrant installed in accordance with NFPA 24 Standard for the Installation of Private Fire Service Mains and Their Appurtenances | ||
¨ | Cooling Tower design and constructed in accordance with NFPA 214, Standard on Water-Cooling Towers |
l | NFPA 30: Flammable and Combustible Liquids Code |
¨ | Separation in accordance with NFPA 30 | ||
¨ | 100% containment in accordance with NFPA 30 |
Revised Final Proposal May 11, 2009 | Biomass Cogeneration Facility and Heating Plants | |
Ameresco Federal Solutions | Savannah River Site | |
Page 17 | Contract DE-AM36-02NT41457 |
¨ | Design and construction in accordance with NFPA 30 | ||
¨ | Hydrant installed in accordance with NFPA 24 Standard for the Installation of Private Fire Service Mains and Their Appurtenances |
Winter peak | Winter average | Summer average | ||||
Year | [kpph] | [kpph] | [kpph] | |||
2009 | [**] | [**] | [**] | |||
2010 | [**] | [**] | [**] | |||
2011 | [**] | [**] | [**] | |||
2012 | [**] | [**] | [**] | |||
2013 | [**] | [**] | [**] | |||
2014 | [**] | [**] | [**] | |||
2015 | [**] | [**] | [**] | |||
2016 | [**] | [**] | [**] | |||
2017 | [**] | [**] | [**] | |||
2018 | [**] | [**] | [**] | |||
2019 | [**] | [**] | [**] | |||
2020 | [**] | [**] | [**] |
Revised Final Proposal May 11, 2009 | Biomass Cogeneration Facility and Heating Plants | |
Ameresco Federal Solutions | Savannah River Site | |
Page 18 | Contract DE-AM36-02NT41457 |
Winter peak | Winter average | Summer average | ||||
Year | [kpph] | [kpph] | [kpph] | |||
2021 | [**] | [**] | [**] | |||
2022 | [**] | [**] | [**] | |||
2023 | [**] | [**] | [**] | |||
2024 | [**] | [**] | [**] | |||
2025 | [**] | [**] | [**] | |||
2026 | [**] | [**] | [**] | |||
2027 | [**] | [**] | [**] | |||
2028 | [**] | [**] | [**] | |||
2029 | [**] | [**] | [**] | |||
2030 | [**] | [**] | [**] | |||
2031 | [**] | [**] | [**] |
Revised Final Proposal May 11, 2009 | Biomass Cogeneration Facility and Heating Plants | |
Ameresco Federal Solutions | Savannah River Site | |
Page 19 | Contract DE-AM36-02NT41457 |

Revised Final Proposal May 11, 2009 | Biomass Cogeneration Facility and Heating Plants | |
Ameresco Federal Solutions | Savannah River Site | |
Page 20 | Contract DE-AM36-02NT41457 |
Utility | Interconnection | O&M Responsibility | ||
Steam
|
New 12, 240 kpph line from plant to existing 24 across Burma Road | Ameresco: To the point of the new valve located in a new 12 line near the point of interconnection (POIC) with the existing steam line. SRS: Upstream of the new valve. | ||
Domestic Water
|
30 gpm, new 2 line from plant to header located outside existing water treatment plant | Ameresco: To the new utility valve outside of power plant. SRS: Downstream of the tie-in to the new valve. |
Revised Final Proposal May 11, 2009 | Biomass Cogeneration Facility and Heating Plants | |
Ameresco Federal Solutions | Savannah River Site | |
Page 21 | Contract DE-AM36-02NT41457 |
Utility | Interconnection | O&M Responsibility | ||
River Water
|
New 12,2200 gpm line from valve house near C-Area to new biomass plant | Ameresco: Downstream of the interconnection valve. SRS: From existing pump station up to interconnection valve at cogeneration facility. | ||
Outfall
|
1200 gpm + storm water runoff, new 24 line to Upper Three Runs Creek | Ameresco: To conduct all testing of the effluent; responsible for maintaining compliance of this discharge. | ||
Sanitary Sewer
|
New 4 line & new lift station, 20 gpm to upside of the existing Lift Station | Ameresco: To the new valve located in the new
line outside of power plant. SRS: Downstream of the new utility valve. |
||
Electrical
|
New 13.8 kV line to/from F Area substation | SRS: From outside of new cogeneration facility | ||
Fire Water System
|
Tapped off the new river water header, prior to cooling tower | Ameresco: Responsible for fire water system | ||
Telephone
Line/Public Address
(PA) System
|
Verizon New Line | Verizon/Ameresco | ||
Data Line
|
Verizon New Line | Verizon/Ameresco |
[**]
Revised Final Proposal May 11, 2009 | Biomass Cogeneration Facility and Heating Plants | |
Ameresco Federal Solutions | Savannah River Site | |
Page 22 | Contract DE-AM36-02NT41457 |
l | Rework of the existing suction pipe | ||
l | Installation of isolation valve in suction pipe | ||
l | Installation of flow control valve & flow meter | ||
l | Installation of instrumentation and valves setup (duplicate system to the P-10 skid) | ||
l | Control modification to allow the pumps to automatically operate based on system requirements |
[**]
Revised Final Proposal May 11, 2009 | Biomass Cogeneration Facility and Heating Plants | |
Ameresco Federal Solutions | Savannah River Site | |
Page 23 | Contract DE-AM36-02NT41457 |
Revised Final Proposal May 11, 2009 | Biomass Cogeneration Facility and Heating Plants | |
Ameresco Federal Solutions | Savannah River Site | |
Page 24 | Contract DE-AM36-02NT41457 |
Revised Final Proposal May 11, 2009 | Biomass Cogeneration Facility and Heating Plants | |
Ameresco Federal Solutions | Savannah River Site | |
Page 25 | Contract DE-AM36-02NT41457 |
l | D-Area Electrical Feeder | ||
l | Pump and Controls Replacement in Building 681-3G, Water Pump Station | ||
l | Installation of existing capacitor at the L-Area Substation 151 |
Revised Final Proposal May 11, 2009 | Biomass Cogeneration Facility and Heating Plants | |
Ameresco Federal Solutions | Savannah River Site | |
Page 26 | Contract DE-AM36-02NT41457 |
Post-ECM | ||||||||||||||||
Annual Utility | Annual O&M | Implementation | Total Annual | |||||||||||||
Savings | Cost Savings | Costs | Savings | |||||||||||||
Baseline Year
(CY 2009) |
[**] | [**] | [**] | $ | 30,658,617 | |||||||||||
Escalated to
Project Year 1 (CY
2012) |
[**] | [**] | [**] | $ | 33,181,197 | |||||||||||
Year 2 |
[**] | [**] | [**] | $ | 34,404,421 | |||||||||||
Year 3 |
[**] | [**] | [**] | $ | 35,322,289 | |||||||||||
Year 4 |
[**] | [**] | [**] | $ | 36,399,646 | |||||||||||
Year 5 |
[**] | [**] | [**] | $ | 37,676,281 | |||||||||||
Year 6 |
[**] | [**] | [**] | $ | 39,368,611 | |||||||||||
Year 7 |
[**] | [**] | [**] | $ | 40,858,535 | |||||||||||
Year 8 |
[**] | [**] | [**] | $ | 42,100,018 | |||||||||||
Year 9 |
[**] | [**] | [**] | $ | 43,817,394 | |||||||||||
Year 10 |
[**] | [**] | [**] | $ | 47,247,150 | |||||||||||
Year 11 |
[**] | [**] | [**] | $ | 49,023,439 | |||||||||||
Year 12 |
[**] | [**] | [**] | $ | 50,831,412 | |||||||||||
Year 13 |
[**] | [**] | [**] | $ | 52,654,059 | |||||||||||
Year 14 |
[**] | [**] | [**] | $ | 54,705,813 | |||||||||||
Year 15 |
[**] | [**] | [**] | $ | 56,773,136 | |||||||||||
Year 16 |
[**] | [**] | [**] | $ | 58,856,493 |
Revised Final Proposal May 11, 2009 | Biomass Cogeneration Facility and Heating Plants | |
Ameresco Federal Solutions | Savannah River Site | |
Page 27 | Contract DE-AM36-02NT41457 |
Post-ECM | ||||||||||||||||
Annual Utility | Annual O&M | Implementation | Total Annual | |||||||||||||
Savings | Cost Savings | Costs | Savings | |||||||||||||
Year 17 |
[**] | [**] | [**] | $ | 60,921,492 | |||||||||||
Year 18 |
[**] | [**] | [**] | $ | 63,483,800 | |||||||||||
Year 19 |
[**] | [**] | [**] | $ | 65,849,637 | |||||||||||
Year 20 |
[**] | [**] | [**] | $ | 68,447,514 |
Month | 2006 O&M Costs |
2007 O&M Costs |
Baseline O&M Cost Savings |
|||||||||
January |
[**] | [**] | [**] | |||||||||
February |
[**] | [**] | [**] | |||||||||
March |
[**] | [**] | [**] | |||||||||
April |
[**] | [**] | [**] | |||||||||
May |
[**] | [**] | [**] | |||||||||
June |
[**] | [**] | [**] | |||||||||
July |
[**] | [**] | [**] | |||||||||
August |
[**] | [**] | [**] | |||||||||
September |
[**] | [**] | [**] | |||||||||
October |
[**] | [**] | [**] | |||||||||
November |
[**] | [**] | [**] | |||||||||
December |
[**] | [**] | [**] | |||||||||
Total | $ | 10,692,844 |
** | Data was not available, so used 2006 data with escalation on labor only | |
*** | Data in this table is presented using 2006 & 2007 dollars and not Baseline year |
Revised Final Proposal May 11, 2009 Ameresco Federal Solutions Page 28 |
Biomass Cogeneration Facility and Heating Plants Savannah River Site Contract DE-AM36-02NT41457 |
Revised Final Proposal May 11, 2009 Ameresco Federal Solutions Page 29 |
Biomass Cogeneration Facility and Heating Plants Savannah River Site Contract DE-AM36-02NT41457 |
2006 Energy Use | 2007 Energy Use | Baseline Energy Use | ||||||||||||||||||||||||||||||||||||||||||||||
Net | Net | Net | ||||||||||||||||||||||||||||||||||||||||||||||
Output | Output | Output | ||||||||||||||||||||||||||||||||||||||||||||||
of D- | of D- | of D- | ||||||||||||||||||||||||||||||||||||||||||||||
Coal | Area | Power | Coal | Area | Power | Area | Power | |||||||||||||||||||||||||||||||||||||||||
Use | Coal Use | Plant | Export | Use | Coal Use | Plant | Export | Coal Use | Coal Use | Plant | Export | |||||||||||||||||||||||||||||||||||||
Month | (tons) | (MBtu) | (MWh) | (MW) | (tons) | (MBtu) | (MWh) | (MW) | (tons) | (MBtu) | (MWh) | (MW) | ||||||||||||||||||||||||||||||||||||
January |
[**] | [**] | [**] | [**] | [**] | [**] | [**] | [**] | [**] | [**] | [**] | [**] | ||||||||||||||||||||||||||||||||||||
February |
[**] | [**] | [**] | [**] | [**] | [**] | [**] | [**] | [**] | [**] | [**] | [**] | ||||||||||||||||||||||||||||||||||||
March |
[**] | [**] | [**] | [**] | [**] | [**] | [**] | [**] | [**] | [**] | [**] | [**] | ||||||||||||||||||||||||||||||||||||
April |
[**] | [**] | [**] | [**] | [**] | [**] | [**] | [**] | [**] | [**] | [**] | [**] | ||||||||||||||||||||||||||||||||||||
May |
[**] | [**] | [**] | [**] | [**] | [**] | [**] | [**] | [**] | [**] | [**] | [**] | ||||||||||||||||||||||||||||||||||||
June |
[**] | [**] | [**] | [**] | [**] | [**] | [**] | [**] | [**] | [**] | [**] | [**] | ||||||||||||||||||||||||||||||||||||
July |
[**] | [**] | [**] | [**] | [**] | [**] | [**] | [**] | [**] | [**] | [**] | [**] | ||||||||||||||||||||||||||||||||||||
August |
[**] | [**] | [**] | [**] | [**] | [**] | [**] | [**] | [**] | [**] | [**] | [**] | ||||||||||||||||||||||||||||||||||||
September |
[**] | [**] | [**] | [**] | [**] | [**] | [**] | [**] | [**] | [**] | [**] | [**] | ||||||||||||||||||||||||||||||||||||
October |
[**] | [**] | [**] | [**] | [**] | [**] | [**] | [**] | [**] | [**] | [**] | [**] | ||||||||||||||||||||||||||||||||||||
November |
[**] | [**] | [**] | [**] | [**] | [**] | [**] | [**] | [**] | [**] | [**] | [**] | ||||||||||||||||||||||||||||||||||||
December |
[**] | [**] | [**] | [**] | [**] | [**] | [**] | [**] | [**] | [**] | [**] | [**] | ||||||||||||||||||||||||||||||||||||
Totals | 161,839 | 3,978,008 | 131,889 |
Revised Final Proposal May 11, 2009 Ameresco Federal Solutions Page 30 |
Biomass Cogeneration Facility and Heating Plants Savannah River Site Contract DE-AM36-02NT41457 |
Revised Final Proposal May 11, 2009 Ameresco Federal Solutions Page 31 |
Biomass Cogeneration Facility and Heating Plants Savannah River Site Contract DE-AM36-02NT41457 |
Revised Final Proposal May 11, 2009 Ameresco Federal Solutions Page 32 |
Biomass Cogeneration Facility and Heating Plants Savannah River Site Contract DE-AM36-02NT41457 |
Plant Parameter | Year 1 | Year 2 | Year 3 | Year 4 | Year 5 | Year 6-9 | Year 10-20 | |||||||||||||||||||||
Total Boiler Capacity Steam Load (k-lbs/yr) |
2,102,400 | 2,102,400 | 2,102,400 | 2,102,400 | 2,102,400 | 2,102,400 | 2,102,400 | |||||||||||||||||||||
Annual Steam Guarantee (k-lbs/yr) |
1,759,485 | 1,759,485 | 1,759,485 | 1,759,485 | 1,759,485 | 1,759,485 | 1,759,485 | |||||||||||||||||||||
Steam Use |
||||||||||||||||||||||||||||
SRS Export Steam Load (k-lbs/yr) |
[**] | [**] | [**] | [**] | [**] | [**] | [**] | |||||||||||||||||||||
Steam Load for Power Generation (k-lbs/yr) |
[**] | [**] | [**] | [**] | [**] | [**] | [**] | |||||||||||||||||||||
Aux Steam Load (k-lb/yr) |
[**] | [**] | [**] | [**] | [**] | [**] | [**] | |||||||||||||||||||||
Power Generation |
||||||||||||||||||||||||||||
Net Green Generation (kWh/yr) |
[**] | [**] | [**] | [**] | [**] | [**] | [**] | |||||||||||||||||||||
Net Green Generation (MBtu/yr) |
[**] | [**] | [**] | [**] | [**] | [**] | [**] | |||||||||||||||||||||
Baseline Power Export from D Area Plant (kWh/yr) |
[**] | [**] | [**] | [**] | [**] | [**] | [**] | |||||||||||||||||||||
Post-ECM Implementation Electricity Purchased from SCE&G (kWh/yr) |
[**] | [**] | [**] | [**] | [**] | [**] | [**] | |||||||||||||||||||||
Post-ECM Implementation electricity Purchased from SCE&G ($/yr)
(*see note) |
[**] | [**] | [**] | [**] | [**] | [**] | [**] | |||||||||||||||||||||
Fuel Supply |
||||||||||||||||||||||||||||
Annual Fuel Consumption for ECM 1 (MBtu/yr) |
2,727,205 | 2,727,205 | 2,727,205 | 2,727,205 | 2,727,205 | 2,727,205 | 2,727,205 | |||||||||||||||||||||
Fuel Required for ECM 1, 100% Biomass (tons/yr) |
317,118 | 317,118 | 317,118 | 317,118 | 317,118 | 317,118 | 317,118 | |||||||||||||||||||||
Fuel Cost for ECM 1, 100% Biomass ($/yr) (**see note) |
[**] | [**] | [**] | [**] | [**] | [**] | [**] |
Revised Final Proposal May 11, 2009 Ameresco Federal Solutions Page 33 |
Biomass Cogeneration Facility and Heating Plants Savannah River Site Contract DE-AM36-02NT41457 |
Plant Parameter | Year 1 | Year 2 | Year 3 | Year 4 | Year 5 | Year 6-9 | Year 10-20 | |||||||||||||||||||||
Post-ECM Non Fuel Utilities *** |
||||||||||||||||||||||||||||
River Water (k-gals/yr & $/yr) |
$ |
460,215 (346,699 |
) | $ |
456,015 (353,842 |
) | $ |
459,033 (366,869 |
) | $ |
460,261 (378,886 |
) | $ |
457,981 (388,319 |
) | $ |
461,026 (402,627 |
) | $ |
454,418 (446,666 |
) | |||||||
Domestic Water (k-gals/yr & $/yr) |
$ |
456 (4,692 |
) | $ |
456 (4,833 |
) | $ |
456 (4,978 |
) | $ |
456 (5,128 |
) | $ |
456 (5,281 |
) | $ |
456 (5,440 |
) | $ |
456 (6,123 |
) | |||||||
Sanitary Sewer (k-gals/yr) |
$ |
456 (3,621 |
) | $ |
456 (3,730 |
) | $ |
456 (3,842 |
) | $ |
456 (3,957 |
) | $ |
456 (4,076 |
) | $ |
456 (4,198 |
) | $ |
456 (4,725 |
) |
* | The power purchased cost is per 2009 unit cost, however the DO schedules are escalated per NIST to account for future price of power. | |
** | Annual biomass cost for years 7-9 and 11-20 are not shown in this table, but escalated from previous year using an escalation factor of 5% | |
*** | Non fuel utility consumption is calculated on full load on expected maximum each year so the consumption is constant throughout the term; the actual cost is escalated each year. |
Revised Final Proposal May 11, 2009 Ameresco Federal Solutions Page 34 |
Biomass Cogeneration Facility and Heating Plants Savannah River Site Contract DE-AM36-02NT41457 |
Activity | ECM 1 | ECM 2 | ||||||
Site Work |
09/01/09 | 07/01/09 | ||||||
Site Utility* |
09/01/09 | 09/01/09 | ||||||
Concrete/Foundation Work |
12/01/09 | 11/01/09 | ||||||
Building Package |
06/01/10 | 01/01/10 | ||||||
Mechanical Install Work |
06/01/10 | 05/01/10 | ||||||
Process Piping Work |
08/01/10 | 05/01/10 | ||||||
Electrical Plant Work |
12/01/10 | 05/01/10 | ||||||
Instrumentation & Controls Work |
12/01/10 | 05/01/10 | ||||||
Insulation Work |
12/01/10 | 05/01/10 | ||||||
Start up & Commissioning |
06/01/11 | 07/01/10 |
* | Design Packages to be submitted throughout the first year of project |
Revised Final Proposal May 11, 2009 Ameresco Federal Solutions Page 35 |
Biomass Cogeneration Facility and Heating Plants Savannah River Site Contract DE-AM36-02NT41457 |
Revised Final Proposal May 11, 2009 Ameresco Federal Solutions Page 36 |
Biomass Cogeneration Facility and Heating Plants Savannah River Site Contract DE-AM36-02NT41457 |
(c) | To the extent that Amerescos [**] | |
(d) | To the extent that Amerescos [**] | |
(e) | Ameresco, upon [**] Ameresco may [**]. |
Revised Final Proposal May 11, 2009 Ameresco Federal Solutions Page 37 |
Biomass Cogeneration Facility and Heating Plants Savannah River Site Contract DE-AM36-02NT41457 |
Revised Final Proposal May 11, 2009 Ameresco Federal Solutions Page 38 |
Biomass Cogeneration Facility and Heating Plants Savannah River Site Contract DE-AM36-02NT41457 |
Revised Final Proposal May 11, 2009 Ameresco Federal Solutions Page 39 |
Biomass Cogeneration Facility and Heating Plants Savannah River Site Contract DE-AM36-02NT41457 |
l | Tractor trailer with walking bed for fuel feed | ||
l | Fuel storage shelter bay | ||
l | Main fuel bin and auger to feed combustor |
Revised Final Proposal May 11, 2009 Ameresco Federal Solutions Page 40 |
Biomass Cogeneration Facility and Heating Plants Savannah River Site Contract DE-AM36-02NT41457 |
l | Metering Bin Feeder | ||
l | 10.5 MBtu/hr combustion unit | ||
l | Full-capacity fuel oil burner | ||
l | Steam heat recovery boiler | ||
l | Multi cyclone | ||
l | SCADA system | ||
l | Automated ash removal system | ||
l | Exhaust stack with aviation lights | ||
l | Boiler auxiliaries | ||
l | Air compressor for L Area | ||
l | Water treatment skid for L Area | ||
l | Fuel Oil Storage |
Revised Final Proposal May 11, 2009 Ameresco Federal Solutions Page 41 |
Biomass Cogeneration Facility and Heating Plants Savannah River Site Contract DE-AM36-02NT41457 |
Revised Final Proposal May 11, 2009 Ameresco Federal Solutions Page 42 |
Biomass Cogeneration Facility and Heating Plants Savannah River Site Contract DE-AM36-02NT41457 |
[**]
[**]
Utility | Interconnection | O&M Responsibility | ||
Steam
|
New 6 150 psig to existing steam line (PRV station in K Area) | Ameresco: to new valve located in new line just prior to POIC with existing steam line; SRS: downstream of valve. | ||
Domestic water (K & L Area) |
30 gpm, new 2 line from plant to header located outside existing water treatment plant. A new 2 line will be installed from the domestic water header to the L Area heating plant to be used as a backup source for feedwater and as a source for the safety shower and eyewash. | Ameresco: to new utility valve outside of water treatment building; SRS: downstream of tie-in. | ||
River water (L Area)
|
New 4, 30 gpm, line from river water header in L Area | Ameresco: to new valve located in new line outside of heating plant; SRS: upstream of utility valve. | ||
Process Sewer
|
2 connection to existing line to Ash Basin for K Area & 2 connection to basin to L-07 outfall for L Area | Ameresco: to new valve located in new line outside of heating plant; SRS: downstream of utility valve. (Ameresco responsible for meeting discharge emission requirements of these lines from the K and L heating plants) |
Revised Final Proposal May 11, 2009 Ameresco Federal Solutions Page 43 |
Biomass Cogeneration Facility and Heating Plants Savannah River Site Contract DE-AM36-02NT41457 |
Utility | Interconnection | O&M Responsibility | ||
Electrical
|
New line from 151-2K in K Area and add new line from 183-2L to the heating plant for the L Area | Ameresco: from connection at heating plant; SRS: upstream of each heating plant. | ||
Telephone Line/PA
System
|
Verizon New Line | Verizon/Ameresco |
Revised Final Proposal May 11, 2009 Ameresco Federal Solutions Page 44 |
Biomass Cogeneration Facility and Heating Plants Savannah River Site Contract DE-AM36-02NT41457 |
l | The K Area water treatment building will be left in place and existing water treatment components will be utilized. Ameresco will maintain the water treatment equipment and building throughout the term of this contract. | ||
l | The air compressor located next to the existing fuel boilers in the K Area will be used for the new biomass combustor system. Ameresco will maintain the air compressor throughout the contract term. |
Revised Final Proposal May 11, 2009 Ameresco Federal Solutions Page 45 |
Biomass Cogeneration Facility and Heating Plants Savannah River Site Contract DE-AM36-02NT41457 |
Post-ECM | ||||||||||||||||
Annual Energy | Annual O&M Cost | Implementation | Total Annual | |||||||||||||
Savings | Savings | Costs | Savings | |||||||||||||
Current Year
(FY 2009) |
[**] | [**] | [**] | $ | 1,188,383 | |||||||||||
Escalated to
Project Year 1 (FY
2012) |
[**] | [**] | [**] | $ | 1,171,260 | |||||||||||
Year 2 |
[**] | [**] | [**] | $ | 1,182,735 | |||||||||||
Year 3 |
[**] | [**] | [**] | $ | 1,207,952 | |||||||||||
Year 4 |
[**] | [**] | [**] | $ | 1,233,416 | |||||||||||
Year 5 |
[**] | [**] | [**] | $ | 1,245,632 | |||||||||||
Year 6 |
[**] | [**] | [**] | $ | 1,284,832 | |||||||||||
Year 7 |
[**] | [**] | [**] | $ | 1,324,974 | |||||||||||
Year 8 |
[**] | [**] | [**] | $ | 1,385,220 | |||||||||||
Year 9 |
[**] | [**] | [**] | $ | 1,446,124 | |||||||||||
Year 10 |
[**] | [**] | [**] | $ | 1,481,648 | |||||||||||
Year 11 |
[**] | [**] | [**] | $ | 1,537,014 | |||||||||||
Year 12 |
[**] | [**] | [**] | $ | 1,593,421 | |||||||||||
Year 13 |
[**] | [**] | [**] | $ | 1,643,974 | |||||||||||
Year 14 |
[**] | [**] | [**] | $ | 1,708,160 | |||||||||||
Year 15 |
[**] | [**] | [**] | $ | 1,773,132 | |||||||||||
Year 16 |
[**] | [**] | [**] | $ | 1,832,320 | |||||||||||
Year 17 |
[**] | [**] | [**] | $ | 1,898,294 | |||||||||||
Year 18 |
[**] | [**] | [**] | $ | 1,972,045 | |||||||||||
Year 19 |
[**] | [**] | [**] | $ | 2,053,597 | |||||||||||
Year 20 |
[**] | [**] | [**] | $ | 2,129,145 |
Revised Final Proposal May 11, 2009 Ameresco Federal Solutions Page 46 |
Biomass Cogeneration Facility and Heating Plants Savannah River Site Contract DE-AM36-02NT41457 |
Revised Final Proposal May 11, 2009 | Biomass Cogeneration Facility and Heating Plants | |
Ameresco Federal Solutions | Savannah River Site | |
Page 47 | Contract DE-AM36-02NT41457 |
O&M Expense | 2003 | 2004 | 2005 | 2006 | 2007 | Baseline Year (2009) |
Average Annual Costs |
|||||||||||||||||||||
Labor Total |
[**] | [**] | [**] | [**] | [**] | [**] | [**] | |||||||||||||||||||||
Material Total |
[**] | [**] | [**] | [**] | [**] | [**] | [**] | |||||||||||||||||||||
Other Consumable
Total |
[**] | [**] | [**] | [**] | [**] | [**] | [**] | |||||||||||||||||||||
Steam Distribution
O&M |
[**] | [**] | [**] | [**] | [**] | [**] | [**] | |||||||||||||||||||||
Subcontracts for
Repair &
Replacement |
[**] | [**] | [**] | [**] | [**] | [**] | [**] | |||||||||||||||||||||
Overhead for O&M |
[**] | [**] | [**] | [**] | [**] | [**] | [**] | |||||||||||||||||||||
Total O&M Cost
Savings |
[**] | [**] | [**] | [**] | [**] | [**] | $551,189 |
Revised Final Proposal May 11, 2009 | Biomass Cogeneration Facility and Heating Plants | |
Ameresco Federal Solutions | Savannah River Site | |
Page 48 | Contract DE-AM36-02NT41457 |
K Plant Production | 2003 | 2004 | 2005 | 2006 | 2007 | Average | ||||||||||||||||||
Fuel Use |
||||||||||||||||||||||||
Fuel Use Gallons |
345,594 | 380,806 | 343,987 | 277,061 | 200,707 | 309,631 | ||||||||||||||||||
Fuel Use MBtu |
47,865 | 52,742 | 47,642 | 38,373 | 27,798 | 42,884 | ||||||||||||||||||
Steam Production |
||||||||||||||||||||||||
Total k-lbs/yr |
36,648 | 40,382 | 36,478 | 29,381 | 21,284 | 32,835 | ||||||||||||||||||
Hours in Season |
3264 | 2904 | 3264 | 2424 | 2112 | 2,794 | ||||||||||||||||||
Average Load lbs/hr |
11,228 | 13,906 | 11,176 | 12,121 | 10,078 | 11,754 |
Revised Final Proposal May 11, 2009 | Biomass Cogeneration Facility and Heating Plants | |
Ameresco Federal Solutions | Savannah River Site | |
Page 49 | Contract DE-AM36-02NT41457 |
ECM Post-ECM | ||||
Heating Plant Parameter | Performance | |||
Typical Operation |
December- April 15 | |||
Expected Steam Production (k-lbs/yr) |
33,300 | |||
Fuel Required for ECM 2, 100% Biomass (MBtu/yr) |
42,844 | |||
Fuel Required for ECM 2, 100% Biomass (tons/yr) |
5,000 | |||
Fuel Cost for ECM 2, 100% Biomass ($/yr) 2009 |
$ | 110,000 | ||
Fuel Cost for ECM 2, 100% Biomass ($/yr) 2012 Year 1 |
$ | 120,200 |
Utility | Annual Consumption | Annual Cost | ||||||
Domestic Water |
2,004 k-gal/yr | $ | 22,861 | |||||
River Water |
2,004 k-gal/yr | $ | 922 | |||||
Electricity |
345,600 kWh/yr | $ | 32,141 |
Revised Final Proposal May 11, 2009 | Biomass Cogeneration Facility and Heating Plants | |
Ameresco Federal Solutions | Savannah River Site | |
Page 50 | Contract DE-AM36-02NT41457 |
Revised Final Proposal May 11, 2009 | Biomass Cogeneration Facility and Heating Plants | |
Ameresco Federal Solutions | Savannah River Site | |
Page 51 | Contract DE-AM36-02NT41457 |
l | The proposed plants will decrease the overall air emissions rates for 1) particulate matter (PM) by more than 400 tons a year, 2) nitrogen oxides (NOx) by more than 2,500 tons a year, and 3) Sulfur Dioxide (SOx) by more than 3,500 tons a year. This will result in a positive impact to the air quality of the local area. | ||
l | Both ECMs will reduce energy consumption by eliminating over 6 miles of steam distribution lines (3.5 miles for ECM 1 and 2.5 miles for ECM 2). The reduced steam distribution pipe will decrease fuel consumption by at least 10% from reduction of in-line steam losses. | ||
l | The proposed cogeneration facility will decrease the amount of river water currently drawn from the Savannah River by over 1,412,000 kgal per year. This is especially significant as the level of the Savannah River is low and this project will support efforts to protect the water level. | ||
l | By replacing fossil fuels with a renewable energy fuel source, green house gas emissions will be reduced by at least 100,000 tons a year significantly decreasing the carbon footprint of the SRS. | ||
l | Although cogeneration facility and heating plants are not practical feasible buildings for Leadership in Energy and Environmental Design (LEED) certifications, both ECMs will incorporate sustainable design methods and incorporate energy efficient technologies into the design. |
Revised Final Proposal May 11, 2009 | Biomass Cogeneration Facility and Heating Plants | |
Ameresco Federal Solutions | Savannah River Site | |
Page 52 | Contract DE-AM36-02NT41457 |
Completion Date/ | ||||||
Permit/Document | Expected Issuance | |||||
(responsible for | (responsible for | |||||
permit) | Status | approval) | Schedule Impact | |||
Site Use Permit (M&O)
|
Site Use Permit approved in October 2007, revision will be submitted to include river water routing, outfall routing and electrical feeder routing. | Initial Site Use Permit Approved, Revision approved in June 2008. (SRS) | Required for Construction & Operation | |||
Power Services
Utilization
Permit(s) (Ameresco)
|
PSUP to be submitted upon approval of IFC drawings. | Approval by end of 2009 (M&O) | Approval before operation | |||
Site Clearance
Permit (M&O)
|
Approval by SRS | Approval before start of construction work. | ||||
Environmental
Assessment
(Ameresco/DOE SRS)
|
Finalizing Draft, currently out for public comment | Issuance of Findings of No Significant Impact (FONSI) received in July 2008 | Prior to process discharge to outfall (operation of plant) | |||
Construction Air
Permit (Ameresco)
|
Submitted in February 2008 to SCDHEC | Approval received in November 2008 (SCDHEC) | Required before Construction Start or Issue of Notice to Start Construction by Government | |||
Operating Air Permit
(Ameresco)
|
To be submitted 180 days after plant commissioning | (SCDHEC) | Required within 180 days of plant commissioning | |||
NPDES 2D Permit
(National Pollutant
Discharge
Elimination System)
(Ameresco/M&O)
|
Resubmitted April 11, 2008 to M&O to submit to SCDHEC as modification to site permit | Draft permit issued in March of 2009 (SCDHEC) with June 2009 being likely the permit issue date | Prior to process discharge to outfall (operation of plant) | |||
401 Water Quality
Certification
(Ameresco)
|
This permit application is submitted simultaneously with the Section 404 permit, | Expected 120 days from submittal of permit (SCDHEC) | Prior to operation of plant | |||
Wetlands Section 404
Permit
(Ameresco/M&O)
|
To be submitted by June 2009 | Expected 120 days from submittal of permit (US Army Corps of Engineers) | Prior to operation of plant |
Revised Final Proposal May 11, 2009 | Biomass Cogeneration Facility and Heating Plants | |
Ameresco Federal Solutions | Savannah River Site | |
Page 53 | Contract DE-AM36-02NT41457 |
Completion Date/ | ||||||
Permit/Document | Expected Issuance | |||||
(responsible for | (responsible for | |||||
permit) | Status | approval) | Schedule Impact | |||
SC R.19-450
Construction in
Navigable Waters
Permit (Ameresco)
|
This permit application is submitted simultaneously with the Section 404 permit | Expected 120 days from submittal of permit (SCDHEC) | Prior to operation of plant | |||
Industrial
Wastewater Treatment
Permit for oil
separator,
neutralization tank
and for retention
pond (Ameresco)
|
To be submitted following the NPDES permit modification approval | Expected by April of 2010 (SCDHEC) | Prior to operation of plant | |||
Notice of Intent for
Storm Water
Discharges from
Large & Small
Construction
Activities
(Ameresco)
|
To be submitted by June 2009 | M&O ESS Review & Approval within 30 |
Prior to construction of start of any site work activities | |||
Storm Water
Pollution Prevention
Plan Including Soil
& Erosion Control
(Ameresco)
|
To be submitted with NOI for Storm water Discharges from Large/Small Construction Activities | See Above | Prior to construction of start of any site work activities | |||
Grading Permit Application (Ameresco)
|
To be submitted with NOI for Storm water Discharges from Large/Small Construction Activities | M&O ESS approval expected within 30 days |
Prior to construction of start of any site work activities | |||
Construction Permit for Domestic Water Tie-in, Permit 1970 (Ameresco) |
To be submitted by December 2009 | M&O ESS approval expected within 30 days (M&O ESS acting authority) |
Prior to construction of water tie-in & inspection/approval required prior to operation of new line | |||
Construction Permit for Sanitary Sewer Connection, Permit 1970 (Ameresco) |
To be submitted by December 2009 | M&O ESS approval expected within 30 days (M&O ESS acting authority) | Prior to construction of sanitary sewer tie-in |
The equipment in both ECMs are permitted under one new construction air permit and will be under the Ameresco permit rather than site permit. Ameresco will be responsible for the air permit and for future air permit renewals throughout the contract term. The following table shows the potential air emissions
Revised Final Proposal May 11, 2009 | Biomass Cogeneration Facility and Heating Plants | |
Ameresco Federal Solutions | Savannah River Site | |
Page 54 | Contract DE-AM36-02NT41457 |
Annual Potential Emissions | |||||||||||
Controlled Emission Rate | Actual/Capacity | ||||||||||
Pollutant | [lb/MBtu] | [tons/yr] | |||||||||
Nitrogen Oxides |
0.15 (with SCNR) | 227/295 | |||||||||
Carbon Monoxide |
0.13 | 137/195 | |||||||||
Volatile Organic Compounds
(VOCs) |
0.15 | 26/31 | |||||||||
Particulate Matter Total |
0.023 | 35/42 | |||||||||
Particulate Matter 10 |
0.0203 | 31/37 | |||||||||
Sulfur Dioxides |
0.025/0.2 with BDF fuel | 46/143 | |||||||||
Controlled Emission Rate | Annual Potential Emissions | |||||||
Pollutant | [lb/MBtu] | [tons/yr] | ||||||
Nitrogen Oxides |
0.219 | 15 | ||||||
Carbon Monoxide |
0.6 | 25 | ||||||
VOCs |
0.0128 | 1 | ||||||
Particulate Matter Total |
0.2 (with multiclone) | 9 | ||||||
Particulate Matter 10 |
0.119 (with multiclone) | 6 | ||||||
Sulfur Dioxides |
0.025 | 1 |
The proposed outfall for ECM 1 will be included as part of the SRS NPDES Permit. The modification to site permit was submitted to the site for approval this past month; it is expected to be incorporated into the Site permit by March 2009. For ECM 2, the K Area boiler blowdown will discharge into the K Area Ash Basin, as opposed to being discharged to an NPDES outfall. The NPDES outfall L-07 was modified to include boiler blowdown discharges for the L Area Biomass Heating Plant. As part of the Memorandum of Understanding/Memorandum of Agreement (MOU/MOA) between Ameresco and M&O Contractor, language will be incorporated to require Ameresco to retain responsibility for compliance of the cogeneration facility outfall and for the K and L Area heating plant effluents.
Revised Final Proposal May 11, 2009 | Biomass Cogeneration Facility and Heating Plants | |
Ameresco Federal Solutions | Savannah River Site | |
Page 55 | Contract DE-AM36-02NT41457 |
The storm water management prevention plan is currently being developed. Once this plan is submitted, the permit application will be submitted to the M&O Contractor staff for approval. It is expected it will be approved within 30 days of submittal.
Under the National Environmental Policy Act (NEPA), any modification to a federal facility or site requires determination of the environmental impact of the proposed change or new process. This requires issuance of a CATEX (categorical exclusion), development of an environmental assessment (EA) to determine finding of no significant impact (FONSI), or development of an environmental impact statement. During the DES phase, the EA was developed to include both proposed ECMs. The document has been placed for public review. The FONSI was issued in July of 2008.
Revised Final Proposal May 11, 2009 | Biomass Cogeneration Facility and Heating Plants | |
Ameresco Federal Solutions | Savannah River Site | |
Page 56 | Contract DE-AM36-02NT41457 |
ECM No. |
ECM Description | M&V Option Used* | Summary of M&V Plan | |||
ECM 1
|
Biomass Cogeneration Facility |
B | Equipment and system performance factors continuously measured. Steam produced from the boilers will be measured and totaled for each performance period year. Fuel Usage will be recorded. Power exported to the site will also be measured and recorded to determine annual green power export. | |||
ECM 2
|
K & L Area Heating Plants | B | Equipment and system performance factors continuously measured. Steam produced from the boilers will be measured and totaled for each performance period year. |
* | M&V options include A, B, C, and D. Guidelines include M&V Guidelines: Measurement & Verification for Federal Energy Projects, Version 2.2; and International Performance Measurement & Verification Protocol (IPMVP), Volume I, March 2002, available at www.eere.energy.gov/femp/financing/superespcs_mvresources.cfm. |
Revised Final Proposal May 11, 2009 | Biomass Cogeneration Facility and Heating Plants | |
Ameresco Federal Solutions | Savannah River Site | |
Page 57 | Contract DE-AM36-02NT41457 |
The energy costs (rates) used to develop the baseline annual cost for ECMs 1 and 2 were provided by SRS based on historical costs. Annual savings were calculated using the current unit cost and for coal and fuel oil and the baseline consumption data as described in Sections 1.2.7 and 2.2.7. Post-ECM implementation non fuel utility costs required for operation of the cogeneration facility and of the heating plants were factored into the savings at the following previously agreed upon unit costs as shown in the following table:
Utility | Unit Costs | |||
Electricity |
$0.093 / kWh | |||
River Water |
$0.69 / k-gallon |
Revised Final Proposal May 11, 2009 | Biomass Cogeneration Facility and Heating Plants | |
Ameresco Federal Solutions | Savannah River Site | |
Page 58 | Contract DE-AM36-02NT41457 |
Utility | Unit Costs | |||
Domestic Water |
$9.42 / k-gallon | |||
Sanitary Waste Treatment |
$7.27 / k-gallon |
For both ECMs, the annual energy rates used for savings calculations were adjusted using the latest escalation factors available from the 2008 National Institute of Standards & Technology (NIST). The applicable NIST escalation rates are shown in Table 4.3 below. O&M cost savings and the performance period O&M cost use an annual escalation factor of 3%.
NIST Fuel Oil | ||||||||
NIST Electrical | NIST Coal | Escalation | O&M Escalation | |||||
Year | Escalation Rates | Escalation Rates | Rates | Rates | ||||
2012
|
[**] | [**] | [**] | [**] | ||||
2013
|
[**] | [**] | [**] | [**] | ||||
2014
|
[**] | [**] | [**] | [**] | ||||
2015
|
[**] | [**] | [**] | [**] | ||||
2016
|
[**] | [**] | [**] | [**] | ||||
2017
|
[**] | [**] | [**] | [**] | ||||
2018
|
[**] | [**] | [**] | [**] | ||||
2019
|
[**] | [**] | [**] | [**] | ||||
2020
|
[**] | [**] | [**] | [**] | ||||
2021
|
[**] | [**] | [**] | [**] | ||||
2022
|
[**] | [**] | [**] | [**] | ||||
2023
|
[**] | [**] | [**] | [**] | ||||
2024
|
[**] | [**] | [**] | [**] | ||||
2025
|
[**] | [**] | [**] | [**] | ||||
2026
|
[**] | [**] | [**] | [**] | ||||
2027
|
[**] | [**] | [**] | [**] | ||||
2028
|
[**] | [**] | [**] | [**] | ||||
2029
|
[**] | [**] | [**] | [**] | ||||
2030
|
[**] | [**] | [**] | [**] |
Revised Final Proposal May 11, 2009 | Biomass Cogeneration Facility and Heating Plants | |
Ameresco Federal Solutions | Savannah River Site | |
Page 59 | Contract DE-AM36-02NT41457 |
Option B ECM Isolation will be used for verification of the performance of ECM 1. Option B focuses [**].
Option B will be used for [**] to the K and L Areas.
Revised Final Proposal May 11, 2009 | Biomass Cogeneration Facility and Heating Plants | |
Ameresco Federal Solutions | Savannah River Site | |
Page 60 | Contract DE-AM36-02NT41457 |
Revised Final Proposal May 11, 2009 | Biomass Cogeneration Facility and Heating Plants | |
Ameresco Federal Solutions | Savannah River Site | |
Page 61 | Contract DE-AM36-02NT41457 |
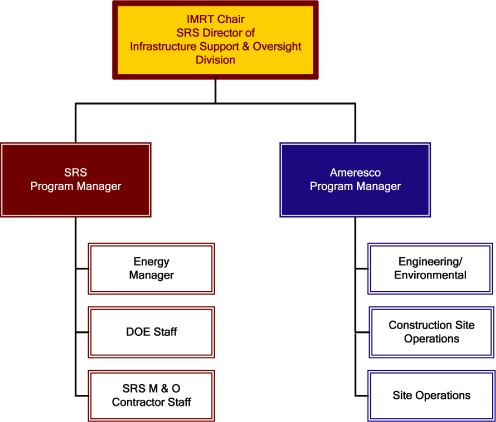
l | Design in accordance with applicable industry codes and design standards for industrial heating plants and power plants (Refer to Appendix D for list of standards) and in accordance with the electrical standards, fire protection standards and stacking lighting standards provided by Government. | ||
l | Design documents will be issued to the Government for review and final concurrence intermittently throughout the first year of the construction period. | ||
l | Acceptance of changes to the approved design requested by the government is at the discretion of Ameresco. |
Revised Final Proposal May 11, 2009 | Biomass Cogeneration Facility and Heating Plants | |
Ameresco Federal Solutions | Savannah River Site | |
Page 62 | Contract DE-AM36-02NT41457 |
l | Ameresco is the responsible authority for the job sites of the proposed ECMs. This includes authority for site management, safety enforcement, document control, quality control, receipt and acceptance of project deliveries, and construction procurement. | ||
l | Ameresco will be responsible for document control management including review and approval of all construction submittals. Ameresco will make electronic copies of major construction submittals available to government representatives upon request. |
Amerescos approach to managing the implementation (construction phase) of the proposed measures will be to assign a fully competent management staff at the construction site and give them the resources and authority to complete our contract obligations safely, timely, and in a professional manner. Each member of the on-site management team, headed by the Site Manager, will have the authority to make project decisions commensurate with their position. Key members of the site project management team include the Site Manager who will also be the Senior Construction Manager, Project Construction Manager (engineering subcontractor representative), Job Superintendent, Site Safety Manager, and Project Documentation Manager. We are currently recruiting, interviewing, and identifying personnel for most site management positions. However, the Site Safety Manager was identified early in the DES phase and has been involved with the project for some time. Mr. Clinton Sandmel will manage the safety program during the construction phase and has interacted with the SRS Safety Office in completing the project safety analyses and plans, as well as overseeing the safety efforts of the geotechnical subcontractor. He is an experienced safety manager and also has experience managing construction safety programs at DOE installations. Mr. Sandmel and other members of the project management team will be relocated (if not already in the local area) to the Aiken/Augusta area for the 30 month construction period mitigating travel and per diem expenses.
Revised Final Proposal May 11, 2009 | Biomass Cogeneration Facility and Heating Plants | |
Ameresco Federal Solutions | Savannah River Site | |
Page 63 | Contract DE-AM36-02NT41457 |
Once construction is complete and the Government accepts the project as operational and the Contract Performance Period begins, the Ameresco staff will shift from implementation to operations using primarily an onsite staff of Ameresco managers, technicians, and support personnel supplemented as necessary by subcontractors and other personnel from within Amerescos corporate resources. The cogeneration facility will operate, and be staffed, 24 hours a days, 7 days a week, 365 days a year while the K and L Area plants, although not staffed, will operate 24 hours a day, 7 days a week during the winter heating season.
Revised Final Proposal May 11, 2009 | Biomass Cogeneration Facility and Heating Plants | |
Ameresco Federal Solutions | Savannah River Site | |
Page 64 | Contract DE-AM36-02NT41457 |
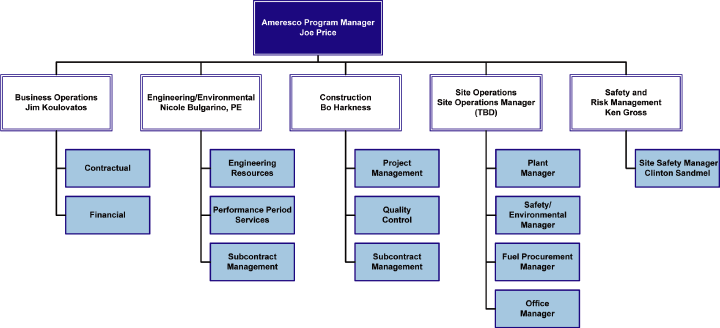
Revised Final Proposal May 11, 2009 | Biomass Cogeneration Facility and Heating Plants | |
Ameresco Federal Solutions | Savannah River Site | |
Page 65 | Contract DE-AM36-02NT41457 |
Revised Final Proposal May 11, 2009 | Biomass Cogeneration Facility and Heating Plants | |
Ameresco Federal Solutions | Savannah River Site | |
Page 66 | Contract DE-AM36-02NT41457 |
Revised Final Proposal May 11, 2009 | Biomass Cogeneration Facility and Heating Plants | |
Ameresco Federal Solutions | Savannah River Site | |
Page 67 | Contract DE-AM36-02NT41457 |
l | Equipment, instrumentation and control systems installed at the Biomass Cogeneration Facility | ||
l | Equipment, instrumentation and control systems installed at the heating plants | ||
l | Buildings and Infrastructures installed at the Biomass Cogeneration Facility Site | ||
l | Building and Infrastructure installed at the K Area Heating Plant Site | ||
l | Building and Infrastructure installed at the L Area Heating Plant Site | ||
l | Utilities within the Facility and the Heating Plant (as defined in Table 1.2 and Table 2.2) |
Revised Final Proposal May 11, 2009 | Biomass Cogeneration Facility and Heating Plants | |
Ameresco Federal Solutions | Savannah River Site | |
Page 68 | Contract DE-AM36-02NT41457 |
l | Access drives and parking lot at the Cogeneration Facility | ||
l | Maintenance of Old Burma Road | ||
l | The existing boiler water treatment equipment and shed at the K Area | ||
l | The existing air compressor at the K Area |
l | Utility interconnections as defined in Table 1.2 and Table 2.2 | ||
l | Existing utility distribution systems | ||
l | All roads except for facility access roads and the reconstructed Old Burma Road | ||
l | New pump system installed at the River Pump House | ||
l | F Area Substation | ||
l | New D Area electrical feeder | ||
l | L Area capacitors | ||
l | All other existing site infrastructure and systems |
l | Operate the facility to meet thermal demand of the Savannah River Site in compliance with applicable local, state and federal permits and regulations. | ||
l | Provide Quality Control for biomass deliveries. | ||
l | Provide a safe work environment for workers and visitors. | ||
l | Perform preventive maintenance in accordance with manufacturer recommendations. | ||
l | Perform major service requirements in accordance with manufacturer recommendations. | ||
l | Maintain professional and positive working relationship with Savannah River Site personnel, SCDHEC, and surrounding neighbors and community. | ||
l | Provide reports as required for M&V activities to meet plant performance guarantees. |
The Safety/Environmental Manager will [**]
The Office Manager will [**]
The Fuel Procurement Manager will [**]
The Plant Manager will [**]
Revised Final Proposal May 11, 2009 | Biomass Cogeneration Facility and Heating Plants | |
Ameresco Federal Solutions | Savannah River Site | |
Page 69 | Contract DE-AM36-02NT41457 |
Revised Final Proposal May 11, 2009 | Biomass Cogeneration Facility and Heating Plants | |
Ameresco Federal Solutions | Savannah River Site | |
Page 70 | Contract DE-AM36-02NT41457 |
Revised Final Proposal May 11, 2009 | Biomass Cogeneration Facility and Heating Plants | |
Ameresco Federal Solutions | Savannah River Site | |
Page 71 | Contract DE-AM36-02NT41457 |
l | Operations including materials and consumables for the cogeneration facility and heating plants, such as costs for the chemicals, urea, diesel fuel, fuel oil, turbine filter, lube oil, and ash disposal. | ||
l | Preventive maintenance includes change out of parts, boiler inspection, boiler cleaning, turbine oil/filter changes, DA tank inspection, pump servicing, grinder and hogger inspection, instrumentation calibration, engine testing, HVAC servicing, building upkeep, Old Burma Road repair, and other service as recommended by equipment suppliers. | ||
l | Unscheduled maintenance includes cost for service and repair not planned on as part of ongoing maintenance. This mainly consists of contracted service support. |
Revised Final Proposal May 11, 2009 | Biomass Cogeneration Facility and Heating Plants | |
Ameresco Federal Solutions | Savannah River Site | |
Page 72 | Contract DE-AM36-02NT41457 |
RESPONSIBILITY/DESCRIPTION | AMERESCOS PROPOSED APPROACH | DOE-SR ASSESSMENT | ||
1. FINANCIAL: |
||||
a. Interest rates: Neither
the Contractor nor the agency
has significant control over
prevailing interest rates.
During all phases of the
project, interest rates will
change with market conditions.
Higher interest rates will
increase project cost,
financing/project term, or
both. The timing of the
Contract award may impact the
available interest rate and
project cost.
|
Ameresco has included preliminary
interest rate information in
Schedule DO-3. The interest rate
shown is indicative of the
financial market at the time of
this Revised Final Proposal and is
provided for information purposes
only. Once locked with Amerescos lender, the interest rate will remain fixed for the term of the contract, thereby providing the DOE-SR with protection against increased interest charges resulting from a variable rate. |
In 6.10 of the
Revised Final
Proposal, the
DOE-SR agrees,
among other things,
to not withhold,
reduce, or setoff
the TOTAL DEBT
SERVICE amount on
Schedule DO-3 in
the event of an
Ameresco default.
The reason for this
is to provide
assurance to
Amerescos lender
that its investment
is secure. The DOE-SR expects the Ameresco to obtain the lowest possible interest rate and will competitively seek financing from several financial institutions. The DOE-SR expects, as consideration for 6.10, that Ameresco will obtain a lower interest rate than the one indicated in the Final Proposal, dated December 8, 2008. |
||
b. Energy prices: Neither the
Contractor nor the agency has
significant control over
actual energy prices. For
calculating savings, the value
of the saved energy may either
be constant, change at a fixed
inflation rate, or float with
market conditions. If the
value changes with the market,
falling energy prices place
the Contractor at risk of
failing to meet cost savings
guarantees. If energy prices
rise, there is a small risk to
the agency that energy
|
The D Area plant that is being
replaced by the Biomass
Cogeneration Facility is fueled by
coal purchased from SCE&G.
Ameresco proposes to establish the
pre-installation baseline for ECMs
1 and 2 based on the consumption
and cost information provided by
SRS and M&O Ameresco personnel.
The baseline costs are escalated at
2008 published NIST rates for each
year of the performance period. The energy savings for all ECMs are calculated based |
The rates used to establish the energy baseline are different than what has been included in DOE HQs database, Energy Management System 4. Based on the unprecedented increases in coal costs over the previous year, the baseline costs associated with coal will come from SRSs current one-year coal contract for the D-Area Powerhouse, which took effect on |
Revised Final Proposal May 11, 2009 | Biomass Cogeneration Facility and Heating Plants | |
Ameresco Federal Solutions | Savannah River Site | |
Page 73 | Contract DE-AM36-02NT41457 |
RESPONSIBILITY/DESCRIPTION | AMERESCOS PROPOSED APPROACH | DOE-SR ASSESSMENT | ||
saving
goals might not be met while
the financial goals are. If
the value of saved energy is
fixed (either constant or
escalated), the agency risks
making payments in excess of
actual energy cost savings.
Clarify how future energy
costs will be treated.
|
on the reduced fuel costs associated
with improved
system efficiencies. To determine
this reduction, the following items
are predetermined for establishing
the pre-installation baseline: the
unit cost of fuel oil and coal, and
the amount of energy produced by
the existing D Area and K Area
plants. The pre-installation baseline data used in this proposal consists of cost and consumption data for a 24 month period as provided by SRS and M&O personnel for ECM 1, and 5 years of data was used to develop the baseline for ECM 2. The future cost of each of these utilities has been escalated by the applicable NIST factors for each year throughout the contract term. Ameresco proposes the DOE-SR assume responsibility for the actual unit cost of utilities (i.e. electricity, coal, water, etc.) including any escalation or de-escalation. If at any time during the term of this contract, the ECMs do not create sufficient savings on an annual basis to fund the amount due Ameresco for reasons within SRS control or for reasons related to changes in unit price of utilities, then SRS will pay Ameresco as agreed or renegotiate the payment schedule and term in a form mutually agreeable to both parties and Amerescos lender such that the outstanding balance of contract payments is fully repaid. Ameresco proposes to assume responsibility for biomass procurement and has estimated the price of biomass based on current local market conditions escalated at [**]% per year. |
November 1,
2008. Based on
market research,
coal is not
expected to
decrease in cost
based on current
and world demand.
In addition, SRSs
electrical rates
have also increased
dramatically over
the last two years
based on the
increased costs of
coal and natural
gas that the Sites
electrical supplier
must recoup through
its electric rates
that have been
approved by the
South Carolina
Public Service
Commission. These
baseline rates will
be escalated in
accordance with
NIST standards. Throughout the performance period, Ameresco will be supplied utilities at no cost but the consumption data will be metered and supplied to the Sites utility department to be included in calculating the true cost of generating steam and/or electricity from the new biomass plants for inclusion in Site supplied utilities. |
Revised Final Proposal May 11, 2009 | Biomass Cogeneration Facility and Heating Plants | |
Ameresco Federal Solutions | Savannah River Site | |
Page 74 | Contract DE-AM36-02NT41457 |
RESPONSIBILITY/DESCRIPTION | AMERESCOS PROPOSED APPROACH | DOE-SR ASSESSMENT | ||
c. Construction costs: The
Contractor is responsible for
determining construction costs
and defining a budget. In a
fixed-price design/build
Contract, the agency assumes
little responsibility for cost
overruns. However, if
construction estimates are
significantly greater than
originally assumed, the
Contractor may find that the
project or measure is no
longer viable and drop it
before Contract award. In any
design/build Contract, the
agency loses some design
control. Clarify design
standards and the design
approval process (including
changes) and how costs will be
reviewed.
|
A significant portion of Amerescos
business is focused on energy
engineering, design and consulting.
Ameresco staff, complemented by
subcontracted experts, are
developing the ECM designs for this
proposal. Additionally, Amerescos
in-house construction management
team has collaborated extensively
with the design team, potential
subcontractors, and equipment
suppliers to assure project
constructability, review budgeted
costs, and provide insight into
procurement options. Having all
these functions involved throughout
the DES Phase substantially lowers
the risk of construction cost
overruns, and ensures a realistic
and balanced approach to innovation
and realism in project design. To manage the risk associated with escalating prices for construction materials and equipment, Ameresco will hold material and labor pricing set forth in Schedule DO 2 included herein through May 15, 2009. The proposal acceptance period may be extended; however, there may be changes in project pricing. The parties will share the risk of construction cost increases that occur prior to contract award; however, Ameresco will assume sole responsibility for cost increases occurring in normal market conditions after contract award as well as responsibility for managing the risks of such increases. However, should cost increases be caused by extraordinary market conditions, the parties will negotiate changes to the construction completion schedule and/or financial terms of the contract as mutually agreeable to both parties. |
Upon submittal of the Revised Final Proposal, a Cost Reasonableness Review of Amerescos Implementation Costs will be performed. Ameresco shall submit a breakdown of the Implementation costs with the Revised Final Proposal to allow the DOE-SR to perform the review. |
Revised Final Proposal May 11, 2009 | Biomass Cogeneration Facility and Heating Plants | |
Ameresco Federal Solutions | Savannah River Site | |
Page 75 | Contract DE-AM36-02NT41457 |
RESPONSIBILITY/DESCRIPTION | AMERESCOS PROPOSED APPROACH | DOE-SR ASSESSMENT | ||
Design-build will be the means of project implementation, and the proposed project will be designed and constructed to meet industry and those local SRS standards identified in this proposal, and included with the contract award. | ||||
[**]. | ||||
The basic contract establishes maximums for Ameresco mark-ups for both the implementation and performance periods. Mark-ups proposed in this proposal are below the maximums allowed by the BAMF Contract. Mark-ups associated with changes resulting from concealed or environmental conditions of the project site, customer requests, or a change in contract requirements will be negotiated at the time the change is incorporated into the contract delivery order, but shall never exceed the maximum allowed by the BAMF Contract. | ||||
d. M&V costs: The agency
assumes the financial
responsibility for M&V costs
directly or through the
Contractor. If the agency
wishes to reduce M&V cost, it
may do so by accepting less
rigorous M&V activities with
more uncertainty in the
savings estimates. Clarify
how project savings are being
verified (e.g. equipment
performance, operational
factors, energy use) and the
impact on M&V costs.
|
Ameresco proposes that M&V Option B ECM Isolation be used to verify the performance of ECM 1 and ECM 2. Project performance will be continuously metered and reported to the DOE-SR on a monthly basis. The metering equipment installed for the project, in combination with the established baseline energy costs and NIST-based annual adjustments, will provide sufficient M&V of project performance without unnecessarily increasing project costs. Section 4.4 describes the M&V plan in detail. | The DOE-SR concurs with the M&V approach for the project. |
Revised Final Proposal May 11, 2009 | Biomass Cogeneration Facility and Heating Plants | |
Ameresco Federal Solutions | Savannah River Site | |
Page 76 | Contract DE-AM36-02NT41457 |
RESPONSIBILITY/DESCRIPTION | AMERESCOS PROPOSED APPROACH | DOE-SR ASSESSMENT | ||
Performance Period M&V costs are escalated annually at a fixed rate of [**]%. | ||||
e. Non-Energy Cost Savings:
The agency and the ESCO may
agree that the project will
include savings from recurring
and/or one-time costs. This
may include one-time savings
from avoided expenditures for
projects that were
appropriated but will no
longer be necessary.
Including one-time cost
savings before the money has
been appropriated entails some
risk to the agency. Recurring
savings generally result from
reduced O&M expenses or
reduced water consumption.
These O&M and water savings
must be based on actual
spending reductions. Clarify
sources of non-energy cost
savings and how they will be
verified.
|
Both proposed ECMs will result in
the shutdown of existing DOE-SR
operated plants eliminating
significant O&M expenses currently
incurred by SRS. The O&M cost
baseline is presented for each ECM
and was developed based on
information, and is collaborative
effort between Ameresco, SRS and
M&O technical personnel. The annual O&M savings have been escalated annually at a fixed rate of [**]%. NOTE: There will be a significant reduction in the consumption of water taken from the Savannah River, although no cost savings related to such reduction in water usage have been included in this proposal. |
The DOE-SR has provided actual O&M costs for both the D-Area Powerhouse and the K-Area Package Boilers. The DOE-SR will review such costs included in the Revised Final Proposal and, if acceptable, provide its concurrence. | ||
f. Delays: Both the
Contractor and the agency can
cause delays. Failure to
implement a viable project in
a timely manner costs the
agency in the form of lost
savings, and can add cost to
the project (e.g.,
construction interest,
remobilization). Clarify
schedule and how delays will
be handled.
|
Ameresco will fully support the
DOE-SR during the review, approval,
and award of the proposed ECMs to
mitigate potential delays as much
as is within Amerescos control.
Further, Ameresco will honor the
pricing proposed herein through May
15, 2009; delays in contract award
beyond that time may result in
increased project cost and will
result in project implementation
delays. Major milestones for obtaining project approvals, delivery order award, and project implementation are indentified in Table 1.7 herein. Ameresco will provide a |
SRS will fully support Ameresco during the review, approval, and award of the proposed ECMs to mitigate potential delays, and award the Delivery Order on schedule. In addition, DOE and the M&O Contractor will work with Ameresco to facilitate a smooth mobilization to the Site and coordinate the interfaces for key support requirements provided by SRS. Critical interface requirements should be identified on Amerescos schedule to allow for adequate up front coordination. |
Revised Final Proposal May 11, 2009 | Biomass Cogeneration Facility and Heating Plants | |
Ameresco Federal Solutions | Savannah River Site | |
Page 77 | Contract DE-AM36-02NT41457 |
RESPONSIBILITY/DESCRIPTION | AMERESCOS PROPOSED APPROACH | DOE-SR ASSESSMENT | ||
detailed project schedule
subsequent to contract award
reflecting the scheduled completion
date for each major element of ECM
1 and 2. The schedule will be
closely monitored throughout the
construction phase by Amerescos
on-site management team as well as
corporate management. Their
proactive involvement will mitigate
the occurrence of delays. Should a
delay occur, Ameresco management
will immediately develop a
mitigation plan, discuss it with
the DOE-SR staff, and then take the
necessary actions to ensure the
project remains on schedule. Schedule Risks & Mitigation Schedule Delays The potential for schedule delays will be constantly monitored, and immediate and appropriate mitigation actions will be taken by Ameresco management personnel if necessary. The schedule is being structured both logically and realistically to minimize the potential for delays; however, should an unavoidable delay occur, Ameresco will work closely with DOE-SR engineers to determine the best course of action and, if necessary, a revised schedule will be developed and proposed. The primary objective of any revision will be to get the work back on track without extending the completion date. Subcontractor Management Ameresco has pre-qualified many firms and will continue to pre-qualify firms that may be selected as |
Revised Final Proposal May 11, 2009 | Biomass Cogeneration Facility and Heating Plants | |
Ameresco Federal Solutions | Savannah River Site | |
Page 78 | Contract DE-AM36-02NT41457 |
RESPONSIBILITY/DESCRIPTION | AMERESCOS PROPOSED APPROACH | DOE-SR ASSESSMENT | ||
subcontractors.
However, Ameresco will continue to
evaluate qualifications and the
firms current workload prior to
executing any subcontracts. If
manpower later becomes an issue,
Ameresco will either direct the
firm to hire additional personnel,
hire additional subcontractors, or
replace the subcontractor. Ameresco will manage subcontractors and suppliers through close control and monitoring of all critical activities. Monitoring and controls include the following procedures: weekly progress meetings, schedule updates, and materials management plan. Late Delivery of Materials/Equipment In order to protect against late delivery of material or equipment and keep the project on schedule, Ameresco will implement and maintain a materials management plan and constantly monitor production and delivery dates. |
||||
g. Major changes in facility:
The agency (or Congress)
controls major changes in
facility use, including
closure. Clarify
responsibilities in the event
of a premature facility
closure, loss of funding, or
other major change.
|
The SRS is not considered a
candidate for closure at any time
in the foreseeable future. Based
on information provided by SRS
personnel, a build-up in operations
is projected to continue past 2020.
The electrical and steam demand
are projected to change in future
years, but it is assumed (almost
certain) that the site will be a
viable entity throughout the
contract term and well beyond. The structure of the proposed project significantly reduces risk associated with changes at the site. Ameresco will be producing steam that will provide two |
The DOE-SR concurs with Amerescos projection of the longevity of SRS operations. If a termination were necessary, the DOE Contracting Officer and Ameresco would proceed utilizing the applicable Federal Acquisition Regulation (FAR) and Department of Energy Acquisition Regulation (DEAR) requirements. |
Revised Final Proposal May 11, 2009 | Biomass Cogeneration Facility and Heating Plants | |
Ameresco Federal Solutions | Savannah River Site | |
Page 79 | Contract DE-AM36-02NT41457 |
RESPONSIBILITY/DESCRIPTION | AMERESCOS PROPOSED APPROACH | DOE-SR ASSESSMENT | ||
benefits to the DOE-SR; steam for
thermal processes and electricity.
Should changes at the facility
result in reduced thermal
requirements, Ameresco will produce
more electricity. The first
priority will be to satisfy the
sites steam needs. Should there
be excess capacity (delta between
guaranteed steam production and
site steam requirements) the steam
will be processed through a turbine
to produce electricity. The
versatility of the process to
satisfy both thermal and electrical
needs of the site mitigates this
risk. Ameresco has assessed the potential for closure of the site and considers it a minimal risk at this time. However, if SRS should close or experience a significant reduction, then Ameresco will be responsible for characterizing and quantifying the impact of the changes on the project. In a severe case, though highly improbable, it may necessitate either a partial or full termination for convenience; however, the contract will include a Termination Liability Schedule to facilitate arriving at appropriate termination costs. If a termination becomes necessary, Ameresco would comply with the applicable Federal Acquisition Regulation (FAR) and Department of Energy Acquisition Regulation (DEAR) requirements. |
||||
2. OPERATIONAL: |
||||
a. Operating hours: The
agency generally has control
over the operating hours.
Increases and decreases in
operating hours can show up as
increases or decreases in
savings depending on
|
Operating hours of the proposed cogeneration facility and heating plants have been pre-determined. The operating hours of SRS facilities obtaining service from the Ameresco plants (i.e., steam and/or electricity) | The DOE-SR concurs with this approach since the ASG will not be dependent on facility operating hours. Excess steam above the customer requirements will be |
Revised Final Proposal May 11, 2009 | Biomass Cogeneration Facility and Heating Plants | |
Ameresco Federal Solutions | Savannah River Site | |
Page 80 | Contract DE-AM36-02NT41457 |
RESPONSIBILITY/DESCRIPTION | AMERESCOS PROPOSED APPROACH | DOE-SR ASSESSMENT | ||
the M&V
method (e.g. operating hours
multiplied by improved
efficiency of equipment vs.
whole building/utility bill
analysis). Clarify whether
operating hours are to be
measured or stipulated and
what the impact will be if
they change. If the operating
hours are stipulated, the
baseline should be carefully
documented and agreed to by
both parties.
|
were also
determined for purposes of
establishing baseline consumption
data, but will have little to no
impact on the operations of the
proposed ECMs unless increased
operating hours contributes to the
site requiring more steam than
provided by the ASG. ECM 1, the cogeneration facility (replacing existing D Area plant) shall operate 24/7 year round and ECM 2, the K and L Area plants will operate 24/7 as necessary over approximately a four month period each year to meet building heating loads. Although operating hours are pre-determined, steam delivery requirements will be both pre-determined and measured. Over the past two years, SRS energy consumption has been relatively consistent in conjunction with the operating hours. Therefore, the energy baseline and guarantees assume predetermined operating hours for the term of the delivery order; however, Ameresco will guarantee an annual quantity of steam production that will not be impacted by changes to facility operating hours. The DOE-SR will control and be responsible for its increasing or decreasing facility operating hours. |
dispatched for electrical generation. | ||
b. Load: Equipment loads can
change over time. The agency
generally has control over
hours of operation,
conditioned floor area,
intensity of use (e.g. changes
in occupancy or level of
automation). Changes in load
can show up as increases or
decreases in savings
depending on the M&V
|
The overall site steam load is expected to decrease in the out years of the contract performance period. Ameresco and DOE-SR personnel worked closely during the DES phase to construct a model of out year steam requirements to accommodate the decreases. Project performance calculations are based on load | The DOE-SR agrees with Amerescos proposed approach. Additional steam requested by the DOE-SR above the ASG will be compensated for at Amerescos incremental biomass expense with a mutually negotiated markup. |
Revised Final Proposal May 11, 2009 | Biomass Cogeneration Facility and Heating Plants | |
Ameresco Federal Solutions | Savannah River Site | |
Page 81 | Contract DE-AM36-02NT41457 |
RESPONSIBILITY/DESCRIPTION | AMERESCOS PROPOSED APPROACH | DOE-SR ASSESSMENT | ||
method.
Clarify whether equipment
loads are to be measured or
stipulated and what the impact
will be if they change. If
the equipment loads are
stipulated, the baseline
should be carefully documented
and agreed to by both parties.
|
projections shown in Table
1.1, which were provided by site
personnel and are assumed by
Ameresco to be correct. Decreasing
steam requirements will be
accommodated by increasing net
green power generation. Increasing
steam requirements above ASG
(excess production) will be
accommodated up to the maximum
plant capacity. Compensation for
the excess steam production will be
included in the annual cost
adjustment. It is proposed that the DOE-SR and Ameresco share the risk of increased load requirements. Ameresco will assume responsibility for providing the steam to meet increased loads up to the maximum plant capacity. However, Ameresco will be compensated for steam deliveries above the guaranteed annual production quantities as provided for by the fuel adjustment provision found in Section 1.3.1.2 of this proposal. |
|||
c. Weather: A number of
energy efficiency measures are
affected by weather. Neither
the Contractor nor the agency
has control over the weather.
Changes in weather can
increase or decrease savings
depending on the M&V method
(e.g. equipment run hours
multiplied by efficiency
improvement vs. whole building
utility bill analysis). If
weather is normalized,
actual savings could be less
than payments for a given
year, but will average out
over the long run. Clearly
specify how weather
corrections will be performed.
|
Neither Ameresco nor the DOE-SR has
control over the weather and
changes in weather can increase or
decrease the amount of steam needed
by SRS facilities. However, the
metric for determining whether
Ameresco has satisfied its
performance guarantees are not
weather dependent; therefore,
weather corrections are not be
necessary. Ameresco proposes that
no weather corrections be made as
neither ECM will be significantly
impacted by the weather since the
baseline has been developed from
historical consumption data. NOTE: Although weather could impact the amount of steam needed for heating purposes, that risk has been |
The DOE-SR agrees with Amerescos proposed approach. |
Revised Final Proposal May 11, 2009 | Biomass Cogeneration Facility and Heating Plants | |
Ameresco Federal Solutions | Savannah River Site | |
Page 82 | Contract DE-AM36-02NT41457 |
RESPONSIBILITY/DESCRIPTION | AMERESCOS PROPOSED APPROACH | DOE-SR ASSESSMENT | ||
addressed by increased electrical generation as outlined in paragraph b above. | ||||
d. User participation: Many
energy conservation measures
require user participation to
generate savings (e.g. control
settings). The savings can be
variable and the Contractor
may be unwilling to invest in
these measures. Clarify what
degree of user participation
is needed and utilize
monitoring and training to
mitigate risk. If performance
is stipulated, document and
review assumptions carefully
and consider M & V to confirm
the capacity to save (e.g.
confirm that the controls are
functioning properly).
|
Ameresco will operate and maintain the systems proposed under both ECMs as defined in Section 5.2.7.1. The ECMs will interconnect with site utility distribution systems that will be maintained by the site M&O Contractor, as is currently the case. The DOE-SR will be the end user of the steam produced by the Ameresco plants. The Government must accept steam deliveries and the site M&O contractor must ensure utility services are available for the ECMs to be effective. The risk of either the DOE-SR not accepting steam deliveries (within the baseline amounts) or the utility systems being down over prolonged period of time is minimal. | The DOE-SR agrees with Amerescos proposed approach. | ||
3. PERFORMANCE: |
||||
a. Equipment performance:
Generally the Contractor has
control over the selection of
equipment and is responsible
for its proper installation,
commissioning, and
performance. Generally the
Contractor has responsibility
to demonstrate that the new
improvements meet expected
performance levels including
specified equipment capacity,
standards of service, and
efficiency. Clarify who is
responsible for initial and
long-term performance, how it
will be verified, and what
will be done if performance
does not meet expectations.
|
Ameresco will retain responsibility for the performance of the equipment throughout the term of the performance period for both ECMs as defined in Section 5.2.7.1. Ameresco has experience and is familiar with the equipment. It selected the equipment based upon efficiency, performance level, and reliability, and in conjunction with the manufacturers service and performance guarantees. Performance of the equipment will be reflected in the annual M&V documentation provided by Ameresco. | The DOE-SR agrees with Amerescos proposed approach. | ||
b. Operations: Responsibility
for operations is negotiable,
and it can impact performance.
Clarify
|
Ameresco will retain operations responsibility and assumes the risks associated with ECM operations | The DOE-SR agrees with the Amerescos proposed approach. |
Revised Final Proposal May 11, 2009 | Biomass Cogeneration Facility and Heating Plants | |
Ameresco Federal Solutions | Savannah River Site | |
Page 83 | Contract DE-AM36-02NT41457 |
RESPONSIBILITY/DESCRIPTION | AMERESCOS PROPOSED APPROACH | DOE-SR ASSESSMENT | ||
responsibility for
operations, the implications
of equipment control, how
changes in operating
procedures will be handled,
and how proper operations will
be assured.
|
throughout the contract
term as defined in Section 5.2.7.1.
Proper operations will be assured
by appropriate staffing levels of
the plant by local Ameresco
personnel and/or contracted
employees. Ameresco site management will implement and oversee plant operations to ensure equipment is operated and maintained to provide an efficient and safe operation that satisfies manufacturer and contract requirements. Title to the biomass fuel will pass to the DOE-SR upon delivery to the plant site. Should the biomass fuel become damaged or destroyed due to the fault or negligence of Ameresco, then Ameresco shall bear responsibility for replacing such damaged biomass fuel. Otherwise, DOE-SRS shall be responsible for any biomass fuel damaged or destroyed for any other reason. |
|||
c. Preventive Maintenance:
Responsibility for maintenance
is negotiable, and it can
impact performance. Clarify
how long-term preventative
maintenance will be assured,
especially if the party
responsible for long-term
performance is not responsible
for maintenance (e.g.,
Contractor provides
maintenance checklist and
reporting frequency). Clarify
who is responsible for
long-term preventive
maintenance to maintain
operational performance
throughout the Contract term.
Clarify what will be done if
inadequate preventive
maintenance impacts
performance.
|
Ameresco assumes responsibility for all maintenance and repairs of the equipment installed in the new facility under the contract term as defined in Section 5.2.7.1. This includes a preventative maintenance program, incidental repairs, and warranty work. Ameresco will verify performance of the maintenance on an on-going basis, with an in-depth review of the maintenance program conducted during annual performance reconciliation. The ongoing costs of operations and maintenance for the equipment is included in the performance period expenses and escalated annually at [**]% for the duration of the performance period. | The DOE-SR agrees with Amerescos proposed approach. |
Revised Final Proposal May 11, 2009 | Biomass Cogeneration Facility and Heating Plants | |
Ameresco Federal Solutions | Savannah River Site | |
Page 84 | Contract DE-AM36-02NT41457 |
RESPONSIBILITY/DESCRIPTION | AMERESCOS PROPOSED APPROACH | DOE-SR ASSESSMENT | ||
d. Equipment Repair and
Replacement: Responsibility
for repair and replacement of
Contractor-installed equipment
is negotiable; however it is
often tied to project
performance. Clarify who is
responsible for the
replacement of failed
components or equipment
throughout the term of the
Contract. Specifically
address potential impacts on
performance due to equipment
failure. Specify expected
equipment life and warranties
for all installed equipment.
Discuss replacement
responsibility when equipment
life is shorter than the term
of the Contract.
|
Ameresco will assume responsibility for the repair and/or replacement of failed components and equipment throughout the term of the contract as specified in Section 5.2.7.2 except for such damaged or destroyed ECM equipment for which the DOE-SR self-insures pursuant to Section 6.5 of the Revised Final Proposal. | As part of the Performance Period expenses, Ameresco has included, and is clearly responsible for, all Repair & Replacement functions. Only Ameresco-installed equipment that is damaged or destroyed for reasons beyond the control and without the fault or negligence of Ameresco, may result in consideration as noted in Section 6.5 of the Revised Final Proposal. |
Revised Final Proposal May 11, 2009 | Biomass Cogeneration Facility and Heating Plants | |
Ameresco Federal Solutions | Savannah River Site | |
Page 85 | Contract DE-AM36-02NT41457 |
a) | Performance/Payment Bond Performance and payment bonds are a requirement of the Contract. The performance bond is purchased by Ameresco to protect the Government and the third party lender against Ameresco non-performance during the implementation period. The performance bond applies only to the installation portion of the work under this contract and does not apply in any way to energy savings guarantees, payments or maintenance provisions, except that the performance bond shall guarantee that the installation will be free of defective materials and workmanship for a period of twelve (12) months following completion and acceptance of the work. Amerescos lender will require the execution a Dual-Obligee Rider naming such lender as an additional or dual-obligee under the performance bond. | ||
b) | Interest During Construction (IDC) This cost represents the interest costs accruing to Ameresco during the proposed implementation period. Amerescos DO-Schedules assume a traditional upfront funding of the Total Amount Financed into an interest bearing escrow account upon award of the contract, Ameresco will be charged interest on the amount funded at the project interest rate and will net these interest charges with interest earnings on the escrow accounts remaining principal balance. Ameresco will receive progress payments |
Revised Final Proposal May 11, 2009 | Biomass Cogeneration Facility and Heating Plants | |
Ameresco Federal Solutions | Savannah River Site | |
Page 86 | Contract DE-AM36-02NT41457 |
for implementation expenses from the escrow account. In addition to the traditional escrow funding approach, Ameresco is exploring a delayed funding structure in lieu of the traditional escrow funding structure proposed herein. Under the delayed funding structure, Amerescos lender will advance progress payments to Ameresco periodically during the construction period. Interest will begin to accrue only on the progress payments made to Ameresco and accrued interest will negatively amortize the outstanding balance. Ameresco believes if it is able to utilize the delayed funding structure it will provide significant savings on interest during construction. | |||
c) | Finance Processing Fee The finance processing fee represents expenses Ameresco will incur to finance the contract. Typically, this fee is a combination of the following applicable expenses: legal fees, origination fees, fees for rating agencies, rate lock fees to fix the interest rate during the implementation period, trustee or fiscal agent fees, and any rate buydown costs. |
Revised Final Proposal May 11, 2009 | Biomass Cogeneration Facility and Heating Plants | |
Ameresco Federal Solutions | Savannah River Site | |
Page 87 | Contract DE-AM36-02NT41457 |
Revised Final Proposal May 11, 2009 | Biomass Cogeneration Facility and Heating Plants | |
Ameresco Federal Solutions | Savannah River Site | |
Page 88 | Contract DE-AM36-02NT41457 |
Revised Final Proposal May 11, 2009 | Biomass Cogeneration Facility and Heating Plants | |
Ameresco Federal Solutions | Savannah River Site | |
Page 89 | Contract DE-AM36-02NT41457 |
Revised Final Proposal May 11, 2009 | Biomass Cogeneration Facility and Heating Plants | |
Ameresco Federal Solutions | Savannah River Site | |
Page 90 | Contract DE-AM36-02NT41457 |
Revised Final Proposal May 11, 2009 | Biomass Cogeneration Facility and Heating Plants | |
Ameresco Federal Solutions | Savannah River Site | |
Page 91 | Contract DE-AM36-02NT41457 |
SCHEDULES
Delivery Order No.: | Contractor Name: | Project Site: | ||||||||||
DE-AT09-09SR22572 dated 15-May-2009 | Ameresco Federal Solutions | Savannah River Site | ||||||||||
(a) | (b) | (c) | ||||||||||
Initial Estimated | Proposed Guaranteed | Annual | ||||||||||
Performance | Annual | Annual | Contractor | |||||||||
Period | Cost Savings | Cost Savings | Payments | |||||||||
Year | $ | $ | $ | |||||||||
ZERO (6) |
[**] | [**] | [**] | |||||||||
ONE |
[**] | [**] | [**] | |||||||||
TWO |
[**] | [**] | [**] | |||||||||
THREE |
[**] | [**] | [**] | |||||||||
FOUR |
[**] | [**] | [**] | |||||||||
FIVE |
[**] | [**] | [**] | |||||||||
SIX |
[**] | [**] | [**] | |||||||||
SEVEN |
[**] | [**] | [**] | |||||||||
EIGHT |
[**] | [**] | [**] | |||||||||
NINE |
[**] | [**] | [**] | |||||||||
TEN |
[**] | [**] | [**] | |||||||||
ELEVEN |
[**] | [**] | [**] | |||||||||
TWELVE |
[**] | [**] | [**] | |||||||||
THIRTEEN |
[**] | [**] | [**] | |||||||||
FOURTEEN |
[**] | [**] | [**] | |||||||||
FIFTEEN |
[**] | [**] | [**] | |||||||||
SIXTEEN |
[**] | [**] | [**] | |||||||||
SEVENTEEN |
[**] | [**] | [**] | |||||||||
EIGHTEEN |
[**] | [**] | [**] | |||||||||
NINETEEN |
[**] | [**] | [**] | |||||||||
TWENTY |
[**] | [**] | [**] | |||||||||
TWENTY-ONE |
[**] | [**] | [**] | |||||||||
TWENTY-TWO |
[**] | [**] | [**] | |||||||||
TWENTY-THREE |
[**] | [**] | [**] | |||||||||
TWENTY-FOUR |
[**] | [**] | [**] | |||||||||
TWENTY-FIVE |
[**] | [**] | [**] | |||||||||
TOTALS |
[**] | [**] | [**] | |||||||||
(1) | The first year DES Proposed Annual Cost Savings shall reflect technical proposal & engineering estimates as presented in DO-4. above represents a 16 month period (January 2012 to April 2013) and is calculated by dividing the DO-4 savings by 12 months and then multiplying such amount by 16 months. | |
(2) | The Guaranteed Annual Cost Savings are based on the site specific M&V plan. | |
(3) | The Annual Contractor Payments represent the deliver order price and should be supported by information submitted in Schedules DO-2 and DO-3. | |
(4) | The Guaranteed Annual Cost Savings must exceed the Annual Contractor Payments for each performance period year. | |
(5) | Provider escalation rates applied to DES Proposed Annual Cost Savings in column (a) as follows: |
(a) | Energy Rates Table S-3; Water Rates [**]%. | ||
(b) | Energy Related O&M Savings [**]%. |
(6) | Year Zero Contractor Payment includes $300,000 deposit into the PPEF. |
Project Site: | Delivery Order No.: | Contractor Name: | ||||||||||||||||
Savannah River Site | DE-AT09-09SR22572 dated 15-May-2009 | Ameresco Federal Solutions | ||||||||||||||||
C.2.2 | ||||||||||||||||||
Technology | (a) | (b) | (c) = (a) x (1+b) | |||||||||||||||
Category | ECM | ECM | Total Implementation | Mark-up | ||||||||||||||
Letter | No. | ECM Description - Title | Size | Expense | % | Implementation Price | ||||||||||||
$ | | |||||||||||||||||
DES/Proposal Development Costs | [**] | [**] | % | $ | 1,164,800 | |||||||||||||
r |
1 | D Area Biomass Replacement Plant | 240,000 pph; 20 MW | [**] | [**] | % | $ | 137,500,762 | ||||||||||
r |
2 | K&L Area Biomass Replacement Plant | (2) 10,500 pph | [**] | [**] | % | $ | 10,507,004 | ||||||||||
[**] | $ | 149,172,566 | ||||||||||||||||
Bonded Amount ($) |
$ 149,172,566 |
Notes: | ||
1) | Total Implementation Expenses shall include direct costs as specified in the Contract or in negotiated B Schedules. | |
2) | Contractor shall propose bonded amount representing the basis of establishing performance and payment bonds per Section H in IDIQ. | |
3) | Proposed bonded amount is assumed to include markup applied to ECM expenses above, unless otherwise specified by Contractor. | |
4) | Bonded Amount ($) negotiated will be used to establish Performance and Payment Bond sums per Section H. |
Project Site: Savannah River Site |
Delivery Order No: DE-AT09-09SR22572 dated 15-May-2009 |
Contractor: Ameresco Federal Solutions |
Delivery Order No: SRS BAMF Revised Final Proposal 11-May-2009 |
Project Capitalization |
||||
Total Implementation Price (DO-2 Total) |
$ | 149,172,566 | ||
Finance Procurement Price ($) |
$ | 25,003,318 | ||
Add: Financed PPEF Deposit (See Note 5) |
$ | 9,200,000 | ||
Less: Pre-Performance Period Payments |
$ | | ||
TOTAL AMOUNT FINANCED |
$ | 183,375,883 |
Applicable Financial |
||||
Index |
Moodys AA Corporate | |||
Term (Years) |
12.0 | |||
Index Rate |
6.14 | % | ||
Added Premium |
2.05 | % | ||
Project Interest Rate |
8.19 | % |
Issue Date: |
May 12, 2009 | |
Source: |
Bloomberg | |
Effective Through: |
N/A |
0 | 1 | 2 | 3 | 4 | 5 | 6 | 7 | 8 | 9 | 10 | 11 | 12 | 13 | 14 | 15 | 16 | 17 | 18 | 19 | 20 | ||||||||||||||||||||||||||||||||||||||||||||||||||||||||||||||||||||
Term 19 years | Year 1 | Year 2 | Year 3 | Year 4 | Year 5 | Year 6 | Year 7 | Year 8 | Year 9 | Year 10 | Year 11 | Year 12 | Year 13 | Year 14 | Year 15 | Year 16 | Year 17 | Year 18 | Year 19 | Year 20 | Totals | |||||||||||||||||||||||||||||||||||||||||||||||||||||||||||||||||||
Annual Cash Flow (Performance Period) |
||||||||||||||||||||||||||||||||||||||||||||||||||||||||||||||||||||||||||||||||||||||||
Debt Service: |
||||||||||||||||||||||||||||||||||||||||||||||||||||||||||||||||||||||||||||||||||||||||
Interest ($) |
[**] | [**] | [**] | [**] | [**] | [**] | [**] | [**] | [**] | [**] | [**] | [**] | [**] | [**] | [**] | [**] | [**] | [**] | [**] | [**] | [**] | [**] | ||||||||||||||||||||||||||||||||||||||||||||||||||||||||||||||||||
Principal Repayment ($) |
[**] | [**] | [**] | [**] | [**] | [**] | [**] | [**] | [**] | [**] | [**] | [**] | [**] | [**] | [**] | [**] | [**] | [**] | [**] | [**] | [**] | [**] | ||||||||||||||||||||||||||||||||||||||||||||||||||||||||||||||||||
TOTAL DEBT SERVICE(a) |
[**] | [**] | [**] | [**] | [**] | [**] | [**] | [**] | [**] | [**] | [**] | [**] | [**] | [**] | [**] | [**] | [**] | [**] | [**] | [**] | [**] | [**] | ||||||||||||||||||||||||||||||||||||||||||||||||||||||||||||||||||
Performance Period Expenses: |
||||||||||||||||||||||||||||||||||||||||||||||||||||||||||||||||||||||||||||||||||||||||
Management/Administration ($) |
[**] | [**] | [**] | [**] | [**] | [**] | [**] | [**] | [**] | [**] | [**] | [**] | [**] | [**] | [**] | [**] | [**] | [**] | [**] | [**] | [**] | [**] | ||||||||||||||||||||||||||||||||||||||||||||||||||||||||||||||||||
Maintenance & Operation ($) |
[**] | [**] | [**] | [**] | [**] | [**] | [**] | [**] | [**] | [**] | [**] | [**] | [**] | [**] | [**] | [**] | [**] | [**] | [**] | [**] | [**] | [**] | ||||||||||||||||||||||||||||||||||||||||||||||||||||||||||||||||||
Repair and Replacement ($) |
[**] | [**] | [**] | [**] | [**] | [**] | [**] | [**] | [**] | [**] | [**] | [**] | [**] | [**] | [**] | [**] | [**] | [**] | [**] | [**] | [**] | [**] | ||||||||||||||||||||||||||||||||||||||||||||||||||||||||||||||||||
Measurement and Verification ($) |
[**] | [**] | [**] | [**] | [**] | [**] | [**] | [**] | [**] | [**] | [**] | [**] | [**] | [**] | [**] | [**] | [**] | [**] | [**] | [**] | [**] | [**] | ||||||||||||||||||||||||||||||||||||||||||||||||||||||||||||||||||
Permits and Licenses ($) |
[**] | [**] | [**] | [**] | [**] | [**] | [**] | [**] | [**] | [**] | [**] | [**] | [**] | [**] | [**] | [**] | [**] | [**] | [**] | [**] | [**] | [**] | ||||||||||||||||||||||||||||||||||||||||||||||||||||||||||||||||||
Insurance ($) |
[**] | [**] | [**] | [**] | [**] | [**] | [**] | [**] | [**] | [**] | [**] | [**] | [**] | [**] | [**] | [**] | [**] | [**] | [**] | [**] | [**] | [**] | ||||||||||||||||||||||||||||||||||||||||||||||||||||||||||||||||||
Property Taxes ($) |
[**] | [**] | [**] | [**] | [**] | [**] | [**] | [**] | [**] | [**] | [**] | [**] | [**] | [**] | [**] | [**] | [**] | [**] | [**] | [**] | [**] | [**] | ||||||||||||||||||||||||||||||||||||||||||||||||||||||||||||||||||
Other Biomass Fuel ($) |
[**] | [**] | [**] | [**] | [**] | [**] | [**] | [**] | [**] | [**] | [**] | [**] | [**] | [**] | [**] | [**] | [**] | [**] | [**] | [**] | [**] | [**] | ||||||||||||||||||||||||||||||||||||||||||||||||||||||||||||||||||
SUBTOTAL Performance Period Expenses |
[**] | [**] | [**] | [**] | [**] | [**] | [**] | [**] | [**] | [**] | [**] | [**] | [**] | [**] | [**] | [**] | [**] | [**] | [**] | [**] | [**] | [**] | ||||||||||||||||||||||||||||||||||||||||||||||||||||||||||||||||||
Performance Period Mark-Up All PPEs other than Biomass at 28% |
[**] | [**] | [**] | [**] | [**] | [**] | [**] | [**] | [**] | [**] | [**] | [**] | [**] | [**] | [**] | [**] | [**] | [**] | [**] | [**] | [**] | [**] | ||||||||||||||||||||||||||||||||||||||||||||||||||||||||||||||||||
Performance Period Mark-Up (%) Biomass at 22% |
[**] | [**] | [**] | [**] | [**] | [**] | [**] | [**] | [**] | [**] | [**] | [**] | [**] | [**] | [**] | [**] | [**] | [**] | [**] | [**] | [**] | [**] | ||||||||||||||||||||||||||||||||||||||||||||||||||||||||||||||||||
Performance Period Mark-Up ($) |
[**] | [**] | [**] | [**] | [**] | [**] | [**] | [**] | [**] | [**] | [**] | [**] | [**] | [**] | [**] | [**] | [**] | [**] | [**] | [**] | [**] | [**] | ||||||||||||||||||||||||||||||||||||||||||||||||||||||||||||||||||
TOTAL PERFORMANCE PERIOD EXPENSES (b) |
[**] | [**] | [**] | [**] | [**] | [**] | [**] | [**] | [**] | [**] | [**] | [**] | [**] | [**] | [**] | [**] | [**] | [**] | [**] | [**] | [**] | [**] | ||||||||||||||||||||||||||||||||||||||||||||||||||||||||||||||||||
PPEF Deposit ECM-2 from Year 0 Savings(c) |
[**] | [**] | [**] | [**] | [**] | [**] | [**] | [**] | [**] | [**] | [**] | [**] | [**] | [**] | [**] | [**] | [**] | [**] | [**] | [**] | [**] | [**] | ||||||||||||||||||||||||||||||||||||||||||||||||||||||||||||||||||
Total Amount Contractor Payments(a) + (b) + (c) |
[**] | [**] | [**] | [**] | [**] | [**] | [**] | [**] | [**] | [**] | [**] | [**] | [**] | [**] | [**] | [**] | [**] | [**] | [**] | [**] | [**] | [**] |
Notes: | ||
1) | Performance Period Expenses shall include only direct costs. | |
2) | Contractor shall specify escalation rate applied to performance period expenses or other sources, in accordance with the IDIQ contract. | |
3) | If applicable, contractor shall specify escalation rate applied to performance period expenses: Applicable escalation is [**]%, with the exception of Biomass which is [**]% | |
4) | Year 0 savings will be applied to Performance Period Expenses for ECM-2 and the PPEF deposit shown in Year 0 above. | |
5) | The PPEF amount represents the aggreagate of the following amounts to financed and deposited into the PPEF: |
a) Sales tax reserve (see Section 6.3 of the Final Proposal) |
$ | 4,613,228 | ||
b) PPEF Funding Amount upon Acceptance |
$ | 4,586,772 | ||
PPEF Deposit from financing proceeds |
$ | 9,200,000 | ||
Contractor: Ameresco Federal Solutions | Project Square Footage (KSF): | |||||||||||||||||||||||||||||||||||||||||||||||||||||||||||||||||||||||
Delivery Order No.: DE-AT09-09SR22572 dated 15-May-2009 | (f) | (g) | (h) | (k) | N/A | |||||||||||||||||||||||||||||||||||||||||||||||||||||||||||||||||||
Project Site: | (a) | (b)(1) | (b)(2) | (c)(1) | (c)(2) | (d)(1) | (d)(2) | (e)(1) | (e)(2) | b1+d1+e1 | b2+c2+d2+e2 | Other Energy- | g+h+j | (m) | ||||||||||||||||||||||||||||||||||||||||||||||||||||||||||
C.2.2 | Project or | Electric | Electric | Electric | Electric | Fuel | Fuel | Oher | Other | Total | Total | Related and | (i) | (j) | Estimated | (l) | m=l/k | |||||||||||||||||||||||||||||||||||||||||||||||||||||||
Tech | Savannah River Site | ECM Energy | Energy | Energy | Demand | Demand | Oil | Oil | Energy | Energy | Energy | Energy | O&M | Water | Water | Annual | Implementation | Simple | ||||||||||||||||||||||||||||||||||||||||||||||||||||||
Category | ECM | Baseline | Savings | Savings | Savings | Savings | Savings | Savings | Savings | Savings | Savings | Cost Savings | Cost Savings | Savings | Savings | Cost Savings | Price | Payback | ||||||||||||||||||||||||||||||||||||||||||||||||||||||
Letter | No. | Description | (MBTU/yr) | (kWh/yr) | ($/yr) | (kW/yr) | ($/yr) | (Mbtu/yr) | ($/yr) | (Mbtu/yr) | ($/yr) | (Mbtu/yr) | ($/yr) | ($/yr) | (k-gal/yr) | ($/yr) | ($/yr) | $ | (yrs) | |||||||||||||||||||||||||||||||||||||||||||||||||||||
q |
DES/Proposal Development Costs | $ | | | $ | | | $ | | | $ | | | $ | | $ | | | | $ | | $ | 1,164,800 | N/A | ||||||||||||||||||||||||||||||||||||||||||||||||
r |
1 | D Area Biomass Replacement Plant | 3,978,008 | (55,415,523 | ) | $ | (3,941,118 | ) | | $ | | | $ | | 3,978,008 | $ | 24,994,446 | 3,788,874 | $ | 21,053,328 | $ | 12,482,882 | (460,671 | ) | (355,013 | ) | $ | 33,181,197 | $ | 137,500,762 | 4.14 | |||||||||||||||||||||||||||||||||||||||||
r |
2 | K&L Area Biomass Replacement Plant | 42,884 | (345,600 | ) | $ | (35,355 | ) | | $ | | 42,884 | $ | 593,563 | | $ | | 41,704 | $ | 558,208 | $ | 638,970 | (4,007 | ) | (25,917 | ) | $ | 1,171,260 | $ | 10,507,004 | 8.97 | |||||||||||||||||||||||||||||||||||||||||
| ||||||||||||||||||||||||||||||||||||||||||||||||||||||||||||||||||||||||
TOTAL |
(55,761,123 | ) | $ | (3,976,474 | ) | | $ | | 42,884 | $ | 593,563 | 3,978,008 | $ | 24,994,446 | 3,830,579 | $ | 21,611,535 | $ | 13,121,852 | (464,678 | ) | $ | (380,930 | ) | $ | 34,352,457 | $ | 149,172,566 | 4.34 | |||||||||||||||||||||||||||||||||||||||||||
Notes: | ||
1) | Project Square Footage (in 1000 SF) Include only building square footage affected by installed ECMs in project. | |
2) | For column (a) insert estimated energy baseline by ECM and total project in MBTU based on M&V approach in technical proposal and DES. | |
3) | Energy conversion factors for MBTU: MBTU=10^6 BTU; Electricity 3413 BTU/kWh; Natural Gas 1031 BTU/100CF; Coal 12,290 BTU/lb; #2 Oil 138,700 BTU/gal. | |
4) | Other energy savings in (e)(1) and (e)(2) represent coal savings. |
Project Site: | Delivery Order No.: | Contractor Name: | ||||||
Savannah River Site | DE-AT09-09SR22572 dated 15-May-2009 | Ameresco Federal Solutions | ||||||
Outstanding Capital | Total Cancellation | |||||||
Investment | Ceiling | |||||||
$ | $ | |||||||
Installation Acceptance |
$ | 183,375,883 | $ | 192,544,677 | ||||
End of Year One |
$ | 173,872,203 | $ | 182,565,813 | ||||
End of Year Two |
$ | 169,186,687 | $ | 177,646,021 | ||||
End of Year Three |
$ | 163,908,479 | $ | 172,103,903 | ||||
End of Year Four |
$ | 157,863,143 | $ | 165,756,300 | ||||
End of Year Five |
$ | 150,837,374 | $ | 158,379,243 | ||||
End of Year Six |
$ | 142,344,922 | $ | 149,462,168 | ||||
End of Year Seven |
$ | 132,506,118 | $ | 139,131,424 | ||||
End of Year Eight |
$ | 121,479,677 | $ | 127,553,661 | ||||
End of Year Nine |
$ | 108,734,351 | $ | 114,171,068 | ||||
End of Year Ten |
$ | 92,487,417 | $ | 97,111,788 | ||||
End of Year Eleven |
$ | 74,132,095 | $ | 77,838,700 | ||||
End of Year Twelve |
$ | 53,511,954 | $ | 56,187,552 | ||||
End of Year Thirteen |
$ | 30,483,995 | $ | 32,008,195 | ||||
End of Year Fourteen |
$ | 4,662,037 | $ | 4,895,139 | ||||
End of Year Fifteen |
$ | | $ | | ||||
End of Year Sixteen |
$ | | $ | | ||||
End of Year Seventeen |
$ | | $ | | ||||
End of Year Eighteen |
$ | | $ | | ||||
End of Year Nineteen |
$ | | $ | | ||||
End of Year Twenty |
$ | | $ | | ||||
End of Year Twenty-one |
$ | | $ | | ||||
End of Year Twenty-two |
$ | | $ | | ||||
End of Year Twenty-three |
$ | | $ | | ||||
End of Year Twenty-four |
$ | | $ | | ||||
End of Year Twenty-five |
$ | | $ | |
(1) | Outstanding Capital Investment Remaining Unamortized principal on Total Amount Financed. | |
(2) | In the event of contract cancellation or termination for convenience the Termination Liability amount set forth on the Termination Liability Schedule will apply for amounts due Contractors lender as set forth in Section 6.7 of Contractors Proposal. | |
(3) | The Contractor has attached a monthly Financing Termination Liability Schedule which must correspond to the annual amounts submitted above in each year for Outstanding Capital Investment. |
Termination Premium |
5.0 | % | ||
Service Period Payments |
467,331,605 | |||
PPEF Deposit ECMs Savings During Construction |
300,000 | |||
Interest Payments |
144,023,365 | |||
Principal Payments |
183,375,883 | |||
Total Payment |
795,030,853 |
Project Site: Savannah River Site | Delivery Order No.: DE-AT09-09SR22572 dated 15-May-2009 | Contractor Name: Ameresco Federal Solutions | ||||||||||||||||||||||||||||||||||||
Beginning of | Payment Due | Lenders Termination | ||||||||||||||||||||||||||||||||||||
Month | Date | Government Payment | Service Period Expenses | PPEF Deposit | Debt Service Payment | Interest | Principal | Outstanding Principal Balance | Premium | Termination Liability | ||||||||||||||||||||||||||||
0 |
06/01/09 | | | | | | | 183,375,883 | 9,168,794 | 192,544,677 | ||||||||||||||||||||||||||||
1 |
07/01/09 | | | | | | | 183,375,883 | 9,168,794 | 192,544,677 | ||||||||||||||||||||||||||||
2 |
08/01/09 | | | | | | | 183,375,883 | 9,168,794 | 192,544,677 | ||||||||||||||||||||||||||||
3 |
09/01/09 | | | | | | | 183,375,883 | 9,168,794 | 192,544,677 | ||||||||||||||||||||||||||||
4 |
10/01/09 | | | | | | | 183,375,883 | 9,168,794 | 192,544,677 | ||||||||||||||||||||||||||||
5 |
11/01/09 | | | | | | | 183,375,883 | 9,168,794 | 192,544,677 | ||||||||||||||||||||||||||||
6 |
12/01/09 | | | | | | | 183,375,883 | 9,168,794 | 192,544,677 | ||||||||||||||||||||||||||||
7 |
01/01/10 | | | | | | | 183,375,883 | 9,168,794 | 192,544,677 | ||||||||||||||||||||||||||||
8 |
02/01/10 | | | | | | | 183,375,883 | 9,168,794 | 192,544,677 | ||||||||||||||||||||||||||||
9 |
03/01/10 | | | | | | | 183,375,883 | 9,168,794 | 192,544,677 | ||||||||||||||||||||||||||||
10 |
04/01/10 | | | | | | | 183,375,883 | 9,168,794 | 192,544,677 | ||||||||||||||||||||||||||||
11 |
05/01/10 | | | | | | | 183,375,883 | 9,168,794 | 192,544,677 | ||||||||||||||||||||||||||||
12 |
06/01/10 | | | | | | | 183,375,883 | 9,168,794 | 192,544,677 | ||||||||||||||||||||||||||||
13 |
07/01/10 | | | | | | | 183,375,883 | 9,168,794 | 192,544,677 | ||||||||||||||||||||||||||||
14 |
08/01/10 | | | | | | | 183,375,883 | 9,168,794 | 192,544,677 | ||||||||||||||||||||||||||||
15 |
09/01/10 | | | | | | | 183,375,883 | 9,168,794 | 192,544,677 | ||||||||||||||||||||||||||||
16 |
10/01/10 | | | | | | | 183,375,883 | 9,168,794 | 192,544,677 | ||||||||||||||||||||||||||||
17 |
11/01/10 | | | | | | | 183,375,883 | 9,168,794 | 192,544,677 | ||||||||||||||||||||||||||||
18 |
12/01/10 | | | | | | | 183,375,883 | 9,168,794 | 192,544,677 | ||||||||||||||||||||||||||||
19 |
01/01/11 | | | | | | | 183,375,883 | 9,168,794 | 192,544,677 | ||||||||||||||||||||||||||||
20 |
02/01/11 | 141,914 | 91,914 | 50,000 | | | | 183,375,883 | 9,168,794 | 192,544,677 | ||||||||||||||||||||||||||||
21 |
03/01/11 | 70,957 | 45,957 | 25,000 | | | | 183,375,883 | 9,168,794 | 192,544,677 | ||||||||||||||||||||||||||||
22 |
04/01/11 | 70,957 | 45,957 | 25,000 | | | | 183,375,883 | 9,168,794 | 192,544,677 | ||||||||||||||||||||||||||||
23 |
05/01/11 | 70,957 | 45,957 | 25,000 | | | | 183,375,883 | 9,168,794 | 192,544,677 | ||||||||||||||||||||||||||||
24 |
06/01/11 | 70,957 | 45,957 | 25,000 | | | | 183,375,883 | 9,168,794 | 192,544,677 | ||||||||||||||||||||||||||||
25 |
07/01/11 | 70,957 | 45,957 | 25,000 | | | | 183,375,883 | 9,168,794 | 192,544,677 | ||||||||||||||||||||||||||||
26 |
08/01/11 | 70,957 | 45,957 | 25,000 | | | | 183,375,883 | 9,168,794 | 192,544,677 | ||||||||||||||||||||||||||||
27 |
09/01/11 | 70,957 | 45,957 | 25,000 | | | | 183,375,883 | 9,168,794 | 192,544,677 | ||||||||||||||||||||||||||||
28 |
10/01/11 | 70,957 | 45,957 | 25,000 | | | | 183,375,883 | 9,168,794 | 192,544,677 | ||||||||||||||||||||||||||||
29 |
11/01/11 | 70,957 | 45,957 | 25,000 | | | | 183,375,883 | 9,168,794 | 192,544,677 | ||||||||||||||||||||||||||||
30 |
12/01/11 | 70,957 | 45,957 | 25,000 | | | | 183,375,883 | 9,168,794 | 192,544,677 | ||||||||||||||||||||||||||||
31 |
01/01/12 | | | | | | | 183,375,883 | 9,168,794 | 192,544,677 | ||||||||||||||||||||||||||||
32 |
02/01/12 | | | | | | | 183,375,883 | 9,168,794 | 192,544,677 | ||||||||||||||||||||||||||||
33 |
03/01/12 | | | | | | | 183,375,883 | 9,168,794 | 192,544,677 | ||||||||||||||||||||||||||||
34 |
04/01/12 | | | | | | | 183,375,883 | 9,168,794 | 192,544,677 | ||||||||||||||||||||||||||||
35 |
05/01/12 | 31,167,469 | 6,652,639 | | 24,514,830 | 15,011,150 | 9,503,680 | 173,872,203 | 8,693,610 | 182,565,813 | ||||||||||||||||||||||||||||
36 |
06/01/12 | 1,330,528 | 1,330,528 | | | | | 173,872,203 | 8,693,610 | 182,565,813 | ||||||||||||||||||||||||||||
37 |
07/01/12 | 1,330,528 | 1,330,528 | | | | | 173,872,203 | 8,693,610 | 182,565,813 | ||||||||||||||||||||||||||||
38 |
08/01/12 | 1,330,528 | 1,330,528 | | | | | 173,872,203 | 8,693,610 | 182,565,813 | ||||||||||||||||||||||||||||
39 |
09/01/12 | 1,330,528 | 1,330,528 | | | | | 173,872,203 | 8,693,610 | 182,565,813 | ||||||||||||||||||||||||||||
40 |
10/01/12 | 1,330,528 | 1,330,528 | | | | | 173,872,203 | 8,693,610 | 182,565,813 | ||||||||||||||||||||||||||||
41 |
11/01/12 | 1,330,528 | 1,330,528 | | | | | 173,872,203 | 8,693,610 | 182,565,813 | ||||||||||||||||||||||||||||
42 |
12/01/12 | 1,330,528 | 1,330,528 | | | | | 173,872,203 | 8,693,610 | 182,565,813 | ||||||||||||||||||||||||||||
43 |
01/01/13 | 1,330,528 | 1,330,528 | | | | | 173,872,203 | 8,693,610 | 182,565,813 | ||||||||||||||||||||||||||||
44 |
02/01/13 | 1,330,528 | 1,330,528 | | | | | 173,872,203 | 8,693,610 | 182,565,813 | ||||||||||||||||||||||||||||
45 |
03/01/13 | 1,330,528 | 1,330,528 | | | | | 173,872,203 | 8,693,610 | 182,565,813 | ||||||||||||||||||||||||||||
46 |
04/01/13 | 1,330,528 | 1,330,528 | | | | | 173,872,203 | 8,693,610 | 182,565,813 | ||||||||||||||||||||||||||||
47 |
05/01/13 | 20,307,715 | 1,389,020 | | 18,918,695 | 14,233,179 | 4,685,516 | 169,186,687 | 8,459,334 | 177,646,021 | ||||||||||||||||||||||||||||
48 |
06/01/13 | 1,389,020 | 1,389,020 | | | | | 169,186,687 | 8,459,334 | 177,646,021 | ||||||||||||||||||||||||||||
49 |
07/01/13 | 1,389,020 | 1,389,020 | | | | | 169,186,687 | 8,459,334 | 177,646,021 | ||||||||||||||||||||||||||||
50 |
08/01/13 | 1,389,020 | 1,389,020 | | | | | 169,186,687 | 8,459,334 | 177,646,021 | ||||||||||||||||||||||||||||
51 |
09/01/13 | 1,389,020 | 1,389,020 | | | | | 169,186,687 | 8,459,334 | 177,646,021 | ||||||||||||||||||||||||||||
52 |
10/01/13 | 1,389,020 | 1,389,020 | | | | | 169,186,687 | 8,459,334 | 177,646,021 | ||||||||||||||||||||||||||||
53 |
11/01/13 | 1,389,020 | 1,389,020 | | | | | 169,186,687 | 8,459,334 | 177,646,021 | ||||||||||||||||||||||||||||
54 |
12/01/13 | 1,389,020 | 1,389,020 | | | | | 169,186,687 | 8,459,334 | 177,646,021 | ||||||||||||||||||||||||||||
55 |
01/01/14 | 1,389,020 | 1,389,020 | | | | | 169,186,687 | 8,459,334 | 177,646,021 | ||||||||||||||||||||||||||||
56 |
02/01/14 | 1,389,020 | 1,389,020 | | | | | 169,186,687 | 8,459,334 | 177,646,021 | ||||||||||||||||||||||||||||
57 |
03/01/14 | 1,389,020 | 1,389,020 | | | | | 169,186,687 | 8,459,334 | 177,646,021 | ||||||||||||||||||||||||||||
58 |
04/01/14 | 1,389,020 | 1,389,020 | | | | | 169,186,687 | 8,459,334 | 177,646,021 | ||||||||||||||||||||||||||||
59 |
05/01/14 | 20,578,026 | 1,450,196 | | 19,127,830 | 13,849,622 | 5,278,208 | 163,908,479 | 8,195,424 | 172,103,903 | ||||||||||||||||||||||||||||
60 |
06/01/14 | 1,450,196 | 1,450,196 | | | | | 163,908,479 | 8,195,424 | 172,103,903 | ||||||||||||||||||||||||||||
61 |
07/01/14 | 1,450,196 | 1,450,196 | | | | | 163,908,479 | 8,195,424 | 172,103,903 | ||||||||||||||||||||||||||||
62 |
08/01/14 | 1,450,196 | 1,450,196 | | | | | 163,908,479 | 8,195,424 | 172,103,903 | ||||||||||||||||||||||||||||
63 |
09/01/14 | 1,450,196 | 1,450,196 | | | | | 163,908,479 | 8,195,424 | 172,103,903 | ||||||||||||||||||||||||||||
64 |
10/01/14 | 1,450,196 | 1,450,196 | | | | | 163,908,479 | 8,195,424 | 172,103,903 | ||||||||||||||||||||||||||||
65 |
11/01/14 | 1,450,196 | 1,450,196 | | | | | 163,908,479 | 8,195,424 | 172,103,903 | ||||||||||||||||||||||||||||
66 |
12/01/14 | 1,450,196 | 1,450,196 | | | | | 163,908,479 | 8,195,424 | 172,103,903 | ||||||||||||||||||||||||||||
67 |
01/01/15 | 1,450,196 | 1,450,196 | | | | | 163,908,479 | 8,195,424 | 172,103,903 | ||||||||||||||||||||||||||||
68 |
02/01/15 | 1,450,196 | 1,450,196 | | | | | 163,908,479 | 8,195,424 | 172,103,903 | ||||||||||||||||||||||||||||
69 |
03/01/15 | 1,450,196 | 1,450,196 | | | | | 163,908,479 | 8,195,424 | 172,103,903 | ||||||||||||||||||||||||||||
70 |
04/01/15 | 1,450,196 | 1,450,196 | | | | | 163,908,479 | 8,195,424 | 172,103,903 | ||||||||||||||||||||||||||||
71 |
05/01/15 | 20,977,066 | 1,514,182 | | 19,462,884 | 13,417,548 | 6,045,336 | 157,863,143 | 7,893,157 | 165,756,300 | ||||||||||||||||||||||||||||
72 |
06/01/15 | 1,514,182 | 1,514,182 | | | | | 157,863,143 | 7,893,157 | 165,756,300 | ||||||||||||||||||||||||||||
73 |
07/01/15 | 1,514,182 | 1,514,182 | | | | | 157,863,143 | 7,893,157 | 165,756,300 | ||||||||||||||||||||||||||||
74 |
08/01/15 | 1,514,182 | 1,514,182 | | | | | 157,863,143 | 7,893,157 | 165,756,300 | ||||||||||||||||||||||||||||
75 |
09/01/15 | 1,514,182 | 1,514,182 | | | | | 157,863,143 | 7,893,157 | 165,756,300 | ||||||||||||||||||||||||||||
76 |
10/01/15 | 1,514,182 | 1,514,182 | | | | | 157,863,143 | 7,893,157 | 165,756,300 | ||||||||||||||||||||||||||||
77 |
11/01/15 | 1,514,182 | 1,514,182 | | | | | 157,863,143 | 7,893,157 | 165,756,300 | ||||||||||||||||||||||||||||
78 |
12/01/15 | 1,514,182 | 1,514,182 | | | | | 157,863,143 | 7,893,157 | 165,756,300 | ||||||||||||||||||||||||||||
79 |
01/01/16 | 1,514,182 | 1,514,182 | | | | | 157,863,143 | 7,893,157 | 165,756,300 | ||||||||||||||||||||||||||||
80 |
02/01/16 | 1,514,182 | 1,514,182 | | | | | 157,863,143 | 7,893,157 | 165,756,300 | ||||||||||||||||||||||||||||
81 |
03/01/16 | 1,514,182 | 1,514,182 | | | | | 157,863,143 | 7,893,157 | 165,756,300 | ||||||||||||||||||||||||||||
82 |
04/01/16 | 1,514,182 | 1,514,182 | | | | | 157,863,143 | 7,893,157 | 165,756,300 |
Termination Premium |
5.0 | % | ||
Service Period Payments |
467,331,605 | |||
PPEF Deposit ECMs Savings During Construction |
300,000 | |||
Interest Payments |
144,023,365 | |||
Principal Payments |
183,375,883 | |||
Total Payment |
795,030,853 |
Project Site: Savannah River Site | Delivery Order No.: DE-AT09-09SR22572 dated 15-May-2009 | Contractor Name: Ameresco Federal Solutions | ||||||||||||||||||||||||||||||||||||
Beginning of | Payment Due | Lenders Termination | ||||||||||||||||||||||||||||||||||||
Month | Date | Government Payment | Service Period Expenses | PPEF Deposit | Debt Service Payment | Interest | Principal | Outstanding Principal Balance | Premium | Termination Liability | ||||||||||||||||||||||||||||
83 |
05/01/16 | 21,529,558 | 1,581,111 | | 19,948,446 | 12,922,677 | 7,025,769 | 150,837,374 | 7,541,869 | 158,379,243 | ||||||||||||||||||||||||||||
84 |
06/01/16 | 1,581,111 | 1,581,111 | | | | | 150,837,374 | 7,541,869 | 158,379,243 | ||||||||||||||||||||||||||||
85 |
07/01/16 | 1,581,111 | 1,581,111 | | | | | 150,837,374 | 7,541,869 | 158,379,243 | ||||||||||||||||||||||||||||
86 |
08/01/16 | 1,581,111 | 1,581,111 | | | | | 150,837,374 | 7,541,869 | 158,379,243 | ||||||||||||||||||||||||||||
87 |
09/01/16 | 1,581,111 | 1,581,111 | | | | | 150,837,374 | 7,541,869 | 158,379,243 | ||||||||||||||||||||||||||||
88 |
10/01/16 | 1,581,111 | 1,581,111 | | | | | 150,837,374 | 7,541,869 | 158,379,243 | ||||||||||||||||||||||||||||
89 |
11/01/16 | 1,581,111 | 1,581,111 | | | | | 150,837,374 | 7,541,869 | 158,379,243 | ||||||||||||||||||||||||||||
90 |
12/01/16 | 1,581,111 | 1,581,111 | | | | | 150,837,374 | 7,541,869 | 158,379,243 | ||||||||||||||||||||||||||||
91 |
01/01/17 | 1,581,111 | 1,581,111 | | | | | 150,837,374 | 7,541,869 | 158,379,243 | ||||||||||||||||||||||||||||
92 |
02/01/17 | 1,581,111 | 1,581,111 | | | | | 150,837,374 | 7,541,869 | 158,379,243 | ||||||||||||||||||||||||||||
93 |
03/01/17 | 1,581,111 | 1,581,111 | | | | | 150,837,374 | 7,541,869 | 158,379,243 | ||||||||||||||||||||||||||||
94 |
04/01/17 | 1,581,111 | 1,581,111 | | | | | 150,837,374 | 7,541,869 | 158,379,243 | ||||||||||||||||||||||||||||
95 |
05/01/17 | 22,491,123 | 1,651,124 | | 20,839,999 | 12,347,547 | 8,492,452 | 142,344,922 | 7,117,246 | 149,462,168 | ||||||||||||||||||||||||||||
96 |
06/01/17 | 1,651,124 | 1,651,124 | | | | | 142,344,922 | 7,117,246 | 149,462,168 | ||||||||||||||||||||||||||||
97 |
07/01/17 | 1,651,124 | 1,651,124 | | | | | 142,344,922 | 7,117,246 | 149,462,168 | ||||||||||||||||||||||||||||
98 |
08/01/17 | 1,651,124 | 1,651,124 | | | | | 142,344,922 | 7,117,246 | 149,462,168 | ||||||||||||||||||||||||||||
99 |
09/01/17 | 1,651,124 | 1,651,124 | | | | | 142,344,922 | 7,117,246 | 149,462,168 | ||||||||||||||||||||||||||||
100 |
10/01/17 | 1,651,124 | 1,651,124 | | | | | 142,344,922 | 7,117,246 | 149,462,168 | ||||||||||||||||||||||||||||
101 |
11/01/17 | 1,651,124 | 1,651,124 | | | | | 142,344,922 | 7,117,246 | 149,462,168 | ||||||||||||||||||||||||||||
102 |
12/01/17 | 1,651,124 | 1,651,124 | | | | | 142,344,922 | 7,117,246 | 149,462,168 | ||||||||||||||||||||||||||||
103 |
01/01/18 | 1,651,124 | 1,651,124 | | | | | 142,344,922 | 7,117,246 | 149,462,168 | ||||||||||||||||||||||||||||
104 |
02/01/18 | 1,651,124 | 1,651,124 | | | | | 142,344,922 | 7,117,246 | 149,462,168 | ||||||||||||||||||||||||||||
105 |
03/01/18 | 1,651,124 | 1,651,124 | | | | | 142,344,922 | 7,117,246 | 149,462,168 | ||||||||||||||||||||||||||||
106 |
04/01/18 | 1,651,124 | 1,651,124 | | | | | 142,344,922 | 7,117,246 | 149,462,168 | ||||||||||||||||||||||||||||
107 |
05/01/18 | 23,215,526 | 1,724,367 | | 21,491,160 | 11,652,355 | 9,838,805 | 132,506,118 | 6,625,306 | 139,131,424 | ||||||||||||||||||||||||||||
108 |
06/01/18 | 1,724,367 | 1,724,367 | | | | | 132,506,118 | 6,625,306 | 139,131,424 | ||||||||||||||||||||||||||||
109 |
07/01/18 | 1,724,367 | 1,724,367 | | | | | 132,506,118 | 6,625,306 | 139,131,424 | ||||||||||||||||||||||||||||
110 |
08/01/18 | 1,724,367 | 1,724,367 | | | | | 132,506,118 | 6,625,306 | 139,131,424 | ||||||||||||||||||||||||||||
111 |
09/01/18 | 1,724,367 | 1,724,367 | | | | | 132,506,118 | 6,625,306 | 139,131,424 | ||||||||||||||||||||||||||||
112 |
10/01/18 | 1,724,367 | 1,724,367 | | | | | 132,506,118 | 6,625,306 | 139,131,424 | ||||||||||||||||||||||||||||
113 |
11/01/18 | 1,724,367 | 1,724,367 | | | | | 132,506,118 | 6,625,306 | 139,131,424 | ||||||||||||||||||||||||||||
114 |
12/01/18 | 1,724,367 | 1,724,367 | | | | | 132,506,118 | 6,625,306 | 139,131,424 | ||||||||||||||||||||||||||||
115 |
01/01/19 | 1,724,367 | 1,724,367 | | | | | 132,506,118 | 6,625,306 | 139,131,424 | ||||||||||||||||||||||||||||
116 |
02/01/19 | 1,724,367 | 1,724,367 | | | | | 132,506,118 | 6,625,306 | 139,131,424 | ||||||||||||||||||||||||||||
117 |
03/01/19 | 1,724,367 | 1,724,367 | | | | | 132,506,118 | 6,625,306 | 139,131,424 | ||||||||||||||||||||||||||||
118 |
04/01/19 | 1,724,367 | 1,724,367 | | | | | 132,506,118 | 6,625,306 | 139,131,424 | ||||||||||||||||||||||||||||
119 |
05/01/19 | 23,674,383 | 1,800,991 | | 21,873,391 | 10,846,951 | 11,026,440 | 121,479,677 | 6,073,984 | 127,553,661 | ||||||||||||||||||||||||||||
120 |
06/01/19 | 1,800,991 | 1,800,991 | | | | | 121,479,677 | 6,073,984 | 127,553,661 | ||||||||||||||||||||||||||||
121 |
07/01/19 | 1,800,991 | 1,800,991 | | | | | 121,479,677 | 6,073,984 | 127,553,661 | ||||||||||||||||||||||||||||
122 |
08/01/19 | 1,800,991 | 1,800,991 | | | | | 121,479,677 | 6,073,984 | 127,553,661 | ||||||||||||||||||||||||||||
123 |
09/01/19 | 1,800,991 | 1,800,991 | | | | | 121,479,677 | 6,073,984 | 127,553,661 | ||||||||||||||||||||||||||||
124 |
10/01/19 | 1,800,991 | 1,800,991 | | | | | 121,479,677 | 6,073,984 | 127,553,661 | ||||||||||||||||||||||||||||
125 |
11/01/19 | 1,800,991 | 1,800,991 | | | | | 121,479,677 | 6,073,984 | 127,553,661 | ||||||||||||||||||||||||||||
126 |
12/01/19 | 1,800,991 | 1,800,991 | | | | | 121,479,677 | 6,073,984 | 127,553,661 | ||||||||||||||||||||||||||||
127 |
01/01/20 | 1,800,991 | 1,800,991 | | | | | 121,479,677 | 6,073,984 | 127,553,661 | ||||||||||||||||||||||||||||
128 |
02/01/20 | 1,800,991 | 1,800,991 | | | | | 121,479,677 | 6,073,984 | 127,553,661 | ||||||||||||||||||||||||||||
129 |
03/01/20 | 1,800,991 | 1,800,991 | | | | | 121,479,677 | 6,073,984 | 127,553,661 | ||||||||||||||||||||||||||||
130 |
04/01/20 | 1,800,991 | 1,800,991 | | | | | 121,479,677 | 6,073,984 | 127,553,661 | ||||||||||||||||||||||||||||
131 |
05/01/20 | 24,570,813 | 1,881,160 | | 22,689,653 | 9,944,326 | 12,745,326 | 108,734,351 | 5,436,718 | 114,171,068 | ||||||||||||||||||||||||||||
132 |
06/01/20 | 1,881,160 | 1,881,160 | | | | | 108,734,351 | 5,436,718 | 114,171,068 | ||||||||||||||||||||||||||||
133 |
07/01/20 | 1,881,160 | 1,881,160 | | | | | 108,734,351 | 5,436,718 | 114,171,068 | ||||||||||||||||||||||||||||
134 |
08/01/20 | 1,881,160 | 1,881,160 | | | | | 108,734,351 | 5,436,718 | 114,171,068 | ||||||||||||||||||||||||||||
135 |
09/01/20 | 1,881,160 | 1,881,160 | | | | | 108,734,351 | 5,436,718 | 114,171,068 | ||||||||||||||||||||||||||||
136 |
10/01/20 | 1,881,160 | 1,881,160 | | | | | 108,734,351 | 5,436,718 | 114,171,068 | ||||||||||||||||||||||||||||
137 |
11/01/20 | 1,881,160 | 1,881,160 | | | | | 108,734,351 | 5,436,718 | 114,171,068 | ||||||||||||||||||||||||||||
138 |
12/01/20 | 1,881,160 | 1,881,160 | | | | | 108,734,351 | 5,436,718 | 114,171,068 | ||||||||||||||||||||||||||||
139 |
01/01/21 | 1,881,160 | 1,881,160 | | | | | 108,734,351 | 5,436,718 | 114,171,068 | ||||||||||||||||||||||||||||
140 |
02/01/21 | 1,881,160 | 1,881,160 | | | | | 108,734,351 | 5,436,718 | 114,171,068 | ||||||||||||||||||||||||||||
141 |
03/01/21 | 1,881,160 | 1,881,160 | | | | | 108,734,351 | 5,436,718 | 114,171,068 | ||||||||||||||||||||||||||||
142 |
04/01/21 | 1,881,160 | 1,881,160 | | | | | 108,734,351 | 5,436,718 | 114,171,068 | ||||||||||||||||||||||||||||
143 |
05/01/21 | 27,112,968 | 1,965,040 | | 25,147,928 | 8,900,994 | 16,246,934 | 92,487,417 | 4,624,371 | 97,111,788 | ||||||||||||||||||||||||||||
144 |
06/01/21 | 1,965,040 | 1,965,040 | | | | | 92,487,417 | 4,624,371 | 97,111,788 | ||||||||||||||||||||||||||||
145 |
07/01/21 | 1,965,040 | 1,965,040 | | | | | 92,487,417 | 4,624,371 | 97,111,788 | ||||||||||||||||||||||||||||
146 |
08/01/21 | 1,965,040 | 1,965,040 | | | | | 92,487,417 | 4,624,371 | 97,111,788 | ||||||||||||||||||||||||||||
147 |
09/01/21 | 1,965,040 | 1,965,040 | | | | | 92,487,417 | 4,624,371 | 97,111,788 | ||||||||||||||||||||||||||||
148 |
10/01/21 | 1,965,040 | 1,965,040 | | | | | 92,487,417 | 4,624,371 | 97,111,788 | ||||||||||||||||||||||||||||
149 |
11/01/21 | 1,965,040 | 1,965,040 | | | | | 92,487,417 | 4,624,371 | 97,111,788 | ||||||||||||||||||||||||||||
150 |
12/01/21 | 1,965,040 | 1,965,040 | | | | | 92,487,417 | 4,624,371 | 97,111,788 | ||||||||||||||||||||||||||||
151 |
01/01/22 | 1,965,040 | 1,965,040 | | | | | 92,487,417 | 4,624,371 | 97,111,788 | ||||||||||||||||||||||||||||
152 |
02/01/22 | 1,965,040 | 1,965,040 | | | | | 92,487,417 | 4,624,371 | 97,111,788 | ||||||||||||||||||||||||||||
153 |
03/01/22 | 1,965,040 | 1,965,040 | | | | | 92,487,417 | 4,624,371 | 97,111,788 | ||||||||||||||||||||||||||||
154 |
04/01/22 | 1,965,040 | 1,965,040 | | | | | 92,487,417 | 4,624,371 | 97,111,788 | ||||||||||||||||||||||||||||
155 |
05/01/22 | 27,979,151 | 2,052,809 | | 25,926,342 | 7,571,020 | 18,355,322 | 74,132,095 | 3,706,605 | 77,838,700 | ||||||||||||||||||||||||||||
156 |
06/01/22 | 2,052,809 | 2,052,809 | | | | | 74,132,095 | 3,706,605 | 77,838,700 | ||||||||||||||||||||||||||||
157 |
07/01/22 | 2,052,809 | 2,052,809 | | | | | 74,132,095 | 3,706,605 | 77,838,700 | ||||||||||||||||||||||||||||
158 |
08/01/22 | 2,052,809 | 2,052,809 | | | | | 74,132,095 | 3,706,605 | 77,838,700 | ||||||||||||||||||||||||||||
159 |
09/01/22 | 2,052,809 | 2,052,809 | | | | | 74,132,095 | 3,706,605 | 77,838,700 | ||||||||||||||||||||||||||||
160 |
10/01/22 | 2,052,809 | 2,052,809 | | | | | 74,132,095 | 3,706,605 | 77,838,700 | ||||||||||||||||||||||||||||
161 |
11/01/22 | 2,052,809 | 2,052,809 | | | | | 74,132,095 | 3,706,605 | 77,838,700 | ||||||||||||||||||||||||||||
162 |
12/01/22 | 2,052,809 | 2,052,809 | | | | | 74,132,095 | 3,706,605 | 77,838,700 | ||||||||||||||||||||||||||||
163 |
01/01/23 | 2,052,809 | 2,052,809 | | | | | 74,132,095 | 3,706,605 | 77,838,700 | ||||||||||||||||||||||||||||
164 |
02/01/23 | 2,052,809 | 2,052,809 | | | | | 74,132,095 | 3,706,605 | 77,838,700 | ||||||||||||||||||||||||||||
165 |
03/01/23 | 2,052,809 | 2,052,809 | | | | | 74,132,095 | 3,706,605 | 77,838,700 |
Termination Premium |
5.0 | % | ||
Service Period Payments |
467,331,605 | |||
PPEF Deposit ECMs Savings During Construction |
300,000 | |||
Interest Payments |
144,023,365 | |||
Principal Payments |
183,375,883 | |||
Total Payment |
795,030,853 |
Project Site: Savannah River Site | Delivery Order No.: DE-AT09-09SR22572 dated 15-May-2009 | Contractor Name: Ameresco Federal Solutions | ||||||||||||||||||||||||||||||||||||
Beginning of | Payment Due | Lenders Termination | ||||||||||||||||||||||||||||||||||||
Month | Date | Government Payment | Service Period Expenses | PPEF Deposit | Debt Service Payment | Interest | Principal | Outstanding Principal Balance | Premium | Termination Liability | ||||||||||||||||||||||||||||
166 |
04/01/23 | 2,052,809 | 2,052,809 | | | | | 74,132,095 | 3,706,605 | 77,838,700 | ||||||||||||||||||||||||||||
167 |
05/01/23 | 28,833,246 | 2,144,652 | | 26,688,594 | 6,068,453 | 20,620,141 | 53,511,954 | 2,675,598 | 56,187,552 | ||||||||||||||||||||||||||||
168 |
06/01/23 | 2,144,652 | 2,144,652 | | | | | 53,511,954 | 2,675,598 | 56,187,552 | ||||||||||||||||||||||||||||
169 |
07/01/23 | 2,144,652 | 2,144,652 | | | | | 53,511,954 | 2,675,598 | 56,187,552 | ||||||||||||||||||||||||||||
170 |
08/01/23 | 2,144,652 | 2,144,652 | | | | | 53,511,954 | 2,675,598 | 56,187,552 | ||||||||||||||||||||||||||||
171 |
09/01/23 | 2,144,652 | 2,144,652 | | | | | 53,511,954 | 2,675,598 | 56,187,552 | ||||||||||||||||||||||||||||
172 |
10/01/23 | 2,144,652 | 2,144,652 | | | | | 53,511,954 | 2,675,598 | 56,187,552 | ||||||||||||||||||||||||||||
173 |
11/01/23 | 2,144,652 | 2,144,652 | | | | | 53,511,954 | 2,675,598 | 56,187,552 | ||||||||||||||||||||||||||||
174 |
12/01/23 | 2,144,652 | 2,144,652 | | | | | 53,511,954 | 2,675,598 | 56,187,552 | ||||||||||||||||||||||||||||
175 |
01/01/24 | 2,144,652 | 2,144,652 | | | | | 53,511,954 | 2,675,598 | 56,187,552 | ||||||||||||||||||||||||||||
176 |
02/01/24 | 2,144,652 | 2,144,652 | | | | | 53,511,954 | 2,675,598 | 56,187,552 | ||||||||||||||||||||||||||||
177 |
03/01/24 | 2,144,652 | 2,144,652 | | | | | 53,511,954 | 2,675,598 | 56,187,552 | ||||||||||||||||||||||||||||
178 |
04/01/24 | 2,144,652 | 2,144,652 | | | | | 53,511,954 | 2,675,598 | 56,187,552 | ||||||||||||||||||||||||||||
179 |
05/01/24 | 29,649,211 | 2,240,763 | | 27,408,448 | 4,380,489 | 23,027,959 | 30,483,995 | 1,524,200 | 32,008,195 | ||||||||||||||||||||||||||||
180 |
06/01/24 | 2,240,763 | 2,240,763 | | | | | 30,483,995 | 1,524,200 | 32,008,195 | ||||||||||||||||||||||||||||
181 |
07/01/24 | 2,240,763 | 2,240,763 | | | | | 30,483,995 | 1,524,200 | 32,008,195 | ||||||||||||||||||||||||||||
182 |
08/01/24 | 2,240,763 | 2,240,763 | | | | | 30,483,995 | 1,524,200 | 32,008,195 | ||||||||||||||||||||||||||||
183 |
09/01/24 | 2,240,763 | 2,240,763 | | | | | 30,483,995 | 1,524,200 | 32,008,195 | ||||||||||||||||||||||||||||
184 |
10/01/24 | 2,240,763 | 2,240,763 | | | | | 30,483,995 | 1,524,200 | 32,008,195 | ||||||||||||||||||||||||||||
185 |
11/01/24 | 2,240,763 | 2,240,763 | | | | | 30,483,995 | 1,524,200 | 32,008,195 | ||||||||||||||||||||||||||||
186 |
12/01/24 | 2,240,763 | 2,240,763 | | | | | 30,483,995 | 1,524,200 | 32,008,195 | ||||||||||||||||||||||||||||
187 |
01/01/25 | 2,240,763 | 2,240,763 | | | | | 30,483,995 | 1,524,200 | 32,008,195 | ||||||||||||||||||||||||||||
188 |
02/01/25 | 2,240,763 | 2,240,763 | | | | | 30,483,995 | 1,524,200 | 32,008,195 | ||||||||||||||||||||||||||||
189 |
03/01/25 | 2,240,763 | 2,240,763 | | | | | 30,483,995 | 1,524,200 | 32,008,195 | ||||||||||||||||||||||||||||
190 |
04/01/25 | 2,240,763 | 2,240,763 | | | | | 30,483,995 | 1,524,200 | 32,008,195 | ||||||||||||||||||||||||||||
191 |
05/01/25 | 30,658,724 | 2,341,347 | | 28,317,378 | 2,495,420 | 25,821,958 | 4,662,037 | 233,102 | 4,895,139 | ||||||||||||||||||||||||||||
192 |
06/01/25 | 2,341,347 | 2,341,347 | | | | | 4,662,037 | 233,102 | 4,895,139 | ||||||||||||||||||||||||||||
193 |
07/01/25 | 2,341,347 | 2,341,347 | | | | | 4,662,037 | 233,102 | 4,895,139 | ||||||||||||||||||||||||||||
194 |
08/01/25 | 2,341,347 | 2,341,347 | | | | | 4,662,037 | 233,102 | 4,895,139 | ||||||||||||||||||||||||||||
195 |
09/01/25 | 2,341,347 | 2,341,347 | | | | | 4,662,037 | 233,102 | 4,895,139 | ||||||||||||||||||||||||||||
196 |
10/01/25 | 2,341,347 | 2,341,347 | | | | | 4,662,037 | 233,102 | 4,895,139 | ||||||||||||||||||||||||||||
197 |
11/01/25 | 2,341,347 | 2,341,347 | | | | | 4,662,037 | 233,102 | 4,895,139 | ||||||||||||||||||||||||||||
198 |
12/01/25 | 2,341,347 | 2,341,347 | | | | | 4,662,037 | 233,102 | 4,895,139 | ||||||||||||||||||||||||||||
199 |
01/01/26 | 2,341,347 | 2,341,347 | | | | | 4,662,037 | 233,102 | 4,895,139 | ||||||||||||||||||||||||||||
200 |
02/01/26 | 2,341,347 | 2,341,347 | | | | | 4,662,037 | 233,102 | 4,895,139 | ||||||||||||||||||||||||||||
201 |
03/01/26 | 2,341,347 | 2,341,347 | | | | | 4,662,037 | 233,102 | 4,895,139 | ||||||||||||||||||||||||||||
202 |
04/01/26 | 2,341,347 | 2,341,347 | | | | | 4,662,037 | 233,102 | 4,895,139 | ||||||||||||||||||||||||||||
203 |
05/01/26 | 7,490,287 | 2,446,615 | | 5,043,672 | 381,634 | 4,662,037 | | | | ||||||||||||||||||||||||||||
204 |
06/01/26 | 2,446,615 | 2,446,615 | | | | | | | | ||||||||||||||||||||||||||||
205 |
07/01/26 | 2,446,615 | 2,446,615 | | | | | | | | ||||||||||||||||||||||||||||
206 |
08/01/26 | 2,446,615 | 2,446,615 | | | | | | | | ||||||||||||||||||||||||||||
207 |
09/01/26 | 2,446,615 | 2,446,615 | | | | | | | | ||||||||||||||||||||||||||||
208 |
10/01/26 | 2,446,615 | 2,446,615 | | | | | | | | ||||||||||||||||||||||||||||
209 |
11/01/26 | 2,446,615 | 2,446,615 | | | | | | | | ||||||||||||||||||||||||||||
210 |
12/01/26 | 2,446,615 | 2,446,615 | | | | | | | | ||||||||||||||||||||||||||||
211 |
01/01/27 | 2,446,615 | 2,446,615 | | | | | | | | ||||||||||||||||||||||||||||
212 |
02/01/27 | 2,446,615 | 2,446,615 | | | | | | | | ||||||||||||||||||||||||||||
213 |
03/01/27 | 2,446,615 | 2,446,615 | | | | | | | | ||||||||||||||||||||||||||||
214 |
04/01/27 | 2,446,615 | 2,446,615 | | | | | | | | ||||||||||||||||||||||||||||
215 |
05/01/27 | 2,556,793 | 2,556,793 | | | | | | | | ||||||||||||||||||||||||||||
216 |
06/01/27 | 2,556,793 | 2,556,793 | | | | | | | | ||||||||||||||||||||||||||||
217 |
07/01/27 | 2,556,793 | 2,556,793 | | | | | | | | ||||||||||||||||||||||||||||
218 |
08/01/27 | 2,556,793 | 2,556,793 | | | | | | | | ||||||||||||||||||||||||||||
219 |
09/01/27 | 2,556,793 | 2,556,793 | | | | | | | | ||||||||||||||||||||||||||||
220 |
10/01/27 | 2,556,793 | 2,556,793 | | | | | | | | ||||||||||||||||||||||||||||
221 |
11/01/27 | 2,556,793 | 2,556,793 | | | | | | | | ||||||||||||||||||||||||||||
222 |
12/01/27 | 2,556,793 | 2,556,793 | | | | | | | | ||||||||||||||||||||||||||||
223 |
01/01/28 | 2,556,793 | 2,556,793 | | | | | | | | ||||||||||||||||||||||||||||
224 |
02/01/28 | 2,556,793 | 2,556,793 | | | | | | | | ||||||||||||||||||||||||||||
225 |
03/01/28 | 2,556,793 | 2,556,793 | | | | | | | | ||||||||||||||||||||||||||||
226 |
04/01/28 | 2,556,793 | 2,556,793 | | | | | | | | ||||||||||||||||||||||||||||
227 |
05/01/28 | 2,672,116 | 2,672,116 | | | | | | | | ||||||||||||||||||||||||||||
228 |
06/01/28 | 2,672,116 | 2,672,116 | | | | | | | | ||||||||||||||||||||||||||||
229 |
07/01/28 | 2,672,116 | 2,672,116 | | | | | | | | ||||||||||||||||||||||||||||
230 |
08/01/28 | 2,672,116 | 2,672,116 | | | | | | | | ||||||||||||||||||||||||||||
231 |
09/01/28 | 2,672,116 | 2,672,116 | | | | | | | | ||||||||||||||||||||||||||||
232 |
10/01/28 | 2,672,116 | 2,672,116 | | | | | | | | ||||||||||||||||||||||||||||
233 |
11/01/28 | 2,672,116 | 2,672,116 | | | | | | | | ||||||||||||||||||||||||||||
234 |
12/01/28 | 2,672,116 | 2,672,116 | | | | | | | | ||||||||||||||||||||||||||||
235 |
01/01/29 | 2,672,116 | 2,672,116 | | | | | | | | ||||||||||||||||||||||||||||
236 |
02/01/29 | 2,672,116 | 2,672,116 | | | | | | | | ||||||||||||||||||||||||||||
237 |
03/01/29 | 2,672,116 | 2,672,116 | | | | | | | | ||||||||||||||||||||||||||||
238 |
04/01/29 | 2,672,116 | 2,672,116 | | | | | | | | ||||||||||||||||||||||||||||
239 |
05/01/29 | 2,792,829 | 2,792,829 | | | | | | | | ||||||||||||||||||||||||||||
240 |
06/01/29 | 2,792,829 | 2,792,829 | | | | | | | | ||||||||||||||||||||||||||||
241 |
07/01/29 | 2,792,829 | 2,792,829 | | | | | | | | ||||||||||||||||||||||||||||
242 |
08/01/29 | 2,792,829 | 2,792,829 | | | | | | | | ||||||||||||||||||||||||||||
243 |
09/01/29 | 2,792,829 | 2,792,829 | | | | | | | | ||||||||||||||||||||||||||||
244 |
10/01/29 | 2,792,829 | 2,792,829 | | | | | | | | ||||||||||||||||||||||||||||
245 |
11/01/29 | 2,792,829 | 2,792,829 | | | | | | | | ||||||||||||||||||||||||||||
246 |
12/01/29 | 2,792,829 | 2,792,829 | | | | | | | | ||||||||||||||||||||||||||||
247 |
01/01/30 | 2,792,829 | 2,792,829 | | | | | | | | ||||||||||||||||||||||||||||
248 |
02/01/30 | 2,792,829 | 2,792,829 | | | | | | | |
Termination Premium |
5.0 | % | ||
Service Period Payments |
467,331,605 | |||
PPEF Deposit ECMs Savings During Construction |
300,000 | |||
Interest Payments |
144,023,365 | |||
Principal Payments |
183,375,883 | |||
Total Payment |
795,030,853 |
Project Site: Savannah River Site | Delivery Order No.: DE-AT09-09SR22572 dated 15-May-2009 | Contractor Name: Ameresco Federal Solutions | ||||||||||||||||||||||||||||||||||||
Beginning of | Payment Due | Lenders Termination | ||||||||||||||||||||||||||||||||||||
Month | Date | Government Payment | Service Period Expenses | PPEF Deposit | Debt Service Payment | Interest | Principal | Outstanding Principal Balance | Premium | Termination Liability | ||||||||||||||||||||||||||||
249 |
03/01/30 | 2,792,829 | 2,792,829 | | | | | | | | ||||||||||||||||||||||||||||
250 |
04/01/30 | 2,792,829 | 2,792,829 | | | | | | | | ||||||||||||||||||||||||||||
251 |
05/01/30 | 2,919,191 | 2,919,191 | | | | | | | | ||||||||||||||||||||||||||||
252 |
06/01/30 | 2,919,191 | 2,919,191 | | | | | | | | ||||||||||||||||||||||||||||
253 |
07/01/30 | 2,919,191 | 2,919,191 | | | | | | | | ||||||||||||||||||||||||||||
254 |
08/01/30 | 2,919,191 | 2,919,191 | | | | | | | | ||||||||||||||||||||||||||||
255 |
09/01/30 | 2,919,191 | 2,919,191 | | | | | | | | ||||||||||||||||||||||||||||
256 |
10/01/30 | 2,919,191 | 2,919,191 | | | | | | | | ||||||||||||||||||||||||||||
257 |
11/01/30 | 2,919,191 | 2,919,191 | | | | | | | | ||||||||||||||||||||||||||||
258 |
12/01/30 | 2,919,191 | 2,919,191 | | | | | | | | ||||||||||||||||||||||||||||
259 |
01/01/31 | 2,919,191 | 2,919,191 | | | | | | | | ||||||||||||||||||||||||||||
260 |
02/01/31 | 2,919,191 | 2,919,191 | | | | | | | | ||||||||||||||||||||||||||||
261 |
03/01/31 | 2,919,191 | 2,919,191 | | | | | | | | ||||||||||||||||||||||||||||
262 |
04/01/31 | 2,919,191 | 2,919,191 | | | | | | | |
[**] |
Final Proposal April 21, 2008
|
Biomass Cogeneration Facility and Heating Plants | |
Ameresco Federal Solutions
|
Savannah River Site | |
Appendix C, ECM 1 Equipment List, Page 1
|
Contract DE-AM36-02NT41457 |
Equipment Description | ESI Equipment # | P&ID | Company | Misc. Notes | ||||
Acid Regen Skid
|
520-522-600-001 | D27 | ||||||
Acid Storage Tank
|
520-522-300-001 | D27 | ||||||
Air Compressor #1
|
530-533-100-001 | D31 | ||||||
Air Compressor #2
|
530-533-100-002 | D31 | ||||||
Air Dryer Skid #1
|
530-533-500-001 | D31 | ||||||
Air Dryer Skid #2
|
530-533-500-002 | D31 | ||||||
Air Heater #1 Expansion Joint
|
610-616-200-004 | D07 | ||||||
Air Heater #2 Expansion Joint
|
610-616-200-008 | D08 | ||||||
Air Receiver
|
530-533-400-001 | D31 | ||||||
Amine Chemical Skid #1
|
510-515-200-002 | D22 | 3 motors | |||||
Amine Chemical Skid #2
|
510-515-200-003 | D22 | 2 motors | |||||
Antiscalant Pump
|
520-522-500-002 | D26 | ||||||
Ash Conditioner
|
460-462-100-001 | D13 | EPI | |||||
Ash Conditioner Rotary Valve
|
460-462-101-001 | D13 | EPI | |||||
Ash Exhauster #1
|
460-462-101-001 | D13 | EPI | |||||
Ash Exhauster #1 Filter
|
460-462-102-001 | D13 | EPI | |||||
Ash Exhauster #2
|
460-462-101-002 | D13 | EPI | |||||
Ash Exhauster #2 Filter
|
460-462-102-002 | D13 | EPI | |||||
Ash Silo
|
460-461-200-001 | D13 | EPI | |||||
Ash Silo Aeration Blower
|
470-471-400-001 | D13 | EPI | |||||
Ash Silo Double Dump Valve
|
460-461-201-001 | D13 | EPI | |||||
Ash Silo Emergency Safety Shower
|
170-176-200-002 | D32 | EPI | |||||
Ash Silo Truck Scale
|
430-431-200-003 | D13 | ||||||
Ash Silo VAC Filter
|
410-414-400-001 | D13 | EPI | |||||
Ash Silo Vent Filter
|
410-414-400-002 | D13 |
Final Proposal April 21, 2008
|
Biomass Cogeneration Facility and Heating Plants | |
Ameresco Federal Solutions
|
Savannah River Site | |
Appendix C, ECM 1 Equipment List, Page 2
|
Contract DE-AM36-02NT41457 |
Equipment Description | ESI Equipment # | P&ID | Company | Misc. Notes | ||||
Ash Silo Vent Filter Fan
|
410-414-303-001 | D13 | EPI | |||||
Baghouse #1
|
320-322-100-001 | D11 | EPI | |||||
Baghouse #1 Expansion Joint
|
610-616-200-011 | D11 | EPI | |||||
Baghouse #2
|
320-322-100-002 | D12 | EPI | |||||
Baghouse #2 Expansion Joint
|
610-616-200-017 | D12 | EPI | |||||
BFB Boiler #1
|
210-211-100-001 | D07 | EPI | |||||
BFB Boiler #1 Air Heater #1
|
250-252-200-001 | D07 | EPI | |||||
BFB Boiler #1 Economizer #1
|
250-251-100-001 | D07 | EPI | |||||
BFB Boiler #2
|
210-211-100-002 | D08 | EPI | |||||
BFB Boiler #2 Air Heater #2
|
250-252-200-002 | D08 | EPI | |||||
BFB Boiler #2 Economizer #2
|
250-251-100-002 | D08 | EPI | |||||
Biofuel Disc Screen
|
440-441-100-001 | D03 | ||||||
Biofuel Hogger
|
440-442-100-001 | D03 | ||||||
Biofuel Metering Bin #1
|
410-412-100-001 | D05 | EPI | (VFDs) 6 motors | ||||
Biofuel Metering Bin #2
|
410-412-100-002 | D05 | EPI | (VFDs) 6 motors | ||||
Biofuel Truck Dump #1
|
430-431-100-001 | D03 | ||||||
Biofuel Truck Dump #2
|
430-431-100-002 | D03 | ||||||
Biofuel Truck Dump #3
|
430-431-100-003 | D03 | ||||||
Biofuel Truck Reclaimer #1
|
430-433-300-001 | D03 | ||||||
Biofuel Truck Reclaimer #2
|
430-433-300-002 | D03 | ||||||
Biofuel Truck Reclaimer #3
|
430-433-300-003 | D03 | ||||||
Biofuel Truck Scale #1
|
430-431-200-001 | D03 | ||||||
Biofuel Truck Scale #2
|
430-431-200-002 | D03 | ||||||
Bleach Chemical Pump Skid
|
510-515-300-001 | D22 | 2 motors | |||||
Boiler #1 CBD Sample Cooler
|
510-518-100-009 | D32 | EPI | |||||
Boiler #1 Hopper #1
|
610-611-100-001 | D14 | EPI | |||||
Boiler #1 Hopper #2
|
610-611-100-002 | D14 | EPI |
Final Proposal April 21, 2008
|
Biomass Cogeneration Facility and Heating Plants | |
Ameresco Federal Solutions
|
Savannah River Site | |
Appendix C, ECM 1 Equipment List, Page 3
|
Contract DE-AM36-02NT41457 |
Equipment Description | ESI Equipment # | P&ID | Company | Misc. Notes | ||||
Boiler #1 Hopper #3
|
610-611-100-003 | D14 | EPI | |||||
Boiler #1 Hopper #4
|
610-611-100-004 | D14 | EPI | |||||
Boiler #1 SNCR Distribution Module
|
340-341-400-001 | D21 | EPI | |||||
Boiler #1 SNCR Metering Module Skid
|
340-341-401-001 | D21 | EPI | |||||
Boiler #1 Steam Drum Sample Cooler
|
510-518-100-002 | D32 | ||||||
Boiler #2 CBD Sample Cooler
|
510-518-100-010 | D32 | ||||||
Boiler #2 Hopper #1
|
610-611-100-005 | D14 | EPI | |||||
Boiler #2 Hopper #2
|
610-611-100-006 | D14 | EPI | |||||
Boiler #2 Hopper #3
|
610-611-100-007 | D14 | EPI | |||||
Boiler #2 Hopper #4
|
610-611-100-008 | D14 | EPI | |||||
Boiler #2 SNCR Distribution Module
|
340-341-400-002 | D21 | EPI | |||||
Boiler #2 SNCR Metering Module Skid
|
340-341-401-002 | D21 | EPI | |||||
Boiler #2 Steam Drum Sample Cooler
|
510-518-100-003 | D32 | ||||||
Boiler Drag Chain
|
430-436-100-001 | D05 | ||||||
Boiler Feed Water Pump #1
|
540-541-100-001 | D18 | VFD | |||||
Boiler Feed Water Pump #2
|
540-541-100-002 | D18 | VFD | |||||
Boiler Feed Water Pump #3
|
540-541-100-003 | D18 | VFD | |||||
Boiler Feedwater Heater
|
530-534-100-001 | D18 | ||||||
Bottom Blowdown Separator
|
530-532-100-001 | D33 | ||||||
Brine Tank
|
520-522-100-001 | D24 | ||||||
C.I.P. Tank
|
520-521-700-001 | D26 | ||||||
C.I.P. Tank Pump
|
520-521-701-001 | D26 | ||||||
Carbon Filter #1
|
510-511-200-001 | D25 | ||||||
Carbon Filter #2
|
510-511-200-002 | D25 | ||||||
Carbon Filter #3
|
510-511-200-003 | D25 | ||||||
Caustic Regen Skid
|
520-522-600-002 | D27 | ||||||
Caustic Storage Tank
|
520-522-200-001 | D27 |
Final Proposal April 21, 2008
|
Biomass Cogeneration Facility and Heating Plants | |
Ameresco Federal Solutions
|
Savannah River Site | |
Appendix C, ECM 1 Equipment List, Page 4
|
Contract DE-AM36-02NT41457 |
Equipment Description | ESI Equipment # | P&ID | Company | Misc. Notes | ||||
Chemical Injection Antiscalant
|
520-522-400-002 | D26 | ||||||
Chemical Injection PH Adjustment
|
520-522-400-001 | D26 | ||||||
Circular Stacker Reclaimer
|
410-412-400-002 | D04 | 3 motors | |||||
Condensate Sample Cooler
|
510-518-100-008 | D32 | ||||||
Continuous Blowdown Flash Tank #1
|
530-532-200-001 | D33 | ||||||
Continuous Blowdown Flash Tank #2
|
530-532-200-002 | D33 | ||||||
Control Oil Filter #1
|
820-823-600-003 | D36 | ||||||
Control Oil Filter #2
|
820-823-600-004 | D36 | ||||||
Conveyor #1
|
430-435-100-001 | D03 | ||||||
Conveyor #1 Tramp Metal Electromagnet
|
430-438-400-001 | D03 | ||||||
Conveyor #2
|
430-435-100-002 | D03 | ||||||
Conveyor #2 Diverter Gate #1
|
430-438-200-001 | D03 | ||||||
Conveyor #3
|
430-435-100-003 | D04 | ||||||
Conveyor #4
|
430-435-100-004 | D04 | ||||||
Conveyor #5
|
430-435-100-005 | D04 | ||||||
Conveyor #6
|
430-435-100-006 | D04 | ||||||
Cooling Tower
|
820-821-100-001 | D20 | ||||||
Cooling Tower Fan #1
|
820-821-300-001 | D20 | VFD | |||||
Cooling Tower Fan #1 Expansion Joint
|
630-636-200-007 | D20 | ||||||
Cooling Tower Fan #2
|
820-821-300-002 | D20 | VFD | |||||
Cooling Tower Fan #2 Expansion Joint
|
630-636-200-008 | D20 | ||||||
Cooling Tower Fan #3
|
820-821-300-003 | D20 | ||||||
Cooling Water Pump #1
|
540-546-100-001 | D20 | VFD | |||||
Cooling Water Pump #1 Expansion Joint #1
|
630-636-200-001 | D20 | ||||||
Cooling Water Pump #2
|
540-546-100-002 | D20 | VFD | |||||
Cooling Water Pump #2 Expansion Joint #1
|
630-636-200-003 | D20 | ||||||
Cooling Water Pump #3
|
540-546-100-003 | D20 | VFD |
Final Proposal April 21, 2008
|
Biomass Cogeneration Facility and Heating Plants | |
Ameresco Federal Solutions
|
Savannah River Site | |
Appendix C, ECM 1 Equipment List, Page 5
|
Contract DE-AM36-02NT41457 |
Equipment Description | ESI Equipment # | P&ID | Company | Misc. Notes | ||||
Cooling Water Pump #3 Expansion Joint #1
|
630-636-200-005 | D20 | ||||||
Deaerator #1
|
530-531-200-001 | D18 | ||||||
Deaerator #2
|
530-531-200-002 | D19 | ||||||
Deaerator Sample Cooler
|
510-518-100-004 | D32 | ||||||
Electric Heater
|
340-341-500-001 | D21 | ||||||
Emergency Oil Pump
|
820-823-100-003 | D35 | ||||||
Exhaust Fan #1
|
160-161-300-001 | D40 | ||||||
Exhaust Fan #2
|
160-161-300-002 | D40 | ||||||
Exhaust Fan #3
|
160-161-300-003 | D40 | ||||||
Exhaust Fan #4
|
160-161-300-004 | D40 | ||||||
Extraction Vapor Fan
|
820-823-700-001 | D35 | ||||||
FAB Fan #1 Expansion Joint
|
610-616-200-001 | D07 | EPI | |||||
FAB Fan #2 Expansion Joint
|
610-616-200-005 | D08 | EPI | |||||
FGR Fan #1
|
610-244-100-001 | D11 | EPI | |||||
FGR Fan #1 Damper
|
610-615-700-001 | D11 | EPI | |||||
FGR Fan #1 Damper Actuator
|
610-615-701-001 | D11 | EPI | |||||
FGR Fan #1 Damper Expansion Joint
|
610-616-200-016 | D11 | EPI | |||||
FGR Fan #1 Expansion Joint
|
610-616-200-002 | D07 | EPI | |||||
FGR Fan #2
|
610-244-100-002 | D12 | EPI | |||||
FGR Fan #2 Damper
|
610-615-700-002 | D12 | EPI | |||||
FGR Fan #2 Damper Actuator
|
610-615-701-002 | D12 | EPI | |||||
FGR Fan #2 Damper Expansion Joint
|
610-616-200-022 | D12 | EPI | |||||
FGR Fan #2 Expansion Joint
|
610-616-200-006 | D08 | EPI | |||||
Fluidizing Air Booster Fan #1
|
310-313-100-001 | D07 | EPI | |||||
Fluidizing Air Booster Fan #1 Damper
|
310-313-500-001 | D07 | EPI | |||||
Fluidizing Air Booster Fan #1 Damper
Actuator
|
310-313-501-001 | D07 | EPI |
Final Proposal April 21, 2008
|
Biomass Cogeneration Facility and Heating Plants | |
Ameresco Federal Solutions
|
Savannah River Site | |
Appendix C, ECM 1 Equipment List, Page 6
|
Contract DE-AM36-02NT41457 |
Equipment Description | ESI Equipment # | P&ID | Company | Misc. Notes | ||||
Fluidizing Air Booster Fan #2
|
310-313-100-002 | D08 | EPI | |||||
Fluidizing Air Booster Fan #2 Damper
|
310-313-500-002 | D08 | EPI | |||||
Fluidizing Air Booster Fan #2 Damper
Actuator
|
310-313-501-002 | D08 | EPI | |||||
Fuel Oil Pump #1
|
520-523-400-001 | D41 | ||||||
Fuel Oil Pump #2
|
520-523-400-002 | D41 | ||||||
Fuel Oil Stainer
|
620-623-400-001 | D41 | ||||||
Fuel Oil Storage Tank
|
520-523-100-001 | D41 | ||||||
Generator
|
810-813-100-001 | D36 | ||||||
Heater
|
820-823-201-001 | D35 | ||||||
Hotwell Pump #1
|
540-542-100-001 | D34 | VFD | |||||
Hotwell Pump #2
|
540-542-100-002 | D34 | VFD | |||||
Hotwell Pump Expansion Joint #1
|
630-636-200-016 | D34 | ||||||
Hotwell Pump Expansion Joint #2
|
630-636-200-017 | D34 | ||||||
Hotwell Pump Expansion Joint #3
|
630-636-200-018 | D34 | ||||||
Hotwell Pump Expansion Joint #4
|
630-636-200-019 | D34 | ||||||
Hotwell Sump Pump
|
540-542-100-001 | D34 | ||||||
Hydrazine Chemical Pump Skid
|
510-515-100-001 | D22 | 3 motors | |||||
ID Fan #1
|
310-311-100-001 | D11 | EPI | |||||
ID Fan #1 Damper #1
|
310-311-500-001 | D11 | EPI | |||||
ID Fan #1 Damper #1 & 2 Actuator
|
310-311-501-001 | D11 | EPI | |||||
ID Fan #1 Damper #1 Expansion Joint
|
610-616-200-013 | D11 | EPI | |||||
ID Fan #1 Damper #2
|
310-311-500-002 | D11 | EPI | |||||
ID Fan #1 Damper #2 Expansion Joint
|
610-616-200-014 | D11 | EPI | |||||
ID Fan #1 Damper Expansion Joint
|
610-616-200-012 | D11 | EPI | |||||
ID Fan #2
|
310-311-100-002 | D12 | EPI | |||||
ID Fan #2 Damper #1
|
310-311-500-003 | D12 | EPI |
Final Proposal April 21, 2008
|
Biomass Cogeneration Facility and Heating Plants | |
Ameresco Federal Solutions
|
Savannah River Site | |
Appendix C, ECM 1 Equipment List, Page 7
|
Contract DE-AM36-02NT41457 |
Equipment Description | ESI Equipment # | P&ID | Company | Misc. Notes | ||||
ID Fan #2 Damper #1 & 2 Actuator
|
310-311-501-002 | D12 | EPI | |||||
ID Fan #2 Damper #1 Expansion Joint
|
610-616-200-019 | D12 | EPI | |||||
ID Fan #2 Damper #2
|
310-311-500-004 | D12 | EPI | |||||
ID Fan #2 Damper #2 Expansion Joint
|
610-616-200-020 | D12 | EPI | |||||
ID Fan #2 Damper Expansion Joint
|
610-616-200-018 | D12 | EPI | |||||
Injector
|
340-341-600-005 | D21 | ||||||
Injector
|
340-341-600-001 | D21 | ||||||
Injector
|
340-341-600-008 | D21 | ||||||
Injector
|
340-341-600-007 | D21 | ||||||
Injector
|
340-341-600-006 | D21 | ||||||
Injector
|
340-341-600-004 | D21 | ||||||
Injector
|
340-341-600-002 | D21 | ||||||
Injector
|
340-341-600-003 | D21 | ||||||
Interstage Storage Tank
|
520-521-900-001 | D26 | ||||||
Lube / Control Oil Tank
|
820-823-400-001 | D35 | ||||||
Lube Oil Filter #1
|
820-823-600-001 | D35 | ||||||
Lube Oil Filter #2
|
820-823-600-002 | D35 | ||||||
Lube Oil Purifier System
|
820-823-200-001 | D35 | ||||||
Main Oil Pump
|
820-823-100-001 | D35 | ||||||
Mist Separator
|
820-823-800-001 | D35 | ||||||
Mixed Bed System Emergency Safety
Shower
|
170-176-200-003 | D32 | ||||||
Mixed Bed Unit #1
|
510-513-100-001 | D27 | ||||||
Mixed Bed Unit #2
|
510-513-100-002 | D27 | ||||||
Multi-media Filter #1
|
510-511-100-001 | D23 | ||||||
Multi-media Filter #2
|
510-511-100-002 | D23 | ||||||
Multi-media Filter #3
|
510-511-100-003 | D23 |
Final Proposal April 21, 2008
|
Biomass Cogeneration Facility and Heating Plants | |
Ameresco Federal Solutions
|
Savannah River Site | |
Appendix C, ECM 1 Equipment List, Page 8
|
Contract DE-AM36-02NT41457 |
Equipment Description | ESI Equipment # | P&ID | Company | Misc. Notes | ||||
Neutralization Pump #1
|
520-521-801-001 | D30 | ||||||
Neutralization Pump #2
|
520-521-801-002 | D30 | ||||||
Neutralization Tank
|
520-521-800-001 | D30 | ||||||
Oil Cooler #1
|
820-823-500-001 | D35 | ||||||
Oil Cooler #2
|
820-823-500-002 | D35 | ||||||
PFA Fan #1 Expansion Joint
|
610-616-200-003 | D07 | ||||||
PFA Fan #2 Expansion Joint
|
610-616-200-007 | D08 | ||||||
PH Adjustment Pump
|
520-522-500-001 | D26 | ||||||
Phosphate Chemical Pump Skid
|
510-515-200-001 | D22 | 3 motors | |||||
Primary Fluidizing Air Fan #1
|
310-312-100-001 | D07 | EPI | |||||
Primary Fluidizing Air Fan #1 Damper
|
310-312-500-001 | D07 | EPI | |||||
Primary Fluidizing Air Fan #1 Damper
Actuator
|
310-312-501-001 | D07 | EPI | |||||
Primary Fluidizing Air Fan #1 SCAH
|
250-253-100-001 | D07 | EPI | |||||
Primary Fluidizing Air Fan #1 Silencer
|
310-312-600-001 | D07 | EPI | |||||
Primary Fluidizing Air Fan #2
|
310-312-100-002 | D08 | EPI | |||||
Primary Fluidizing Air Fan #2 Damper
|
310-312-500-002 | D08 | EPI | |||||
Primary Fluidizing Air Fan #2 Damper
Actuator
|
310-312-501-002 | D08 | EPI | |||||
Primary Fluidizing Air Fan #2 SCAH
|
250-253-100-002 | D08 | EPI | |||||
Primary Fluidizing Air Fan #2 Silencer
|
310-312-600-002 | D08 | EPI | |||||
Primary Superheater #1
|
210-211-200-001 | D15 | EPI | |||||
Primary Superheater #2
|
210-211-200-002 | D16 | EPI | |||||
Process Lift Pump #1
|
530-532-400-001 | D33 | ||||||
Process Lift Pump #2
|
530-532-400-002 | D33 | ||||||
RO Feed Pump #1
|
510-511-400-001 | D26 | ||||||
RO Feed Pump #1 Filter
|
510-511-401-001 | D26 | ||||||
RO Feed Pump #2
|
510-511-400-002 | D26 |
Final Proposal April 21, 2008
|
Biomass Cogeneration Facility and Heating Plants | |
Ameresco Federal Solutions
|
Savannah River Site | |
Appendix C, ECM 1 Equipment List, Page 9
|
Contract DE-AM36-02NT41457 |
Equipment Description | ESI Equipment # | P&ID | Company | Misc. Notes | ||||
RO Feed Pump #2 Filter
|
510-511-401-002 | D26 | ||||||
RO Forwarding Pump #1
|
510-511-400-003 | D26 | ||||||
RO Forwarding Pump #2
|
510-511-400-004 | D26 | ||||||
RO System
|
510-511-300-001 | D26 | ||||||
Sample Cooler Emergency Safety Shower
|
170-176-200-001 | D32 | ||||||
Sand Bucket Elevator #1
|
430-434-100-001 | D14 | ||||||
Sand Bucket Elevator #2
|
430-434-100-002 | D14 | ||||||
Sand Drag Chain #1
|
430-436-100-002 | D14 | ||||||
Sand Drag Chain #2
|
430-436-100-003 | D14 | ||||||
Sand Drag Chain #3
|
430-436-100-004 | D14 | ||||||
Sand Drag Chain #4
|
430-436-100-005 | D14 | ||||||
Sand Silo #1
|
410-411-310-001 | D14 | ||||||
Sand Silo #1 Bin Vent Filter
|
410-414-300-004 | D14 | ||||||
Sand Silo #1 Screw Conveyor
|
420-423-100-003 | D14 | VFD | |||||
Sand Silo #1 Vent Filter Fan
|
410-414-301-001 | D14 | ||||||
Sand Silo #2
|
410-411-310-002 | D14 | ||||||
Sand Silo #2 Bin Vent Filter
|
410-414-300-005 | D14 | ||||||
Sand Silo #2 Screw Conveyor
|
420-423-100-004 | D14 | VFD | |||||
Sand Silo #2 Vent Filter Fan
|
410-414-301-002 | D14 | ||||||
Secondary Superheater #1
|
210-211-200-004 | D15 | ||||||
Secondary Superheater #2
|
210-211-200-003 | D16 | ||||||
Stack #1
|
610-614-100-001 | D11 | ||||||
Stack #1 Expansion Joint
|
610-616-200-015 | D11 | EPI | |||||
Stack #2
|
610-614-100-002 | D12 | EPI | |||||
Stack #2 Expansion Joint
|
610-616-200-021 | D12 | EPI | |||||
Burner #1 Boiler #1
|
240-241-200-002 | D06 | EPI | |||||
Start-up Burner #1 Boiler #2
|
240-241-200-004 | D06 | EPI | Not shown on P&ID |
Final Proposal April 21, 2008
|
Biomass Cogeneration Facility and Heating Plants | |
Ameresco Federal Solutions
|
Savannah River Site | |
Appendix C, ECM 1 Equipment List, Page 10
|
Contract DE-AM36-02NT41457 |
Equipment Description | ESI Equipment # | P&ID | Company | Misc. Notes | ||||
Burner #2 Boiler #1
|
240-241-200-003 | D06 | EPI | |||||
Start-up Burner #2 Boiler #2
|
240-241-200-005 | D06 | EPI | Not shown on P&ID | ||||
Steam Turbine
|
810-811-300-001 | D36 | ||||||
Sulphuric Acid Chemical Pump Skid
|
510-515-300-002 | D22 | 2 motors | |||||
Supply Fan #1
|
160-161-200-001 | D40 | ||||||
Supply Fan #2
|
160-161-200-002 | D40 | ||||||
Supply Fan #3
|
160-161-200-003 | D40 | ||||||
Supply Fan #4
|
160-161-200-004 | D40 | ||||||
Supply Fan #5
|
160-161-200-005 | D40 | ||||||
Supply Fan #6
|
160-161-200-006 | D40 | ||||||
Supply Fan #7
|
160-161-200-007 | D40 | ||||||
Supply Fan #8
|
160-161-200-008 | D40 | ||||||
Surface Condenser
|
820-822-100-001 | D34 | ||||||
Surface Condenser Expansion Joint #1
|
630-636-200-011 | D34 | ||||||
Surface Condenser Expansion Joint #2
|
630-636-200-012 | D34 | ||||||
Surface Condenser Expansion Joint #3
|
630-636-200-013 | D34 | ||||||
Surface Condenser Expansion Joint #4
|
630-636-200-014 | D34 | ||||||
Surface Condenser Expansion Joint #5
|
630-636-200-015 | D34 | ||||||
TDF Reclaimer
|
430-433-300-004 | D05 | ||||||
Treated Water Storage Tank
|
520-521-300-001 | D28 | ||||||
Treated Water Transfer Pump #1
|
540-544-100-001 | D28 | ||||||
Treated Water Transfer Pump #2
|
540-544-100-002 | D28 | ||||||
Urea Circulation Module
|
340-341-301-001 | D21 | EPI | |||||
Urea Circulation Pump #1
|
340-341-300-001 | D21 | EPI | |||||
Urea Circulation Pump #2
|
340-341-300-002 | D21 | EPI | |||||
Urea Metering Pump #1
|
340-341-300-003 | D21 | EPI | |||||
Urea Metering Pump #2
|
340-341-300-004 | D21 | EPI |
Final Proposal April 21, 2008
|
Biomass Cogeneration Facility and Heating Plants | |
Ameresco Federal Solutions
|
Savannah River Site | |
Appendix C, ECM 1 Equipment List, Page 11
|
Contract DE-AM36-02NT41457 |
Equipment Description | ESI Equipment # | P&ID | Company | Misc. Notes | ||||
Urea Metering Pump #3
|
340-341-300-005 | D21 | EPI | |||||
Urea Metering Pump #4
|
340-341-300-006 | D21 | EPI | |||||
Urea Storage Tank
|
340-341-200-001 | D21 | EPI | |||||
Urea Storage Tank Inlet Expansion Joint
|
630-636-200-009 | D21 | EPI | |||||
Urea Storage Tank Outlet Expansion Joint
|
630-636-200-010 | D21 | EPI | |||||
Urea Tank / Acid / Bleach Emergency
Safety Shower
|
170-176-200-004 | D32 | EPI | |||||
Vacuum Pump #1
|
820-822-201-001 | D34 | ||||||
Vacuum Pump #2
|
820-822-201-001 | D34 | ||||||
Vibrating Feeder #1
|
320-321-300-001 | D14 | 2 motors | |||||
Vibrating Feeder #2
|
320-321-300-002 | D14 | 2 motors | |||||
Water Booster Pump #1
|
540-543-100-001 | D21 | ||||||
Water Booster Pump #2
|
540-543-100-002 | D21 | ||||||
Water Booster Pump #3
|
540-543-100-003 | D21 | ||||||
Water Booster Pump #4
|
540-543-100-004 | D21 | ||||||
Water Softener #1
|
510-512-100-001 | D24 | ||||||
Water Softener #2
|
510-512-100-002 | D24 |
Final Proposal April 21, 2008
|
Biomass Cogeneration Facility and Heating Plants | |
Ameresco Federal Solutions
|
Savannah River Site | |
Appendix C, ECM 2 Equipment List, Page 1
|
Contract DE-AM36-02NT41457 |
Equipment Description | Equipment # | P&ID | Company | Misc. Notes | ||||
Area K Air Accumulator
|
530-533-400-002 | D05 | Hurst Boiler & Welding Co., Inc. | |||||
Area K Air Heater
|
250-252-200-001 | D05 | Hurst Boiler & Welding Co., Inc. | |||||
Area K Amine to Steam Line
Chemical Pump #2
|
510-515-300-001 | D23 | ||||||
Area K Air Compressor
|
530-533-100-001 | D05 | Existing Air Compressor | |||||
Area K Air Receiver
|
530-533-400-001 | D05 | Existing Air Compressor | |||||
Area K BFW Pump #1
|
540-541-100-001 | D11 | Hurst Boiler & Welding Co., Inc. | |||||
Area K BFW Pump #2
|
540-541-100-002 | D11 | Hurst Boiler & Welding Co., Inc. | |||||
Area K BFW Sample Cooler
|
510-518-100-003 | D19 | Process Power & Equipment Sales, Inc. | |||||
Area K Biofuel Metering Bin
|
440-443-200-001 | D03 | Hurst Boiler & Welding Co., Inc. | |||||
Area K Blowdown Seperator Tank
|
530-532-100-001 | D21 | Hurst Boiler & Welding Co., Inc. | |||||
Area K Blowdown Sump Pump #1
|
540-549-300-001 | D21 | ||||||
Area K Blowdown Sump Pump #2
|
540-549-300-002 | D21 | ||||||
Area K Brine Tank
|
510-512-100-003 | D19 | ||||||
Area K Building Exhaust Fan
|
160-161-300-001 | D26 | ||||||
Area K Building Supply Fan
|
160-161-200-001 | D26 | ||||||
Area K CBD Sample Cooler
|
510-518-100-002 | D19 | Process Power & Equipment Sales, Inc. | |||||
Area K DCS of PLC System (BFW)
|
720-725-100-002 | |||||||
Area K DCS or PLC System (Boiler)
|
720-725-100-001 | Hurst Boiler & Welding Co., Inc. | ||||||
Area K Deaerator
|
530-531-100-001 | D11 | Hurst Boiler & Welding Co., Inc. | |||||
Area K Duplex Water Softener A
|
510-512-100-001 | D19 | ||||||
Area K Duplex Water Softener B
|
510-512-100-002 | D19 | ||||||
Area K Electric Heater #1
|
160-162-500-001 | D26 | ||||||
Area K Electric Heater #2
|
160-162-500-002 | D26 |
Final Proposal April 21, 2008
|
Biomass Cogeneration Facility and Heating Plants | |
Ameresco Federal Solutions
|
Savannah River Site | |
Appendix C, ECM 2 Equipment List, Page 2
|
Contract DE-AM36-02NT41457 |
Equipment Description | Equipment # | P&ID | Company | Misc. Notes | ||||
Area K Electric Heater #3
|
160-162-500-003 | D26 | ||||||
Area K Feeder Magnet
|
430-438-400-001 | D03 | ||||||
Area K Fly Ash Multiclone
|
320-321-100-001 | D05 | Hurst Boiler & Welding Co., Inc. | |||||
Area K Fly Ash Reinjection Fan
|
610-244-100-001 | D07 | Hurst Boiler & Welding Co., Inc. | |||||
Area K Fly Ash Rotary Air Valve #1
|
320-321-200-001 | D07 | Hurst Boiler & Welding Co., Inc. | |||||
Area K Fly Ash Rotary Air Valve #2
|
320-321-200-002 | D07 | Hurst Boiler & Welding Co., Inc. | |||||
Area K Fuel Oil Back-Up Burner
|
240-241-200-001 | D15 | Hurst Boiler & Welding Co., Inc. | |||||
Area K Fuel Oil Pump
|
240-243-100-002 | D15 | Hurst Boiler & Welding Co., Inc. | |||||
Area K Fuel Oil Pump #1 (ON HOLD)
|
HOLD | D13 | ||||||
Area K Fuel Oil Pump #2 (ON HOLD)
|
HOLD | D13 | ||||||
Area K Fuel Oil Storage Tank
|
520-523-100-001 | D13 | ||||||
Area K Fuel Sizing Screen
|
440-441-100-001 | D03 | Hurst Boiler & Welding Co., Inc. | |||||
Area K Hybrid Boiler
|
210-213-100-001 | D05 | Hurst Boiler & Welding Co., Inc. | |||||
Area K Hydrazine to DA Chemical
Pump #1
|
510-515-100-001 | D23 | ||||||
Area K ID Fan
|
310-311-200-001 | D05 | Hurst Boiler & Welding Co., Inc. | |||||
Area K Inclined Drag Chain Conveyor
|
430-436-100-001 | D03 | Hurst Boiler & Welding Co., Inc. | |||||
Area K MCC/PLC Room A.C.
|
160-162-300-001 | D26 | ||||||
Area K Metering Bin Screw Conveyor
#1
|
430-432-100-001 | D03 | Hurst Boiler & Welding Co., Inc. | |||||
Area K Metering Bin Screw Conveyor
#2
|
430-432-100-002 | D03 | Hurst Boiler & Welding Co., Inc. | |||||
Area K Non Return Valve
|
220-221-100-001 | D09 | Hurst Boiler & Welding Co., Inc. | |||||
Area K Oil Burner Fan
|
310-313-100-001 | D15 | Hurst Boiler & Welding Co., Inc. | |||||
Area K Overfire Air Fan
|
310-314-100-001 | D05 | Hurst Boiler & Welding Co., Inc. | |||||
Area K Phosphate to BFW Chemical
Pump #3
|
510-515-200-001 | D23 | ||||||
Area K Pit Sump Pump
|
540-549-300-005 | D03 |
Final Proposal April 21, 2008
|
Biomass Cogeneration Facility and Heating Plants | |
Ameresco Federal Solutions
|
Savannah River Site | |
Appendix C, ECM 2 Equipment List, Page 3
|
Contract DE-AM36-02NT41457 |
Equipment Description | Equipment # | P&ID | Company | Misc. Notes | ||||
Area K Reciprocating Floor Hydraulic
System
|
430-438-700-001 | D03 | Hurst Boiler & Welding Co., Inc. | |||||
Area K Reciprocating Grate Stoker
|
230-231-300-001 | D07 | Hurst Boiler & Welding Co., Inc. | |||||
Area K Reclaim Vibratory Feeder
|
430-432-200-001 | D03 | Hurst Boiler & Welding Co., Inc. | |||||
Area K Safety Eyewash & Shower
|
170-176-200-001 | D19 | ||||||
Area K Sootblower #1
|
220-223-100-001 | D05 | Hurst Boiler & Welding Co., Inc. | |||||
Area K Sootblower #2
|
220-223-100-002 | D05 | Hurst Boiler & Welding Co., Inc. | |||||
Area K Sootblower #3
|
220-223-100-003 | D05 | Hurst Boiler & Welding Co., Inc. | |||||
Area K Sootblower #4
|
220-223-100-004 | D05 | Hurst Boiler & Welding Co., Inc. | |||||
Area K Sootblower #5
|
220-223-100-005 | D05 | Hurst Boiler & Welding Co., Inc. | |||||
Area K Stack
|
610-614-100-002 | D05 | Hurst Boiler & Welding Co., Inc. | |||||
Area K Stainless Steel Lab Sink
|
170-179-300-001 | D19 | ||||||
Area K Steam Sample Cooler
|
510-518-100-001 | D19 | Process Power & Equipment Sales, Inc. | |||||
Area K Truck Reclaimer Reciprocating
Floor
|
430-433-200-001 | D03 | Hurst Boiler & Welding Co., Inc. | |||||
Area K Truck Unloading Hydraulic
System
|
430-431-100-001 | D03 | Hurst Boiler & Welding Co., Inc. | |||||
Area K Underfire Air Fan
|
310-312-100-001 | D05 | Hurst Boiler & Welding Co., Inc. | |||||
Area K Vacuum Breaker
|
220-221-200-001 | D11D | Hurst Boiler & Welding Co., Inc. | |||||
Area L Air Accumulator
|
530-533-400-003 | D06 | Hurst Boiler & Welding Co., Inc. | |||||
Area L Air Compressor
|
530-533-100-001 | D25 | ||||||
Area L Air Heater
|
250-252-200-002 | D06 | Hurst Boiler & Welding Co., Inc. | |||||
Area L Air Receiver
|
530-533-400-001 | D25 | ||||||
Area L Amine to Steam Line Chemical
Pump #2
|
510-515-300-002 | D24 | ||||||
Area L Ash Removal Drag Chain
Conveyor
|
460-464-600-002 | D08 | Hurst Boiler & Welding Co., Inc. | |||||
Area L Ash Roll-Off Dumpster
|
460-461-400-002 | D08 |
Final Proposal April 21, 2008
|
Biomass Cogeneration Facility and Heating Plants | |
Ameresco Federal Solutions
|
Savannah River Site | |
Appendix C, ECM 2 Equipment List, Page 4
|
Contract DE-AM36-02NT41457 |
Equipment Description | Equipment # | P&ID | Company | Misc. Notes | ||||
Area L BFW Pump #1
|
540-541-100-003 | D12 | Hurst Boiler & Welding Co., Inc. | |||||
Area L BFW Pump #2
|
540-541-100-004 | D12 | Hurst Boiler & Welding Co., Inc. | |||||
Area L BFW Sample Cooler
|
510-518-100-006 | D20 | Process Power & Equipment Sales, Inc. | |||||
Area L Biofuel Metering Bin
|
440-443-200-002 | D04 | Hurst Boiler & Welding Co., Inc. | |||||
Area L Blowdown Seperator Tank
|
530-532-100-002 | D22 | Hurst Boiler & Welding Co., Inc. | |||||
Area L Blowdown Sump Pump #1
|
540-549-300-003 | D22 | ||||||
Area L Blowdown Sump Pump #2
|
540-549-300-004 | D22 | ||||||
Area L Brine Tank
|
510-512-100-006 | D19 | ||||||
Area L Building Exhaust Fan
|
160-161-300-002 | D27 | ||||||
Area L Building Supply Fan
|
160-161-200-002 | D27 | ||||||
Area L CBD Sample Cooler
|
510-518-100-005 | D20 | Process Power & Equipment Sales, Inc. | |||||
Area L Coalescing Prefilter
|
530-533-700-001 | D25 | ||||||
Area L DCS of PLC System (BFW)
|
720-725-100-004 | |||||||
Area L DCS or PLC System (Boiler)
|
720-725-100-003 | Hurst Boiler & Welding Co., Inc. | ||||||
Area L Deaerator
|
530-531-100-002 | D12 | Hurst Boiler & Welding Co., Inc. | |||||
Area L Duplex Water Softener A
|
510-512-100-004 | D20 | ||||||
Area L Duplex Water Softener B
|
510-512-100-005 | D19 | ||||||
Area L Electric Heater #1
|
160-162-500-004 | D27 | ||||||
Area L Electric Heater #2
|
160-162-500-005 | D27 | ||||||
Area L Electric Heater #3
|
160-162-500-006 | D27 | ||||||
Area L Feeder Magnet
|
430-438-400-002 | D04 | ||||||
Area L Fly Ash Multiclone
|
320-321-100-003 | D06 | Hurst Boiler & Welding Co., Inc. | |||||
Area L Fly Ash Reinjection Fan
|
610-244-100-002 | D08 | Hurst Boiler & Welding Co., Inc. | |||||
Area L Fly Ash Rotary Air Valve #1
|
320-321-200-004 | D08 | Hurst Boiler & Welding Co., Inc. | |||||
Area L Fly Ash Rotary Air Valve #2
|
320-321-200-005 | D08 | Hurst Boiler & Welding Co., Inc. |
Final Proposal April 21, 2008
|
Biomass Cogeneration Facility and Heating Plants | |
Ameresco Federal Solutions
|
Savannah River Site | |
Appendix C, ECM 2 Equipment List, Page 5
|
Contract DE-AM36-02NT41457 |
Equipment Description | Equipment # | P&ID | Company | Misc. Notes | ||||
Area L Fuel Oil Back-Up Burner
|
240-241-200-002 | D16 | Hurst Boiler & Welding Co., Inc. | |||||
Area L Fuel Oil Pump
|
240-243-100-001 | D16 | Hurst Boiler & Welding Co., Inc. | |||||
Area L Fuel Oil Pump #1 (ON HOLD)
|
HOLD | D14 | ||||||
Area L Fuel Oil Pump #2 (ON HOLD)
|
HOLD | D14 | ||||||
Area L Fuel Oil Storage Tank
|
520-523-100-001 | D14 | ||||||
Area L Fuel Sizing Screen
|
440-441-100-002 | D04 | Hurst Boiler & Welding Co., Inc. | |||||
Area L Hybrid Boiler
|
210-213-100-002 | D06 | Hurst Boiler & Welding Co., Inc. | |||||
Area L Hydrazine to DA Chemical
Pump #1
|
510-515-100-002 | D24 | ||||||
Area L ID an
|
310-311-200-002 | D06 | Hurst Boiler & Welding Co., Inc. | |||||
Area L Inclined Drag Chain Conveyor
|
430-436-100-002 | D04 | Hurst Boiler & Welding Co., Inc. | |||||
Area L MCC/PLC Room A.C.
|
160-162-300-002 | D27 | ||||||
Area L Metering Bin Screw Conveyor
#1
|
430-432-100-003 | D04 | Hurst Boiler & Welding Co., Inc. | |||||
Area L Metering Bin Screw Conveyor
#2
|
430-432-100-004 | D04 | Hurst Boiler & Welding Co., Inc. | |||||
Area L Non Return Valve
|
220-221-100-002 | D-0 | Hurst Boiler & Welding Co., Inc. | |||||
Area L Oil Burner Fan
|
310-313-100-002 | D16 | Hurst Boiler & Welding Co., Inc. | |||||
Area L Overfire Air Fan
|
310-314-100-002 | D06 | Hurst Boiler & Welding Co., Inc. | |||||
Area L Particulate Afterfilter
|
530-533-700-002 | D25 | ||||||
Area L Phosphate to BFW Chemical
Pump #3
|
510-515-200-002 | D24 | ||||||
Area L Pit Sump Pump
|
540-549-300-006 | D04 | ||||||
Area L Reciprocating Floor Hydraulic
System
|
430-438-70-002 | D04 | Hurst Boiler & Welding Co., Inc. | |||||
Area L Reciprocating Grate Stoker
|
230-231-300-002 | D08 | Hurst Boiler & Welding Co., Inc. | |||||
Area L Reclaim Vibratory Feeder
|
430-432-200-001 | D04 | Hurst Boiler & Welding Co., Inc. | |||||
Area L Refrigerant Air Dryer
|
530-533-500-001 | D25 |
Final Proposal April 21, 2008
|
Biomass Cogeneration Facility and Heating Plants | |
Ameresco Federal Solutions
|
Savannah River Site | |
Appendix C, ECM 2 Equipment List, Page 6
|
Contract DE-AM36-02NT41457 |
Equipment Description | Equipment # | P&ID | Company | Misc. Notes | ||||
Area L Safety Eyewash & Shower |
170-176-200-002 | D20 | ||||||
Area L Sootblower #1 |
220-223-100-006 | D06 | Hurst Boiler & Welding Co., Inc. | |||||
Area L Sootblower #2 |
220-223-100-007 | D06 | Hurst Boiler & Welding Co., Inc. | |||||
Area L Sootblower #3 |
220-223-100-008 | D06 | Hurst Boiler & Welding Co., Inc. | |||||
Area L Sootblower #4 |
220-223-100-009 | D05 | Hurst Boiler & Welding Co., Inc. | |||||
Area L Sootblower #5 |
220-223-100-010 | D05 | Hurst Boiler & Welding Co., Inc. | |||||
Area L Stack |
610-614-100-001 | D06 | Hurst Boiler & Welding Co., Inc. | |||||
Area L Stainless Steel Lab Sink |
170-179-300-002 | D20 | ||||||
Area L Steam Sample Cooler |
510-518-100-004 | D20 | Process Power & Equipment Sales, Inc. | |||||
Area L Truck Reclaimer Reciprocating
Floor |
430-433-200-002 | D04 | Hurst Boiler & Welding Co., Inc. | |||||
Area L Truck Unloading Hydraulic
System |
430-431-100-002 | D04 | Hurst Boiler & Welding Co., Inc. | |||||
Area L Underfire Air Fan |
310-312-100-002 | D06 | Hurst Boiler & Welding Co., Inc. | |||||
Area L Vacuum Breaker |
220-221-200-002 | D12 | Hurst Boiler & Welding Co., Inc. |
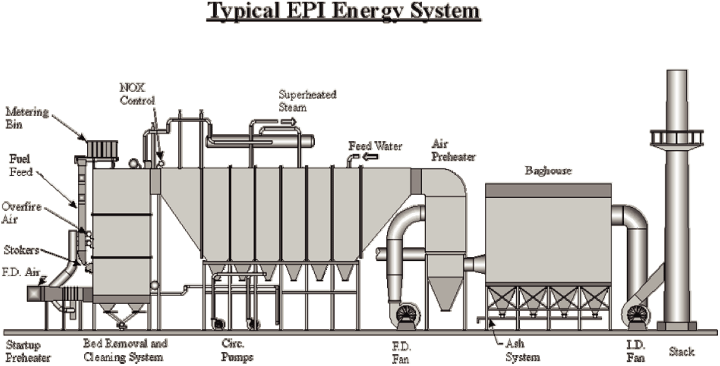
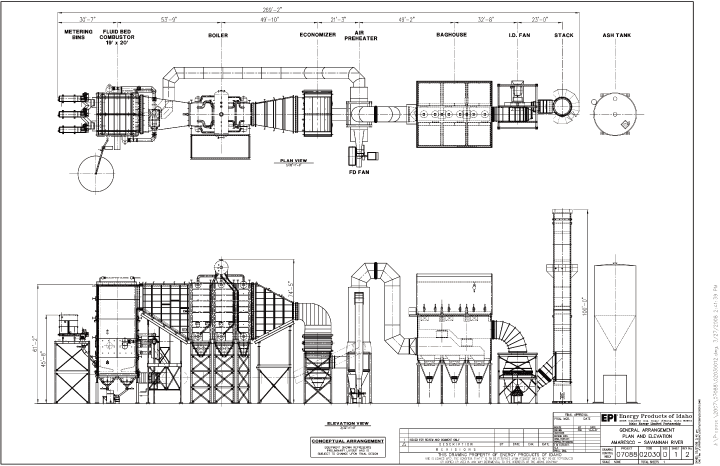
Station | Description | |||||||||
No. | % moisture | wood/325 | TDF/325 | |||||||
1 | Fuel , % Btu (LHV) |
|||||||||
wood |
100.0 | % | 70.0 | % | ||||||
TDF |
0.0 | % | 30.0 | % | ||||||
DGS |
0.0 | % | 0.0 | % | ||||||
Fuel, TPY |
||||||||||
wood |
184,769 | 128,575 | ||||||||
TDF |
0 | 13,246 | ||||||||
DGS |
0 | 0 | ||||||||
B.D. Blend Analysis |
||||||||||
Carbon, %: |
50.80 | 56.08 | ||||||||
Hydrogen, %: |
6.00 | 6.47 | ||||||||
Sulfur, %: |
0.08 | 0.15 | ||||||||
Oxygen, %: |
41.43 | 35.29 | ||||||||
Nitrogen, %: |
0.37 | 0.44 | ||||||||
Chlorine, %: |
0.00 | 0.00 | ||||||||
Ash/Other, %: |
1.32 | 1.38 | ||||||||
As Fired Moisture, %: |
50.00 | 45.43 | ||||||||
As Fired HHV BTU/lb: |
4,300 | 5,338 | ||||||||
As Fired LHV BTU/lb: |
3,509 | 4,545 | ||||||||
Flowrate lb/hr: |
42,185 | 32,379 | ||||||||
H MBtu/hr, LHV: |
148.02 | 147.15 | ||||||||
Ash + Lime Flow, lb/hr: |
397 | 413 | ||||||||
Limestone lb/hr: |
105 | 165 | ||||||||
2 | FD Fan |
|||||||||
Ambient Air lb/hr: |
175,100 | 183,000 | ||||||||
Total Air Flow lb/hr: |
175,100 | 183,000 | ||||||||
Temp oF: |
80 | 80 | ||||||||
ACFM: |
40,200 | 42,000 | ||||||||
dPress in WC: |
52 | 52 | ||||||||
Theor Power Hp: |
450 | 470 | ||||||||
Excess Air: |
35 | % | 44 | % | ||||||
3 | Bed |
|||||||||
Surface area, ft2: |
873 | 873 | ||||||||
Heat trans., MBtu/hr: |
29 | 30 | ||||||||
Bed Dia, ft: |
0.00 | 0 | ||||||||
Bed Width, ft: |
20.00 | 20.00 | ||||||||
Bed Length, ft: |
19.10 | 19.10 | ||||||||
Temp F: |
1,514 | 1,546 | ||||||||
4 | Vapor Space |
|||||||||
Temp F: |
1,760 | 1,790 | ||||||||
Surface area, ft2: |
650 | 650 | ||||||||
Heat trans., MBtu/hr: |
12 | 12 | ||||||||
Velocity fps: |
9.3 | 9.2 | ||||||||
Flowrate lb/hr: |
217,000 | 215,100 | ||||||||
ACFM: |
213,100 | 210,400 | ||||||||
5 | Boiler |
|||||||||
Gas Flow lb/hr: |
217,000 | 215,100 | ||||||||
ACFM: |
213,100 | 210,400 | ||||||||
Gas H MBtu/hr: |
112.08 | 109.81 | ||||||||
Boiler duty, M Btu/hr: |
73.89 | 73.07 | ||||||||
Steam Temp F: |
825 | 825 | ||||||||
Steam Press (psia): |
850 | 850 | ||||||||
Steam Flow lb/hr: |
120,000 | 120,000 | ||||||||
Ash lb/hr: |
100 | 100 | ||||||||
Consummables |
||||||||||
Limestone lb/hr |
105 | 165 | ||||||||
Ammonia-as aqueous, lb/hr |
71 | 317 | ||||||||
Hydrated Lime lb/hr |
0 | 0 | ||||||||
Air Preheater/ SCAH |
||||||||||
Gas In Temp, F: |
437 | 441 | ||||||||
Gas out Temp, F: |
325 | 325 | ||||||||
Air Out Temp, F |
269 | 262 | ||||||||
APH Duty., MBtu/hr: |
7.00 | 7.00 | ||||||||
SCAH Duty, M Btu/hr: |
0 | 0 | ||||||||
7 | Economizer |
|||||||||
Gas In Temp, F: |
685 | 685 | ||||||||
Gas out Temp, F: |
437 | 441 | ||||||||
H2O in Temp, F: |
370 | 370 | ||||||||
H2O Out Temp, F |
487 | 482 | ||||||||
Heat Trans., MBtu/hr: |
15.75 | 14.99 | ||||||||
Ash lb/hr: |
0 | 0 | ||||||||
10 | Baghouse |
|||||||||
flow, lb/hr |
217,017 | 215,106 | ||||||||
ACFM |
75,247 | 73,455 | ||||||||
Temp, F; |
325 | 325 | ||||||||
moisture, wt%: |
15.97 | % | 12.68 | % | ||||||
H, MM Btu/hr |
15.59 | 14.91 | ||||||||
Ash lb/hr: |
294 | 306 | ||||||||
11 | ID Fan |
|||||||||
ACFM: |
75,247 | 73,455 | ||||||||
Temp, F: |
325 | 325 | ||||||||
SP, in H2O: |
19 | 19 | ||||||||
BHP |
341 | 333 | ||||||||
12 | Stack |
|||||||||
Gas Temp F: |
334 | 334 | ||||||||
Gas Flow lb/hr: |
217,017 | 215,106 | ||||||||
ACFM: |
76,134 | 74,321 | ||||||||
Enthalpy MBtu/hr: |
16.17 | 15.46 | ||||||||
Vol (dry)%O2: |
5.5 | % | 6.5 | % | ||||||
Wt% H2O: |
16.0 | % | 12.7 | % | ||||||
Overall balance | ||||||||||
Total energy Input, MBtu/hr HHV: | 181.4 | 172.8 | ||||||||
Boiler Duty, MBtu/hr: | 128.5 | 128.5 | ||||||||
Efficiency, %: | 70.8 | 74.3 |
EPI Energy Products of Idaho | ||||||||||||||
4006 Industrial Ave. Coeur d Alene, Idaho 83814 | ||||||||||||||
PROJ. MGR. | DATE | Idaho Energy Limited Partnership | ||||||||||||
PROCESS FLOW DIAGRAM (Customary U.S. Units) | ||||||||||||||
ORIGNTR | BY | DATE | Ameresco | |||||||||||
CHECKED | mlm | 11/19/07 | Savannah River | |||||||||||
PROJ. ENG. | PROJECT | CODE | SHEET | OF | REV | |||||||||
filename |
4 2 08 | 04/03/08 | S07088 | 0201 | 1 | 1 | 2 |
Fluidized Bed Combustors | Page 1 of 3 |

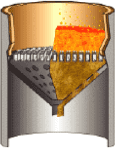
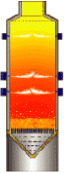
Fluidized Bed Combustors | Page 2 of 3 |
![]() |
Low combustion temperatures and low excess air within the bed reduces the formation of certain emissions such as NOx. | |
![]() |
High combustion efficiency results in flue gases that contain low amounts of CO. | |
![]() |
Emissions such as SOx and NOx may be abated within the fluidized bed system by injecting limestone into the bed and ammonia into the vapor space. |
Fluidized Bed Combustors | Page 3 of 3 |
4006 Industrial Ave
Coeur dAlene, Idaho USA 83815-8928
Phone (208) 765-1611 ~ Fax (208) 765-0503
Email: epi2@energyproducts.com
Last modified: April 3, 2008
*
Benefits of Fluidized Bed Combustion continued... | Page 2 |
| Low combustion temperatures and low excess air within the bed reduce the formation of certain emissions such as NOx. | |
| High combustion efficiency results in flue gases that contain low amounts of CO. | |
| Emissions such as SOx and NOx may be abated within the fluidized bed system by injecting limestone into the bed and ammonia into the vapor space. |
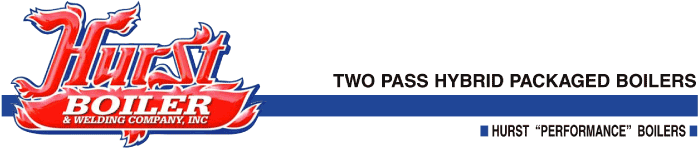
HD SERIES | Fire Tube / Water Tube Hybrid | |
Design |
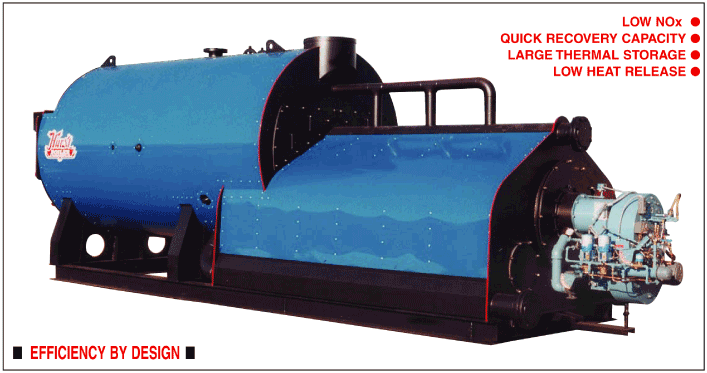
Fires on any liquid or gaseous fuel. | ||
Sizes from 100 to 2500 horsepower | ||
with pressures to 450 PSI. | ||
The Only Boiler with the Recovery of a Watertube and the Thermal Reserve of a Firetube... |
Inherently low heat release enhances firing performance to reach outputs and emissions requirements
not possible with other shell type boilers.
Designed, constructed and stamped
in accordance with the requirements
of the ASME Boiler Codes.
|
![]() |
![]() |
Inspected and registered with the National Board of Boiler & Pressure Vessel Inspectors. |

§ | Efficient 2-Pass Design | |
§ | Flexibility- Gas, Oil, Heavy Oil and Combination Gas/Oil | |
§ | ASME Code Constructed & Stamped for 15 PSI Steam/30 Water | |
§ | Registered with the National Board of Boiler Inspectors | |
§ | Competitively Priced, Easily maintained, Designed for Efficiency | |
§ | Large Furnace Volume for Ultimate Combustion Efficiency | |
§ | Unified Refractory Base Floor | |
§ | Steel Skids / Lifting Eyes | |
§ | Easy Access to fireside Surfaces | |
§ | Low Heat Release 5 Sq. Ft./HP. | |
§ | Ample Waterside Cleanout Openings | |
§ | Fully Automatic Operations | |
§ | U.L. Listed, Forced Draft Burners | |
§ | Hybrid (Water/Fire Tube) Design | |
§ | U.L. Listed Controls & Trim |
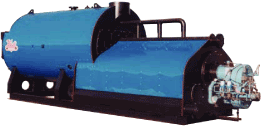
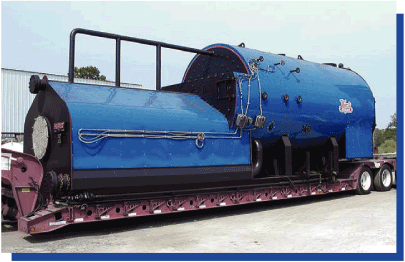
| Operating & limit pressure control | |
| Modulating pressure control (when appl.) | |
| Water column with gauge glass probe type combination low water cut-off & pump control (not shown) | |
| Probe type auxiliary low water cut-off with manual reset | |
| Water column drain valve | |
| Safety relief valve(s) per ASME Code | |
| Steam Gauge |
| Operating & limit temperature control | |
| Modulating temperature control (when appl.) | |
| Low water cut-off control with manual reset | |
| Combination pressure, temperature gauge | |
| Hot water return baffle for shock resistance | |
| Safety relief valve(s) per ASME Code | |
| Stack thermometer |

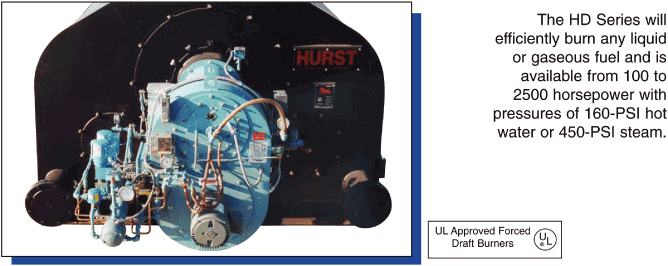
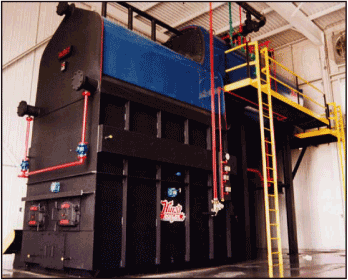
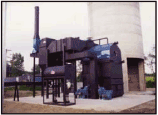
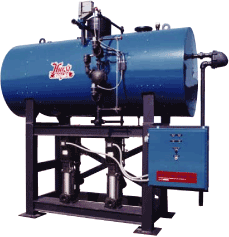
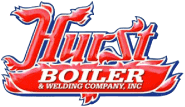
P. O. Drawer 529
|
Represented by: | |||
21971 Highway 319 N. |
||||
Coolidge, Georgia 31738 |
||||
1-877-994-8778 (Toll Free) |
||||
(229) 346-3545 (Tel.) |
||||
(229) 346-3874 (Fax.) |
||||
e-mail: info@hurstboiler.com
|
Revised 07/03 |
Coolidge, Georgia 31738
Phone: 229-346-3545 | Fax: 229-346-3874 |
WOOD WASTE FIRED STEAM BOILER
(10,350 POUNDS OF STEAM PER HOUR)
1250 ROBERTS BOULEVARD
KENNESAW, GEORGIA 30144
JOB SITE: SAVANNAH RIVER
1.
|
Scope of Equipment: | 300 Horsepower / 150 psig | ||
Design Wet Wood Fired | ||||
Boiler to include: | ||||
- Deaerator | ||||
- Oil back-up burner | ||||
- Combustion air pre-heater | ||||
- Stack, 100 free standing | ||||
- Recprocating floor, 6 section | ||||
- Cross-over conveyor with screen | ||||
2.
|
Fuel Requirements: | 11/2" x 21/2" x 5/8" or less in size and 50% by weight or less in moisture content. | ||
3.
|
Approximate Fuel Usage at Maximum Firing Rate: | 3200 lbs. per hour based on 50% moisture content. | ||
4.
|
Boiler Rating: | 300 Boiler horsepower (10,350 lbs. of steam per hour from and at 212o f) | ||
5.
|
Boiler Pressure: | 150 psig design. Maximum recommended operating pressure is 135 psig |
||
6.
|
Boiler Design: | High Pressure Hybrid (Fire Tube/Water Tube Design) Built in accordance with the ASME Code |
ESI, INCORPORATED.
1. | Boiler room/storage layout drawings for locating new equipment. | ||
2. | Foundation details for proposed waste fired boiler based on 2000 PSF soil conditions. | ||
3. | Assistance in completing and filing of boilers environmental emission permit. | ||
4. | All required installation prints and specifications required to install the proposed equipment. | ||
5. | Two (2) sets of operating and maintenance manuals. |
ESI, INCORPORATED.
1. | Check out of all system components to assure proper rotation, alignment, sequencing, function, etc. | |
2. | Start-up of the system to test operation of controls, conveyors and other related equipment. | |
3. | Adjustment of controls to provide efficient operation of all boiler functions | |
4. | Start-up of the equipment with mill personnel to familiarize them with proper operation and maintenance procedure. | |
5. | Hurst Boiler & Welding Co., Inc.s personnel will be on site until all equipment is started-up and operating to the satisfaction of the Purchaser. Start-up services are a part of this proposal, and no additional charges will be billed to the purchaser for these services. | |
6. | Hurst Boiler & Welding Co., Inc. start-up personnel will be on site for a minimum of ten days. |
ESI, INCORPORATED.
1. | Metering bin / retort type underfed stoker complete with AC-type variable speed controller | |
2. | Cast-iron grates with angle and tee bars | |
3. | Substochiometric combustion air system to include: |
| Dual belt driven blowers with VFD, TEFC motor and OSHA belt guard | ||
| Zoned undergrate plenum. |
4. | Gasification chamber casing to include: |
| Furnace front of 1/2" steel plate | ||
| Furnace sides and rear of 1/4" steel plate reinforced with angle and channel irons |
5. | Chamber lining of: |
| 9" refractory wall, and radiant arch with a service temperature of: 3000F | ||
| 2" M block, service temperature of: 1900F | ||
| 2" mineral wool, service temperature: 1200F |
6. | Two air cooled observation ports with heat shields and tinted site glasses | |
7. | Two cast iron overfire access doors with heat shield and lockable handles | |
8. | Undergrate access doors | |
9. | Skids and support assembly. |
ESI, INCORPORATED.
1. | Combustion air system to include: |
| Belt driven blower with VFD, TEFC motor and OSHA belt guard | ||
| Prefabricated combustion air duct work for interconnection of blower to zoned air port plenum. |
2. | Combustion chamber casing complete with the following: |
| Casing of 1/4" steel plate with inlet and outlet flanges | ||
| Angle and channel iron reinforcement |
3. | Chamber lining of: |
| 9" refractory wall, and radiant arch with a service temperature: 3000F | ||
| 2" M block, service temperature: 1900F | ||
| 2" mineral, wool, service temperature: 1200F. |
ESI, INCORPORATED.
1. | The generator (firetube) section includes: |
| Front and rear smoke boxes complete with twin hinged air tight doors. Doors internally insulated and incorporate abrasion resistant shield on the interior of the doors. | ||
| Steam, water inspection and blowdown openings. | ||
| Lugs for connecting support structure. |
2. | The radiant (watertube) section includes: |
| 1/2" front plate and rear plate. | ||
| Support assembly for attaching to combustion chamber casing. | ||
| Blowdown openings on each lower drum. | ||
| Flanged inspection openings on the end of each drum. |
3. | Both the generator and radiant sections of the Hybrid boiler are insulated with 2 of high density fiberglass and clad with 22 gauge Paint-Grip zinc coated steel jacket material and galvanized screws for attachment and joining |
4. | Pressure vessel manufactured by Hurst Boiler & Welding Co., Inc. and guaranteed to be free from defects in materials and workmanship for a period of one year. |
ESI, INCORPORATED.
1. | Relief valves per ASME Code |
2. | Boiler bottom blowdown valves |
| Two (2) in generator section, quick-opening | ||
| Two (2) in radiant section, quick-opening | ||
| One (1) slow opening |
3. | Surface blowdown valves consisting of one (1) needle and one (1) check | |
4. | Main steam valving to include: angle non-return, pp spool and gate per ASME. | |
5. | Steam line necessary for the installation of the steam flow transmitter, approximately 20' | |
6. | Chemical feed valves consisting of one (1) gate and two (2) check valves | |
7. | Steam pressure gauge with pigtail and gauge cock. | |
8. | Boiler feedwater valving to include: globe valve, two (2) check valves and stop valve. | |
9. | Low water limits: |
| Primary: Probe type with tricocks, gauge glass and pump controller | ||
| Secondary: Probe type. (Probe type high water cut-off) |
10. | Pressure limits include: |
| Opening limit | ||
| High pressure limit | ||
| Low pressure limit | ||
| 4-20 milliamp pressure transmitter for fuel feed /combination air modulation. |
ESI, INCORPORATED.
11. | Blowdown separator built in accordance with the ASME Code to include: |
| Blowdown inlet (screwed) | ||
| Drain (flanged) | ||
| Vent (flanged) | ||
| Exhaust stack (flanged) to vent above building roof line. |
12. | Access platforms, ladders and one set of stairs will be provided to access: |
| Rear smoke box | ||
| Water column | ||
| Feedwater valve train | ||
| Main steam valving | ||
| Induced draft fan |
13. | Soot blowers, fixed zone, air with necessary piping, header and valving. | |
14. | Necessary pipe and fittings for the installation of the above trim. | |
15. | Steam flow meter with totalizer and transmitter. |
ESI, INCORPORATED.
1. | Flanged breeching, prefabricated of angle iron reinforced 3/16 steel plate for routing flue gas from boiler to multi-clone | |
2. | Combustion air preheater, vertical configuration, oversized to include |
| Collection hopper with flanged inlet, outlet and access door | ||
| Rotary airlock ash discharge valve with drive |
3. | Dry mechanical multiple cyclone flyash arrestor with 9 diameter clones to include: |
| Collection hopper with flanged inlet, outlet and access door | ||
| Rotary airlock ash discharge valve with drive |
4. | Flyash conveyor to transfer flyash to boiler room exterior | |
5. | Flanged transition of angle iron reinforced 3/16 steel plate for routing flue gas from multicyclone to induced draft fan | |
6. | Centrifugal type induced draft fan designed for combustion air service complete with: |
| Pillow block roller bearings (located outside hot gas stream) | ||
| Heavy duty shaft with heat slinger | ||
| Variable frequency drive | ||
| TEFC motor, belt drive and OSHA belt guard |
7. | Ground mounted induced draft fan and 100 self-supporting stack with EPA stack test ports. |
ESI, INCORPORATED.
1. | 12' support structure | |
2. | Factory insulation and jacketing | |
3. | Boiler feedwater pumps, two each for proposed boiler to include: |
| Electric motors | ||
| Variable frequency drive | ||
| Suction manifold | ||
| Pump suction piping, isolation valving and strainers | ||
| Pump discharge manifold with isolation valving and pressure gauges |
4. | Water gauge glass set, pressure gauge and thermometer | |
5. | Over flow trap | |
6. | McDonnell Miller high and low water switches | |
7. | ASME safety relief valves | |
8. | Vent and vacuum breaker | |
9. | Steam pressure reducing valve, Fisher pneumatic globe valve | |
10. | Freshwater make-up valve, Fisher pneumatic globe valve | |
11. | Tank drain valve |
ESI, INCORPORATED.
1. | Six section reciprocating floor to include: |
| Hydraulic cylinders | ||
| Hoses and fittings |
2. | Concrete imbediment for mounting hydraulic cylinders | |
3. | Hydraulic power unit with reservoir and valve block | |
4. | Vibrating cross-over conveyor with fuel screening section | |
5. | Incline chain conveyor |
| WD110 chain | ||
| UHMW ware plate | ||
| Shafts, sprockets, bearings and drive |
ESI, INCORPORATED.
An integrated control system housed in a free standing, pre wired panel for automatic operation will be provided for each boiler to include: |
1. | Control Panel |
| NEMA 12 control enclosure | ||
| Enclosure prefabricated of 10 gauge plate | ||
| Primed and painted interior and exterior. |
2. | Main disconnect | |
3. | Control voltage transformer | |
4. | Cooling as required, air to air exchanger | |
5. | Allen Bradley MicroLogix / 1756 System processor | |
6. | Power supply Rack Communication modules | |
7. | Input and output modules | |
8. | Allen Bradley RS View runtime package to represent system required parameters and variables running on a desktop computer. Operator interface is through this interface. | |
9. | Allen Bradley PowerFlex 70 and 700 480v variable frequency drives | |
10. | Input line reactors | |
11. | DeviceNet communication to processor | |
12. | Variable frequency drives will be provided for: |
| Metering bin drive | ||
| Underfire combustion air fan | ||
| Overfire combustion air fan | ||
| Induced draft fan |
13. | Local motor disconnects are provided at each motor |
ESI, INCORPORATED.
14. | Control enclosure is completely wired, shop tested and Includes terminal strip terminations, ready for connection to field devices | |
15. | Control system incorporates equipment mounted, 4-20 milliamp transmitters for controlling/monitoring: |
| Steam flow | ||
| Steam pressure | ||
| Boiler water level | ||
| Furnace temperature |
16. | Limits and Alarms: |
| Primary boiler low water | Limit/Alarm | Automatic Reset | |||
| Secondary boiler low water | Limit/Alarm | Manual Reset | |||
| High water cut-off | Limit/Alarm | Automatic Reset | |||
| Low boiler steam pressure | Alarm | Automatic Reset | |||
| High boiler steam pressure | Limit/Alarm | Automatic Reset | |||
| Low draft (Furnace) | Limit/Alarm | Automatic Reset | |||
| High temperature (Furnace) | Limit/Alarm | Automatic Reset |
17. | A separate feedwater pump panel will be provided for the proposed feedwater pumps to include motor controls |
ESI, INCORPORATED.
ESI, INCORPORATED.
TURBINE GENERATOR SET
PROJECT 10167 Rev 2
March 26, 2008
Turbine model | TMCE 25000A | |||||||||||||||
Load point | 1 | 2 | 3 | |||||||||||||
Power at generator output |
18,700 | 17,000 | 8,180 | KW | ||||||||||||
Inlet pressure |
850 | 850 | 850 | Psia | ||||||||||||
Inlet temperature |
825 | 825 | 825 | º F | ||||||||||||
Throttle flow |
240,000 | 240,000 | 240,000 | Lb/h | ||||||||||||
Extraction pressure |
385 | 385 | 385 | Psig | ||||||||||||
Extraction flow |
80,000 | 100,000 | 195,000 | Lb/h | ||||||||||||
Exhaust pressure |
3.3 | 2.7 | 1.5 | HgA | ||||||||||||
Exhaust flow |
160,000 | 140,000 | 45,000 | Lb/h | ||||||||||||
Turbine speed |
6000 | 6000 | 6000 | Rpm | ||||||||||||
Generator speed |
1800 | 1800 | 1800 | Rpm | ||||||||||||
Tolerance |
1 | | | % |
1) | Rotation direction seen from turbine to generator | |
2) | Gearbox efficiency (approx.): 98,5% Generator efficiency 97,6% (approx. WEG) |
Turbine Materials |
||
Steam chest
|
ASTM A 217 WC1 | |
Turbine Casing
|
ASTM A 217 WC1 | |
Exhaust casing
|
ASTM A 516 Gr.60 | |
Rotor (integral)
|
SAE 4340 | |
Nozzles
|
AISI 420 | |
Blades
|
AISI 420 | |
Internal parts of valves
|
SAE 4340 | |
Bearing lining
|
Babbitt (white metal) | |
Steam piping / Oil piping
|
ASTM A 106 / AISI 304 (*) |
(*) | Oil piping will be supplied in SS for pressure and return lines |
Based on IEC standard, publishing 45:
Inlet steam pressure: 880 psig
Inlet steam temperature: 839,4 ºF
Inlet | Extraction | Outlet | ||||
DN (in) |
10 | 10 | 95 X 38 | |||
PN (psi) |
900 | 600 | 30 | |||
Norma |
ANSI B 16.5 | ANSI B 16.5 | | |||
Direction |
Right - Downwards (*) | Up or Down | Up or Down |
(*) Seen from the turbine to the generator |
§ | Overspeed (mechanical / electronic) | |
§ | 3-way solenoid valve (electric) | |
§ | Manual trip | |
§ | Excessive radial bearings vibration | |
§ | Excessive axial displacement | |
§ | High bearing metal temperature |
Woodward CPC (2)
Servo-motors by TGM
Magnetic pick-ups (3)
Gearbox |
||
Type
|
Parallel shafts, horizontally split casing | |
Input power
|
19240 kW | |
Input/Output speed
|
6000/1800 rpm | |
Gearing type
|
Double-helical | |
Teeth
|
Case hardened and grounded | |
Bearing
|
Babbitt | |
Casing
|
Cast iron | |
Service Factor (AGMA)
|
1.3 | |
Turning Gear |
||
Type
|
Electric | |
Power
|
15 kW (approx.) | |
Engage / disengage
|
Manual / automatic | |
Couplings |
||
High Speed |
||
Type |
Disk | |
Speed
|
6000 rpm | |
Lubrication
|
Not required | |
Protection
|
SAE 1020 plate | |
Low Speed |
||
Type |
Rigid | |
Speed
|
1800 rpm | |
Lubrication
|
Not required | |
Protection
|
SAE 1020 plate |
§ Type
|
Worm | |
§ Oil pressure
|
10 kgf/cm 2 | |
§ Driven by
|
Low speed gearbox shaft | |
§ Oil specification
|
ISO VG 68 | |
Auxiliary oil pump |
||
§ Type
|
Worm | |
§ Oil pressure
|
10 kgf/cm 2 | |
§ Driven by
|
Electric motor | |
§ Current type
|
A/C | |
§ Frequency
|
60 Hz | |
§ Speed
|
1760 rpm | |
§ Configuration
|
B 3 | |
§ Protection
|
IP 55 | |
Emergency oil pump |
||
§ Type
|
Gear | |
§ Oil pressure
|
1,5 kgf/cm 2 | |
§ Driven by
|
Electric motor | |
§ Current type
|
DC | |
§ Speed
|
1800 rpm | |
Oil cooler duplex (Standard TGM) |
||
§ Cooling water temperature inlet (max.)
|
86 ºF (*) | |
§ Cooling water temperature outlet
|
95 ºF | |
§ Oil inlet temperature
|
140 ºF | |
§ Oil outlet temperature
|
113 ºF | |
§ Pressure drop
|
4 psig | |
§ Cooling water pressure
|
100 psig |
(*) | To be confirmed by the customer |
Materials |
||
§ Tubes
|
AISI 304 | |
§ Tubes sheets
|
ASTM A 285 Gr. C | |
§ Water chamber
|
ASTM A 285 Gr. C | |
§ Casing
|
ASTM A 285 Gr. C |
§ Type
|
Duplex | |
§ Strainer mesh
|
25 µm | |
§ Pressure drop
|
0,2 kgf/cm 2 | |
§ Strainer material
|
Stainless steel |
§ Oil type
|
ISO VG 68 | |
§ Material
|
Structural steel (carbon steel) |
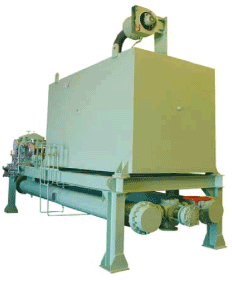
Measurement points | QT | LC | PA | AL | TR | |||||
Governing system |
||||||||||
Woodward governor 505 E |
1 | X | ||||||||
CPC |
2 | X | ||||||||
Magnetic Pick-ups |
3 | X | ||||||||
Steam System |
||||||||||
Inlet steam pressure |
1 | PIT | PI | |||||||
Wheel chamber pressure |
1 | PIT | PI | |||||||
Extraction pressure |
1 | PIT | PI | |||||||
Exhaust pressure |
1/1 | PIT/PS | PI | H | HH | |||||
Inlet steam temperature |
1 | TE | TI | |||||||
Extraction temperature |
1 | TE | TI | |||||||
Exhaust steam temperature |
1 | TE | TI | |||||||
Lubrication system |
||||||||||
Pressure after oil pumps |
1 | PIT | PI | |||||||
Oil pressure at gearbox inlet |
1 | PI | ||||||||
Lubrication oil pressure |
1/1 | PIT/PS | PI | LL | ||||||
Differential pressure in the oil filter |
1 | DPS | H | |||||||
Oil temperature before the oil cooler |
1 | TI | ||||||||
Oil temperature after the oil cooler |
1 | TE | TI | H | ||||||
Turbine bearing metal temperature (RTD Pt 100) |
4 | TE | TI | H | HH | |||||
Gearbox bearing metal temperature (RTD Pt 100) |
4 | TE | TI | H | HH | |||||
Control System |
||||||||||
Impulse oil pressure |
1/1 | PIT/PS | PI | L | ||||||
Control oil pressure |
1 | PIT | PI | |||||||
Others |
||||||||||
Manual trip |
1 | HV | HS | |||||||
Turbine trip indicator |
1 | ZS | ZI | X | ||||||
Turbine speed |
1 | SE | SI | HH | ||||||
Auxiliary oil pump motor (on-off) |
1 | HS | ||||||||
Oil tank low level |
1 | LE | LI | L | ||||||
Electronic overspeed system |
1 | SE | SI | H | HH | |||||
Radial vibration probes turbine |
4 | VE | VI | H | HH | |||||
Radial vibration probes gearbox |
8 | VE | VI | H | HH | |||||
Radial vibration probes generator |
4 | VE | VI | H | HH | |||||
Keyphasor |
1 | ZE | ZI | H | HH | |||||
Axial displacement turbine (probes by TGM) |
2 | ZE | ZI | H | HH |
PS: Pressure switch
DPS: Differential pressure switch
TR: Trip
HS: Manual Key
LC: Local
LI: Level indicator
LT: Level transmitter
PA: Panel
PI: Pressure indicator
PIT: Pressure transmitter
L: Low signal
LL: Very low signal
SI: Rotation indicator
SE: Rotation sensor
TE: Temperature sensor
TI: Temperature indicator
VI: Vibration indicator
VE: Vibration sensor
VT: Vibration transmitter
ZE: Displacement sensor
ZI: Displacement indicator
ZS: Limit switch
H: High signal
HH: Very high signal
HV: Hand Valve
Function | Voltage | Frequency | Observation | |||
Safety | 125 Vdc | |||||
Auxiliary for control panel | 220 Vac | 60 Hz | ||||
Instrumentation | 24 Vdc | |||||
Direct current | 24 Vdc | |||||
Auxiliary pump | 220/380/440 Vac | 60 Hz | ||||
Emergency pump | 125 Vdc |
Section #1 - Generator Section |
||
1 | Vacuum Breaker Element, 1200A 15kV 500mVA |
|
1 | Vacuum Breaker Compartment,1200A 5kV |
|
1 | Vacuum Breaker MOC/TOC Switch |
|
1 | Generator Voltage Transformer Drawout Tray |
|
1 | Generator Control Transformer Drawout Tray |
|
1 | Section, indoor vertical section |
|
1 | Section, main copper buswork |
|
2 | Voltage Transformers |
|
1 | Control Power Transformer, 3kVA |
|
3 | Current Transformers |
|
Section #2 - Bus VTs |
||
1 | Bus Voltage Transformer Drawout Tray |
|
1 | Section, indoor vertical section |
|
1 | Section, main copper buswork |
|
2 | Voltage Transformers |
|
1 | Set, space heaters and cabinet lamps |
|
1 | Set, breaker standard accessories |
|
1 | Sets, control wire, wiretags, terminal blocks, fuses |
|
Surge Cabinet | ||
1 | Vertical housing NEMA 4 Stainless Steel |
|
3 | Lightning Arrestors |
|
3 | Surge Capacitors |
|
1 | Space Heater |
|
1 | Cabinet Lamp |
|
1 | PT drawout tray |
|
1 | CPT drawout tray |
|
3 | voltage transformers |
|
1 | control transformer |
|
Neutral Grounding Resistor | ||
1 | NGR, 400A 10 Second, NEMA 4 Stainless Steel enclosure |
|
3 | Differential Current Transformers |
Turbine / Generator Control Panel | ||
NEMA 4 Stainless Steel vertical section w/vortex air cooler & |
||
1 | temperature controller |
|
1 | Woodward 505 Governor |
|
1 | Woodward SPM-D11/LSXR Synchronizer |
|
1 | Woodward Protech 203 Electronic Trip |
|
1 | Basler DECS-200 |
|
1 | GE SR-489 Multilin Generator Protection Relay |
|
1 | Lot, Test Blocks |
|
1 | Synchroscope |
|
1 | Lockout Relay |
|
16 | Auxiliary Relays |
|
1 | Lot, Control Switches |
|
1 | Lot, Relay Surge Suppressors |
|
1 | Space Heater |
|
1 | Thermostat |
|
1 | Interior Light |
|
1 | Interior Light Switch |
|
1 | Switch Generator Circuit Breaker Trip/Close |
|
1 | Switch Governor Speed Lower/N/Raise |
|
1 | Switch AVR Voltage Lower/N/Raise |
|
2 | 24VDC Power supply-20A (redundant) |
|
1 | Lot, Wire, Terminal blocks, fuses, fuseblocks |
|
1 | Lot, commissioning spare parts |
|
1 | Lot of Nameplates & Engraving |
|
1 | Lot of Pilot Lights & Pushbuttons |
|
1 | Lot of Meters (KW/Kvar/V/A, Frequency etc...) |
|
1 | Lot, miscellaneous controls, etc |
|
PLC Control Material |
||
1 | ControlLogix Processor, 64 MB CompactFlash (1756-L61)) |
|
1 | Backup Battery, (1756-BA1) |
|
1 | ControlLogix Chassis, 17 slot (1756-A17) |
|
1 | Controllogix Power supply, 75 Watts (1756-PA75/C) |
|
1 | Prosoft Modbus Interface Card (MV156-MCM) |
|
1 | Ethernet Interface Card (1756-ENBT) |
|
1 | 16-Channel Analog Input, single ended (1756-IF16) |
|
3 | 6-Channel RTD Input (1756-IR61) |
|
1 | 16-Input Card, AC (1756-IA16) |
2 | 16-channel input Card , DC (1756-IB16) |
|
3 | 16-Relay Output Card, Isolated (1756-OW161) |
|
8 | Removable Terminal Block, 36 point (1756-TBCH) |
|
4 | Removable Terminal Block, 20 point (1756-TBNH) |
|
4 | Extended Housing Terminal Block (1756-TBE) |
|
2 | DH-485 Interface Module (1761-NET-AIC) |
|
1 | PanelView+ 1000 w/Ethernet (2711P-T10C4A2) |
|
1 | RSViewME Software for HMI (9701-VWSTMENE) |
|
1 | Miscellaneous Communications Cables for HMI & PLC |
|
1 | Industrial Network Switch (Hirschmann RS2-4TX/1FX) |
|
Bently Nevada | ||
1 | 19" Rack, 14 slots (P/N 3500/05-01-00-00-00) |
|
1 | Rack Interface Module (P/N 3500/20-01-02-00) |
|
1 | Rack Power Supply, 120VAC & 24VDC (P/N 3500/15-01- 04-00) |
|
1 | Keyphasor Module (P/N 3500/25-01-01-00) |
|
5 | Proximity/Seismic Monitor Module (P/N 3500/42-01-00) |
|
2 | 4-Channel Relay Module (P/N 3500/32-01-00) |
|
1 | Communication Gateway, Modbus RS-485 (P/N 3500/92- 02-01) |
|
1 | 3-Channel Overspeed Protection System (P/N 3500/53- 03-00) |
Quantity |
: 01 | |
Model |
: SSW 1000 | |
Frame |
: 1000 | |
Output |
: 23125 kVA | |
Poles/ Nominal speed |
: 04 / 1800 rpm | |
Over Speed |
: 20% | |
Voltage |
: 13800 V | |
Frequency |
: 60 HZ | |
Power factor |
: 0,80 | |
Protection degree |
: IP-54 | |
Cooling system |
: Totally enclosed - 2 X 65% water-air cooled | |
(CACW) |
||
Mounting |
: B3 (Horizontal) | |
Environment |
: 40OC and 1000 m | |
Duty |
: S1 | |
Insulation class |
: F | |
Temperature rise |
: 80OC | |
Bearing type |
: Sleeve Bearing |
-(02) Bearing temperature detector (01 per bearing): PT-100
- Space heaters, 220 V, 600 Watts;
- Oil Flow Sight-Viewer
- Water Flow Viewer
- Water Flow detector in the water inlet (heat exchanger)
- Water leakage detector
- Water temperature detector inlet and outlet: PT-100
- Air temperature detector inlet and outlet: PT-100
- Grounding Brush
- Neutral connection box
- Air water cooling system, two heat exchangers for each generator.
- Water leakage detector
- Bently Nevada Probes (DE + NDE bearings). Installed by WEG but supplied by
steam turbine manufacturer.
NBR 5052 Synchronous machines.
NBR 5117 Synchronous machines.
ISO 1940 Balancing quality.
VDE 0530 Turning electrical machines.
NEMA MG-1 Part 32 and 33 Synchronous Generators.
Insulation Class | Temperature Class | Temperature rise ºC | ||
F | 155ºC | 105ºC max (or 80ºC) |
§ | TGM extraction/condensing steam turbine model TMCE 25000A for generator drive | ||
§ | Gearbox, parallel shafts, single stage, double helical type with tuning gear, s.f.= 1.3 | ||
§ | High/Low speed couplings with coupling guards | ||
§ | Complete oil unit for turbine, gearbox and generator including mechanical oil pump, auxiliary lube oil pump, emergency oil pump, twin oil filters, twin oil coolers, oil reservoir, and oil vapor extractor. Provided on skid. | ||
§ | Common baseplate for turbine and gearbox | ||
§ | CPC (2) + Magnetic Pick-Ups (3) | ||
§ | Probes for vibration and axial displacement of the TG set (19) factory mounted and wired to junction box | ||
§ | Junction boxes and wiring to JB (not UL listed but meet NEMA standards) | ||
§ | UL listed instruments / motors where possible | ||
§ | Turbine / generator control panel including: | ||
§ | Woodward 505 E governor | ||
§ | Woodward Protech 203 overspeed protection | ||
§ | Bently Nevada 3500 vibration system | ||
§ | Allen Bradley ControlLogix with HMI | ||
§ | Basler DEC 200 | ||
§ | GE SR-489 Multilin Generator Protection Relay | ||
§ | Auto Synchronization | ||
§ | Transmitters with mounting rack | ||
§ | RTDs factory mounted and wired to junction box | ||
§ | Painting according to TGM export plan | ||
§ | Manual steam drain valves | ||
§ | Visual indicators for returning lube oil from bearings | ||
§ | Weg TEWAC generator mounted on separate sole plate | ||
§ | Medium voltage switchgear including: | ||
§ | Circuit breaker panel | ||
§ | Neutral grounding resistor panel | ||
§ | Surge protection panel | ||
§ | Starter, batteries and charger for DC emergency oil pump | ||
§ | Export packing for Brazilian equipment | ||
§ | Customs and port handling charges | ||
§ | Freight and insurance to job site | ||
§ | Shop tests to manufacturers standards. Third party inspections not included. (*) | ||
§ | Steam sealing system Field piping by others | ||
§ | Installation, start up, and training supervision (See conditions) | ||
§ | Acoustic hood for turbine and gearbox (option) (supplied loose) | ||
§ | Spare parts for 2 year operation (option) |
(*) | In case of external inspection, hired by the customer, TGM will evaluate impacts of demands to its standard Inspections & Tests Plan. Relevant impacts such as costs and delivery time will be charged to the customer. |
§ | Inlet flange of the turbine emergency trip valve | |
§ | Inlet flange of the gland steam sealing system | |
§ | Exhaust flange of the turbine | |
§ | Outlet flange of the turbine extraction | |
§ | Inlet and outlet flanges of the extraction trip valve |
§ | Inlet flange of the oil cooler | |
§ | Outlet flange of the oil cooler | |
§ | Inlet & outlet flange of generator water cooling section |
§ | Junction boxes terminals | |
§ | Control panel terminals | |
§ | Switchgear panel terminals |
§ | Outlet flange of the drain valves |
§ | Inlet connections of the instruments/devices |
Supply & return connections of lube oil skid | ||
Supply & return connections on turbine / gear basplate | ||
Supply & return connections of generator bearings |
§ | Steam, condensate and cooling water lines and accessories/instrumentation (valves, supports, joints, insulation, condensate separator devices, etc...) out of the limits of supply; | |
§ | Civil works and foundation calculations; | |
§ | Overhead crane; | |
§ | Steam condenser and accessories/appurtenances; | |
§ | Cooling water tower and water circulating pumps | |
§ | Gland steam condenser, piping and accessories | |
§ | Fire protection systems; | |
§ | Electrical and mechanical interconnection out of the limits of supply; | |
§ | Utilities such as electric energy, water, compressed air, welding materials and others; | |
§ | Flushing oil and first lube oil filling; | |
§ | Stairways, scaffold, platforms and similar; | |
§ | Safety and control valves out of the limits of supply | |
§ | Anchor bolts set and leveler | |
§ | Explosion proof instruments / accessories | |
§ | Wiring between local junction boxes and control panel | |
§ | Wiring between generator and switchgear panels | |
§ | No-load running test | |
§ | Performance test | |
§ | Heat stability test | |
§ | High speed balancing | |
§ | Any special design, accessory and documentation (submittals) out of standard scope of supply | |
§ | Any other equipment not listed in this proposal |
Denomination | Requirement | Test according to | ||
Type of lube oil |
TD 68 | |||
Viscosity class ISO |
ISO VG 68 | DIN 51519 | ||
Nº (coordination) |
25 | |||
Cinematic viscosity |
65,5 mm 2/s (cSt) | DIN 51550 together with, | ||
at 40ºC |
8,7 mm 2/s (cSt) | DIN 51561 or DIN 51562 | ||
at 100ºC |
||||
Dynamic viscosity average at 40ºC |
65,5 x 10-3 Pas | |||
Viscosity index not less than |
95 | |||
Density at 15ºC not more than |
0,9 Kg/l | DIN 51757 | ||
Ignition point as per Cleveland not less then |
200ºC | DIN 51376 |
Denomination | Requirement | Test according to | ||
Pourpoint = or < |
-6ºC | DIN 51597 | ||
Neutralization index not to exceed |
(+) 0,1 mg KOH/g oil | DIN 51558 part I | ||
Saponification index not to exceed |
(+) 0,15mgKOH/g oil | DIN 51559 | ||
Ashes (oxide) not to exceed |
(+) 0,01% w/w | |||
Water |
g/100g | DIN 51582 | ||
Solid foreign matter below detectable levels |
g/100g | DIN 59592 | ||
Water separation capacity (max) |
300 s | DIN 51589 part I | ||
Water separation capacity at 50ºC (Max) |
5 min | DIN 51381 | ||
Corrosion effect on copper corrosion degree (Max) |
2....100 A3 | DIN 51759 (3h up to 100ºC) | ||
Corrosion protection (steel) |
0....A (corrosion free) | DIN 51585 | ||
Neutralization index increase after 1000 h |
2,0 mg KOH/g oil | DIN 51587 | ||
Capacity of specific load (gearbox) |
Normal test FZG | DIN 51354 (A/8, 3/90) | ||
6-7 degree | ASTM D 1947-68 | |||
IP166/65 |
(+) | When active substances are used the above values are higher. |
PH |
7 | |
Carbonic acid |
3 g/l | |
Carbonate hardness |
6°dH | |
Carbonate hardness for polymorph phosphates |
12°dH | |
Non-carbonate hardness |
80°dH | |
Clorets |
400 mg/l | |
Sulfates |
500 mg/l | |
Total salt |
3000 mg/l | |
Total alkalinity |
15 mgl/l | |
Silic acid |
200 mg/l | |
Particles in suspension |
10 mg/l |
SRS Engineering Standards Manual
|
Manual: WSRC-TM-95-1 | |||
Attachment 1
|
Date: 9/13/07 | Page 1 of 7 | ||
National Codes and Standards for Engineering/Design Tasks Matrix
|
ENGINEERING STANDARDS BOARD | Revision 17 |
Approved by:
|
Ken Stevens, Signature on File | |||
GENERAL SERVICE | PRODUCTION | SAFETY | ||||||||
APPLICATION | COMPONENT | See Note | SUPPORT | SIGNIFICANT | SAFETY CLASS | |||||
ENVIRONMENTAL QUALIFICATIONS |
None | IEEE-323 | ||||||||
SEISMIC QUALIFICATIONS |
EQUIPMENT, COMPONENTS |
IBC |
Applicable national codes and standards are listed in SRS Engineering Standard 01061 (if seismic qualification is required) | |||||||
CHEMICAL & TOXICOLOGICAL HAZARDS | OSHA, AICHE Safety Standards, API Safety Standards, ACGIH Requirements, NEPA* | |||||||||
N/A |
||||||||||
PRESSURE VESSELS, all services as defined in the ASME BPV Code |
ASME VIII-2004 Div. 1 or Div. 2 * | Yes | ||||||||
POWER BOILERS | ASME I-2004* | Yes | ||||||||
TRANSPORTATION PACKAGING | 49 CFR | N/A | ||||||||
HEATING BOILERS | ASME IV-2004* | N/A | ||||||||
PROCESS EQUIPMENT VESSELS & TANKS |
FIBER-REINFORCED PLASTIC PRESSURE VESSELS |
ASME X-2004* API-12P |
N/A | |||||||
STORAGE TANKS | API-620, ANSI/ASME B96.1 (Aluminum Alloy)* | N/A | ||||||||
WATER STORAGE TANKS | AWWA D-100* | N/A | ||||||||
PROCESS TANKS FOR | API-620, API-650, | API-650 and NFPA-30 | ||||||||
FLAMMABLE LIQUIDS | UL-142 (above ground), NFPA 30, NFPA 326 | |||||||||
PETROLEUM STORAGE TANKS | API-650* | API-650 | ||||||||
UL-58 and UL-1316 (under ground) | ||||||||||
CHEMICAL PROCESS PUMPS | ANSI/ASME B73, 1M & 2M, Hydraulic Institute Standards* | |||||||||
API-674, API-675, ASME B73.5M N/A | ||||||||||
PROCESS EQUIPMENT PUMPS |
POTABLE & SANITARY WATER PUMPS | AWWA E101* | This standard has been withdrawn | |||||||
FUEL OIL SERVICES PUMPS | API-610* | No, N/A | ||||||||
OTHER PROCESS SERVICE PUMPS |
Hydraulic Institute Standards, API, ASME * | No |
* | Codes and standards listed in the lower classifications are also requirements for the higher classifications. Where requirements in the lower classifications conflict with requirements in the higher classifications, the more restrictive requirement governs. |
SRS Engineering Standards Manual
|
Manual: WSRC-TM-95-1 | |||
Attachment 1
|
Date: 9/13/07 | Page 2 of 7 | ||
National Codes and Standards for Engineering/Design Tasks Matrix
|
ENGINEERING STANDARDS BOARD | Revision 17 |
GENERAL SERVICE | PRODUCTION | SAFETY | ||||||||
APPLICATION | COMPONENT | See Note | SUPPORT | SIGNIFICANT | SAFETY CLASS | |||||
POWER SYSTEMS (PIPING & VALVES) |
ASME B31.1-2001* | Yes | ||||||||
PROCESS SYSTEMS (PIPING & VALVES) |
ASME B31.3-2002 and B31.3 is for process |
No using B31.1 since it is applicable to power plants | ||||||||
Clarification in the application of these codes and standards is provided in SRS Engineering Standard 15060 (WSRC-TM-95-1) | ||||||||||
No | ||||||||||
PIPING & VALVES
|
BUILDING SERVICES (PIPING & VALVES) |
ASME B31.3-2002 or B31.9-2004* | No | |||||||
WATER DISTRIBUTION SERVICES (PIPING & VALVES) | AWWA C Series* | No using International Plumbing Code | ||||||||
REFRIGERATION PIPING | ASME B31.3-2002 or B31.5-2001 | N/A | ||||||||
OTHER BASIC CODES & | AWWA* | No | ||||||||
STANDARDS | API, ASME I-2004 | No and Yes as applicable | ||||||||
(PIPING & VALVES) | ASME B31.5-2001 | N/A | ||||||||
PLUMBING
|
PLUMBING SYSTEMS in infra-structure facilities |
International Plumbing Coe (IPC) * | Yes | |||||||
PROCESS EQUIPMENT GENERAL |
MOISTURE SEPARATORS OIL LUBRICATORS |
ANSI/B93.114M (restricted use of nonmetallic bowls)* | N/A, see comment | |||||||
GLOVE BOXES | NFPA 801, NFPA 45, NFPA 69, AGS-G001-1998* | |||||||||
AGS-G003-1998, ANSI/ASTM C852 | N/A | |||||||||
STRUCTURAL | GENERAL DESIGN | Applicable national codes and standards are listed in SRS Engineering Standard 01060. No IBC | ||||||||
CIVIL | GENERAL DESIGN | Applicable national codes and standards are listed in SRS Engineering Standard 01060. No IBC | ||||||||
SURVEYING | FGDC-STD-007.4 (Federal Geographic Data Committee) | No | ||||||||
GENERAL DESIGN | OSHA, NFPA 101, 220 & 221, NRCA* | Yes International Building Code & International Fire Code | ||||||||
ARCHITECTURAL | PHYSICALLY HANDICAPPED | UFAS* | No, except on administration building | |||||||
BUILDING CODE | International Building Code (IBC)* | Yes |
* | Codes and standards listed in the lower classifications are also requirements for the higher classifications. Where requirements in the lower classifications conflict with requirements in the higher classifications, the more restrictive requirement governs. |
SRS Engineering Standards Manual
|
Manual: WSRC-TM-95-1 | |||
Attachment 1
|
Date: 9/13/07 | Page 3 of 7 | ||
National Codes and Standards for Engineering/Design Tasks Matrix
|
ENGINEERING STANDARDS BOARD | Revision 17 |
GENERAL SERVICE | PRODUCTION | SAFETY | ||||||||
APPLICATION | COMPONENT | See Note | SUPPORT | SIGNIFICANT | SAFETY CLASS | |||||
MECHANICAL HANDLING | CRANES | ASE NOG-1 | ||||||||
EQUIPMENT | CMAA 70, CMAA 74, CMAA III-5, 11, 12 and 17; ASME B30.2, B30.11* No | |||||||||
OTHER HANDLING EQUIPMENT | AISC* ANSI N14.6 |
|||||||||
GENERAL FIRE PROTECTION | NFPA Fire Codes and Standards, Building Code (IBC), Uniform Fire Code, 29-CFR-1910 | |||||||||
For exceptions to these codes and standards refer to Standard 01120, Attachment 1* | Yes | |||||||||
AUTOMATIC SPRINKLER | NFPA 13, 15, 25, 72, Building Code (IBC)* | Yes | ||||||||
SYSTEMS | ||||||||||
WATER MIST SYSTEMS | NFPA 72, 750, Building Code (IBC)* | Yes | ||||||||
STANDPIPE SYSTEMS | NFPA 14, Building Code (IBC)* | Yes | ||||||||
FOAM SYSTEMS | NFPA 11, 11A, 16, 18, Building Code (IBC)* | Yes | ||||||||
FIRE PUMPS | NFPA 20, 25, 30, 70-2005, 72, Building Code (IBC)* | Yes | ||||||||
WATER SUPPLIES | NFPA 13, 20, 22, 24 291, 1142, Building Code (IBC)* | 1142 does not apply | ||||||||
WATER DISTRIBUTION AND FIRE | NFPA 24, 25, 1141, 1963, Building Code (IBC)* | Yes | ||||||||
HOSE | ||||||||||
LIQUID RUN-OFF CONTROL | NFPA 30, 70-2005, 801, Building Code (IBC)* | 801 does not apply. Additional, 850 will be used | ||||||||
GASEOUS FIRE SUPPRESSION | NFPA 12, 2001, Building Code (IBC)* | Yes | ||||||||
SYSTEMS | ||||||||||
FIRE PROTECTION SYSTEMS | CHEMICAL FIRE SUPPRESSION | NFPA 17, 17A, 72, 96, Building Code (IBC)* | 96 does not apply | |||||||
FIRE ALARM & DETECTION | NFPA 70-2005, 72, 90A, 101, 170, 801, UL 268A, Building Code (IBC)* not apply | No to UL 268A, 801 does | ||||||||
LIFE SAFETY | NFPA 70-2005, 101, 110, 111, Building Code (IBC)* | |||||||||
FIRE EXTINGUISERS | 29-CFR-1910.57, NFPA 10, 30, 51B, 95, Building Code (IBC)* | Yes | ||||||||
CONSTRUCTION SITES | 29-CFR-1926 SubPart F, NFPA 1, 241, Building Code (IBC)* | Yes | ||||||||
PERMANENT STRUCTURES | NFPA 220, Building Code (IBC)* | Yes | ||||||||
TEMPORARY BUILDINGS | Building Code (IBC)* | Yes | ||||||||
FIRE EXPOSURE PROTECTION | NFPA 1, 80a, 1144, Building Code (IBC)* | 1142 does not apply | ||||||||
VENTILATION SYSTEMS | NFPA 90A, 90B, 91, 92A, 204M, 601, UL 586, UL 900, Building Code (IBC)* | No to UL 586 & UL 900 | ||||||||
FIRE RATED CONSTRUCTION | NFPA 80A, 90A, 101, 220, 221, Building Code (IBC)* | |||||||||
Building Code (IBC) (Area Separation) | ||||||||||
Building Code (IBC) (Occupation Separation) | Yes | |||||||||
NFPA 80 | ||||||||||
STRUCTURAL DESIGN | NFPA 220, Building Code (IBC)* | Yes | ||||||||
CABLE INSTALLATIONS | NFPA 13, 70-2005, 70B, 70E-2004, 262, Building Code (IBC)* | Yes | ||||||||
COOLING TOWERS | NFPA 214, Building Code (IBC)* | Yes |
* | Codes and standards listed in the lower classifications are also requirements for the higher classifications. Where requirements in the lower classifications conflict with requirements in the higher classifications, the more restrictive requirement governs. |
SRS Engineering Standards Manual
|
Manual: WSRC-TM-95-1 | |||
Attachment 1
|
Date: 9/13/07 | Page 4 of 7 | ||
National Codes and Standards for Engineering/Design Tasks Matrix
|
ENGINEERING STANDARDS BOARD | Revision 17 |
GENERAL SERVICE | PRODUCTION | SAFETY | ||||||||
APPLICATION | COMPONENT | See Note | SUPPORT | SIGNIFICANT | SAFETY CLASS | |||||
ELECTRONIC COMPUTER/DATA PROCESSING SYSTEMS | NFPA 75* | Yes | ||||||||
ELECTRICAL TRANSFORMERS | NFPA 70-2005, Building Code (IBC)* | Yes | ||||||||
EXPLOSIVES | NFPA 68,69, 70-2005, 495, 498, 780, Building Code (IBC) | ATF 5400 | ||||||||
27-CFR, Parts 55 & 181 49-CFR, Parts 100 to 199 | Title 18 USC 40* | N/A | ||||||||
GLOVEBOXES, HOT CELLS, HOODS AND CANYONS | NFPA 45, 69, 90A, 91, 801 Building Code (IBC)* | N/A | ||||||||
HAZARDOUS MATERIALS | NFPA 30, 30B, 55, 58, 59A, 704, 801, Building Code (IBC)* | 30B, 58, 59A & 801 does not apply | ||||||||
FIRE PROTECTION SYSTEMS | LABORATORIES | NFPA 45, 801, Building Code (IBC)* | N/A | |||||||
LASERS | NFPA 70-2005, 79, 115, 21-CFR 1040, ANSI Z136.1-2000* | N/A | ||||||||
PRYOPHORIC MATERIALS & COMBUSTIBLE METALS | NFPA 68, 69, 480, 481, 482, 651, 801, Building Code (IBC)* | N/A | ||||||||
Record Storage | NFPA 232* | Yes | ||||||||
ABANDONED, SHUTDOWN, or DEACTIVATED BUILDINGS | Abandoned Facilities & Facilities undergoing D&D NFPA 801 | N/A | ||||||||
FIRE SYSTEM TESTING | Per NFPA installation codes and standards except as revised in the S/RIDs NFPA 25 & 72 | Per NFPA installation codes and standards unless permitted by AB documents to allow S/RIDs modified test frequencies | ||||||||
NFPA 37, 70-2005, 70E-2004, 101, 110, 111, 708 & 496 | IEEE-577* | IEEE-308, 336, 338 IEEE-379, 384, 603 |
||||||||
ANSI/IEEE-C2, NEMA-C84.1, NEMA ICS ASHRAE-90 | ||||||||||
SYSTEM DESIGN | IES Lighting Handbook | |||||||||
ELECTRICAL SYSTEMS | IEEE Series C37, C57, C62 | |||||||||
IEEE-141, 242, 739, 399, 446, 450, 484, 485, 493 | NFPA Only | |||||||||
IEEE-1015 | ||||||||||
UL-508, 96 & 96A* | ||||||||||
GROUNDING & LIGHTNING PROTECTION | ANSI/IEEE-C2, NFPA 70-2005, 780 IEEE-80, IEEE-142, IEEE-1050, IEEE-1100* |
NFPA Only |
* | Codes and standards listed in the lower classifications are also requirements for the higher classifications. Where requirements in the lower classifications conflict with requirements in the higher classifications, the more restrictive requirement governs. |
SRS Engineering Standards Manual
|
Manual: WSRC-TM-95-1 | |||
Attachment 1
|
Date: 9/13/07 | Page 5 of 7 | ||
National Codes and Standards for Engineering/Design Tasks Matrix
|
ENGINEERING STANDARDS BOARD | Revision 17 |
GENERAL SERVICE | PRODUCTION | SAFETY | ||||||||
APPLICATION | COMPONENT | See Note | SUPPORT | SIGNIFICANT | SAFETY CLASS | |||||
AIR FLOW & CONTROL | S 29 CFR 1910 Subparts G & H* | |||||||||
NFPA 90A, 90B & 91 | As required by IFC & International Mechanical Code | |||||||||
AIR HEATERS | Industry Standards* | ASME AG-1 | ||||||||
NFPA As required by IFC & International Mechanical Code | ||||||||||
AIR HANDLING UNITS (HVAC only) |
ARI 430* As required by IFC & International Mechanical Code | ASME AG-1 | ||||||||
FILTER HOUSINGS (NATS only) |
ASME N509* As required by IFC & International Mechanical Code | ASME AG-1 | ||||||||
HVAC EQUIPMENT | DAMPERS | SMACNA Standards, ASME N509, NFPA 90A, UL 555 & 555S | ASME AG-1 | |||||||
and | NFPA 801 (NATS only)* As required by IFC & Inter Mechanical Code | |||||||||
NUCLEAR AIR | DUCTWORK | SMACNA Standards* As required by IFC & International Mechanical Code | ||||||||
TREATMENT | FANS | AMCA* As required by IFC & International Mechanical Code | ||||||||
SYSTEMS |
||||||||||
(NATS) EQUIPMENT (Installed in Nuclear Facilities) |
FILTERS | ASHRAE (HVAC only), ASME N509* The use of ASME AG-1 is required for all HEPA filters that fall within the requirements of Engineering Standard 15888 |
ASME AG-1 As required by IFC & International Mechanical Code |
|||||||
ADSORBERS (NATS only) |
ASME N509* | N/A | ASME AG-1 | |||||||
DUCT INSULATION | ASHRAE Fundamentals Handbook, Chapter 26, insulation of Mechanical Systems | |||||||||
As required by IFC & International Mechanical Code | ||||||||||
REFRIGERATION UNITS | ARI 450* | N/A | ASME AG-1 | |||||||
(HVAC only) COILS |
ARI 410* | N/A | ASME AG-1 |
* | Codes and standards listed in the lower classifications are also requirements for the higher classifications. Where requirements in the lower classifications conflict with requirements in the higher classifications, the more restrictive requirement governs. |
SRS Engineering Standards Manual
|
Manual: WSRC-TM-95-1 | |||
Attachment 1
|
Date: 9/13/07 | Page 6 of 7 | ||
National Codes and Standards for Engineering/Design Tasks Matrix
|
ENGINEERING STANDARDS BOARD | Revision 17 |
GENERAL SERVICE | PRODUCTION | SAFETY | ||||||||||||
APPLICATION | COMPONENT | See Note | SUPPORT | SIGNIFICANT | SAFETY CLASS | |||||||||
COATINGS | SSPC for above ground steel * | No to NACE | ||||||||||||
NACE for concrete & underground steel | ||||||||||||||
NDE | ASME V-2004, ASNT, ASME B31.1-2001, B31.3-2002, B&PV Code-2004, * | AMSE V, ASME B31.1 and AWS | ||||||||||||
API, AWS, AWWA, ASTM Volume 03.03 | ||||||||||||||
MATERIALS | GASKETS, PACKAGING, etc. | ANSI B16.5, B1620, B16.21, DIN 3535 Part 4 | ||||||||||||
ASTM D149, D792, D1708, D2000, F36, F37B, F38, F104, F146, F152, F433 | ||||||||||||||
ASME Section VIII-2004 Div. 1 for m and y data * | Yes | |||||||||||||
CORROSION EVALUATION | ASTM A262, A763, G28, NACE * | No | ||||||||||||
INSULATION | For materials specification & testing ASTM Volume 04.06 | Yes | ||||||||||||
For selection & application None | ||||||||||||||
MATERIAL | ||||||||||||||
Steel | AWS D1.1, (Alternate ASME Section IX-2004) * | Yes | ||||||||||||
STRUCTURAL | Aluminum | AWS D1.2, (Alternate ASME Section IX-2004) * | Yes | |||||||||||
Sheet Steel | AWS D1.3, (Alternate ASME Section IX-2004) * | Yes | ||||||||||||
Stainless Steel | AWS D1.6, (Alternate ASME Section IX-2004) * | Yes | ||||||||||||
HVAC | MATERIAL | AWS D9.1, (Alternate ASME Section IX-2004) * | Yes | |||||||||||
Sheet Metal | ||||||||||||||
METALLIC | ||||||||||||||
MATERIALS | Power | ASME B31.1-2001 * | Yes | |||||||||||
WELDING & JOINING
|
Process | ASME B31.3-2002, (also see Standard 15060) * | No B31.1 | |||||||||||
PIPING | Refrigeration | ASME B31.5-2001 or B31.3-2002 * | N/A | |||||||||||
Bldg Services | ASME B31.9-2004 or B31.3-2002 * | No B31.1 | ||||||||||||
Fire Protection | NFPA, ASME B31.1-2001 * | Yes | ||||||||||||
Non-Metallic | ASME B31.3-2002 (also see Standard 15060) * | Yes | ||||||||||||
Copper-Solder | Copper Tube Handbook * | No | ||||||||||||
PRESSURE VESSELS | ASME Section VIII-2004, ASME Section I-2004 * | Yes | ||||||||||||
TANKS | API, ASME * | Yes | ||||||||||||
WELDING SAFETY | ANSI Z49.1-2005 * | Yes |
* | Codes and standards listed in the lower classifications are also requirements for the higher classifications. Where requirements in the lower classifications conflict with requirements in the higher classifications, the more restrictive requirement governs. |
SRS Engineering Standards Manual
|
Manual: WSRC-TM-95-1 | |||
Attachment 1
|
Date: 9/13/07 | Page 7 of 7 | ||
National Codes and Standards for Engineering/Design Tasks Matrix
|
ENGINEERING STANDARDS BOARD | Revision 17 |
GENERAL SERVICE | PRODUCTION | SAFETY | ||||||||
APPLICATION | COMPONENT | See Note | SUPPORT | SIGNIFICANT | SAFETY CLASS | |||||
TELECOMMUNICATIONS SYSTEMS | PATHWAYS AND SPACES | ANSI/TIA/EIA 569-B, ANSI/TIA/EIA-758-A, TIA/EIA-222-F * NFPA 70-2005 (NEC), NFPA 76, ANSI/IEEE C-2 (NESC) |
N/A | |||||||
For exceptions/deviations to these standards/codes, see Telecommunications Std 16055, Section 3.3 | ||||||||||
COMMERCIAL BUILDING WIRING | ANSI/TIA/EIA-568-B.1 thru B.3.1, ANSI/TIA/EIA-598-B, ANSI/TIA/EIA-526-7 and 526-14A * ANSI/TIA/EIA-758-A, NFPA 70-2005 (NEC), ANSI/IEEE C-2 (NESC) |
N/A | ||||||||
For exceptions/deviations to these standards/codes, see Telecommunications Std 16055, Section 3.3 | ||||||||||
GROUNDING AND BONDING REQUIREMENTS |
ANSI-J-STD-607-A * NFPA 70-20005 (NEC), ANSI/IEEE C-2 (NESC) |
N/A | ||||||||
For exceptions/deviations to these standards/codes, see Telecommunications Std 16055, Section 3.3 | ||||||||||
GENERAL DESIGN | ISA-S5.1, S5.3 ANSI N323 * |
ISA | Applicable standards are listed in WSRC Eng. Std 01703 | IEEE-323, 336, 338 IEEE-379, 384 |
||||||
INSTRUMENTATION & CONTROLS |
SETPOINTS & SCALING | None | ISA-S67.04 * | |||||||
MONITORING | HPS-N13.1, ANSI-N42.18, NFPA 70-2005 * |
ANS 8.3 (Nuclear criticality only) | ANSI-N320 | |||||||
NFPA | ||||||||||
PROGRAMMABLE DIGITAL EQUIPMENT GENERAL DESIGN |
Applicable standards are listed in WSRC Eng. Std 01703 | |||||||||
HUMAN FACTORS ENGINEERING |
GENERAL DESIGN | IEEE-1023, IEEE-845, NUREG-0700 * | N/A | |||||||
EXPLOSIVES SAFETY |
GENERAL DESIGN | DOE Manual 440.1-1A,
1/9/2006 * NFPA 69 & 495 |
N/A |
* | Codes and standards listed in the lower classifications are also requirements for the higher classifications. Where requirements in the lower classifications conflict with requirements in the higher classifications, the more restrictive requirement governs. |
[**] |
[**] |